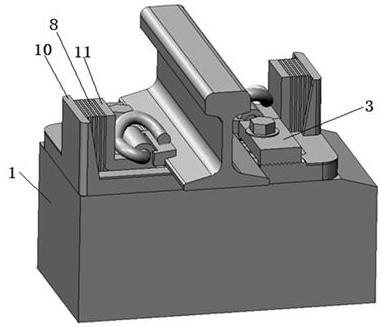
1.本发明涉及一种轨道减振扣件及其刚度调节设计方法,属于轨道减振扣件技术领域。
背景技术:
2.为了进一步降低地铁造成的声音污染及环境振动及结构二次噪声,越来越多的地铁线路提出采用高弹性减振扣件取代普通扣件。由于高弹性减振扣件大幅降低了轨道扣件的整体垂向刚度,扣件的综合减振效果得到了很大的提升,较好的解决了轨道交通运营中产生的振动及噪声问题。但是,随着这些高弹性扣件的大量使用,钢轨逐渐出现了磨损较快的现象,甚至出现了严重的波磨。主要原因是:1)这些扣件在降低垂向刚度的同时也降低了横向刚度,使得钢轨的垂向振动及横向振动加大,导致钢轨横向滑移加大,从而导致钢轨磨损增大,甚至出现波磨;2)由于扣件刚度降低,钢轨轨头偏转刚度随之降低,轮轨相互作用产生的横向力不断往复地作用于钢轨的轨头部分,带动钢轨在其横向两侧反复发生偏转,钢轨产生摆振,进一步加剧了钢轨的波磨。
3.目前地铁中等减振扣件的常用两种减振方式为:组合式减振扣件(以双层非线性减振扣件为代表)、硫化一体式减振扣件(压缩型、剪切型两种)。其工作原理都为通过橡胶受载产生压缩或者剪切变形来实现减振功能,从而削弱轮轨作用传递到路基的振动和冲击。但是现有技术存在的主要问题是:1)现有的硫化一体式轨道减振扣件:压缩型,垂向刚度较大,减振效果有限;剪切型,垂向刚度较小,有较好的减振效果,但是横向刚度有限,横向稳定性不佳。
4.2)现有的非硫化一体式轨道减振扣件:对横向位移控制虽然也采用了塑料或者尼龙类硬性绝缘部件,但是内部结构较为复杂,众多装配零件之间的相互配合使得减振扣件在使用过程中大大增加了零件之间的磨损的可能性,不便于后期对产品的维护,且安装拆卸繁琐。
5.3)目前一般轨道减振扣件的减振效果有限,对于二次结构噪声投诉问题作用不大,具有较高减振性能(减振效果达到8db以上)的减振扣件种类仍较少。
技术实现要素:
6.本发明提供的轨道减振扣件及其刚度调节设计方法,增加轨道减振扣件的横向刚度,限制钢轨横向位移,有效控制减振本体受到横向力时带来的翻转,减小减振本体的横向弯矩,提高钢轨轨头的偏转刚度,控制钢轨轨头横向位移,减小因钢轨横向移动而产生的波磨,提高轨道减振扣件的横向稳定性,实现减振本体垂向小载荷小刚度、大载荷具有限位保护刚度的承载需求,保证减振效果,并提高行车安全性。
7.为达到上述目的,本发明采用的技术方案是:一种轨道减振扣件,固定在轨枕上,包括垫在轨枕上的减振本体、将减振本体固定在轨枕上的螺栓扣板组件、将钢轨压紧在减振本体上的轨距块和装在减振本体上并压紧轨
距块的弹条,其特征在于:所述的减振本体包括底板和通过橡胶层与底板硫化连接的顶板,底板两侧设有沿垂向的外挡肩,顶板上设有与外挡肩相对应且位于外挡肩内侧的内挡肩,内挡肩设置在钢轨外侧,橡胶层从顶板底部向上伸延至内挡肩和外挡肩之间。
8.优选的,所述的底板上开有与顶板相对应的通孔,顶板通过橡胶层硫化连接在通孔中,通孔孔壁为由外向内倾斜的倾斜面,顶板外侧壁为与通孔孔壁平行相对的倾斜面,使通孔孔壁与顶板外侧壁之间的橡胶层呈由外向内倾斜的剪切结构。
