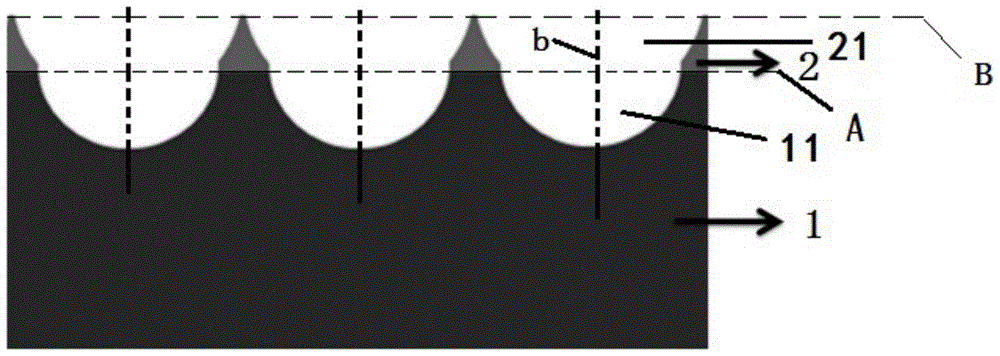
本发明涉及一种硅基网络结构领域,尤其涉及一种微纳米复合硅基网络结构及其制备方法。
背景技术:
近年来,随着微纳加工技术的不断发展,广大研究者通过平面微纳米加工技术、探针工艺及模型工艺制备各种微纳米阵列结构。例如中国发明专利cn101339128a《一种表面等离子体共振成像纳米结构阵列芯片制备方法》,利用真空真镀、激光直写、光刻等半导体加工工艺制备了周期性纳米结构的金属点阵芯片,并用于表面等离子体共振成像阵列芯片。中国专利cn103668130a《一种金属纳米结构的制备方法》采用光刻、化学合成等方法制备一种金属纳米结构,该方法工艺简单、效率高,可对结构形状与位置精准控制,有效提高了金属纳米结构材料光提取效率和光吸收效率。中国专利cn102556952b《金属杯-柱复合纳米结构阵列及其制备方法》,以单层聚苯乙烯球为掩膜采用等离子体刻蚀技术制备了一种具有较小纳米尺寸间隙的金属杯-柱复合纳米结构阵列并应于拉曼检测,该发明制备方法兼容性好、效率高、成本低并实现了单分子的拉曼检测。微纳米阵列结构的制备方法大体可以分为人工构筑法和自组装法两大类,人工构筑法包括光刻技术、束流刻蚀技术、纳米压印技术及微接触印刷等;自组装法包括分子自组装、胶体自组装及模板法等。借助于纳米材料的优异性能,微纳米阵列结构不但具有结构均一有序、高比表面积,同时在电学、磁学及光学等方面也都展现出诸多优异的性能,比如电子散射效应、量子效应、强光吸收、发光及非线性光学特性等特点,因而利用微纳加工技术制备微纳阵列结构,并应用于电子、生物、化工及储能等领域具有重要意义。
技术实现要素:
本发明的主要目的,在于提供一种新型硅基网络结构及其制备方法,能够制备多种不同材料复合的不同尺寸的葫芦状孔洞微纳米阵列结构。
所述硅基网络结构包括:硅基底,上表面具有多个阵列分布的球状孔洞;材料层,位于所述硅基底上表面,所述材料层具有多个阵列分布的半球状穿孔,其中所述半球状穿孔正好位于所述球状孔洞上方并且连通所述球状孔洞,而共同组成多个阵列分布的葫芦状孔洞;包覆层,设置于所述硅基底与所述材料层表面上,沿着所述葫芦状孔洞的内表面分布,其中,所述包覆层包括金属、金属化合物或高分子材料层。
在一实施例中,所述的硅基底上表面与材料层下表面分布在同一平面;所述硅基底上表面的球状孔洞为有球缺的孔洞;所述材料层的半球状穿孔为有球带体的孔洞,所述球带体上表面与材料层上表面分布在同一平面,所述球带体下表面与所述材料层下表面分布在同一平面;所述的球缺与球带体同轴;所述有球缺的孔洞和球带体的孔洞共同组成所述葫芦状孔洞。
在一实施例中,所述葫芦状孔洞为六方密排或者立方密排成阵列结构,所述阵列结构呈网络状分布。
在一实施例中,所述硅基底上表面的球状孔洞其直径为100nm~100μm;所述材料层的材料包括但不限于tio2、zno、al2o3、cuo、tin中的一种,位于所述材料层上的半球状穿孔其直径为100nm~100μm,高度为50nm~50μm。
在一实施例中,所述包覆层材料为金属、金属化合物或高分子材料,其中,金属包括但不限于pt/au/ag/cu/al/zn/cr/ti中的至少一种;金属化合物包括但不限于tio2、zno、al2o3、cuo、gan、tin中的一种;高分子材料包括但不限于聚乙烯、聚丙烯、聚氯乙烯、酚醛树脂中的至少一种;所述包覆层的厚度为5~500nm。
本发明提供一种硅基网络结构的制备方法,包括以下步骤:在硅基底上表面自组装微纳米球阵列;在具自组装了微纳米球阵列的所述硅基底表面旋涂前驱体溶液;将所述硅基底放置在退火炉中退火,在所述硅基底表面形成微纳米碗阵列结构;以等离子刻蚀技术对所述硅基底进行刻蚀,形成微纳米葫芦状阵列结构;在微纳米葫芦状阵列结构表面形成金属、金属化合物、或高分子材料层,以形成葫芦状复合微纳米阵列结构。
在一实施例中,所述在硅基底上表面自组装微纳米球阵列的步骤,包括:将微纳米球悬浮液与叔丁醇按体积比1:1混合,并利用微注射器缓慢注入放有所述硅基底的水溶液中;将水溶液放干,使所述微纳米球沉积在硅基底表面,其中所述微纳米球为聚苯乙烯或二氧化硅纳米球,并且会自组装成六方密排的单层纳米球阵列于所述硅基底表面。
