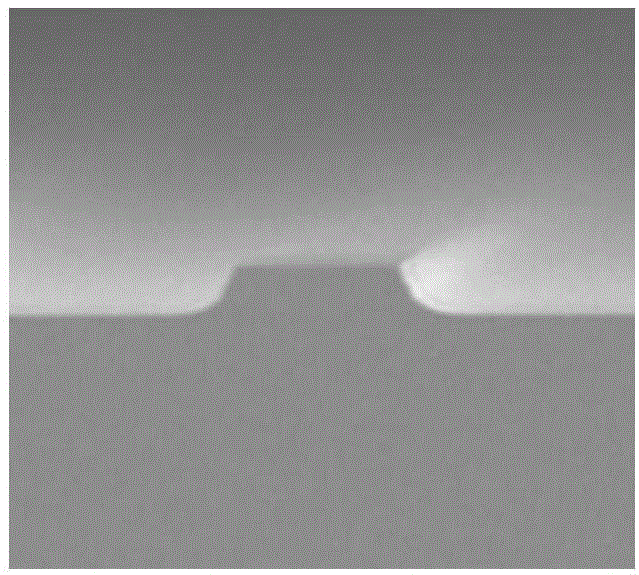
本发明属于材料科学技术领域,具体涉及一种基于图案化表面的皮升数量级的注射器及其制备方法。
背景技术:
超微量液体体积的精确操控在临床诊断、药物分析、细胞培养和单细胞直接注射药物等领域具有广泛的应用(richardpariza,chem.rev.2006,106,2990-3001;samuelk.sia,labchip,2012,12,2118–2134),然而为了实现这种超微量注射技术的实际应用和商品化,还有很多问题亟待解决。皮升数量级的液体应该被限定在小微米范围的空间内,人们相继提出了阵列微井基底、微针尖挤出直接获取和微流体等方法来实现皮升数量级液滴的获取,其中,阵列微井基底无法控制液体的挥发,微针尖挤出获取的方法成本比较高昂,微流体由于其成本低廉、样品量较低、可控的样品挥发等特点被广泛应用。
目前多种获取定量超微体积液体的微流体器件已经相继被报道,比如数字微流体和液体微流体,但是这类微流体器件难以实现精准的超微量液体的操控,并且数字微流体的成本比较高昂,制备工艺相对复杂,这与微流体简单、低廉、高效的特性相违背。微流体中被动阀门是基于孔道表面的laplace压力实现对微孔道中的流体进行操控,被动阀门功能的实现不需要复杂的外部控制器件,并且对微孔道中流体的操控相对准确,为超微量液体的获取提供了新思路。然而目前的微流体被动阀门器件多难以连续地获取皮升及其以下数量级的液体,原因是多数微流体器件的孔道是由软质材料构成,当孔道尺寸降到小微米数量级(10μm),孔道就会变形进而发生塌陷堵塞流体,于是探索一种简单的微流体超微量注射器的制备方法实现对皮升数量级的液体的连续获取和操控是研究人员亟待解决的问题。
技术实现要素:
为了解决现有技术中存在的上述缺点,本发明的目的是提供一种简单、低廉的基于图案化表面的皮升量级的玻璃—硅超微量注射器及其制备方法。本发明的制备方法涉及光刻技术与等离子刻蚀方法结合制备硅片表面的微米图案化结构阵列,通过气相沉积技术对图案化结构表面进行修饰进而与带有梯形孔道的玻璃表面键和制备微流体超微量注射器。整个过程操作简单,成本低廉,不涉及昂贵的制备技术,并且所制备的微流体超微量注射器具有很好的稳定性。硅基底上每个疏水的图案化微条带结构可在玻璃微通道中形成一个被动阀门,这种被动阀门的阈值压力(即所能阻挡的最大流体压力)与其在微孔道中的长度(与孔道垂直方向)成负相关,通过计算对这种微条带阵列进行排列,可以在梯形微孔道中形成阈值压力不同并且任意两阀门间体积相等的微阀门阵列。通过控制流体的压力我们可以控制流体前端在微阀门中的位置,即梯形微孔道中液体的填充量,利用气体切断梯形微孔道端点处的流体,从而实现定量的皮升数量级液体的获取和操控。本发明对液体体积的操控主要是通过对条带结构表面气液固三相线的调控来实现的,重要的是芯片是由玻璃或硅构成的,不存在因孔道变形而导致的液体体积误差。此外,玻璃或硅材质芯片不会因小微米尺寸(10μm)的孔道发生坍塌而导致无法获取皮升量级的液体。本发明超微量注射器对液体体积的获取具有很好的重复性和准确性,整个过程不需要外部复杂的电路元件和辅助设备,有效的降低了芯片的制备和运行成本。
本发明通过如下技术方案实现:
基于图案化表面的皮升量级的超微量注射器的制备方法,具体步骤如下:
