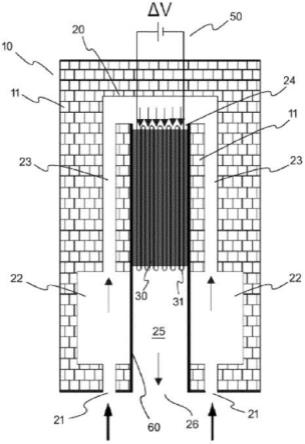
1.本发明涉及一种用于从进料反应性混合物流中生产氢气和/或合成气和/或二氧化碳的反应器壳体,特别涉及一种具有电加热结构化陶瓷催化剂的反应器壳体。本发明还涉及一种使用电阻加热对结构化陶瓷催化剂进行电加热的相关方法。
背景技术:
2.对于数量不足以满足经济条件的所有情况,往往会燃用紧急滞留气体。这些在偏远地区的释放使通过卡车或管道运输不经济。将这种天然气转化为产品(如甲醇、柴油、汽油、溶剂和其他碳氢化合物)是减少二氧化碳(co2)排放的必要机会。用于生产上述液体的所有方法都涉及第一步,其中含甲烷气体经过处理后转化为合成气。
3.另一方面,将氨、液态碳氢化合物以及生物质基产品转化为甲醇、乙醇和沼气或其他含甲烷气体的制氢装置的必要性日益增加。因此,除了大型集中型工厂外,对小型和分布式工厂生产氢气的需求也很大,因为这将改善和促进供应链,否则将依赖于大型生产设施,然后将氢气作为液化或加压气体运输。如果实现了这一点,这种燃料在该地区的广泛使用不仅有利于基于燃料电池的应用,也有利于氢可以用作绿色燃料和/或试剂和/或原料和/或能源载体的所有其他情况。
4.除上文所述外,还越来越有必要清除来自人为工业活动的对流层臭氧水平的任何污染物质。根据欧洲联盟挥发性有机成分(voc)的定义,各国的环境法规在挥发性有机成分(voc)的排放方面不断变得更加严格。必须去除voc,直到浓度通常低于ppm(每百万分之)的必要性,不仅需要传统的氧化火焰或高于自燃的温度,还需要在高于200℃的温度下运行的催化剂。为了达到自动可持续的火焰和/或所需的反应温度,通常会使用额外的燃料,最终有助于增加co2的排放量。在一些申请中,电也被用于达到自燃温度,如us2014/0283812 a1中报告的。
5.2018年,生产和使用的氢气超过7000万吨,主要用于氨生产、精炼工艺和甲醇生产。不同的估计认为,在未来10年内,氢气需求将快速急剧增长,并将翻一番。
6.目前80%以上的可用h2,是通过蒸汽重整(sr)反应(i)使天然气和/或轻质石脑油与蒸汽反应生成的。该反应是高度吸热反应,因此约20%的反应天然气与变压吸附(psa)产生的燃料气一起在重整器中燃烧,以将温度保持在约900℃。剩余部分主要通过非催化部氧化(po)产生,即使涉及放热反应(ii),也需要复杂和昂贵的设备和高于1200℃的温度。
7.ch4 h2o co 3h2(i)
8.ch4 1/2o
2 co 3h2(ii)
9.ch4 co
2 2co 2h2(iii)
10.除sr和po外,生产合成气的一种常见技术是自动热重整(atr),它需要大型且昂贵的气体预热炉、纯氧和高度脱硫的试剂。atr的最终产物是合成气,主要用于甲醇和费托合成。
11.当只使用sr和po,h2是所需的最终产物时,在这两种情况下,所产生的合成气进一
步发生水煤气变换反应(wgs)(iv)。
12.co h2o co2 h2(iv)
13.即使燃烧重整器具有接近50%的能源效率,sr工艺的总体能源效率也高于90%,这可能来自于规模经济的高热回收。
14.补偿反应吸热所需的热量是燃烧甲烷和其他燃料产生的,释放出的co2约占世界排放量的3%。重整器管浸没在燃烧重整器内,靠近燃烧器。在重整器管内,使用负载在陶瓷材料上的镍基催化剂。由于温度高于900℃,催化剂热导率低,以及强烈吸热的sr反应,管的直径从100mm到150mm不等,以限制重整器管内的温度梯度。优化后的重整器管直径保持了强温度梯度,导致催化剂效率因子通常低于10%,需要数百个充满催化剂的重整器管,长度从10m到13m不等。下游的wgs步骤涉及放热的wgs反应。根据催化剂的不同,wgs工艺需要的温度从150℃到400℃。
