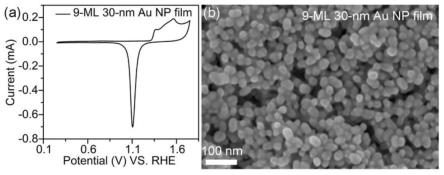
1.本发明涉及纳米多孔材料制作的技术领域,具体而言,涉及一种通过高效、温和、可控的直流电焊接,制备高纯度的三维纳米多孔金属的方法。
背景技术:
2.近年来,三维多孔金属如三维纳米多孔金(npg)因其高的比表面积和金的固有特性而引起的高导电性、大表面积、表面等离激元和电化学活性等特性,获得人们的广泛关注。因此,三维npg在表面增强拉曼散射、催化、生化传感和能量存储等领域都具有广阔的应用前景。对于所有这些下游的应用,它们能实现的基础是三维npg大规模、低成本和可行性强的制造方法。
3.目前,三维npg的制备方法主要可分为电化学阳极氧化法、模板沉积法和脱合金法三种类型。其中,电化学阳极氧化法是通过金电极在腐蚀性电解质溶液中的蚀刻,制备三维npg。模板沉积法是通过物理或电化学的方法,将金沉积到多孔模板中,随后的去除模板,从而制得三维npg。而脱合金法是目前最常用的三维多孔金制备方法,一般来说,它利用合金组分的物理化学性质差异,例如电化学活性、蒸气压或溶解度,有选择地从合金中去除多余的成分,从而剩下三维多孔金骨架,制得三维npg。但由于合金法的制备过程中存在能耗高、资源浪费、腐蚀性试剂的使用、多余组分的残留等问题,目前脱合金法还不是特别理想的方法。
4.此外,随着纳米合成技术的不断发展,各种各样的纳米颗粒溶胶都可通过合适的手段制备出来。除了其多样化的应用领域,高质量、高纯度的纳米颗粒溶胶的易得性也表明它们是自下而上制造纳米多孔材料的理想构件。例如,金纳米孔超结构(如海绵)状已经成功地通过ph诱导的金纳米颗粒(au np)在溶液中的线性聚集,卤素离子诱导的aunp在溶液中的三维聚集,hcl、热辐射和光辐射诱导/激活的aunp界面二维组装,硫代聚乙二醇和水热处理诱导au np在溶液中三维自组装。虽然文献上已经报道了许多方法,但它们多数在某种程度上具有较差的普遍性,因为它们需要精细地控制制造过程中条件,并且无法精细调节纳米多孔结构的纳米结构。
技术实现要素:
5.本发明的第一目的在于提供一种通过直流电焊接制备三维纳米多孔金属的全新思路和方法,旨在高效、温和、可控地制备三维纳米多孔金属。
6.本发明第二目的在于,提供所述的直流电焊接方法制得的三维纳米多孔金属。
7.本发明第三目的在于,提供所述的直流电焊接方法制得的三维纳米多孔金属在制备光学、电学、电化学、传感中的至少一种器件中的应用。
8.现有的三维多孔金属主要是通过电化学阳极氧化法、模板沉积法和脱合金法制备,本发明跳脱出行业固有制备思维,在行业内首次提出采用金属颗粒的纳米焊接的思路制备三维多孔金属,但研究发现,不同于单层金属纳米焊接,纳米焊接制备三维多孔金属还
存在诸多技术难点需要攻克,例如,需要克服金属颗粒膜层间适配性差、难于复合形成多孔金属膜前驱体的问题,此外,还需要克服层内和层间金属颗粒界面难于同步熔合以及容易出现结构塌陷等问题。针对纳米焊接制备三维多孔金属存在的难点,本发明人经过深入研究,提供以下技术方案:
9.一种三维纳米多孔金属的直流电焊接制备方法,包括以下步骤:
10.步骤(1):
11.在基底表面进行n次金属颗粒膜的逐层复合处理,形成n层金属颗粒膜依次复合的多层复合前驱体;其中,第二次~第n次复合前,预先对上一次的金属颗粒膜表面进行干燥以及等离子体处理;所述的n为大于或等于2的整数;
12.步骤(2):
13.向多层复合前驱体通入电流强度为0.2~0.6a的直流电,进行直流电强化焊接处理,制得三维纳米多孔金属。