在一实施例中,所述退火温度为400-800℃,退火时间为20~60min。
在一实施例中,所述以等离子体刻蚀技术对所述硅基底进行刻蚀的步骤,是采用电感耦合等离子体(icp)系统,刻蚀气体为sf6或o2;刻蚀气体的流速为5~40sccm(standardcubiccentimeterperminute),o2流速为5~40sccm,刻蚀时间为5~2000s,icp功率为200~300w,rf功率为10~30w。
在一实施例中,所述的前驱体溶液,包括tio2溶液、zno溶液、cuo溶液中的至少一种。
与现有技术相比,本发明的有益效果是:
本发明能够制备多种不同材料复合的不同尺寸的葫芦状孔洞微纳米阵列结构,其中,微纳米阵列结是由不同材料层叠加构成,且不同材料层分别具有球状孔洞与半球状穿孔而共同组成葫芦状孔洞。藉此,可复合两种以上材料的性质,同时可形成良好的微纳米光学腔,有效的增强光的吸收。本发明制备工艺简单,通过退火、等离子体刻蚀、磁控溅射等工艺制备得到葫芦状孔洞微纳米阵列结构。所述微纳米阵列结构能够有效地均匀分散分析物,同时还具有微纳米阵列结构独特的半导体光电性质,如高的光吸收率、表面等离激元效应等,在物理、化学、能源及生命科学等领域具有潜在应用。
此外,本发明采用溶液法在硅基底表面自组装微纳米球掩膜,其相比于传统的旋涂法及提拉法,操作更加简单,有效减少了微纳米球的使用,同时工艺稳定,在硅基底表面可获得均一单层六方密排的微纳米球阵列结构。本发明以退火后形成的微纳米碗阵列结构直接作为掩膜进行等离子体刻蚀获得六方密排的微纳米槽阵列结构,工艺步骤简单连续。
附图说明
下面结合附图和实施例对本发明作进一步说明。
图1:本发明所制备葫芦状孔洞的硅基底阵列结构截面示意图。
图2:本发明所制备硅基底阵列结构表面微观形貌图。
图3:本发明所制备葫芦状孔洞的硅基底阵列结构截面示意图。
图4:本发明所制备硅基底阵列结构表面微观形貌图。
图5:本发明所提供硅基网络结构的制备方法流程图。
图6:本发明所提供的硅基网络结构的制备工艺图。
具体实施方式
下面将结合本发明实施例中的附图,对本发明的技术方案进行描述,显然,所描述的实施例是本申请一部分实施例,而不是全部的实施例。基于本申请中的实施例,本领域普通技术人员在没有做出创造性劳动前提下所获得的所有其他实施例,都属于本申请保护的范围。
本发明提供一种硅基网络结构及其制备方法,能够制备多种不同材料复合的不同尺寸的葫芦状孔洞微纳米阵列结构。
请参考图1至图4,图1为具有葫芦状孔洞的硅基底阵列结构截面示意图;图2为硅基底阵列结构表面微观形貌图;图3为硅基底阵列结构截面示意图;图4为硅基底阵列结构表面微观形貌图。
请同时参见图1和图3,硅基网络结构包括:硅基底1,上表面具有多个阵列分布的球状孔洞11;材料层2,位于硅基底1上表面,材料层2具有多个阵列分布的半球状穿孔21,其中所述半球状穿孔21正好位于所述球状孔洞11上方并且连通所述球状孔洞11,而共同组成多个阵列分布的葫芦状孔洞;包覆层3,设置于硅基底1与材料层2表面上,沿着所述葫芦状孔洞的内表面分布,其中,包覆层3包括金属、金属化合物或高分子材料层。
在一实施例中,所述的硅基底1上表面与材料层2下表面分布在同一平面a;硅基底1上表面的球状孔洞11为有球缺的孔洞,材料层2的半球状穿孔21为有球带体的孔洞,所述球带体上表面与材料层2上表面分布在同一平面b,所述球带体下表面与材料层2下表面分布在同一平面a;所述的球缺与球带体同轴b;所述有球缺的孔洞和球带体的孔洞共同组成葫芦状孔洞。在此实施例中,所述球缺的球缺底面与所述硅基底上表面分布在同一平面a;所述球带体下表面与所述球缺的球缺底面大小相同且与所述材料层下表面分布在同一平面a。
请同时参见图2和图4中俯视硅基底1上表面的微观形貌图,在一实施例中,所述葫芦状孔洞为六方密排或者立方密排成阵列结构,所述阵列结构呈网络状分布。
