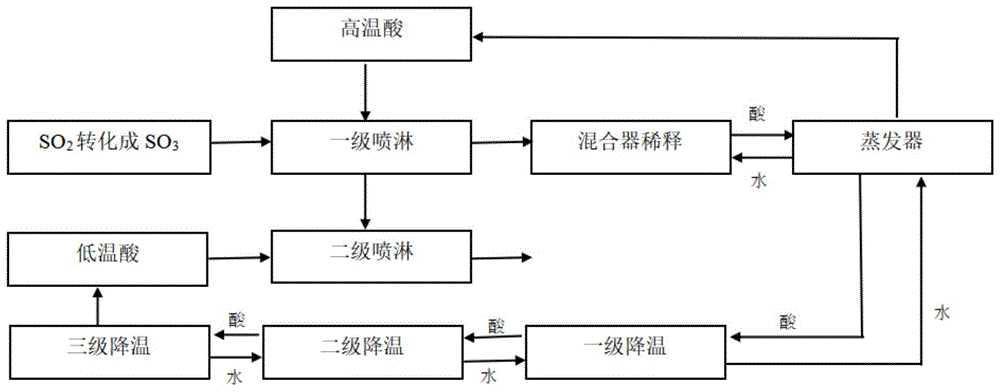
本发明属于硫酸生产热量回收技术领域,具体涉及一种砂酸低位余热回收方法及其回收系统。
背景技术:
通过硫磺生产硫酸的过程包括硫磺焙烧、so2转化成so3、so3吸收等工序,这三个工序产生的热量分别占总热量的56%、19%以及25%,目前硫酸生产中,只利用到硫磺焙烧过程中的高位热能进行生产副产品过热蒸汽,而对于so2转化成so3、so3吸收等工序的低位热能均没有好好利用。
目前so2转化成so3后,通常采用的技术手段是:酸吸后进行酸冷,高温烟气温度高达250℃,砂酸转化工段反应后的余热通过一吸酸吸收后,通过大量的冷却循环水换热带走,造成大量的热量损失,同时增加了电耗和为降低污染污排放。
行业内还有一种hrs处理流程,其处理过程为:“含三氧化硫气体从塔底进入由塔顶排出。该塔装有上下两级填料层,下一级填料层的上塔酸是220℃、w(h2so4)99%以上的硫酸,上一级填料层的上塔酸则是与传统吸收工艺浓度和温度相似的硫酸,以确保三氧化硫吸收率。两股酸都从塔底流入与塔相连的泵槽,然后由hrs酸循环泵送入hrs锅炉生产0.3~1.0mpa饱和蒸汽。由于酸吸收三氧化硫后浓度增加,需通过hrs稀释器加水以维持浓度,水稀释后的循环酸回到hrs热回收塔的下一级再进行吸收”,该技术虽然有对热量进行回收,但是蒸汽产量较低,而且是在高温酸稀释前进行热量回收,浪费了稀释热。
技术实现要素:
本发明的目的在于提供一种砂酸低位余热回收方法及其回收系统,以解决上述提及现有硫酸生产热量回收技术存在的热量利用不充分的技术问题。
为实现上述目的,本发明采用的技术方案如下:
一种砂酸低位余热回收方法,包括如下步骤:
(1)so2转化成so3后,采用两级喷淋吸收so3,一级喷淋采用质量分数为99.1%-99.3%、190℃以上温度的高温酸,吸收烟气中的热量;二级喷淋采用质量分数为98.5%、70℃以下温度的低温酸,保证吸收率;
(2)一级喷淋塔输出的质量百分数不低于99.5%的高温酸,通入混合器,并加水稀释;
(3)加水稀释的高温酸送往蒸发器,与蒸发器中的水进行换热产生蒸汽,根据浓度以及各循环槽液位,一部分送回一级喷淋,一部分逐级降温后送往二级喷淋,逐级降温过程为:
3a将蒸发器出来的酸通入中压给水加热器,与中压给水加热器中的水进行换热;
3b将自3a步骤出来的酸送入低压蒸汽给水加热器,与低压蒸汽给水加热器中的水进行换热;
3c将自3b步骤出来的酸送入脱盐水加热器,与脱盐水加热器中的脱盐水进行换热;
其中,脱盐水依次自脱盐水加热器、低压蒸汽给水加热器、中压给水加热器加热后进入蒸发器。
作为优选地,步骤(3)中,逐级降温过程中,所述中压给水加热器中的水加热至175℃,低压蒸汽给水加热器中的水加热至150℃,脱盐水加热器中的脱盐水加热至102℃,高温酸由190℃以上高温降至120℃。
作为优选地,所述步骤(2)中使用的稀释水为步骤(3)中蒸发器中的水。
一种砂酸低位余热回收系统,包括用于喷淋吸收so3的两级喷淋塔、用于稀释高温酸的混合器,用于逐级降温的中压给水加热器、低压蒸汽给水加热器和脱盐水加热器,用于连接各设备以供通酸通水的管道以及管道上的阀门。
