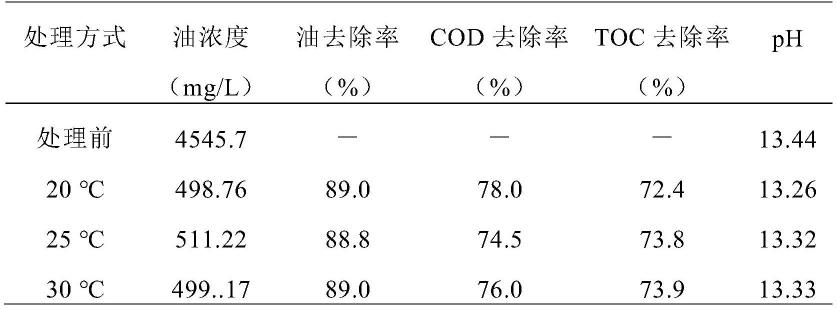
1.本发明属于水处理技术领域,尤其涉及一种用于油水分离的超润湿性材料及其制备方法和应用,该用于油水分离的超润湿性材料耐强碱,可用于纳乳液的油水两相分离。
背景技术:
2.含油乳化液废水有恶化水质、危害人体健康、污染环境和影响自然景观的严重问题,世界上各国都对排放废水含油浓度做出规定和限制,我国规定含油废水最高允许排放的质量浓度是10mg/l,而轧钢厂最新排放指标为小于1mg/l;其中所谓乳化液,就是一种液相以细小液滴的形式分布于另一种液相中,形成两种液相组成的足够稳定的系统,将其称之为乳化液。浓含油废水处理的难易程度随其来源及油污的状态和组成不同而有差异,其处理手段大体为以物理方法分离,以化学法去除,以生物法降解。
3.在冷轧生产过程中,碱洗处理采用强碱性的复合碱洗液,通常由浓度在25
±
5g/l的naoh和一定浓度的具有表面活性功能的混合脱脂剂按一定比例配置而成的强碱溶液。该强碱溶液用于清洗钢板表面的残油和残铁,为了保证清洗效果,naoh和表面活性剂过量投加,清洗后产生的碱洗废液即为一种浓含油废水,因混合脱脂剂的存在,油脂(水解及未水解组分)将以稳定的水包油乳液形式稳定分散于其中,且油滴粒径极小,为纳米级,为纳乳液形态,这就进一步造成了碱洗液中油类物质的难以去除,同时因其强碱性的环境,对处理设备的材料选择带来了一定的挑战。碱洗废液中的主要污染物是悬浮物和油,将这两种污染物取出后,碱洗废液可回用至碱洗环节,将过量投加的naoh和表面活性剂循环利用,达到资源回收目的;对碱洗废液这种强碱性纳乳液的源头净化回用的必要性业内已经达成共识,并尝试了多种处理工艺,均是对现有成熟水处理技术的组合叠加,如磁性分离器 超滤,斜板沉淀 微滤,转毂式磁性过滤 高速离心分离等组合工艺的。
4.近年来,随着超润湿材料的研究和制备的进步,该技术发展成为一种新型高效分离技术,并逐步得到废水处理领域的重视,用于含油废水的油水分离处理。目前,可用于废水中油水分离超润湿材料主要包括:超亲水/水下超疏油材料、超亲油/超疏水材料、超疏水/超疏油材料、响应性超润湿材料等。其中,具有超亲水/水下超疏油性和超亲油/超疏水性的两类超润湿材料可对水相和油相表现出截然相反的亲和性,是分离油水混合物和油水乳液的最具潜力的新材料。其中,超亲水/水下超疏油材料可分散于水相中,主要用于分离水包油乳液,而超亲油/超疏水材料可分散于油相中,主要用于分离油包水乳液。然而,上述超亲水和超亲油材料仅能对含有单一表面活性剂稳定的乳液进行分离,而对含有混合脱脂剂等复合表面活性组分的高稳定性微乳液和纳乳液难以分离。同时超润湿材料的机械强度、循环使用性、耐性也直接影响其工业应用前景。
5.现有技术中,关于超润湿材料的相关研究如下:
6.申请号201810782001.4公开了一种超疏水海绵的制备方法及其在油包水乳液分离中的应用,利用胺与丙烯酸酯基团之间的1,4-共轭加成反应,在海绵表面构造微纳米复合物,随后与含有胺基的长链烷烃反应,降低材料的表面能,从而获得具有超疏水特性的海
