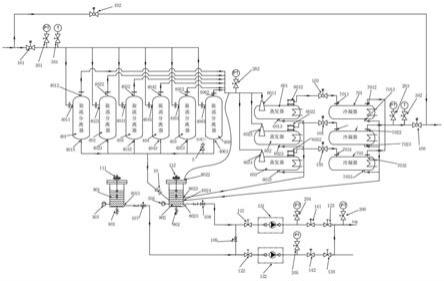
1.本发明涉及油田设备技术领域,具体是一种智能相变分离混烃机组。
背景技术:
2.油田伴生气是采油生产过程中从油藏中逸出的不稳定烃类和其它气体混合物,多作为采油井场和站点的加热炉的燃料。目前常规气液分离装置无法有效分离件生气中的混烃和水分。生产过程中伴生气析出凝析液经常堵塞加热炉供气管线,导致加热炉供气管路堵塞。冬季严寒季节,此问题更为突出。由此产生的加热炉熄火、爆燃等故障司空见惯,产生了严重安全环保隐患。同时,油田常规气液分离装置分离出来的凝析液无法自动回收,部分现场凝析液直接排至废液坑,或被当地村民强行收集,造成严重环境污染和社会治安综合治理漏洞,形成重大风险源点。近年部分采油厂自行研发“自流式凝析油装置",在一定程度上解决了凝析油回收问题,但该装置又将收集的凝析液重新注入井内,造成凝析油的循环往复,不能从根本上解决问题。
3.油田工作站虽然安装了油气分离器,但分离效果不佳,由于伴生气中水分和凝析液含量较高,严重影响加热炉的正常使用或外输压缩机的正常工作;设备运行中需人工手动排除分离器内和燃烧器前端凝析液至废液坑,造成环境二次污染,且人工排液劳动强度大、存在严重安全隐患。研发具有自主知识产权的油田加热炉用智能相变分离混烃机组,从根本上解决了伴生气分离效率低、油田加热炉燃烧点火因难、熄火、凝析液自动回收输送等问题,从而提高分离效率,有效提升了系统运行的安全、节能、环保性能,具有显著的社会效益和经济效益。
技术实现要素:
4.本发明的目的在于提供一种智能相变分离混烃机组,以解决上述背景技术中提出的问题。
5.为实现上述目的,本发明提供如下技术方案:智能相变分离混烃机组,包括第一旋流分离器、第二旋流分离器、第三旋流分离器、第四旋流分离器、第五旋流分离器、第六旋流分离器、第一蒸发器、第二蒸发器、第三蒸发器、第一冷凝器、第二冷凝器、第三冷凝器、第一集液罐、第二集液罐,其特征在于所述六个旋流分离器并联设置且连通于第二集液罐,所述三个蒸发器并联设置并连通于第二集液罐,所述三个冷凝器并联设置并连通于第二集液罐,所述旋流分离器与蒸发器、冷凝器依次管道串联连接。
6.作为本发明的进一步技术方案:在所述旋流分离器入气口连通管道上安装有第一电动球阀,与所述第一电动球阀所在管道并联的管道上安装有第二电动球阀,在所述第一蒸发器出口与第一冷凝器入口连通管道上安装有第三电动球阀,在所述第二蒸发器出口与第二冷凝器入口连接通道上安装有第四电动球阀,在所述第三蒸发器出口与第三冷凝器入口连接通道上安装有第五电动球阀,在所述冷凝器出口共同连通的管道上安装有第六电动
球阀,在所述第一排污口连通的管道上安装有第七电动球阀,在所述第二排污口连通的管道上安装有第八电动球阀,在所述两排污口共同连接的管道上安装有第九电动球阀。
7.作为本发明的更进一步技术方案:在所述第一电动球阀与旋流分离器入气口间的管路上还安装有第一压力传感器,在所述旋流分离器排气口与所述蒸发器入口间的管路上安装有第二压力传感器,在所述冷凝器出口连接的管路上安装有第三压力传感器,在所述第二排污口的连接管道上安装有第四压力传感器和第六压力传感器,所述第四压力传感器设置在第一排液泵后管道上,所述第六压力传感器设置在靠近去外输管路的一侧,在所述第一排污口的连接管道上安装有第五压力传感器,所述第五压力传感器设置在第二排液泵后管道上。
8.作为本发明的再进一步技术方案:在所述第一压力传感器旁安装有第一温度传感器,在所述第三压力传感器旁还安装有第二温度传感器;在所述第一集液罐上,安装有第一浮球液位开关、第三温度传感器和第一排污阀,所述第二集液罐上安装有第二浮球液位开关、第四温度变送器和第二排污阀。
9.作为本发明的再进一步技术方案:在所述的第一排液泵前管路上安装有第一手动球阀,在所述第一排液泵后管路上安装有第三手动球阀,在所述第二排液泵前管路上安装有第二手动球阀,在所述第二排液泵后管路上安装有第四手动球阀。