与现有技术相比,本发明具有以下有益效果:
1、本发明通过通过逐级降温将产酸的剩余热量充分利用,充分预热了给水,吨酸产汽率提高了20%~25%,同时用清水代传统的低浓度酸来稀释高浓度酸,增加了稀释热,利于提高产汽率,从产汽率0.4(0.4吨蒸汽/吨折百98%酸)提升至0.48(0.48吨蒸汽/吨折百98%酸),最高达到0.50(0.50吨蒸汽/吨折百98%酸);
2、本发明充分利用了so2转化成so3、so3吸收甚至高温酸稀释等工序的低位热能,热量浪费少;
3、对于本公司生产而言,本发明方法可年产蒸汽129360吨蒸汽,可节约煤炭1.7万吨/年,直接年创造效益1800万。
附图说明
图1为本发明提供的砂酸低位余热回收方法的工艺流程图。
具体实施方式
如图1所示,为本发明提供的砂酸低位余热回收方法的工艺流程示意图,包括如下步骤:
(1)so2转化成so3后,采用两级喷淋吸收so3,一级喷淋采用质量分数为99.1%-99.3%、190℃以上温度的高温酸,二级喷淋采用质量分数为98.5%、70℃以下温度的低温酸;
(2)一级喷淋塔输出的质量百分数不低于99.5%的高温酸,通入混合器,并加水稀释;
(3)加水稀释的高温酸送往蒸发器,与蒸发器中的水进行换热产生蒸汽,根据浓度以及各循环槽液位,一部分送回一级喷淋,一部分逐级降温后送往二级喷淋,逐级降温过程为:
3a将蒸发器出来的酸通入中压给水加热器,与中压给水加热器中的水进行换热;
3b将自3a步骤出来的酸送入低压蒸汽给水加热器,与低压蒸汽给水加热器中的水进行换热;
3c将自3b步骤出来的酸送入脱盐水加热器,与脱盐水加热器中的脱盐水进行换热;
其中,脱盐水依次自脱盐水加热器、低压蒸汽给水加热器、中压给水加热器加热后进入蒸发器。
用以匹配该处理方法的处理系统,包括用于喷淋吸收so3的两级喷淋塔、用于稀释高温酸的混合器,用于逐级降温的中压给水加热器、低压蒸汽给水加热器和脱盐水加热器,用于连接各设备以供通酸通水的管道以及管道上的阀门。
下面结合各实施例对本发明作进一步说明,本发明的方式包括但不仅限于以下实施例。
实施例1
本实施例按照以下步骤处理so2转化成so3后的气体:
(1)so2转化成so3后,采用两级喷淋吸收so3,一级喷淋采用质量分数为99.3%、200℃的高温酸,二级喷淋采用质量分数为98.5%、70℃的低温酸;
(2)一级喷淋塔输出的质量百分数不低于99.5%的高温酸,通入混合器,并加水稀释,得260℃左右的高温酸;
(3)加水稀释的高温酸送往蒸发器,与蒸发器中的水进行换热产生蒸汽,换热后的高温酸温度为200℃,根据浓度以及各循环槽液位,一部分送回一级喷淋,一部分逐级降温后送往二级喷淋,逐级降温过程为:
3a将蒸发器出来的酸通入中压给水加热器,与中压给水加热器中的水进行换热;
3b将自3a步骤出来的酸送入低压蒸汽给水加热器,与低压蒸汽给水加热器中的水进行换热;
3c将自3b步骤出来的酸送入脱盐水加热器,与脱盐水加热器中的脱盐水进行换热;