(1)、微流体超微量注射器下表面基片的处理:将基片置于丙酮中超声清洗三遍,每次1~2min,再用无水乙醇清洗三遍,每次1~2min,之后用去离子水超声清洗至无有机溶剂残留;随后对基片进行酸性氧化处理(质量分数为98%浓硫酸和质量分数为30%过氧化氢的混合溶液,两者体积比为7:3),之后用去离子水清洗至无酸液,存放于去离子水中待用;
(2)、将步骤(1)所得的基片置于氧等离子体清洗机中清洗5~10min,使其表面接枝上羟基,再在基片表面旋涂一层光刻胶(旋涂条件为1000~3000rpm,10~60s,胶膜厚度为2~4μm);随后将基片置于图案化微结构阵列掩模板下紫外曝光10~30s,再将基片置于显影液中浸泡10~30s,得到图案化的光刻胶表面;
(3)、将步骤(2)所得的图案化光刻胶表面置于等离子刻蚀机腔体中,刻蚀时间为2~20min;之后将基片置于无水乙醇中超声清洗5~10min,再用去离子水超声清洗5~10min;随后将基片置于氧等离子体清洗机中清洗5~10min,使其表面接枝为羟基,再通过气相沉积法使基片表面接枝上疏水的材料,便在基片表面上得到疏水的形貌图案化结构阵列;
(4)、将带有均匀铬膜和光刻胶层的玻璃板置于微孔道掩膜版下紫外灯曝光10~30s,所述光刻胶层在上层(胶膜厚度为1~2μm),铬膜在下层(胶膜厚度为50~200nm),再将玻璃板置于显影液中浸泡10~30s,得到图案化光刻胶的旋有铬层的玻璃表面;之后置于铬刻蚀液中浸泡2~5min除去表面铬层,得到带有图案化的铬层的玻璃表面;将上述表面置于玻璃刻蚀液(质量比hf:hno3:nh4f:h2o=25:23.5:9.35:450)中浸泡20~120min即得到玻璃微孔道轮廓;之后利用金刚石打孔机对玻璃微孔道出入口进行打孔即得到成型的玻璃微孔道,将所得到的玻璃微流体孔道与步骤(3)中制备的图案化结构阵列表面清洗后压在一起进行键和1~3天便得到了基于图案化表面的玻璃-硅皮升量级的超微量注射器。
步骤(1)中使用的基片为玻璃载玻片、石英片或单晶硅片。
步骤(2)中使用的光刻胶为正性光刻胶bp212-37s、bp212-45或负性光刻胶su-8。
步骤(2)中使用的紫外灯波长是365nm,功率为30~100w。
步骤(2)中使用的显影液为质量分数0.5~2%的氢氧化钠溶液或光刻胶专用显影液。
步骤(2)中的图案化微结构阵列掩模版为铬层图案化和菲林打印的微米级条带阵列,其中,掩膜版条带阵列的数量和相对位置是根据需要所计算设计得出的。
步骤(3)中刻蚀气压为0~20mtorr,刻蚀温度10~20℃,刻蚀基底气体流速10~50sccm,刻蚀功率为rf为0~400w,icp为0~400w,刻蚀气体为氧气、三氟甲烷/六氟化硫、三氟甲烷/氩气等单独气体或多组分混合气体。
步骤(3)中疏水的接枝材料为1h,1h,2h,2h-过氟辛基三氯硅烷(pfs)或三氯十八硅烷(ots)。
步骤(4)中使用的玻璃板是旋涂有金属层和光刻胶牺牲层的玻璃片,所述光刻胶牺牲层在上,金属层在下。
步骤(4)中使用的铬刻蚀液为硝酸铈铵和硝酸按体积比为6%的混合溶液。
步骤(4)中使用的微孔道掩膜版为由梯形、长方形等多边形相连形状组成的微芯片孔道模型,各形状的大小和相对位置是根据所获取液体体积大小和连续状态所精确计算设计的。
与现有技术相比,本发明的优点如下:
1、本发明制备过程简单,通过图案化表面形成多个连续的被动微阀门,进而组成微流体超微量注射器,整个过程不需要复杂的制备技术,较大程度的简化了芯片的加工难度。
