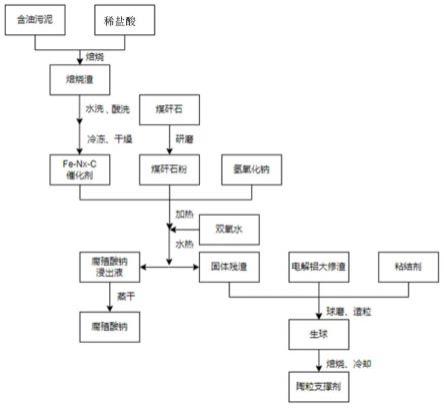
1.本发明属于固废资源化利用技术领域,具体涉及一种利用煤矸石制备石油开采用腐植酸钠和陶粒支撑剂的方法及其应用。
技术背景
2.目前煤炭开采、石油开采炼制过程以及铝冶炼过程都会产生大量的固体废物和危险废物。煤炭开采过程中会产生占原煤总产量15%~20%的煤矸石,天然直接堆存的煤矸石,经长期风吹日晒雨淋、氧化自燃等物理化学作用,随之会造成一系列的环境和生态问题。石油开采炼制过程产生大量含油污泥,其中含有高毒性致畸致癌的放射性物质、重金属和多环芳烃等,含油污泥已被许多国家认定为危险废物。电解铝行业电解槽每五年大修一次,大修时产生的废渣统称为大修渣,主要包括废阴极炭块、耐火材料、保温砖和吸附附着的电解质,露天堆放造成环境污染,属于危险废物。与此同时,煤矸石中含有20%~40%的碳、52%~65%的二氧化硅、16~36%的氧化铝以及少量氧化镁、氧化铁等,具有很高的再利用价值;含油污泥中富含碳氢化合物,可以以含油污泥为前躯体,制备低成本、高附加值的碳材料,如催化剂;大修渣成分复杂,含有碳化硅、氧化铝、氧化铁、氟化物等成分,也可进行二次利用。上述固废、危废均具有很高的再利用价值,选择合适的方法将其资源化,既做到合理处置,又能够变废为宝,产生经济价值。
3.石油开采过程中需要借助水力压裂技术使固体颗粒注入地下岩层,支撑起岩层裂缝,从而提高油气的通过率,这些固体颗粒称为石油压裂支撑剂。陶粒支撑剂的原料一般是含铝矿物,因此多生产于我国中部地区。而我国新疆地区含有大量的石油资源,开采过程需要大量陶粒支撑剂,需从距离较远的中部地区运输,导致产生了较高的运输成本。与此同时,新疆地区存有大量煤矸石,煤矸石中具有的丰富的氧化铝、二氧化硅成分,与陶粒主要的原料组分相同,可作为制备陶粒的原料。此外,石油开采过程中还需要腐植酸钠,其作为钻井液具有降滤失、降粘等作用,对安全高效钻井、防止钻井事故的发生有着重要的作用。因此,如果能够以煤矸石为主要原料制取腐植酸钠和陶粒支撑剂,不仅做到固体废物资源化利用为具有实际应用价值的产品,还可以就地取材,节省大量运输成本。
4.目前,已有学者利用煤矸石提取腐植酸钠,钟仁华等(中国专利申请cn202010764930.x一种煤矸石提取腐植酸的方法)将煤矸石颗粒与氢氧化钠溶液混合、过滤,将上清液与乙酸混合、沉淀得到腐植酸钠,然而该方法中煤矸石氧化程度低,导致腐植酸提取率低。同时,也有较多研究单位和研究者利用煤矸石制备陶粒支撑剂。苏根华等(cn202110095057.4一种煤矸石低密度石油陶粒支撑剂的制备工艺)利用煤矸石经过脱碳、脱水、脱硫后焙烧,制备出低密度石油陶粒支撑剂,然而,对于煤矸石中的碳组分并未进行有效利用,煤矸石利用率不高;高峰等(cn201910477980.7一种煤矸石基多孔陶粒支撑剂的制备方法)利用煤矸石做原料、碳粉做造孔剂,并加入二氧化锰进行焙烧,最终制备出多孔陶粒支撑剂,然而该方法不仅煤矸石利用率不高,还加入过多添加剂,增加了经济成本。由
此可见,目前缺少一种针对煤矸石制取腐植酸钠和陶粒支撑剂的高利用率、低成本的方法。
技术实现要素:
5.为了解决现有技术的缺点和不足之处,本发明的主要目的在于提供一种利用煤矸石制备石油开采用腐植酸钠和陶粒支撑剂的方法。