其中,脱盐水依次自脱盐水加热器、低压蒸汽给水加热器、中压给水加热器加热后进入蒸发器。
其中,步骤(3)中,逐级降温过程中,所述中压给水加热器中的水加热至175℃,低压蒸汽给水加热器中的水加热至150℃,脱盐水加热器中的脱盐水加热至102℃,高温酸由200℃降至120℃。最终,本实施例中的产汽率的达到0.50吨蒸汽/吨折百98%酸。
实施例2
本实施例按照以下步骤处理so2转化成so3后的气体:
(1)so2转化成so3后,采用两级喷淋吸收so3,一级喷淋采用质量分数为99.3%、200℃的高温酸,二级喷淋采用质量分数为98.5%、70℃的低温酸;
(2)一级喷淋塔输出的质量百分数不低于99.5%的高温酸,通入混合器,并加水稀释,得260℃左右的高温酸;
(3)加水稀释的高温酸送往蒸发器,与蒸发器中的水进行换热产生蒸汽,换热后的高温酸温度为200℃,根据浓度以及各循环槽液位,一部分送回一级喷淋,一部分逐级降温后送往二级喷淋。
最终,本实施例中的产汽率为0.4吨蒸汽/吨折百98%酸。
实施例3
本实施例按照以下步骤处理so2转化成so3后的气体:
(1)so2转化成so3后,采用两级喷淋吸收so3,一级喷淋采用质量分数为99.1%、200℃的高温酸,二级喷淋采用质量分数为98.5%、70℃的低温酸;
(2)一级喷淋塔输出的质量百分数不低于99.5%的高温酸,通入混合器,并加水稀释,得250℃左右的高温酸;
(3)加水稀释的高温酸送往蒸发器,与蒸发器中的水进行换热产生蒸汽,换热后的高温酸温度为200℃,根据浓度以及各循环槽液位,一部分送回一级喷淋,一部分逐级降温后送往二级喷淋,逐级降温过程为:
3a将蒸发器出来的酸通入中压给水加热器,与中压给水加热器中的水进行换热;
3b将自3a步骤出来的酸送入低压蒸汽给水加热器,与低压蒸汽给水加热器中的水进行换热;
3c将自3b步骤出来的酸送入脱盐水加热器,与脱盐水加热器中的脱盐水进行换热;
其中,脱盐水依次自脱盐水加热器、低压蒸汽给水加热器、中压给水加热器加热后进入蒸发器。
其中,步骤(3)中,逐级降温过程中,所述中压给水加热器中的水加热至175℃,低压蒸汽给水加热器中的水加热至150℃,脱盐水加热器中的脱盐水加热至102℃,高温酸由200℃降至120℃。最终,本实施例中的产汽率的达到0.49吨蒸汽/吨折百98%酸。
实施例4
本实施例按照以下步骤处理so2转化成so3后的气体:
(1)so2转化成so3后,采用两级喷淋吸收so3,一级喷淋采用质量分数为99.1%、190℃的高温酸,二级喷淋采用质量分数为98.5%、70℃的低温酸;
(2)一级喷淋塔输出的质量百分数不低于99.5%的高温酸,通入混合器,并加水稀释,得250℃左右的高温酸;
(3)加水稀释的高温酸送往蒸发器,与蒸发器中的水进行换热产生蒸汽,换热后的高温酸温度为190℃,根据浓度以及各循环槽液位,一部分送回一级喷淋,一部分逐级降温后送往二级喷淋,逐级降温过程为:
3a将蒸发器出来的酸通入中压给水加热器,与中压给水加热器中的水进行换热;
3b将自3a步骤出来的酸送入低压蒸汽给水加热器,与低压蒸汽给水加热器中的水进行换热;