2、本发明可连续的获取皮升数量级的液体,我们可以根据需要来设计所需获取液体体积的大小和连续范围,最小可连续获取体积为6pl,此时孔道尺寸在10-20μm之间,利用pdms等软质材料做芯片材料在此尺寸维度会由于孔道尺寸过小而坍塌,从而造成孔道堵塞,导致获取失败。
3、本发明设有液体体积反馈孔道,并且芯片材质是由硬质玻璃或硅材料制成,芯片孔道不会塌陷造成液体体积误差,液体获取的准确率高达98%以上。
4、本发明的所制备的微流体超微量注射器可以获取多表面能和多种类的定量的超微量体积液体,其中包含低表面能的醇水混合液、血液、油相液体等。
5、本发明所获取的超微量液体可用于实际的应用,在本发明的案例中,结合多个超微量注射器,可以混合定量的超微量液体。
本发明制备过程操作简单,低廉的器件就可以实现皮升数量级液体连续精确的获取,我们可以根据需要调整超微量注射器的量程和分度值,玻璃或硅材质芯片不会因小微米孔道坍塌而导致获取误差和失败,运行过程中不要昂贵的能量输入,可集成与于大多数实验平台,并且器件具有良好的稳定性。
附图说明
图1:基于实施例3所制备的图案化硅条带结构的扫描电子显微镜照片;
图2:基于实施例4所制备的皮升超微量注射器的截取不同体积液体的电子显微镜照片,此注射器量程为500.0pl,分度值为50.0pl,每个格子腔体内的空间体积是相同的,通过调节流体的入口压力来控制流体前端在注射器中停留的位置;(a)当孔道内流体内部压力为127.0mbar时,流体前端停留在第一个条带处,即流体填充满第一个格子;(b)当孔道内流体内部压力为134.0mbar时,流体前端停留在第三个条带处,即流体填充满前三个格子;(c)当孔道内流体内部压力为140.0mbar时,流体前端停留在第五个条带处,即流体填充满前五个格子;(d)当孔道内流体内部压力为150.0mbar时,流体前端停留在第八个条带处,即流体填充满前八个格子;(e-h)利用气体截取在梯形微孔道中的流体,分别得到精准的定量的不同的皮升数量级的液体,气体的压力为200.0mbar,所得到的液体体积分别为48.50(e)、150.00(f)、251.52(g)和398.51(h)pl;从图中可以看出通过该超微量注射器得到不同体积的定量的皮升液体;
图3:基于实施例5所制备的不同分度值和量程的超微量注射器的显微镜照片;在不同孔道高度的超微量注射器中,应用不同压力可以使流体前端停在需要的条带位置,从而得到定量的液体体积;(a)量程为250.0pl、分度值为25.0pl的注射器,图中流体应用压力为172.0mbar,流体停留在第6个条带位置;(b)量程为1000.0pl、分度值为100.0pl的注射器,图中流体应用压力为93.0mbar,流体停留在第6个条带位置;c)量程为1500.0pl、分度值为150.0pl的注射器,图中流体应用压力为68.0mbar,流体停留在第6个条带位置;(d-f)利用气体截断不同长度的气柱,分别得到精准的不同量的皮升数量级的液体,气体压力均为200.0mbar,所得到的液体体积分别为150.09(d)、599.02(e)和897.18(f)pl;从图中可以看出通过改变微孔道的高度可以得到不同量程的超微量注射器;
