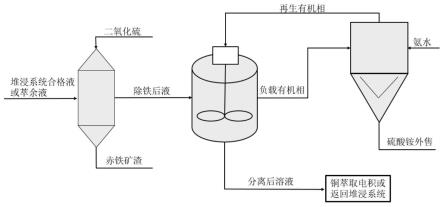
1.本发明属于有色金属冶炼领域,具体涉及一种利用次生硫化铜矿生物堆浸系统中有价元素的方法。
背景技术:
[0002]“生物堆浸-萃取-电积”流程作为一种处理低品位矿石的工艺,具有资源利用高效、工艺流程短、生产成本低、污染小等优点,越来越受到人们的重视,尤其在处理低品位次生硫化铜铜矿中得到了广泛应用,目前全球有近20座次生硫化铜矿矿山采用该项技术。
[0003]
次生硫化铜矿中往往伴生有黄铁矿,在次生硫化铜矿生物堆浸过程中,黄铁矿发生氧化反应产生三价铁与硫酸,氧化放出的热量以及产生的三价铁促进次生硫化铜矿的浸出。但如果次生硫化铜矿中伴生的黄铁矿较多,而耗酸脉石较少的情况下,随着溶液不断在系统中循环,黄铁矿的氧化会导致系统中酸铁积累过剩,萃取返酸以及沉矾产酸等因素也会加剧系统中酸过剩的情况,从而对后续萃取-电积生产带来不利影响。首先,如果进入萃取的合格液酸浓度过高,会降低萃取效率,减少铜传递量,最终导致阴极铜产量受限;其次,合格液的铁浓度过高,会导致电积液中含铁量过高,严重影响电流效率,造成生产成本过高。堆浸系统化学反应如下:
[0004]
(1)辉铜矿浸出—铜萃取过程
[0005]
辉铜矿氧化:cu2s 5o2 h2so4=2cuso4 h2o
[0006]
辉铜矿浸出:cu2s 2fe2(so4)3=2cuso4 4feso4 s
[0007]
萃取返酸:cuso4 2hr=cur2 h2so4[0008]
(2)黄铁矿氧化产酸产铁过程
[0009]
黄铁矿氧化:4fes2 15o2 2h2o=2fe2(so4)3 2h2so4[0010]
fe
3
成矾:3fe
3
2so4
2- 7h2o=(h3o)fe3(so4)2(oh)6↓
5h
[0011]
在生产实际中,通常采用开路部分萃余液后利用石灰或者石灰石中和的方法来降低系统中的酸铁度,但此方法一方面成本较高,另一方面产生的中和渣对环境影响巨大。“一种生物冶金过程中利用铁矾生成实现铁平衡的方法”(cn101984095a)中提出了控制堆浸体系酸和铁浓度的方法,使铁在矿堆内部沉矾、萃余液利用石灰石中和自由酸后再返回堆场喷淋,该方法会产生大量中和渣,存在堆存占用空间、污染周边环境、夹带铜金属损失等缺点,而且铁矾覆盖在矿石表面会阻碍铜矿物的浸出;“一种硫化铜矿生物堆浸系统调控酸和铁的方法”(cn107354298b)提出可以通过每层堆浸单元浸出完成后,在上层铺设一定粒度、厚度的石灰石,通过对石灰石层厚度的控制,来调节堆浸系统中的酸铁浓度,但这种方法仅能在初期对系统中的酸铁浓度作出一定调整,随着堆浸的进行,石灰石消耗以及石灰石表面与硫酸反应钝化,将不会再起到相应的作用。
技术实现要素:
[0012]
(一)要解决的技术问题
[0013]
本发明要解决的技术问题是:如何提供一种降低次生硫化铜矿生物堆浸系统中酸铁浓度的方法用于解决次生硫化铜矿堆浸系统中酸铁积累过剩以及萃取返酸导致系统中酸过剩的问题。
[0014]
(二)技术方案
[0015]
为解决上述技术问题,本发明提供一种降低次生硫化铜矿生物堆浸系统中酸铁浓度的方法,其包括以下步骤:
[0016]
步骤1:向堆浸系统合格液或萃余液中通入二氧化硫,启动搅拌机促使二氧化硫与溶液充分混合,控制通气速度10~100l/l-液
·
h,反应时间2~4h,将合格液或萃余液中的fe
3
还原fe
2
;
[0017]
步骤2:控制合格液或萃余液中fe
2
氧化水解过程反应时间为1-4h、反应温度为180~200℃、氧分压400~500kpa,fe