3c将自3b步骤出来的酸送入脱盐水加热器,与脱盐水加热器中的脱盐水进行换热;
其中,脱盐水依次自脱盐水加热器、低压蒸汽给水加热器、中压给水加热器加热后进入蒸发器。
其中,步骤(3)中,逐级降温过程中,所述中压给水加热器中的水加热至165℃,低压蒸汽给水加热器中的水加热至140℃,脱盐水加热器中的脱盐水加热至60℃,高温酸由190℃降至70℃。最终,本实施例中的产汽率的达到0.47吨蒸汽/吨折百98%酸。
本发明涉及到高浓度的硫酸处理,因此,在实际生产过程中,应当注意:
1生产前的准备
1.1检查气体管道、水管道、酸管道、阀门是否正确安装。
1.2检查所有管道、阀门是否完好,无漏点。
1.3检查所有仪表、电器是否正常,显示是否准确。
1.4对酸系统、水系统、蒸汽系统进行清洗、吹扫。
1.5对dcs控制、连锁设置进行测试,看是否可以投入运行。
1.6检查电、水、压空是否供应正常。
1.7检查应急物资是否准备到位。
2清洗、吹扫
2.1酸洗
2.1、二级循环酸系统灌酸
当高温循环槽液位达到1400mm时停止灌酸。
2.2、启动高温循环泵。
2.3、密切注视泵槽液位变化,液位下降到低至900mm时,向泵槽加酸。
2.4、每小时分析一次循环酸浓度,确保酸浓不低于97.5%,如果酸浓低于97.5%,停止酸循环,系统换酸。
2.5、当系统酸浓连续8小时保持不变后停止酸循环。
2.6、酸循环结束后将酸排入干吸工段。
3、水管清洗
3.1脱盐水管道清洗
打开脱盐水管道上的根部阀和低点排水阀,关闭脱盐水加热器进出口阀,当排水清澈后,打开脱盐水加热器进出口阀、换热器壳程排水阀和低点排水阀,冲洗出口管道。
3.2中压蒸发器给水、低压蒸发器给水及蒸汽发生器回路清洗。
3.3打开除氧器出水阀,关闭蒸发器给水泵进口阀,打开排水阀,冲洗泵进口管道。
3.4关闭蒸发器给水加热器水进出口阀和旁路阀,打开进口管路上的排放阀,打开蒸汽发生器上的排气阀,锅炉底部排污阀、紧急排污阀,关闭蒸汽出口阀。
3.5关闭液位调节阀,打开旁路阀,启动1台蒸汽蒸发器给水泵,微开出口阀,冲洗蒸发器给水加热器进口管路,当进口管路上的排放水干净后打开蒸汽给水加热器水进出口阀,蒸汽发生器水进口阀当定期排污膨胀器排出水干净后关闭蒸汽发生器的所有排放阀,使蒸汽发生器达到正常操作液位,打开连续排污阀,冲洗锅炉取样冷却器回路。停止蒸发器给水泵。
3.6关闭连续排污阀和液位调节阀的旁路阀,打开底部排放阀将蒸汽发生器的水排尽。关闭蒸汽发生器给水加热器进出口阀,打开水旁路阀和加热器壳体排水阀,关闭混合器进口的水切断阀,打开排放阀。启动一台混合器给水泵冲洗混合器加水管,当排放的水干净后停混合器给水泵。
3.7打开中压锅炉给水加热器管程放净阀,打开中压锅给水加热器进水阀。冲洗压锅炉给水加热器及进水管;打开去中压锅炉给水主管上放净阀,关闭管程放净阀,冲洗中压锅炉给水加热器出水管道;
4蒸汽管道吹扫
4.1蒸发器出口断开后,将蒸汽输送管道接入消声器,并将蒸汽放散阀打开,待准备完毕后,由调度通知五车间送汽,对蒸汽输送管道进行吹扫。
