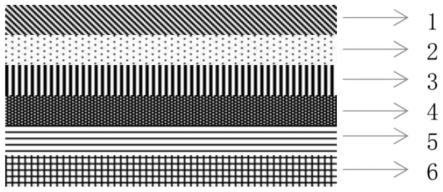
1.本技术涉及保护膜技术领域,具体涉及一种硅胶保护膜及其制备方法和电子产品。
背景技术:
2.近些年来,2.5d、3d手机由于出色的显示效果和使用体验,其在终端市场中的占比越来越大,随之而来,原有2d时代的手机保护膜由于固有缺陷,在贴合这些曲面屏产品时,会出现白边、起翘、贴合不良等问题,已不能满足使用需求,为此人们在原有基础上进行了不同方案的改善。
3.目前常见的解决方案包括以下几种,其一是采用硬化层、pet(polyethylene terephthalate,聚对苯二甲酸乙二醇酯)基材层、压敏胶层结构,贴合前通过热压方式将保护膜进行弯折,提高与曲面屏贴合程度,此方法需要根据手机机型定制模具,并且因为模具精度等问题,实际贴合度不高,贴合后不可避免存在白边、起翘等问题;另外一种常见方法是采用tpu(thermoplastic polyurethanes,热塑性聚氨酯弹性体橡胶)替代原有pet基材,在tpu基材上下两面分别涂布硬化层和压敏胶层,可以有效改善原有pet基材挺度大、不易贴合等问题,但由于tpu基材偏软,使用中存在易划伤等问题。
4.近两年新兴起另外一种方法,采用硬化层、pet基材层、tpu/亚克力层、有机硅压敏胶层,依靠tpu/亚克力层缓冲过渡、光固化定型,从而实现高度贴合。但此结构中tpu和亚克力层耐高温性能稍弱,不利于后续压敏胶层充分固化;同时,tpu/亚克力层与有机硅压敏胶也存在溶剂选择性、附着力不稳定、铂金催化剂中毒风险。此外,tpu/亚克力涂布后大多需要经历熟化,整个生产周期变长,成本相应增加。
技术实现要素:
5.有鉴于此,本发明提供了一种硅胶保护膜及其制备方法和电子产品。该硅胶保护膜防指纹、耐刮伤、易贴合成型,可应用于曲面屏幕贴合保护。
6.为了实现上述发明目的,本发明提供以下技术方案:
7.本发明提供了一种硅胶保护膜,该硅胶保护膜自上而下依次包括硅胶上保层、硬化层、基材层、双固化硅橡胶层、有机硅压敏胶层;
8.其中,硅胶上保层提供对硬化层的保护,防止运输、生产过程中对硬化层的污染和破坏;硬化层提供高硬度和爽滑效果;双固化硅橡胶层为热固化和光固化双重固化体系,通过调节硅氢键与碳碳双键的摩尔比,采用热固化初步成型,后续贴合时再通过光固化完成贴合定型;有机硅压敏胶层实现对af屏良好粘接力。
9.以重量份计,双固化硅橡胶层中各制备原料的用量如下:
[0010][0011]
优选地,以重量份计,双固化硅橡胶层中各制备原料的用量如下:
[0012][0013][0014]
作为优选,乙烯基封端聚硅氧烷的结构式如式i所示:
[0015][0016]
其中,r1为甲基,r2为乙烯基,m为500~5000,n为0~300,乙烯基含量为0.05%~0.8%。
[0017]
优选地,式i中,m为2000~5000,n为10~50,乙烯基含量为0.05%~0.45%。
[0018]
在本发明提供的实施例中,式i中,m为4800,n为30,乙烯基含量为0.24%。
[0019]
作为优选,(甲基)丙烯酰氧丙基改性硅油的结构式如式ii所示:
[0020][0021]
其中,r1为甲基,r3为(甲基)丙烯酰氧丙基,p为200~2000,q为0~500,双键含量为0.5~3.5%。
[0022]
在本发明提供的实施例中,p为1200,q为30,双键含量为0.9%。
[0023]