10.作为本发明的再进一步技术方案:在所述第四压力传感器后管路上还安装有第一背压阀,所述第一背压阀设置在第四压力传感器和第三手动球阀之间,在所述第五压力传感器后管路上还安装有第二背压阀,所述第二背压阀设置在第五压力传感器和第四手动球阀之间。
11.作为本发明的再进一步技术方案:在所述旋流分离器排液口与第二集液罐(802)上的第一进液口连接的管路上还安装有加液阀和检修阀。
12.与现有技术相比,本发明的有益效果是:伴生气中混烃和水分经有效分离后,可大大提高分离效率,避免油田伴生气因环境温度下降而造成的管路堵塞、输送压缩机故障,从根本上解决了油田加热炉燃烧点火因难、加热炉熄火、爆燃、燃烧不完全、火嘴积碳严重或火烧炉体等问题,确保系统安全运行;另外凝析液自动回收输送,能够将油田现有油气分离器、旋流分离装置和低温相变分离装置产生的凝析液回收并自动全密闭输送至输油管道系统,既降低风险又避免了凝析液排放过程中对环境造成二次污染,提升生态效益;同时通过物联网技术实现了对设备的远程监测及控制,实现了无人值守,从而有效提升了系统运行的安全、节能、环保性能,具有显著的社会效益和经济效益。
附图说明
13.图1为智能相变分离混烃机组的工艺流程图。
14.图中:101
‑
第一电动球阀、102
‑
第二电动球阀、103
‑
第三电动球阀、104
‑
第四电动球阀、105
‑
第五电动球阀、106
‑
第六电动球阀、107
‑
第七电动球阀、108
‑
第八电动球阀、109
‑
第九电动球阀、201
‑
第一压力传感器、202
‑
第二压力传感器、203
‑
第三压力传感器、204
‑
第四压力传感器、205
‑
第五压力传感器、206
‑
第六压力传感器、301
‑
第一温度传感器、302
‑
第二温度传感器、303
‑
第三温度传感器、304
‑
第四温度传感器、401
‑
第一旋流分离器、402
‑
第二旋流分离器、403
‑
第三旋流分离器、404
‑
第四旋流分离器、405
‑
第五旋流分离器、406
‑
第
六旋流分离器、5
‑
加液阀、601
‑
第一蒸发器、602
‑
第二蒸发器、603
‑
第三蒸发器、701
‑
第一冷凝器、702
‑
第二冷凝器、703
‑
第三冷凝器、801
‑
第一集液罐、802
‑
第二集液罐、901
‑
第一排污阀、902
‑
第二排污阀、10
‑
检修阀、111
‑
第一浮球液位开关、112
‑
第二浮球液位开关、121
‑
第一手动球阀、122
‑
第二手动球阀、123
‑
第三手动球阀、124
‑
第四手动球阀、131
‑
第一排液泵、132
‑
第二排液泵、141
‑
第一背压阀、142
‑
第二背压阀。
具体实施方式
15.下面将结合本发明实施例中的附图,对本发明实施例中的技术方案进行清楚、完整地描述。
16.实施例1如图1所示的智能相变分离混烃机组,包括第一旋流分离器401、第二旋流分离器402、第三旋流分离器403、第四旋流分离器404、第五旋流分离器405、第六旋流分离器406、第一蒸发器601、第二蒸发器602、第三蒸发器603、第一冷凝器701、第二冷凝器702、第三冷凝器703、第一集液罐801、第二集液罐802,第一旋流分离器401,包括:第一旋流分离器本体401,用于初步分离油田伴生气中的水分及液态混烃类物质;第一旋流分离器入气口4011,设置于第一旋流分离器401侧面,用于供油田伴生气进入旋流分离器内;第一旋流分离器排气口4012,设置于第一旋流分离器401顶部且连通第一旋流分离器401,用于排出初步分离的伴生气;第一旋流分离器排液口4013,设置于第一旋流分离器401底部且连通第一旋流分离器401,用于排出在第一旋流分离器中401分离出的凝析液;第二旋流分离器402,包括:第二旋流分离器本体402,用于初步分离油田伴生气中的水分及液态混烃类物质;第二旋流分离器入气口4021,设置于第二旋流分离器402侧面,用于供油田伴生气进入旋流分离器内;第二旋流分离器排气口4022,设置于第二旋流分离器402顶部且连通第二旋流分离器402,用于排出初步分离的伴生气;第二旋流分离器排液口4023,设置于第二旋流分离器402底部且