4.2接调度通知后,热电岗位人员关闭蒸汽主管排空阀,打开主蒸汽管道上的支路阀门,缓慢打开低压蒸汽管道上的手动进气阀,调节阀门开度使低压蒸汽管温度以每小时50℃/h速率升温,压力维持在0.1-0.2mpa。
4.3当温度升温至190℃后,砂酸岗位人员关闭放散阀,开始管道升压,关闭砂酸放空阀,调节热电进汽阀,逐步升压,在升压过程中巡检管道是否存在异常,有异常需处理,无异常继续升压,当升压至0.5mpa后,打开砂酸蒸汽放散阀,检查无异常后,再关闭砂酸蒸汽放散阀,继续升压至0.8mpa,连续进行多次升压、泄压。
4.4多次升压、泄压无异常后,开始对管道连续吹扫,打开热电蒸汽进气阀对管道进行吹扫。
5.系统灌酸
关闭混合器加水管路上的水调节阀、切断阀和混合器进口出的手动切断阀。关闭混合器压缩空气管路上的切断阀和混合器进口出的手动切断阀。打开给水排放阀和压缩空气排气阀。
5.1蒸汽发生器液位设为手动,关闭液位调节阀,关闭底部排污阀。
5.2向系统罐酸,当循环槽液位达到1400mm时,停止灌酸。打开蒸发器给水加热器,脱盐水加热器的排酸阀,利用高温循环槽向换热器灌酸。
5.2关闭高温循环槽,蒸发器给水加热器、脱盐水加热器的排酸阀,重新灌酸使循环槽液位达到1400mm。
5.3将蒸汽发生器出口至混合器管道上的酸阀门打开25%,高温循环槽液位控制器设为手动,关闭液位调节阀。
5.4打开高温循环泵轴承箱、轴封的冷却水和压缩空气阀门,启动高温循环酸泵,调节蒸汽发生器至混合器的流量为920m3/h。
5.5密切注视泵槽液位变化,液位下降低于900mm时关闭循环泵,向泵槽内加酸,激活混合器进口酸低-低流量连锁。
5.6打开酸浓分析仪和酸管线及分析冷却系统冷却水管上的所有阀门。
5.7当高温泵槽液位处于或高于正常操作液位后,将液位控制器设为自动,设定值为900mm。打开蒸发器出口去蒸发器给水加热器和脱盐水加热器的阀门,让酸串入干燥和二吸。操作中液位不得低于设定值。
5.8启动二吸塔酸循环泵,二吸塔酸循环,打开热回收塔二级酸管路上的阀门准备向二级供酸,将二级酸流量控制器设为自动,将流量设定值缓慢从0提高至58m3。
5.9注意二吸塔酸循环槽液位的变化,如果液位下降到低位报警值,将二吸酸流量控制器设为手动并关闭流量调节阀,待二吸酸液位恢复正常后将二吸酸流量控制器设为自动并恢复向二级供酸。
5.10检查并保持高温循环槽及二吸循环槽在正常液位。
5.11检查至二级酸流量酸流量是否在设计值或正常操作值
5.12保持冷酸循环24h以上,每4h对热回收塔一级进口酸浓人工分析一次。
5.13当酸循环4h后,启动蒸发器给水泵,将蒸汽发生器液位控制器设为自动,设定值为220mm。打开蒸发器给水加热器和脱盐水加热器给水进出口阀,关闭旁路阀。
5.14系统查漏,在酸循环24小时内,需要内混合器、换热器、蒸发器进行系统泄露检查。
6、生产操作
6.1.1沸腾炉投运前低温热回收系统的操作。
沸腾炉投运前,低温热回收的系统各项检查已完成,循环水系统、脱盐水系统、中压蒸发器给水系统、低压蒸发器给水系统及循环酸均已运行。低温热回收系统已经完成的操作如下。
6.1.2热回收塔和高温循环槽。