15.从液体试剂和含甲烷气体作为两步工艺生产氢气的现有技术在试剂组成和生产能力方面灵活性较低。目前的工艺是资本密集型的,当规模经济的热回收无法实现时,它们的能源效率低于60%。除了额外的热交换器,还需要锅炉、反应器、管道、阀门、流量计、配件和容器。此外,工厂的复杂和定制设计以及启动操作降低了工艺灵活性。
16.为解决上述问题,出现了各种尝试。例如,us2013/0028815a1和ep3574991a1公开了电气化金属催化剂载体的应用。然而,不足的比表面积和较差的载体-活性相相互作用导致催化剂稳定性不足。此外,所得宏观结构具有相当大的横截面,降低了电阻,因此需要高电流,这使设计复杂化。由于这些原因,对于高于600℃的温度,没有商用气流加热器使用由金属制成的带电宏观结构。关于结构化金属催化剂用于高温反应的更多细节,也可以在pauletto gianluca等人撰写的“fecrai作为催化剂载体”一文中找到,该文发表于chemicalreviews2020,120,15,p.7516-7550。
17.除上述内容外,有关合成气生产的综合信息也可在jens rostrup nielsen和lars j.christiansen撰写的“合成气制造概念”一书中找到。
18.在过去几年中,将可再生氨裂解为氢气已成为供应可再生氢气的有趣生产途径。特别是可再生能源氨被用作能源载体,在可再生能源高可用性的地方生产。这里,能量被经济地收集并转化为具有高能量密度的并且可以很容易地作为液体运输的化学物质。运输后,高附加值的可再生氨通过催化热化学方法(高于500℃)转化为可再生氢气:氨裂解。需要高效、紧凑、耐腐蚀且价格低廉的模块,以便将可再生氨转化为氢用于燃料电池应用。特别是,电气化氨裂解器最大限度地降低了运行成本,因为它避免了消耗高附加值的可再生氨,以通过在低效率的燃烧炉中燃烧产生热量。
技术实现要素:
19.鉴于现有技术中遇到的上述技术问题,本发明的一个目的是减少投资成本、设备数量、能源消耗、二氧化碳排放以及用于生产氢气、合成气或二氧化碳的反应器的尺寸。
20.本发明的另一目的是提供一种用于生产氢气、合成气或二氧化碳的反应器,该反应器在产品容量和加入各种反应性混合物流(甚至含有相应量的二氧化碳、硫化或含氮化合物)的可能性方面具有更大的灵活性。
21.本发明的另一目的是提供一种使用电阻加热元件进行电加热的反应器,该电阻加
热元件与反应性混合物蒸汽直接接触,并且可以在1000℃以上的温度下操作,从而使加热元件、结构化陶瓷催化剂和反应性混合物流之间的温差最小化。
22.为了实现上述目的或将从详细描述中公开的或推断的目的,本发明涉及一种用于从进料反应性混合物流生产氢气和/或合成气和/或二氧化碳的反应器壳体,该反应器壳体包括:
23.至少一个反应流导管,形成在所述反应器壳体内,并基本上具有供所述反应性混合物流进料的至少一个反应流入口、所述反应性混合物流离开所述反应器壳体的反应流出口和设置在所述反应流入口和所述反应流出口之间的至少一个催化剂部,
24.绝缘填料,至少部分地围绕所述反应流导管,
25.至少一种结构化陶瓷催化剂,容纳在所述催化剂部中,并具有多个并列的中空陶瓷子单元,所述中空陶瓷子单元被配置为允许反应性混合物流通过其中,
26.至少一个电阻式电加热装置,为蜿蜒的,并通过至少两个电馈线连接到电源,用于将所述结构化陶瓷催化剂加热到预定的反应温度,
27.其中所述电加热装置以使得在所述中空陶瓷子单元的内部仍然存在流动通道的方式布置在至少一些所述中空陶瓷子单元的内部。
28.在反应器壳体的一个可能的实施例中,所述电加热装置包括蜿蜒部,使得其在所述结构化陶瓷催化剂内以蜿蜒的方式延伸,所述结构化陶瓷催化剂是由所述中空陶瓷子单元形成的束。
29.在反应器壳体的另一可能的实施例中,所述陶瓷子单元是陶瓷管。
30.在反应器壳体的另一可能的实施例中,所述电阻加热元件优选为电阻丝。
31.在反应器壳体的另一可能的实施例中,所述电加热装置和所述电源被配置为将所述结构化陶瓷催化剂加热至300℃至1300℃之间的温度。
