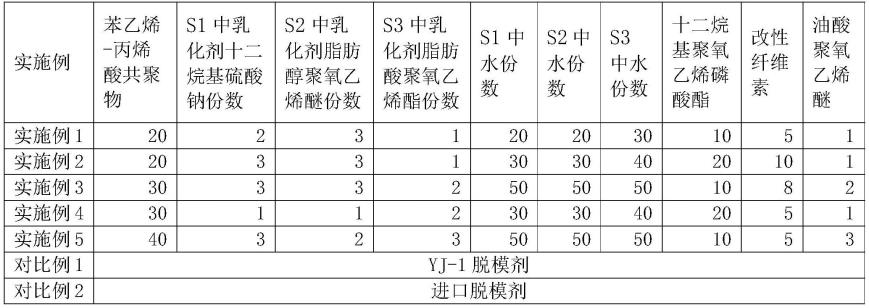
1.本发明涉及无硅脱模剂技术领域,具体涉及一种脱模性能优异的不含硅脱模剂及其制备方法。
背景技术:
2.铝合金压铸成型工艺在汽车配件上广泛使用,铝合金具有重量轻、机械性能好和出色的加工性能,以及可回收利用等一系列优点。铝合金具有良好的压铸成型性能,压铸产品尺寸稳定易于后加工。随着行业下游客户新产品、新技术、新工艺的应用以及环保压力,不断地对铝合金压铸产品提出新的要求。目前在很多行业和产品均限制硅元素的使用,并发布了相关的环保限制指令。在实际生产过程中,特别是一些精密制造工艺,硅油生产的脱模剂往往会导致严重的积碳现象,给脱模以及产品尺寸造成非常大的困扰;且对于一些需要在后续工艺进行氧化着色的产品,硅油生产的脱模剂往往会影响着色。市面上也有一些不含硅油的脱模剂,但是往往因其耐高温性能不好导致模具损坏严重且脱模剂使用量大,而大量使用脱模剂后脱模剂在高温下分解使得产品表面发黑,从而存在脱模效果欠佳的问题,具体为模具脏污而保养及更换周期频繁、产品产量及良品率低、使用成本过高、容易堵塞管道等。因此,开发一款不含硅油且脱模性能良好的脱模剂可弥补市场脱模剂产品的不足,对脱模剂市场应用及提升脱模产品质量具有重要意义。
技术实现要素:
3.本发明意在提供一种脱模性能优异的不含硅脱模剂及其制备方法,以解决现有无硅脱模剂脱模效果欠佳导致模具保养及更换周期频繁的技术问题。
4.为达到上述目的,本发明采用如下技术方案:一种脱模性能优异的不含硅脱模剂,包括如下质量份数的原料:苯乙烯-丙烯酸共聚物20~40份、有机磷酸酯10~20份、改性纤维素5~10份、乳化剂3~9份、表面活性剂1~3份和水70~150份。
5.本方案的原理及优点是:
6.1、与现有技术采用的含硅氧烷的脱模剂相比,本方案采用不含硅的原料进行复配,通过不同原料的相互作用,形成具有显著热稳定性、成膜性能、缓腐蚀性及润滑性能的不含硅脱模剂,符合环保指标;本方案所得脱模剂在产品和模具表面形成致密的疏水隔离层,有效改善模具滑块抽芯顶针以及点冷型芯的润滑效果,从而降低模具保养及更换周期,有效降低模具更换成本及时间,从而显著提升生产效率。
7.2、与现有技术采用的无硅脱模剂脱模效果欠佳相比,本方案所得脱模剂在产品生产中尤其是铝合金产品生产的过程中具有优异的性能,如24h产品生产量均大于9450件,产品良品率高达93%,产品表面光滑且成型效果好;有效避免出现现有含硅脱模剂具有的加工后的零件难清洗从而影响零件后工序的表面处理等问题。
8.3、本方案采用具有优异的热稳定性、防粘性能、水分散性能的苯乙烯-丙烯酸共聚物,使得制备的脱模剂耐温效果好、成膜效果佳,尤其是苯乙烯-丙烯酸共聚物形成线性结
构,其中苯乙烯和丙烯酸交替聚合,在共聚物中均匀地分散,使其制备的脱模剂更均匀的附着在模具及脱模产品表面,使得产品具有均匀的氧化着色性能,完全不影响产品的后续应用。
9.4、本方案采用有机磷酸酯和改性纤维素复配,两者相互作用,使得有机磷酸酯的润滑性能与改性纤维素的粘附性能叠加,显著提升脱模剂的成膜效果,改善脱模剂在模具上的成膜厚度和流变性能;结合有机磷酸酯的缓腐蚀性能,有效保持模具清洁干净,保护模具不受铝料的侵蚀。
10.5、与现有技术中脱模剂原料成本高相比,本方案中原料成本低、用量少,且原料绿色环保,有效降低脱模剂产品的环保压力和脱模剂生产成本。