连通第二旋流分离器402,用于排出在第二旋流分离器中402分离出的凝析液;第三旋流分离器403,包括:第三旋流分离器本体403,用于初步分离油田伴生气中的水分及液态混烃类物质;第三旋流分离器入气口4031,设置于第三旋流分离器403侧面,用于供油田伴生气进入旋流分离器内;第三旋流分离器排气口4032,设置于第三旋流分离器403顶部且连通第三旋流分离器403,用于排出初步分离的伴生气;第三旋流分离器排液口4033,设置于第三旋流分离器403底部且连通第三旋流分离器403,用于排出在第三旋流分离器中403分离出的凝析液;第四旋流分离器404,包括,第四旋流分离器本体404,用于初步分离油田伴生气中的水分及液态混烃类物质;第四旋流分离器入气口4041,设置于第四旋流分离器404侧面,用于供油田伴生气进入旋流分离器内;第四旋流分离器排气口4042,设置于第四旋流分离器404顶部且连通第四旋流分离器404,用于排出初步分离的伴生气;第四旋流分离器排液口4043,设置于第四旋流分离器404底部且连通第四旋流分离器404,用于排出在第四旋流分离器中404分离出的凝析液;第五旋流分离器405,包括,第五旋流分离器本体405,用于初步分离油田伴生气中的水分及液态混烃类物质;第五旋流分离器入气口4051,设置于第四旋流分离器405侧面,用于供油田伴生气进入旋流分离器内;第五旋流分离器排气口4052,设置于第五旋流分离器405顶部且连通第五旋流分离器405,用于排出初步分离的伴生气;第五旋流分离器排液口4053,设置于第五旋流分离器405底部且连通第五旋流分离器
405,用于排出在第五旋流分离器中405分离出的凝析液;第六旋流分离器406,包括第六旋流分离器本体406,用于初步分离油田伴生气中的水分及液态混烃类物质;第六旋流分离器入气口4061,设置于第六旋流分离器406侧面,用于供油田伴生气进入旋流分离器内;第六旋流分离器排气口4062,设置于第六旋流分离器406顶部且连通第六旋流分离器406,用于排出初步分离的伴生气;第六旋流分离器排液口4063,设置于第六旋流分离器406底部且连通第六旋流分离器406,用于排出在第六旋流分离器中406分离出的凝析液;所述六个旋流分离器为并联关系,其入气口并联于主入气管,其出气口并联于主排气管;第一蒸发器601,用于给未分离净的伴生气降温,在低温环境中深度分离水分及混烃类物质,提升分离效率,包括第一蒸发器入口6011,设置于第一蒸发器601顶部并通过管道连通于旋流分离器的排气口4012、4022、4032、4042、4052、4062;以及第一蒸发器出口6012,设置于第一蒸发器601顶部远离第一蒸发器入口6011一侧;第一蒸发器排液口6013,设置于第一蒸发器601底部,用于排出第一蒸发器601中分离出的凝析液;第二蒸发器602,用于给未分离净的伴生气降温,在低温环境中深度分离水分及混烃类物质,提升分离效率,包括第二蒸发器入口6021,设置于第二蒸发器602顶部并通过管道连通于旋流分离器的排气口4012、4022、4032、4042、4052、4062;以及第二蒸发器出口6022,设置于第二蒸发器602顶部远离第二蒸发器入口6021一侧;第二蒸发器排液口6023,设置于第二蒸发器602底部,用于排出第二蒸发器602中分离出的凝析液;第三蒸发器603,用于给未分离净的伴生气降温,在低温环境中深度分离水分及混烃类物质,提升分离效率,包括第三蒸发器入口6031,设置于第三蒸发器603顶部并通过管道连通于旋流分离器的排气口4012、4022、4032、4042、4052、4062;以及第三蒸发器出口6032,设置于第三蒸发器603顶部远离第三蒸发器入口6031一侧;第三蒸发器排液口6033,设置于第三蒸发器603底部,用于排出第三蒸发器603中分离出的凝析液;第一冷凝器701,用于提高伴生气的温度,使伴生气出口温度调节至安全输送温度,包括第一冷凝器入口7011,设置于第一冷凝器701顶部并通过管道连通与第一蒸发器的出口6012;以及第一冷凝器出口7012,设置于第一冷凝