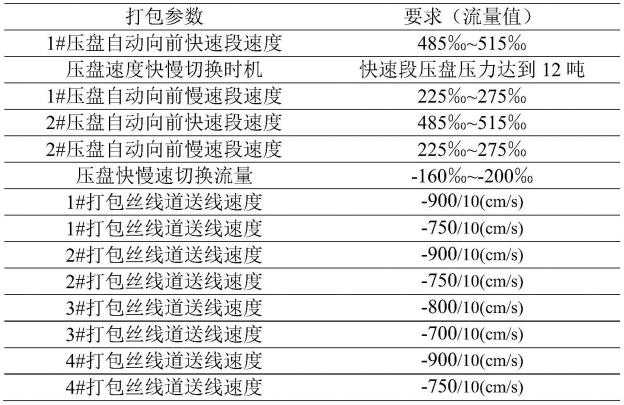
一种利用55sicr热轧盘条吐丝超前量和打包模式来减少打包挤压伤方法
技术领域
1.本发明属于轧钢技术领域,具体涉及一种利用55sicr热轧盘条吐丝超前量和打包模式来减少打包挤压伤方法,具体的说是一种基于高速热轧盘条生产线、通过控制终轧速度与吐丝速度差量,实现控制盘条内圈径、整体包形和包长,以匹配特定打包模式,来减少55sicr热轧盘条打包挤压伤的方法。
背景技术:
2.55sicr热轧盘条作为目前主流的悬架弹簧原材料,为保证悬架弹簧最终的疲劳强度和寿命,对于盘条表面质量有着很高要求。一般55sicr热轧盘条目前应用于悬架弹簧,最多是φ13.0~16.0mm两火材,疲劳寿命要求50万次以上,工作应力强度可达1850~2050mpa,在如此高的应力条件下,原材料表面质量要求就特别高。
3.目前,55sicr热轧盘条表面应光滑,不应有裂纹、折叠、耳子、结疤、分层及夹杂;允许有局部的压痕、凸块、划痕及麻点,其深度或高度从实际尺寸算起应不大于0.07mm。对以上的各类缺陷,国内外各大钢企都已基本形成一套相对可靠的控制经验,上述缺陷发生的频次正在日益减少。除此之外,造成原材料表面缺陷一个主要环节就是盘条的打包过程,主要会造成盘条与盘条之间的挤压伤,形貌上有条状挤压伤、点状挤压伤、打包丝磕碰勒伤等三类,一般打包挤压伤深度均在0.07mm以上,如果去除不干净,会对最终的悬架弹簧疲劳寿命造成直接影响,疲劳寿命可能大幅度降低。
4.汽车悬架弹簧55sicr一般的加工工艺都是抛丸-预拉拔-探伤-修磨-拉拔-热处理-探伤-成品钢丝,但如果原材料热轧盘条表面存在大量的打包挤压伤,会很大程度影响修磨工序的工作效率,正常的一包1.9吨盘条从抛丸到修磨结束的时间在30~45min,表面打包挤压伤多的盘条同样1.9吨,从抛丸到修磨结束可以需要120~180min,大大降低了汽车悬架弹簧钢丝生产效率。一般主流的汽车悬架弹簧钢丝生产企业都希望上游原材料供应商可以将单包的原材料缺陷按照0.05mm精度进行涡流探伤,控制在100个点之内,少数企业行车先进企业要求缺陷≤60点/包。
5.综上对于55sicr热轧盘条表面质量,特别是打包挤压伤的控制,也就尤为重要。传统的思路都是调试好特定的打包程序,通过优化打包过程来减少和控制打包挤压伤的数量,生产性的预防控制方法较少,如何从轧制、冷却过程来控制盘条内圈径、整体包形和包长,以匹配特定打包模式,从而预防后道打包挤压伤的方法还较为空白。
技术实现要素:
6.本发明的目的在于提供一种利用55sicr热轧盘条吐丝超前量和打包模式来减少打包挤压伤方法,核心是基于高速热轧盘条生产线、通过控制终轧速度与吐丝速度差量,实现控制盘条内圈径、整体包形和包长,以匹配特定打包模式,来减少55sicr热轧盘条打包挤压伤的方法。所述得到的盘条内圈径92~105mm,打包前盘条包长稳定在180~210cm,包形
紧凑,错圈均匀,打包过程无盘条挤压声,打包后包形完好,不易塌包、斜包,可多层堆放、运输,包长控制在150~160cm,拆包检查目视可见打包挤压伤在45~60点/包,下游客户下料涡流探伤按照0.05mm缺陷点数稳定控制在≤60点/包。
7.为了达到上述技术目的,本发明提供了一种利用55sicr热轧盘条吐丝超前量和打包模式来减少打包挤压伤方法,钢坯加热、控制轧制、吐丝振摆、吐丝超前量、防挤压伤模式打包,具体工艺步骤如下:
8.(1)钢坯在蓄热式加热炉800~1150℃的温度环境中加热85~140min;
9.(2)钢坯出加热炉后,以800~950℃分别经过粗、中、精轧变形和mini轧机变形;
10.(3)轧后通过调节水箱流量,使吐丝温度控制在860~910℃;
