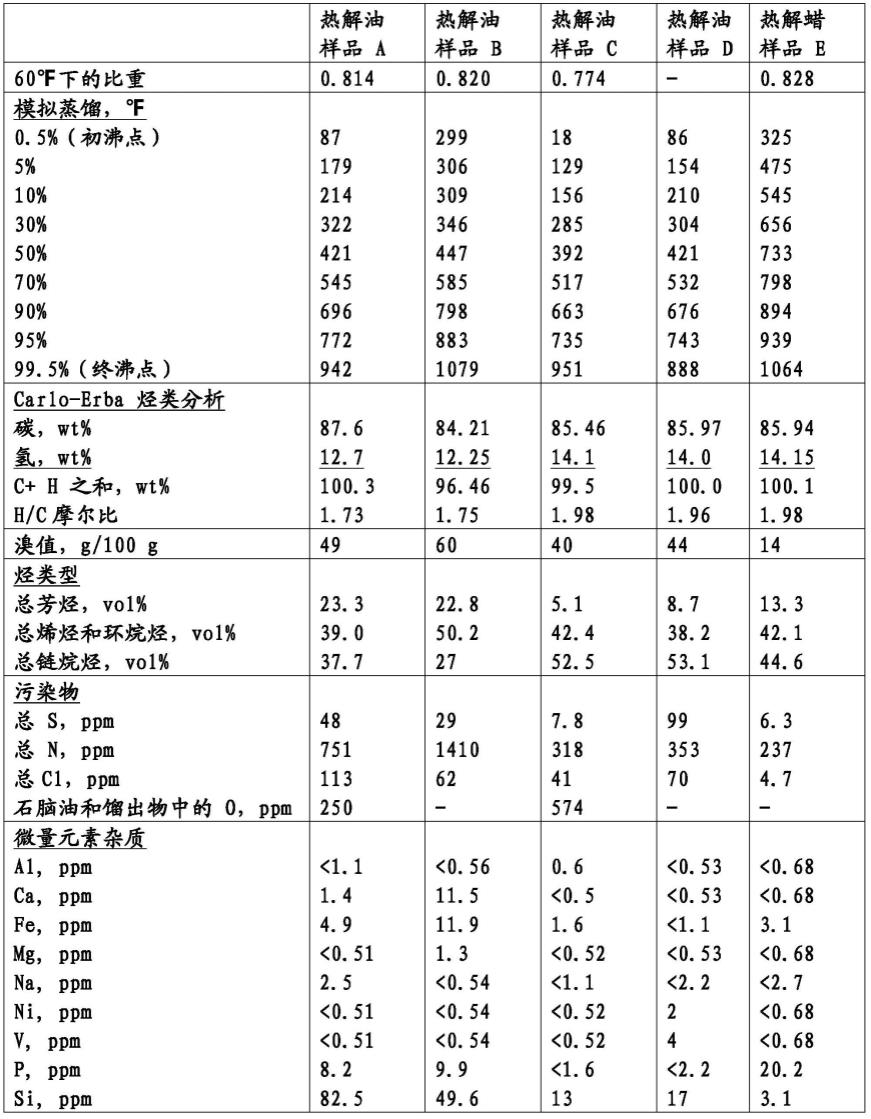
通过原油单元和异构化脱蜡单元将塑料废物转化为聚乙烯和润滑油的循环经济
背景技术:
1.世界塑料生产的增长极为迅速。根据plasticseurope market research group的数据,2016年世界塑料产量为3.35亿吨,2017年为3.48亿吨,2018年为3.59亿吨。根据麦肯锡公司的数据,2016年全球塑料废物量估计约为每年2.6亿吨,如按目前的轨迹继续下去,预计到2030年将达到每年4.6亿吨。
2.一次性塑料垃圾已成为一个日益重要的环境问题。目前,选择将聚乙烯和聚丙烯废塑料回收为增值化学品和燃料产品的似乎很少。目前,只有少量聚乙烯和聚丙烯通过化学回收法进行回收,其中回收和清洁的聚合物颗粒在热解单元中热解以制造燃料(石脑油、柴油)、料流裂化装置进料或软蜡。
3.将废塑料转化为烃类润滑剂的方法是已知的。例如,美国专利no.3845157公开了废的或原始聚烯烃如乙烯/烯烃共聚物裂解形成气态产物,再将其进一步加工生产合成烃润滑剂。美国专利no.4642401公开了通过在150-500℃的温度和20-300巴的压力下加热粉碎的聚烯烃废物来生产液态烃。美国专利no.5849964公开了一种将废塑料材料解聚成挥发相和液相的方法。挥发相被分离成气相和冷凝物。使用标准精炼技术将液相、冷凝物和气相精炼成液体燃料组分。美国专利no.6143940公开了一种将废塑料转化为重质蜡组合物的工序。美国专利no.6150577公开了一种将废塑料转化为润滑油的方法。ep0620264公开了一种从废的或原始聚烯烃生产润滑油的方法,是在流化床中将废料热裂化以形成蜡状产物,任选地使用加氢处理,然后催化异构化和分馏以回收润滑油。
4.涉及将废塑料转化为润滑油方法的其它文件包括美国专利no.6288296、6774272、6822126、7834226、8088961、8404912和8696994,和美国专利公开号no.2019/0161683、2016/0362609和2016/0264885。前述专利文件通过引用整体并入本文。
5.目前通过热解进行化学回收的方法无法对塑料行业产生重大影响。目前的热解操作生产的是劣质燃料成分(石脑油和柴油系列产品),但这些产品可以足够少的量调混到燃料供应中。然而,如果要回收大量废旧聚乙烯和聚丙烯以解决环境问题,这种简单的调混就无法持续。从热解单元生产的产品质量太差,无法以大量(例如5-20vol.%调混)调混入运输燃料中。
6.为了使一次性塑料实现工业上大量回收以减少其对环境的影响,需要更强大的方法。改进后的方法应该为废旧聚乙烯和聚丙烯塑料建立“循环经济”,其中废塑料被有效回收利用,作为聚合物和高价值副产品的起始材料。
技术实现要素:
7.提供一种将废塑料转化为回收料用于聚乙烯聚合的连续方法。所述方法包括选择含有聚乙烯和/或聚丙烯的废塑料,并将废塑料通过热解反应器以将至少一部分聚烯烃废物热裂化并产生热解流出物。热解流出物被分离成尾气、石脑油/柴油馏分、重质馏分和烧焦物。
8.此方法与炼油厂结合是本方法的一个重要方面,并允许用诸如聚乙烯的一次性使用废塑料来创立循环经济。因此,将石脑油/柴油馏分送至炼油厂原油单元,从原油单元蒸馏塔回收直馏石脑油馏分(c
5-c8)并将其送至蒸汽裂解装置以生产乙烯。将来自热解单元的重质馏分送至异构化脱蜡装置以生产基础油。
9.在另一个实施方案中,提供一种将包括聚乙烯的废塑料转化为回收料用于聚乙烯聚合的连续方法。所述方法包括选择含有聚乙烯和聚丙烯的废塑料,并通过热解反应器使废塑料热裂解至少一部分聚烯烃废物并产生热解流出物。热解流出物被分离成废气,石脑油/柴油馏分,重馏分和烧焦物。石脑油/柴油馏分被送至炼油厂的原油单元,从中回收丙烷和丁烷(c
3-c4)馏分。将(c
3-c4)馏分送至蒸汽裂解装置中用于生产乙烯。来自热解单元的重质馏分可送至异构化脱蜡装置以生产润滑基础油。
10.炼油厂通常有其自己的流入炼油厂单元的烃进料。送入炼油厂单元的由废塑料热解产生的石脑油/柴油或蜡状重质馏分的流量可以占流入炼油厂单元总流量的任何实际的或可调节的体积%。一般来说,废塑料热解产生的馏分的流量,出于实际原因,可最高至总流量即炼油厂流量和馏分流量总和的约50vol%。在一个实施方案中,石脑油/柴油的流量最高至总流量的约20vol%。