9.优选的,所述的顶板底部的橡胶层中开有向上凹进的底凹槽,底凹槽中至少具有一个向下凸出的橡胶凸台,橡胶凸台与轨枕顶面隔开不接触。
10.优选的,所述的通孔呈工字型,通孔中部具有两根沿底板长度方向设置的挡条,两根挡条在底板上对称分布,通孔孔壁与顶板外侧壁之间的橡胶层包括沿通孔长度方向设置的横向倾斜橡胶层和沿通孔宽度方向设置的纵向倾斜橡胶层 ,横向倾斜橡胶层由外向内倾斜的角度大于纵向倾斜橡胶层由外向内倾斜的角度。
11.优选的,所述的外挡肩与底板一体成型,外挡肩为具有内腔的凹腔板,内挡肩与顶板一体成型,外挡肩与内挡肩之间的橡胶层沿垂向设置且未将外挡肩的内腔填满,在外挡肩与内挡肩之间的橡胶层中硫化至少一层沿垂直设置的隔板。
12.优选的,所述的螺栓扣板组件包括铺设在减振本体上的扣板、穿过扣板、减振本体并旋紧在轨枕上的螺栓和垫在扣板顶面及底板且套在螺栓上的垫圈,底板上开有锯齿形状的锯齿槽,扣板的底面设有与锯齿槽配合的锯齿,锯齿伸入锯齿槽中将扣板定位在底板上。
13.优选的,所述的扣板上开有供螺栓贯穿的安装孔,安装孔为沉台孔,安装孔的沉台中放置双层弹簧圈,双层弹簧圈随螺栓的旋紧而被压缩在安装孔中并压紧顶板。
14.以上所述的轨道减振扣件的刚度调节设计方法,其特征在于:根据轨道减振扣件的垂向刚度需求,设计顶板与底板之间的橡胶层的结构和厚度,以调节轨道减振扣件的垂向刚度;根据轨道减振扣件的横向刚度需求,设计外挡肩与内挡肩之间的橡胶层的结构和厚度,以调节设计轨道减振扣件的横向刚度。
15.优选的,“设计顶板与底板之间的橡胶层的结构和厚度,以调节轨道减振扣件的垂向刚度”是指设计通孔孔壁与顶板外侧壁之间的橡胶层的倾斜角度和厚度,以调节轨道减振扣件的垂向静刚度,设计橡胶凸台与轨枕顶面的间距,以调节轨道减振扣件在承载过程中的垂向变刚度拐点;“设计外挡肩与内挡肩之间的橡胶层的结构和厚度,以调节设计轨道减振扣件的横向刚度特性”是指设计外挡肩和内挡肩之间的橡胶层的厚度,以调节轨道减振扣件的横向初始刚度,设计外挡肩与内挡肩之间的橡胶层中隔板的厚度和数量,以调节轨道减振扣件在承载过程中的横向非线性刚度。
16.优选的,“设计通孔孔壁与顶板外侧壁之间的橡胶层的倾斜角度和厚度”是指设计纵向倾斜橡胶层和横向倾斜橡胶层的倾斜角度和厚度。
17.发明的有益效果是:1.本发明的轨道减振扣件,底板和顶板通过橡胶层硫化成整体式结构的减振本体,减振本体无需零件组装成型,避免使用过程中减振本体因零件内部摩擦而带动的结构磨损,延长减振本体的使用寿命,橡胶从下至上一体硫化,实现了底板、顶板、内外挡肩和橡胶层的一体化结构,确保了扣件具有高的减振效果和结构稳定性,减化扣件的结构,扣件维护保养更加简单方便。在底板上设置外挡肩,在顶板上设置内挡肩,橡胶层从顶板底部延伸
至内外挡肩之间,增加轨道减振扣件的横向刚度,限制钢轨横向位移,有效控制减振本体受到横向力时带来的翻转,减小减振本体的横向弯矩,提高钢轨轨头的偏转刚度,控制钢轨轨头横向位移,减小因钢轨横向移动而产生的波磨,提高轨道减振扣件的横向稳定性。