11.优选的,所述有机磷酸酯为十二烷基聚氧乙烯磷酸酯。采用上述方案,本方案所有有机磷酸酯具有优异的热稳定性和润滑性能,同时具有良好的缓腐蚀性能,便于制备的脱模剂应用于高温金属件铸造中。
12.优选的,所述乳化剂为十二烷基硫酸钠、脂肪醇聚氧乙烯醚、脂肪酸聚氧乙烯酯中的任意一种或两种组合。采用上述方案,乳化剂环保高效,使脱模剂在储运时具有优异的动力学和热力学稳定性,同时在使用过程中具有快速的干燥成膜性能;同时还有效地降低了乳化剂的使用量,从而降低生产成本。
13.优选的,所述表面活性剂为脂肪酸聚氧乙烯醚。采用上述方案,便于进一步改善产品的分散清洁效果,防止模具及管道的淤堵,延长模具的使用寿命。
14.一种脱模性能优异的不含硅脱模剂的制备方法,包括如下步骤:
15.s1:将苯乙烯-丙烯酸共聚物、乳化剂与水混合,加热搅拌后冷却、静置得到溶液ⅰ;
16.s2:将十二烷基聚氧乙烯磷酸酯、乳化剂与水混合,加热搅拌后冷却、静置得到溶液ⅱ;
17.s3:将改性纤维素、乳化剂与水混合,加热搅拌后冷却、静置得到溶液ⅲ;
18.s4:将上述步骤得到的溶液ⅰ、溶液ⅱ、溶液ⅲ与水混合得到混合溶液,向混合溶液中加入脂肪酸聚氧乙烯醚,搅拌后静置即得不含硅脱模剂。
19.本方案的原理及优点是:
20.1、与现有技术中脱模剂生产工艺复杂相比,本方案将原料与乳化剂、水加热搅拌混合即可获得脱模剂产品,显著降低脱模剂生产难度,也显著提升脱模剂生产效率,更加适用于大规模生产;本方案生产出的脱模剂在铝合金铸件的实际生产应用中具有显著的热稳定性能,且能快速的干燥成膜,显著提升铝合金铸件生产效率,申请人实验发现,本方案制备的脱模剂具有非常优异的脱模性能,如在24h的铝合金铸件生产的产量大于9450件,且铝合金产品的良品率高达93%,产品表面光滑且成型效果好。
21.2、本方案采用分步法将原料苯乙烯-丙烯酸共聚物、十二烷基聚氧乙烯磷酸酯和改性纤维素分别形成乳液,原料本身具有较高的热稳定性、润滑性能、粘附性能和缓腐蚀性能使得原料制备得到的脱模剂乳液具有优异的动力学和热力学稳定性,便于运输和储存;当需要使用时,只需要将各种原料乳液和表面活性剂、水混合即可快速形成脱模剂产品,从而提高生产效率。
22.3、本方案中脱模剂的制备条件温和,且制备得到的产品具有优异的动力学稳定性和热力学稳定性,将其应用于铝合金铸件的实际生产中,其具有显著的热稳定性和成膜效
果,使得铝合金产品表面光滑、成型效果好且产品表面氧化着色均匀;另一方面,本方案所得脱模剂在各组分的协同增效作用下,制备的脱模剂在铝合金表面形成致密的疏水隔离层,有效改善模具滑块抽芯顶针以及点冷型芯的润滑效果,还能提高铝合金铸件质量和表面光洁度,显著提升铝合金铸件的生产质量和生产效率。
23.优选的,在s1中,加热搅拌的温度为60~80℃,加热搅拌的时间为0.5~1.5h。申请人实验发现,将苯乙烯-丙烯酸共聚物与乳化剂混合后,采用上述方案,有效形成苯乙烯-丙烯酸共聚物的乳化溶液,尤其是在70℃的恒温条件下具有最高的稳定性,有效保障制得脱模剂的热稳定性。
24.优选的,在s2和s3中,加热搅拌的温度为70~90℃,加热搅拌的时间为0.5~1.5h。采用上述方案,制备所得脱模剂乳液具有较高热稳定性,且能使得制得的脱模剂在50℃时保持长效热稳定性;便于脱模剂乳液的保存和运输,在保障脱模剂的脱模效果的同时进一步简化脱模剂的制备流程。
