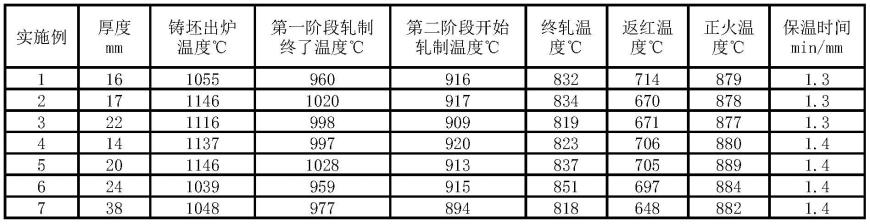
1.本发明涉及钢材生产技术领域,特别是涉及一种低温压力容器用微合金钢板及其生产方法。
背景技术:
2.随着石油化工等行业的发展,低温技术的开发促进了低温压力容器用钢的发展。传统方式是通过添加ni来改善低温冲击韧性,但ni是一种较贵重元素,会增加生产成本,并且含ni钢加热时易形成难以去除的致密氧化铁皮,影响产品表面质量。在复杂严峻的宏观环境、急剧变化的行业形势下,需要实现高效益、高效率生产,因此急需开发出一种高效率低成本低温压力容器用钢板的生产工艺。
3.目前在中厚板产品方面,常见的低温压力容器用钢板的成分设计主要是添加ni或v-n思路设计,如:
4.申请号为cn200710113574.x的发明专利公开了一种低温压力容器用钢板的生产方法,其钢板成分组成为:c:0.12~0.19%,si:0.15~0.45%,mn:1.2~1.6%,nb:0.015~0.050%,ti:0.01~0.03%,ni:0.10~0.35%,al:0.015~0.050%,p:0~0.015%;s:0~0.01%,其余为fe及不可避免的杂质。该钢的成分中含有ni元素,合金成本较高,最低冲击温度仅能满足-40℃的要求。
5.申请号为cn201711139404.9的发明专利公开了一种低温压力容器用钢板及其制造方法,其钢板成分组成为:c:0.110~0.140%,si≤0.15%,mn:1.30~1.60%,p≤0.015%,s≤0.005%,v:0.21~0.30%,n:0.0090~0.0220%,alt≤0.020%,其余为fe及不可避免的夹杂,同时满足:1.6≤v/c≤2.8,0.9≤v/(c si)≤1.25。该钢的成分中含有大量v元素,不仅合金成本较高,并且对焊接性能不利。920~960℃较高的正火温度以及长时间保温,也会增加工序成本,降低生产效率。
6.申请号为cn201210253970.3的发明专利公开了一种屈服强度460mpa级正火高强韧钢板及其制造方法”,其钢板成分组成为:c:0.14%~0.20%,si:0.20%~0.60%,mn:1.20%~1.70%,v:0.12%~0.20%,ni:0.15%~0.40%,n:0.005%~0.020%,alt:0.005%~0.040%,p≤0.015%,s≤0.005%,其余量为fe和不可避免的杂质。该钢的成分mn-v-ni-n系的成分设计,合金成本较高。
7.上述钢板中加入的贵重金属含量较多,并且部分生产方法不利于高效生产,生产成本较高。
技术实现要素:
8.鉴于以上所述现有技术的缺点,本发明的目的在于提供一种低温压力容器用微合金钢板及其生产方法,在保证足够的低温韧性前提下,不添加ni、v等贵重元素,采用nb、ti微合金化,通过“控轧控冷 正火”的生产工艺,高效率生产出低成本的低温压力容器用钢板。
9.为实现上述目的及其他相关目的,本发明第一方面提供一种低温压力容器用微合金钢板所述钢板的化学成分按质量百分数计包括:c 0.10~0.15%,si 0.19~0.25%,mn 1.40~1.50%,p≤0.015%,s≤0.007%,alt 0.020~0.045%,ti 0.010~0.020%,nb 0.010~0.020%,其余为fe和不可避免的杂质。
10.进一步,所述钢板的化学成分按质量百分数计包括:c 0.12~0.15%,si 0.19~0.24%,mn 1.41~1.50%,p≤0.015%,s≤0.007%,alt 0.022~0.044%,ti 0.012~0.020%,nb 0.012~0.018%,其余为fe和不可避免的杂质。