14.本发明研究发现,创新地采用等离子体辅助的逐层复合方式,进一步配合非溶液体系下的直流电强化纳米强化方式以及直流电强化电流强度的联合控制,能够实现协同,能够成功构建纳米多孔金属,有效控制焊接均匀性,避免难于焊接熔合以及结构塌陷等问题,且制备的材料具有优异的性能。不仅如此,本发明制备条件温和、容易实现,且金属结构容易条件,具有良好的制备前景。
15.本发明研究发现,所述的多层前驱体的逐层复合思路以及等离子体的联合辅助,能够有效克服金属纳米颗粒层的层间不适配的问题,利于多层金属颗粒膜的复合,利于多孔金属的制备。
16.本发明中,采用逐层金属颗粒复合方式并在金属颗粒层复合后进行干燥-等离子体处理后再复合下一层的金属颗粒层,如此利于克服金属颗粒层的层间不适配的问题。
17.本发明所述的金属颗粒膜复合过程例如为:在基底上先形成第一层的金属颗粒膜,随后经干燥-等离子体处理后,再复合第二层的金属颗粒膜,随后经干燥-等离子体处理后再复合下一层的金属颗粒层,重复干燥-等离子体-金属颗粒膜复合处理操作n-1次,从而制得逐层复合有n层金属颗粒膜的多孔前驱体。
18.本发明中,基底为非导电基底,优选为不导电的玻璃基底。
19.本发明中,所述的各层金属纳米颗粒膜可基于现有方法制备,如可以采用液-液界面自组装或气-液界面转移形成各层的金属颗粒膜。所述的液-液界面自组装步骤例如为:预先制备分散有纳米金属颗粒的水悬浮液,随后和疏水溶剂混合,在水-疏水溶剂界面进行金属颗粒的自组装(界面重排),收集界面自组装得到的金属纳米颗粒层,即为所述的各层的金属纳米颗粒膜。本发明中,所述的各层的金属纳米颗粒膜指收集得到的主要为单层金属颗粒排列形成的膜层,但不排除局部可能存在多层金属颗粒堆叠的情况。另外,各层金属颗粒膜中,所述的金属纳米颗粒之间的间隙小于或等于2nm。本发明中,多层复合前驱体中,层间的金属颗粒间隙小于或等于1nm;优选为相互接触。
20.本发明中,所述的金属颗粒的材质、颗粒粒径以及逐层复合的层数可根据制得的多孔金属材料的应用场景要求进行调整。
21.本发明中,所述的金属颗粒为导电金属的纳米颗粒;优选地,所述的导电金属为金、银、钯、铂中的至少一种。
22.本发明中,所述的金属颗粒为球形颗粒,其粒径为3~100nm;优选为3~70nm;进一步优选为10~50nm。
23.作为优选,所述的n为2~350的整数;优选为2~20的整数。
24.本发明中,对金属颗粒膜层的表面进行干燥处理,用于脱除其中的溶剂以及固化:本发明所述的干燥例如为自然干燥。干燥后,再对金属颗粒膜层进行等离子体处理,随后再复合下层的单层金属颗粒膜。
25.本发明中,所述的等离子体处理过程中的功率小于或等于80w;优选为20~50w,进一步优选为30~40w。研究发现,通过优选功率的n2等离子体处理,利于改善层间金属颗粒的性质适配性,利于金属颗粒膜层的复合。
26.本发明中,等离子体处理气体氛围是n2、惰性气体中的至少一种。
27.本发明中,n2等离子体处理的时间0.5~1min。
28.本发明中,最后一层的金属颗粒膜复合后,经干燥处理后进行后续的直流电强化焊接。
29.本发明研究发现,创新地采用非溶液体系下的直流电强化焊接工艺,配合电流强度的协同控制,能够利于层内和层间金属的均匀焊接,避免结构塌陷,利于制得性能优异的三维多孔金属。
30.本发明中,焊接过程在干燥气氛中进行。本发明研究发现,在非溶剂性电强化下,进一步配合直流电强化方式的控制,能够进一步诱导层内和层间金属颗粒的表面电子局域化,从而实现金属表面原子扩散。
31.优选地,所述的干燥气氛为干燥的空气、氮气、惰性气体中至少一种。
32.本发明研究发现,在直流电作用下,能够有效诱导金属纳米颗粒表面电子局域化,可促使金属表面原子扩散,实现金属纳米颗粒之间的焊接;研究还发现,在所述的非溶液直流电强化下,进一步配合电流强度的控制,能够进一步协同改善层内和层间金属颗粒的焊接效果。优选地,所述的电流强度为0.2~0.5a;进一步优选为0.3~0.4a;