绵材料;通过机械挤压的方式,有效降低了海绵材料的孔径,满足了乳液油水分离对于孔径的要求;与蠕动泵相结合,实现了仅依靠重力驱动的连续式乳液油水分离,分离效率高达99.90%以上,通量高达55000
±
5000l m-2
h-1
bar-1
;该技术的超润湿材料基底为海绵,海绵为无定形固体,机械强度差容易形变,不适合工程化的长期应用,海绵的耐强碱性能较弱,在强碱环境下使用寿命有限,且该材料在纳乳液领域的应用效果有待确认。
7.申请号201810693339.2公开了一种可同时用于乳液分离、染料吸附和烟雾吸附的多功能纸的制备方法,包括如下步骤:(1)羟基磷灰石纳米线的制备:分别取氯化钙的水溶液,氢氧化钠的水溶液,在室温下边搅拌边逐滴加入到无水乙醇和油酸的混合溶液中,接着向上述溶液中逐滴加入磷酸二氢钠的水溶液,搅拌均匀后,形成乳白色的粘稠液体,然后将上述溶液混合物转移到反应釜中,置于温度为180℃的条件下反应24h,反应后冷却至室温,经过离心,然后反复分别用无水乙醇和去离子水搅拌洗涤3次,之后将羟基磷灰石纳米线分散在去离子水中备用,从而完成羟基磷灰石纳米线的制备;(2)羟基磷灰石纳米线的增韧:取羧甲基纤维素在室温连续搅拌下加入到100ml的去离子水中,超声0.5~1h后得到粘稠的羧甲基纤维素溶液,取一定量的羧甲基纤维素溶液加入到步骤1溶液中,搅拌6~8h,从而完成强度较好的羟基磷灰石纳米线的制备;(3)金属有机骨架纳米颗粒的掺杂:取四氯化锆粉末加入到n,n二甲基甲酰胺和浓盐酸的混合溶液中,超声10~20min,取有机配体加入到20ml n,n二甲基甲酰胺溶液中,待溶解完成后加入到混有四氯化锆的混合溶液中继续超声10~20min,然后将上述溶液混合物转移到反应釜中,置于温度为80℃的条件下反应24h.反应后冷却至室温,经过离心,然后反复分别用n,n二甲基甲酰胺和无水乙醇搅拌洗涤3次,之后进行真空抽滤,粉末在真空干燥箱中80℃中干燥12h后备用,取金属有机骨架粉末加入到步骤2的混合溶液中,搅拌6~8h,之后进行真空抽滤,在真空干燥箱60℃干燥24h,完成多功能纸的制备;该技术制备的一种吸附用纸,吸附饱和后即抛弃,无法重复循环利用,耐碱性也较差。
8.申请号201910946637.2公开了一种基于喷涂的用于高效收集水雾的混合亲疏水材料表面的制备方法包括磷酸铝无机粘结剂的合成、二氧化锆纳米颗粒和氧化亚铜微粒的喷涂、低表面能物质长烷烃链硫醇的选择性修饰、水雾收集等步骤;该技术基于无机粘结剂可复合多种粒子在多种基底材料表面构筑稳定耐磨的超疏水、超亲水和亲疏水相间材料表面,采用简单的喷涂方法和十八烷基硫醇选择性修饰的方式在不锈钢网上成功制备出超亲水-超疏水混合材料表面。该技术虽属于超润湿材料制备领域,但其设计的目的为从大气中收集水,不用于在油水混合体系中的油水两相分离,不属于油水分离领域和水处理领域。
9.申请号201911269559.3公开了一种超强机械性能的超疏水油漆,由以下质量份的原料制得:环氧树脂1~10份,聚乙二醇0.4~2.4份,二氧化钛1~2.5份,1h,1h,2h,2h-全氟辛基三乙氧基硅烷1.6~5份,聚(n-异丙基丙烯酰胺)0.02~0.12份,氟硅烷0.1~1.2份,固化剂0.2~1.2份;该技术还提供了超疏水油漆的制备方法,通过磁力搅拌、超声处理制得;该技术虽属于超润湿材料制备领域,但不用于在油水混合体系中的油水两相分离,不属于水处理领域。