11.进一步,所述钢板的化学成分按质量百分数计包括:c 0.13~0.15%,si 0.19~0.24%,mn 1.42~1.50%,p≤0.015%,s≤0.007%,alt 0.024~0.044%,ti 0.014~0.020%,nb 0.012~0.017%,其余为fe和不可避免的杂质。
12.进一步,所述钢板的化学成分按质量百分数计包括:c 0.13~0.15%,si 0.19~0.24%,mn 1.42~1.50%,p≤0.015%,s≤0.005%,alt 0.024~0.044%,ti 0.014~0.020%,nb 0.012~0.017%,其余为fe和不可避免的杂质。
13.进一步,所述钢板的厚度为10mm~40mm,优选为14mm~38mm。
14.本发明第二方面提供根据第一方面所述的低温压力容器用微合金钢板的生产方法,包括如下步骤:kr铁水脱硫,转炉冶炼,lf精炼,rh精炼,连铸,铸坯加热,轧制,冷却,正火热处理,出炉后空冷。
15.进一步,所述生产方法中,kr铁水脱硫工序为:采用kr铁水脱硫,确保s含量≤0.005%。
16.进一步,所述生产方法中,转炉冶炼工序为:采用转炉冶炼,出钢全程钢包底吹氩,终点氧含量300~700ppm。
17.进一步,所述生产方法中,lf精炼工序为:采用lf精炼,深处理,钢包底吹氩,软吹时间≥5min,精炼时间≥30min,白渣保持时间≥10min。
18.进一步,所述生产方法中,rh精炼工序为:采用rh精炼,本处理,极限真空度≤273pa,极限真空度保持时间≥15min,软吹时间≥5min。
19.进一步,所述生产方法中,连铸工序为:采用连铸,中间包钢水n含量≤40ppm,恒速浇注。
20.进一步,所述生产方法中,加热工序为:铸坯在加热炉中加热,加热系数7~13min/cm,出炉温度1030~1150℃,保证铸坯烧透且加热均匀。
21.进一步,所述生产方法中,轧制工序为:采用两阶段控制轧制,第一阶段轧制终了温度≥950℃,第二阶段开始轧制温度≤920℃,终轧温度810~860℃。
22.进一步,所述生产方法中,冷却工序为:采用水冷方式,返红温度640~720℃。
23.进一步,所述生产方法中,热处理工序为:采用正火工艺进行热处理,正火温度875~890℃,炉内保温时间1.3~1.4min/mm,出炉后空冷。
24.如上所述,本发明的低温压力容器用微合金钢板及其生产方法,具有以下有益效果:
25.本发明采用nb、ti微合金化成分设计思路,通过“控轧控冷 正火”的生产工艺,在保证钢板具有足够的低温韧性的同时,通过降低合金成本,较添加ni、v元素设计思路的低温压力容器用钢板吨钢降本300元/吨以上,可实现低温压力容器用钢板低成本生产。
具体实施方式
26.以下通过特定的具体实例说明本发明的实施方式,本领域技术人员可由本说明书所揭露的内容轻易地了解本发明的其他优点与功效。本发明还可以通过另外不同的具体实施方式加以实施或应用,本说明书中的各项细节也可以基于不同观点与应用,在没有背离本发明的精神下进行各种修饰或改变。
27.本发明提供了一种低温压力容器用微合金钢板,所述钢板的化学成分按质量百分数计包括:c 0.13~0.15%,si 0.19~0.24%,mn 1.42~1.50%,p≤0.015%,s≤0.007%,alt 0.024~0.044%,ti 0.014~0.020%,nb 0.012~0.017%,其余为fe和不可避免的杂质。
28.进一步地,钢板的厚度为10mm~40mm,优选为14mm~38mm。
29.本发明提供的低温压力容器用微合金钢板的生产方法,包括如下步骤:
30.(1)采用kr铁水脱硫,确保s含量≤0.005%;
31.(2)采用转炉冶炼,出钢全程钢包底吹氩,终点氧含量300~700ppm;
32.(3)采用lf精炼,深处理,钢包底吹氩,软吹时间≥5min,精炼时间≥30min,白渣保持时间≥10min;