32.在反应器壳体的另一可能的实施例中,所述中空陶瓷子单元具有纵向通道。
33.在反应器壳体的另一可能的实施例中,所述反应流导管还包括预热/混合部、反应流通道和冷却部,所述预热/混合部形成在所述反应流入口的延续部分中,用于预热/混合所述反应性混合物流,所述反应流通道将所述预热/混合部连接到所述催化剂部,所述冷却部形成在所述催化剂部的延续部分中,用于在离开所述反应流出口之前冷却离开的反应流。
34.在反应器壳体的另一可能的实施例中,其具有在1巴至150巴之间的设计压力。
35.本发明还涉及一种在反应器壳体中通过催化反应从进料反应性混合物流生产氢气和/或合成气和/或二氧化碳的方法,所述催化反应选自以下组成的组:氨裂解、蒸汽重整、干法重整、部分氧化、反向水煤气变换、voc氧化反应及其组合,所述反应器壳体包括至少一个反应流导管、绝缘填料、至少一种结构化陶瓷催化剂、至少一个电阻式电加热装置,所述反应流导管具有至少一个反应流入口、反应流出口和设置在所述反应流入口和所述反应流出口之间的至少一个催化剂部,所述绝缘填料至少部分地围绕所述反应流导管,所述结构化陶瓷催化剂容纳在所述催化剂部中,并具有多个中空陶瓷子单元,所述中空陶瓷子单元被配置为允许所述反应性混合物流通过其中,所述电阻式电加热装置通过连接到电源的至少两个电馈线供电,用于将所述结构化陶瓷催化剂加热到预定的反应温度。所述方法包括以下步骤:
36.将所述电加热装置以使得所述中空陶瓷子单元内的流动通道仍存在的方式布置在至少一些所述中空陶瓷子单元内部,
37.通过电源给所述电加热装置通电,使得所述结构化陶瓷催化剂被加热至300℃至1300℃之间的温度,
38.将压力在1巴至150巴之间的所述反应性混合物流通过所述反应入口送入所述反应器壳体,
39.允许所述反应性混合物流以所述反应性混合物流接触所述电加热装置的方式通过所述中空陶瓷子单元,
40.允许所述反应性混合物流从所述反应流出口流出。
41.在该方法的可能应用中,所述电加热装置沿着所述结构化陶瓷催化剂蜿蜒。
42.在该方法的另一可能应用中,通过所述反应流入口供给的所述反应流在1巴至150巴的压力下被预热至500℃至600℃的温度,并在到达所述结构化陶瓷催化剂之前进入所述反应流导管的所述预热/混合部。
43.在该方法的另一可能应用中,从所述结构化陶瓷催化剂排出的所述反应流在从所述反应性混合物出口排出之前在所述反应流导管的冷却部中冷却至150℃至800℃的温度。
44.在该方法的另一可能应用中,所述反应性混合物流通过设置在预热/混合部和冷却部之间的热交换装置或通过设置在所述预热/混合部内部或附近的附加电加热装置,利用所述冷却部的热量预热。
45.在该方法的另一可能应用中,用于生产氢气和/或合成气和/或二氧化碳的反应类型选自由氨裂解、蒸汽重整、干法重整、部分氧化、反向水煤气变换、voc氧化反应及其组合组成的组。
46.附图标记
47.10 反应器壳体
48.11 绝缘填料
49.20 反应流导管
50.21 反应性混合物流入口
51.22 预热/混合部
52.23 反应流通道
53.24 催化剂部
54.25 冷却部
55.26 反应性混合物流出口
56.30 结构化陶瓷催化剂
57.31 中空陶瓷子单元
58.311 子单元入口
59.312 子单元出口
60.313 流动通道
61.40 电加热装置
62.41 蜿蜒部
63.50 电源
64.51 电馈线
65.60 热交换装置
附图说明
66.图1示出了反应器壳体的垂直横截面。
67.图2示出了反应器壳体的水平横截面。
68.图3示出了反应器壳体中使用的结构化陶瓷催化剂的横垂直截面。
69.图4示出了反应器壳体中形成的反应流导管的替代实施例。
具体实施方式
70.现在将参考附图,通过非限制性示例更具体地描述本发明的优选实施例。