33.优选地,焊接处理的时间为5s~20min,,进一步优选为20s~15min;更进一步优选为1~5min。
34.优选地,相对电流强度为电流强度/(金属颗粒粒径
×
n),其范围为0.3~4ma/nm;进一步优选为0.7~3.5ma/nm。
35.本发明一种制备npg的直流电焊接方法,综合液-液界面自组装、气-液界面转移、自然干燥-等离子体处理等过程制备多层au np薄膜,通过直流电对待处理的多层aunp薄膜对au np表面进行电子局域化处理,从而促使au np表面原子扩散,实现aunp之间的纳米焊接,制得npg。
36.本发明创新地发现,采用等离子体辅助方式制备多层au np薄膜,并对金属纳米颗粒表面电子进行局域化处理,能够促使金属表面原子扩散,在快速、温和、可控的条件下即可实现au np之间的纳米焊接,进而高效制备高纯度的三维纳米多孔金属。本发明优选的方案,提供了一种可行的自下而上纳米焊接策略,从不同尺寸的au np中制备高纯度的三维npg。au np首先通过界面自组装技术和分层转移技术获得多层au np薄膜(表示为x-mly-nmau np薄膜,x和y分别代表au np薄膜的层数(即单层的数量)和au np的尺寸(直径)),然后通入直流电对其进行纳米焊接。因此,这种自下而上的方法的可调控性很强,可以通过改
30-nmnpg)的电化学和形貌表征。
72.其中,图13中,a为7-ml 30-nm npg在0.5m h2so4(扫速为50mv
·
s-1
)中的循环伏安曲线;b为7-ml 30-nmnpg的sem图像。
73.图14:为9-ml 30-nmau np薄膜经过0.4a的直流电处理5分钟后制得的npg(9-ml 30-nmnpg)的电化学和形貌表征。
74.其中,图14中,a为9-ml 30-nm npg在0.5m h2so4(扫速为50mv
·
s-1
)中的循环伏安曲线;b为9-ml 30-nmnpg的sem图像。
75.图15:为x-ml 30-nmau np薄膜经过直流电处理5分钟后制得的npg的ecsa汇总。
76.图16:为17-ml 16-nmau np薄膜(17-ml 16-nmaunp film)经过0.403a的直流电处理5分钟后制得的npg(17-ml 16-nm npg)的电化学和形貌表征。
77.其中,图16中,a为17-ml 16-nm au np film和17-ml 16-nm npg在0.5mh2so4(扫速为50mv
·
s-1
)中的循环伏安曲线;b为17-ml 16-nm npg的sem图像。
78.图17:为9-ml 30-nmau np薄膜(9-ml 30-nmau np film)经过0.4a的直流电处理5分钟后制得的npg(9-ml 30-nmnpg)的电化学和形貌表征。
79.其中,图17中,a为9-ml 30-nm au np film和9-ml 30-nm npg在0.5mh2so4(扫速为50mv
·
s-1
)中的循环伏安曲线;b为9-ml 30-nm的sem图像。
80.图18:为6-ml 50-nmau np薄膜(6-ml 50-nm au np film)经过0.444a的直流电处理5分钟后制得的npg(6-ml 50-nmnpg)的电化学和形貌表征。
81.其中,图18中,a为6-ml 50-nm au np film和6-ml 50-nm npg在0.5mh2so4(扫速为50mv
·
s-1
)中的循环伏安曲线;b为6-ml 50-nmnpg的sem图像。
82.图19:为x-mly-nmau np薄膜经过直流电处理5分钟前、后的ecsa汇总。
