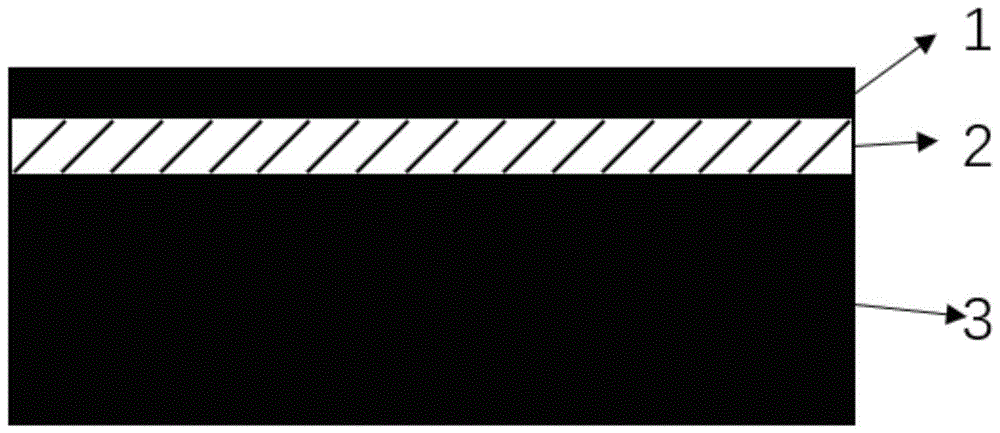
本发明涉及一种适用于宇宙微波背景辐射探测的超导探测器玻璃窗的制备工艺,属于超导电子学技术领域。
背景技术:
超导电子学是超导物理与电子技术相结合的一门交叉学科,以超导微观理论和多种量子效应为基础,以约瑟夫森结、超导平面微纳结构为主要结构单元,可形成无源器件、微波有源器件、传感器/探测器等多种超导电子学器件和电路,在噪声、速度、功耗、带宽等方面具有传统半导体器件和电路无可比拟的优势,在极高限灵敏度探测、量子信息处理、量子计量、高性能计算和前沿基础研究等领域可发挥不可替代的作用。特别地,超导探测器,如超导转变边探测器及微波动态电感传感器,具备超高灵敏度,是目前国际上正在研发的用于宇宙微波背景辐射探测的一类探测器。该类探测器的研制过程非常复杂,包含十几道工艺,如超导铌导线、超导微带线、超导转变边探测器、微波动态电感传感器、过孔、高指数介质层(如sinx、sio2等)、超薄玻璃窗(0.5~20μm)的制备等。为保证制备出的探测器具备超高灵敏度,制备工艺的每一步都必须保证100%的成功率;第二,制备出的探测器在宇宙极限温度(1k甚至100mk以下)都必须具备超导电性;第三,为保证超导材料不被复杂的集成电路工艺损坏,整个探测器研制过程要求所有工艺温度不能超过150℃,这对整个集成电路工艺都提出了挑战。其复杂度及诸多限制导致制备此类探测器的难度极大。
针对此类超导探测器,为进行阻抗匹配,接收宇宙微波背景辐射信号的探测器主体omt(orthmodetransducer)需位于超薄硅或超薄氮化硅玻璃窗上;为降低噪声,微波动态电感传感器需位于超薄硅玻璃窗上;为降低热导,超导转变边探测器同样需位于超薄氮化硅玻璃窗上。因此,超薄玻璃窗在这类探测器中是非常重要的一步工艺,然而,此类探测器研制的复杂性决定了传统的玻璃窗研制方案无法应用于此类探测器的研制中,这是因为传统的玻璃窗研制通常采用koh溶液进行湿法刻蚀来获得氮化硅玻璃窗,此类方法获得的玻璃窗的侧壁有一定的角度(54.7°),而用于宇宙微波背景辐射探测的超导探测器玻璃窗的侧壁需为90°或接近90°,因此湿法刻蚀工艺无法满足要求。用于刻蚀90°侧壁的工艺为bosch工艺,为保护侧壁,通常采用c4f8气体沉积聚合物;采用sf6及o2混合气刻蚀硅,采用此种方法最终可以刻蚀出90°侧壁的玻璃窗。
通常玻璃窗的厚度要求几十微米甚至几百微米,然而bosch工艺要求玻璃窗的厚度不能太薄。这是因为采用bosch工艺进行刻蚀时,会在晶圆的玻璃窗一侧通一定气压的氦气(3~20mtorr),用于耗散bosch工艺过程中由等离子体轰击样品带来的热量,此种办法可保证刻蚀的均一性及稳定性。然而,当玻璃窗的厚度只有几微米甚至几百纳米时,极薄的玻璃窗无法承受背部的氦气气压,从而导致玻璃窗破碎,器件研发失败。