71.在图1中,示出了从进料反应流(即反应性混合物流)生产氢气和/或合成气和/或二氧化碳的反应器壳体(10)。具有绝缘填料(11)的所述反应器壳体(10)主要包括反应性混合物导管(20)和结构化陶瓷催化剂(30),反应性混合物导管(20)形成在反应器壳体内,以便被绝缘填料(11)围绕,结构化陶瓷催化剂(30)由多个并列的中空陶瓷子单元(31)形成,中空陶瓷子单元(31)布置在反应性混合物导管(20)内,以在反应器壳体内实现氨裂解和/或蒸汽重整和/或干法重整和/或者部分氧化和/或反向水煤气变换和/或voc氧化。结构化陶瓷催化剂(30)是一束并置的中空陶瓷子单元(31),中空陶瓷子单元(31)配备有电加热装置(40),该电加热装置(40)通过至少两个电馈线(51)供电,该电馈线以与反应器壳(10)绝缘的方式穿过反应器壳体(10)。该电馈线(51)连接到电源(50),电源优选设置在反应器壳体(10)的外部,并被配置为将结构化陶瓷催化剂(30)加热至期望的温度,以便进行预期的反应。由于这种布置,反应性混合物流流过反应性混合物管道(20),并在被结构化陶瓷催化剂(30)反应后从中排出。下面将详细说明结构和工艺细节。
72.反应流导管(20)按下游顺序包括反应流入口(21)、预热/混合部(22)、反应流通道(23)、催化剂部(24)、冷却部(25)和反应流出口(26)。所述结构化陶瓷催化剂(30)布置在所述催化剂部(24)内。另一方面,如图1所示,在本发明的一个优选实施例中,在预热/混合部(22)和冷却部(25)之间提供了热交换装置(60),以将冷却部(25)中离开的反应性混合物流的热量充分地传递到预热/混合部(22)。反应流的结构细节,如横截面、尺寸或前进路径可能会根据具体应用的设计要求而改变。例如,如图4所示,反应流导管(20)可包括四个独立的反应流入口。
73.参考图1和图2,结构化陶瓷催化剂(30)是由多个并列的中空陶瓷子单元(31)形成的“结构化催化床”,在反应发生的地方形成束。结构化陶瓷催化剂(30)的每个中空陶瓷子单元(31)具有流动通道(313),该流动通道允许反应性混合物流通过。结构化陶瓷催化剂(30)可以由多个并列形成束的管、颗粒、泡沫、整体式或其他中空陶瓷形状形成。因此,中空陶瓷子单元(31)的形成和部署限定了结构化陶瓷催化剂(30)的结构。中空陶瓷子单元(31)的材料选自由sio2、al2o3、y2o3、wo3、zro2、tio2、mgo、cao、ceo2、feo2、zno2及其组合组成的组,其支持催化活性材料,例如pt、ru、rh、ir、pd或ni。此外,在替代实施方案中,反应器壳体(10)可以包括一种以上的结构化陶瓷催化剂,它们彼此串联或并联和/或具有相同或不同的规格。
74.在可用于在这些反应条件下操作的不同结构的陶瓷催化剂(30)中,将使用陶瓷材料,因为金属载体,即使它们通常具有良好的热性能,也可能会使电加热装置(40)短路,导致加热不良和/或不均匀,从而降低电加热装置的寿命。负载在结构化陶瓷催化剂(30)上的催化活性物质是iiib至ib族的过渡金属(d区元素)和/或两种或多种可能包括碱金属的活性物质的组合。结构化陶瓷催化剂(30)将经历多相催化剂制备,作为传统上用于多相催化剂合成的初始润湿浸渍和/或浸渍和/或者载体洗涤涂覆和/或原位合成。结构化陶瓷催化剂(30)的布置方式使得进料反应性混合物流可以具有0.1ms至30000ms的接触时间。与此相关,接触时间是用结构化陶瓷催化剂的体积除以反应流的体积流速得到的。