11.(4)吐丝机开启振摆“322”模式,即摆动周期3秒/次、左右摆动幅度
±
2.0%;
12.(5)控制吐丝超前量在-3.0%~-4.5%,即吐丝速度要慢于轧件出mini轧机的速度3.0%~4.5%;保证盘条内圈径92~105mm,包长稳定在180~210cm,匹配后续打包模式;
13.(6)吐丝后上斯太尔摩风冷线,落料集卷。
14.(7)采用西门子打包机进行打包,打包丝采用φ8mmdbs-2打8道,打捆压力设定12吨,打包模式弹簧钢专用防挤压伤模式,具体打包参数设置如表1,打包后包长控制在150~160cm。
15.进一步的,步骤(1)160*160*11000mm钢坯在蓄热式加热炉加热一段800~860℃的温度环境中加热30~50min,加热二段920~1100℃的温度环境中加热30~50min,均热段1100~1150℃的温度环境中加热25~40min。
16.进一步的,步骤(4)吐丝机开启振摆“322”模式,即摆动周期3秒/次、左右摆动幅度
±
2.0%。
17.进一步的,步骤(5)吐丝机控制吐丝超前量在-3.0%~-4.5%,即吐丝速度要慢于轧件出mini轧机的速度3.0%~4.5%,吐丝速度控制在23.875m/s~27.16m/s,通过控制终轧速度与吐丝速度差量,实现控制盘条内圈径在92~105mm、包长稳定在180~210cm、整体包形完好,以匹配步骤(7)特定打包模式。
18.进一步的,步骤(7)采用西门子打包机进行打包,打包丝采用φ8mmdbs-2打8道,打捆压力设定12吨,打包模式弹簧钢专用防挤压伤模式,固化打包参数,实现一次压下高速段保证打包后的包长,压盘位移距离与包长匹配,一次压下慢速段和二次压下段的缓慢挤压,从而减少打包挤压伤,具体打包参数设置如表1。
19.表1 12吨弹簧钢防挤伤模式参数
[0020][0021]
1#压盘(右侧压盘)、2#压盘(左侧压盘)液压比例阀开启48.5%~51.5%,压盘快速前期位移(实测0.50~0.60m/s),接触到盘条端部后受到反作用阻力,仪表显示压力12吨,切换到慢速段,快慢切换时机可以通过压盘快慢速切换流量来调节,即12吨*(1-20%)~12吨*(1-16%)=9.6~10.08吨适用于弹簧钢防挤伤模式;
[0022]
1#压盘(右侧压盘)、2#压盘(左侧压盘)液压比例阀开启22.5%~27.5%,压盘慢速前期位移(实测0.05~0.06m/s),同时打包丝1#~4#线道首先分别以90cm/s、90cm/s、80cm/s、90cm/s速度从打包丝线筒内抽丝送线,压盘保持慢速度段压力9.6~10.08吨,1#~4#线道打包丝分别以75cm/s、75cm/s、70cm/s、75cm/s收紧并打结,压盘反向移动,打包完成。
[0023]
负值是操作界面上一种特定标识方法。
[0024]
所述55sicr热轧盘条化学成分按照质量百分数计,配比为c:0.51~0.59%,si:1.20~1.60%,mn:0.50~0.80%,cr:0.50~0.80%,p≤0.025%,s≤0.020%,ni≤0.35%,cu≤0.25%,其余为铁和不可避免的杂质。
[0025]
本发明得到的55sicr热轧盘条内圈径92~105mm,打包前盘条包长稳定在180~210cm,包形紧凑,错圈均匀,打包过程无盘条挤压声,打包后包形完好,不易塌包、斜包,可多层堆放、运输,包长控制在150~160cm,拆包检查目视可见打包挤压伤在45~60点/包,下游客户下料涡流探伤按照0.05mm(高标准探伤精度)缺陷点数稳定控制在≤60点/包。若下游客户下料涡流探伤按照0.10mm(目前国内的常用标准),批量验证缺陷点数稳定控制在≤8点/包,