25.优选的,在s1中,乳化剂为十二烷基硫酸钠,苯乙烯-丙烯酸共聚物与十二烷基硫酸钠的质量份数比为20~40:1~3。因十二烷基硫酸钠易溶于水,对碱和硬水不敏感,具有优异的乳化效果,采用上述方案,便于苯乙烯-丙烯酸共聚物与水形成乳状液,且因其(十二烷基硫酸钠)生物降解度》90%,便于脱模剂使用后的降解处理,显著降低环保压力。
26.优选的,在s2中,乳化剂为脂肪醇聚氧乙烯醚,十二烷基聚氧乙烯磷酸酯与脂肪醇聚氧乙烯醚的质量份数比为10~20:1~3。采用上述方案,脂肪醇聚氧乙烯醚具有的酸碱稳定性及乳化效果,便于形成热稳定好的脱模剂乳液;且因其对酸碱稳定,有效维持脱模剂的稳定性,避免使用过程中被原料腐蚀,进一步提升脱模剂的耐腐蚀性,有效保持模具清洁干净,保护模具不受铝料的侵蚀。
27.优选的,在s3中,乳化剂为脂肪酸聚氧乙烯酯,改性纤维素与脂肪酸聚氧乙烯酯的质量份数比为5~10:1~3。采用上述方案,脂肪酸聚氧乙烯酯无毒、无刺激,且具有良好的乳化、增溶、润湿、分散、柔软及抗静电等表面活性,其与改性纤维素乳化形成乳液,充分发挥原料的粘附性能、乳化性能和分散性,显著提升脱模剂整体的脱模性能。
具体实施方式
28.下面结合实施例对本发明做进一步详细的说明,但本发明的实施方式不限于此。若未特别指明,下述实施例所用的技术手段为本领域技术人员所熟知的常规手段;所用的实验方法均为常规方法;所用的材料、试剂等,均可从商业途径得到。
29.以具体实施例展示一种脱模性能优异的不含硅脱模剂及其制备方法和其在铝合金铸件生产过程中的性能及效果说明。其中实施例1~5展示不同原料配比制备得到的脱模剂,对比例1~2分别展示现有yj-1脱模剂和进口脱模剂对铝合金铸件生产的效果;实施例1~5、对比例1~2中脱模剂制备过程中的原料成分及用量上的差异如表1所示。以实施例1为例,说明本方案中热稳定性能优异的脱模剂及其制备方法。
30.实施例1
31.一种脱模性能优异的不含硅脱模剂,包括如下质量份数的原料:
32.本实施例具体包括如下质量份数的原料:包括如下质量份数的原料:苯乙烯-丙烯酸共聚物20~40份、有机磷酸酯10~20份、改性纤维素5~10份、乳化剂3~9份、表面活性剂
1~3份和水70~150份。本实施例具体包括如下质量份数的原料:苯乙烯-丙烯酸共聚物20份、有机磷酸酯10份、改性纤维素5份、乳化剂6份、表面活性剂1份和水70份。
33.其中,有机磷酸酯为十二烷基聚氧乙烯磷酸酯。本方案有机磷酸酯具有优异的热稳定性和润滑性能,同时具有良好的缓腐蚀性能,便于制备的脱模剂应用于高温金属件铸造中。
34.乳化剂为十二烷基硫酸钠、脂肪醇聚氧乙烯醚、脂肪酸聚氧乙烯酯中的任意一种或两种组合,本实施例具体三种组合。乳化剂环保高效,使脱模剂在储运时具有优异的动力学和热力学稳定性,同时在使用过程中具有快速的干燥成膜性能;同时还有效地降低了乳化剂的使用量,从而降低生产成本。
35.表面活性剂为脂肪酸聚氧乙烯醚,本实施例具体为油酸聚氧乙烯醚。便于进一步改善产品的分散清洁效果,防止模具及管道的淤堵,延长模具的使用寿命。
36.本方案还提供一种脱模性能优异的不含硅脱模剂的制备方法,包括如下步骤:
37.s1:将苯乙烯-丙烯酸共聚物20份、乳化剂(本实施例具体为十二烷基硫酸钠)2份与水20份混合,加热至70℃(可选温度范围为60~80℃)后1000r/min搅拌1h(可选范围为0.5~1.5h),冷却静置得到苯乙烯-丙烯酸共聚物乳液;