75.如图2和图3所示,本发明的电加热装置(40)布置在中空陶瓷子单元(31)内,以便从内部加热结构化陶瓷催化剂(30)。详细地,在本发明的优选实施例中,电加热装置(40)蜿蜒穿过多个中空陶瓷子单元(31)中的一些或全部。由于该实施例,中空陶瓷子单元(31)被电加热装置(40)加热,从而结构化陶瓷催化剂(30)从内部加热。电加热装置(40)与结构化陶瓷催化剂(30)的物理接近(或接触)以及与反应性混合物流的直接接触增强了通过辐射、对流和传导的热传递。这种接近将使结构化陶瓷催化剂(30)能够在300℃至1300℃的温度下运行。与此相关,结构化陶瓷催化剂(30)和电加热装置(40)的组合必须以这样的方式布置,即在保持受流动通道(313)的尺寸影响的高热和传质的同时使压降最小化。例如,优选的是,电加热装置(40)的尺寸设计成在中空陶瓷子单元(31)内部留下足够的流动通道(313),从而在保持与结构化陶瓷催化剂(30)(即中空陶瓷子单元(31)的内壁)的接近的同时,反应性混合物流的流动受到最小的影响。因此,在优选实施例中,电加热装置(40)是具有足够柔性的电阻丝,使得其在将中空陶瓷子单元(31)捆扎起来之后蜿蜒。由于反应性混合物流被限制在由电加热装置(40)和中空陶瓷子单元(31)形成的小间隙内,所以电加热装置(40)和加热的反应性混合物流之间的温差被最小化。这对径向温度梯度有直接影响,从而对碳形成电位有直接影响,在重整反应的情况下,碳形成电位取决于热表面(电加热装置(40)和结构化陶瓷催化剂(30))的温度与反应性混合物流的温度。热表面(电加热装置(40)和结构化陶瓷催化剂(30))彼此接近,具有高的视角因子,并与反应性混合物流直接接触。
76.电加热装置(40)的电阻是通过使用最小数量的导线来实现的,这些导线在结构化陶瓷催化剂(30)内蜿蜒而成,结构化陶瓷催化剂形成为一束中空陶瓷子单元(31)。电加热装置(40)是电阻加热丝,其具有相当大的直径,优选大于2mm,因此能够在1000℃以上的温度下工作。根据第二欧姆定律,加热装置(40)的电阻是使用长的蜿蜒线而不是短的和小直径的线或丝来实现的。
77.由于电加热装置(40)布置在中空结构化陶瓷催化剂(30)内,电阻加热丝得益于中空陶瓷子单元(31)提供的机械支撑和几何限制。由于这种配置,由于纵向形状的电阻加热丝的非常高的稳定性,特别是由于具有催化作用的材料的存在,与已经公开的任何其他设备相比,电加热装置(40)的最大功率显著增加。表面载荷不受电磁力、热膨胀或1300℃以下极高工作温度引起的较低物理性能的限制。
78.如果电加热装置(40)嵌入结构化陶瓷催化剂(30)的主体内,则通常高于1000℃的高操作温度将由于电加热装置40和结构化陶瓷催化剂(30)的热膨胀系数之间的失配而引起机械应力。因此,陶瓷负载的催化剂(30)将破裂并失效。
79.此外,由于电加热装置(40)蜿蜒穿过多个中空陶瓷子单元(31)中的一些或全部,
因此无需使用连接器元件将电加热装置(40)彼此连接,这将导致:电加热装置(40)的不均匀性和不规则性,尤其是近电位焊接,由于多个电加热装置(40)的并联连接而导致的电阻的减小、额外的工作量减少和制造的复杂性减小。
80.另一方面,电加热装置(40)在结构化陶瓷催化剂(30)内的部署取决于中空陶瓷子单元(31)的选定类型和几何特性,例如管、颗粒、泡沫、整体式或其他中空陶瓷形状。
81.例如,如图3所示,结构化陶瓷催化剂是一束并列的中空陶瓷管,形成了网格状横截面。由于这种并列布置,反应性混合物流的流动被限制在电加热装置(40)所在的流动通道(313)内。如果中空陶瓷子单元(31)以非并列的方式形成束,则在相邻中空陶瓷子单元(32)之间留下的区域中可能发生旁路。由于所述旁路区域在流动通道(313)的外部,因此不与电加热装置(40)和中空陶瓷子单元(31)的内表面直接接触,反应性混合物流的温度降低,导致反应器的效率降低。因此,如果在反应器壳体(10)中形成整体式结构化陶瓷催化剂,则电加热装置(40)纵向放置在中空陶瓷子单元(31)内,平行于反应性混合物流的流动方向延伸,而电加热装置(20)的蜿蜒部(41)保持在中空陶瓷子单元(31)外。在用安装的电加热装置(40)形成中空陶瓷子单元(31)的束之后,电阻线从第一中空陶瓷子单元(31)的子单元入口(311)插入,并从其另一端的子单元出口(312)引出,然后插入第二中空陶瓷子单元(31)子单元出口并从其子单元入口引出,如图1、图2和图3所示。