在一实施例中,硅基底1上表面的球状孔洞11其直径为100nm-100μm,材料层2的材料包括但不限于tio2、zno、al2o3、cuo、tin中的一种,位于材料层2上的半球状穿孔21其直径为100nm~100μm,高度为50nm~50μm。
在一实施例中,所述包覆层3材料为金属、金属化合物或高分子材料。其中,金属包括但不限于pt、au、ag、cu、al、zn、cr、ti中的至少一种;金属化合物包括但不限于tio2、zno、al2o3、cuo、gan、tin中的一种;高分子材料包括但不限于聚乙烯、聚丙烯、聚氯乙烯、酚醛树脂中的至少一种。包覆层3的厚度为5~500nm。
请参照图5和图6,本发明亦提供一种制备上述硅基网络结构的制备方法及其工艺制程,包括以下步骤:
s1:在硅基底1上表面自组装微纳米球阵列4,如图6(a)所示;
s2:在具自组装了微纳米球阵列的所述硅基底表面旋涂前驱体溶液,如图6(b)所示;
s3:将所述硅基底放置在退火炉中退火,在所述硅基底表面形成微纳米碗阵列结构,如图6(c)所示;
s4:以等离子刻蚀技术对所述硅基底进行刻蚀,形成微纳米葫芦状阵列结构,如图1所示,如图6(d)所示;
s5:如图6(e)所示,在微纳米葫芦状阵列结构表面形成金属、金属化合物、或高分子材料层,以形成如图3所示的葫芦状复合微纳米阵列结构。
在一实施例中,所述在硅基底上表面自组装微纳米球阵列的步骤,包括:将微纳米球悬浮液与叔丁醇按体积比1:1混合,并利用微注射器缓慢注入放有所述硅基底的水溶液中;将水溶液放干,使所述微纳米球沉积在硅基底表面,其中所述微纳米球为聚苯乙烯或二氧化硅纳米球,并且会自组装成六方密排的单层纳米球阵列于所述硅基底表面。
在一实施例中,硅基底为单面或双面抛光的硅片或二氧化硅等其他衬底材料。
在一实施例中,所述退火温度为400~800℃,退火时间为20~60min。优选的温度范围为450~550℃,时间为20~40mins。
在一实施例中,所述以等离子刻蚀技术对所述硅基底进行刻蚀的步骤,是采用电感耦合等离子体(icp)系统,刻蚀气体为sf6或o2;刻蚀气体的流速为5~40sccm(standardcubiccentimeterperminute),o2流速为5~40sccm,刻蚀时间为5s~2000s,icp功率为200~300w,rf功率为10~30w。
在一实施例中,所述的前驱体溶液,包括tio2溶液、zno溶液、cuo溶液中的至少一种。
在一实施例中,在自组装微纳米球阵列的步骤前,更包括对硅基底进行rca(radiocorporationofamerica)清洗,于清洗后再于硅基底表面自组装六方密排的单层聚苯乙烯或二氧化硅微纳米球。
在一实施例中,所述微纳米球分散液浓度为2%~20%wt,微纳米球直径为300nm~10μm。
在一实施例中,tio2溶液浓度范围为0.1~0.5mol/l。
在一实施例中,进行等离子体刻蚀的时间在10~3000s。
在一实施例中,步骤s5所述的金属包括pt/au/ag/cu/al/zn/cr中的至少一种。
以下并通过六个具体实施例详细说明本发明所提供制备方法的制作流程与条件。
实施例1:
a、硅基底的制备
sa1:选取电阻率为0.001-0.009ω·cm,厚度为800μm的4英寸n型双面抛光的硅片。
sa2:对sa1中的硅片进行rca标准清洗以去除表面各种杂质和污染物。具体清洗步骤如下:
1)首先将100ml的氢氟酸与2000ml的水混合配制成氢氟酸溶液,同时将硅片支架清洗、吹干待用,然后将硅片放置于支架上。
2)配制3#液:将660ml的硫酸与220ml的双氧水按3:1混合(先加双氧水后加硫酸)获得3#液,同时用一容器对纯水进行加热。
3)将盛有硅片的支架放置于3#液中进行煮洗,加热温度为250℃,时间为15分钟,煮洗完后将其取出,然后放置于60~80℃的热水中进行冲洗5分钟。
4)配制1#液,将1l的去离子水,200ml的氨水和200ml的双氧水依次加入烧杯中获得1#液,将1#液加热至75℃后将硅片放入1#液中水浴10分钟。