18.2.在底板上开设通孔,顶板硫化连接在通孔中,顶板外侧壁与通孔孔壁之间的橡胶层呈由外向内倾斜的剪切结构,使橡胶层具有足够的压减变形空间,从而使减振本体的垂向静刚度较低,刚度平顺减振效果好,减振扣件承受垂向小载荷时具有小垂向刚度,保证减振效果,在垂向载荷增大时通过橡胶凸台与轨枕顶面的接触,使减振本体的垂向刚度瞬时增加,形成变刚度拐点,使减振扣件承受垂向大载荷时具有限位保护刚度,提高承载能力保护钢轨,提高行车安全性,实现减振本体垂向小载荷小刚度、大载荷具有限位保护刚度的承载需求。
19.3.在外挡肩与内挡肩的橡胶层中设置隔板,增加内外挡肩之间的橡胶层的横向压缩刚度,使减振扣件的横向刚度呈非线性变化,在横向承载增大时减振扣件的横向刚度呈非线性增加,有效控制减振本体受横向载荷时的横向位移和翻转,从而控制钢轨轨头的横向位移,进一步提高钢轨的横向稳定性,减少钢轨横向磨损,提高减振扣件横向承载的可靠性。
20.4.将扣板上的安装孔设计为沉台孔,在安装孔的沉台中放置双层弹簧圈,螺栓旋紧到位双层弹簧圈被压缩,双层弹簧圈对顶板施加弹性压紧力,当顶板向上运动时双层弹簧圈的弹性压力限制其向上产生位移,使减振本体具有抗拔能力,延长减振本体的使用寿命。
21.5.轨道减振扣件在垂向具有刚度可调节及限位保护刚度的功能,在横向具有非线性刚度,保证横向稳定性的功能,在受力过程中具有抗拉拔保证结构稳定性的功能,满足承载过程中的刚度需求并保证结构的可靠性。
22.6.本发明的轨道减振扣件的刚度调节设计方法,根据轨道减振扣件的垂向刚度需求,设计顶板与底板之间的橡胶层的结构和厚度,根据轨道减振扣件的横向刚度需求,设计外挡肩与内挡肩之间的橡胶层的结构和厚度,即根据轨道减振扣件的实际承载工况对其进行刚度调节,保证减振扣件的减振可靠性,以提高钢轨在实际承载过程中的稳定性。
附图说明
23.图1为具体实施方式中轨道减振扣件装在枕轨上压紧钢轨的示意图。
24.图2为轨道减振扣件与钢轨的分解示意图。
25.图3为减振本体的剖视图。
26.图4为底板的示意图。
27.图5为顶板的示意图。
28.图6为扣板的示意图。
29.图7为轨道减振扣件的垂向刚度曲线图。
30.图8为轨道减振扣件的横向刚度曲线图。
具体实施方式
31.下面结合图1~8对本发明的实施例做详细说明。
32.轨道减振扣件,固定在轨枕1上,包括垫在轨枕1上的减振本体2、将减振本体2固定在轨枕1上的螺栓扣板组件3、将钢轨4压紧在减振本体2上的轨距块5和装在减振本体2上并压紧轨距块5的弹条6,其特征在于:所述的减振本体2包括底板7和通过橡胶层8与底板7硫化连接的顶板9,底板7两侧设有沿垂向的外挡肩10,顶板9上设有与外挡肩10相对应且位于外挡肩10内侧的内挡肩11,内挡肩11设置在钢轨4外侧,橡胶层8从顶板9底部向上伸延至内挡肩11和外挡肩10之间。