6.本发明的另一个目的在于提供上述利用煤矸石制备石油开采用腐植酸钠和陶粒支撑剂的方法的应用。
7.本发明的目的通过以下技术方案实现:
8.一种利用煤矸石制备石油开采用腐植酸钠和陶粒支撑剂的方法,包括如下步骤:
9.(1)将含油污泥和盐酸混合焙烧,洗涤、干燥,得到fe-n
x-c催化剂;
10.(2)将煤矸石、步骤(1)得到的fe-n
x-c催化剂和氢氧化钠混匀,于空气中200~400℃保温0.5~2h;然后加入双氧水,水热反应,得到腐植酸钠浸出液和固体残渣;
11.(3)将步骤(2)得到的腐植酸钠浸出液蒸干,即可得到腐植酸钠;
12.(4)将步骤(2)得到的固体残渣、电解铝大修渣和粘结剂混合,球磨造粒,得到生球;将生球高温焙烧,冷却,即得陶粒支撑剂。
13.步骤(1)中,所述的含油污泥优选为含有fe、c、n元素的污泥。
14.步骤(1)中,所述的盐酸优选为稀盐酸;进一步优选为1~4m、ph=2~3的稀盐酸;更优选为1m、ph=2的稀盐酸。
15.步骤(1)中,所述的含油污泥和盐酸优选按质量体积比(g:ml)5~10:3~5计算。
16.步骤(1)中,所述的焙烧的条件优选为:在氮气气氛中,以5℃/min的升温速率升温至300~600℃保温0.5~3h;更优选为:在氮气气氛中,以5℃/min的升温速率升温至500~600℃保温2h。
17.步骤(1)中,所述的洗涤优选为:先水洗再酸洗;进一步优选为先用去离子水洗、再用盐酸洗;更优选为先用去离子水洗、再用1m盐酸在回流条件下酸洗。
18.步骤(1)中,所述的干燥优选为冷冻干燥。
19.步骤(2)中,所述的煤矸石、fe-n
x-c催化剂和氢氧化钠优选按质量比20~100:0.5~3:5~20。
20.步骤(2)中,所述的保温优选为:200~400℃保温1~1.5h;更优选为200~300℃保温1~1.5h。
21.步骤(2)中,所述的煤矸石与双氧水优选按质量体积比g:ml 20~100:5~20计算。
22.步骤(2)中,所述的水热反应的条件优选为100~300℃、6~24h;更优选为100~120℃、12h。
23.步骤(4)中,所述的固体残渣、电解铝大修渣和粘结剂优选按质量比10~30:10~25:2~5计算。
24.步骤(4)中,所述的电解铝大修渣至少包括氧化铝和碳化硅;更优选包括如下组分:氧化铝、氟化物和碳化硅。
25.步骤(4)中,所述的粘结剂优选包括聚乙烯醇和羧甲基纤维素钠中的至少一种。
26.步骤(4)中,所述的高温焙烧的条件为:以5~10℃/min升温速率至1050~1200℃,保温0.5~2h。
27.一种腐植酸钠,通过上述方法制备得到。
28.一种陶粒支撑剂,通过上述方法制备得到。
29.所述的腐植酸钠、陶粒支撑剂和/或利用煤矸石制备石油开采用腐植酸钠和陶粒支撑剂的方法在固废资源化利用中的应用。
30.本发明的原理为:
31.(1)在催化剂的制备中,利用氯化焙烧法将含油污泥碳化,得到碳材料。在此过程中,通过含油污泥和盐酸混合焙烧得到纳米片结构;同时,酸性盐酸能够改变其中金属离子的存在形式,增加游离铁离子含量。然后铁离子与含油污泥中的含氮化合物(如吡咯、吡啶等)发生络合反应,铁元素经热解成功锚定在碳材料表面,经活化焙烧后,最终得到fe-n
x-c材料,表现出层次化的多孔结构,有较高的fe-n
x
含量,且fe-n
x
均匀分布在碳材料中,使得该fe-n