1)调节至混合器的流量(fi-9001)900m3/h。
2)二级进口流量控制器(fic-9002)设为自动调节,流量设定值60m3/h。
3)激活混合器进口酸流量低-低流量连锁(fsll-9001)。
4)高温循环槽液位控制器(lic-9001)设为自动调节,液位设定值900mm。
5)检查1级循环酸浓度显示器(aic-9002a,b,ai-9003,ai-9004,ai-9005)是否显示基本相同的酸浓度。
6)激活低-低酸浓联锁(asll-9002)
6.1.3混合器。
1)一级酸浓控制器(aic-9002)设为自动调节,浓度设定值99.0%。
2)混合器加水调节阀和切断阀(av9002和xv-9001)处于关闭,排液阀(xv-9002)打开。混合器串酸调节阀和切断阀(hv-9003和xv-9003)处于关闭。
3)混合器加水管线上的手动切断阀,除混合器进口处的一个关闭外,其余全部打开。
4)激活混合器水进口低-低压力联锁(psl-9001)。
5)混合器压缩空气进口切断阀(xv-9005)打开,排气阀(xv-9004)关闭。
6)打开混合器压缩空气管路上的手动阀,让空气流过管路系统,然后关闭靠近混合器进口的切断阀。
7)激活压缩空气低-低联锁(psl-9002),检查现场压力表(pg-9062)的读数。
8)再次确认混合器入口处的加水阀和空气阀关闭。
6.1.4蒸汽发生器
1)蒸汽发生器液位控制器(lic-9002)投入运行,液位设定值220mm。
2)关闭蒸汽放空阀,打开锅炉连续排污阀。
6.1.5中压给水加热器
中压给水加热器给水进、出口阀门打开,旁路阀关闭。
6.1.6低压给水加热器
低压给水加热器给水进、出口阀门打开、旁路阀关闭。
6.1.7脱盐水加热器
脱盐水进、出口阀门打开、旁路阀关闭。
6.2沸腾炉投运后低温热回收系统的操作
1)调节转化器各段的入口温度为正常操作温度。
2)打开混合器进口处的加水阀和压缩空气阀,调节压缩空气阀的开度使空气压力(pg-9062)为0.4mpa。
3)再次确认二级进口流量控制器(fic-9002)已经激活。
4)当转化器床温度开始上升产出so3气体送入热回收塔后,塔内的酸浓度开始上升。当浓度达到99.0%后加水阀(av-9002)自动打开,向混合器加水。
5)开始进行热酸运行阶段的泄漏检查。
6)在蒸汽发生器压力(pg-9067)达到设定值0.8mpa前,一级酸进口处的人工取样分析每15分钟一次。酸温正常后,人工取样次数可减少到1班1次。
3.3运行正常操作
3.3.1低温热回收系统设有紧急停车联锁,一旦怀疑系统有酸泄漏,应立即启动该联锁。
当联锁系统关闭装置并排放蒸汽发生器时,系统其它设备中仍有浓度较低的高温硫酸存在。必须人工分析各设备中的酸,如果酸浓降低至97.5%以下应尽快将设备中的酸全部排出。
上述实施例仅为本发明的优选实施方式之一,不应当用于限制本发明的保护范围,但凡在本发明的主体设计思想和精神上作出的毫无实质意义的改动或润色,其所解决的技术问题仍然与本发明一致的,均应当包含在本发明的保护范围之内。
本文用于企业家、创业者技术爱好者查询,结果仅供参考。