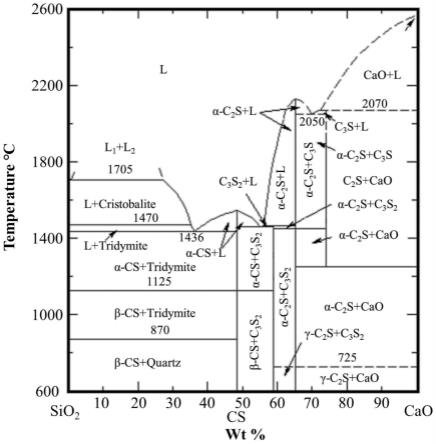
1.本发明涉及硅砖技术领域,特别是指一种添加四水硝酸钙的硅砖及其制备方法。
背景技术:
2.硅砖是在硅质原料(废硅砖和sio2含量不小于96wt%的硅石)中加入矿化剂和结合剂,经混练、成型、干燥、烧成等工序制得的sio2含量>94wt%的硅质耐火材料。硅砖具有荷重软化温度点高、高温体积稳定性好、高温蠕变性能优异等特性,且性价比优,广泛应用于玻璃窑、焦炉和热风炉等大型高温装备。
3.在硅砖的使用温度下,鳞石英是sio2的最终凝聚稳定相。因此以鳞石英为主,含有少量方石英,以及少于1wt%残余石英的硅砖在大型工业窑炉内能够呈现出较好的使用效果。矿化剂是实现硅砖在生产过程中硅石原料至鳞石英相转变的关键性因素,其作用在于:(1)矿化剂能够在高温下形成液相量可控的含sio2液相,促进鳞石英的生成,鳞石英的生成需要高温下sio2在其饱和液相中进行溶解-析晶过程,无液相存在的高温条件下,石英将会朝着亚稳态方石英、方石英的方向转变,无法转变为鳞石英;(2)矿化剂能够通过形成液相缓冲砖坯烧成时因膨胀所产生的应力,防止制品产生松散和开裂,硅石在加热过程中的快速晶型转变会产生较大体积膨胀,使硅砖的烧成比其他耐火材料困难。
4.目前我国生产硅砖广泛采用的矿化剂为cao-feo系。其中,氧化铁的铁主要是轧钢皮(铁鳞),并要求其含fe2o3 feo》90%,以细粉形式加入;氧化钙因极易水化,难以在大气中保存,以石灰乳(氢氧化钙溶液)的形式加入。
5.然而,在实际使用过程中,石灰乳搭配铁鳞的矿化剂组合存在以下几点问题:(1)微量的铁鳞细粉难以在硅砖中分散均匀,石灰乳溶液则容易絮凝,不易分散;(2)ca(oh)2在500℃左右发生分解产生的大量水蒸气能够导致砖坯内部压力增大,增大热风炉热风出口组合砖,玻璃炉拱脚和弦砖以及焦炉跨顶砖等大型硅砖制品(长≥350mm,宽≥250mm,高≥200mm)的烧成难度;(3)含有铁质矿化剂的硅砖中玻璃相含量高(10-20wt%),这部分玻璃相在硅砖长达十年以上的使用时间内会发生聚集以及缓慢流失,进而严重影响硅砖的使用性能及寿命;(4)氧化钙的生产主要是通过石灰石(caco3)的加热分解,其副产物co2(g)的大量产生严重有悖于现今我国“双碳”政策下的发展理念。因此,探寻新型矿化剂,提供一种绿色环保且高性能的大型硅砖及其制备方法是本发明的主要目的。
技术实现要素:
6.本发明要解决的技术问题是提供一种添加四水硝酸钙的硅砖及其制备方法。本发明借助于四水硝酸钙原料混炼时易分散、高温烧成过程中逐步分解等特性以及sio
2-cao体系中较低的玻璃相生成量解决了现有硅砖制备技术中采用“铁鳞 石灰乳”作为矿化剂时存在的矿化剂难以分散、烧成过程难以控制以及砖内玻璃相含量高等问题。本发明制备方法简单,原料丰富且性价比优,烧成过程易控,适宜大型硅砖的工业化生产,成品砖具有较高的合格率和鳞石英含量。
7.为解决上述技术问题,本发明提供如下技术方案:
8.本发明第一方面提供一种硅砖,所述硅砖包括矿化剂,所述矿化剂包括四水硝酸钙。
9.所述矿化剂中可以包括或包括铁鳞等其他常规组分。优选地,所述矿化剂由四水硝酸钙组成,不含铁鳞。该优选方案下,更利于提升鳞石英含量,降低玻璃相含量。
10.其中,优选地,所述硅砖中四水硝酸钙的质量含量为0.1%~10%。该优选方案下,四水硝酸钙含量适宜,能够在硅砖中分散均匀,更利于提升鳞石英含量。
11.本发明中仅四水硝酸钙能达到本发明的特定效果,且四水硝酸钙作为一种化肥材料更易获取。而硝酸钙不具有四水硝酸钙的低熔点特性,且硝酸钙属危险品。
12.在一些实施方式中,本发明的硅砖以硅石和废硅砖为主要硅质原料,以四水硝酸钙为矿化剂。
13.在一些优选实施方式中,所述硅砖还包括硅石组分和废硅砖,以四水硝酸钙、硅石组分和废硅砖的总量为基准,废硅砖的质量含量为1%~30%,硅石组分的质量含量为50%~98.9%。
14.更优选地,所述硅砖还包括结合剂,结合剂的量为四水硝酸钙、硅石组分和废硅砖的总量的0.5%~5%。
