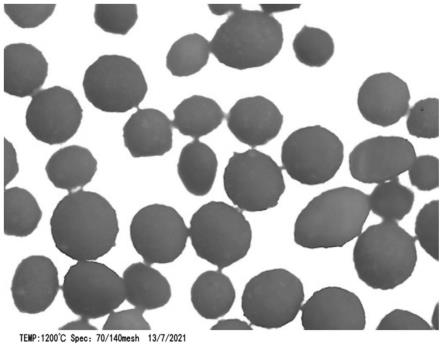
1.本发明涉及油气田井下水力压裂用陶粒支撑剂的制备技术,具体涉及一种利用煤矸石为原料的低密度高强度陶粒支撑剂及其制备方法。
背景技术:
2.压裂用陶粒支撑剂是石油、天然气工业水力压裂过程中,随压裂液一起泵入到地层裂缝中起支撑裂缝、增大油气导流率的专用材料。石油天然气深井开采时,高闭合压力低渗透性矿床经压裂处理后,使含油气岩层裂开,油气从裂缝形成的通道中汇集而出;陶粒支撑材料随同高压溶液进入地层充填在岩层裂隙中,起到支撑裂隙不因应力释放而闭合的作用,从而保持高导流能力,使油气畅通,增加产量30~50%,延长油气井服务年限。
3.现有的压裂用陶粒支撑剂主要分为三类:陶粒、石英砂和树脂包砂。
4.石英砂强度低并且破裂后的碎屑会堵塞裂缝,降低导流率,不能满足深井开采的要求,其主要用于浅层油气井。各种树脂包砂解决了石英砂强度低的难题,但生产成本高,工艺复杂,所以很少使用。烧结陶粒因强度高、化学稳定性好、优越的性价比已被越来越多的油田广泛采用,主要用于深层油气井,但密度偏高,对压裂设备、压裂携带液要求高,施工成本高。
5.传统人工制备压裂用陶粒支撑剂的主要原材料是铝土矿或高岭土。虽然我国矿产资源比较丰富,储量高;但随着国家加大页岩气开发力度,造成陶粒支撑剂的大量需求,原材料价位不断高升,生产成本不断上涨,间接导致油气开采压裂施工成本增加,且铝土矿也成为一种紧缺资源。
6.煤矸石是来源于煤炭开采和洗选过程中产生的固体废物,约占煤炭产量的10%-20%,是我国最主要的固体废弃物之一。目前我国煤矸石已累计堆存达50亿吨以上,但还没有行之有效的处理方式,主要用作井下充填、铺路、制作土壤改良剂、做建筑材料和发电等。煤矸石作为四川攀枝花市排放量最大的工业固体废弃物之一,据初步统计已累计堆积近1.2亿万吨,并以每年150万-180万吨速度递增,占用大量土地,造成环境污染。在煤矸石再利用方面,攀枝花通过再次洗选、矸石发电、生产低端建材和水泥掺和料等途径,年均消耗量不足100万吨,而且普遍存在技术含量不高、附加值低、经济效益不明显等问题,同时还存在二次污染的风险。大量的煤矸石若不处理加以利用,不仅占用土地资源,导致资源浪费,对生态环境和地表水也造成了较大的破坏和污染。
7.cn105906318a公开了一种利用煤矸石制备低密度陶粒支撑剂及其制备方法。其原料组成为:煤矸石75~90%,砂土10~25%,该制备工艺是按一定质量百分比称取煤矸石和砂土进行混料,然后加入适量粘结剂,在糖衣锅或爱立许强力搅拌机中成球,最后于硅钼棒箱式炉或回转窑1100~1200℃之间烧结,冷却后过筛,即得到具有一定粒度分布的低密度陶粒支撑剂。
8.因此,探索出一条利用煤矸石为原料制备低密度高强度陶粒支撑剂的绿色环保工
艺,从而生产出高附加值、适用于储藏较深的石油页岩气压裂用的陶粒支撑剂,是亟需解决的问题。
技术实现要素:
9.本发明提供一种利用煤矸石为原料的低密度高强度陶粒支撑剂及其制备方法,以解决现有技术利用煤矸石制备的陶粒支撑剂密度高强度低且经济效益不明显,以及原料铝土矿、高岭土资源的紧缺等问题,从而满足低成本高附加值的生产需要,实现资源综合利用。
10.本发明的技术方案如下:
11.一种利用煤矸石为原料的低密度高强度陶粒支撑剂,所述陶粒支撑剂具有以下重量百分比的原料组成:
12.煤矸石:15%-85%,
13.陶瓷土:15%-85%,
14.其中,在所述陶粒支撑剂中,莫来石的含量为30%-60%,石英相含量为25%-40%,其他为非晶体态玻璃相,
15.所述陶粒支撑剂的体积密度为1.2-1.48g/cm3,在86mpa闭合压力下的破碎率为5.3%-8.9%。
16.进一步地,所述煤矸石包含以下重量百分比的组成:al2o3含量为9%-53%,sio2含量为43%-63%,fe2o3含量为3%-9%,k2o含量为1%-6%,tio2含量为2%-9%,其他不可避免的杂质含量为0.5%-2%。
17.进一步地,所述陶瓷土包含以下重量百分比的组成:al2o3含量为16%-38%,sio2含量为45%-62%,fe2o3含量为1%-4%,k2o含量为1%-5%,tio2含量为1%-5%,其他不可避免的杂质含量为0.5%-1%。
18.本发明中,所述煤矸石由于含碳量比较低,含铝量相对较高,主要成分为sio2和al2o3,是陶粒支撑剂的主要成分,其它成分如cao、fe2o3、mgo等可以作为烧结助熔剂和矿化剂,具有广阔的综合利用开发前景;以煤矸石为原料制备低密度、高强度的压裂支撑剂,不仅有利于煤矸石的高值利用,变废为宝,还能够降低陶粒支撑剂的生产成本。
19.本发明还提供一种前述低密度高强度的陶粒支撑剂的制备方法,所述方法包括如下步骤:
20.(1)将煤矸石、陶瓷土分别研磨至粒径小于800目标准筛的筛孔尺寸,得到初始粉料;
21.(2)将所述初始粉料按所述煤矸石:所述陶瓷土的重量百分比含量为:15%-85%:15%-85%,进行均匀混合,得到混合粉料;
22.(3)将所述混合粉料放置于φ4.5制粒机中,添加自来水进行造粒,所述自来水含量为12-14.5重量%;
23.(4)将步骤3制得的球形胚体置于干燥箱中进行烘干,烘干后将所述球形胚体依次通过50目筛和140目筛筛分,得到50目-140目粒径的球形颗粒胚体,所述烘干条件为在120℃-250℃的温度下下烘干处理20min-40min;
24.(5)将步骤4制得的50目-140目粒径的球形颗粒胚体置于回转窑中进行烧结,以5
℃/min的升温速度升温至1000-1300℃,保温1-2h后随炉冷却至室温,最后将得到的所述球形颗粒胚体依次通过70目筛和140目筛筛分,从而获得70目-140目粒径的陶粒支撑剂。
25.进一步地,步骤5中,所述回转窑的长度为55m、直径为3.8m。
26.通过本发明的制备方法制得的陶粒支撑剂,能够满足气田井下水力压裂支撑剂技术要求(sy/t5108-2014、q/sh31400072—2015标准的技术要求),在86mpa闭合压力下破碎率低于9%,体积密度低于1.65g/cm3(高密度≥1.8g/cm3,中密度1.65-1.8g/cm3,低密度≤1.65g/cm3,超低密度≤1.55g/cm3)。
27.陶粒支撑(陶粒支撑剂)随同高压溶液进入地层充填在岩层裂隙中,起到支撑裂隙不因应力释放而闭合的作用,从而保持高导流能力。除了要求高强度外,其圆度及球度也极其重要,因为其基本原理是利用支撑剂颗粒与颗粒之间形成的空隙,在支撑岩石裂缝不闭合的同时利用空隙形成导流能力。空隙的大小及质量取决于支撑剂的圆度和球度,常规的石英砂、树脂包砂其圆度和球度都不能满足气田井下水力压裂支撑剂技术要求(sy/t5108-2014、q/sh31400072—2015标准的技术要求),球度和圆度均要≥0.7。