5)配制2#液,将240ml盐酸,240ml双氧水加入1200ml温度为60~80℃热水中获得2#液,将硅片放入2#液中水浴15分钟,然后取出放入60~80℃的热水中冲洗5分钟。
6)将硅片置于10%氢氟酸溶液中3分钟以去除表面氧化层,最后再用去离子水冲洗20分钟。
b、在硅基底上表面自组装微纳米球阵列结构
sb1:将质量分数为5%、直径为530nm的聚苯乙烯微纳米球分散液与叔丁醇按体积比为1:1混合,将混合液放置水中超声5分钟,然后采用50μl微注射器将40μl的微纳米球分散液以45度倾斜角10μl/min的速度缓慢注入到置有经过步骤a处理过的硅片的水槽中(其中硅片应完全被水浸没),使微纳米球单层紧密排列在水溶液表面,待微纳米球铺满整个水面后打开水槽底部小孔开始缓慢放水,使水表面微纳米球沉积在硅片表面,随后放置于通风橱中使其自然风干。
c、制备硅基网络结构中的材料层
sc1:取0.546ml浓度为75wt%二(乙酰丙酮基)钛酸二异丙酯异丙醇溶液与5ml乙醇混合获得浓度为0.15mol/l的tio2前驱体溶液,随后采用匀胶机将前驱体溶液旋涂在自组装了微纳米球阵列的所述硅基底表面,匀胶机旋涂参数为5000rpm、时间30s,使溶液均匀分散在表面并自然风干。
sc2:将上述硅片放入马弗炉中退火,退火温度为500℃,时间30min,硅基底上表面形成材料层,形状为阵列分布的半球状穿孔形成微纳米碗阵列结构,孔径直径为530nm。
d、制备硅基网络结构中阵列分布的球状孔洞
sd1:将硅基底表面形成了阵列分布的半球状穿孔材料层置于si500电感耦合等离子刻蚀系统进行刻蚀,刻蚀参数为:icp电极功率200w,rf功率15w,sf6流量20sccm,刻蚀时间20s,刻蚀深度为200nm,此时在硅基底上表面形成阵列分布的球状孔洞,孔洞上表面圆形直径为480nm,深度为200nm,其中半球状穿孔正好位于该球状孔洞上方并且连通所述球状孔洞,而共同组成多个阵列分布的葫芦状孔洞,如图2所示。
e、制备硅基网络结构的包覆层
se1:将硅片表面具有阵列分布的葫芦状孔洞的硅片,采用explorer-14磁控溅射镀膜系统沉积金属层,溅射功率为200w,沉积厚度为20nm,此时硅片截面示意图如图3所示,金属层为au层时点样区微观结构如图4所示,其中这个au层也可以是ag、cu、al、ti、ni、pt。
本实施例成功制备了500纳米左右的二氧化钛与硅复合葫芦状孔洞纳米阵列结构,阵列单元呈六方密排,通过进一步在表面沉积20纳米厚金获得如图4所示au/tio2/si复合葫芦状纳米阵列结构,由于表面au纳米颗粒的表面等离激元共振效应,能够增强二氧化钛对光的吸收,提高电子态密度,从而进一步增强表面二氧化钛的光催化效应,其在在物理、化学、能源及生命科学等领域具有潜在应用。
实施例2:
a、硅基底的制备
sa1:选取电阻率为0.1ω·cm,厚度为500μm的4英寸n型双面抛光的硅片。
sa2:对硅片进行rca标准清洗以去除表面各种杂质和污染物,清洗步骤如下:
1)首先将100ml的氢氟酸与2000ml的水混合配制成氢氟酸溶液,同时将硅片支架清洗、吹干待用,然后将硅片放置于支架上。
2)配制3#液,将660ml的硫酸与220ml的双氧水按3:1混合(先加双氧水后加硫酸)获得3#液,同时用一容器对纯水进行加热。
3)将盛有硅片的支架放置于3#液中进行煮洗,加热温度为250℃,时间为15分钟,煮洗完后将其取出,然后放置于60~80℃的热水中进行冲洗5分钟。
4)配制1#液,将1l的去离子水,200ml的氨水和200ml的双氧水依次加入烧杯中获得1#液,将1#液加热至75℃后将硅片放入1#液中水浴10分钟。
5)配制2#液,将240ml盐酸,240ml双氧水加入1200ml热水中获得2#液,将硅片放入2#液中水浴15分钟,然后取出放入60~80℃的热水中冲洗5分钟。
6)将硅片置于10%氢氟酸溶液中3分钟以去除表面氧化层,最后再用去离子水冲洗20分钟。
b、在硅基底上表面自组装微纳米球阵列结构