15.更优选地,所述硅砖中,四水硝酸钙的质量含量为5%~6.5%,废硅砖的质量含量为8.5%~11.5%,硅石组分的质量含量为83.5%~85%。该优选方案下,更利于最大化提升鳞石英含量,降低玻璃相含量。
16.在一些实施方式中,所述硅石组分包括粒度为≤3mm且>1mm的第一硅石骨料和粒度≤1mm的第二硅石骨料,以及粒度≤200目的硅石细粉。
17.在一些更优选的实施方式中,,所述硅石组分包括粒度为≤2.5mm且>0.5mm的第一硅石骨料和粒度≤0.5mm的第二硅石骨料,以及粒度≤200目的硅石细粉。该优选方案下,能够实现颗粒的紧密堆积,更利于提升产品的致密程度。
18.更优选地,以硅石组分的总量为基准,所述硅石组分中第一硅石骨料的质量含量为15%~40%,第二硅石骨料的质量含量为15%~70%、优选30%~70%,硅石细粉的质量含量为15%~45%。该优选方案下,能够实现最佳的颗粒级配,更利于提升产品的机械性能。
19.其中,优选地,所述废硅砖的粒度≤0.5mm。
20.应当理解的是,所述废硅砖由生产的硅砖残品破碎制得。
21.本发明第二方面提供第一方面所述的硅砖的制备方法,包括如下步骤:
22.s1、将包括矿化剂的原料进行混合搅拌,制成泥料;
23.s2、采用压力机将s1中的泥料压制成砖坯,经干燥、烧结制得成品。
24.其中,优选地,s2中所述干燥的过程包括:将砖坯在小于200℃温度下干燥24~48h至残余水分<1.0wt%。该优选方案下,能够将砖坯内水分充分排出,更利于砖坯在烧成过程中的稳定性。
25.其中,优选地,s2中所述烧结的过程包括:升温至1450~1510℃保温24~48h。该优选方案下,能够满足砖坯内石英向鳞石英的转变要求,更利于提升产品的鳞石英含量。
26.本发明中,所述结合剂可以采用本领域所有常规的结合剂种类,例如纸浆废液结
合剂。
27.本发明的上述技术方案的有益效果如下:
28.本发明在硅砖中使用单一钙质矿化剂四水硝酸钙与其他必要的常规原料(如硅石组分原料)一同构建的sio
2-cao二元系能够在硅砖的烧成过程中产生液相量可控的含sio2液相。由如图1所示的sio
2-cao二元相图可以看出,cao-sio2体系在靠近sio2侧(cao含量28%以下)液相的最低生成温度为1436℃,至1705℃完全转变为二液相区,并且在这期间液相线走向趋陡;其证实来自于四水硝酸钙的cao能够单独作为矿化剂满足硅砖在常规烧成和使用温度下生成液相的同时又不会对sio2构成强溶剂。
29.本发明以四水硝酸钙作为硅砖矿化剂具有以下几点优势:(1)首先四水硝酸钙熔点仅45℃,在硅砖原料的混炼过程中,因摩擦产生的热量足以使四水硝酸钙转变为液相,进而能够实现其在硅砖中的均匀分布;(2)四水硝酸钙的脱水可以在硅砖的干燥过程进行,在硅砖的烧成过程中脱水后的四水硝酸钙逐步分解为亚硝酸钙和氧化钙,分解过程呈多步进行,不会在砖内产生过大压力;(3)单独使用钙质矿化剂能够有效降低降低硅砖内玻璃相含量,进而有利于提升其使用性能及寿命。本发明提供一种以四水硝酸钙作为矿化剂的硅砖及其制备方法,在满足鳞石英含量≥60wt%的基础上实现高性能大型硅砖的绿色生产。
30.本发明针对目前采用“铁鳞 石灰乳”作矿化剂生产硅砖时的不足和缺陷,选取四水硝酸钙作为矿化剂组分(或组分之一)制备硅砖,还具有以下有益效果:
31.(1)四水硝酸钙在硅砖原料的混炼过程中转变为液相,进而实现其在硅砖中的均匀分布;
32.(2)四水硝酸钙的脱水可以在硅砖的干燥过程进行,脱水后的四水硝酸钙在硅砖的烧成过程中逐步分解为亚硝酸钙和氧化钙,分解过程呈多步进行,不会在砖内产生过大压力;
33.(3)单独使用钙质矿化剂四水硝酸钙能够有效降低硅砖内玻璃相含量,进而有利于提升其使用性能及寿命;
34.(4)本发明的硅砖强度高、高温体积稳定性好、高温抗热震稳定性和高温蠕变性能优异;
35.(5)本发明制备方法简单,原料丰富且性价比优,烧成过程易控,适宜大型硅砖的工业化生产,合格率高。
