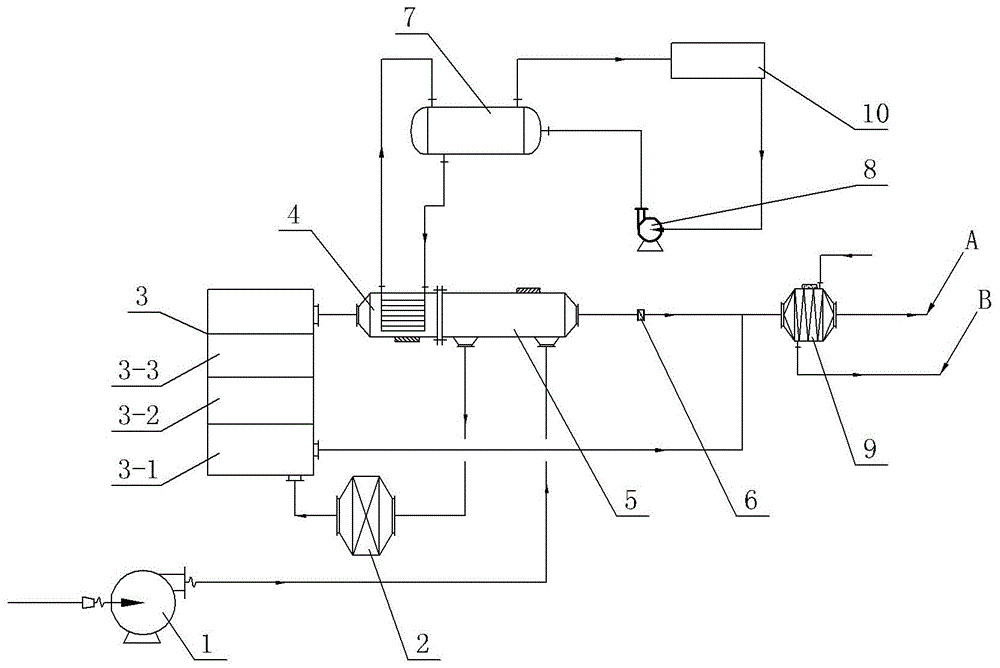
本发明涉及余热回收领域,具体涉及一种废气余热回收方法。
背景技术:
催化氧化工艺在voc废气治理中较为常用,该工艺借助催化剂使有机废气在较低的起燃温度下进行无焰燃烧,使有机废气分解为无毒的二氧化碳和水,达到废气治理的目的。目前,燃烧后的热量由气体带出并与即将燃烧的废气进行换热,回收利用部分热量,存在余热利用率不高的问题。
技术实现要素:
本发明的目的在于提供一种有利于提高废气燃烧后余热利用率的回收方法。
为达到上述目的,本发明的技术方案提供一种废气余热回收方法,包括如下步骤:
步骤1:准备一种废气余热回收系统,包括催化氧化床、余热炉、预热器、换热器和汽包,催化氧化床包括换热段、加热段和催化段,预热器包括废气出口和气体入口,预热器的废气出口、换热段、加热段、催化段、余热炉、预热器的气体入口和换热器依次连通,预热器和换热器之间设有控制阀,汽包和余热炉连通,催化段、换热段和换热器连通;
步骤2:从预热器废气出口出来的废气依次经过换热段、加热段和催化段后,在催化段无焰燃烧,产生高温气体;
步骤3:高温气体进入余热炉后加热从汽包下来的热水转化为蒸汽,蒸汽供外部用汽设备使用后冷凝下来的热水循环回用至汽包;
步骤4:经过余热炉后的气体经预热器的气体入口进入预热器,与废气进行换热,二次回收热量;
步骤5:不需要蒸汽时,关闭控制阀,经过预热器的废气进入催化氧化床,废气在催化段无焰燃烧后产生的高温气体进入换热段,与进入催化氧化床的废气进行换热,回收热能温度降低进入换热器,继续加热换热器内的工业水,制成热水供外部使用。
本方案的技术效果是:1、使用多级回收热能,高温气体在余热炉阶段热交换产生蒸汽,在预热器阶段与废气进行换热,有效的提高了余热的利用率;2、副产出的蒸汽附加值高,可用于外部的用汽设备生产使用;3、可自由切换,当不需要蒸汽时,可通过控制阀对高温气体的流向路径进行切换,并于换热器处副产生热水。
进一步的,步骤1的换热段内设有换热机构,换热机构包括热气管、废气管和两根连接管,热气管倾斜设置,热气管的上端与催化段连通,热气管的下端与换热器连通;废气管转动设置于热气管内,废气管上固定有螺旋片和收集盘,收集盘内设有与废气管连通的收集腔;两根连接管固定设置于换热段内且套设在废气管外,两根连接管各自位于废气管的上下两端;废气管的侧壁和连接管的侧壁均设有能够连通的孔洞,位于下端的连接管的孔洞与预热器连通,位于上端的连接管的孔洞与加热段连通;
步骤5中,废气在催化段无焰燃烧后产生的高温气体进入换热段后进入热气管内随螺旋片流动,将热量传递给废气管;
步骤6:当高温气体流动至收集盘处时,在螺旋片的挤压作用下高温气体被压缩,经过收集盘后高温气体膨胀,高温气体降低温度并将热量传递给废气管;
步骤7:废气管转动的过程中,当废气管上的孔洞与连接管上的孔洞对准连通时,经预热器的废气从废气管的下端喷射进入废气管内吸收高温气体传递给废气管的热量;在废气管继续转动的过程中,当废气管上的孔洞与连接管上的孔洞错开时,经过预热器后的废气被阻断无法进入废气管内;