sb1:将质量分数为5%、直径为1000nm的二氧化硅微纳米球分散液与叔丁醇按体积比为1:1混合,将混合液放置水中超声5分钟,然后采用50μl微注射器将40μl的微纳米球分散液以45度倾斜角10μl/min的速度缓慢注入到置有硅片的水槽中(其中硅片应完全被水浸没),使微纳米球单层紧密排列在水溶液表面,待微纳米球铺满整个水面后打开水槽底部小孔开始缓慢放水,使水表面微纳米球沉积在硅片表面,随后放置于通风橱中使其自然风干。
c、制备硅基网络结构中的材料层
sc1:将zn(oac)2·2h2o(>98%)和聚环氧乙烷(peo)(mw=1500)溶解于去离子水中获得0.01mol/l的zn(oac)2前驱体溶液,随后采用匀胶机将前驱体溶液旋涂在自组装了微纳米球阵列的所述硅基底表面,匀胶机旋涂参数为5000rpm、时间30s,使溶液均匀分散在表面并自然风干。
sc2:将上述硅片放入马弗炉中退火,退火温度为450℃,时间60min,硅基底上表面形成氧化锌材料层,形状为阵列分布的半球状穿孔形成微纳米碗阵列结构,孔径直径为1000nm。
d、制备硅基网络结构中阵列分布的球状孔洞
sd1:将硅基底表面形成了阵列分布的半球状穿孔材料层置于si500电感耦合等离子刻蚀系统进行刻蚀,刻蚀参数为:icp电极功率200w,rf功率15w,sf6流量30sccm,刻蚀时间25s,刻蚀深度为450nm,此时在硅基底上表面形成阵列分布的球状孔洞,孔洞上表面圆形直径为800nm,深度为450nm,其中半球状穿孔正好位于该球状孔洞上方并且连通所述球状孔洞,而共同组成多个阵列分布的葫芦状孔洞。
e、制备硅基网络结构的包裹层
se1:将硅片表面具有阵列分布的葫芦状孔洞的硅片采用磁控溅射镀膜系统沉积金属氧化层,沉积厚度为50nm的tio2层,其中tio2金属氧化物层也可以是al2o3、tio2、zro2。
本实施例成功制备了1000纳米左右的氧化锌与硅复合葫芦状孔洞微纳米阵列结构,阵列单元呈六方密排,通过进一步在表面沉积50纳米tio2层获得复合葫芦状微纳米阵列结构。
实施例3:
a、硅基底的制备
sa1:选取电阻率为0.1ω·cm,厚度为500μm的4英寸n型双面抛光的硅片。
sa2.对硅片进行rca标准清洗以去除表面各种杂质和污染物,清洗步骤如下:
1)首先将100ml的氢氟酸与2000ml的水混合配制成氢氟酸溶液,同时将硅片支架清洗、吹干待用,然后将硅片放置于支架上。
2)配制3#液,将660ml的硫酸与220ml的双氧水按3:1混合(先加双氧水后加硫酸)获得3#液,同时用一容器对纯水进行加热。
3)将盛有硅片的支架放置于3#液中进行煮洗,加热温度为250℃,时间为15分钟,煮洗完后将其取出,然后放置于60~80℃热水中进行冲洗5分钟。
4)配制1#液,将1l的去离子水,200ml的氨水和200ml的双氧水依次加入烧杯中获得1#液,将1#液加热至75℃后将硅片放入1#液中水浴10分钟。
5)配制2#液,将240ml盐酸,240ml双氧水加入1200ml热水中获得2#液,将硅片放入2#液中水浴15分钟,然后取出放入60~80℃热水中冲洗5分钟。
6)将硅片置于10%氢氟酸溶液中3分钟以去除表面氧化层,最后再用去离子水冲洗20分钟。
b、在硅基底上表面自组装微纳米球阵列结构
sb1:首先将清洗后的硅基底置于q150微波等离子去胶机在n2气氛下进行活化1分钟,随后将质量分数为40%、直径为10μm的二氧化硅微纳米球分散液利用匀胶机将2ml的二氧化硅微纳米球分散液旋涂在硅基底表面,匀胶机参数为先在500rpm下运转5s,随后在2500rpm下运转30s,使二氧化硅微纳米球单层紧密排列于硅基底表面。
c、制备硅基网络结构中的材料层
sc1:将6.09克分析纯mgcl2·6h2o置于50毫升容积的烧杯中,加入去离子水溶解,随后在加入7.2克分析纯co(nh2)2,搅拌后用分析纯hcl调节溶液ph值在3-9之间,形成氧化镁前驱体溶液,随后采用匀胶机将前驱体溶液旋涂在自组装了微纳米球阵列的所述硅基底表面,匀胶机旋涂参数为5000rpm、时间30s,使溶液均匀分散在表面并自然风干。