图4:基于实施例6所制备的获取低表面能液体的超微量注射器的显微镜照片;六组图中的实验液体是不同的,以取300pl液体为目标获取值;(a,b)获取定量的5%乙醇-水混合液体,图中所得到的5%乙醇-水混合液体积为300.27pl;(c,d)获取定量的10%乙醇-水混合液,图中所得到的10%乙醇-水混合液体积为298.35pl;(e,f)获取定量的20%-乙醇水混合液体,图中所得到的20%乙醇-水混合液体积为301.25pl;(g,h)获取定量的皮升血液,图中所得到的血液体积为297.12pl;(i,j)获取定量的皮升菜籽油液体,图中所得到的菜籽油液体体积为301.34pl;(k,l)获取定量的5%胰岛素溶液,图中所得到的5%胰岛素溶液体积为301.52pl;从图中可以看出本发明可以获取多表面能和多种类定量皮升液体;
图5:通过在一个微芯片中集成两个本发明的超微量注射器所制备的超微量混合器模型图和利用其定量混合所检测的荧光显微镜照片;(a)基于实施例7所制备的精准定量的超微量混合器的模型图;(b-c)从左到右注射器1获取的蓝光激发的荧光液体体积分别是500.0、400.0、300.0、200.0、100.0、0.0pl,注射器2获取的绿光激发的荧光液体体积分别是0.0、100.0、2000.0、300.0、400.0、500.0pl,二者经过混合后流到检测区域;(b)两种荧光染料梯度定量混合的蓝检测以上混合液体的荧光显微镜照片;(c)两种荧光染料梯度定量混合的绿光检测以上混合液体的荧光显微镜照片;从图中可以看出通过在微芯片中集成两个超微量注射器,可以对皮升数量级液体进行定量混合;
图6:基于实例8所制备的pdms材质的超微量注射器获取皮升液体失败实施例,pdms微孔道发生坍塌,堵塞微孔道。
具体实施方式
下面结合实施例对本发明做进一步的阐述,而不是要以此对本发明进行限制。
实施例1:亲水基底的制备
所用基底为单晶硅片(100),将基底用玻璃刀裁至3cm长,2cm宽大小,依次置于丙酮、乙醇和去离子水超声三遍,每次1~2min,之后放入质量分数为98%浓硫酸和质量分数为30%过氧化氢的混合溶液(体积比为7:3)中水浴加热至120℃,保持5小时,即得到亲水基底;然后将混合酸溶液倒入废液瓶中,将得到的基底用去离子水反复超声洗涤5次,每次1~2min,保存在去离子水中待用。
实施例2:图案化光刻胶阵列结构基底的制备
将硅片置于氧等离子体清洗机中清洗5min,再在硅片表面旋涂一层光刻胶(旋涂条件为3000rpm,60s);随后将匀胶基片置于图案化微结构阵列掩模板下紫外曝光10-30s,紫外曝光14s,再将硅片置于专用显影液中浸泡30s,得到图案化的光刻胶表面,根据所需要获取液体体积的大小和量程,我们通过计算设计了响应的条带掩膜版,光刻掩版图案的不同我们得到多种具有不同图案并且与多种芯片微孔道分别匹配的图案化光刻胶表面;其中,图案化微结构阵列掩模板是铬层图案化和菲林打印的微米级条带阵列。
实施例3:疏水图案化硅结构阵列结构基底的制备
将实例2得到的图案化光刻胶阵列结构基底置于等离子刻蚀机腔体中,刻蚀时间为10min(刻蚀气压为6mtorr,刻蚀温度10℃,刻蚀功率为rf为50w,icp为100w);之后将基底置于无水乙醇中超声清洗10min,除去表面残留的光刻胶,再用去离子水超声清洗5min,用氮气吹干;将得到的基底置于氧等离子体清洗机中清洗5min使基底表面带有羟基,再通过气相沉积法使基片表面接枝上1h,1h,2h,2h-过氟辛基三氯硅烷,便得到疏水的图案化硅结构阵列,根据光刻胶图案的不同我们可以得到具有不同图案的可与多种形状微芯片孔道分别匹配的图案化硅结构阵列表面。