此外,在研制宇宙微波背景辐射探测器过程中,除了要制备玻璃窗外,还需要考虑探测器从晶圆上分离的问题。通常,制备探测器芯片的方法是首先进行工艺加工,然后采用晶圆切割机将芯片按照所需尺寸进行切割。此种方案虽简单易操作,然而在制备带玻璃窗的探测器时,切割机的切割力度太大,极易破坏玻璃窗,特别是针对含大阵列玻璃窗的探测器时,任何一个玻璃窗的破碎都将使得整个芯片无法使用。
技术实现要素:
本发明所要解决的技术问题是:解决制备宇宙微波背景辐射探测的超导探测器玻璃窗时极薄玻璃窗无法耐受高背部氦气气压的难题;解决玻璃窗制备过程中玻璃窗一侧已经制备好的探测器图形被损坏的难题;解决在整个工艺过程,如芯片与玻璃窗晶圆分离、光刻胶残留物去除、芯片清洗、芯片烘干时极薄玻璃窗易碎的难题。
为了解决上述问题,本发明提供了一种适用于超导探测器玻璃窗的制备工艺的制备工艺,其特征在于,包括以下步骤:
步骤1):准备玻璃窗晶圆,其依次包括硅或氮化硅玻璃窗层、二氧化硅截止层及硅层;
步骤2):在玻璃窗层采用光刻工艺制备芯片边界切割槽一的图形,并采用氟基气体刻蚀芯片边界切割槽一,直到将芯片边界切割槽一内的硅或氮化硅及二氧化硅截止层全部刻蚀完毕;
步骤3):采用有机溶剂丙酮溶解石蜡,制备粘合物;将玻璃窗晶圆的玻璃窗层一侧与一片透明的承载晶圆用制备好的粘合物键合;玻璃窗层与承载晶圆进行键合时,须保证两者之间没有气泡,根据需要辅助以压实的砝码及加热装置;
步骤4):采用背部对准方式在玻璃窗晶圆的硅层一侧对应芯片边界切割槽一的位置采用光刻工艺制备芯片边界切割槽二及玻璃窗图案;然后,采用bosch工艺刻蚀出芯片边界切割槽二及玻璃窗结构,直到将硅层全部刻蚀完毕,露出二氧化硅截止层;
步骤5):采用氢氟酸或氟化氢气体去除玻璃窗晶圆上露出的二氧化硅层;
步骤6):采用氧气等离子体清洗经历过深硅刻蚀工艺的玻璃窗晶圆;
步骤7):将玻璃窗晶圆和承载晶圆的键合结构放置在可溶解粘合物的溶剂中浸泡,直到玻璃窗晶圆与承载晶圆分开,含玻璃窗结构的芯片从玻璃窗晶圆上分开;其中,为防止被溶解的粘合物或光刻胶残留物回落到晶圆上,玻璃窗一侧朝下放置;为使玻璃窗晶圆和承载晶圆的键合结构在不接触容器底部的情况下朝下放置,需使用晶圆支架进行配合;为防止分离的玻璃窗在接触容器底部时由于硬接触带来的玻璃窗破碎的风险,在容器底部放置缓冲物,为芯片落到容器底部提供缓冲;
步骤8):采用有机溶剂浸泡方式清洗从玻璃窗晶圆上分开的芯片;
步骤9):风干或烘干芯片。
优选地,所述步骤1)中硅或氮化硅玻璃窗面的厚度为0.3~20μm,二氧化硅截止层的厚度为200~500nm,普通硅层的厚度为200~1000μm。
优选地,所述步骤2)中芯片边界切割槽一的形状为方形、长方形、多边形或圆形;所述氟基气体采用chf3、sf6或cf4,其气压为10~150mtorr,刻蚀功率为100~1000w。