附图说明
36.图1为四水硝酸钙与硅石组分原料构成的sio
2-cao二元相图。
具体实施方式
37.为使本发明要解决的技术问题、技术方案和优点更加清楚,下面将结合附图及具体实施例进行详细描述。本发明中,所有含量除另外说明外,均以质量计。
38.实施例1
39.先将81.5wt%的硅石组分、15wt%的废硅砖和3.5wt%四水硝酸钙混合,外加上述混合料2wt%的纸浆废液结合剂,混炼均匀,压制成型;干燥后置入隧道窑中于1450℃保温30h烧成,制得硅砖。干燥的过程包括:将砖坯在100℃温度下干燥24h至残余水分<
1.0wt%。
40.其中,硅石组分由粒度为≤2.5mm且>0.5mm的第一硅石骨料和粒度≤0.5mm的第二硅石骨料,以及粒度≤200目的硅石细粉组成;硅石组分中第一硅石骨料的质量含量为30wt%,第二硅石骨料的质量含量为55wt%,硅石细粉的质量含量为15wt%。废硅砖的粒度≤0.5mm。
41.所得硅砖经检测,显气孔率为19.0%,体积密度为1.84g/cm3,常温耐压强度为46.7mpa,荷重软化温度为1679℃,鳞石英含量64%,方石英含量27%,玻璃相含量5%。
42.实施例2
43.先将81.5wt%的硅石组分(组成同实施例1)、15wt%的废硅砖(粒度同实施例1)和3.5wt%四水硝酸钙混合,外加上述混合料1wt%的纸浆废液结合剂,混炼均匀,压制成型;干燥后置入隧道窑中于1460℃保温48h烧成,制得硅砖。
44.所得硅砖经检测,显气孔率为19.1%,体积密度为1.85g/cm3,常温耐压强度为47.3mpa,荷重软化温度为1673℃,鳞石英含量66%,方石英含量25%,玻璃相含量5%。
45.实施例3
46.先将85.0wt%的硅石组分(组成同实施例1)、10wt%的废硅砖(粒度同实施例1)和5.0wt%四水硝酸钙混合,外加上述混合料2wt%的纸浆废液结合剂,混炼均匀,压制成型;干燥后置入隧道窑中于1450℃保温30h烧成,制得硅砖。
47.所得硅砖经检测,显气孔率为18.3%,体积密度为1.86g/cm3,常温耐压强度为60.7mpa,荷重软化温度为1666℃,鳞石英含量68%,方石英含量24%,玻璃相含量4%。
48.实施例4
49.先将83.5wt%的硅石组分(组成同实施例1)、10wt%的废硅砖(粒度同实施例1)和6.5wt%四水硝酸钙混合,外加上述混合料2wt%的纸浆废液结合剂,混炼均匀,压制成型;干燥后置入隧道窑中于1460℃保温48h烧成,制得硅砖。
50.所得硅砖经检测,显气孔率为17.8%,体积密度为1.87g/cm3,常温耐压强度为58.7mpa,荷重软化温度为1673℃,鳞石英含量69%,方石英含量24%,玻璃相含量4%。
51.实施例5
52.先将84.5wt%的硅石组分(组成同实施例1)、10wt%的废硅砖(粒度同实施例1)、0.5wt%铁鳞和5wt%四水硝酸钙混合,外加上述混合料1wt%的纸浆废液结合剂,混炼均匀,压制成型;干燥后置入隧道窑中于1460℃保温48h烧成,制得硅砖。
53.所得硅砖经检测,显气孔率为20.0%,体积密度为1.83g/cm3,常温耐压强度为45.7mpa,荷重软化温度为1658℃,鳞石英含量63%,方石英含量21%,玻璃相含量13%。
54.实施例6
55.参照实施例4的方法进行,不同的是,硅石组分包括粒度为≤3mm且>1mm的第一硅石骨料和粒度≤1mm的第二硅石骨料,以及粒度≤200目的硅石细粉。
56.所得硅砖经检测,显气孔率为20.1%,体积密度为1.79g/cm3,常温耐压强度为36.5mpa,荷重软化温度为1670℃,鳞石英含量63%,方石英含量30%,玻璃相含量4%。
57.以上所述是本发明的优选实施方式,应当指出,对于本技术领域的普通技术人员来说,在不脱离本发明所述原理的前提下,还可以做出若干改进和润饰,这些改进和润饰也应视为本发明的保护范围。
再多了解一些
本文用于创业者技术爱好者查询,仅供学习研究,如用于商业用途,请联系技术所有人。