82.如果选择泡沫型,即开孔型,作为中空陶瓷子单元(31)用于结构化陶瓷催化剂,则电加热装置(40)可以与由泡沫结构限定的中空陶瓷子单元(31)类似地全方位延伸。详细地,电加热装置(40)从结构化陶瓷催化剂(30)的入口到出口穿过限定流动通道(313)的开口单元,从而沿着电加热装置(40)的布置形成加热通道。在这种情况下,由于结构化陶瓷催化剂(30)的开孔泡沫的全方位开放结构,反应性混合物流全方位流动。电加热装置的蜿蜒以与前述实施例类似的方式进行。
83.优选地,电加热装置(40)包括电线形式的电阻加热元件。由于所述电线的尺寸和几何结构以及其与催化活性材料的接近,这可以承受高达1400℃的温度,但也可以蜿蜒。
84.鉴于本发明的上述结构性质,下面将详细解释反应的进行过程。
85.一旦反应性混合物流通过反应流入口(21),由一种或多种以下试剂组成的一种或多种液体试剂流发生汽化和/或雾化/雾化:氨、石脑油、醇、水、其他精炼产品、含甲烷流、含voc的气体流和氧化流。进料液体和/或气体试剂(即反应性混合物流)可能使用蒸汽和/或气态流进行雾化和/或汽化,其中蒸汽和/或者空气和/或氧气和/或二氧化碳的氧化流也被进料。进料至反应性混合物入口(21)的所述反应性混合物流可能在低于沸点的温度下被预热,因此位于反应器壳体内的蒸发将用于冷却反应产物并有助于控制温度。送入反应性混合物入口(21)的所述反应性混合物流的温度范围为25℃至600℃,优选低于200℃,压力范围为1巴(bar)至150巴,优选低于50巴。
86.反应性混合物流在送入反应流入口(21)之前经历的汽化和/或雾化/喷雾(例如通过超声波)必须确保液体流的最佳相变并避免气相反应。必须避免蒸发和混合不良,因为:
[0087]-它们可能导致碳质沉积物的形成,
[0088]-它们可能会产生冷点和/或热点,这可能损坏包括结构化陶瓷催化剂的反应器壳体,
[0089]-它们可能会在反应器壳体内产生可燃袋,并可能存在安全问题,
[0090]-它们可能会降低反应生成所需产物的产率,
[0091]-它们可能需要结构化陶瓷催化剂(30)中附加和额外的能量消耗。
[0092]
在反应器的各种实施方案中,液体形式的反应性混合物流的进料可以在设备中的单个或多个点和/或位置进行。通过优化反应流导管(20)几何形状的设计和/或使用具有高热性能(热导率高于10wm-1
℃-1
)的高表面积材料,可以改善膨胀和雾化。
[0093]
在预热/混合部(22)中,从反应流入口(21)的末端开始,到反应流通道(23)的入口结束,实现了进料反应性混合物流的预热和混合。在该部中,来自反应流入口(21)的雾化、汽化或雾化形式的反应性混合物流在50℃至600℃的温度和1巴至150巴的压力下加热,形成可能的两相液气反应性混合物,并混合。
[0094]
在一优选实施方案中,在预热/混合部(22)中提供了额外的电加热装置,用于加热反应流。
[0095]
在另一优选实施例中,冷却部(25)中的热量通过设置在预热/混合部(22)和冷却部(25)之间的热交换装置(60)传递到预热/混合部(22)。例如,在反应性混合物出口(26)处发生的额外放热(放热)反应(例如wgs)在150℃至400℃的温度下提供额外的加热,其中的热量通过热交换装置(60)传递到预热/混合部(22),例如设置在预热/混合部(22)和反应性混合物出口(26)之间的导热壁。
[0096]
在预热/混合部(22)中,反应性混合物流在进入反应流通道(23)之前也通过混合而均匀化。混合功能的目的是在进入结构化陶瓷催化剂(30)之前使反应性混合物流均匀化并提高温度。
[0097]