优选地,所述步骤3)中溶解石蜡时,石蜡与丙酮的质量比为10:1~1:10;所述砝码材质为铜或铝;所述加热装置为热板、烘箱、真空烘箱,加热的温度为100~150℃。
优选地,所述步骤5)中氢氟酸的质量浓度为2%~100%;所述氟化氢气体的纯度为99%~99.9999%;所述氢氟酸为氢氟酸与氟化铵的混合物,两者的质量比为1:50~50:1。
优选地,所述步骤6)中氧气等离子的氧气气压为10~150mtorr,功率为100~1000w。
优选地,所述步骤7)中根据图纸设计不同,浸泡时间区间为0.5~72小时;所述晶圆支架为中空的长方形、正方形或圆形框架;所述缓冲物为无尘纸。
优选地,所述步骤8)中有机溶剂的纯度为分析纯或cmos纯;所述有机溶剂为丙酮、异丙醇或乙醇。
优选地,所述步骤9)中烘干的温度为100~150℃。
相比现有技术,本发明具有如下有益效果:
1.本发明提出的玻璃窗制备方案中的键合方法,一方面能解决bosch工艺中极薄玻璃窗无法耐受高背部氦气气压的难题;另一方面能保证已制备探测器图形的玻璃窗一侧被完全保护,将探测器图形的结构完整性提高到100%;第三,承载晶圆的透明设计还为下一步的背部对准提供可行性。
2.本发明提出的玻璃窗制备方案从芯片分离、光刻胶残留物去除、芯片清洗、芯片烘干等多角度出发来解决玻璃窗破裂的难题,将玻璃窗的制备成功率提高到100%。在芯片分离中,创造性地采用刻蚀工艺来进行芯片分离,此种方法替代了传统的切割力度大的晶圆切割机来进行芯片分离,从而规避了芯片分离时玻璃窗破坏的风险;在光刻胶残留物去除中,采用氧气等离子体清洗,规避了高强度的超声清洗带来的玻璃窗破坏的风险;在芯片清洗中,采用在有机溶剂中浸泡的方式清洗芯片,规避了高强度的超声清洗带来的玻璃窗破坏的风险;在芯片烘干中,采用风干或晾干方式,规避了高压氮气带来的玻璃窗破坏的风险。
3.本发明采用氢氟酸或氟化氢气体去除玻璃窗上残留的二氧化硅层,可降低超导探测器的噪声,提高超导探测器的性能。
4.本发明所提出的方案均采用传统微纳加工工艺中常用的设备,无需添置新设备,制造成本低,且方案设计简单。
5.本发明除能解决宇宙微波背景辐射探测的超导探测器玻璃窗的研制需求,还可应用于x射线光源上所需的超导探测器的研制上,具备广泛适用性。
附图说明
图1-9为本发明提供的适用于超导探测器玻璃窗的制备工艺中不同步骤下的玻璃窗晶圆、承载晶圆、玻璃窗晶圆和承载晶圆的键合结构截面;其中,图3为图2的俯视图,图6为图5的俯视图。
具体实施方式
为使本发明更明显易懂,兹以优选实施例,并配合附图作详细说明如下。
实施例
一种适用于超导探测器玻璃窗的制备工艺,包括以下步骤:
步骤1:准备玻璃窗晶圆,其依次包括硅或氮化硅材质的玻璃窗层1、二氧化硅截止层2及硅层3,如图1所示;