2
经氧化水解后生成固相赤铁矿渣,实现铜铁分离,将固相赤铁矿渣排出堆浸系统,主要反应如下:
[0018]
2feso4 0.5o2 2h2o=fe2o3↓
2h2so4ꢀꢀꢀꢀꢀꢀꢀꢀꢀꢀꢀ
(1);
[0019]
步骤3:按一定比例的三(2-乙基己基)胺、磺化煤油和异构十三醇配置萃取液,采用三级逆流萃取工序与步骤2中除铁后液充分搅拌混合,使除铁后液中硫酸从水相被萃取到有机相,设三级反萃,选用水作为反萃剂,将萃取产生的负载有机相与水充分搅拌混合,使负载相中酸进入水相中,获得稀酸溶液,反映方程式如下;
[0020][0021][0022]
步骤4:将步骤3反萃后溶液经过澄清分离后,所得酸铁浓度降低后溶液送至铜萃取-电积系统生产阴极铜或返回堆浸系统,所得稀酸溶液排除堆浸系统外。
[0023]
其中,所述步骤3中萃取液中各项试剂配置比例为:
[0024]
所述三(2-乙基己基)胺配置比例为40%-50%;
[0025]
所述磺化煤油配置比例为10%-20%;
[0026]
所述异构十三醇配置比例为35%-40%。
[0027]
其中,在给定温度下将负载有机相经水反萃后得到回收产品纯稀硫酸溶液,再生后的有机相循环使用,所述反萃反应是步骤3中反应式(2)与(3)的逆过程。
[0028]
其中,所述步骤3中当用水作为反萃剂时,反萃取温度为20~30℃。
[0029]
其中,所述的萃取方式中萃取条件为温度30℃、相比a/o=1:2~1:3,经过3级萃取。
[0030]
其中,所述的萃取方式中反萃条件为温度30℃、相比a/o=2:1~1:1,经过3级反萃。
[0031]
其中,所述除铁和萃取方法适用于湿法冶金生物堆浸领域或者其他需要调解系统中溶液酸铁度的技术领域。
[0032]
(三)有益效果
[0033]
与现有技术相比较,本发明具备如下有益效果:
[0034]
1)本发明通过赤铁矿除铁工艺降低堆浸系统溶液或萃余液的铁浓度,其工艺除铁效率高且无需添加剂。
[0035]
2)本发明通过溶剂萃取的方法降低堆浸系统溶液的酸度,利于产出低酸度的合格液,保证萃取过程的铜传递量。
[0036]
3)相较于传统中和法,本发明可有效避免中和渣产生及处理成本,而且不引入其他杂质元素。
附图说明
[0037]
图1为本发明方法流程图。
具体实施方式
[0038]
为使本发明的目的、内容、和优点更加清楚,下面结合附图和实施例,对本发明的具体实施方式作进一步详细描述。
[0039]
为解决上述技术问题,本实施例提供一种降低次生硫化铜矿生物堆浸系统中酸铁浓度的方法,如图1所示,其包括以下步骤:
[0040]
步骤1:向堆浸系统合格液或萃余液中通入二氧化硫,启动搅拌机促使二氧化硫与溶液充分混合,控制通气速度10~100l/l-液
·
h,反应时间2~4h,将合格液或萃余液中的fe
3
还原fe
2
;
[0041]
步骤2:控制合格液或萃余液中fe
2
氧化水解过程反应时间为1-4h、反应温度为180~200℃、氧分压400~500kpa,fe
2
经氧化水解后生成固相赤铁矿渣,实现铜铁分离,将固相赤铁矿渣排出堆浸系统,主要反应如下:
[0042]
2feso4 0.5o2 2h2o=fe2o3↓
2h2so4ꢀꢀꢀꢀꢀꢀꢀꢀꢀꢀꢀ
(1);
[0043]
步骤3:按一定比例的三(2-乙基己基)胺、磺化煤油和异构十三醇配置萃取液,采用三级逆流萃取工序与步骤2中除铁后液充分搅拌混合,使除铁后液中硫酸从水相被萃取到有机相,设三级反萃,选用水作为反萃剂,将萃取产生的负载有机相与水充分搅拌混合,使负载相中酸进入水相中,获得稀酸溶液,反映方程式如下;