28.通过本发明的制备方法制得的陶粒支撑剂,区别于目前市售的陶粒支撑剂最显著的一个特征是,本发明的陶粒支撑剂产品的球度和圆度均在1.0以上,通过sem图片(图1至图3)可以直观地观察到产品外观性能优势。这样高的球度和圆度证明导流能力优于球度和圆度在0.7-0.9区间的陶粒支撑剂(如图4所示),从而可提高井田产量30%左右,且不会因为闭合问题造成井田堵塞,有益于延长井田服务年限。
29.通过本发明制备的陶粒支撑剂解决了传统支撑剂在气田井深部开采时因其破碎率高、体积密度大达不到理想压裂效果等缺陷,不仅降低了气田开采成本,且实现了煤矸石固体废弃物的再利用,达到了资源综合利用的目的,减少了固体废弃物堆积而造成的环境污染和破坏及减少土地占用,具有显著的经济效益和社会效益。
附图说明
30.图1为实施例1的陶粒支撑剂的sem照片;
31.图2为实施例2的陶粒支撑剂的sem照片;
32.图3为实施例3的陶粒支撑剂的sem照片;
33.图4为现有技术中的陶粒支撑剂的两张sem照片。
具体实施方式
34.下面结合实施例对本发明进行详细说明,本实施例在以本发明技术方案为前提下进行实施,给出详细的实施方式和具体的操作过程。
35.实施例1
36.一种利用煤矸石为原料的低密度高强度陶粒支撑剂,所述陶粒支撑剂具有以下重量百分比的原料组成:
37.煤矸石:80%
38.陶瓷土:20%,
39.所述煤矸石包含以下重量百分比的组成::al2o3含量为30.5%,sio2含量为54.5%,fe2o3含量为7%,k2o含量为3%,tio2含量为4%,其他不可避免的杂质含量为1%,
40.所述陶瓷土包含以下重量百分比的组成:al2o3含量为29.4%,sio2含量为59.6%,fe2o3含量为3%,k2o含量为3%,tio2含量为4%,
41.其中,在所述陶粒支撑剂中,莫来石的含量为35.2%,石英相含量为30.3%,其他为非晶体态玻璃相34.5%,
42.实施例1的陶粒支撑剂的制备过程为:
43.(1)将煤矸石、陶瓷土分别研磨至粒径小于800目标准筛的筛孔尺寸,得到初始粉料;
44.(2)将所述初始粉料按所述煤矸石:所述陶瓷土的重量百分比含量为:80%:20%,进行均匀混合,得到混合粉料;
45.(3)将所述混合粉料放置于φ4.5制粒机中,添加自来水进行造粒,所述自来水含量为12重量%;
46.(4)将步骤3制得的球形胚体置于干燥箱中进行烘干,烘干后将所述球形胚体依次通过50目筛和140目筛筛分,得到50目-140目粒径的球形颗粒胚体,所述烘干条件为在120℃-250℃的温度下下烘干处理30min;
47.(5)将步骤4制得的50目-140目粒径的球形颗粒胚体置于长度55m直径3.8m的回转窑中进行烧结,以5℃/min的升温速度升温至1200℃,保温1-2h后随炉冷却至室温,最后将得到的所述球形颗粒胚体依次通过70目筛和140目筛筛分,从而获得70目-140目粒径的陶粒支撑剂。
48.制备的陶粒支撑剂,主要晶相为石英和莫来石,1200℃下煅烧的陶粒支撑剂的体积密度为1.32g/cm3,86mpa闭合压力下破碎率5.6%,球度1.0,圆度1.0(如图1的sem照片所示),视密度3.2g/cm3,浊度(ftu)27.9,酸溶解度6.2%,满足页岩气井使用要求。