11.除其它因素外,已经发现通过添加炼油厂操作可以将废热解油和蜡升级为更高价值的产品,例如汽油、航空燃料、柴油和润滑油。另外,通过添加炼油厂操作,已经发现可以从废料热解油有效和高效地生产清洁石脑油(c
5-c8)或c
3-c4并用于最终的聚乙烯聚合物生产。从回收的塑料到产品质量等同于原始聚合物的聚乙烯产品的整个过程实现了积极的经济性。
附图说明
12.图1描述了热解废塑料以生产燃料或蜡的目前实践(基础案例)。
13.图2描述了建立废塑料循环经济的本方法。
14.图3描述了废塑料回收的塑料类型分类。
具体实施方式
15.在本方法中,提供一种通过组合不同工业过程将废聚乙烯和/或聚丙烯回收利用再回到原始聚乙烯以建立循环经济的方法。大部分聚乙烯和聚丙烯聚合物用于一次性塑料,并在使用后被丢弃。一次性塑料垃圾已成为日益重要的环境问题。目前,将聚乙烯和聚丙烯废塑料回收为增值化学品和燃料产品的选择似乎很少。当前,只有少量聚乙烯/聚丙烯通过化学回收法进行回收,其中将回收和清洁的聚合物颗粒在热解单元中热解以制造燃料(石脑油、柴油)、蒸汽裂解装置进料或软蜡。
16.乙烯是生产量最大的石化基础原料。通过蒸汽裂解每年生产数亿吨乙烯。蒸汽裂解装置使用气态进料(乙烷、丙烷和/或丁烷)或液体进料(石脑油或瓦斯油)。这是一种非催化裂化工艺,是在非常高的温度下运行,最高可达850℃。
17.聚乙烯广泛用于各种消费品和工业产品。聚乙烯是最常用的塑料,每年生产的聚乙烯树脂超过1亿吨。它的主要用途是包装(塑料袋、塑料薄膜、土工膜、包括瓶子在内的容器等)。聚乙烯以三种主要形式生产:高密度聚乙烯(hdpe,约0.940-0.965g/cm-3
)、线性低密
度聚乙烯(lldpe,约0.915-0.940g/cm-3
)和低密度聚乙烯(ldpe,《0.930g/cm-3
),具有相同的化学式(c2h4)n但分子结构不同。hdpe具有低支化度的短侧链,而ldpe具有非常高支化度的长侧链,lldpe是具有大量短支链的基本线性聚合物,通常由乙烯与短链α-烯烃共聚制成。
18.低密度聚乙烯(ldpe)在150
–
300℃和1000-3000大气压的超高压下通过自由基聚合生产。该方法使用少量氧气和/或有机过氧化物引发剂来生产平均每个聚合物分子含约4000
–
40000个碳原子且具有许多分支的聚合物。高密度聚乙烯(hdpe)在相对低压(10-80大气压)和80-150℃温度下在催化剂存在下制造。一般使用ziegler-natta有机金属催化剂(氯化钛(iii)与烷基铝)和phillips型催化剂(负载于二氧化硅的氧化铬(iv)),并且通过采用环管反应器的淤浆工艺或通过采用流化床反应器的气相工艺进行生产。将氢气与乙烯混合以控制聚合物的链长。线型低密度聚乙烯(lldpe)的制造条件与hdpe相似,不同之处是乙烯与短链α-烯烃(1-丁烯或1-己烯)共聚。
19.现今,由于上述回收工作的低效和无效,只有一小部分废聚乙烯产品被收集起来进行回收。
20.图1示出了当今工业中操作的热解废塑料燃料或蜡的工艺图。如上所述,通常将聚乙烯和聚丙烯废物一起分选为1。清洁的聚乙烯/聚丙烯废物2在热解单元3中转化为废气4和热解油(液体产品)。来自热解单元的废气4用作操作热解单元的燃料,且只有热解单元用于商业目的。现场的蒸馏单元将热解油分离以生产石脑油和柴油5产品,这些产品销往燃料市场。重质热解油馏分6被再循环回热解单元3以使燃料产率最大化。将烧焦物7从热解单元3中移出。重质馏分6富含长链线形烃,并且很蜡质(即,冷却至环境温度时形成石蜡)。可以从重质馏分6中分离出蜡并销往蜡市场。
21.本方法通过将废聚合物热解产物料流集成到炼油厂操作中来大量地转化热解聚乙烯和/或聚丙烯废塑料。得到的工艺过程生产用于聚合物(石脑油或用于乙烯裂解装置的c
3-c4)以及高质量汽油和柴油燃料和/或高质量基础油的原料。
22.一般而言,本方法为聚乙烯工厂提供循环经济。聚乙烯是由纯乙烯聚合而成的。可以使用蒸汽裂解装置制造清洁乙烯。可将石脑油或c
3-c4料流进料至蒸汽裂解装置。然后将乙烯聚合来生成聚乙烯。。
23.通过添加炼油厂的操作,将废热解油和蜡升级为更高价值的产品(汽油和柴油、基础油),和为蒸汽裂解装置生产清洁lpg和石脑油并最终生产聚乙烯聚合物。从回收的塑料到产品质量等同于原始聚合物的聚乙烯产品的整个过程实现了积极经济。