x-c催化剂具有优异的性能。发生的反应如下:
32.fe
3
c5h5n c
xhx
c6h6→
fe-n
x-c
33.(2)煤矸石中含有20%~40%的碳,加入氢氧化钠和fe-n
x-c催化剂,在空气气氛下,将煤矸石原料活化,随后通过双氧水和水热过程转变为腐植酸,并形成腐植酸钠。水热和氧化过程使腐植酸产生内聚合,腐植酸分子量增加,并生成新的活性基团,优化腐植酸钠性能;本发明氧化过程中加入纳米级催化剂fe-n
x-c,与反应物更加充分地接触,有利于催化氧化反应,提高腐植酸钠转化率,具有用量少但催化效果显著的特点;充分氧化使得本发明腐植酸钠产率更高,可达25.2%。发生的反应如下:
34.nnaoh r-(cooh)2→
r-(coona)n nh2o
35.(3)水热后剩余固体残渣为含铝固体,主要以氧化铝形式存在,含量达51%左右,其次是二氧化硅,而氧化铝和二氧化硅是制备陶粒的主要原料,其中二氧化硅起到骨架作用,氧化铝可以提高陶粒的强度。因此利用氧化铝含量更高的固体残渣,并进一步添加其他辅料,可将制成强度更高的陶粒支撑剂。此外,电解铝大修渣中含也有丰富的氧化铝,可进一步提升陶粒支撑剂强度。利用固体残渣与电解铝大修渣混合,并添加粘结剂,按照一定比例混合后造粒,随后进行高温焙烧,成品中形成刚玉相和莫来石相,保证了陶粒支撑剂的抗压强度。电解铝大修渣中含有碳化硅,在被烧过程中能够产生少量co2气体,使陶粒产生孔隙,在保证强度的同时降低密度,优化了陶粒支撑剂的性能;电解铝大修渣中所含有的氟化物在烧结过程中能够与硅、镁等物质形成mg7f2(sio4)3矿相,在提高抗压能力的同时减少氟的浸出率,减少环境污染;此外,煤矸石、电解铝大修渣中均含有的少量金属氧化物,如氧化铁等,在烧结过程中可充当烧结助剂,无需另外添加烧结剂而达到降低烧结温度的效果,从而节省成本。
36.与现有技术相比,本发明具有如下优点和有益效果:
37.本发明利用煤矸石、电解铝大修渣等固废、危废来制造陶粒,摆脱了传统陶粒制造技术中原料所需要的高品位铝矾土矿或不可再生的粘土资源,针对新疆地区石油产业对陶粒支撑剂和腐植酸钠的需求缺口,因地制宜,采用新疆大量存放的固体废物煤矸石作为腐植酸钠和陶粒的主要制备原料,就地取材,将废物资源化利用的同时节省运输成本。
38.本发明有效利用原料中存在的各个组分:有效利用煤矸石中的大量碳、氧化铝、二氧化硅等主要成分,实现了对煤矸石的高度资源化利用;此外,有效利用了辅料的固体废物中存在的其他元素,如可以利用电解铝大修渣中的碳化硅作为发泡剂、利用氟化物提高抗
压强度、利用金属氧化物作为烧结助剂降低温度,不仅降低烧结温度,还减小陶粒密度、增强陶粒强度,实现陶粒性能的进一步优化。按照本发明所述的利用煤矸石制备石油开采用腐植酸钠和陶粒支撑剂的方法可得到20~40目陶粒支撑剂成品,其体积密度为1.02g/cm3,52mpa闭合压力下的破碎率为4.9%,满足石油开采使用需求。
39.本发明发现并制备了一种纳米级催化剂——利用含油污泥制备的fe-n
x-c催化剂,不仅对危险废物含油污泥进行了有效处置和资源化利用,还使腐植酸钠产率提高至25%以上。按照本发明所述的利用煤矸石制备石油开采用腐植酸钠和陶粒支撑剂的方法制备的腐植酸钠成品的各项指标为:水分8.5%,ph为9.4,筛余量7.0%,室温下降粘率为75.8%,滤失量降低率为41.3%,符合相关国家标准;本发明所述方法制备的腐植酸钠也可进一步加工,与尿素、苯酚等进行合成,制备性能更好的降滤失剂、降粘剂等。