作为优选,(甲基)丙烯酰氧丙基改性硅树脂为mq/mt硅树脂,其中m和t上具有(甲基)丙烯酰氧丙基,双键含量为1.0%~5.0%,m/q或m/t为0.6~1.2;
[0024]
优选地,(甲基)丙烯酰氧丙基改性硅树脂的双键含量为3.0%~5.0%,m/q或m/t为0.7~1.0。
[0025]
在本发明提供的实施例中,(甲基)丙烯酰氧丙基改性硅树脂的双键含量为3.5%,m/q或m/t为0.75。
[0026]
作为优选,乙烯基mq树脂的乙烯基含量为0.5%~2.0%,m/q为0.6~0.9;
[0027]
在本发明提供的实施例中,乙烯基mq树脂的乙烯基含量为1.2%,m/q为0.65。
[0028]
作为优选,交联剂为端侧含氢硅油,端侧含氢硅油的含氢量为0.05%~1.2%,粘度为15~75mpa.s;
[0029]
在本发明提供的实施例中,端侧含氢硅油的含氢量为0.2%~0.95%,粘度为15~75mpa.s。
[0030]
作为优选,锚固剂为陶氏锚固剂297;
[0031]
作为优选,附着力添加剂为硅烷偶联剂、钛酸酯增粘剂、硼酸酯增粘剂中的至少一种;在本发明提供的实施例中,附着力添加剂为硅烷偶联剂。
[0032]
作为优选,铂金催化剂为陶氏催化剂dc-4000;
[0033]
作为优选,抑制剂为甲基丁炔醇;
[0034]
作为优选,光引发剂为巴斯夫1173、184、369、651、tpo、907中的至少一种;在本发明提供的实施例中,光引发剂为巴斯夫184。
[0035]
作为优选,稀释溶剂为甲苯和/或乙酸乙酯。
[0036]
对于上述锚固剂、附着力添加剂、铂金催化剂、抑制剂、光引发剂、稀释溶剂的种类并非限定于此,只要是本领域认可的种类,均在本发明的保护范围内。
[0037]
作为优选,双固化硅橡胶层中硅氢键与碳碳双键摩尔比为(0.05~0.5)/1;
[0038]
作为优选,双固化硅橡胶层的厚度为35~90μm。
[0039]
作为优选,硅胶上保层为涂布有硅胶的pet基材,剥离力为1~10gf/in;作为优选,硅胶上保层的厚度为50~70μm;其中,硅胶上保层中硅胶层的厚度为5~15μm。
[0040]
作为优选,硬化层为聚氨酯改性丙烯酸酯。作为优选,硬化层的厚度为2~5μm;
[0041]
作为优选,基材层为pet基材层。作为优选,pet基材层的厚度为15~50μm;硬度为
1-3h,透光率>90%,雾度<1%,水接触角>107
°
,动摩擦系数<0.2;
[0042]
作为优选,有机硅压敏胶层为常规胶水,如陶氏7695、7685等。作为优选,有机硅压敏胶层的厚度为15~45μm;剥离力为300~1200gf/in,对af屏剥离力>20gf/in。
[0043]
作为优选,硅胶保护膜的有机硅压敏胶层之下还包括离型膜层。
[0044]
作为优选,离型膜层为氟素离型膜层。氟素离型膜层实现对有机硅压敏胶层的保护。
[0045]
作为优选,氟素离型膜为透明pet基材的离型膜,厚度为40~60μm,离型力为1~3gf/in。
[0046]
优选地,硅胶保护膜的透光率>90%,雾度<1%,水接触角>107
°
,动摩擦系数<0.2,对af屏剥离力>20gf/in。
[0047]
本发明还提供了上述硅胶保护膜的制备方法,包括如下步骤:
[0048]
将(甲基)丙烯酰氧丙基改性硅树脂、部分稀释溶剂混合,选择添加或不添加乙烯基mq树脂,升温至60~90℃,搅拌1~2h;加入乙烯基封端聚硅氧烷、(甲基)丙烯酰氧丙基改性硅油、抑制剂,搅拌3~5h,得到半成品胶水;将半成品胶水、剩余稀释溶剂、交联剂、锚固剂、附着力添加剂、铂金催化剂、光引发剂混合,得到双固化硅橡胶层浆料;