器701的顶部远离第一冷凝器入口7011的一侧,第一冷凝器排液口7013,设置于第一冷凝器701的底部,用于排出第一冷凝器701中的凝析液;第二冷凝器702,用于提高伴生气的温度,使伴生气出口温度调节至安全输送温度,包括:第二冷凝器入口7021,设置于第二冷凝器702顶部并通过管道连通与第二蒸发器的出口6022;以及第二冷凝器出口7022,设置于第二冷凝器702的顶部远离第二冷凝器入口7021的一侧,第二冷凝器排液口7023,设置于第二冷凝器702的底部,用于排出第二冷凝器702中的凝析液;第三冷凝器703,用于提高伴生气的温度,使伴生气出口温度调节至安全输送温度,包括第三冷凝器入口7031,设置于第三冷凝器703顶部并通过管道连通与第三蒸发器的出口6032;以及第三冷凝器出口7032,设置于第三冷凝器703的顶部远离第三冷凝器入口7031的一侧,第三冷凝器排液口7033,设置于第三冷凝器703的底部,用于排出第三冷凝器703中的凝析液;第一集液罐801,用于储存现场现有油气分离器分离出的凝析液;设置第一排污口8011,用于排出第一集液罐801中的凝析液;第二集液罐802,用于储存旋流分离器和蒸发器、冷凝器中分离出的凝析液,包括第一进液口8021,设置于第二集液罐802的侧面并连通于旋流分离器401、402、403、404、405、406的排液口4013、4023、4033、4043、4053、4063;第二进液口8023,与第一进液口8021相对设置在第二集液罐802的侧面并连通于蒸发器601、602、603的排液口6013、6023、6033;第三进液口8024,设置在第三进液口8023一侧并连通于冷凝器701、
702、703的排液口7013、7023、7033;第二排污口8025,用于排出第二集液罐802中的凝析液;第一排液泵131,连通于第一集液罐801的第一排污口8011和第二集液罐802的第二排污口8025;第二排液泵132,连通于第一集液罐801的第一排污口8011和第二集液罐802的第二排污口8025。
17.本发明的智能相变分离混烃机组整个装置包括旋流分离、低温相变分离、凝析液自动回收和凝析液自动输送四部分,其中旋流分离包括六个旋流分离器4,低温相变分离包括三组分离装置,每组一个蒸发器6、一个冷凝器7,低温相变分离系统运行时,蒸发器6的进出口压差大于设定值时,系统自动切换至备用蒸发器6,同时该蒸发器转为化霜状态,化霜时仅允许其中一路化霜,任何时候都必须满足系统有两路以上的制冷通路,从而保证伴生气的稳定供应。具体工作时,伴生气进入旋流分离器4,旋流分离器4输出管路连接三组蒸发器6,以初始状态所述第一蒸发器601和第二蒸发器602运行为例,当所述第一蒸发器601的进出口压差大于设定值时,系统切换至所述第三蒸发器603运行,同时所述第一蒸发器601转为化霜状态,待化霜时间达到预设时间时,停止化霜,进入备用状态;冷凝器可以适当提高伴生气的温度,将伴生气出口温度调节至安全输送温度,有利于伴生气的运输,低温相变分离温度由压缩机的频率、冷媒分配等因素来控制,凝析液回收装置包括两个集液管,第一集液罐801储存现场现有油气分离器分离出的凝析液,第二集液罐802储存旋流分离器、蒸发器、冷凝器分离出的凝析液,当液位达到设定的上限液位时,电动球阀打开,此时凝析液通过泵输出至外部系统中,当液位下降到设定的下限液位时,泵停止工作,相应电动球阀关闭。
18.进一步的,为了使系统安全节能,高效分离,在所述旋流分离器入气口4011、4021、4031、4041、4051、4061连通管道上安装有第一电动球阀101,与所述第一电动球阀101所在管道并联的管道上安装有第二电动球阀102,在所述第一蒸发器出口6012与第一冷凝器入口7011连通管道上安装有第三电动球阀103,在所述第二蒸发器出口6022与第二冷凝器入口7021连接通道上安装有第四电动球阀104,在所述第三蒸发器出口6032与第三冷凝器入口7031连接通道上安装有第五电动球阀105,在所述冷凝器出口7012、7022、7032共同连通的管道上安装有第六电动球阀106,在所述第一排污口8011连通的管道上安装有第七电动球阀107,在所述第二排污口8025连通的管道上安装有第八电动球阀108,在所述两排污口8011、8025共同连接的管道上安装有第九电动球阀109。当电动球阀109关闭时,两集液罐排液各自独立;当排液泵131出现问题时(电机过热载、不排液等情况),打开电动球阀109,此时排液泵132承担两路集液罐的排液;当排液泵132出现问题时(电机过热载、不排液等情况),打开电动球阀109,此时排液泵131承担两路集液罐的排液。