40.综上,本发明对多种固废进行了资源化利用,产生具有实际应用价值的两种产品,不仅减轻废物带来的环境污染,还减少了珍稀资源的使用,有利于绿色、环保、可持续发展。
附图说明
41.图1为利用煤矸石制备石油开采用腐植酸钠和陶粒支撑剂的方法流程图。
42.图2为fe-n
x-c催化剂的sem图。
43.图3为fe-n
x-c催化剂的tem图。
44.图4为20~40目陶粒支撑剂的实物图。
45.图5为对比例2制备得到的含铁催化剂的实物图。
具体实施方式
46.下面结合具体实施例对本发明做进一步说明,但本发明所保护范围不局限于所述内容。
47.以下实施例中所用煤矸石均来源于新疆昌吉市硫磺沟镇的硫磺沟矿井;煤矸石包括如下质量分数的各组分:sio
2 35.97%、al2o
3 23.74%、mgo 2.72%、fe2o
3 2.20%、s 0.07%、c 32.42%。
48.含油污泥取自中国石油化工股份有限公司的储罐清洗油泥,为流动性好的黑色浆料;含油污泥包括如下质量分数的各组分:有机元素:c 22.23%、h 4.895%、o 29.672%、n 1.84%、s 2.702%、无机元素:fe 8.82%、si 5.78%、ca 6.24%、al 7.38%、na 3.78%、mg 0.36%。
49.电解铝大修渣取自新疆新能源(集团)环境发展有限公司;电解铝大修渣包括如下质量分数的各组分:al2o
3 25.3%、氟化物7.9%、na 12.6%、sic 6.7%、ca 5.3%、fe2o
3 3.1%、氰化物0.04%、c 15.6%。
50.实施例1:
51.一种利用煤矸石制备石油开采用腐植酸钠和陶粒支撑剂的方法,流程如图1所示。具体包括如下步骤:
52.(1)将5g含油污泥、3ml稀盐酸(1m、ph=2)混合研磨2h置于管式炉,在氮气气氛下,以5℃/min的升温速率加热至500℃并保持2h;焙烧结束后依次用去离子水进行水洗、1m hcl在80℃下回流12h进行酸洗,最后冷冻干燥,得到fe-n
x-c催化剂;
53.(2)将煤矸石研磨至200目,取20g煤矸石粉加入0.5g fe-n
x-c催化剂、氢氧化钠5g混合均匀,在空气气氛加热至200℃,保持60分钟;随后加入5ml双氧水,并在水热反应釜中120℃下进行12h水热反应,得到腐植酸钠浸出液和固体残渣;
54.经测定,固体残渣包括如下质量分数的各组分:sio
2 30.43%、al2o
3 51.62%、mgo 5.33%、fe2o
3 2.41%、s 0.07%、c 7.60%。
55.(3)将步骤(2)得到的腐植酸钠浸出液蒸发、干燥后得到5.04g腐植酸钠;
56.(4)取步骤(2)得到的固体残渣10g与10g电解铝大修渣和2g羧甲基纤维素钠(cas号:9004-32-4)粘结剂混合,球磨至200目,加水造粒得到20~40目生球,在箱式烧结炉中以5℃/min升温速率至1100℃焙烧,保温2小时,冷却后得到20~40目陶粒支撑剂。
57.本实施例得到的fe-n
x-c催化剂是一种纳米级碳材料,图2为其sem图,由图可见,该催化剂由多孔碳纳米片堆积的块装材料与少量褶皱片层组成,具有层次化的多孔结构和明显的不规则取向堆积。图3为其tem图,由图可见,fe以纳米颗粒状均匀地分散在碳材料上。