49.实施例2
50.一种利用煤矸石为原料的低密度高强度陶粒支撑剂,所述陶粒支撑剂具有以下重量百分比的原料组成:
51.煤矸石:50%,
52.陶瓷土:50%,
53.所述煤矸石包含以下重量百分比的组成:al2o3含量为25.5%,sio2含量为59.5%,fe2o3含量为8%,k2o含量为3%,tio2含量为3%,其他不可避免的杂质含量为1%,
54.陶瓷土原料组成及其重量百分比为:al2o3含量为35.4%,sio2含量为52.6%,fe2o3含量为4%,k2o含量为4%,tio2含量为3%,其他不可避免的杂质含量为1%,
55.其中,在所述陶粒支撑剂中,莫来石的含量为40.4%,石英相含量为32.3%,其他为非晶体态玻璃相27.3%,
56.实施例2的陶粒支撑剂的制备过程为:
57.(1)将煤矸石、陶瓷土分别研磨至粒径小于800目标准筛的筛孔尺寸,得到初始粉料;
58.(2)将所述初始粉料按所述煤矸石:所述陶瓷土的重量百分比含量为:50%:50%,进行均匀混合,得到混合粉料;
59.(3)将所述混合粉料放置于φ4.5制粒机中,添加自来水进行造粒,所述自来水含量为13.5重量%;
60.(4)将步骤3制得的球形胚体置于干燥箱中进行烘干,烘干后将所述球形胚体依次通过50目筛和140目筛筛分,得到50目-140目粒径的球形颗粒胚体,所述烘干条件为在120℃-250℃的温度下下烘干处理30min;
61.(5)将步骤4制得的50目-140目粒径的球形颗粒胚体置于长度55m直径3.8m的回转窑中进行烧结,以5℃/min的升温速度升温至1250℃,保温3h后随炉冷却至室温,最后将得到的所述球形颗粒胚体依次通过70目筛和140目筛筛分,从而获得70目-140目粒径的陶粒支撑剂。
62.制备的陶粒支撑剂,主要晶相为石英和莫来石,1250℃下煅烧的陶粒支撑剂的体积密度为1.22g/cm3,86mpa闭合压力下破碎率5.3%,球度1.2,圆度1.2(如图2的sem照片所示),视密度2.5g/cm3,浊度(ftu)27.9,酸溶解度5.6%,酸溶解度5.6%,满足页岩气井使用要求。
63.实施例3
64.一种利用煤矸石为原料的低密度高强度陶粒支撑剂,所述陶粒支撑剂具有以下重量百分比的原料组成:
65.煤矸石:40%,
66.陶瓷土:60%,
67.所述煤矸石包含以下重量百分比的组成:al2o3含量为25.5%,sio2含量为47.5%,fe2o3含量为7%,k2o含量为3%,tio2含量为3%,其他不可避免的杂质含量为1%,
68.陶瓷土原料组成及其重量百分比为:al2o3含量为26.8%,sio2含量为60.7%,fe2o3含量为3%,k2o含量为5%,tio2含量为4%,其他不可避免的杂质含量为0.5%,
69.其中,在所述陶粒支撑剂中,莫来石的含量为40.4%,石英相含量为32.3%,其他为非晶体态玻璃相27.3%,
70.实施例3的陶粒支撑剂的制备过程为:
71.(1)将煤矸石、陶瓷土分别研磨至粒径小于800目标准筛的筛孔尺寸,得到初始粉料;
72.(2)将所述初始粉料按所述煤矸石:所述陶瓷土的重量百分比含量为:40%:60%,进行均匀混合,得到混合粉料;
73.(3)将所述混合粉料放置于φ4.5制粒机中,添加自来水进行造粒,所述自来水含量为12重量%;
