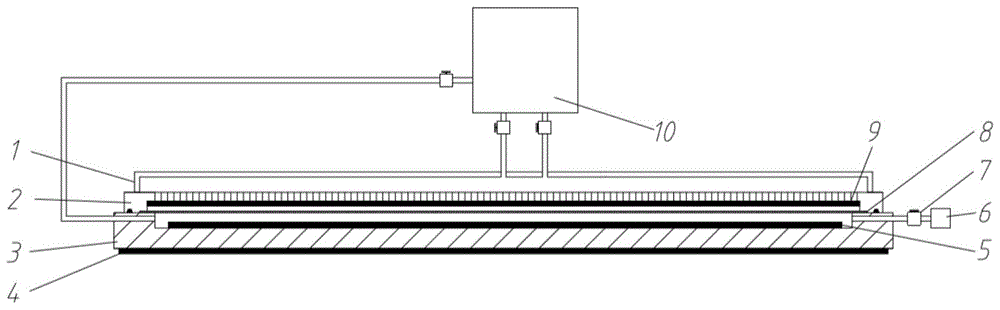
所属技术领域:
本发明公开了一种真空压力成型制备大面积、高深宽比的mems工艺制备方法及装置。属于微纳加工领域。
技术背景:
传统纳米压印技术主要有三种:热塑纳米压印技术、紫外固化压印技术和微接触纳米压印技术。纳米压印技术大都是不连续的生产工艺过程,难以进行大规模和大面积的生产。为了克服这些难题,滚轴式纳米压印得以出现。滚轴式纳米压印技术有连续压印、产量高、成本低和系统组成简单等特点。有两种实现工艺:一种是将掩模版直接制作到滚轴上,可以通过直接在金属滚轴上刻蚀或者利用弹性掩模套在滚轴上实现,滚轴的转动将图形连续地压入已旋涂好光刻胶(温度达到玻璃化温度以上)的基板上,滚轴的滚动实现了压入和脱模两个步骤。还可以是在弹性掩模版上利用滚轴滚动施压,但均匀性难以保证;另一工艺是将滚轴式压印技术和紫外压印技术相结合,紫外固化纳米压印技术光刻胶本身就是液态,紫外光固化可以将紫外光束很好地控制到滚轴和光刻胶分离的区域,采用的基板可以是弹性基板或者是如si样的硬基板。然而滚轴式纳米压印技术因其技术特点,设备整体置于真空环境中,不能使用气体表面活性剂,脱模效果受到限制,因此难以加工高深宽比的结构。
发明目的:
针对传统纳米压印所存在的大面积、高深宽比结构的加工难题,本发明提出了一种制备柔性微纳功能结构的方法,有效的解决了大面积和高深宽比的问题。本发明的目的在于提供一种真空压力成型制备大面积、高深宽比的柔性微纳功能结构的方法及装置。
技术方案:
一种真空压力成型制备大面积、高深宽比的柔性微纳功能结构的装置,主要包括由上壳体1和下壳体3构成的具有气密性的密闭腔室;所述腔室被待压印的薄膜8分成上下两个部分,薄膜上侧与上壳体1以及孔板2所围成的部分为上腔室12,薄膜下侧与下壳体3所围成的部分为下腔室11;所述下腔室11底部为模具层5,所述模具5上表面提供待压印图形的母版;所述上腔室12内有一与薄膜层8平行的孔板层2;所述上腔室12和下腔室11均与气流控制装置10连通,所述气流控制装置10可控的实现上、下腔室的真空度和压力差要求。所述下壳体底部有加热装置4,优选的,为加热薄膜。
可选的,在孔板层2的下表面贴敷一层海绵防护层9。
本发明的真空压力成型制备大面积、高深宽比的柔性微纳功能结构的方法,包括以下步骤:
步骤一:通过气流控制装置10同时对上下腔室抽真空,要求上腔室12空气流速大于下腔室11,控制过程中上腔室12压力不大于下腔室11,以免薄膜8在压差下发生形变,提前接触到模具5对薄膜8造成损伤。抽真空过程中,薄膜两侧压差不大于p1,防止压差过大对薄膜8造成损伤;抽真空过程结束后,上下腔室达到加工状态,上腔室12气压为0.1-0.3pa,下腔室11比上腔室12气压大,但是应当小于1pa。抽真空过程结束后接通下壳体3底部加热薄膜4的电源,对下壳体3进行加热,壳体外表面要求达到90℃,均匀度为±2℃,通过热传递的方式将热量传入壳体内部。
优选的,p1=100pa;
步骤二:通过气流控制装置10将加热后气化的表面活性剂6注入下腔室11,同时对上腔室12进行加压,使薄膜8两侧压差不大于p1,待气化的表面活性剂充满下腔室11时,关闭气压阀7,同时停止对上腔室12进行加压。在静置一段时间待表面活性剂布满模具5上表面;
步骤三:再次对上下腔室抽真空,抽真空过程中控制上腔室12空气流速大于下腔室11,并使抽真空过程中薄膜8两侧压差不大于p1;抽真空过程结束后,上腔室12气压为0.1-0.3pa,下腔室11比大,但同时保证气压低于1pa。
步骤三:再次对上下腔室抽真空,要求上腔室12空气流速大于下腔室11,控制过程中上腔室12压力不大于下腔室11。抽真空过程中,薄膜8两侧压差不大于p1,防止压差过大对薄膜8造成损伤;抽真空过程结束后,上下腔室达到加工状态,上腔室12气压为0.1-0.3pa,下腔室11比上腔室12气压大,但是应当小于1pa。