预热/混合部(22)可以具有所有不同的几何形状,包括半球形和抛物面。该区域可以是空的和/或填充有固体,以形成随机或结构化的基质,从而改善混合和传热,并减小尺寸。因此,根据该部的不同设计,传输现象可能依赖于不同的传输现象。预热/混合部(22)的设计还必须避免冷表面的存在,这可能导致液体试剂的沉积和/或影响反应器的机械稳定性和可能的水-汽变换平衡的热流冷却不良。此外,在给定成分、温度和压力的情况下,当进料反应性混合物流在可燃极限内时,反应性混合物流的线性速率必须高于火焰速率。
[0098]
随后,预热和混合的反应物流进入反应流通道(23),在那里,由于覆盖通道的隔热填料(11),发生了最小的传热。然后,反应性混合物流进入设置在催化剂部(24)内的结构化陶瓷催化剂(30)。在结构化陶瓷催化剂中,通过与结构化陶瓷催化剂(30)的支撑催化活性材料的中空陶瓷子单元(31)的壁物理接触,反应性混合物流经历催化反应,例如氨裂解和/或sr和/或dr和/或po和/或反wgs和/或voc氧化。中空陶瓷子单元(31)被配置为防止其间的任何流旁路。换言之,流经结构化陶瓷催化剂(30)的整个反应性混合物流流经多个流动通道(313),与电加热装置(40)和催化活性材料直接接触。当结构化陶瓷催化剂(30)从300℃加热到1300℃时,实现催化反应。
[0099]
如上所述,通过沿着中空陶瓷子单元(31)中的一些或所有的蜿蜒的电加热装置(40)提供所需的热量,从而以有效的方式加热结构化陶瓷催化剂(30)。由于这种布置,通过结构化陶瓷催化剂(30)的反应性混合物流不仅温度升高,而且将在被有效且均匀加热的结构化陶瓷催化剂(30)的表面上反应,最小化可能导致碳质沉积物和/或对反应的热影响和/或低催化剂效率因子的任何温度梯度。此外,结构化陶瓷催化剂(30)内达到的温度(通常高于1000℃)将增加反应速率,这需要减少接触时间,将导致紧凑和小型反应器。
[0100]
最终反应产物将包括氢气和/或合成气和/或co2的混合物,这取决于进料组成和发生的反应。在氨裂解和/或sr和/或dr和/或po和/或反向wgs和/或完全氧化结束时,反应性混合物的温度为300℃至1300℃,优选约1000℃。
[0101]
如上所述,以本发明的方式为结构化陶瓷催化剂(30)配备蜿蜒的电加热装置(40)的进一步优点如下:
[0102]-限制二次反应的可能性,
[0103]-快速启动,
[0104]-防止不同环境和/或火焰之间高温和/或跨表面热传递的原位热生成,
[0105]-使用吸热反应作为增加电阻加热元件寿命的能量吸收器来保持电阻加热元件的低表面温度的可能性,
[0106]-使用由电阻丝制成的蜿蜒电加热装置(40)的可能性,该装置可在1300℃的温度下在由中空陶瓷子单元捆绑而成的结构化陶瓷催化剂中运行,
[0107]-避免用于电阻丝的连接器元件的可能性,因此需要焊接或其他连接,这些连接会导致电加热装置(40)的局部不均匀性,这将导致局部热点并导致电加热装置(40)失效,
[0108]-根据进料反应性混合物流组成的差异容易地增加功率占空比的可能性,
[0109]-严格的温度控制也将促进和弥补设备容量的可能变化,
[0110]-所使用的电加热装置(40)的电阻需要标准的工作电压和电流,这一事实现在用于电阻加热器中,避免了在导电材料的带电宏观结构的情况下所需的复杂的电输送系统,如在nicr或fecrai合金或sic的情况下,
[0111]-在结构化陶瓷催化剂(30)内均匀达到高温的可能性,这将降低能耗,因为具有冷表面和/或热表面的可能性最小化,从而减少了防止任何催化剂失活(例如通过碳沉积)所需的氧化共反应物的量,
[0112]-在使重整反应期间存在的氧化共反应物的量最小化之后使产物选择性最大化的可能性,
[0113]-提高操作温度从而在吸热反应中转化试剂的可能性,而不受提供物理限制的表面的最高操作温度的限制,如位于燃烧室内的重整管的情况,
[0114]-由于结构化陶瓷催化剂(30)内的径向温度梯度最小化,形成碳的可能性最小化,