[0026]
本发明通过吐丝机开启振摆“322”模式,即摆动周期3秒/次、左右摆动幅度
±
2.0%,可实现盘条与盘条之间的提前错圈到位,包形紧凑,可有效避免打包过程中的强制位移错圈,从而造成盘条之间的挤压伤。
[0027]
本发明首次提出将吐丝机控制吐丝超前量在特定的范围,即吐丝速度要慢于轧件出mini轧机的速度在特定范围,以获得特定的盘条内圈径和打包前的包长,来匹配现有的弹簧钢专用防挤压伤模式,吐丝机开启振摆“322”模式,即摆动周期3秒/次、左右摆动幅度
±
2.0%。
[0028]
本发明核心控制吐丝机吐丝超前量在-3.0%~-4.5%,即吐丝速度要慢于轧件出mini轧机的速度3.0%~4.5%,保证盘条内圈径92~105mm,有效缩短打包前包长,包长稳
定在180~210cm,以匹配现有弹簧钢打包模式,减少了位移挤压,从而减少打包挤压伤。
具体实施方式
[0029]
本发明下面结合高速线材控轧控冷技术,以160*160*11000mm断面的钢坯,轧制为φ13.0mm、φ16.0mm成品规格55sicr热轧盘条的生产实施进行说明。
[0030]
实施例1(φ13.0mm 55sicr热轧盘条)
[0031]
1、钢坯加热
[0032]
轧坯成分c:0.53%,si:1.42%,mn:0.66%,cr:0.67%,p:0.013%,s:0.008%,ni:0.014%,cu:0.012%,其余为铁和不可避免的杂质。
[0033]
将160*160*11000mm断面的钢坯在蓄热式加热炉加热一段850~860℃的温度环境中加热45min,加热二段930~1090℃的温度环境中加热40min,均热段1100~1130℃的温度环境中加热30min。
[0034]
2、控制轧制
[0035]
钢坯出加热炉后,通过开启18mpa的高压水除去钢坯表面氧化铁皮,钢坯的开轧温度为900~1020℃;钢坯通过开启机架间冷却水,使精轧机的轧制温度在880~920℃、控制到达mini轧机的温度控制在820~860℃,mini轧机轧速28.0m/s。
[0036]
3、吐丝成圈
[0037]
终轧后通过调节水箱流量,使盘条的吐丝温度控制在860~900℃,吐丝速度控制在26.75m/s,吐丝超前量实际-4.46%,开启吐丝振摆“322”模式,摆动周期3秒/次、左右摆动幅度
±
2.0%。
[0038]
4、轧后控冷
[0039]
吐丝成圈后,盘条在斯太尔摩辊道上开启风机保温冷却,采用鼻锥芯棒集卷成包,下线打包前包长在197~205cm,盘条内圈径在94~98cm。
[0040]
5、打包入库
[0041]
西门子打包机进行打包(型号为1ndbs020023自动捆扎机、打捆机),打包丝采用φ8mmdbs-2打8道,打捆压力设定12吨,打包模式弹簧钢专用防挤压伤模式,实际打包参数如下表2。
[0042]
表2φ13.0mm 55sicr热轧盘条打包参数
[0043]
[0044]
按照实施例1生产的得到55sicr热轧盘条内圈径94~98mm,打包前盘条包长稳定在197~205cm,包形紧凑,错圈均匀,打包过程无盘条挤压声,打包后包形完好,不易塌包、斜包,可多层堆放、运输,打包后包长控制在155~160cm,表面实物质量参见下表3。
[0045]
表3φ13.0mm 55sicr热轧盘条表面质量
[0046][0047]
拆包检查目视可见打包挤压伤在45~60点/包,下游客户下料涡流探伤按照0.05mm缺陷点数稳定控制在32~60点/包。
[0048]
实施例2(φ16.0mm 55sicr热轧盘条)
[0049]
1、钢坯加热
[0050]