58.本实施例腐植酸钠产率为25.2%,得到的腐植酸钠成品水分8.5%,ph为9.4,筛余量7.0%,室温下降粘率为75.8%,滤失量降低率为41.3%,符合相关国家标准;
59.陶粒支撑剂成品如图4所示,大小为20~40目,体积密度为1.02g/cm3,52mpa闭合压力下的破碎率为4.9%,69mpa闭合压力下的破碎率为6.8%,满足石油开采使用需求。
60.实施例2:
61.一种利用煤矸石制备石油开采用腐植酸钠和陶粒支撑剂的方法,包括如下步骤:
62.(1)使用球磨机将煤矸石研磨至200目,取1g fe-n
x-c催化剂(fe-n
x-c催化剂按照实施例1步骤(1)制备)、50g煤矸石粉末和氢氧化钠10g混合均匀,在空气气氛加热至250℃,保持90分钟;随后加入15ml双氧水进一步氧化,并在水热反应釜中100℃下进行12h水热反应,得到腐植酸钠浸出液和固体残渣;
63.经测定,固体残渣包括如下质量分数的各组分:sio
2 28.53%、al2o
3 49.32%、mgo 4.73%、fe2o
3 4.35%、s 0.11%、c 8.57%。
64.(2)将步骤(1)得到的腐植酸钠浸出液蒸干后得到腐植酸钠11.81g;
65.(3)取步骤(1)得到的固体残渣30g与25g电解铝大修渣混合,使用球磨机球磨至200目,加入5g/ml聚乙烯醇1ml作为粘结剂,使用ro型爱立许造粒机造粒得到20~40目生球,在箱式烧结炉中以5℃/min升温速率至1200℃焙烧,保温2小时,冷却后得到20~40目陶粒支撑剂。
66.本实施例腐植酸钠产率为23.6%,得到的腐植酸钠成品水分8.2%,ph为8.6,筛余量7.4%,室温下降粘率为76.3%,滤失量降低率为41.9%,符合相关国家标准;
67.陶粒支撑剂成品为20~40目,体积密度为0.96g/cm3,52mpa闭合压力下的破碎率为3.4%,69mpa闭合压力下的破碎率为5.6%,符合国家标准,满足石油开采使用需求。
68.实施例3:
69.一种利用煤矸石制备石油开采用腐植酸钠和陶粒支撑剂的方法,包括如下步骤:
70.(1)将10g含油污泥、5ml稀盐酸(1m、ph=2)混合研磨3h置于管式炉,在氮气气氛下,以5℃/min的升温速率加热至600℃并保持2h;焙烧结束后依次用去离子水进行水洗、1m hcl在80℃下回流12h进行酸洗,最后冷冻干燥,得到fe-n
x-c催化剂;
71.(2)将煤矸石研磨至200目,取100g煤矸石粉加入3.0g fe-n
x-c催化剂、氢氧化钠20g混合均匀,在空气气氛加热至300℃,保持90分钟;随后加入20ml双氧水,并在水热反应釜中120℃下进行12h水热反应,得到腐植酸钠浸出液和固体残渣;
72.经测定,固体残渣包括如下质量分数的各组分:sio
2 30.79%、al2o
3 48.36%、mgo 5.67%、fe2o
3 3.94%、s 0.09%、c 10.32%。
73.(3)将步骤(2)得到的腐植酸钠浸出液蒸发、干燥后得到24.43g腐植酸钠;
74.(4)取步骤(2)得到的固体残渣20g与20g电解铝大修渣和4g羧甲基纤维素钠(cas号:9004-32-4)粘结剂混合,球磨至200目,加水造粒得到20~40目生球,在箱式烧结炉中以5℃/min升温速率至1150℃焙烧,保温2小时,冷却后得到20~40目陶粒支撑剂。