实施例4:皮升超微量注射器的制备
将带有均匀铬膜和光刻胶层的玻璃板置于微孔道掩膜版下紫外灯曝光12s,再将基片置于显影液中浸泡30s,得到图案化光刻胶的旋有铬层的玻璃表面;之后置于铬刻蚀液中浸泡5min,得到带有图案化的铬层的玻璃表面;将上述表面置于玻璃刻蚀液(质量比hf:hno3:nh4f:h2o=25:23.5:9.35:450)中浸泡25min即得到玻璃微孔道轮廓;之后利用金刚石打孔机对玻璃微孔道出入口进行打孔即得到成型的玻璃微孔道,将所得到的玻璃微流体孔道与实例(3)中制备的图案化结构阵列压在一起进行键和2天便得到了基于图案化表面的皮升量级的超微量注射器。
实施例5:不同分度值和量程皮升超微量注射器的制备
将带有均匀铬膜和光刻胶层的玻璃板置于微孔道掩膜版下紫外灯曝光12s,再将基片置于显影液中浸泡30s,得到图案化光刻胶的旋有铬层的玻璃表面;之后置于铬刻蚀液中浸泡5min,得到带有图案化的铬层的玻璃表面;将上述表面置于玻璃刻蚀液(质量比hf:hno3:nh4f:h2o=25:23.5:9.35:450)中浸泡15、45、75min即得到不通高度的玻璃微孔道轮廓;之后利用金刚石打孔机对玻璃微孔道出入口进行打孔即得到成型的玻璃微孔道,将所得到的玻璃微流体孔道与实例(3)中制备的图案化结构阵列压在一起进行键和2天便得到了基于图案化表面的不同分度值和量程皮升超微量注射器。
实施例6:低表面能超微量注射器的制备
将带有均匀铬膜和光刻胶层的玻璃板置于微孔道掩膜版下紫外灯曝光12s,再将基片置于显影液中浸泡30s,得到图案化光刻胶的旋有铬层的玻璃表面;之后置于铬刻蚀液中浸泡5min,得到带有图案化的铬层的玻璃表面;将上述表面置于玻璃刻蚀液(质量比hf:hno3:nh4f:h2o=25:23.5:9.35:450)中浸泡25min即得到玻璃微孔道轮廓;之后利用金刚石打孔机对玻璃微孔道出入口进行打孔即得到成型的玻璃微孔道,将所得到的玻璃微流体孔道与实例(3)中制备的图案化结构阵列压在一起进行键和3天便得到了基于图案化表面的低表面能超微量注射器。
实施例7:精准定量的超微量混合器的制备
将带有均匀铬膜和光刻胶层的玻璃板置于具有两个微孔道掩膜版下紫外灯曝光12s,再将基片置于显影液中浸泡30s,得到图案化光刻胶的旋有铬层的玻璃表面;之后置于铬刻蚀液中浸泡5min,得到带有图案化的铬层的玻璃表面;将上述表面置于玻璃刻蚀液(质量比hf:hno3:nh4f:h2o=25:23.5:9.35:450)中浸泡25min即得到玻璃微孔道轮廓;之后利用金刚石打孔机对玻璃微孔道出入口进行打孔即得到成型的玻璃微孔道,将所得到的玻璃微流体孔道与实例(3)中制备的图案化结构阵列压在一起进行键和2天便得到了基于图案化表面的精准定量的超微量混合器。
实施例8:pdms材质超微量注射器的制备
将聚二甲基硅氧烷(pdms)预聚体与固化剂按质量比10:1的比例混合均匀,真空脱气30min后,倾倒至微芯片孔道模板表面,置于温度为60℃的烘箱中,固化8h,将其揭起便得到了pdms微流体芯片;将所得到的pdms微孔道表面与实例3中制备的图案化硅结构微阵列表面压到一起便得到了pdms材质的微流体超微量注射器件。
本文用于企业家、创业者技术爱好者查询,结果仅供参考。