83.图20:为在0.1m koh 1.0m ch3oh电解液中,甲醇在9-ml 30-nmau np film电极及制备的9-ml 30-nm npg电极上的电催化氧化。
84.其中,图20中,a为循环伏安曲线(扫速为10mv
·
s-1
);b为交流阻抗图谱及模拟的等效电路图(插图);c为在1.1v(参比电极为可逆氢电极)电势下的计时电流曲线。
85.图21:为电流强度在下限范围和上限范围内焊接处理9-ml 30-nm aunp薄膜后的形貌表征。
86.其中,图21中,a为9-ml 30-nm au np薄膜经过0.1a的直流电处理5分钟后制得的sem表征图;b为9-ml 30-nm au np薄膜经过3.0a的直流电处理5秒钟后制得的sem表征图.
87.图22:为在不同氛围和电流类型下处理2-ml 50-nm au np薄膜后的形貌表征。
88.其中,图22中,a为2-ml 50-nm aunp薄膜经过0.2a的直流电在空气中焊接处理5min后的sem表征图;b为2-ml 50-nm aunp薄膜经过0.2a的直流电在水中焊接处理5min后的sem表征图;c为2-ml 50-nm au np薄膜经过0.2a 50hz的交流电在空气中焊接处理5min后的sem表征图
89.图23:直流电纳米焊接机理的示意图。
具体实施方案
90.下面将结合实施例对本发明的实施方案进行详细描述,但是本领域技术人员将会理解,下列实施例仅用于说明本发明,而不应视为限制本发明的范围。实施例中未注明具体
条件者,按照常规条件或制造商建议的条件进行。所用试剂或仪器未注明生产厂商者,均为可以通过市售购买获得的常规产品。
91.本发明所提供方法,是将经典的frens法(即在柠檬酸三钠作为稳定剂和还原剂的环境中还原氯金酸)得到的50nmau np(au np),通过界面自组装的方法,组装成致密的au np薄膜,随后进行外场强化、低温、溶液-扩散、温和、速度可控的奥斯特瓦尔德纳米焊接,从而在避免破坏被焊接的au np的原本形貌和结构的同时,增强了aunp薄膜的导电性和电催化活性。
92.本发明方法具体步骤可参考如下:
93.(a)由frens法所得到的au np分散液的浓度约为57.91μg nps/ml;所述的aunp为球形颗粒。
94.其中,用以分散au np的溶剂为水,稳定剂为合成反应前添加的柠檬酸三钠。
95.(b)采用界面自组装的方式,将au np组装成致密的aunp薄膜,并转移至2mm
×
10mm的玻璃基底上,自然干燥后,重复转移,得到多层au np薄膜组成的前驱体;
96.作为优选,界面自组装的主要细节为,首先将制得的20ml au np分散液置入50ml的烧杯中;随后加入约5ml环己烷,形成清晰的水-油界面;随后快速注入10ml乙醇,引发au np在水-油界面自组装成致密aunp薄膜;最后,将水-油界面上au np薄膜上层的环己烷移除,并将au np薄膜重复转移到相应的基底上。待au np薄膜在自然干燥后,在40w的功率下,进行表面等离子(n2气氛)处理30s,为下一层au np薄膜的转移提供支持,根据制备需要,重复进行界面自组装-干燥-等离子体处理n-1次,最后一次组装完成后,干燥获得n层单层的aunp薄膜逐层复合的多层材料。
97.而如上所形成的多层aunp薄膜,即为本发明中待焊接处理的对象。
98.(c)将如上所制得的多层aunp薄膜进行干燥,放置在焊接装置中,在干燥空气氛围内进行直流电焊接,并用精密测试电源b2912a(keysight,united states),对焊接过程中的金膜的电阻进行测试与记录,然后计算相对电阻变化率,随焊接条件的变化。
99.作为优选,在直流电焊接过程中,所用直流电强度有0.2、0.3、0.4、0.5、0.6a,通过调节电流强度,对制得的npg的性能和微观结构进行调节。