33.以上所述的轨道减振扣件,底板7和顶板9通过橡胶层8硫化成整体式结构的减振本体2,减振本体2无需零件组装成型,避免使用过程中减振本体2因零件内部摩擦而带动的结构磨损,延长减振本体2的使用寿命,橡胶从下至上一体硫化,实现了底板7、顶板9、内外挡肩和橡胶层8的一体化结构,确保了扣件具有高的减振效果和结构稳定性,减化扣件的结构,扣件维护保养更加简单方便。在底板7上设置外挡肩10,在顶板9上设置内挡肩11,橡胶层8从顶板9底部延伸至内外挡肩之间,增加轨道减振扣件的横向刚度,限制钢轨横向位移,有效控制减振本体受到横向力时带来的翻转,减小减振本体的横向弯矩,提高钢轨轨头的偏转刚度,控制钢轨轨头横向位移,减小因钢轨横向移动而产生的波磨,提高轨道减振扣件的横向稳定性。
34.其中,所述的底板7上开有与顶板9相对应的通孔71,顶板9通过橡胶层8硫化连接在通孔71中,通孔孔壁70为由外向内倾斜的倾斜面,顶板外侧壁为与通孔孔壁平行相对的倾斜面,使通孔孔壁与顶板外侧壁之间的橡胶层8呈由外向内倾斜的剪切结构。通孔孔壁70与顶板外侧壁之间呈剪切结构的橡胶层8,使橡胶层具有足够的压减变形空间,从而使减振本体的垂向静刚度较低,刚度平顺减振效果好,减振扣件承受垂向小载荷时具有小垂向刚度,保证减振效果。
35.其中,所述的顶板9底部的橡胶层8中开有向上凹进的底凹槽82,底凹槽82中至少具有一个向下凸出的橡胶凸台83,橡胶凸台83与轨枕1顶面隔开不接触。在垂向载荷增大时通过橡胶凸台83与轨枕1顶面的接触,使减振本体2的垂向刚度瞬时增加,形成变刚度拐点,使减振扣件承受垂向大载荷时垂向刚度增大至限位保护刚度,提高承载能力保护钢轨,提高行车安全性,实现减振本体垂向小载荷小刚度、大载荷具有限位保护刚度的承载需求。
36.其中,所述的通孔71呈工字型,通孔71中部具有两根沿底板长度方向设置的挡条72,两根挡条72在底板上对称分布,通孔孔壁70与顶板外侧壁之间的橡胶层8包括沿通孔长度方向设置的横向倾斜橡胶层和沿通孔宽度方向设置的纵向倾斜橡胶层81 ,横向倾斜橡胶层由外向内倾斜的角度大于纵向倾斜橡胶层81由外向内倾斜的角度。如图4所示,通孔71呈工字型,由两个孔联通形成,两个孔之间形成对称设置的挡条72,档条73增加底板7与顶板9的硫化连接面积,增加两者间硫化连接的可靠性,且通过挡条72可限制顶板9相对于底板7的横向和纵向位移,保证减振本体2的整体式结构的可靠性和稳定性,从图4中可以看出通孔孔壁70包括沿通孔长度方向设置的横向孔壁701和沿通孔宽度方向设置的纵向孔壁702,纵向孔壁702靠近外挡肩10,纵向孔壁702与底板顶面即水平面的夹角更小,其倾斜角度更小,纵向孔壁702与相对的顶板外侧壁之间的橡胶层8为纵向倾斜橡胶层81,纵向倾斜橡胶层81倾斜角度更小,其相对应的垂向静刚度会更大,而横向孔壁701与底板顶面即水平面的夹角更大,其倾斜角度更大,横向孔壁701与相对的顶板外侧壁之间的橡胶层8为横向倾斜橡胶层,横向倾斜橡胶层的倾斜角度更大,其相对应的垂向静刚度会更小,通过调节纵
向倾斜橡胶层81和横向倾斜橡胶层的倾斜角度和厚度,可调节减振本体2的垂向静刚度,即图7中o点到a点的斜率。