10.鉴于上述对强碱性纳乳液型废液处理的必要性和紧迫性,弥补现有超润湿材料在适用性上的缺陷和不足,迫切需要开发出一种对纳米油滴处理效果好,再生简单,耐受强碱,并有工业应用前景的超润湿材料,作为配套技术,配合实现碱洗废液的预处理回用。
技术实现要素:
11.针对现有技术中存在的上述缺陷,本发明的目的是提供一种用于油水分离的超润湿性材料及其制备方法和应用,在碱洗废液物理除油方法研究的过程中总结产生的,弥补现有材料在适用性的缺陷和不足;该超润湿性材料能在氢氧化钠含量在15%-25%的强碱环境下,从油滴粒径纳米级的油水混合乳化液中分离出油分,具有耐强碱、机械强度高、用重复使用、油水分离灵敏度高的特点,对纳乳液中的油去除效率高,从而使碱洗废液实现资源回用。
12.为实现上述目的,本发明采用如下技术方案:
13.本发明的第一方面提供了一种用于油水分离的超润湿性材料的制备方法,包括以下步骤:
14.(1)胶粘剂的制备:经超声洗涤、烘干处理后的石英砂与氢氧化钠、苯乙烯混合后,在反应釜中合成胶粘剂;
15.(2)复合瓷粉的制备:经超声洗涤、烘干处理后的陶瓷微粉,加入二氧化钛,混匀后得到复合瓷粉;
16.(3)烧结合成:将复合瓷粉加入到胶粘剂中,混合均匀后,在氩气条件下进行烧结处理,合成中间烧结物;
17.(4)亲油表面处理:将清洗后的中间烧结产物置于二甲基二氯硅烷、三氟乙酰胺和四氯化钛的混合试剂中浸泡,再将浸泡后的中间烧结产物进行干燥处理得到超润湿性材料。
18.优选地,所述步骤(1)中:
19.所述烘干处理过程中,烘干温度为105
±
5℃,烘干时间为60-70min;和/或
20.所述石英砂与所述氢氧化钠、苯乙烯的质量比为1:4-6:0.3-0.6;和/或
21.所述反应釜中,反应温度为200-250℃,反应时间为45-60min。
22.优选地,所述步骤(1)、步骤(2)中:所述超声洗涤过程中,采用蒸馏水作为洗涤液,洗涤时间为30-40min,重复3-5次,每次超声洗涤均采用未使用过的蒸馏水。
23.优选地,所述步骤(2)中:
24.所述烘干处理过程中,温度为105
±
5℃,烘干时间为90-100min;和/或
25.所述陶瓷微粉与所述二氧化钛的质量比为3-4:1。
26.优选地,所述步骤(3)中:
27.所述复合瓷粉与所述胶粘剂的质量比为2-3:1;和/或
28.所述烧结处理的温度为500-800℃,烧结时间为60-90min;和/或
29.所述氩气的流量为0.2-0.5l/min;和/或
30.所述中间烧结产物的孔隙度为55-65%,孔径为2.5-5nm。
31.优选地,所述步骤(4)中:
32.所述中间烧结产物的清洗过程中,采用蒸馏水以体积比1:1循环清洗30-40min;和/或
33.所述中间烧结产物与所述混合试剂的体积比为1:3-4;和/或
34.所述混合试剂中,所述二甲基二氯硅烷、三氟乙酰胺与四氯化钛的质量比为4-5:2-3:1;和/或
35.所述浸泡时间为4-5h;和/或
36.所述干燥处理过程中,采用40-50℃的热空气吹扫60-90min。