19.进一步的,为了方便对进出气及凝析液运输的控制,在所述第一电动球阀101与旋流分离器入气口4011、4021、4031、4041、4051、4061间的管路上还安装有第一压力传感器201,在所述旋流分离器排气口4012、4022、4032、4042、4052、4062与所述蒸发器入口6011、6021、6031间的管路上安装有第二压力传感器202,在所述冷凝器出口7012、7022、7032连接的管路上安装有第三压力传感器203,在所述第二排污口的连接管道上安装有第四压力传感器204和第六压力传感器206,所述第四压力传感器204设置在第一排液泵131后管道上,所述第六压力传感器206设置在靠近去外输管路的一侧,在所述第一排污口的连接管道上安装有第五压力传感器205,所述第五压力传感器205设置在第二排液泵132后管道上。即通
过六个压力传感器对整个装置的压力进行监控,在所述第一压力传感器201旁安装有第一温度传感器301,在所述第三压力传感器203旁还安装有第二温度传感器302。系统通过控制进入冷凝器的换热量来控制伴生气出口温度。
20.进一步的,为方便对凝析液的液位及稳定进行检测,所述第一集液罐上801安装有第一浮球液位开关111、第三温度传感器303和第一排污阀901,所述第二集液罐802上安装有第二浮球液位开关112、第四温度变送器304和第二排污阀902。实施例2本实施例在实施例1的基础上进一步进行优化,在所述第四压力传感器204后管路上还安装有第一背压阀141,所述第一背压阀141设置在第四压力传感器204和第三手动球阀123之间,在所述第五压力传感器205后管路上还安装有第二背压阀142,所述第二背压阀142设置在第五压力传感器205和第四手动球阀124之间。
21.进一步的,为方便对集液罐旋流分离器分离后凝析液的控制,在所述旋流分离器排液口4013、4023、4033、4043、4053、4063与第二集液罐802上的第一进液口8021连接的管路上还安装有加液阀5和检修阀10。
22.工作原理:本装置利用智能控制系统,首先利用旋流分离器对伴生气中的油水混合物进行分离,对未分离净的伴生气再利用蒸发器进行降温处理,使伴生气中的油水混合物析出,进一步地提高气液分离效率,经降温处理后的伴生气再经过冷凝器,利用冷凝器放出的热量加热伴生气使其温度升高,从而可以将伴生气出口温度调节至安全输送温度,同时可以自动回收处理工作现场产生的凝析液,利用双泵排凝逻辑输送凝析液至外输管网或用户指定的容器中,从而进一步提高能源的利用效率,达到安全、环保、降碳的目的,为实现双碳目标贡献力量。
23.对于本领域技术人员而言,显然本发明不限于上述示范性实施例的细节,而且在不背离本发明的精神或基本特征的情况下,能够以其他的具体形式实现本发明。因此,无论从哪一点来看,均应将实施例看作是示范性的,而且是非限制性的,本发明的范围由所附权利要求而不是上述说明限定,因此旨在将落在权利要求的等同要件的含义和范围内的所有变化囊括在本发明内。不应将权利要求中的任何附图标记视为限制所涉及的权利要求。
24.此外,应当理解,虽然本说明书按照实施方式加以描述,但并非每个实施方式仅包含一个独立的技术方案,说明书的这种叙述方式仅仅是为清楚起见,本领域技术人员应当将说明书作为一个整体,各实施例中的技术方案也可以经适当组合,形成本领域技术人员可以理解的其他实施方式。
再多了解一些
本文用于企业家、创业者技术爱好者查询,结果仅供参考。