37.其中,所述的外挡肩10与底板7一体成型,外挡肩10为具有内腔的凹腔板,内挡肩11与顶板9一体成型,外挡肩10与内挡肩11之间的橡胶层8沿垂向设置且未将外挡肩10的内腔填满。外挡肩10具有向内凹进的内腔,内挡肩11呈板状,橡胶层8硫化连接内外挡肩,但并未将外挡肩10的内腔填满,使外挡肩10内腔中预留出橡胶层8压缩变形的流动空间,在减振本体2横向承载时内外挡肩间的橡胶层8被压缩,橡胶层8压缩变形向外挡肩10的内腔中流动,与外挡肩10内壁接触,可提高橡胶层8的刚度,同时避免橡胶层8因内外挡肩的相对横向位移过大而被压伤形成永久性损害,提高内外挡肩间橡胶层8的刚度提升速度,并防止橡胶层8损伤,延长橡胶层8的疲劳寿命;在外挡肩10与内挡肩11之间的橡胶层8中硫化至少一层沿垂直设置的隔板12,增加内外挡肩之间的橡胶层8的横向压缩刚度,使减振扣件的横向刚度呈非线性变化,在横向承载增大时减振扣件的横向刚度呈非线性增加,有效控制减振本体2受横向载荷时的横向位移和翻转,从而控制钢轨轨头的横向位移,进一步提高钢轨的横向稳定性,减少钢轨横向磨损,提高减振扣件横向承载的可靠性。设计隔板12的厚度和数量,可以调节轨道减振扣件在承载过程中的横向非线性刚度,保证轨道减振扣件在实际承载工况中满足横向刚度需求。
38.其中,所述的螺栓扣板组件3包括铺设在减振本体2上的扣板31、穿过扣板31、减振本体2并旋紧在轨枕1上的螺栓32和垫在扣板31顶面及底板且套在螺栓32上的垫圈33,底板7上开有锯齿形状的锯齿槽73,扣板31的底面设有与锯齿槽73配合的锯齿311,锯齿311伸入锯齿槽73中将扣板31定位在顶板9上,保证扣板31相对于底板7的定位可靠性,提高减振本体2固定在枕轨1上的稳定性。
39.其中,所述的扣板31上开有供螺栓贯穿的安装孔312,安装孔312为沉台孔,安装孔312的沉台中放置双层弹簧圈34,双层弹簧圈34随螺栓32的旋紧而被压缩在安装孔312中并压紧顶板9。将扣板31上的安装孔312设计为沉台孔,在安装孔312的沉台中放置双层弹簧圈34,螺栓旋紧到位双层弹簧圈34被压缩,双层弹簧圈34对顶板9施加弹性压紧力,当顶板9向上运动时双层弹簧圈34的弹性压力限制其向上产生位移,使减振本体具有抗拔能力,延长减振本体的使用寿命。
40.以上所述的轨道减振扣件在垂向具有刚度可调节及限位保护刚度的功能,在横向具有非线性刚度,保证横向稳定性的功能,在受力过程中具有抗拉拔保证结构稳定性的功能,满足承载过程中的刚度需求并保证结构的可靠性。
41.本发明还保护以上所述的轨道减振扣件的刚度调节设计方法,其特征在于:根据轨道减振扣件的垂向刚度需求,设计顶板9与底板7之间的橡胶层8的结构和厚度,以调节轨道减振扣件的垂向刚度;根据轨道减振扣件的横向刚度需求,设计外挡肩10与内挡肩11之间的橡胶层8的结构和厚度,以调节设计轨道减振扣件的横向刚度。