100.作为优选,在直流电焊接过程中,固定输入的电流强度为0.4a,通过调节通电时间,对制得的npg的性能和微观结构进行调节。
101.作为优选,在直流电焊接过程中,固定au np的直径为30nm,通过调节au np薄膜的厚度(也即是单层aunp薄膜的层数,接近au np的直径
×
层数),本文分别采用厚度为1(单层,作为对比)、3、5、7、9层,对制得的npg的厚度进行调节。
102.作为优选,在直流电焊接过程中,在接近的多层au np薄膜的总厚度(17层16nm aunp薄膜、9层30nm au np薄膜、6层50nm au np薄膜)和相对电流强度为1.48ma/nm(本发明中的相对电流强度通过实际电流强度/(薄膜的层数
×
颗粒直径计算而成)),通过调节au np的尺寸,本文分别采用直径为16nm、30nm、和50nm au np组装而成的au np薄膜为前驱体,对制得的npg的性能和微观结构进行调控。
103.作为优选,直流电焊接多层aunp薄膜过程中,除了探究焊接时间对npg性能和形貌影响的焊接时间为0-15min,和不同焊接环境(空气或水)及不同类型的电流(直流或交流)的对比实验中的时间为20min,其他探究过程的焊接时间均为5min。
104.实施例1
105.按照如下方法,进行aunp的界面自组装及转移:
106.步骤1:将制得的20ml au np(粒径为30nm)分散液置入50ml的烧杯中,随后加入约5ml环己烷,形成清晰的水-油界面。
107.步骤2:快速注入10ml乙醇,引发au np在水-油界面自组装成致密au np薄膜,随后将水-油界面上au np薄膜上层的环己烷移除,将该致密的au np薄膜转移至2mm
×
10mm的玻璃基底上,自然干燥后,得到单层的au np薄膜;
108.此外,根据制备需要进行逐层自组装转移处理,且转移下一层之前,预先对au np薄膜进行自然干燥以及n2等离子体处理(40w)30s;最后一层转移完成后,进行干燥处理,得到n层复合的多层膜,例如,本案例分别在第一单层膜表面进行2次、4次、6次和8次的干燥-等离子体处理后的转移处理,分别制得3、5、7和9层(所述的层数也即使逐层复合的次数)逐层复合的多层aunp薄膜组成的前驱体(分别标记为3-ml 30-nm au np薄膜、5-ml 30-nm au np薄膜、7-ml 30-nm au np薄膜、9-ml 30-nm aunp薄膜);
109.实施例1中au np的界面自组装和转移,及不同层au np膜的数码照片,及其在自制纳米焊接装置中的纳米焊接的示意图,请参考图1。由图1可知,随着多层aunp薄膜层数的增多,其金的光泽逐渐加深。
110.实施例2
111.按照如下方法,进行多层aunp薄膜的不同电流强度下的直流电焊接:
112.步骤1:用精密测试电源b2912a设置输出各电流强度条件下对应的参数。
113.步骤2:将转移至玻璃基底上干燥的多层au np薄膜(实施例1制得的9-ml30-nm au np薄膜),放置到焊接装置中,并在大气环境中,室温下,且分别在电流强度为0.2、0.3、0.4、0.5、0.6a的条件下,对多层aunp薄膜进行焊接5min。
114.步骤3:对在不同电流强度下焊接多层au np薄膜5min后制得的npg进行电化学表征和sem表征。