轧坯成分c:0.55%,si:1.41%,mn:0.67%,cr:0.65%,p:0.010%,s:0.008%,ni:0.010%,cu:0.015%,其余为铁和不可避免的杂质。
[0051]
将160*160*11000mm断面的钢坯在蓄热式加热炉加热一段850~860℃的温度环境中加热35min,加热二段930~1060℃的温度环境中加热38min,均热段1100~1145℃的温度环境中加热32min。
[0052]
2、控制轧制
[0053]
钢坯出加热炉后,通过开启18mpa的高压水除去钢坯表面氧化铁皮,钢坯的开轧温度为900~1020℃;钢坯通过开启机架间冷却水,使精轧机的轧制温度在880~920℃、控制到达mini轧机的温度控制在820~860℃,mini轧机轧速25.0m/s。
[0054]
3、吐丝成圈
[0055]
终轧后通过调节水箱流量,使盘条的吐丝温度控制在860~900℃,吐丝速度控制在24.23m/s,吐丝超前量实际-3.08%,开启吐丝振摆“322”模式,摆动周期3秒/次、左右摆动幅度
±
2.0%。
[0056]
4、轧后控冷
[0057]
吐丝成圈后,盘条在斯太尔摩辊道上开启风机保温冷却,采用鼻锥芯棒集卷成包,下线打包前包长在180~196cm,盘条内圈径在92~96cm。
[0058]
5、打包入库
[0059]
西门子打包机进行打包,打包丝采用φ8mmdbs-2打8道,打捆压力设定12吨,打包模式弹簧钢专用防挤压伤模式,实际打包参数如下表4。
[0060]
表4φ16.0mm 55sicr热轧盘条打包参数
[0061][0062]
按照实施例2生产的得到55sicr热轧盘条内圈径92~96mm,打包前盘条包长稳定在180~196cm,包形紧凑,错圈均匀,打包过程无盘条挤压声,打包后包形完好,不易塌包、斜包,可多层堆放、运输,打包后包长控制在155~160cm,表面实物质量参见下表5。
[0063]
表5φ16.0mm 55sicr热轧盘条表面质量
[0064][0065]
拆包检查目视可见打包挤压伤在46~56点/包,下游客户下料涡流探伤按照0.05mm缺陷点数稳定控制在32~58点/包。
[0066]
对比例1(φ13.0mm 55sicr热轧盘条)
[0067]
对比例1与实施例1相比,主要区别在于:步骤5打包参数中将打包压力加大至18吨,1#、2#压盘自动向前快速段速度的流量加大为550
‰
,其他条件均同实施例1。
[0068]
按照对比例1生产的得到55sicr热轧盘条内圈径94~98mm,打包前盘条包长稳定在197~205cm,包形完好,但打包过程盘条挤压声明显,打包后包偏短,易从c型钩滑落,打包后包长仅有130~145cm,表面实物质量参见下表6。
[0069]
表6φ13.0mm 55sicr热轧盘条表面质量
[0070]
[0071]
拆包检查目视可见打包挤压伤在217~303点/包,下游客户下料涡流探伤按照0.05mm缺陷点数稳定控制在354~456点/包。
[0072]
对比例2(φ16.0mm 55sicr热轧盘条)
[0073]
对比例2与实施例2相比,主要区别在于:步骤5打包参数中1#压盘自动向前快速段速度流量调整为400
‰
、1#压盘自动向前慢速段速度流量调整为365
‰
、2#压盘自动向前快速段速度流量调整为410
‰
、2#压盘自动向前慢速段速度流量调整为360
‰
,其他条件同实施例2。
[0074]
按照对比例2生产的得到55sicr热轧盘条内圈径92~96mm,打包前盘条包长稳定在183~196cm,包形完好,但打包过程盘条慢速段挤压声明显,打包后包形偏长,易塌包、斜包,不可多层堆放、运输,打包后包长控制在172~180cm,表面实物质量参见下表7。
[0075]