24.热解单元生产的产物质量差,含有钙、镁、氯化物、氮、硫、二烯、重质组分等污染物,这些产物不能大量用于运输燃料的调混。已经发现,通过让这些产品通过炼油厂单元,可以在预处理单元中捕获污染物并减少它们的负面影响。燃料组分可以采用适当的具有化学转化过程的炼油厂单元进行进一步升级,通过集成工艺过程生产的最终运输燃料更高质并满足燃料质量要求。本方法将升级腊成有价值的润滑基础油。本集成工艺方法将生产更清洁的石脑油料流用于蒸汽裂解装置进料,以产生用于生产聚乙烯的乙烯。这些大型合规生产使回收利用塑料的“循环经济”成为可能。
25.进出炼油厂操作的碳是“透明的”,这意味着来自废塑料的所有分子不一定最终都进入循环回聚烯烃工厂的确切烯烃产品中,但仍被认为是“红利”,因为进出炼油厂的净“绿”碳是积极的。采用这些集成工艺,聚乙烯工厂所需的原始原料量将显著减少。
26.图2示出了本发明的集成方法,将炼油厂操作与回收进行集成来有效生产聚乙烯。图2中,混合的废塑料一起归类为21,清洁的废塑料22在热解单元23中转化为废气24和热解油(液体产物)及任选的热解蜡(环境温度下为固体产物)。来自热解单元的废气24可用作燃料以运行热解单元23。热解油通常经场区的蒸馏单元被分离成石脑油/柴油馏分25和重质馏分26。热解步骤完成后,将烧焦物27从热解单元23中移出。
27.热解单元可以位于废塑料收集站点附近,该地点可以远离炼油厂、靠近炼油厂或在炼油厂内。当热解单元远离炼油厂,则热解油(石脑油/柴油和重质油)可以通过卡车、驳船、轨道车或管道输送到炼油厂。然而,优选热解单元位于废塑料收集站点内或炼油厂内。
28.本方法的优选起始材料是主要含有聚乙烯和聚丙烯的分类废塑料(塑料回收分类类型2、4和5)。预分选的废塑料经过清洗、切碎或造粒后送入热解装置进行热裂解。图3描述了废塑料回收的塑料类型分类。分类类型2、4和5分别是高密度聚乙烯、低密度聚乙烯和聚丙烯。可以使用聚乙烯和聚丙烯废塑料的任意组合。对于本方法,优选是至少一些聚乙烯废塑料。
29.废塑料的适当分选对于减少n、cl和s等污染物非常重要。含有聚对苯二甲酸乙二醇酯(塑料回收分类类型1)、聚氯乙烯(塑料回收分类类型3)和其它聚合物(塑料回收分类类型7)需要分选出到小于5%,优选小于1%,最优选小于0.1%。本方法可以容忍适量的聚苯乙烯(塑料回收分类类型6)。需要将废聚苯乙烯分选出至低于30%,优选低于20%,最优选低于5%。
30.废塑料清洗可去除金属污染物,例如钠、钙、镁、铝和来自其它废物来源的非金属污染物。非金属污染物包括来自元素周期表第iv族的污染物,例如二氧化硅,来自第v族的污染物,例如磷和氮化合物,来自第vi族的污染物,例如硫化合物,以及来自第vii族的卤化物污染物,例如氟化物、氯化物和碘化物。残留金属、非金属污染物和卤化物需要去除至低于50ppm,优选低于30ppm,最优选低于5ppm。
31.如果洗涤不能充分去除金属、非金属污染物和卤化物杂质,则可以使用单独的保护床来去除金属和非金属污染物。
32.通过在热解区中于热解条件下接触塑料材料进料来进行热解,将其中至少一部分进料裂解,从而形成包括1-烯烃和n-链烷烃的热解区流出物。热解条件包括约400-700℃,优选约450-650℃的温度。常规热解技术教导了高于大气压的操作条件。参见例如美国专利no.4642401。此外,已经发现通过调节压力往下,可以控制所期望产品的产率。参见例如美国专利no.6150577。因此,在期望有这种控制的一些实施方案中,热解压力是低于大气压的。
33.图2示出了本集成方法,其中仅来自裂解单元23的石脑油/柴油馏分25被送至原油单元脱盐罐28以生产c
5-c8石脑油29,优选c
5-c7石脑油,最优选c
5-c6石脑油,用于蒸汽裂解装置30的进料。蒸汽裂解装置30产生乙烯36。将乙烯送至聚合单元40以生产聚乙烯。聚乙烯用于聚乙烯消费品41。
34.炼油厂通常有其自己的流入炼油厂单元的烃进料。送入炼油厂单元即本文的原油单元的由废塑料热解产生的石脑油/柴油的流量可以占流入炼油厂单元总流量的任何实际的或可调节的体积%。一般来说,废塑料热解产生的石脑油/柴油的流量,出于实际原因,可