38.s2:将十二烷基聚氧乙烯磷酸酯10份、乳化剂(本实施例具体为脂肪醇聚氧乙烯醚3份)与水20份混合,加热至80℃(可选温度范围为70~90℃)后1000r/min搅拌1h(可选范围为0.5~1.5h),冷却静置得到十二烷基聚氧乙烯磷酸酯乳液;
39.s3:将改性纤维素(购买至美国ashland公司,牌号natrosol plus)5份、乳化剂(本实施例具体为脂肪酸聚氧乙烯酯)1份与水30份混合,加热至80℃(可选温度范围为70~90℃)后1000r/min搅拌1h(可选范围为0.5~1.5h),冷却静置得到改性纤维素乳液;
40.s4:将上述步骤得到各原料乳液(包括苯乙烯-丙烯酸共聚物乳液、十二烷基聚氧乙烯磷酸酯乳液和改性纤维素乳液)混合形成混合溶液,向混合溶液中加入油酸聚氧乙烯醚1份,搅拌混匀后静置即得不含硅脱模剂。
41.表1实施例1~5、对比例1~2中脱模剂在原料成分及用量上的差异
[0042][0043]
实验数据表明,采用原料与不同乳化剂混合形成的乳液制备脱模剂,其脱模效果差异不大,因此只展示其中一种原料与乳化剂的组合方式,即苯乙烯-丙烯酸共聚物与十二烷基硫酸钠、十二烷基聚氧乙烯磷酸酯与脂肪醇聚氧乙烯醚、改性纤维素与脂肪酸聚氧乙烯酯的组合说明不同苯乙烯-丙烯酸共聚物、十二烷基聚氧乙烯磷酸酯及改性纤维素用量对脱模剂的热稳定性能、脱模效果等的影响。
[0044]
实验例:脱模剂性能检测
[0045]
为了表征脱模剂的性能,对实施例1~5、对比例1~2所得脱模剂进行了以下检测,具体检测方法如下:
[0046]
1)乳液粒径与多分散性:取样实施例1~5、对比例1~2所得脱模剂,在激光粒度仪中扫描,检测结果为扫描5次取平均值;
[0047]
2)剪切稳定性:将实施例1~5、对比例1~2所得脱模剂稀释100倍后用高速搅拌器(转速为1000r/min)搅拌30min,不破乳、不分层、不沉淀即判定为稳定;
[0048]
3)离心稳定性:将实施例1~5、对比例1~2所得脱模剂稀释10倍后在1000r/min条件下离心30min,不破乳、不分层、不沉淀即判定为稳定;
[0049]
4)热稳定性:将取样实施例1~5、对比例1~2所得脱模剂,在50℃烘箱内闭口放置24小时,不破乳、不分层、不沉淀即判定为稳定;
[0050]
5)铝合金腐蚀性:将经过抛光处理的铝合金块准确称重,随后浸入实施例1~5、对比例1~2所得脱模剂原液中,50℃保温24小时后取出用蒸馏水冲洗干净,干燥后称重,比较铝合金块前后的质量以及外观有无变化,比较脱模剂前后有无变色,若铝合金块在处理前后的重量差异在0.1%范围内、脱模剂颜色在处理前后无变化,则判定为脱模剂对铝合金无腐蚀性;
[0051]
6)脱模效果:使用实施例1~5、对比例1~2所得脱模剂,在10机台上生产铝合金产品(具体为中隔板)240小时,统计产品的产量、良品率、模具保养周期、机台备品配件(顶针、型芯等)损耗后取平均值,以此评价脱模剂的脱模效果。
[0052]
7)氧化着色性能:使用实施例1~5、对比例1~2所得脱模剂生产压铸工件,将压铸工件进行氧化着色,着色时选择浅色,以方便观察对着色的影响。实施例1~5、对比例1~2所得脱模剂性能测试结果详见表2。
[0053][0054]