33.(4)采用rh精炼,本处理,极限真空度≤273pa,极限真空度保持时间≥15min,软吹时间≥5min;
34.(5)采用连铸,中间包钢水n含量≤40ppm,恒速浇注;
35.(6)铸坯在加热炉中加热,加热系数7~13min/cm,出炉温度1030~1150℃,保证铸坯烧透且加热均匀;
36.(7)轧制:采用两阶段控制轧制,第一阶段轧制终了温度≥950℃,第二阶段开始轧制温度≤920℃,终轧温度810~860℃;
37.(8)冷却:采用水冷方式,返红温度640~720℃;
38.(9)热处理:采用正火工艺进行热处理,正火温度875~890℃,炉内保温时间1.3~1.4min/mm,出炉后空冷。
39.下面具体的例举实施例以详细说明本发明。同样应理解,以下实施例只用于对本发明进行具体的说明,不能理解为对本发明保护范围的限制,本领域的技术人员根据本发明的上述内容作出的一些非本质的改进和调整均属于本发明的保护范围。下述示例具体的工艺参数等也仅是合适范围中的一个示例,即本领域技术人员可以通过本文的说明做合适的范围内选择而并非要限定于下文示例的具体数值。
40.实施例1
41.一种低温压力容器用微合金钢板,厚度为16mm,其化学成分按质量百分数计包括:c0.14%,si 0.23%,mn 1.49%,p 0.014%,s 0.003%,alt 0.036%,ti 0.015%,nb 0.014%,其余为fe和不可避免的杂质;其生产方法如下:
42.(1)采用kr铁水脱硫;
43.(2)采用转炉冶炼,出钢全程钢包底吹氩,终点氧含量300~700ppm;
44.(3)采用lf精炼,深处理,钢包底吹氩,软吹时间≥5min,精炼时间≥30min,白渣保持时间≥10min;
45.(4)采用rh精炼,本处理,极限真空度≤273pa,极限真空度保持时间≥15min,软吹
时间≥5min;
46.(5)采用连铸,中间包钢水n含量≤40ppm,恒速浇注;
47.(6)铸坯在加热炉中加热,加热系数7~13min/cm,出炉温度1055℃,保证铸坯烧透且加热均匀;
48.(7)轧制:采用两阶段控制轧制,第一阶段轧制终了温度960℃,第二阶段开始轧制温度916℃,终轧温度832℃;
49.(8)冷却:采用水冷方式,返红温度714℃;
50.(9)热处理:采用正火工艺进行热处理,正火温度879℃,炉内保温时间1.3min/mm,出炉后空冷。
51.实施例2
52.一种低温压力容器用微合金钢板,厚度为17mm,其化学成分按质量百分数计包括:c0.14%,si 0.22%,mn 1.49%,p 0.010%,s 0.003%,alt 0.044%,ti 0.016%,nb 0.012%,其余为fe和不可避免的杂质;其生产方法如下:
53.(1)采用kr铁水脱硫;
54.(2)采用转炉冶炼,出钢全程钢包底吹氩,终点氧含量300~700ppm;
55.(3)采用lf精炼,深处理,钢包底吹氩,软吹时间≥5min,精炼时间≥30min,白渣保持时间≥10min;
56.(4)采用rh精炼,本处理,极限真空度≤273pa,极限真空度保持时间≥15min,软吹时间≥5min;
57.(5)采用连铸,中间包钢水n含量≤40ppm,恒速浇注;
58.(6)铸坯在加热炉中加热,加热系数7~13min/cm,出炉温度1146℃,保证铸坯烧透且加热均匀;
59.(7)轧制:采用两阶段控制轧制,第一阶段轧制终了温度1020℃,第二阶段开始轧制温度917℃,终轧温度834℃;
60.(8)冷却:采用水冷方式,返红温度670℃;
61.(9)热处理:采用正火工艺进行热处理,正火温度878℃,炉内保温时间1.3min/mm,出炉后空冷。
62.实施例3
63.一种低温压力容器用微合金钢板,厚度为22mm,其化学成分按质量百分数计包括:c0.13%,si 0.23%,mn 1.46%,p 0.015%,s 0.005%,alt 0.030%,ti 0.014%,nb 0.014%,其余为fe和不可避免的杂质;其生产方法如下:
64.(1)采用kr铁水脱硫;
65.(2)采用转炉冶炼,出钢全程钢包底吹氩,终点氧含量300~700ppm;
66.(3)采用lf精炼,深处理,钢包底吹氩,软吹时间≥5min,精炼时间≥30min,白渣保持时间≥10min;
67.(4)采用rh精炼,本处理,极限真空度≤273pa,极限真空度保持时间≥15min,软吹时间≥5min;
68.(5)采用连铸,中间包钢水n含量≤40ppm,恒速浇注;
69.(6)铸坯在加热炉中加热,加热系数7~13min/cm,出炉温度1116℃,保证铸坯烧透
且加热均匀;
70.(7)轧制:采用两阶段控制轧制,第一阶段轧制终了温度998℃,第二阶段开始轧制温度909℃,终轧温度819℃;
71.(8)冷却:采用水冷方式,返红温度671℃;
72.(9)热处理:采用正火工艺进行热处理,正火温度877℃,炉内保温时间1.3min/mm,出炉后空冷。
73.实施例4
74.一种低温压力容器用微合金钢板,厚度为14mm,其化学成分按质量百分数计包括:c0.14%,si 0.19%,mn 1.50%,p 0.013%,s 0.005%,alt 0.026%,ti 0.015%,nb 0.016%,其余为fe和不可避免的杂质;其生产方法如下:
75.(1)采用kr铁水脱硫;
76.(2)采用转炉冶炼,出钢全程钢包底吹氩,终点氧含量300~700ppm;
77.(3)采用lf精炼,深处理,钢包底吹氩,软吹时间≥5min,精炼时间≥30min,白渣保持时间≥10min;
78.(4)采用rh精炼,本处理,极限真空度≤273pa,极限真空度保持时间≥15min,软吹时间≥5min;
79.(5)采用连铸,中间包钢水n含量≤40ppm,恒速浇注;
80.(6)铸坯在加热炉中加热,加热系数7~13min/cm,出炉温度1137℃,保证铸坯烧透且加热均匀;
81.(7)轧制:采用两阶段控制轧制,第一阶段轧制终了温度997℃,第二阶段开始轧制温度920℃,终轧温度823℃;
82.(8)冷却:采用水冷方式,返红温度706℃;
83.(9)热处理:采用正火工艺进行热处理,正火温度880℃,炉内保温时间1.4min/mm,出炉后空冷。
84.实施例5
85.一种低温压力容器用微合金钢板,厚度为20mm,其化学成分按质量百分数计包括:c0.14%,si 0.19%,mn 1.50%,p 0.013%,s 0.005%,alt 0.026%,ti 0.015%,nb 0.016%,其余为fe和不可避免的杂质;其生产方法如下:
86.(1)采用kr铁水脱硫;
87.(2)采用转炉冶炼,出钢全程钢包底吹氩,终点氧含量300~700ppm;
88.(3)采用lf精炼,深处理,钢包底吹氩,软吹时间≥5min,精炼时间≥30min,白渣保持时间≥10min;
89.(4)采用rh精炼,本处理,极限真空度≤273pa,极限真空度保持时间≥15min,软吹时间≥5min;
90.(5)采用连铸,中间包钢水n含量≤40ppm,恒速浇注;
91.(6)铸坯在加热炉中加热,加热系数7~13min/cm,出炉温度1146℃,保证铸坯烧透且加热均匀;
92.(7)轧制:采用两阶段控制轧制,第一阶段轧制终了温度1028℃,第二阶段开始轧制温度913℃,终轧温度837℃;
93.(8)冷却:采用水冷方式,返红温度705℃;
94.(9)热处理:采用正火工艺进行热处理,正火温度889℃,炉内保温时间1.4min/mm,出炉后空冷。
95.实施例6
96.一种低温压力容器用微合金钢板,厚度为24mm,其化学成分按质量百分数计包括:c0.14%,si 0.24%,mn 1.49%,p 0.010%,s 0.003%,alt 0.035%,ti 0.020%,nb 0.014%,其余为fe和不可避免的杂质;其生产方法如下:
97.(1)采用kr铁水脱硫;
98.(2)采用转炉冶炼,出钢全程钢包底吹氩,终点氧含量300~700ppm;
99.(3)采用lf精炼,深处理,钢包底吹氩,软吹时间≥5min,精炼时间≥30min,白渣保持时间≥10min;
100.(4)采用rh精炼,本处理,极限真空度≤273pa,极限真空度保持时间≥15min,软吹时间≥5min;
101.(5)采用连铸,中间包钢水n含量≤40ppm,恒速浇注;
102.(6)铸坯在加热炉中加热,加热系数7~13min/cm,出炉温度1039℃,保证铸坯烧透且加热均匀;
103.(7)轧制:采用两阶段控制轧制,第一阶段轧制终了温度959℃,第二阶段开始轧制温度915℃,终轧温度851℃;
104.(8)冷却:采用水冷方式,返红温度697℃;
105.(9)热处理:采用正火工艺进行热处理,正火温度884℃,炉内保温时间1.4min/mm,出炉后空冷。
106.实施例7
107.一种低温压力容器用微合金钢板,厚度为38mm,其化学成分按质量百分数计包括:c0.15%,si 0.22%,mn 1.42%,p 0.012%,s 0.004%,alt 0.024%,ti 0.015%,nb 0.017%,其余为fe和不可避免的杂质;其生产方法如下:
108.(1)采用kr铁水脱硫;
109.(2)采用转炉冶炼,出钢全程钢包底吹氩,终点氧含量300~700ppm;
110.(3)采用lf精炼,深处理,钢包底吹氩,软吹时间≥5min,精炼时间≥30min,白渣保持时间≥10min;
111.(4)采用rh精炼,本处理,极限真空度≤273pa,极限真空度保持时间≥15min,软吹时间≥5min;
112.(5)采用连铸,中间包钢水n含量≤40ppm,恒速浇注;
113.(6)铸坯在加热炉中加热,加热系数7~13min/cm,出炉温度1048℃,保证铸坯烧透且加热均匀;
114.(7)轧制:采用两阶段控制轧制,第一阶段轧制终了温度977℃,第二阶段开始轧制温度894℃,终轧温度818℃;
115.(8)冷却:采用水冷方式,返红温度648℃;
116.(9)热处理:采用正火工艺进行热处理,正火温度882℃,炉内保温时间1.4min/mm,出炉后空冷。
117.实施例1~7中的钢板的钢板化学成分组成、生产主要工艺参数如表1、表2所示,经检测,钢板的实物性能如表3所示。
118.表1.实施例1~7的钢板化学成分组成(按质量百分数计,%)
119.实施例csimnpsalttinb10.140.231.490.0140.0030.0360.0150.01420.140.221.490.0100.0030.0440.0160.01230.130.231.460.0150.0050.0300.0140.01440.140.191.500.0130.0050.0260.0150.01650.140.191.500.0130.0050.0260.0150.01660.140.241.490.0100.0030.0350.0200.01470.150.221.420.0120.0040.0240.0150.017
120.表2.实施例1~7的钢板生产主要工艺参数
[0121][0122]
表3.实施例1~7的钢板实物性能
[0123][0124]
上述实施例仅例示性说明本发明的原理及其功效,而非用于限制本发明。任何熟悉此技术的人士皆可在不违背本发明的精神及范畴下,对上述实施例进行修饰或改变。因此,举凡所属技术领域中具有通常知识者在未脱离本发明所揭示的精神与技术思想下所完成的一切等效修饰或改变,仍应由本发明的权利要求所涵盖。
再多了解一些
本文用于企业家、创业者技术爱好者查询,结果仅供参考。