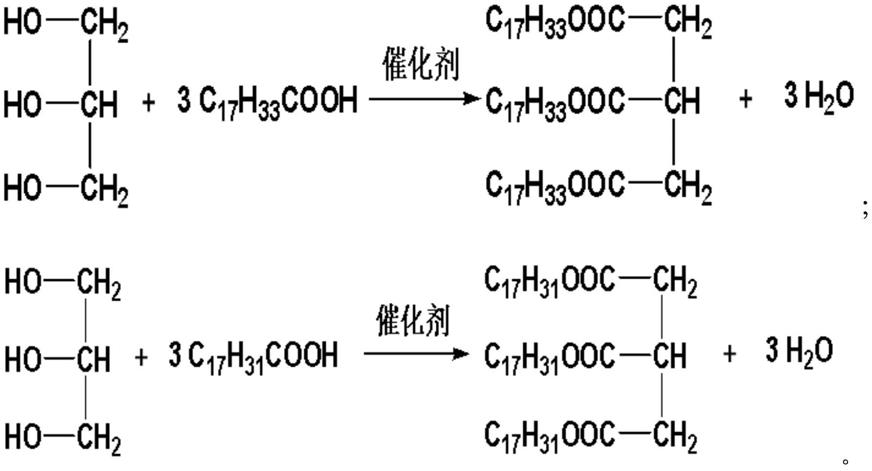
1.本发明属于绝缘油技术领域,具体涉及一种天然酯基础油及其制备方法和天然酯绝缘油及其应用。
背景技术:
2.绝缘油广泛应用于各种电力设备尤其是变压器中,一般起到绝缘及散热的作用。传统绝缘油大多为矿物绝缘油,主要成分为多种烃类的混合物,具有价格低廉及理化介电性能佳的优点,但其燃点较低、防火性较差,生物降解度低、环保性较差。而天然酯绝缘油具备燃点较高、防火性较好及生物降解度高、环保性较好的特点而受到广泛应用。
3.目前的天然酯绝缘油主要源于天然油料作物,如大豆、菜籽、山茶花籽及葵花籽等,其主要制备方法为天然油料作物经过压榨得到粗油,然后通过吸附等流程进行净化,得到较为纯净的绝缘油,但是此方法制备的天然酯绝缘油中包含硬脂酸,使得天然酯绝缘油的倾点较高,难以在低温地区应用,同时其运动粘度较大、流动性较差,不利于电力设备的散热,易造成火灾,危害社会及人身安全。
4.因此,如何降低天然酯绝缘油的倾点及运动粘度成为现有技术的难点。
技术实现要素:
5.本发明的目的在于提供一种天然酯基础油及其制备方法和天然酯绝缘油及其应用。本发明提供的天然酯绝缘油具有较低的倾点及运动粘度。
6.为了实现上述发明目的,本发明提供以下技术方案:
7.本发明提供了一种天然酯基础油的制备方法,包括如下步骤:
8.(1)将木浆浮油进行蒸馏浓缩,得到硫酸盐皂;
9.(2)将所述步骤(1)得到的硫酸盐皂与磷酸混合,进行酸化处理,得到酸化产物;
10.(3)将所述步骤(2)得到的酸化产物进行真空精馏,得到精馏产物;
11.(4)将所述步骤(3)得到的精馏产物与甘油、催化剂和水混合,进行酯化反应,得到天然酯基础油。
12.优选地,所述步骤(1)中蒸馏浓缩的温度为80~100℃,蒸馏浓缩的时间为1~3h。
13.优选地,所述步骤(2)中磷酸与硫酸盐皂的质量比为(3~6):100。
14.优选地,所述步骤(3)中真空精馏的温度为98~102℃或108~112℃或118~122℃。
15.优选地,所述步骤(4)中甘油与精馏产物的体积比为(1~3):1。
16.优选地,所述步骤(4)中催化剂为脂肪酶;所述催化剂与精馏产物的质量比为(1~3):100。
17.优选地,所述步骤(4)中水与精馏产物的质量比为(3~7):100。
18.本发明提供了上述技术方案所述制备方法制备的天然酯基础油,包括三油酸甘油酯和/或三亚油酸甘油酯。
19.本发明还提供了一种天然酯绝缘油,包括抗氧化剂、金属钝化剂、降凝剂、传统天然酯绝缘油、矿物绝缘油和合成酯绝缘油中的一种或多种和上述技术方案所述的天然酯基础油。
20.本发明还提供了上述技术方案所述天然酯绝缘油在电力设备中的应用。本发明提供了一种天然酯基础油的制备方法,包括如下步骤:将木浆浮油进行蒸馏浓缩,得到硫酸盐皂;将得到的硫酸盐皂与磷酸混合,进行酸化处理,得到酸化产物;将得到的酸化产物进行真空精馏,得到精馏产物;将得到的精馏产物与甘油、催化剂和水混合,进行酯化反应,得到天然酯基础油。本发明采用磷酸酸化处理硫酸盐皂,同时分离不皂化物,精馏后进行酯化制备天然酯基础油,制备的天然酯基础油的主要成分为三油酸甘油酯和/或三亚油酸甘油酯,具有较低的倾点及运动粘度。实施例的结果显示,采用本发明制备的天然酯基础油制备的天然酯绝缘油100℃的运动粘度为7.735mm2/s、40℃的运动粘度为32.01mm2/s、倾点为
‑
25℃。
21.此外,本发明采用木浆浮油为原料,能够变废为宝、节约资源、产生附加经济价值。
具体实施方式
22.本发明提供了一种天然酯基础油的制备方法,包括如下步骤:
23.(1)将木浆浮油进行蒸馏浓缩,得到硫酸盐皂;