[0049]
将硬化层与基材层复合,得到复合硬化膜;
[0050]
在复合硬化膜的硬化层表面复合硅胶上保层;
[0051]
将双固化硅橡胶层浆料涂布在复合硬化膜的基材层表面,经第一固化,得到具有双固化硅橡胶层的复合硬化膜;
[0052]
将有机硅压敏胶层复合在复合硬化膜的双固化硅橡胶层表面,经第二固化,得到硅胶保护膜。
[0053]
作为优选,混合时搅拌的转速为200~500r/min。
[0054]
作为优选,半成品胶水、剩余稀释溶剂、交联剂、锚固剂、附着力添加剂、铂金催化剂、光引发剂依次混合,加入的时间间隔为5~10min。
[0055]
优选地,上述制备步骤中,加入光引发剂后需要黄光/避光环境下操作。
[0056]
作为优选,第一固化为在130~150℃下固化0.5~1.5min;
[0057]
作为优选,第二固化为在150~160℃下固化1~2min。
[0058]
作为优选,所述第二固化之后还包括复合离型膜层的步骤。
[0059]
本发明还提供了一种具有曲面屏幕的电子产品,包括上述硅胶保护膜。
[0060]
与现有技术相比,本发明具有的有益效果为:
[0061]
本发明的硅胶保护膜防指纹、耐刮伤、易贴合成型,可应用于曲面屏幕贴合保护。
[0062]
相较于热压方案,本发明硅胶保护膜中双固化硅橡胶层和有机硅压敏胶层可一次工序涂布成型,工艺简单,生产效率高,在使用时,通过冷贴合、光固化定型,具有贴合度好、良率高、不易反弹等优点。
[0063]
相较于其他多层复合结构方案,本发明方案不用熟化,缩短生产周期,胶层涂布时可一次工序完成,效率提高,且可以避免附着力不稳定、固化不良等隐患。
附图说明
[0064]
图1为本发明保护膜的结构示意图。
[0065]
附图中:1-硅胶保护膜(上保层),2-硬化层,3-pet基材层,4-双固化硅橡胶层,5-有机硅压敏胶层,6-氟素离型膜层。
具体实施方式
[0066]
本发明公开了一种硅胶保护膜及其制备方法和电子产品,本领域技术人员可以借鉴本文内容,适当改进工艺参数实现。特别需要指出的是,所有类似的替换和改动对本领域技术人员来说是显而易见的,它们都被视为包括在本发明。本发明的方法及应用已经通过较佳实施例进行了描述,相关人员明显能在不脱离本发明内容、精神和范围内对本文所述的方法和应用进行改动或适当变更与组合,来实现和应用本发明技术。
[0067]
本发明中所用试剂、仪器或材料等均可通过商业渠道获得。
[0068]
下面结合实施例,进一步阐述本发明:
[0069]
实施例1
[0070]
如图1所示,自上而下,本发明实施例硅胶保护膜各层及其厚度如下:
[0071]
硅胶上保层60μm,硬化层3μm,pet基材层23μm,双固化硅橡胶层70μm,有机硅压敏胶层30μm,氟素离型膜层50μm。
[0072]
本发明实施例保护膜制备方法如下:
[0073]
(1)双固化硅橡胶的制备
[0074]
在不锈钢反应釜中依次加入10份乙烯基mq树脂、40份(甲基)丙烯酰氧丙基改性硅树脂、200份甲苯,200-500r/min,升温至75℃搅拌1h,加入100份乙烯基封端聚硅氧烷、50份(甲基)丙烯酰氧丙基改性硅油、0.3份抑制剂,继续搅拌3-5h,冷却降温,取上述半成品胶水,200-500r/min搅拌速度,依次加入200份溶剂(甲苯:乙酸乙酯的体积比为1:1)、1.5份含氢量为0.65%的交联剂、2.0份锚固剂、3.0份附着力添加剂、4.0份铂金催化剂、4.0份光引发剂,加入间隔为5-10min,之后避光环境下操作。
