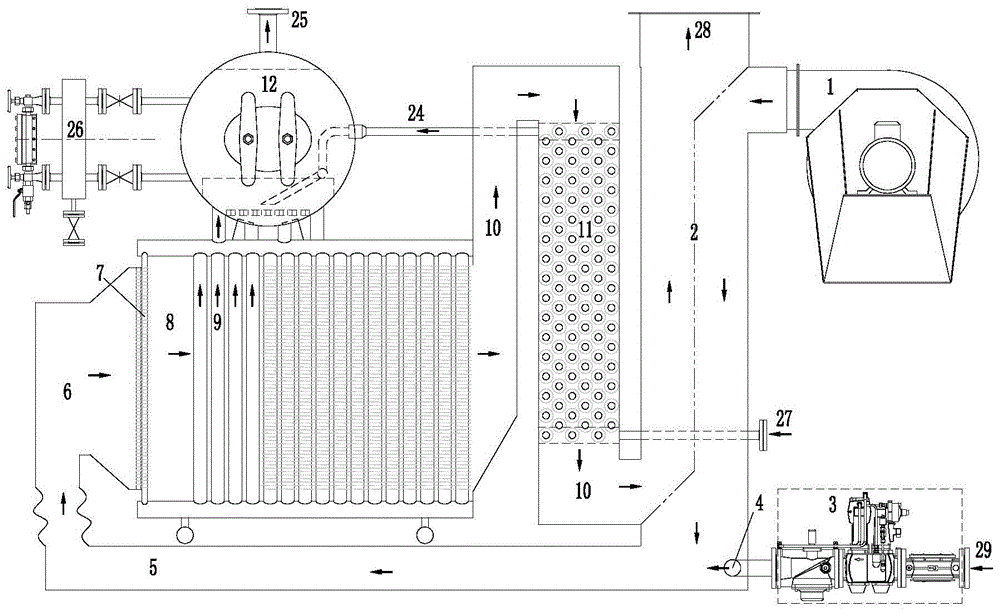
技术领域:
本发明属于燃气蒸汽锅炉技术领域,具体涉及一种新型低氮排放冷焰燃烧一体化蒸汽锅炉。
背景技术:
:
目前30吨以下的燃天然气蒸汽锅炉,大部分采用wns型卧式内燃火管蒸汽锅炉;4吨以下燃天然气蒸汽锅炉除wns型锅炉外,还有lss型贯流锅炉。
这两种炉型各有优缺点,其中wns型锅炉采用卧式内燃全湿背式结构,配套高效螺纹烟管,所有蒸发受热均内置在锅壳内,高温烟气在内,水在外,并配有完善的保温外包设计,散热损失少,热效率高,水容量大,安全性好,使用寿命长,检修方便,特别适合长时间稳定运行。但缺点是水容量大,冷态启炉时间较长,当锅炉长时间间歇运行时,或热备用运行时,综合能效低。
lss型贯流锅炉采用立式水管结构,水容量小,产汽速度快,特别适合间歇式运行;但由于其水容量小,汽水分界面在管内,对水质要求较高,使用寿命短,无法检修;另外,本体出烟温度高,即便尾部加装节能器,设计热效率也相对较低。
所以,发明一种锅炉结构,综合两者的优点,开发一种低nox排放,设计热效率和综合运行能效均高,结构紧凑,同时便于检修的燃天然气蒸汽锅炉是本发明的目标。
技术实现要素:
:
本发明的目的是,提出一种新型蒸汽锅炉,综合wns型锅炉和lss贯流锅炉的优点,标准化程度高,便于预制备件,可快速拼装成形或维修更换,设计热效率高,水容量相对较低,综合能效高,产汽速度快,同时务必满足燃天然气,且氧量低于3.5%时,nox排放小于30mg/m3的低氮要求。
本发明的技术方案是,一种新型低氮排放冷焰燃烧一体化蒸汽锅炉,主要由风机1、空气预热器2、燃气阀组3、燃气分配管4、风道5、配风室6、水冷炉排7、炉膛8、对流区9、烟道10、节能器11、汽包12、下降管13、下降联通管14、水位控制器26等组成。锅炉本体部分由两组膜式壁模块15、多组炉排对流区模块16、汽包12、下降管13、下降联通管14等拼装而成;其中对膜式壁模块15及炉排对流区模块16进行标准化、系列化设计。目前按0.5-2t/h、2-8t/h、8-30t/h三个区间分成三种标准类型模块,涵盖了wns型单炉胆锅炉的所有规格。
炉排对流区模块16主要由模块引入管17、模块下集箱18、炉排翅片管19、对流区光管20、对流区翅片管20-1、模块上集箱21、模块引出管22组成。膜式壁模块15主要由模块引入管17、模块下集箱18、膜式壁管32、膜式壁扁钢32-1、模块上集箱21、模块引出管22组成。这两种规格的模块相互拼装,组成了锅炉本体受热部件,囊括了水冷炉排7、炉膛8、对流区9三个功能区,组装完毕之后,只需用管道与汽包12相连即可快速组成锅炉本体。当需要增加或减少锅炉容量时,只需增加或减少炉排对流区模块16的数量即可。
低氮排放采用了全预混冷焰燃烧技术,采用了低温空气预热器2 全新结构的水冷炉排7,水冷炉排7主要由翅片管19、多孔陶瓷23组成,实现低nox排放低于30mg/m3的目标。