最高至总流量即炼油厂流量和石脑油/柴油流量总和的约50vol%。在一个实施方案中,石脑油/柴油的流量最高至总流量的约20vol%。在另一个实施方案中,石脑油/柴油的流量最高至总流量的10vol%。已发现约20vol%的量对炼油厂的影响相当实用,同时还提供了极好的结果且是一个可以适应的量。由热解产生的石脑油/柴油量当然可以控制,以便送入炼油厂单元的馏分提供所期望的体积%流量。进入脱蜡单元的重质腊馏分流量同样可以控制和/或调整。
35.炼油厂原油单元将原油分离成多个馏分,例如液化石油气(lpg)、石脑油、煤油、柴油和瓦斯油,这些馏分将进一步处理成有用的石油产品。炼油厂原油单元具有原油处理段,通常称为脱盐罐,和原油蒸馏或分馏段。蒸馏段通常包括常压蒸馏单元和真空蒸馏单元。
36.来自热解单元的石脑油/柴油馏分被送至脱盐罐,以去除油中所含的盐和固体,从而保护下游设备免受污染物的有害影响。为了去除盐,将水与油混合,通常加热到约215
°
f-280
°
f的温度,并允许在脱盐单元中分离。
37.将脱盐的油送至蒸馏塔底部加热至约340-372℃(644-700℉)的常压蒸馏单元,并在分馏塔的不同点移出液体以生产各种燃料。来自原油单元的燃料可送至炼油厂的各种升级单元,以去除杂质(氮、硫),并将馏分进行催化转化以改善产品性能如辛烷值和十六烷值。常压蒸馏塔的底部渣油也称为常压渣油,一般被送至减压蒸馏塔以生产减压瓦斯油(650-1050℉)和减压渣油。真空瓦斯油可用于生产润滑油或进一步裂解以生产汽油、航空燃料和柴油燃料。
38.蒸汽裂解装置和乙烯聚合单元优选位于炼油厂附近,以便原料(丙烷、丁烷、石脑油)可以通过管道输送。对于位置远离炼油厂的石化厂,原料可以通过卡车、驳船、轨道车或管道输送。
39.来自热解油的重质石脑油/柴油可以与来自原油单元蒸馏的烃合并,并作为重质石脑油、柴油、常压瓦斯油料流31送至适当的炼油厂单元32,用于升级成清洁汽油和柴油33。。
40.来自热解单元的重质蜡状热解油26可以送至基础油脱蜡单元34,用含沸石的贵金属催化剂进行异构化脱蜡或加氢异构化,生产出具有优良粘度指数和倾点的润滑基础油35。重质蜡状馏分的流量可以根据所需的容纳量按需控制和调整。
41.异构化脱蜡单元将链烷烃的蜡状重烃材料(通常约650℉沸点)转化为高粘度指数(vi)润滑油。此单元一般包括进料加氢处理段、异构化脱蜡段和蒸馏段。
42.脱蜡单元的进料优选先在加氢处理步骤中进行加氢。加氢处理作为脱蜡单元的一部分进行。加氢处理步骤的进料去除了大部分任何含氮、含硫和/或含氧的污染物。加氢处理步骤还会使部分烯烃、二烯烃和芳烃饱和,以提高脱蜡单元进料的质量。能去除污染物同时避免裂解所采用的典型加氢处理条件包括温度范围约为190℃(374℉)-340℃(644℉),压力范围约为400-3000psig,空速(lhsv)范围约为0.1hr-1-20hr-1
,氢循环率范围约为400-15000scf/b。加氢处理催化剂包括加氢处理单元中常规使用的含ni、mo、co、w等金属和氧化铝、二氧化硅、硅铝氧化物等多孔载体的催化剂。
43.将经过加氢处理的重质烃与含有贵金属、中孔分子筛和粘结剂的异构化脱蜡催化剂一起送至脱蜡反应器。催化剂优选包含中孔(10元环)分子筛,如zsm-23、zsm-35、zsm-48、zsm-5、ssz-32、ssz-91、sapo-11、sapo-31和sapo-41。贵金属包括viii族金属如pt、pd或pt
和pd的混合物。一般来说,多孔氧化铝或二氧化硅用于粘结材料以生成用于固定床反应器的催化剂颗粒。脱蜡反应器的典型反应条件包括温度范围为200℃(392℉)至约475℃(887℉),压力范围为约200-3000psig,空速(lhsv)范围为约0.2hr-1-10hr-1
,氢气循环率约400-15000scf/b不等。异构化脱蜡催化剂将正构链烷烃转化为异构链烷烃,从而降低所得油的倾点并形成高vi值润滑油。
44.将来自异构化脱蜡段的流出物烃送至蒸馏单元,以将流出物分离成各种油馏分,例如,沸点高于约650℉的基础油馏分,沸点约300-700℉的柴油馏分,以及沸点约80-400℉的汽油馏分。汽油、航空燃料和柴油馏分的沸点将根据季节和当地规格进行调整。
45.在另一个实施方案中,从炼油厂原油单元28中回收c
3-c4馏分37。该料流也可以进入蒸汽裂解装置30以生产乙烯36。然后可以将乙烯聚合40并制成消费品产品41。
46.通过本发明的集成方法实现了循环经济和有效及高效回收活动的益处。