115.实施例2中,不同电流强度下焊接多层aunp薄膜5min后制得的npg的电化学表征,以及相关的sem表征图,请参考图2-8。由图2-8可知,与未焊接的9-ml 30nm aunp薄膜相比,经过直流电焊接制得的三维纳米多孔金的有效电化学面积(ecsa)随直流电强度的增加而不断降低,同时电阻值也逐渐降低。这表明,相邻aunp之间形成了牢固的结合,这不仅降低了aunp薄膜的整体ecsa,而且降低了其电阻(因为形成了有效的电子传递路径)。此外,通过对不同直流电强度下制得的三维纳米多孔金的sem表征图可知,在相同的处理时间(此处为5min),随着直流强度的增加,纳米焊接在0.2a时开始形成相邻au nps之间的牢固的结合,而这种结合在0.3和0.4a时变得更加明显,导致三维纳米多孔金中连续韧带的形成。如果进一步增加直流电的强度,部分区域的韧带尺寸甚至比au np母体的还要宽,同时,纳米孔也变得更宽,这表明在韧带的某些部位存在表面扩散原子的过分沉积。因此,在三维纳米多孔金的制备过程中,采用的直流电其强度不可过强,因为过宽的韧带和过大的纳米孔可能会破坏三维纳米多孔金的某些性能,例如,其电催化性能。
116.实施例3
117.按照如下方法,进行多层au np薄膜在固定电流强度,不同通电时间下的焊接:
118.步骤1:固定电流强度为0.4a,设置不同通电时间。
119.步骤2:将转移至玻璃基底上的多层au np薄膜(实施例1制得的9-ml30-nm au np薄膜),放置到焊接装置中,并在大气环境中,室温下,对多层au np薄膜进行焊接0-15min,并实时监控焊接过程中aunp薄膜的电阻变化。
120.步骤3:对不同通电时间焊接处理制得的npg进行电化学表征;
121.步骤4:根据电化学性能和电阻随时间变化的规律,选择性取各条件焊接后的aunp薄膜,进行形貌表征。
122.实施例3中,不同通电时间焊接处理制得的npg的电化学性质、电阻变化情况,以及sem表征图像,请参考图9。由图9可知,随着直流电纳米焊接时间的增加,制得的三维纳米多孔金的ecsa和电阻在0~7min内会迅速下降,基于sem表征图,在10~20s的焊接时间内,即可形成一个由韧带和纳米孔组成的高度互联的三维纳米多孔金,韧带尺寸与au nps的母体接近。随着焊接时间大于20s后的持续增大,韧带不断变宽。
123.实施例4
124.按照如下方法,在直流电焊接过程中,通过调节前驱体多层30-nmau np薄膜的层数(1、3、5、7、9层;实施例1制备),通过直流电焊接对制得的npg的厚度进行调节:
125.步骤1:将转移至玻璃基底上的多层au np薄膜(aunp为球形颗粒,其尺寸为30nm),放置到自主设计的焊接装置中,并在大气环境中,室温下,在不同的电流强度(0.044a对1层,0.311a对3、5、7层,0.4a对9层)下对多层30-nmau np薄膜进行焊接5min。
126.步骤2:对不同层数的多层30-nm au np薄膜焊接处理5min制得的npg进行电化学表征及sem表征;
127.实施例4中,不同层数的多层30-nmau np薄膜焊接处理5min制得的npg的电化学性质,以及sem表征图像,请参考图10-15。由图10-15可知,随着30-nmau np薄膜层数的增多,焊接后制得的三维纳米多孔金的ecsa和厚度都逐渐增大,因而可以通过改变初始au np薄膜来改变制得的三维纳米多孔金结构和性能。
128.实施例5
129.按照如下方法,在直流电焊接过程中,通过调节前驱体多层au np薄膜的au np的尺寸,通过直流电焊接对制得的npg的性能和微观结构进行调节:
130.步骤1:将转移至玻璃基底上的多层aunp薄膜(17-ml16-nmaunp薄膜、9-ml 30-nmau np薄膜、6-ml 50-nmau np薄膜),放置到自主设计的焊接装置中,并在大气环境中,室温下,在1.48ma/nm电流密度下(0.403a对17-ml16-nm au np薄膜、0.4a对9-ml 30-nm au np薄膜、0.444a对6-ml50-nmau np薄膜)对多层aunp薄膜进行焊接5min。