74.(4)将步骤3制得的球形胚体置于干燥箱中进行烘干,烘干后将所述球形胚体依次通过50目筛和140目筛筛分,得到50目-140目粒径的球形颗粒胚体,所述烘干条件为在120℃-250℃的温度下下烘干处理30min;
75.(5)将步骤4制得的50目-140目粒径的球形颗粒胚体置于长度55m直径3.8m的回转窑中进行烧结,以5℃/min的升温速度升温至1300℃,保温2.5h后随炉冷却至室温,最后将得到的所述球形颗粒胚体依次通过70目筛和140目筛筛分,从而获得70目-140目粒径的陶粒支撑剂。
76.制备的陶粒支撑剂,主要晶相为石英和莫来石,1300℃下煅烧的陶粒支撑剂的体积密度为1.34g/cm3,86mpa闭合压力下破碎率6.2%,球度1.0,圆度1.0(如图3的sem照片所示),视密度3.2g/cm3,浊度(ftu)26.6,酸溶解度6.2%,满足页岩气井使用要求。
77.实施例4
78.一种利用煤矸石为原料的低密度高强度陶粒支撑剂,所述陶粒支撑剂具有以下重量百分比的原料组成:
79.煤矸石:60%,
80.陶瓷土:40%,
81.所述煤矸石包含以下重量百分比的组成:al2o3含量为26.5%,sio2含量为46.5%,fe2o3含量为7%,k2o含量为3%,tio2含量为3%,其他不可避免的杂质含量为1%,
82.陶瓷土原料组成及其重量百分比为:al2o3含量为28%,sio2含量为59%,fe2o3含量为3%,k2o含量为5%,tio2含量为4%,其他不可避免的杂质含量为0.5%,
83.其中,在所述陶粒支撑剂中,莫来石的含量为35.2%,石英相含量为30.6%,其他为非晶体态玻璃相34.2%,
84.实施例4的陶粒支撑剂的制备过程为:
85.(1)将煤矸石、陶瓷土分别研磨至粒径小于800目标准筛的筛孔尺寸,得到初始粉料;
86.(2)将所述初始粉料按所述煤矸石:所述陶瓷土的重量百分比含量为:60%:40%,进行均匀混合,得到混合粉料;
87.(3)将所述混合粉料放置于φ4.5制粒机中,添加自来水进行造粒,所述自来水含量为12重量%;
88.(4)将步骤3制得的球形胚体置于干燥箱中进行烘干,烘干后将所述球形胚体依次通过50目筛和140目筛筛分,得到50目-140目粒径的球形颗粒胚体,所述烘干条件为在120℃-250℃的温度下下烘干处理30min;
89.(5)将步骤4制得的50目-140目粒径的球形颗粒胚体置于长度55m直径3.8m的回转窑中进行烧结,以5℃/min的升温速度升温至1250℃,保温3h后随炉冷却至室温,最后将得到的所述球形颗粒胚体依次通过70目筛和140目筛筛分,从而获得70目-140目粒径的陶粒支撑剂。
90.制备的陶粒支撑剂,主要晶相为石英和莫来石,1200℃下煅烧的陶粒支撑剂的体积密度为1.42g/cm3,86mpa闭合压力下破碎率7.6%,球度1.0,圆度1.0,视密度3.8g/cm3,浊度(ftu)28.8,酸溶解度6.5%,满足页岩气井使用要求。
91.以上所述,仅是本发明的较佳实施例而已,并非是对本发明作任何其他形式的限制,而依据本发明的技术实质所作的任何修改或等同变化,仍属于本发明所要求保护的范围。
再多了解一些
本文用于创业者技术爱好者查询,仅供学习研究,如用于商业用途,请联系技术所有人。