24.(2)将所述步骤(1)得到的硫酸盐皂与磷酸混合,进行酸化处理,得到酸化产物;
25.(3)将所述步骤(2)得到的酸化产物进行真空精馏,得到精馏产物;
26.(4)将所述步骤(3)得到的精馏产物与甘油、催化剂和水混合,进行酯化反应,得到天然酯基础油。
27.如无特殊说明,本发明对所述各组分的来源没有特殊的限定,采用本领域技术人员熟知的市售产品即可。
28.本发明将木浆浮油进行蒸馏浓缩,得到硫酸盐皂。
29.在本发明中,所述木浆浮油优选来源于造纸工业中的副产品,更优选为:用naoh和na2s的混合液蒸煮松木片的过程中,松木里的脂肪酸和树脂酸被碱皂化,形成脂肪酸和树脂酸的钠盐以及中性物溶解形成的黑液。
30.在本发明中,所述木浆浮油在蒸馏浓缩前优选依次进行水洗和过滤。
31.本发明对所述水洗和过滤的操作没有特殊的限定,采用本领域技术人员熟知的水洗和过滤的操作的技术方案即可。在本发明中,所述水洗和过滤能够去除木浆浮油中不溶性的纤维素,避免对产品性能产生影响。
32.在本发明中,所述蒸馏浓缩的温度优选为80~100℃,更优选为90℃;所述蒸馏浓缩的时间优选为1~3h,更优选为2h。在本发明中,所述蒸馏浓缩过程中去除木浆浮油中的大部分水分,使得硫酸盐皂结晶析出。在本发明中,所述硫酸盐皂的主要成分为树脂酸盐、脂肪酸盐和不皂化物。
33.得到硫酸盐皂后,本发明将所述硫酸盐皂与磷酸混合,进行酸化处理,得到酸化产物。
34.在本发明中,所述磷酸的质量分数优选为33%。在本发明中,所述磷酸与硫酸盐皂的质量比优选为(3~6):100,更优选为(4~5):100。本发明将磷酸与硫酸盐皂的质量比限
定在上述范围内,能够使硫酸盐皂中的脂肪酸盐和树脂酸盐充分酸化,形成脂肪酸和树脂酸进入水相,并将不溶于水相的不皂化物去除。
35.在本发明中,所述酸化处理的温度优选为20~30℃;所述酸化处理的时间优选为10~60min,更优选为20~40min。本发明将所述酸化处理的温度和时间限定在上述范围内,能够使酸化处理更加完全。
36.在本发明中,所述酸化处理过程中的反应方程式如下所示:
37.3rcoona h3po4→
na3po4 3rcooh。
38.酸化处理完成后,本发明优选将所述酸化处理后的产物依次进行水洗和分相,得到酸化产物。
39.在本发明中,所述水洗时的水优选为高纯水;所述水的体积优选为酸化处理后产物体积的15~30%,更优选为20~25%;所述水洗的温度优选为70~90℃,更优选为80℃。在本发明中,所述水洗优选首先在搅拌条件下进行,然后静置。在本发明中,所述搅拌的时间优选为20~40min,更优选为30min;所述搅拌的速率优选为200~400rpm,更优选为300rpm;所述静置的时间优选为1.5~2.5h,更优选为2h。在本发明中,所述水洗用于去除酸化产物中的磷酸。
40.本发明对所述分相的操作没有特殊的限定,采用本领域技术人员熟知的分相的技术方案即可。在本发明中,所述分相用于分出水相,用于后续精馏,并将不溶于水的不皂化物去除,避免对产物性能产生影响。在本发明中,所述不皂化物能够再次提取其中的植物甾醇等应用于药物领域。
41.得到酸化产物后,本发明将所述酸化产物进行真空精馏,得到精馏产物。
42.在本发明中,所述真空精馏的真空度优选为7~9pa,更优选为8pa;所述真空精馏的温度优选为98~102℃或108~112℃或118~122℃,更优选为100℃或110℃或120℃。当真空精馏的温度为98~102℃时,所述蒸馏产物为油酸;当真空精馏的温度为108~112℃时,所述蒸馏产物为油酸和亚油酸的混合物;当真空精馏的温度为118~122℃时,所述蒸馏产物为亚油酸。本发明对所述真空精馏的时间没有特殊的限定,当没有馏分蒸出即可。