42.以上所述的轨道减振扣件的刚度调节设计方法,根据轨道减振扣件的垂向刚度需求,设计顶板9与底板7之间的橡胶层8的结构和厚度,根据轨道减振扣件的横向刚度需求,设计外挡肩10与内挡肩11之间的橡胶层8的结构和厚度,即根据轨道减振扣件的实际承载工况对其进行刚度调节,保证减振扣件的减振可靠性,以提高钢轨在实际承载过程中的稳定性。
43.其中,“设计顶板9与底板7之间的橡胶层8的结构和厚度,以调节轨道减振扣件的垂向刚度”是指设计通孔孔壁70与顶板外侧壁之间的橡胶层8的倾斜角度和厚度,以调节轨道减振扣件的垂向静刚度,设计橡胶凸台83与轨枕1顶面的间距,以调节轨道减振扣件在承载过程中的垂向变刚度拐点;“设计外挡肩10与内挡肩11之间的橡胶层8的结构和厚度,以调节设计轨道减振扣件的横向刚度特性”是指设计外挡肩10和内挡肩11之间的橡胶层8的厚度,以调节轨道减振扣件的横向初始刚度,设计外挡肩10与内挡肩11之间的橡胶层中隔板12的厚度和数量,以调节轨道减振扣件在承载过程中的横向非线性刚度。如图7所示的轨道减振扣件的垂向刚度曲线,a点为变刚度拐点,设计通孔71孔壁与顶板9外侧壁之间的橡胶层8的倾斜角度和厚度,调节垂向刚度曲线中oa的斜率,设计橡胶凸台83与轨枕1顶面的间距,调节产生变刚度拐点时顶板9底部的橡胶层8的压缩位移,以调节变刚度拐点在垂向刚度曲线中的位置,实现减振本体垂向小载荷小刚度、大载荷具有限位保护刚度的承载需求。如图8所示轨道减振扣件的横向刚度曲线,设计外挡肩10和内挡肩11之间的橡胶层8的厚度,调节横向刚度曲线的初始刚度,在内挡肩11和外挡肩10之间的橡胶层8中硫化隔板12,使横向刚度曲线呈非线性,设计外挡肩10与内挡肩11之间的橡胶层8中隔板12的厚度和数量,调节横向刚度曲线的陡峭度,即调节横向刚度在承载过程中的增加速度,以满足减振本体的横向刚度需求。
44.其中,“设计通孔孔壁71与顶板外侧壁之间的橡胶层8的倾斜角度和厚度”是指设计纵向倾斜橡胶层81和横向倾斜橡胶层的倾斜角度和厚度。从图4中可以看出通孔孔壁70包括沿通孔长度方向设置的横向孔壁701和沿通孔宽度方向设置的纵向孔壁702,纵向孔壁702靠近外挡肩10,纵向孔壁702与底板顶面即水平面的夹角更小,其倾斜角度更小,纵向孔壁702与相对的顶板外侧壁之间的橡胶层8为纵向倾斜橡胶层81,纵向倾斜橡胶层81倾斜角度更小,其相对应的垂向静刚度会更大,而横向孔壁701与底板顶面即水平面的夹角更大,其倾斜角度更大,横向孔壁701与相对的顶板外侧壁之间的橡胶层8为横向倾斜橡胶层,横向倾斜橡胶层的倾斜角度更大,其相对应的垂向静刚度会更小,通过调节纵向倾斜橡胶层81和横向倾斜橡胶层的倾斜角度和厚度,可调节减振本体2的垂向静刚度,即图7中o点到a点的斜率。
45.以上结合附图对本发明的实施例的技术方案进行完整描述,需要说明的是所描述的实施例仅仅是本发明的一部分实施例。基于本发明中的实施例,本领域普通技术人员在没有做出创造性劳动的前提下所获得的所有其他实施例,都属于本发明保护的范围。
再多了解一些
本文用于创业者技术爱好者查询,仅供学习研究,如用于商业用途,请联系技术所有人。