37.本发明的第二方面提供了一种根据本发明第一方面所述的制备方法制备的用于油水分离的超润湿性材料。
38.本发明的第三方面提供了一种根据本发明第二方面所述的用于油水分离的超润湿性材料在油水分离领域的应用。
39.优选地,采用所述用于油水分离的超润湿性材料以浸润的方式对强碱性纳乳液进行油水分离处理。
40.优选地,所述强碱性纳乳液经所述油水分离处理处理后,油的去除率≥88%。
41.本发明所提供的一种用于油水分离的超润湿性材料及其制备方法和应用,还具有以下几点有益效果:
42.1、本发明的用于油水分离的超润湿性材料能在氢氧化钠含量在15%-25%的强碱环境下,从油滴粒径纳米级的油水混合乳化液中分离出油分,具有耐强碱、机械强度高、用重复使用、油水分离灵敏度高的特点,对纳乳液中的油去除效率高,从而使碱洗废液实现资源回用;
43.2、本发明的用于油水分离的超润湿性材料,在碱洗废液物理除油方法研究的过程中总结产生的,弥补现有材料在适用性的缺陷和不足,该超润湿性材料能适应强碱环境,对纳乳液中的油去除效率高,从而使得碱洗废液实现资源回用。
具体实施方式
44.为了能更好地理解本发明的上述技术方案,下面结合实施例进一步说明本发明的技术方案。
45.本发明所提供的用于油水分离的超润湿性材料的制备方法,包括以下步骤:
46.(1)胶粘剂的制备:经超声洗涤、烘干处理后的石英砂与氢氧化钠、苯乙烯混合后,在反应釜中合成胶粘剂;
47.具体过程为:首先对石英砂进行处理,采用蒸馏水作为洗涤剂对石英砂进行超声洗涤,其中石英砂的质量与蒸馏水体积之间的比值满足≤0.3g/ml(比如30g石英砂采用100ml蒸馏水洗涤),控制洗涤时间为30-40min,重复3-5次,每次超声洗涤均采用未使用过的蒸馏水;再将超声洗涤后的石英砂置于烘箱中进行烘干处理,控制烘干温度为105
±
5℃,烘干时间为60-70min;然后将洗净烘干后的石英砂,与化学纯氢氧化钠、苯乙烯以质量比为1:4-6:0.3-0.6混合,在反应釜中以200-250℃的反应温度反应45-60min,合成粘稠混合物,即为超润湿材料制备所用的胶粘剂。
48.(2)复合瓷粉的制备:经超声洗涤、烘干处理后的陶瓷微粉,加入二氧化钛,混匀后得到复合瓷粉;
49.具体过程为:首先对陶瓷微粉进行处理,采用蒸馏水作为洗涤剂对陶瓷微粉进行超声洗涤,其中陶瓷微粉的质量与蒸馏水体积之间的比值满足<0.35g/ml(比如50g陶瓷微粉采用150ml蒸馏水洗涤),控制洗涤时间为30-40min,重复3-5次,每次超声洗涤均采用未使用过的蒸馏水;再将超声洗涤后的陶瓷微粉置于烘箱中进行烘干处理,控制烘干温度为105
±
5℃,烘干时间为90-100min;然后在洗净烘干后的陶瓷微粉中,加入二氧化钛,混匀后
得到复合瓷粉,其中陶瓷微粉与二氧化钛的质量比为3-4:1。
50.(3)烧结合成:将复合瓷粉加入到胶粘剂中,混合均匀后,在氩气条件下进行烧结处理,合成中间烧结物;
51.具体过程为:将复合瓷粉加入到胶粘剂中,控制复合瓷粉与胶粘剂的质量比为2-3:1,混合均匀后,在500-800℃的温度下进行烧结处理,在烧结的同时,以0.2-0.5l/min的流量导入氩气,在此烧结条件下,控制烧结时间为60-90min;烧结处理结束后,合成整块筒状产物,即为中间烧结产物,其孔隙度为55-65%,孔径为2.5-5nm。