47.提供以下实施例以进一步说明本方法及其益处。这些实施例是例示说明性的而不是限制性的。
48.实施例1:商业来源热解油和蜡的性质
49.热解油和蜡样品从商业来源获得,它们的性质总结在表1中。这些热解样品是由主要含有聚乙烯和聚丙烯的废塑料通过在大约400-600℃、接近大气压的热解反应器中无需添加任何气体或催化剂条件下热分解制备的。热解单元一般生成气体、液体油产物、任选的蜡产物和烧焦物。将含热裂解烃的热解单元塔顶气流冷却来收集冷凝物,作为热解油(环境温度下为液体)和/或热解蜡(环境温度下为固体)。热解油是热解单元的主要产品。一些单元除热解油外还生产热解蜡作为单独的产品。
50.表1
51.由废塑料热解获得的油和蜡的性质
0.9、沸程为18至1100℉的优质烃料流,如同热解油或热解蜡中的情况。
55.热解产物是相当纯的主要由碳和氢组成的烃。氢碳摩尔比从1.7变动到接近2.0。溴值在14-60的范围内,表明来自烯烃和芳烃的不饱和度不等。芳烃含量在5-23vol.%范围,严苛程度越高的单元会产生更多的芳烃。根据热解单元的工艺条件,热解产物的石蜡含量在20vol.%中值到50vol.%中值。热解产物含有大量烯烃。样品a和b是在较严苛条件如较高热解温度和/或较长停留时间下生产的热解油,含有更高的芳烃和更低的链烷烃成分,因此h/c摩尔比约为1.7和溴值为50-60。样品c和d是在不太严苛的条件下生产的,热解油的链烷烃含量较高,因此h/c摩尔比接近2.0和溴值约为40。样品e即热解蜡主要是链烷烃即饱和烃,含有大量的正构烃(相对于支化烃),具有仅为14的低溴值。
56.以下实施例2-5示出了用于运输燃料的废塑料热解油的评估。
57.实施例2:作为运输燃料评估的热解油的分馏
58.将样品d蒸馏以生成代表汽油(350℉-)、航空燃料(350
–
572℉)、柴油(572
–
700℉)和重质(700℉
)馏分的烃馏分。表2总结了蒸馏产物馏分中的沸点分布和杂质分布。
59.表2
60.热解油蒸馏成燃料馏分
[0061][0062]
实施例3:热解油馏分用于汽油燃料的评估
[0063]
样品f是汽油燃料沸程的热解油,对其进行评估以评定用作汽油燃料的潜力。样品f的碳数范围为c5
–
c12,是典型的汽油燃料。
[0064]
由于热解油的烯烃性质,氧化稳定性(astm d525)和生胶倾向(astm d381)被认定为最关键的要检查的性质。研究辛烷值(ron)和马达法辛烷值(mon)也是发动机性能的关键性质。ron和mon值是由详细的烃gc分析估算的。
[0065]
表3
[0066]
热解油石脑油馏分用于汽油燃料的评估
[0067][0068]
样品f是汽油燃料沸程的热解油馏分,由于其质量差,本身不能用作汽车汽油燃料。此来自热解油的汽油馏分显示出非常差的氧化稳定性,与目标稳定性超过1440分钟相比,样品f仅90分钟后就失败。热解汽油的洗胶质目标超过4mg/100ml,表明有严重生胶倾向。与参比汽油相比,热解汽油的辛烷值较差。使用优质无铅汽油作为参比汽油。
[0069]
我们还考察了将有限量的热解汽油馏分与参比汽油调混的可能性。我们的研究显示,样品f能以可最高至15vol.%的量调混到炼油厂汽油中,同时仍能满足燃料性能目标。通过将热解汽油产物与炼油厂燃料整合,可以保持整体产品质量。
[0070]
这些结果表明,热解油生产的汽油馏分作为汽油燃料的效用有限。优选在炼油厂单元中进行升级以将此热解油的汽油馏分转化为满足汽油燃料性能目标的烃。
[0071]
实施例4:热解油馏分用于航空燃料的评估
[0072]
样品g是航空燃料沸程的热解油馏分,对其进行评估以评定用作航空燃料的潜力。样品g的碳数范围为c9
–
c18,是典型的航空燃料。
[0073]
由于热解油的烯烃性质,航空燃料热氧化试验(d3241)被认为是最关键的试验。热解油航空燃料馏分自身即样品g仅具有36分钟的氧化稳定性,表明纯热解航空燃料馏分不适合用作航空燃料。
[0074]
我们制备了5vol.%热解航空燃料馏分(样品g)与炼油厂生产的航空燃料的调混物。如表4所示,该调混物在航空燃料氧化试验中仍然失败。
[0075]
表4
[0076]
热解油航空燃料馏分用于航空燃料的评估
[0077] 航空燃料热氧化试验参比航空燃料通过样品g与参比航空燃料的5/95vol.%调混物失败
[0078]