烟风系统:风机1将冷空气加压后进入空气预热器2预热成热空气;经过燃气阀组3减压、燃气分配管4分流后的天然气与热空气在风道5内混合均匀,进入配风室6,然后混合气经过水冷炉排7后点燃形成火焰在炉膛8内燃烧,接着高温烟气依次进过对流区9、烟道10、节能器11、空气预热器2、出烟口28,最后经烟囱排入大气。
给水系统:经软化除氧后的给水经水泵加压后,进入节能器11预热,预热后的水进入汽包12,经过自然循环加热后变成汽水混合物,经过汽包12内部的分离装置进行汽水分离,分离出的饱和蒸汽经主汽阀供给用户使用。
汽水循环系统:锅炉采用自然循环,汽包12内的饱和水,经过下降管13、下降联通管14,分别进入膜式壁模块15、炉排对流区模块16,经过加热后变成汽水混合物,再次进入汽包12,通过密度差形成自然循环。
本发明的有益效果,本发明涉及一种新型低氮排放冷焰燃烧一体化蒸汽锅炉,本体受热面结构采用模块化拼装式设计,标准化程度高,品控管理简单,增容维修简便,特别适合锅炉行业因季节性生产不均衡带来的产能浪费问题。
本发明涉及一种新型低氮排放冷焰燃烧一体化蒸汽锅炉,采用全预混冷焰燃烧技术,设计了一种全新的水冷炉排结构,使得全预混火焰背面得到有效冷却,增大了辐射面,降低了燃烧温度,实现了低nox燃烧;同时降低了炉膛尺寸,使得该发生器结构更加小巧紧凑。
本发明涉及一种新型低氮排放冷焰燃烧一体化蒸汽锅炉,增设了空气预热器,在适当提高空气温度的同时,进一步降低了排烟温度,提高了热效率,使季节性能耗差异降至更低;另外,水容量小,综合能效高。
本发明涉及一种新型低氮排放冷焰燃烧一体化蒸汽锅炉,空气预热器与本体受热面一样,采用标准化、模块化拼装式设计,大幅提高了工作效率,减少了浪费;同时空气预热器采用304全不锈钢结构,可以耐氧化和酸性腐蚀,提高了使用寿命。
附图说明:
图1为锅炉结构正视图;
图2为锅炉结构侧视图;
图3为锅炉结构俯视图;
图4为水冷炉排7结构示意图,其中a为炉排截面图,b为a的侧视图;
图5为标准受热面模块示意图,其中a为炉排对流区模块,b为膜式壁模块。
图中序号说明:
1—风机,2—空气预热器,3—燃气阀组,4—燃气分配管,5—风道,6—配风室,
7—水冷炉排,8—炉膛,9—对流区,10—烟道,11—节能器,12—汽包,
13—下降管,14—下降连通管,15—侧边膜式壁模块,16—炉排对流区模块,
17—模块引入管,18—模块下集箱,19—炉排翅片管,20—对流区光管,
20-1—对流区翅片管,21—模块上集箱,22—模块引出管,23—多孔陶瓷,
24—节能器出水管,25—主蒸汽口,26—水位控制器,27—给水入口,28—出烟口,
29—燃气进口,30—排污口,31—火焰区,32—膜式壁管,32-1—膜式壁扁钢
具体实施方式:
本发明的各项发明内容具体实施方式如下:
本发明涉及一种新型低氮排放冷焰燃烧一体化蒸汽锅炉,主要由风机1、空气预热器2、燃气阀组3、燃气分配管4、风道5、配风室6、水冷炉排7、炉膛8、对流区9、烟道10、节能器11、汽包12、下降管13、下降联通管14、水位控制器26等组成。