43.得到精馏产物后,本发明将所述精馏产物与甘油、催化剂和水混合,进行酯化反应,得到天然酯基础油。
44.在本发明中,所述甘油与精馏产物的体积比优选为(1~3):1,更优选为2:1。在本发明中,所述甘油与精馏产物中的油酸和/或亚油酸反应形成酯。本发明将甘油与精馏产物的体积比限定在上述范围内,能够使精馏产物酯化的更加充分。
45.在本发明中,所述催化剂优选为脂肪酶;所述催化剂与精馏产物的质量比优选为(1~3):100,更优选为2:100。本发明将催化剂与精馏产物的质量比限定在上述范围内,能够催化酯化反应更加充分的进行。
46.在本发明中,所述水与精馏产物的质量比优选为(3~7):100,进一步优选为(4~6):100,最优选为5:100。本发明将水与精馏产物的质量比限定在上述范围内,能够使酯化反应更加充分的进行。
47.本发明对所述精馏产物与甘油、催化剂和水的混合的操作没有特殊的限定,采用本领域技术人员熟知的物料混合的技术方案即可。
48.在本发明中,所述酯化反应优选在搅拌条件下进行;所述搅拌的速率优选为200~
400rpm,更优选为300rpm。在本发明中,所述酯化反应的温度优选为50~70℃,更优选为60℃;所述酯化反应的时间优选为10~14h,更优选为12h。本发明将所述酯化反应的温度和时间限定在上述范围内,能够使酯化反应更加充分,提高转化率。
49.在本发明中,所述酯化反应的方程式如下所示:
[0050][0051]
酯化反应完成后,本发明优选对所述酯化反应的产物进行精炼处理,得到天然酯基础油。
[0052]
在本发明中,所述精炼优选包括依次进行的水洗、脱色、碱炼和干燥。
[0053]
本发明对所述水洗的操作没有特殊的限定,采用本领域技术人员熟知的水洗的技术方案即可。
[0054]
在本发明中,所述脱色优选为采用白土和活性炭混合进行脱色。在本发明中,所述白土的质量优选为酯化产物质量的1~3%,更优选为2%;所述活性炭的质量优选为酯化产物质量的1~3%,更优选为2%;所述脱色的温度优选为80~100℃,更优选为90℃;所述脱色的时间优选为0.5~1.5h,更优选为1h;所述脱色的真空度优选为7~9pa,更优选为8pa。本发明将所述脱色的脱色剂、温度、时间等参数限定在上述范围内,能够使脱色更加完全。
[0055]
脱色完成后,本发明优选将所述脱色的产物进行过滤。
[0056]
本发明对所述过滤的操作没有特殊的限定,采用本领域技术人员熟知的过滤的技术方案即可。在本发明中,所述过滤用于去除白土和活性炭。
[0057]
在本发明中,所述碱炼优选加入碱液。在本发明中,所述碱液优选为氢氧化钠溶液;所述碱液的质量浓度优选为30%;所述碱液的体积优选为脱色产物体积的20%;所述碱炼优选为先在45℃处理3h,再在85℃处理2h。在本发明中,所述碱炼优选在搅拌条件下进行;所述搅拌的速率优选为200~400rpm,更优选为300rpm。在本发明中,所述碱炼用于去除产物中的杂质。本发明将碱炼的温度和时间等参数限定在上述范围内,能够将杂质充分去除,提高产物纯度。
[0058]
在本发明中,所述干燥的温度优选为60~80℃,更优选为70℃;所述干燥的时间优选为1~3h,更优选为2h;所述干燥的真空度优选为7~9pa,更优选为8pa。本发明将干燥的温度和时间等限定在上述范围内,能够充分去除产物中的水分,提高产物纯度。
[0059]
本发明采用磷酸酸化处理硫酸盐皂,同时分离不皂化物,再进行酯化制备天然酯基础油,制备的天然酯基础油的主要成分为三油酸甘油酯和/或三亚油酸甘油酯,控制各组分的用量、反应温度和时间等工艺参数,提高产物纯度,此外,本发明采用木浆浮油为原料,能够变废为宝、节约资源、产生附加经济价值。