52.(4)亲油表面处理:将清洗后的中间烧结产物置于二甲基二氯硅烷、三氟乙酰胺和四氯化钛的混合试剂中浸泡,再将浸泡后的中间烧结产物进行干燥处理得到超润湿性材料。
53.具体过程为:首先对中间烧结产物进行清洗,采用蒸馏水以体积比为1:1,循环清洗30-40min,然后将洗净的中间烧结产物置于二甲基二氯硅烷、三氟乙酰胺和四氯化钛的混合试剂中浸泡,在室温下浸泡4-5h,其中混合试剂中二甲基二氯硅烷、三氟乙酰胺和四氯化钛的质量比为4-5:2-3:1,中间烧结产物与混合试剂的体积比为1:3-4;之后再将浸泡后的中间烧结产物进行干燥处理,采用40-50℃的热空气吹扫60-90min吹至中间烧结产物干燥,即可得到用于油水分离的超润湿性材料。
54.上述制备的用于油水分离的超润湿性材料在油水分离领域中应用,尤其是在强碱性纳乳液(纳乳液是指油脂以稳定的水包油乳液形式稳定分散于其中,且油滴粒径极小,为纳米级)中应用,在具体使用时,将用于油水分离的超润湿性材料以浸润的方式对强碱性纳乳液进行油水分离处理,强碱性纳乳液经油水分离处理处理后,油的去除率≥88%,cod去除率≥74%,toc去除率≥72%。
55.下面结合具体的例子对本发明的一种用于油水分离的超润湿性材料及其制备方法和应用进一步介绍;
56.实施例1
57.本实施例中用于油水分离的超润湿性材料通过以下步骤制备而成:
58.(1)胶粘剂的制备:取30g石英砂,使用100ml蒸馏水超声洗涤30min,然后更换未使用的蒸馏水再重复清洗2次,将清洗后的石英砂置于烘箱105
±
5℃、60min烘干备用;然后取洗净烘干的石英砂,与化学纯氢氧化钠、苯乙烯以质量比为1:4:0.3混合,在反应釜中以200℃的反应温度反应45min,合成粘稠混合物,即为超润湿材料制备所用的胶粘剂。
59.(2)复合瓷粉的制备:取陶瓷微粉50g,使用150ml蒸馏水超声清洗30min,然后更换未使用的蒸馏水再重复清洗2次,将清洗后的陶瓷微粉置于烘箱105
±
5℃、60min烘干备用。然后在洗净干燥后的陶瓷微粉中,加入二氧化钛,投加陶瓷微粉与二氧化钛的质量比为3:1,混匀后得到复合瓷粉,备用。
60.(3)烧结合成:将复合瓷粉以质量比为2:1加入胶粘剂中,混合均匀后,在500℃的温度下进行烧结,在烧结的同时,以0.2l/min的流量导入氩气,在此烧结条件下,控制烧结时间为60min;烧结处理结束后,合成整块筒状产物,即为中间烧结产物,其孔隙度55%,孔径分布2.5nm。
61.(4)亲油表面处理:采用蒸馏水以体积比为1:1对中间烧结产物进行清洗,循环清洗30min;然后将洗净的中间烧结产物置于二甲基二氯硅烷、三氟乙酰胺和四氯化钛质量比
为5:2:1的混合试剂中浸泡,在常温下浸泡4-5h,烧结产物和混合试剂体积比为1:3。浸泡完成后取出中间烧结产物后进行干燥处理,使用40℃的热空气吹扫60min,将中间烧结产物吹至干燥,即可得到本实施例的用于油水分离的超润湿性材料。
62.实施例2
63.本实施例中用于油水分离的超润湿性材料通过以下步骤制备而成:
64.(1)胶粘剂的制备:取30g石英砂,使用100ml蒸馏水超声洗涤40min,然后更换未使用的蒸馏水再重复清洗4次,将清洗后的石英砂置于烘箱105
±
5℃、70min烘干备用;然后取洗净烘干的石英砂,与化学纯氢氧化钠、苯乙烯以质量比为1:6:0.6混合,在反应釜中以250℃的反应温度反应60min,合成粘稠混合物,即为超润湿材料制备所用的胶粘剂。
65.(2)复合瓷粉的制备:取陶瓷微粉50g,使用150ml蒸馏水超声清洗40min,然后更换未使用的蒸馏水再重复清洗4次,将清洗后的陶瓷微粉置于烘箱105
±
5℃、70min烘干备用。然后在洗净干燥后的陶瓷微粉中,加入二氧化钛,投加陶瓷微粉与二氧化钛的质量比为4:1,混匀后得到复合瓷粉,备用。
66.(3)烧结合成:将复合瓷粉以质量比为3:1加入胶粘剂中,混合均匀后,在500-800℃的温度下进行烧结,在烧结的同时,以0.5l/min的流量导入氩气,在此烧结条件下,控制烧结时间为90min;烧结处理结束后,合成整块筒状产物,即为中间烧结产物,其孔隙度65%,孔径分布5nm。
67.(4)亲油表面处理:采用蒸馏水以体积比为1:1对中间烧结产物进行清洗,循环清洗40min;然后将洗净的中间烧结产物置于二甲基二氯硅烷、三氟乙酰胺和四氯化钛质量比为4:2:1的混合试剂中浸泡,在常温下浸泡4-5h,烧结产物和混合试剂体积比为1:4。浸泡完成后取出中间烧结产物后进行干燥处理,使用50℃的热空气吹扫90min,将中间烧结产物吹至干燥,即可得到本实施例的用于油水分离的超润湿性材料。
68.实施例3
69.本实施例中用于油水分离的超润湿性材料通过以下步骤制备而成:
70.(1)胶粘剂的制备:取30g石英砂,使用100ml蒸馏水超声洗涤35min,然后更换未使用的蒸馏水再重复清洗3次,将清洗后的石英砂置于烘箱105
±
5℃、65min烘干备用;然后取洗净烘干的石英砂,与化学纯氢氧化钠、苯乙烯以质量比为1:5:0.5混合,在反应釜中以230℃的反应温度反应55min,合成粘稠混合物,即为超润湿材料制备所用的胶粘剂。
71.(2)复合瓷粉的制备:取陶瓷微粉50g,使用150ml蒸馏水超声清洗35min,然后更换未使用的蒸馏水再重复清洗3次,将清洗后的陶瓷微粉置于烘箱105
±
5℃、65min烘干备用。然后在洗净干燥后的陶瓷微粉中,加入二氧化钛,投加陶瓷微粉与二氧化钛的质量比为3.5:1,混匀后得到复合瓷粉,备用。
72.(3)烧结合成:将复合瓷粉以质量比为2.5:1加入胶粘剂中,混合均匀后,在500-800℃的温度下进行烧结,在烧结的同时,以0.2-0.5l/min的流量导入氩气,在此烧结条件下,控制烧结时间为60-90min;烧结处理结束后,合成整块筒状产物,即为中间烧结产物,其孔隙度60%,孔径分布4nm。
73.(4)亲油表面处理:采用蒸馏水以体积比为1:1对中间烧结产物进行清洗,循环清洗35min;然后将洗净的中间烧结产物置于二甲基二氯硅烷、三氟乙酰胺和四氯化钛质量比为5:2:1的混合试剂中浸泡,在常温下浸泡4-5h,烧结产物和混合试剂体积比为1:3.5。浸泡
完成后取出中间烧结产物后进行干燥处理,使用45℃的热空气吹扫70min,将中间烧结产物吹至干燥,即可得到本实施例的用于油水分离的超润湿性材料。