75.本实施例腐植酸钠产率为24.4%,得到的腐植酸钠成品水分7.8%,ph为8.6,筛余量8.4%,室温下降粘率为78.3%,滤失量降低率为40.9%,符合相关国家标准;
76.陶粒支撑剂成品为20~40目,体积密度为1.22g/cm3,52mpa闭合压力下的破碎率为4.4%,69mpa闭合压力下的破碎率为6.4%,符合国家标准,满足石油开采使用需求。
77.对比例1:不加fe-n
x-c催化剂对腐植酸钠产率的影响
78.将煤矸石研磨至200目,取50g煤矸石粉末和氢氧化钠10g混合均匀,在空气气氛加热至300℃,保持90分钟;随后加入20ml双氧水,并在水热反应釜中120℃下进行12h水热反应,得到腐植酸钠浸出液,蒸发、干燥;计算腐植酸钠产率。
79.经计算,腐植酸钠产率仅为15.6%。
80.对比例2:不加盐酸对催化剂形成及腐植酸钠产率的影响
81.(1)将10g含油污泥研磨3h置于管式炉,在氮气气氛下,以5℃/min的升温速率加热至600℃并保持2h;焙烧结束后依次用去离子水进行水洗、1m hcl在80℃下回流12h进行酸洗,最后冷冻干燥,得到含铁催化剂,如图5;从图5可以看出,该含铁催化剂分布不均匀、呈现大颗粒状。
82.(2)将煤矸石研磨至200目,取100g煤矸石粉加入3.0g含铁催化剂、氢氧化钠20g混合均匀,在空气气氛加热至300℃,保持90分钟;随后加入20ml双氧水,并在水热反应釜中120℃下进行12h水热反应,得到腐植酸钠浸出液,蒸发、干燥得到腐植酸钠。
83.经计算,腐植酸钠产率仅为16.3%。与实施例3的结果对比可知,加入盐酸有利于纳米级催化剂的形成,并提高腐植酸钠的产率。
84.对比例3:无盐酸、双氧水处理对腐植酸钠产率的影响
85.将煤矸石研磨至200目,取50g煤矸石粉末和氢氧化钠10g混合均匀,在空气气氛加热至300℃,保持90分钟;在水热反应釜中120℃下进行12h水热反应,得到腐植酸钠浸出液,蒸发、干燥;计算腐植酸钠产率。
86.经计算,腐植酸钠产率仅为7.1%。可见,过氧化氢作为绿色氧化剂,其反应副产物为水,对环境无害,作为制备腐植酸钠的氧化剂有利于提高腐殖酸钠的产率。
87.对比例4:固体残渣与电解铝大修渣作为制备陶瓷支撑剂原料
88.取煤矸石30g与25g电解铝大修渣混合,使用球磨机球磨至200目,加入5g/ml聚乙烯醇1ml作为粘结剂,使用ro型爱立许造粒机造粒得到20~40目生球,在箱式烧结炉中以5℃/min升温速率至1200℃焙烧,保温2小时,冷却后得到陶粒支撑剂。
89.所得陶粒支撑剂的体积密度为0.93g/cm3。52mpa闭合压力下的破碎率为7.3%,
69mpa闭合压力下的破碎率为10.4%。可见,当直接使用煤矸石和电解铝大修渣制备陶粒支撑剂时,所得成品抗压强度低,而实施例2使用铝含量更高的固体残渣制备陶粒支撑剂效果更优。
90.上述实施例为本发明较佳的实施方式,但本发明的实施方式并不受上述实施例的限制,其他的任何未背离本发明的精神实质与原理下所作的改变、修饰、替代、组合、简化,均应为等效的置换方式,都包含在本发明的保护范围之内。
再多了解一些
本文用于创业者技术爱好者查询,仅供学习研究,如用于商业用途,请联系技术所有人。