[0060]
本发明提供了上述技术方案所述制备方法制备的天然酯基础油,包括三油酸甘油酯和/或三亚油酸甘油酯。
[0061]
本发明提供的天然酯基础油具有较低的倾点及运动粘度。
[0062]
本发明还提供了一种天然酯绝缘油,包括抗氧化剂、金属钝化剂、降凝剂、传统天然酯绝缘油、矿物绝缘油和合成酯绝缘油中的一种或多种和上述技术方案所述的天然酯基础油。
[0063]
在本发明中,所述抗氧化剂优选包括丁基对苯二酚、2,6
‑
二叔丁基
‑4‑
甲基苯酚、没食子酸丙酯、丁羟基茴香醚或生育酚;所述抗氧化剂的质量分数优选≤5%。在本发明中,所述抗氧化剂用于提高天然酯绝缘油的抗氧化性能。
[0064]
在本发明中,所述金属钝化剂优选包括苯并三氮唑、5
‑
甲基苯并三氮唑、n
‑
[2
‑
(2
‑
乙基己基)
‑
氨甲基]
‑
甲基苯并三氮唑或irgamet39;所述金属钝化剂的质量分数优选≤0.01%。在本发明中,所述金属钝化剂用于提高天然酯绝缘油的耐腐蚀性。
[0065]
在本发明中,所述降凝剂包括长链烷基萘、聚甲基丙烯酸酯或聚α
‑
烯烃;所述降凝剂的质量分数优选≤0.02%。在本发明中,所述降凝剂用于降低天然酯绝缘油的凝固点。
[0066]
本发明对所述传统天然酯绝缘油、矿物绝缘油和合成酯绝缘油的具体种类没有特殊的限定,采用本领域技术人员熟知的市售产品即可。在本发明中,所述传统天然酯绝缘油、矿物绝缘油和合成酯绝缘油的质量分数优选为0~100%。
[0067]
本发明提供的天然酯绝缘油具有较低的倾点及运动粘度。
[0068]
本发明对所述天然酯绝缘油的制备方法没有特殊的限定,采用本领域技术人员熟知的物料混合的技术方案即可。
[0069]
本发明还提供了上述技术方案所述天然酯绝缘油在电力设备中的应用。
[0070]
本发明对所述天然酯绝缘油在电力设备中的应用的操作没有特殊的限定,采用本领域技术人员熟知的天然酯绝缘油在电力设备中的应用的技术方案即可。
[0071]
下面将结合本发明中的实施例,对本发明中的技术方案进行清楚、完整地描述。显然,所描述的实施例仅仅是本发明一部分实施例,而不是全部的实施例。基于本发明中的实施例,本领域普通技术人员在没有做出创造性劳动前提下所获得的所有其他实施例,都属于本发明保护的范围。
[0072]
实施例1
[0073]
(1)将木浆浮油依次进行水洗、过滤,然后在90℃蒸馏浓缩2h,得到硫酸盐皂;
[0074]
(2)将硫酸盐皂与质量分数为33%的磷酸混合(磷酸与硫酸盐皂的质量比为5:100),25℃进行酸化处理30min,然后加入产物体积20%的高纯水,80℃搅拌30min,静置2h,分出水相,得到酸化产物;
[0075]
(3)将酸化产物在100℃、8pa条件下真空精馏,得到精馏产物油酸;
[0076]
(4)将精馏产物油酸与甘油(甘油与精馏产物的体积比为2:1)、脂肪酶(脂肪酶与精馏产物的质量比为2:100)和水(水与精馏产物的质量比为5:100)混合,60℃搅拌反应12h
(油酸转化率为96%),然后将产物进行水洗,加入产物质量2%的白土和产物质量2%的活性炭,90℃、8pa条件下真空进行脱色,过滤,然后加入产物体积20%的氢氧化钠溶液(质量分数30%)、45℃搅拌3h再85℃搅拌2h进行碱炼,最后在70℃、8pa条件下真空干燥2h,得到天然酯基础油,其主要成分为三油酸甘油酯。
[0077]
实施例2
[0078]
在实施例1制备的天然酯基础油中,加入质量分数为0.3%的丁羟基茴香醚和质量分数为0.01%的金属钝化剂irgamet39,混合均匀,得到天然酯绝缘油。