这些结果表明,热解油所生产的航空燃料馏分完全不适合航空燃料,需要在炼油厂单元中进行升级以将此热解油的航空燃料馏分转化为满足航空燃料性能目标的烃。
[0079]
实施例5:热解油馏分用于柴油燃料的评估
[0080]
样品h是柴油燃料沸程的热解油,对其进行评估以评定用作柴油燃料的潜力。样品h的碳数范围为c14
–
c24,是柴油的典型范围。
[0081]
样品h含有大量的正构烃。由于正构烃倾向于表现出蜡状特性,因此倾点(astm d5950-14)和浊点(astm d5773)等冷流特性被认为是最关键的测试。
[0082]
我们用10vol.%和20vol.%样品h与炼油厂生产的柴油制备了两种调混物。然而,
对于倾点要低于-17.8℃(0℉)的目标倾点,两个调混物仍是失败。
[0083]
表5
[0084]
热解油柴油馏分用于柴油的评估
[0085][0086]
这些结果表明,此热解油自身完全不适合用于柴油燃料,需要在炼油厂单元中进行升级以将此热解油的柴油馏分转化为符合柴油燃料性能目标的烃。
[0087]
实施例6:热解油送至原油单元或脱盐单元进行共处理
[0088]
表1的结果显示,主要源自聚乙烯和聚丙烯废料的分选塑料的工业热解过程产生了主要由碳和氢构成的优质热解油。采用良好的分选和高效的热解单元操作,氮和硫杂质水平低至足以使现代炼油厂可以将热解原料共同进料到其加工单元进行处理,而不会产生有害影响。
[0089]
然而,一些热解油可能仍含有大量金属(ca、fe、mg)和其它非金属(n、p、si、cl、o),它们可能会对炼油厂转化单元的运行产生负面影响。对于具有高杂质含量的热解油产物,优选地在送入原油单元之前将其进料到脱盐单元,以便将大部分杂质用预处理器有效去除。
[0090]
通过将热解原料送入原油单元或送入原油单元前的脱盐单元,热解油被分馏成多个组分,并在后续转化单元中进行转化,包括链烷烃异构化单元、航空燃料加氢处理单元、柴油加氢处理单元、流化催化裂化装置(fcc)、烷基化单元、加氢裂化单元和/或焦化单元,以制备具有满意产品性能的汽油、航空燃料和柴油燃料。转化单元(fcc或加氢裂化单元)还将重质馏分(对应于样品i)转化为优质运输燃料。
[0091]
在原油单元后,热解油将在后续的转化单元中进一步转化。以下实施例7以fcc单元为例,说明在炼油厂转化单元中将废塑料热解油转化为优质运输燃料。
[0092]
实施例7:热解油在fcc中的转化
[0093]
为研究废塑料热解油共处理对fcc的影响,用样品a和c进行了一系列实验室试验。真空瓦斯油(vgo)是fcc的典型进料。将20%热解油与vgo的调混物和纯热解油的fcc运行与纯vgo进料的fcc运行进行了比较。
[0094]
fcc实验是在kayser technology inc.制造的model c ace(先进裂化评价)装置上使用来自炼油厂的再生平衡催化剂(ecat)进行的。该反应器是使用n2作为流化气体的固定流化床反应器。催化裂化实验在大气压和900℉反应器温度下进行。通过改变催化剂的量,使催化剂/油比在5-8之间变动。使用配备有gc和fid检测器的炼油厂气体分析仪(rga)收集和分析气体产品。在1300℉的空气存在下进行废催化剂的原位再生,再生烟气通过leco单元以确定焦炭产率。将液体产物称重并在gc中进行分析,以进行模拟蒸馏(d2887)和c
5-组成分析。在物料平衡的情况下,确定焦炭、干气组分、lpg组分、汽油(c5-430℉)、轻循环油(lco,430-650℉)和重循环油(hco,650℉
)的产率。结果总结在下表6中。
[0095]
表6
[0096]
热解油共进料至fcc的评价
[0097][0098]
*:转化率
–
430℉
馏分转化为430℉-的转化率
[0099]
**:燃料沸程范围内整个液体产品中n和o的杂质含量,通过gcx gc测定,ppm
[0100]
***:辛烷值,(r m)/2,由fcc汽油的详细烃gc分析来估算。
[0101]
表6中的结果表明,最高至20vol.%热解油的共进料仅使fcc单元运行发生非常轻微变化,这表明最高至20%热解油的共处理是很容易实现的。调混20vol.%的样品a或样品c导致焦炭和干气产率轻微降低,汽油产率略有增加,lco和hco略有降低,这在大多数情况下都是有利的。由于热解油的链烷烃性质,20%a和c的调混物将辛烷值降低了约3-5个数值。凭借炼油厂操作的灵活性,这些辛烷值的减少可以通过调混或进料位置调整来补偿。