步骤四:通过气流控制装置10对上腔室12进行加压,使气体均匀通过孔板层2,压力p2均布薄膜8上表面,压力p2使薄膜8面积的80%以上在压力的作用下与模具接触。此时,壳体及薄膜8已经达到薄膜8材料玻璃化温度,在压力的作用下,薄膜8发生塑性变形,随后停止加热,待装置温度下降至室温后,停止对上腔室12进行加压,以此将上腔室12和下腔室11恢复至一个大气压。
优选的,所述p2设置为十个大气压;
步骤五:将所述上壳体1打开,获得压印过后的图形化薄膜。
有益效果:
本装置创新点在于(权利保护):
(1)与传统纳米压印技术将装置整体置于真空环境中进行制备相比,本装置简化了真空设备,缩小了真空环境所需要的体积,使得工作环境更容易保持,缩短了工艺前的准备时间,几秒内即可形成真空环境。
(2)传统纳米压印采用机械加压的方式,因受力的问题会导致产品的结构不均匀,本装置采用气压的方式,使薄膜受力均匀,提高了产品的质量。
(3)因为装置采用了(1)中所提到的简化真空装置,工艺过程中可以采用气态的表面活性剂对模具进行处理,处理完可以快速恢复真空环境,因此可以选用脱模效果更好的表面活性剂,如氟硅烷,对模具进行处理。解决了制备高深宽比结构的难题。
本发明借鉴了塑料制品常用的真空注塑,采用一种特别的压力成型方法对薄膜进行加工。为了保证加工质量,需要对腔室进行严格的预处理。首先要将整个工作空间抽至真空,这一操作避免了模具中的微量空气难以压缩导致成品结构高度参差不齐;此外,要使表面活性剂布满整个模具表面,尽量避免脱模时造成结构被拔断的情况。通过改变装置的大小,可以加工不同面积的薄膜,可实现大面积薄膜的加工;并且在真空的环境下进行加工,有效解决了模具微结构中空气体积不可忽略的问题。本发明通过将真空注塑与脱模的技术结合起来,实现了制备大面积、高深宽比的柔性微纳功能结构的目的。
包括上壳体1、下壳体3、孔板2、薄膜8、密封条、气流控制装置10,表面活性剂10等组成。上壳体1扣下后,将用于加工的薄膜8夹在上下模具之间,通过薄膜8,使上壳体1与下壳体3中的腔室分为上下两个部分。通过上下腔室的不同步真空来实现柔性微纳功能结构的制备。依次对上、下腔室抽真空,随后将表面活性剂气体注入下腔室,静置待活性剂均布模具5表面后,再次对下腔室11抽真空,随后对上腔室11进行加压,并对下壳体3进行加热,待薄膜8充分塑形后,将上壳体1打开,通过辊子缓慢、均匀地将薄膜卷起。通过抽真空的方式,避免了模具5内残留空气对微结构成型时所带来的巨大影响,提高了产品的质量,同时也提高了产品的成品率。
附图说明:
图1是实施例中真空压力成型制备大面积、高深宽比的柔性微纳功能结构的装置示意图
图2是图1的局部放大图。
图3是实施例中孔板示意图;
图4是实施例中工作装置内压力变化示意图。
具体实施例:
参阅图1-图3;本实施例中的装置主要由以下几部分组成:
孔板:孔板材料采用铝板,截面为正方形,最外轮廓为84cm,工作截面为60cm,为了使压力均匀,工作截面上均布φ6的小孔,使气压均匀分布在薄膜8上,保证加工的质量。孔板2下方为一正方形凹槽,凹槽内需要粘贴一张防护海绵网9,避免薄膜8被过度拉伸以及过分接触上方圆孔导致薄膜损坏。
上壳体:上壳体材料采用铝板,截面为正方形,最外轮廓为68cm,工作截面边长为60cm,部件下端有一宽度为10mm、深度为5mm的密封槽。为维持装置的气密性,通过周围的孔与孔板进行紧固连接。壳体的上方加工出两个通气的小孔,通气孔与气流控制装置10相连。加工界面棱角处需倒角。
下壳体:下壳体材料采用铝板,截面为正方形,最外轮廓为84cm,工作界面边长为60cm。螺纹长度为2cm,因操作过程中上下壳体需要频繁打开和关闭,采用合页与上壳体连接,下壳体的最大厚度为2cm,壳体的一个侧面加工六个螺纹孔,孔径为φ10,距离工作界面4cm的位置加工出一宽10mm,深5mm的密封槽,将橡胶密封条埋在沟槽中。为保持腔室密封性良好,在下壳体3的边缘加工五个竖直通孔,孔径为φ20,与上壳体1通过螺栓来进行紧固。下壳体3的侧面还有一连接至腔室内部的通孔,与气流控制装置10连接。加工界面棱角处需倒角。