烟风系统:风机1将冷空气加压后进入空气预热器2预热成热空气;经过燃气阀组3减压、燃气分配管4分流后的天然气与热空气在风道5内混合均匀,进入配风室6,然后混合气经过水冷炉排7后点燃形成火焰在炉膛8内燃烧,接着高温烟气依次进过对流区9、烟道10、节能器11、空气预热器2、出烟口28,最后经烟囱排入大气。
给水系统:经软化除氧后的给水经水泵加压后,进入节能器11预热,预热后的水进入汽包12,经过自然循环加热后变成汽水混合物,经过汽包12内部的分离装置进行汽水分离,分离出的饱和蒸汽经主汽阀供给用户使用。
汽水循环系统:锅炉采用自然循环,汽包12内的饱和水,经过下降管13、下降联通管14,分别进入膜式壁模块15、炉排对流区模块16,经过加热后变成汽水混合物,再次进入汽包12,通过密度差形成自然循环。
标准化模块设计的实施方式:如附图5a所示,炉排对流区模块16主要由模块引入管17、模块下集箱18、炉排翅片管19、对流区光管20、对流区翅片管20-1、模块上集箱21、模块引出管22组成,这些结构用于组成锅炉本体受热面的水冷炉排7、炉膛8、对流区9三个区域,并通过模块上下集箱18、21的紧密排列而实现烟气上下区域密封。炉排对流区模块16属于主受热面模块,主要由其来实现负荷增减。
如附图5b所示,膜式壁模块15主要由模块引入管17、模块下集箱18、膜式壁管32、膜式壁扁钢32-1、模块上集箱21、模块引出管22组成。用于水冷炉排7、炉膛8、对流区9这三个受热面区的两侧密封。
如附图1、2、3所示,锅炉本体主要由膜式壁模块15、炉排对流区模块16、1个汽包12、四组下降管13、两组下降联通管14组成。其中,水冷炉排7、炉膛8、对流区9三个受热面采用模块化设计,由序15和序16两种规格的模块搭配使用来实现三个受热面区域的功能。如图3,多组炉排对流区模块16并排放置在中间,两侧各放置一组膜式壁模块15,从而组成了锅炉本体受热面,然后通过管道联通到汽包12,实现自然循环。
目前,针对0.5-30t/hwns型单炉胆卧式内燃锅炉,采用对标设计,将锅炉吨位分为0.5-2t/h、2t/h-8t/h、8-30t/h三个区段,需要为每个区段设计一种类型的标准模块,故此需要为膜式壁模块15和炉排对流区模块16各设计三套,共六个规格的标准模块,即可实现0.5-30t/h所有规格新型低氮燃气蒸汽锅炉的本体受热面快速设计。
这种标准化、模块化的设计方式大幅减少了设计工作量;同时,标准化模块化的部件应用,使得产品可以实现批量化生产,使得制作更简便、质量更有保障、生产周期更短、库存备料更方便、资源利用率更高、浪费更少;对锅炉企业来说,可实现规模化生产,生产成本更低廉,也能为用户提供更好、更快捷、更加标准化的服务。
低氮燃烧的实施方式:如附图4所示,水冷炉排7结构由多孔陶瓷23和翅片管19组成,空气与天然气的混合气经由多孔陶瓷23上的小孔,均匀的流向翅片管19上的螺旋翅片区,沿着螺旋翅片19-1之间通道将混合气预热后,进入炉膛燃烧。