sc2:将上述硅片放入马弗炉中退火,退火温度为700℃,时间30min,硅基底上表面形成氧化镁材料层,形状为阵列分布的半球状穿孔形成微纳米碗阵列结构,孔径直径为10μm。
d、制备硅基网络结构中阵列分布的球状孔洞
sd1:将硅基底表面形成了阵列分布的半球状穿孔材料层置于si500电感耦合等离子刻蚀系统进行刻蚀,刻蚀参数为:icp电极功率200w,rf功率15w,sf6流量20sccm,刻蚀时间500s,刻蚀深度为5μm,此时在硅基底上表面形成阵列分布的球状孔洞,孔洞上表面圆形直径为8μm,深度为5μm,其中半球状穿孔正好位于该球状孔洞上方并且连通所述球状孔洞,而共同组成多个阵列分布的葫芦状孔洞。
e、制备硅基网络结构的包覆层
se1:将硅片表面具有阵列分布的葫芦状孔洞的硅片采用磁控溅射镀膜系统沉积金属氮化物层,沉积厚度为150nm,其中这个金属氮化物层也可以aln、gan。
本实施例成功制备了10微米左右的氧化镁与硅复合葫芦状孔洞微纳米阵列结构,阵列单元呈六方密排,通过进一步在表面沉积150纳米金属氮化物层获得复合葫芦状微纳米阵列结构。
实施例4:
a、硅基底的制备
sa1:选取电阻率为0.001-0.009ω·cm,厚度为800μm的4英寸n型双面抛光的硅片。
sa2.对硅片进行rca标准清洗以去除表面各种杂质和污染物,清洗步骤如下:
1)首先将100ml的氢氟酸与2000ml的水混合配制成氢氟酸溶液,同时将硅片支架清洗、吹干待用,然后将硅片放置于支架上。
2)配制3#液,将660ml的硫酸与220ml的双氧水按3:1混合(先加双氧水后加硫酸)获得3#液,同时用一容器对纯水进行加热。
3)将盛有硅片的支架放置于3#液中进行煮洗,加热温度为250℃,时间为15分钟,煮洗完后将其取出,然后放置于60~80℃的热水中进行冲洗5分钟。
4)配制1#液,将1l的去离子水,200ml的氨水和200ml的双氧水依次加入烧杯中获得1#液,将1#液加热至75℃后将硅片放入1#液中水浴10分钟。
5)配制2#液,将240ml盐酸,240ml双氧水加入1200ml热水中获得2#液,将硅片放入2#液中水浴15分钟,然后取出放入60~80℃的热水中冲洗5分钟。
6)将硅片置于10%氢氟酸溶液中3分钟以去除表面氧化层,最后再用去离子水冲洗20分钟。
b、在硅基底上表面自组装微纳米球阵列结构
sb1:将质量分数为5%、直径为360nm的聚苯乙烯微纳米球分散液与叔丁醇按体积比为1:1混合,将混合液放置水中超声5分钟,然后采用50μl微注射器将40μl的微纳米球分散液以45度倾斜角10μl/min的速度缓慢注入到置有硅片的水槽中(其中硅片应完全被水浸没),使微纳米球单层紧密排列在水溶液表面,待微纳米球铺满整个水面后打开水槽底部小孔开始缓慢放水,使水表面微纳米球沉积在硅片表面,随后放置于通风橱中使其自然风干。
c、制备硅基网络结构中的材料层
sc1:取0.546ml浓度为75wt%二(乙酰丙酮基)钛酸二异丙酯异丙醇溶液与5ml乙醇混合获得浓度为0.15mol/l的tio2前驱体溶液,随后采用匀胶机将前驱体溶液旋涂在自组装了微纳米球阵列的所述硅基底表面,匀胶机旋涂参数为5000rpm、时间30s,使溶液均匀分散在表面并自然风干。
sc2:将上述硅片放入马弗炉中退火,退火温度为500℃,时间30min,硅基底上表面形成二氧化钛材料层,形状为阵列分布的半球状穿孔形成微纳米碗阵列结构,孔径上表面圆形直径为360nm。
d、制备硅基网络结构中阵列分布的球状孔洞
sd1:将硅基底表面形成了阵列分布的半球状穿孔材料层置于si500电感耦合等离子刻蚀系统进行刻蚀,刻蚀参数为:icp电极功率200w,rf功率15w,sf6流量20sccm,刻蚀时间10s,刻蚀深度为100nm,此时在硅基底上表面形成阵列分布的球状孔洞,孔洞上表面圆形直径为280nm,深度为100nm,其中半球状穿孔正好位于该球状孔洞上方并且连通所述球状孔洞,而共同组成多个阵列分布的葫芦状孔洞。
e、制备硅基网络结构的包覆层
se1:将硅片表面具有阵列分布的葫芦状孔洞的硅片,采用公知的方法进行使用聚酰胺酸溶液制备聚酰亚胺薄膜,即可以通过使聚酰胺酸溶液浇铸在硅片上进而在阵列结构硅基点阵表面沉积25nm聚酰亚胺高分子层。