74.实施例4
75.本实施例中,取连退机组的强碱浓油废液,即强碱性纳乳液,使用实施例1中制备的用于油水分离的超润湿材料进行处理,在不同温度下,以浸润的方式处理碱洗废液。处理效果如下表1所示,强碱性纳乳液在20℃、25℃和30℃下,经实施例1制备的超润湿材料处理前后的主要污染物浓度变化;结果显示对应的油去除率分别为98.6%、97.9%和98.6%,处理效果稳定,说明温度不影响超润湿材料对强碱性纳乳液的处理效果,处理前后ph无明显影响,保留了有效的碱成分,如现场需要,亦可调和后回用至生产段。
76.表1强碱性纳乳液处理前后的分析数据
[0077][0078]
其中,表1中的分析方法参照标准废水中油含量检测方法gb/t7490-1987萃取红外分光光度法,高锰酸盐指数(codmn)的测定gb/t 11892-89,废水温度使用水银温度计测定。
[0079]
实施例5
[0080]
本实施例中,取某冷轧机组的强碱浓油废液,即强碱性纳乳液,使用实施例2中制备的用于油水分离的超润湿材料进行浸润处理,分别处理1此、串联处理2此、串联处理3次,进出废液对比分析数据如表2所示,结果显示处理一次即可达到良好的除油效果,多次串联处理亦可提高除油效率,但提高的不明显,如对除油效率要求高,可酌情进行多级串联处理,但多级处理损耗一定的碱度,不利于资源回收利用。
[0081]
表2强碱性纳乳液处理前后的分析数据
[0082][0083]
其中,表2中的分析方法参照标准废水中油含量检测方法gb/t7490-1987萃取红外分光光度法,高锰酸盐指数(codmn)的测定gb/t 11892-89。
[0084]
实施例6
[0085]
本实施例中,取冷轧机组的强碱浓油废液,即强碱性纳乳液,取应用1个月后的实施例3中制备的超润湿材料进行反洗处理,反洗使用50℃工业水,循环清洗3次,对比反洗前后的除油性能的变化。对比数据如下表3所示,结果显示,反洗后的再生材料除油率略有下降,但不明显,可能是清洗不完全的原因,可适当增加清洗次数,或更换新鲜的反洗用水,以提高反洗效率。
[0086]
表3超润湿材料反洗再生材料效果分析数据
[0087][0088]
其中,表3中的分析方法参照标准废水中油含量检测方法gb/t7490-1987萃取红外分光光度法。
[0089]
综上所述,本发明的用于油水分离的超润湿性材料能在氢氧化钠含量在15%-25%的强碱环境下,从油滴粒径纳米级的油水混合乳化液中分离出油分,具有耐强碱、机械强度高、用重复使用、油水分离灵敏度高的特点,对纳乳液中的油去除效率高,从而使碱洗废液实现资源回用;该用于油水分离的超润湿性材料,在碱洗废液物理除油方法研究的过程中总结产生的,弥补现有材料在适用性的缺陷和不足,该超润湿性材料能适应强碱环境,对纳乳液中的油去除效率高,从而使得碱洗废液实现资源回用。
[0090]
本技术领域中的普通技术人员应当认识到,以上的实施例仅是用来说明本发明,而并非用作为对本发明的限定,只要在本发明的实质精神范围内,对以上所述实施例的变化、变型都将落在本发明的权利要求书范围内。
再多了解一些
本文用于创业者技术爱好者查询,仅供学习研究,如用于商业用途,请联系技术所有人。