采用多孔陶瓷23是为了利用陶瓷的耐热性及低热导性,隔绝火焰透过翅片间隙投射来的辐射热不被传导到混合气入口处,确保进入水冷炉排7前的混合气不被快速加热,提高设备的安全性。
多孔陶瓷23一端为平面,另一端与翅片管19翅端圆弧贴合;其上均匀开制了多排小孔,每排小孔均正对翅片管19中心线,每排小孔两两之间的节距为翅片19-1节距的2-3倍。天然气预混气常温回火最小孔径为3.8mm,由于本锅炉设置了空气预热器故此实际混合气温将会达到50-60℃,故而此处开孔直径仅为2.4mm,较小的孔径可以有效防止回火,同时可以确保整个燃烧面气流均匀;另外2.4mm的孔径也可确保细小的灰尘通过,不会出现堵塞。
翅片管19上的螺旋翅片19-1材质为耐热不锈钢,基管材料可采用碳钢或不锈钢,基管与翅片需用连续激光焊接,确保100%焊透率。采用翅片管19的目的是使得火焰背面得到有效冷却,降低火焰温度;同时可利用翅片对混合气进行分流和预热,确保整个面均成为燃烧面,扩大火焰冷却面积,降低火焰温度。通过以上措施,可以实现在3.5%氧量条件下,火焰温度低于1400℃,氮氧化物低于30mg/m3。
高效的实施方式:如附图1、2、3所示,在锅炉尾部设置了节能器11、空气预热器2,确保在设计条件下,锅炉出口烟气温度降低至55℃以下,烟气冷凝率不低于8%,锅炉设计效率达到98%,达到gb24500-2020工业锅炉能效限定值及能效等级燃气锅炉1级能效限定值,燃气冷凝锅炉3级能效限定值。同时,空气预热温度不大于60℃,较低的空气温度可以保证低nox的实现。
锅炉本体部分对流区9分成两个部分,前部为光管20结构,用于吸收高温烟气和阻挡炉膛火焰辐射;后部为螺旋翅片管20-1结构,采用碳钢基管 耐热不锈钢翅片(激光熔融焊接工艺),使得本体出口烟温不大于饱和温度 30℃。较低的本体出口温度使得节能器出口烟温降低至75℃成为可能,这也保证了尾部空预器空气升温不会高于60℃。
为了提高空气预热器2的换热效率,换热面采用多层薄壁平板结构;烟气自下而上,空气自上而下纯逆流布置;窄通道设计,平板之间的间隙仅5mm;换热平板采用0.3mm的304大水珠压花不锈钢板,可以耐氧化和酸性腐蚀;这些结构设计大幅增加了烟气和空气的换热系数,比常规列管式空气预热器换热系数增加2倍以上;也使得结构尺寸和设备重量大幅降低,制造也更加简单;最重要的是,也可像锅炉本体受热面一样实现标准化模块化制作,增减负荷只需通过增减平板层数即可。
锅炉本体和节能器11均采用水管结构,汽包12采用横置式,大幅缩小了锅炉水容量,该锅炉水容量与同规格lss型贯流锅炉相比略大1倍左右;与wns型锅炉相比仅为其1/5弱。较小的水容量,使得锅炉产汽速度快,对于长时间间歇运行的锅炉,停炉时能耗相对较小。另外,可在出烟口处设置了烟道蝶阀,由于烟道采用立式几形弯结构,停炉时通过关闭烟道蝶阀,可在烟道内形成热空气塞,减少了热空气从缝隙中流失,从而锁住炉内热量,大幅减少了高温空气从烟囱口排出,降低停炉热损。通过这些设计使得锅炉综合能效大幅提高。
本文用于企业家、创业者技术爱好者查询,结果仅供参考。