步骤2:在玻璃窗层1侧采用光刻工艺制备芯片边界切割槽的图形,并采用氟基气体刻蚀芯片边界切割槽4,直到将芯片边界切割槽4内的硅或氮化硅及二氧化硅截止层全部刻蚀完毕,如图2、3所示;
步骤3:采用有机溶剂丙酮溶解石蜡,制备粘合物;将玻璃窗晶圆的玻璃窗层1一侧与一片承载晶圆5用制备好的粘合物键合,如图4所示;玻璃窗层1与承载晶圆5进行键合时,须保证两者之间没有气泡,可辅助以压实的砝码及热板、烘箱或真空烘箱;
步骤4:在玻璃窗晶圆的硅层3一侧对应芯片边界切割槽一4的位置采用光刻工艺制备芯片边界切割槽二及玻璃窗图案;然后,采用bosch工艺刻蚀出芯片边界切割槽二6及玻璃窗结构7,直到将硅层3全部刻蚀完毕,露出二氧化硅截止层2,如图5、6所示;
步骤5:采用氢氟酸或氟化氢气体去除玻璃窗晶圆上露出的二氧化硅层2,如图7所示;
步骤6:采用氧气等离子体清洗经历过深硅刻蚀工艺的玻璃窗晶圆;
步骤7:将键合晶圆放置在可溶解粘合物的溶剂中浸泡,直到玻璃窗晶圆与承载晶圆5分开,含玻璃窗结构的芯片从玻璃窗晶圆上分开;其中,为防止被溶解的粘合物、光刻胶残留物回落到晶圆上,玻璃窗一侧朝下放置;为使键合晶圆在不接触容器底部的情况下朝下放置,需使用晶圆支架8进行配合,如图8所示;为防止分离的玻璃窗在接触容器底部时由于硬接触带来的玻璃窗破碎的风险,可在容器10底部放置缓冲物9,为芯片落到容器底部提供缓冲,如图9所示。
步骤8:采用有机溶剂浸泡方式清洗从玻璃窗晶圆上分开的芯片;
步骤9:采用风干、低温烘烤等方式烘干芯片。
所述步骤1中玻璃窗层1的厚度为0.3~20μm,二氧化硅截止层2的厚度为200~500nm,硅层3的厚度为200~1000μm。
所述步骤2中光刻时可采用光刻胶制备图案,光刻胶厚度为4~20μm。
所述步骤2中氟基气体为chf3、sf6或cf4,气压为10~150mtorr,刻蚀功率100~1000w。
所述步骤2中芯片边界切割槽的图形可为长方形、正方形、圆形。
所述步骤3中石蜡粘合物可采用丙酮溶解,石蜡与丙酮的混合比区间为10:1~1:10。
所述步骤3中砝码材质为铜、铝。
所述步骤3中热板、烘箱、真空烘箱的温度为100~150℃。
所述步骤5中氢氟酸的浓度为2%~100%。
所述步骤5中氟化氢气体的纯度为99%~99.9999%。
所述步骤5中氢氟酸可为氢氟酸与氟化铵的混合物(即boe),混合比区间为1:50~50:1。
所述步骤6中氧气等离子的氧气气压区间为10~150mtorr,功率区间为100~1000w。
所述步骤7中根据图纸设计不同,浸泡时间区间为0.5~72小时。
所述步骤7中的晶圆支架可为中空的长方形、正方形、圆形框架。
所述步骤7中的缓冲物为无尘纸。
所述步骤8中有机溶剂为分析纯或cmos纯。
所述步骤8中有机溶剂为丙酮、异丙醇、乙醇等。
所述步骤9中加热时温度为100~150℃。
本文用于企业家、创业者技术爱好者查询,结果仅供参考。