[0079]
实施例3
[0080]
(1)将木浆浮油依次进行水洗、过滤,然后在90℃蒸馏浓缩2h,得到硫酸盐皂;
[0081]
(2)将硫酸盐皂与质量分数为33%的磷酸混合(磷酸与硫酸盐皂的质量比为5:100),25℃进行酸化处理30min,然后加入产物体积20%的高纯水,80℃搅拌30min,静置2h,分出水相,得到酸化产物;
[0082]
(3)将酸化产物在120℃、8pa条件下真空精馏,得到精馏产物亚油酸;
[0083]
(4)将精馏产物亚油酸与甘油(甘油与精馏产物的体积比为2:1)、脂肪酶(脂肪酶与精馏产物的质量比为2:100)和水(水与精馏产物的质量比为5:100)混合,60℃搅拌反应12h(亚油酸转化率为96%),然后将产物进行水洗,加入产物质量2%的白土和产物质量2%的活性炭,90℃、8pa条件下真空进行脱色,过滤,然后加入产物体积20%的氢氧化钠溶液(质量分数30%)、45℃搅拌3h再85℃搅拌2h进行碱炼,最后在70℃、8pa条件下真空干燥2h,得到天然酯基础油,其主要成分为三亚油酸甘油酯。
[0084]
实施例4
[0085]
在实施例2制备的天然酯基础油中,加入质量分数为0.3%的丁羟基茴香醚、质量分数为0.01%的金属钝化剂irgamet39和质量分数为0.01%降凝剂聚甲基丙烯酸甲酯,混合均匀,得到天然酯绝缘油。
[0086]
实施例5
[0087]
(1)将木浆浮油依次进行水洗、过滤,然后在90℃蒸馏浓缩2h,得到硫酸盐皂;
[0088]
(2)将硫酸盐皂与质量分数为33%的磷酸混合(磷酸与硫酸盐皂的质量比为5:100),25℃进行酸化处理30min,然后加入产物体积20%的高纯水,80℃搅拌30min,静置2h,分出水相,得到酸化产物;
[0089]
(3)将酸化产物在110℃、8pa条件下真空精馏,得到精馏产物油酸和亚油酸的混合物;
[0090]
(4)将精馏产物与甘油(甘油与精馏产物的体积比为2:1)、脂肪酶(脂肪酶与精馏产物的质量比为2:100)和水(水与精馏产物的质量比为5:100)混合,60℃搅拌反应12h(油酸和亚油酸的转化率为96%),然后将产物进行水洗,加入产物质量2%的白土和产物质量2%的活性炭,90℃、8pa条件下真空进行脱色,过滤,然后加入产物体积20%的氢氧化钠溶液(质量分数30%)、45℃搅拌3h再85℃搅拌2h进行碱炼,最后在70℃、8pa条件下真空干燥2h,得到天然酯基础油,其主要成分为三油酸甘油酯和三亚油酸甘油酯的混合物(三油酸甘油酯和三亚油酸甘油酯的质量比为2:8)。
[0091]
实施例6
[0092]
在实施例3制备的天然酯基础油中,加入质量分数为0.3%的丁羟基茴香醚和质量
分数为0.01%的金属钝化剂irgamet39,混合均匀,得到天然酯绝缘油。
[0093]
测试实施例2、4、6制备的天然酯绝缘油的生物降解率,结果表明,实施例2、4、6制备的天然酯绝缘油在28天内的生物降解率>90%。
[0094]
将实施例2、4、6制备的天然酯绝缘油和传统天然酯绝缘油(fr3)进行性能测试,各测试标准和数据列于表1。
[0095]
表1实施例2、4、6制备的天然酯绝缘油和传统天然酯绝缘油的性能
[0096][0097]
从表1中可以看出,本发明制备的天然酯绝缘油具有较低的运动粘度,有利于设备散热,具有较低的倾点,更利于应用于低温地区。
[0098]
以上所述仅是本发明的优选实施方式,应当指出,对于本技术领域的普通技术人员来说,在不脱离本发明原理的前提下,还可以做出若干改进和润饰,这些改进和润饰也应视为本发明的保护范围。
再多了解一些
本文用于企业家、创业者技术爱好者查询,结果仅供参考。