气流控制装置10:控制气流的进出与速度,保证装置内的压力变化不超出安全范围,本实施例中的气流控制装置10包括与腔室相通的气压阀7、具备加热控制的表面活性剂6存储腔及其他部分;
防护海绵网:海绵网上同样均布小孔,为使空气通顺流动,孔的大小和位置与孔板2相同。厚度为2mm。面积为60cmx60cm。
加热薄膜:聚酰亚胺加热薄膜,通电后可以均匀发热,规格为24v,50w。将其贴在下壳体3的底部,对装置进行均匀加热。面积为70cmx70cm。
下壳体3与孔板2上需要加装密封条来保持气密性。孔板2与上壳体1通过螺栓进行连接,要求紧固良好,使密封条紧密贴合,螺母采取防松措施,防止在反复使用中螺母松动,出现气体泄漏的现象。
将金属电铸的微结构模具5固定于下壳体3内部的中心,为保证加工质量,注意粘贴时模具下方不能留有气泡,翘起的边角要固定牢固。孔板的下方要粘贴一层海绵防护网9,防止薄膜8两侧压力变化不均匀导致薄膜8破裂。
使用本实施例中装置进行真空压力成型制备大面积、高深宽比的柔性微纳功能结构的方法,先进行如下准备工作的调试:
进行加工前对气压阀7进行调节,使上腔室12的气压减小略快于下腔室11,压差不超过100pa,这么做的目的是为了防止pet薄膜8在结构成型步骤之前接触模具5,对薄膜8造成一部分损伤,影响后续的成型步骤,导致结构成型不完全。同时,需要将所有部件组装好进行气密性检测,避免加工时出现问题。
同时,将金属电铸的微结构模具5固定于下壳体3内部的中心,将海绵防护层9固定于孔板2下方,用于加工的pet薄膜8固定在下壳体3上方,覆盖整个工作截面。用于对装置加热的加热薄膜4粘贴于下壳体3的底部中心位置。
上壳体1与下壳体3通过螺栓进行紧固后,两壳体之间形成一个密封腔体,pet薄膜8被夹在上下壳体中间,并将封闭腔体分为上下两个部分,薄膜8上侧与上壳体1所围的部分为上腔室12,薄膜8下侧与下壳体3所围的部分为下腔室11。
调试完成后,具体的加工步骤如下:
步骤一:同时对上下腔室抽真空,控制上腔室12空气流速略大于下腔室11,使过程中上腔室12压力略小于下腔室11,以免pet薄膜8提前接触到模具5对薄膜8造成损伤,最终上腔室12的气压为0.2pa,下腔室11的气压为0.7pa。抽真空过程中薄膜8两侧压差不大于100pa。,防止压差过大对薄膜8造成损伤。抽真空结束后接通下壳体3底部的加热薄膜4的电源,对下壳体3进行加热,壳体外表面加热至90℃,均匀度为±2℃,通过热传递的方式将热量传入壳体内部。
步骤二:对液体表面活性剂10(78560-45-9)进行加热使其气化,将表面活性剂气体注入下腔室11,同时将对上腔室12进行加压,使薄膜8两侧压差不超过100pa,在静置一段时间后,待表面活性剂布满模具5表面;
步骤三:再次对上下腔室抽真空,注意薄膜8两侧压差。仍要使薄膜8两侧压力差不超过100pa,最终上腔室12的气压为0.2pa,下腔室11的气压为0.7pa。
步骤四:采用气流控制装置10对上腔室12进行加压,通过孔板2使气压均布薄膜8上表面,压力为十个大气压,使pet薄膜8发生塑性变形,十五分钟后停止加热,待装置温度下降至室温后,停止加压,依次将上腔室12、下腔室11与大气连通,将压力恢复至一个大气压。
步骤五:将封闭腔室打开,用一缓慢均匀滚动的辊子将pet薄膜卷起,至此,制备过程结束。
工作装置内压力变化如图4所示,p_0为标准大气压,实线为上腔室12压力,虚线为下腔室11压力。a点处为初始状态,上下腔室压力均为一个标准大气压;步骤一开始对上下腔室抽真空,过程中控制上腔室12压力不大于下腔室11,步骤一结束后上下腔室达到加工状态b点;步骤二通过气流控制装置10将气化的表面活性剂注入下腔室,同时对上腔室12进行加压,待表面活性剂充满下腔室11,停止对上腔室12加压,此时上下腔室压力变化到达c点处;步骤三再次对上下腔室抽真空,过程中上腔室12压力依然不大于下腔室11,步骤结束后达到加工状态d点;步骤四通过气流控制装置10对上腔室12进行加压,优选的,压力为十个标准大气压,上腔室12压力变化到达e点,下腔室11始终保持真空状态。
本文用于企业家、创业者技术爱好者查询,结果仅供参考。