实验结果表明,本方案的不含硅脱模剂的脱模性能优异,尤其是热稳定性高、润滑性能和脱模性能佳、乳液动力学和热力学稳定性好,对铝合金产品无腐蚀性等,显著优于现
有常用yj-1脱模剂和进口脱模剂的脱模效果。本方案实施例1~5制备所得脱模剂在多种原料的共同增效下,形成的脱模剂中固形物粒径较小,从而使得脱模剂乳液均一稳定(如实施例1~5中脱模剂乳液均具有较好的热稳定性、剪切稳定性、离心稳定性),尤其是对铝合金类约650~750℃的高温产品具有优异的脱模效果,也充分展现脱模剂的热稳定性。
[0055]
本方案实施例1~5制备的脱模剂在用于铝合金铸件生产时,24h铝合金的产量大于9450件(其中,使用实施例3中脱模剂时铝合金的产量高达9800件),显著高于使用对比例1~2时铝合金的产量(24h铝合金的产量为9200~9300件),且铝合金的良品率也较高,尤其是对比例3中铝合金的良品率高达96%,充分证明本方案制备的脱模剂具有非常优异的脱模效果,还能提高铝合金锻件质量和表面光洁度;同时使用本方案脱模剂还能明显降低模具保养次数和型芯用量,如采用实施例3脱模剂进行铝合金制造时型芯用量仅为45个,显著低于使用对比例1~2时的型芯用量(型芯用量均为60个);采用实施例1~5所得脱模剂进行铝合金铸件生产时模具保养频次(2次)明显低于采用对比例1~2所得脱模剂进行铝合金铸件生产时的模具保养频次(4次),显著节约模具维修成本和停机维修成本,进一步提升生产效率;主要是因为本方案中脱模剂中固形物分散性好,使得脱模剂在实际生产中成膜厚度均匀,成膜效果好,在模具和产品之间形成防温隔离的效果,避免生产过程中损伤磨具,提升对顶针和型芯的润滑效果,有效降低模具滑块抽芯顶针及型芯用量。
[0056]
且通过对铝合金铸件产品(中隔板)的氧化着色性能的检测,发现使用本方案中脱模剂脱模的产品具有良好、均匀的氧化着色性能,显著优于现有技术中脱模剂的脱模效果(使用对比例1~2脱模所得产品,其氧化着色均表现为有色差,表面具有不均匀斑块);主要是因为本方案采用的苯乙烯-丙烯酸共聚物具有优异的热稳定性、防粘性及水分散性等性能,尤其是苯乙烯-丙烯酸共聚物形成线性结构,其中苯乙烯和丙烯酸交替聚合,在共聚物中均匀地分散,使其制备的脱模剂更均匀的附着在模具及脱模产品表面,使得产品具有均匀的氧化着色性能,完全不影响产品的后续应用。
[0057]
综上,本方案通过将均匀聚合的苯乙烯-丙烯酸共聚物、有机磷酸酯和改性纤维素等结合起来,各组分间相互协同增效,显著提升脱模剂的脱模效果,且原料均绿色环保无毒,显著降低脱模剂的环保压力;同时有机磷酸酯和改性纤维素复配,显著增加脱模剂的黏附性而提升成膜效果,改善脱模剂在模具上的成膜厚度和流变性能,在模具和产品之间形成防温隔离的效果,有效保持模具清洁干净,避免生产过程中损伤磨具,尤其是对铝合金类约650~750℃的高温产品具有显著的脱模效果,充分展现脱模剂的热稳定性。
[0058]
以上所述的仅是本发明的实施例,方案中公知的具体技术方案和/或特性等常识在此未作过多描述。应当指出,对于本领域的技术人员来说,在不脱离本发明技术方案的前提下,还可以作出若干变形和改进,这些也应该视为本发明的保护范围,这些都不会影响本发明实施的效果和专利的实用性。本技术要求的保护范围应当以其权利要求的内容为准,说明书中的具体实施方式等记载可以用于解释权利要求的内容。
再多了解一些
本文用于企业家、创业者技术爱好者查询,结果仅供参考。