[0102]
fcc单元将热解油裂化成燃料范围的烃,减少了杂质,并将正链烷烃异构化为异链烷烃。所有这些化学过程都将改善热解油和蜡的燃料性质。通过将热解油与沸石催化剂共同进料通过fcc工艺单元,燃料范围内的氧和氮杂质显着减少,从约300-1400ppm n减少到约30ppm n,从约250-540ppm o减少到约60-80ppm o。所有这些共进料产品的烃成分都在典型的fcc汽油范围内。
[0103]
100%热解油的fcc运行显示辛烷值大量减少约13-14个数值。这表明热解油的共
处理优选于纯100%热解油的处理。
[0104]
实施例8:通过将废塑料热解产物共进料至炼油厂原油单元产生c
3-c4和/或石脑油原料
[0105]
通过将全部热解油送入原油单元或原油单元前的脱盐单元,热解油被分馏成多个组分。通过热解油共进料,炼油厂原油单元生成大量可进料至蒸汽裂解装置的含有回收成分的清洁丙烷、丁烷和石脑油料流。如果不是全部,至少一部分料流要进料至蒸汽裂解装置。
[0106]
实施例9:回收的c
3-c4和/或石脑油进料至蒸汽裂解装置用于生产乙烯,然后生产循环利用的聚乙烯树脂和聚乙烯消费品
[0107]
通过根据实施例8将热解产物共进料至原油单元而生成的丙烷、丁烷和石脑油料流是共进料至蒸汽裂解装置用于生产具有回收成分的乙烯的良好原料。然后,将乙烯在聚合单元进行处理以生产含有一些回收聚乙烯/聚丙烯衍生料的聚乙烯树脂,而新生产聚乙烯的质量等同于完全由原始石油资源制成的原始聚乙烯。然后将含有回收材料的聚乙烯树脂进一步加工以生产各种满足消费品需求的聚乙烯产品。这些聚乙烯消费品现在包含化学回收的循环使用聚合物,而聚乙烯消费品的质量等同于完全由原始聚乙烯聚合物制成的产品。这些化学回收聚合物产品与机械回收聚合物产品不同,后者的质量不及由原始聚合物制成的聚合物产品。
[0108]
实施例10:热解蜡送至异构化脱蜡单元进行共处理以生产润滑基础油
[0109]
表1的结果表明,分拣塑料的工业热解过程,主要来自聚乙烯和聚丙烯废料,产生主要由碳和氢制成的热解蜡。研究了通过加氢异构化脱蜡工艺从热解蜡中制造润滑基础油的各种工艺方案。
[0110]
热解蜡中仍含有过高量的氮和硫杂质、金属(ca、fe、mg)和其它非金属(p、si、cl、o),这些杂质对含贵金属(pt、pd或pt和pd的组合)和沸石如zsm-11、zsm-23、zsm-48、ssz-32、ssz-91、sapo-11、sapo-31和sapo-41的加氢异构化脱蜡催化剂的性能产生负面影响。
[0111]
试图通过直接进料纯热解油使用脱蜡催化剂来制备优质润滑基础油的尝试没有成功,如下面实施例11所示。为保持催化剂活性,对于将热解蜡直接进料至加氢异构化脱蜡单元,共进料水平需要限制在低于10vol.%,优选低于5vol.%。体积百分比限制可能来自氮杂质,其对沸石活性有害。合并进料的氮水平需要保持在低于5ppm氮,优选低于1ppm氮。
[0112]
或者,将热解蜡共进料至加氢裂化单元以除去s、n和其它杂质。加氢裂化单元将热解蜡氢化并除去杂质。加氢裂化单元的苛刻程度可以调整,以最大限度地提高合并进料的基础油产率。加氢裂化单元的共进料水平可最高达50vol.%,优选为20vol.%。在此情况下,体积百分比限制可能来自金属杂质或n杂质或p杂质,取决于单元配置和催化剂的选择。然后将含有加氢裂化热解蜡的底部馏分(650℉ )送入加氢异构化脱蜡单元以制备润滑基础油。
[0113]
或者,将热解蜡送入专用的加氢单元以除去s、n和其它杂质,然后送入加氢异构化脱蜡单元以制备基础油。加氢步骤非常容易地除去杂质,如下面的实施例12所示。加氢处理的蜡可以任何体积百分比共进料进行加氢异构化脱蜡。
[0114]
以下实施例11和12展示了用废塑料热解蜡作为原料在炼油厂转换单元中制备优质基础油的不成功路线和成功工艺路线。
[0115]
实施例11:仅通过加氢异构化脱蜡工艺从回收的热解蜡生产基础油
[0116]
为评估从回收的蜡生产基础油的潜力,将样品e(粗热解蜡)真空蒸馏来产生690℉
馏分即样品j。在含pt/ssz-32/氧化铝催化剂的间歇式高压釜单元中,将100%样品j以10:1的油/催化剂重量比,于650℉和800psig h2压力下进行加氢异构化过夜。将氢化产物减压蒸馏,产生690℉