本实施例成功制备了360纳米左右的二氧化钛与硅复合葫芦状孔洞微纳米阵列结构,阵列单元呈六方密排,通过进一步在表面沉积25纳米聚酰亚胺高分子层获得复合葫芦状微纳米阵列结构。
实施例5:
a、硅基底的制备
sa1:选取电阻率为0.001-0.009ω·cm,厚度为800μm的4英寸n型双面抛光的硅片。
sa2:对sa1中的硅片进行rca标准清洗以去除表面各种杂质和污染物。具体清洗步骤如下:
1)首先将100ml的氢氟酸与2000ml的水混合配制成氢氟酸溶液,同时将硅片支架清洗、吹干待用,然后将硅片放置于支架上。
2)配制3#液:将660ml的硫酸与220ml的双氧水按3:1混合(先加双氧水后加硫酸)获得3#液,同时用一容器对纯水进行加热。
3)将盛有硅片的支架放置于3#液中进行煮洗,加热温度为250℃,时间为15分钟,煮洗完后将其取出,然后放置于60~80℃的热水中进行冲洗5分钟。
4)配制1#液,将1l的去离子水,200ml的氨水和200ml的双氧水依次加入烧杯中获得1#液,将1#液加热至75℃后将硅片放入1#液中水浴10分钟。
5)配制2#液,将240ml盐酸,240ml双氧水加入1200ml热水中获得2#液,将硅片放入2#液中水浴15分钟,然后取出放入60~80℃的热水中冲洗5分钟。
6)将硅片置于10%氢氟酸溶液中3分钟以去除表面氧化层,最后再用去离子水冲洗20分钟。
b、在硅基底上表面自组装微纳米球阵列结构
sb1:将质量分数为5%、直径为100μm的聚苯乙烯微纳米球分散液与叔丁醇按体积比为1:1混合,将混合液放置水中超声5分钟,然后采用50μl微注射器将40μl的微纳米球分散液以45度倾斜角10μl/min的速度缓慢注入到置有经过步骤a处理过的硅片的水槽中(其中硅片应完全被水浸没),使微纳米球单层紧密排列在水溶液表面,待微纳米球铺满整个水面后打开水槽底部小孔开始缓慢放水,使水表面微纳米球沉积在硅片表面,随后放置于通风橱中使其自然风干。
c、制备硅基网络结构中的材料层
sc1:取0.546ml浓度为75wt%二(乙酰丙酮基)钛酸二异丙酯异丙醇溶液与5ml乙醇混合获得浓度为0.15mol/l的tio2前驱体溶液,随后采用匀胶机将前驱体溶液旋涂在自组装了微纳米球阵列的所述硅基底表面,匀胶机旋涂参数为5000rpm、时间30s,使溶液均匀分散在表面并自然风干。
sc2:将上述硅片放入马弗炉中退火,退火温度为500℃,时间30min,硅基底上表面形成材料层,形状为阵列分布的半球状穿孔形成微纳米碗阵列结构,孔径直径为100μm。
d、制备硅基网络结构中阵列分布的球状孔洞
sd1:将硅基底表面形成了阵列分布的半球状穿孔材料层置于si500电感耦合等离子刻蚀系统进行刻蚀,刻蚀参数为:icp电极功率200w,rf功率15w,sf6流量20sccm,刻蚀时间2500s,刻蚀深度为25μm,此时在硅基底上表面形成阵列分布的球状孔洞,孔洞上表面圆形直径为50μm,深度为25μm,其中半球状穿孔正好位于该球状孔洞上方并且连通所述球状孔洞,而共同组成多个阵列分布的葫芦状孔洞。
e、制备硅基网络结构的包覆层
se1:将硅片表面具有阵列分布的葫芦状孔洞的硅片,磁控溅射镀膜系统沉积金属层,溅射功率为200w,沉积厚度为500nm。
本实施例成功制备了100微米左右的二氧化钛与硅复合葫芦状孔洞微纳米阵列结构,阵列单元呈六方密排,通过进一步在表面沉积500纳米金属层获得复合葫芦状微纳米阵列结构。
实施例6:
a、硅基底的制备
sa1:选取电阻率为0.001-0.009ω·cm,厚度为800μm的4英寸n型双面抛光的硅片。
sa2:对sa1中的硅片进行rca标准清洗以去除表面各种杂质和污染物。具体清洗步骤如下:
1)首先将100ml的氢氟酸与2000ml的水混合配制成氢氟酸溶液,同时将硅片支架清洗、吹干待用,然后将硅片放置于支架上。
2)配制3#液:将660ml的硫酸与220ml的双氧水按3:1混合(先加双氧水后加硫酸)获得3#液,同时用一容器对纯水进行加热。