[0044][0045][0046]
步骤4:将步骤3反萃后溶液经过澄清分离后,所得酸铁浓度降低后溶液送至铜萃取-电积系统生产阴极铜或返回堆浸系统,所得稀酸溶液排除堆浸系统外。
[0047]
其中,所述步骤3中萃取液中各项试剂配置比例为:
[0048]
所述三(2-乙基己基)胺配置比例为40%-50%;
[0049]
所述磺化煤油配置比例为10%-20%;
[0050]
所述异构十三醇配置比例为35%-40%。
[0051]
其中,在给定温度下将负载有机相经水反萃后得到回收产品纯稀硫酸溶液,再生后的有机相循环使用,所述反萃反应是步骤3中反应式(2)与(3)的逆过程。
[0052]
其中,所述步骤3中当用水作为反萃剂时,反萃取温度为20~30℃。
[0053]
其中,所述的萃取方式中萃取条件为温度30℃、相比a/o=1:2~1:3,经过3级萃取。
[0054]
其中,所述的萃取方式中反萃条件为温度30℃、相比a/o=2:1~1:1,经过3级反
萃。
[0055]
其中,所述除铁和萃取方法适用于湿法冶金生物堆浸领域或者其他需要调解系统中溶液酸铁度的技术领域。
[0056]
实施例1
[0057]
为解决上述技术问题,本发明提供一种利用次生硫化铜矿生物堆浸系统中有价元素的方法,如图1所示,本发明所处理的高酸铁合格液含铜3.7g/l,酸浓度8.6g/l,铁浓度14.7g/l,具体工序操作、控制条件和试验结果如下:
[0058]
(1)fe
3
还原过程控制:向合格液中通入二氧化硫,启动搅拌促使与溶液充分混合,控制通气速度50~80l/(l-液
·
h),反应时间2.5h。
[0059]
(2)fe
2
氧化水解过程控制:控制反应温度为180℃、氧分压400kpa的操作条件,反应时间4h,fe
2
经氧化水解后生成固相赤铁矿渣(fe2o3)。
[0060]
(3)萃取液配置:萃取剂由胺类萃取剂、稀释剂和相调节剂组成,配方为40%三(2-乙基己基)胺(teha),20%磺化煤油,40%异构十三醇。
[0061]
(4)采用逆流萃取工序使合格液与上述萃取液充分搅拌混合。萃取条件为温度30℃、相比a/o=1:3,经过3级萃取。反萃条件为水作为反萃剂,温度30℃、相比a/o=1:1,经过3级反萃。反萃取温度为30℃。
[0062]
(5)试验结果:除铁率90%,产出的赤铁矿渣含铁59%、含铜小于0.5%、含硫小于2%,经处理后可作为炼铁或生产水泥等的原料;经3级萃取和3级反萃,硫酸总萃取率为90%以上,总反萃取率为94%以上,出口水相酸的质量浓度为6g/l左右,产品酸的质量浓度为7g/l左右,且为纯净硫酸溶液。
[0063]
实施例2
[0064]
参见图1,本发明所处理的高酸铁合格液含铜5.1g/l,酸浓度13.5g/l,铁浓度32g/l,具体工序操作、控制条件和试验结果如下:
[0065]
(1)fe
3
还原过程控制:向合格液中通入二氧化硫,启动搅拌促使与溶液充分混合,控制通气速度50~80l/(l-液
·
h),反应时间3.5h。
[0066]
(2)fe
2
氧化水解过程控制:控制反应温度为190℃、氧分压400kpa的操作条件,反应时间3h,fe
2
经氧化水解后生成固相赤铁矿渣(fe2o3)。
[0067]
(3)萃取液配置:萃取剂由胺类萃取剂、稀释剂和相调节剂组成,配方为45%三(2-乙基己基)胺(teha),20%磺化煤油,35%异构十三醇。
[0068]
(4)采用逆流萃取工序使合格液与上述萃取液充分搅拌混合。萃取条件为温度30℃、相比a/o=1:2,经过3级萃取。反萃条件为水作为反萃剂,温度30℃、相比a/o=1:1,经过3级反萃。反萃取温度为30℃。