表7φ16.0mm 55sicr热轧盘条表面质量
[0076][0077]
拆包检查目视可见打包挤压伤在136~236点/包,下游客户下料涡流探伤按照0.05mm缺陷点数稳定控制在156~257点/包。
[0078]
对比例3(φ13.0mm 55sicr热轧盘条)
[0079]
对比例3与实施例1相比,主要区别在于:将实施例1步骤3吐丝速度调整为27.65m/s,吐丝超前量实际-1.25%;步骤5打包参数中1#压盘自动向前快速段速度流量调整为510
‰
、1#压盘自动向前慢速段速度流量调整为260
‰
、2#压盘自动向前快速段速度流量调整为510
‰
、2#压盘自动向前慢速段速度流量调整为260
‰
、压盘快慢速切换流量调整为-145
‰
,其他条件同实施例1。
[0080]
按照对比例3生产的得到55sicr热轧盘条内圈径85~87mm,打包前盘条包长稳定在230~260cm,包形松散,打包过程盘条挤压声明显,打包后包形偏长,易塌包、斜包,不可多层堆放、运输,打包后包长控制在175~180cm,表面实物质量参见下表8。
[0081]
表8φ13.0mm 55sicr热轧盘条表面质量
[0082][0083]
[0084]
拆包检查目视可见打包挤压伤在132~226点/包,下游客户下料涡流探伤按照0.05mm缺陷点数稳定控制在112~268点/包。
[0085]
对比例4(φ13.0mm 55sicr热轧盘条)
[0086]
对比例4与实施例1相比,主要区别在于:将实施例1步骤3吐丝速度调整为27.17m/s,吐丝超前量实际-2.96%;步骤5打包参数中1#压盘自动向前快速段速度流量调整为480
‰
、1#压盘自动向前慢速段速度流量调整为220
‰
、2#压盘自动向前快速段速度流量调整为480
‰
、2#压盘自动向前慢速段速度流量调整为220
‰
、压盘快慢速切换流量调整为-205
‰
,其他条件同实施例1。
[0087]
按照对比例4生产的得到55sicr热轧盘条内圈径83~86mm,打包前盘条包长稳定在240~260cm,包形松散,打包过程盘条挤压声明显,打包后包形偏长,易塌包、斜包,不可多层堆放、运输,打包后包长控制在180~190cm,表面实物质量参见下表9。
[0088]
表9φ13.0mm 55sicr热轧盘条表面质量
[0089][0090]
拆包检查目视可见打包挤压伤在107~233点/包,下游客户下料涡流探伤按照0.05mm缺陷点数稳定控制在117~245点/包。
[0091]
对比例5(φ13.0mm 55sicr热轧盘条)
[0092]
对比例5与实施例1相比,主要区别在于:将实施例1步骤3吐丝速度调整为26.71m/s,吐丝超前量实际-4.61%;其他条件同实施例1。
[0093]
按照对比例5生产的得到55sicr热轧盘条内圈径83~88mm,打包前盘条包长稳定在220~240cm,包形松散,打包过程盘条挤压声明显,打包后包形偏长,易塌包、斜包,不可多层堆放、运输,打包后包长控制在175~190cm,表面实物质量参见下表10。
[0094]
表10φ13.0mm 55sicr热轧盘条表面质量
[0095][0096]
拆包检查目视可见打包挤压伤在109~189点/包,下游客户下料涡流探伤按照0.05mm缺陷点数稳定控制在121~202点/包。
[0097]
对比例6(φ16.0mm 55sicr热轧盘条)
[0098]
对比例6与实施例2相比,主要区别在于:将实施例1步骤3吐丝速度调整为24.75m/s,吐丝超前量实际-1.00%;步骤5打包参数中1#压盘自动向前快速段速度流量调整为520
‰
、1#压盘自动向前慢速段速度流量调整为210
‰
、2#压盘自动向前快速段速度流量调整为520