步骤8:废气在废气管内流动的过程中,废气中的颗粒物进入收集盘的收集腔内。
本方案的技术效果是:气体在催化段无焰燃烧后产生的高温气体从热气管的上端进入热气管内,废气管转动带动螺旋片转动,在螺旋片的导流挤压作用下流动,并充分将热量传递给废气管;当高温气体流动至收集盘处时,由于收集盘与热气管的内侧壁之间形成间隙,高温气体在经过间隙时,在螺旋片的挤压作用下高温气体被压缩,经过收集盘后高温气体膨胀,有利于高温气体降低温度并将热量传递给废气管,相较于现有技术热量交换量更多,换热效率提高了近20%;另外高温气体在螺旋片的挤压作用下快速排出热气管,一方面能够避免失去热量的气体反吸热量,另一方面有利于热气快速排出,避免氧化床的换热段、加热段或催化段发生泄漏。
废气管转动的过程中,当废气管上的孔洞与连接管上的孔洞对准连通时,经预热器的废气从废气管的下端喷射进入废气管内吸收高温气体传递给废气管的热量;在废气管继续转动的过程中,当废气管上的孔洞与连接管上的孔洞错开时,经过预热器后的废气被阻断无法进入废气管内,通过间歇进气使得已经进入废气管内的废气充分吸热,有利于提高废气的燃烧效果;而且废气在废气管内流动的过程中,废气中的颗粒物进入收集盘的收集腔内,也有利于提高废气的燃烧效果。
综上,本申请通过提出“蓄气加压传热”的发明构思,充分提高了换热效率和废气的燃烧效果,同时避免了回收系统出现漏气的情况。
进一步的,步骤2中产生高温气体的温度为350-500℃。本方案的技术效果是:废气依次经过换热段、加热段和催化段后有利于产生后续热能回收需要的高温气体。
进一步的,步骤5中废气在催化段产生的高温气体温度降至120℃进入换热器。本方案的技术效果是:有利于充分提高换热效率。
进一步的,换热机构中位于下端的连接管的孔洞朝下设置,位于上端的连接管的孔洞朝上设置,废气管上下两端的孔洞位于废气管的同一侧。本方案的技术效果是:有利于确保废气在废气管内充分进行热传递后再排出废气管。
进一步的,步骤1中一种废气余热回收系统还包括水泵,水泵与汽包连通。本方案的技术效果是:汽包内产生蒸汽经过用气设备后冷凝成为热水,在水泵的作用下,能及时将热水补充至汽包内。
进一步的,步骤1中热气管的倾斜角度为30°。本方案的技术效果是:更加有利于从废气管下端进入的废气平缓流动。
进一步的,换热机构中收集盘位于废气管的下端。本方案的技术效果是:便于对颗粒物进行收集,同时高温气体膨胀降低温度并将热量传递给废气管后,喷射至废气管内的废气能立即与废气管进行热交换。
进一步的,步骤1中余热炉和预热器制作成为一体。本方案的技术效果是:余热炉与预热器制作成为一体,可减少热量的损失。
进一步的,换热机构中废气管上的螺旋片上下两端稀疏分布,中部密集分布。本方案的技术效果是:便于快速对热气管上端的热气进行导流加压。
附图说明
图1为本发明实施例的框图;
图2为换热机构的示意图。
具体实施方式
下面通过具体实施方式进一步详细说明:
说明书附图中的附图标记包括:风机1、阻火器2、催化氧化床3、换热段3-1、加热段3-2、催化段3-3、余热炉4、预热器5、控制阀6、汽包7、水泵8、换热器9、用汽设备10、伺服电机11、热气管12、废气管13、连接管14、螺旋片15、收集盘16、收集腔17、孔洞18。
实施例一:
一种废气余热回收方法,包括如下步骤:
步骤1:准备如图1所示的一种废气余热回收系统,包括风机1、阻火器2、催化氧化床3、余热炉4、预热器5、换热器9、汽包7、水泵8和管道。预热器5包括废气进口、废气出口、气体入口和气体出口,风机1通过管道与预热器5的废气进口连通,阻火器2通过管道与预热器5的废气出口连通。
催化氧化床3包括换热段3-1、加热段3-2和催化段3-3,阻火器2、换热段3-1、加热段3-2、催化段3-3、余热炉4、预热器5的气体入口和换热器9依次通过管道连通,预热器5和换热器9之间的管道上安装有控制阀6。
汽包7和余热炉4连通形成循环管路,同时汽包7通过管道依次与用汽设备10和热水泵8连通形成循环管路。催化氧化床3的催化段3-3和换热段3-1之间设置有内部通道,即催化段3-3、换热段3-1和换热器9连通。
步骤2:如图1所示,废气由风机1送入预热器5,预热器5废气出口出来的气体经过阻火器2后进入催化氧化床3,催化氧化床3分为换热段3-1、加热段3-2及催化段3-3,气体依次经过后在催化段3-3无焰燃烧,温度350-500℃。
步骤3:从催化氧化床3出来的高温气体进入余热炉4,加热从汽包7下来的热水转化为蒸汽,蒸汽回流至汽包7汽液分离,副产出蒸汽,蒸汽供外部用汽设备10使用后冷凝下来的热水经水泵8循环回用至汽包7。
步骤4:从余热炉4出来的气体进入预热器5与从风机1过来的废气进行换热,二次回收热量,经热量回收的气体从预热器5出来经控制阀6(此时控制阀6处于打开状态)、换热器9后从a所示位置达标排放。
步骤5:不需要蒸汽时,关闭控制阀6;废气由风机1送入预热器5,预热器5出来的气体经过阻火器2后进入催化氧化床3,气体在催化氧化床3的催化段3-3无焰燃烧,温度350-500℃。高温气体通过催化氧化床3内部通道进入换热段3-1与进催化氧化床3的废气进行换热,回收热能温度降至120℃左右进入换热器9,换热器9内设置有盘管,气体继续加热从换热器9上方流入换热器9盘管内的工业水,制成热水从b所示位置排出外供使用;气体自换热器9的壳层排出。
实施例二:
在实施例一的基础上,如图1所示的换热段3-1内设置有换热机构,如图2所示,换热机构包括伺服电机11、热气管12、废气管13和两根连接管14,热气管12通过螺栓倾斜固定设置在换热段3-1内,热气管12的上端通过内部通道与催化段3-3连通,热气管12的下端通过管道与换热器9连通。
伺服电机11通过螺栓固定安装在换热段3-1内,伺服电机11的型号可选用mr-j2s-100a,废气管13的下端与伺服电机11的输出轴焊接,废气管13的上端与催化氧化床3的侧壁转动连接,废气管13转动设置在热气管12内。