3)将盛有硅片的支架放置于3#液中进行煮洗,加热温度为250℃,时间为15分钟,煮洗完后将其取出,然后放置于60~80℃的热水中进行冲洗5分钟。
4)配制1#液,将1l的去离子水,200ml的氨水和200ml的双氧水依次加入烧杯中获得1#液,将1#液加热至75℃后将硅片放入1#液中水浴10分钟。
5)配制2#液,将240ml盐酸,240ml双氧水加入1200ml温度为60~80℃的热水中获得2#液,将硅片放入2#液中水浴15分钟,然后取出放入60~80℃的热水中冲洗5分钟。
6)将硅片置于10%氢氟酸溶液中3分钟以去除表面氧化层,最后再用去离子水冲洗20分钟。
b、在硅基底上表面自组装微纳米球阵列结构
sb1:将质量分数为5%、直径为100nm的聚苯乙烯微纳米球分散液与叔丁醇按体积比为1:1混合,将混合液放置水中超声5分钟,然后采用50μl微注射器将40μl的微纳米球分散液以45度倾斜角10μl/min的速度缓慢注入到置有经过步骤a处理过的硅片的水槽中(其中硅片应完全被水浸没),使微纳米球单层紧密排列在水溶液表面,待微纳米球铺满整个水面后打开水槽底部小孔开始缓慢放水,使水表面微纳米球沉积在硅片表面,随后放置于通风橱中使其自然风干。
c、制备硅基网络结构中的材料层
sc1:取0.546ml浓度为75wt%二(乙酰丙酮基)钛酸二异丙酯异丙醇溶液与5ml乙醇混合获得浓度为0.15mol/l的tio2前驱体溶液,随后采用匀胶机将前驱体溶液旋涂在自组装了微纳米球阵列的所述硅基底表面,匀胶机旋涂参数为5000rpm、时间30s,使溶液均匀分散在表面并自然风干。
sc2:将上述硅片放入马弗炉中退火,退火温度为500℃,时间30min,硅基底上表面形成材料层,形状为阵列分布的半球状穿孔形成微纳米碗阵列结构,孔径直径为100nm。
d、制备硅基网络结构中阵列分布的球状孔洞
sd1:将硅基底表面形成了阵列分布的半球状穿孔材料层置于si500电感耦合等离子刻蚀系统进行刻蚀,刻蚀参数为:icp电极功率200w,rf功率15w,sf6流量20sccm,刻蚀时间5s,刻蚀深度为50nm,此时在硅基底上表面形成阵列分布的球状孔洞,孔洞上表面圆形直径为80-100nm,深度为50nm,其中半球状穿孔正好位于该球状孔洞上方并且连通所述球状孔洞,而共同组成多个阵列分布的葫芦状孔洞,如图1所示。
e、制备硅基网络结构的包覆层
se1:将硅片表面具有阵列分布的葫芦状孔洞的硅片,采用explorer-14磁控溅射镀膜系统沉积金属层,溅射功率为200w,沉积厚度为5nm。
本实施例成功制备了100纳米左右的二氧化钛与硅复合葫芦状孔洞微纳米阵列结构,阵列单元呈六方密排,通过进一步在表面沉积5纳米厚金复合葫芦状微纳米阵列结构。
与现有技术相比,本发明的有益效果是:
本发明能够制备多种不同材料复合的不同尺寸的葫芦状孔洞微纳米阵列结构,其中,微纳米阵列结是由不同材料层叠加构成,且不同材料层分别具有球状孔洞与半球状穿孔而共同组成葫芦状孔洞。藉此,可复合两种以上材料的性质,同时可形成良好的微纳米光学腔,有效的增强光的吸收。本发明制备工艺简单,通过退火、等离子体刻蚀、磁控溅射等工艺制备得到葫芦状孔洞微纳米阵列结构。所述微纳米阵列结构能够有效地均匀分散分析物,同时还具有微纳米阵列结构独特的半导体光电性质,如高的光吸收率、表面等离激元效应等,在物理、化学、能源及生命科学等领域具有潜在应用,如催化领域。
此外,本发明采用溶液法在硅基底表面自组装微纳米球掩膜,其相比于传统的旋涂法及提拉法,操作更加简单,有效减少了纳米球的使用,同时工艺稳定,在硅基底表面可获得均一单层六方密排的微纳米球阵列结构。本发明以退火后形成的微纳米碗阵列结构直接作为掩膜进行等离子体刻蚀获得六方密排的微纳米槽阵列结构,工艺步骤简单连续。
上述实施例用于例示性说明本发明的原理及其功效,而非用于限制本发明。任何熟习此项技艺的人士均可在不违背本发明的精神及范畴下,对上述实施例进行修改。因此本发明的权利保护范围,应如权利要求所列。
本文用于企业家、创业者技术爱好者查询,结果仅供参考。