[0075]
(2)硅胶保护膜的制备
[0076]
1)采用微凹涂布方法,在50μm pet基材的电晕面涂布硅胶,固化时需采用梯度升温,且保障在150℃下保持1min,使其充分固化,最终干胶厚度控制在10μm,得到硅胶上保层;
[0077]
2)采用微凹辊在pet基材层上涂布硬化涂层,先热固后光固,控制光固化能量,硬度控制在1-3h,水滴角≥108
°
,涂布厚度控制在3μm,得到复合硬化膜;
[0078]
将硅胶上保层复合在复合硬化膜的硬化面(pet基材表面),收卷;
[0079]
3)采用刮刀或slot die涂布方法,在上述硬化膜背离上保层面涂布前述步骤制备的双固化硅橡胶,固化时保障在135℃下保持1min,再经过第二涂布头,在上述双固化硅橡胶表面涂布有机硅压敏胶层,采用梯度升温,保障在160℃下保持2min,使胶层能够充分固化,最终双固化硅橡胶厚度为70μm,压敏胶层厚度为30μm,再复合上氟素离型膜,收卷,得到半成品硅胶保护膜;
[0080]
4)将上述保护膜经模切、贴合、uv光照后完全固化贴合。
[0081]
实施例2
[0082]
本发明实施例硅胶保护膜各层厚度如下:
[0083]
上保层60μm,硬化层3μm,pet基材层15μm,双固化硅橡胶层40μm,有机硅压敏胶层
20μm,氟素离型膜层50μm。
[0084]
双固化硅橡胶和硅胶保护膜制备方法与实施例1相同。
[0085]
实施例3
[0086]
本发明实施例硅胶保护膜各层厚度与实施例1相同。
[0087]
其中,双固化硅橡胶原料组成及制备方法如下:
[0088]
在不锈钢反应釜中依次加入30份乙烯基mq树脂、60份(甲基)丙烯酰氧丙基改性硅树脂、200份甲苯,200-500r/min,升温至75℃搅拌1h,加入70份乙烯基封端聚硅氧烷、40份(甲基)丙烯酰氧丙基改性硅油、0.3份抑制剂,继续搅拌3-5h,冷却降温,取上述半成品胶水,200-500r/min搅拌速度,依次加入200份溶剂(甲苯:乙酸乙酯的体积比为1:1)、2.5份含氢量为0.90%的交联剂、2.0份锚固剂、3.0份附着力添加剂、4.0份铂金催化剂、5.0份光引发剂,加入间隔为5-10min。
[0089]
发明实施例制备方法与实施例1相同。
[0090]
实施例4
[0091]
本发明实施例硅胶保护膜各层厚度如下:
[0092]
上保层60μm,硬化层2μm,pet基材层23μm,双固化硅橡胶层40μm,有机硅压敏胶层30μm,氟素离型膜层50μm。
[0093]
双固化硅橡胶原料不包括乙烯基mq树脂。
[0094]
其中,双固化硅橡胶原料组成及制备方法如下:
[0095]
在不锈钢反应釜中依次加入20份(甲基)丙烯酰氧丙基改性硅树脂、200份甲苯,200-500r/min,升温至75℃搅拌1h,加入120份乙烯基封端聚硅氧烷、60份(甲基)丙烯酰氧丙基改性硅油、0.3份抑制剂,继续搅拌3-5h,冷却降温,取上述半成品胶水,200-500r/min搅拌速度,依次加入200份溶剂(甲苯:乙酸乙酯的体积比为1:1)、1.5份含氢量为0.55%的交联剂、2.5份锚固剂、2.5份附着力添加剂、3.0份铂金催化剂、3.0份光引发剂,加入间隔为5-10min。
[0096]
发明实施例制备方法与实施例1相同。
[0097]
对比例1