废气管13上焊接有螺旋片15和收集盘16,收集盘16内开有与收集腔17,收集腔17与废气管13连通。催化氧化床3的侧壁上焊接有支撑杆,两根连接管14均与支撑杆焊接,而且两根连接管14均套设在废气管13外,即废气管13与两根连接管14转动连接,两根连接管14各自位于废气管13的上下两端。
废气管13的侧壁和连接管14的侧壁均开有能够连通的孔洞18,位于下端的连接管14的孔洞18通过管道与阻火器2连通,位于上端的连接管14的孔洞18通过管道与加热段3-2连通。其中,位于下端的连接管14的孔洞18朝下设置,位于上端的连接管14的孔洞18朝上设置,废气管13上下两端的孔洞18位于废气管13的同一侧,即废气管13转动至如图2所示状态下时,废气管13上下两端的孔洞18均位于废气管13下侧。
步骤5:在实施例一的基础上,不需要蒸汽时,高温气体通过催化氧化床3的内部通道后从热气管12的上端进入热气管12内,伺服电机11带动废气管13转动的过程中带动螺旋片15转动,高温气体在螺旋片15的导流挤压作用下流动,并充分将热量传递给废气管13。
步骤6:当高温气体流动至收集盘16处时,由于收集盘16与热气管12的内侧壁之间形成间隙,高温气体在经过间隙时,在螺旋片15的挤压作用下高温气体被压缩,经过收集盘16后高温气体膨胀,有利于高温气体降低温度并将热量传递给废气管13,相较于现有技术热量交换量更多,换热效率提高了近20%。
另外高温气体在螺旋片15的挤压作用下快速排出热气管12,一方面能够避免失去热量的气体反吸热量,另一方面有利于热气快速排出,避免氧化床的换热段3-1、加热段3-2或催化段3-3发生废气或气体泄漏。
步骤7:废气管13转动的过程中,当废气管13上的孔洞18与连接管14上的孔洞18对准连通时,经阻火器2的废气从废气管13的下端喷射进入废气管13内吸收高温气体传递给废气管13的热量;在废气管13继续转动的过程中,当废气管13上的孔洞18与连接管14上的孔洞18错开时,经过预热器5后的废气被阻断无法进入废气管13内,通过间歇进气使得已经进入废气管13内的废气充分吸热,有利于提高废气的燃烧效果。
步骤8:废气在废气管13内流动的过程中,废气中的颗粒物进入收集盘16的收集腔17内进行收集,也有利于提高废气的燃烧效果。
实施例三:
在实施例二的基础上,如图2所示,本实施例中热气管12的倾斜角度为30°,收集盘16位于废气管13的下端,同时废气管13上下两端的螺旋片15分布更为稀疏,废气管13中部的螺旋片15的间距分布更为密集。另外如图1所示,余热炉4和预热器5制作成为一体,即余热炉4的尾部和预热器5的气体入口直接焊接并连通。
以上所述的仅是本发明的实施例,方案中公知的具体结构及特性等常识在此未作过多描述。应当指出,对于本领域的技术人员来说,在不脱离本发明结构的前提下,还可以作出若干变形和改进,这些也应该视为本发明的保护范围,这些都不会影响本发明实施的效果和专利的实用性。
本文用于企业家、创业者技术爱好者查询,结果仅供参考。