沸点且澄清的油即样品k。样品的性质总结在表中
[0117]
表7
[0118]
用pt/沸石催化剂将热解蜡进行脱蜡
[0119][0120]
[0121]
样品j,从废塑料热解分馏的690℉
软蜡,是100℃为cst的低粘度蜡,具有出色粘度指数为169。然而,软蜡含有大量的n(180ppm)和p(32.5ppm),它们将在加氢异构化脱蜡过程中钝化沸石催化剂活性。脱蜡并蒸馏的油即样品k的粘度指数为162,倾点为12℃。尽管样品e的倾点从42℃大幅降低,但相对于-15℃或更低的行业目标,12℃的倾点仍然非常差。这种油不能用于高性能的现代润滑剂,因为当环境温度降至12℃以下时,这种油会失去流体/油特性,并且油会变成粘稠或固体状的材料。
[0122]
此研究表明,为从废塑料热解蜡中生产出可接受的基础油,热解蜡需要加氢处理或加氢裂化以减少n杂质和其它杂质。
[0123]
实施例12:通过加氢处理后进行加氢异构化脱蜡工艺生产含有回收成分的品质基础油
[0124]
将样品e(粗热解蜡)在含有nimo/氧化铝催化剂的连续固定床单元中于625℉反应器温度和1200psig压力下进行氢化。采用相对于催化剂床体积1.5hr-1
的液体进料流速和2500scf/bbl的h2/烃的流速来生产氢化产品,其主要是蜡。对氢化产物进行真空蒸馏,以产生650
°f
馏分,作为氢化热解石蜡即样品l。
[0125]
样品l即由废塑料热解制成的氢化蜡,在含有pt/zzs-91/氧化铝催化剂的连续固定床单元中于625℉反应器温度和400psig压力下进行加氢异构化脱蜡。采用相对于催化剂床体积1.0hr-1
的液体进料流速和2500scf/bbl的h2/烃的流速来生产脱蜡油。将脱蜡油真空蒸馏以产生690℉
馏分作为最终的脱蜡基础油产品即样品m。结果总结在表8中。
[0126]
表8
[0127]
热解蜡进行加氢处理/脱蜡用于生产基础油
[0128]
热解蜡用pt/沸石催化剂进行加氢和脱蜡用于生产润滑基础油
[0129][0130]
热解蜡即样品e进行加氢能生产高质量的氢化蜡即样品l.加氢后所有微量杂质都被完全去除,因为样品l没有测出可能损害脱蜡催化剂的杂质。本实施例显示,从主要含有聚乙烯、聚丙烯的废塑料中可以有效地生产出高质量的纯链烷烃,并且轻度加氢是净化废塑料衍生蜡的非常有效的方法。
[0131]
将氢化蜡(样品l)进行加氢异构化脱蜡可生产出高质量4cst基础油,其粘度指数为135,倾点为-35℃,浊点为-17℃(样品m)。在质量方面,这种由废塑料热解制成的基础油属于iii类基础油类别。考虑到样本k观察到的不良性质,这些积极的结果非常令人意外。低
粘度4cst基础油是非常期望的,因为它广泛用作汽车润滑油中的组分。
[0132]
实施例11和12清楚地显示,通过仔细选择共进料工艺配置和工艺条件,可以从热解聚乙烯和聚丙烯废料中获得的蜡制成高质量基础油。结果清楚地显示,从废塑料热解蜡制备基础油的优选方式是加氢之后进行加氢异构化脱蜡过程。生产的含有回收成分的最终基础油的质量与传统炼油厂用原始原油加工生产的基础油相当或更优。
[0133]
上述实施例一起清楚地示出了一种新的回收大量聚乙烯和聚丙烯衍生废塑料的有效方法,即通过热解进行化学回收,然后通过高效集成将热解产物共进料至炼油厂。这种集成允许优质燃料、润滑油和循环利用的聚合物的生产。
[0134]
本文中所使用的词语“包括”或“包含”旨在作为开放性连接词,意思是包含命名的元素,但不一定排除其它未命名的元素。词语“基本由
……
组成”或“基本上由
……
组成”旨在表示排除对组成具有任何重要意义的其它元素。词语“是由
……
组成”或“由
……
组成”意在作为一种连接词,意指排除所列举元素之外的所有元素,除了仅有的少量杂质。
[0135]
本文引用的所有专利和出版物均在不与本文不一致的范围内通过引用并入本文。应当理解,上述实施方案的某些上述结构、功能和操作对于实践本发明不是必需的,且仅仅为了例示性实施方案或实施方案的完整性而包括在描述中。此外,应当理解,上述引用的专利和出版物中阐述的具体结构、功能和操作可以结合本发明实施,但它们对于本发明的实施不是必需的。因此,应当理解,本发明可以如具体描述的那样以其它方式实施,只要不实际背离由所附权利要求限定的本发明的精神和范围。
再多了解一些
本文用于企业家、创业者技术爱好者查询,结果仅供参考。