[0098]
本对比例结构如下:
[0099]
上保层60μm,硬化层3μm,pet基材层100μm,有机硅压敏胶层35μm,氟素离型膜层50μm。
[0100]
本对比例为热压工艺,使用时通过热压模具将保护膜压合成所需形状,完成贴合。
[0101]
对比例2
[0102]
本对比例为多层复合结构,其中,双固化定型胶层为热固和光固双固化体系,结构如下:
[0103]
上保层60μm,硬化层3μm,pet基材层23μm,双固化定型胶层(亚克力材料)60μm,硅胶层30μm,氟素离型膜50μm。
[0104]
贴合工艺同本发明实施例1。
[0105]
测试例
[0106]
将上述实施例和对比例制备的保护膜进行性能测试,性能测试项目包括铅笔硬度、耐刮擦/2000次来回、室温3d贴合度、室温15d贴合度、70℃*3d贴合度、双85*3d贴合度
(“双85”即温度85℃、湿度85%rh)、水煮2h测试、模切测试、透光率、雾度和af屏剥离力。具体测试方法如下:
[0107]
(1)铅笔硬度测试:采用手摇式铅笔硬度测试仪进行测试,测试标准参照gb/t-6739-2006,测试方法是将保护膜的有机硅压敏胶层贴在玻璃板上,使用9h-6b铅笔进行操作。
[0108]
(2)耐刮擦测试:钢丝绒耐磨测试采用酒精耐摩擦测试仪进行测试,将样片制备为50mm
×
50mm大小固定在测试台,将0000级钢丝绒缠绕在20mm
×
20mm大小的摩擦头上,施加1000g砝码循环2000次观察表面划伤状态。
[0109]
(3)翘曲性(贴合性)测试:将样片制备为75mm
×
160mm大小,完全贴合手机屏幕后,进行相应条件的实验测试,观察是否出现翘起、有无白边等现象。
[0110]
(4)水煮2h测试:将保护膜放入蒸馏水中,连续煮沸2小时后取出,划百格、手搓。观察是否出现脱胶现象。
[0111]
(5)模切测试:模切过程中观察边缘位置溢胶情况。
[0112]
(6)透光率、雾度:采用雾度计进行测试。透过率越高,雾度越低,表面光学性能越好。
[0113]
(7)af屏剥离力测试:参照astmd3330测试方法,将钢板用水滴角为115
°
的af屏来代替测试剥离力。
[0114]
测试结果如下:
[0115]
表1
[0116][0117]
由上述测试结果可知,对比例在实贴时,常温下短时间内不会出现翘起和白边问题,但随着时间延长,逐渐出现细白边现象,并且在老化条件出现了严重的翘起和白边问题;实施例中,实施例3由于整体硬度较高,内应力较大,随着老化进行,逐渐出现白边现象,而随着硅橡胶层强度过度减弱(如实施例4),实贴剥离力更高,抗翘曲、抗白边初始效果较好,但随着老化进行,出现了一定程度白边异常,此外由于胶体强度过低,还存在模切溢胶的问题。
[0118]
综合对比发现,实施例1的实际效果更好,此实施例初始热固化时,硅橡胶层硬度适中,压敏胶层粘接力大,使用时,可进行快速贴合,随后通过uv光照射固化,此时,硅橡胶层中残留的大量光固化基团可进行快速二次固化定型,此过程中,软硬适中的硅橡胶层在尽可能控制内应力产生的同时,保障保护膜整体定型,减少压敏胶层受力程度,避免起翘和白边的发生。
[0119]
以上所述仅是本发明的优选实施方式,应当指出,对于本技术领域的普通技术人员来说,在不脱离本发明原理的前提下,还可以做出若干改进和润饰,这些改进和润饰也应视为本发明的保护范围。
再多了解一些
本文用于创业者技术爱好者查询,仅供学习研究,如用于商业用途,请联系技术所有人。