[0115]-在循环条件下达到1400℃温度的可能性,可用于催化剂活化和/或从可能的碳质沉积物和/或硫和/或极高沸点化合物等中毒物质中再生。
[0116]
离开设置在催化剂部(24)中的结构化陶瓷催化剂(30)的反应性混合物流在冷却部(25)中进行冷却,在冷却部中,如上所述,通过预热/混合部(22)之间的壁与之进行热交换。该部用于在离开催化剂部(24)的反应性混合物流和存在于预热/混合部(22)中的反应性混合流之间进行热交换。该部将涉及气体和/或气-液之间的变换,可能涉及相变,从而最大限度地提高可去除的热量。离开催化剂部(24)并进入冷却部(25)的气相在一区域中流动,该区域可以具有任何几何形状/构型,并可能包含增强传热界面处湍流和/或径向热传导的高导电结构化或/随机填充材料。快速冷却步骤依赖于来自沸腾液体的高传热和强温度梯度,将使冷却时间最小化,从而避免任何不希望的反应,如甲烷化和一氧化碳歧化。
[0117]
在一优选实施方案中,用水或蒸汽进行气体淬火也可用于进一步冷却离开催化剂部(24)的反应性混合物流。在预热/混合部(22)和冷却部(25)之间发生的逆流热交换将改
善热传递。产品流和反应流之间的能量传递将在同一设备中进行,从而强化工艺并降低资本投资成本,避免额外的热交换器、管道、阀门、流量计、配件和容器。在一优选实施方案中,在冷却部(25)内的温度降低之后,还可以使用能够在150℃至400℃的温度下促进放热wgs反应的系统,为预热/混合部(22)提供额外的加热辅助。
[0118]
最后,反应性混合物流在离开反应器壳体(10)之前到达反应流出口(26)。
[0119]
通过上述关于氨裂解和/或sr和/或dr和/或po和/或反向wgs和/或voc氧化反应的系统和工艺,可以获得以下结果:
[0120]-完全去除高温吸热反应所需的燃料气燃烧产生的co2,
[0121]-依赖可再生电能并在热化学反应后将其转化为能量载体的可能性,
[0122]-高(火用)效率(high exergy efficiency),
[0123]-避免温度梯度的可能性,这将导致低催化剂效率系数和大反应器体积,
[0124]-转化广泛的反应性混合物并产生广泛的合成气组合物的可能性,
[0125]-在sr和/或dr和/或po和/或反向wgs和/或完全氧化之间切换主要反应的广泛反应性混合物的处理和反应的可能性,
[0126]-dr反应工业化的可能性,因此co2用于合成气和/或氢气的最终生产,
[0127]-避免昂贵的高温燃烧炉和下游尾气处理的可能性,
[0128]-缩小合成气和/或氢气生产装置的规模直到目前不能使工艺经济的流量的可能性,
[0129]-减少上游热交换器尺寸和/或数量和/或避免任何预热的可能性,不仅简化了工艺,而且还减少了燃料气的消耗,从而减少了co2的产生,
[0130]-减少了资本和操作成本的可能性,强化了工艺,减少了设备的体积和数量,
[0131]-在反应中添加空气和/或氧气的可能性,从而降低了电加热元件必须供应的能量需求,
[0132]-在不存在惰性气体(如氮气)和未反应气体的情况下,气体最终流中存在co2的可能性,使得低成本co2分离用于碳封存成为可能,
[0133]-依靠基于生物质的试剂从大气中去除co2,然后进行下游co2分离的可能性,
[0134]-在不使用任何额外燃料的情况下去除voc杂质的可能性,
[0135]-快速启动时间、反应不同组成和反应性混合物流流动的灵活性,其允许快速改变合成气和/或氢气生产,减少试剂的积累和储存,
[0136]-使用不同类型的起始试剂生产氢气和/或合成气的可能性,使工艺经济性与工厂设计期间假定的试剂价格脱钩,从而可以在使用相同方法和设备的同时切换到最便宜的试剂。
[0137]-使用极高温度(高于1000℃)和高压的可能性,从而减少设备体积,进一步降低资本成本、热损失、安全问题和人员足迹。
再多了解一些
本文用于创业者技术爱好者查询,仅供学习研究,如用于商业用途,请联系技术所有人。