‰
、2#压盘自动向前慢速段速度流量调整为210
‰
、压盘快慢速切换流量调整为-205
‰
,其他条件同实施例2。
[0099]
按照对比例6生产的得到55sicr热轧盘条内圈径83~87mm,打包前盘条包长稳定在230~260cm,包形松散,打包过程盘条挤压声明显,打包后包形偏长,易塌包、斜包,不可多层堆放、运输,打包后包长控制在178~183cm,表面实物质量参见下表11。
[0100]
表11φ16.0mm 55sicr热轧盘条表面质量
[0101][0102]
拆包检查目视可见打包挤压伤在114~222点/包,下游客户下料涡流探伤按照0.05mm缺陷点数稳定控制在128~213点/包。
[0103]
对比例7(φ16.0mm 55sicr热轧盘条)
[0104]
对比例7与实施例2相比,主要区别在于:将实施例1步骤3吐丝速度调整为24.26m/s,吐丝超前量实际-2.96%;步骤5打包参数中1#压盘自动向前快速段速度流量调整为460
‰
、1#压盘自动向前慢速段速度流量调整为210
‰
、2#压盘自动向前快速段速度流量调整为460
‰
、2#压盘自动向前慢速段速度流量调整为210
‰
、压盘快慢速切换流量调整为-145
‰
,其他条件同实施例1。
[0105]
按照对比例7生产的得到55sicr热轧盘条内圈径83~89mm,打包前盘条包长稳定在235~260cm,包形松散,打包过程盘条挤压声明显,打包后包形偏长,易塌包、斜包,不可多层堆放、运输,打包后包长控制在180~195cm,表面实物质量参见下表12。
[0106]
表12φ16.0mm 55sicr热轧盘条表面质量
[0107][0108][0109]
拆包检查目视可见打包挤压伤在107~233点/包,下游客户下料涡流探伤按照0.05mm缺陷点数稳定控制在117~245点/包。
[0110]
对比例8(φ16.0mm 55sicr热轧盘条)
[0111]
对比例8与实施例2相比,主要区别在于:将实施例1步骤3吐丝速度调整为23.87m/s,吐丝超前量实际-4.52%,其他条件同实施例2。
[0112]
按照对比例8生产的得到55sicr热轧盘条内圈径80~86mm,打包前盘条包长稳定在240~260cm,包形松散,打包过程盘条挤压声明显,打包后包形偏长,易塌包、斜包,不可多层堆放、运输,打包后包长控制在180~185cm,表面实物质量参见下表13。
[0113]
表13φ16.0mm 55sicr热轧盘条表面质量
[0114][0115]
拆包检查目视可见打包挤压伤在113~213点/包,下游客户下料涡流探伤按照0.05mm缺陷点数稳定控制在121~220点/包。
[0116]
本发明得到的55sicr热轧盘条内圈径92~105mm,打包前盘条包长稳定在180~210cm,包形紧凑,错圈均匀,打包过程无盘条挤压声,打包后包形完好,不易塌包、斜包,可多层堆放、运输,包长控制在150~160cm,拆包检查目视可见打包挤压伤在45~60点/包,下游客户下料涡流探伤按照0.05mm缺陷点数稳定控制在≤60点/包。本发明核心是基于高速热轧盘条生产线、通过控制终轧速度与吐丝速度差量,实现控制盘条内圈径、整体包形和包长,以匹配特定打包模式,来减少55sicr热轧盘条打包挤压伤的方法。
[0117]
本发明中所用原料、设备,若无特别说明,均为本领域的常用原料、设备;本发明中所用方法,若无特别说明,均为本领域的常规方法。以上所述仅为本发明的较好实施方式,并不用以限制本发明,凡是依据本发明的技术实质对以上实施例作的修改,均包含在本发明的保护范围之内。
再多了解一些
本文用于创业者技术爱好者查询,仅供学习研究,如用于商业用途,请联系技术所有人。