[0069]
(5)试验结果:除铁率91%,产出的赤铁矿渣含铁61%、含铜小于0.5%、含硫小于2%,经处理后可作为炼铁或生产水泥等的原料;经3级萃取和3级反萃,硫酸总萃取率为90%以上,总反萃取率为95%以上,出口水相酸的质量浓度为8g/l左右,产品酸的质量浓度为12g/l左右,且为纯净硫酸溶液。
[0070]
实施例3
[0071]
参见图1,本发明所处理的高酸铁合格液含铜7.2g/l,酸浓度23g/l,铁浓度49g/l,具体工序操作、控制条件和试验结果如下:
[0072]
(1)fe
3
还原过程控制:向合格液中通入二氧化硫,启动搅拌促使与溶液充分混合,控制通气速度60~100l/(l-液
·
h),反应时间4h。
[0073]
(2)fe
2
氧化水解过程控制:控制反应温度为200℃、氧分压400kpa的操作条件,反应时间2h,fe
2
经氧化水解后生成固相赤铁矿渣(fe2o3)。
[0074]
(3)萃取液配置:萃取剂由胺类萃取剂、稀释剂和相调节剂组成,配方为50%三(2-乙基己基)胺(teha),10%磺化煤油,40%异构十三醇。
[0075]
(4)采用逆流萃取工序使合格液与上述萃取液充分搅拌混合。萃取条件为温度30℃、相比a/o=1:2,经过3级萃取。反萃条件为水作为反萃剂,温度30℃、相比a/o=2:1,经过3级反萃。反萃取温度为30℃。
[0076]
(5)试验结果:除铁率92%,产出的赤铁矿渣含铁65%、含铜小于0.5%、含硫小于2%,经处理后可作为炼铁或生产水泥等的原料;经3级萃取和3级反萃,硫酸总萃取率为90%以上,总反萃取率为94%以上,出口水相酸的质量浓度为9g/l左右,产品酸的质量浓度为20g/l左右,且为纯净硫酸溶液。
[0077]
实施例4
[0078]
参见图1,本发明所处理的高酸铁萃余液含铜1.64g/l,酸浓度17g/l,铁浓度37g/l,具体工序操作、控制条件和试验结果如下:
[0079]
(1)fe
3
还原过程控制:向合格液中通入二氧化硫,启动搅拌促使与溶液充分混合,控制通气速度60~100l/(l-液
·
h),反应时间3.5h。
[0080]
(2)fe
2
氧化水解过程控制:控制反应温度为200℃、氧分压400kpa的操作条件,反应时间2h,fe
2
经氧化水解后生成固相赤铁矿渣(fe2o3)。
[0081]
(3)萃取液配置:萃取剂由胺类萃取剂、稀释剂和相调节剂组成,配方为45%三(2-乙基己基)胺(teha),20%磺化煤油,35%异构十三醇。
[0082]
(4)采用逆流萃取工序使合格液与上述萃取液充分搅拌混合。萃取条件为温度30℃、相比a/o=1:2,经过3级萃取。反萃条件为水作为反萃剂,温度30℃、相比a/o=1:1,经过3级反萃。反萃取温度为30℃。
[0083]
(5)试验结果:除铁率92%,产出的赤铁矿渣含铁64%、含铜小于0.5%、含硫小于2%,经处理后可作为炼铁或生产水泥等的原料;经3级萃取和3级反萃,硫酸总萃取率为90%以上,总反萃取率为95%以上,出口水相酸的质量浓度为9g/l左右,产品酸的质量浓度为15g/l左右,且为纯净硫酸溶液。
[0084]
以上所述仅是本发明的优选实施方式,应当指出,对于本技术领域的普通技术人员来说,在不脱离本发明技术原理的前提下,还可以做出若干改进和变形,这些改进和变形也应视为本发明的保护范围。
再多了解一些
本文用于创业者技术爱好者查询,仅供学习研究,如用于商业用途,请联系技术所有人。