131.步骤2:对焊接前的多层au np薄膜和焊接后制得的npg进行电化学表征及sem表征;
132.实施例5中,焊接前的多层au np薄膜和焊接后制得的npg的电化学性质,以及sem表征图像,请参考图16-19。由图16-19可知,制得的npg纳米结构(韧带和纳米孔的尺寸)可以通过改变初始aunps的尺寸来有效调节。
133.实验例1
134.以实施例3中,未进行直流电焊接的9-ml 30-nmau np薄膜和经0.4a直流电焊接5min后制得的npg为实验材料,进行电化学、电学、sem形貌表征,电催化性能表征,结果如图2、5、8、20所示。
135.由图2a、5a、8a中的电化学可知,经焊接处理后制得的npg的ecsa相比前驱体9-ml 30-nmau np薄膜会有略微的下降,这是因为在焊接处理过程中,au np之间的间隙被填充,导致有部分电化学活性位点的消失。此外,由图2b和图5b中的sem表征图可知,经焊接处理后au np之间原有的间隙被填充,而制得的npg由具有整体互连的纳米韧带和纳米孔组成。由图8b中的电学数据可知,经焊接处理后制得的npg的电阻相比前驱体9-ml 30-nmaunp薄膜会有明显的下降,这就进一步证明在焊接处理过程中,au np之间的间隙被填充,au np之间的电流传输阻力更小。
136.由图20a中的循环伏安曲线可知,在正扫描时,9-ml 30-nmau np薄膜和9-ml 30-nm npg均在1.22v左右出现了甲醇电氧化的氧化峰。在甲醇电氧化过程中,oh-阴离子首先吸附在au电极表面,导致au氧化物的形成,进而导致甲醇电氧化。在负扫描时,它们都在1.13v处出现了还原峰,这是由于剩余的au氧化物被剥离造成的。值得注意的是,npg上甲醇电氧化的峰值电流强度(89.13μa/cm2)是未焊接的9-ml 30nmau np薄膜上的峰值电流强度(53.1250μa/cm2)的1.68倍。显然,经焊接处理后制得的npg相比前驱体未焊接的9-ml 30nmau np薄膜对甲醇电氧化表现出更优异的电催化活性,这可以通过eis研究进一步理解。图20b为9-ml 30-nmau np薄膜和9-ml 30-nmnpg在n2饱和的0.1mkoh 1.0m ch3oh溶液中的交流阻抗图谱,以及它们的等效电路(插图)。9-ml 30-nmau np薄膜和9-ml 30-nm npg均在高频区呈半圆形,在低频区没有warburg阻抗线,表明反应动力学受电荷转移过程控制。所得9-ml 30-nm npg的电解质阻抗rs(70.87ω
·
cm2)与9-ml 30-nm au np薄膜的(92.76ω
·
cm2)相当,但电荷传递阻抗要小得多(2529.63对4763.00ωcm2)。因此,相对于其母体9-ml 30-nmaunp薄膜,9-ml 30-nm npg对甲醇电氧化的电催化活性显着提高,这归因于其高电导率、更多暴露的电化学活性位点和大表面积的协同作用。
137.我们最终使用计时电流法研究检查了9-ml 30-nm au np薄膜和9-ml30-nm npg的电催化性能的稳定性(图20c)。在1.1v(相对于可逆氢电极)电势下极化4000秒后,9-ml 30-nmaunp薄膜和9-ml 30-nm npg上的极化电流密度分别从25.50μa/cm2降低到12.76μa/cm2,从48.11μa/cm2降低到27.49μa/cm2。在长时间运行过程中,9-ml 30-nm npg提供了更高的初始和最终电流密度,分别是未焊接的前驱体的1.89倍和2.15倍,这表明焊接处理后,制得的9-ml 30-nmnpg相比9-ml 30-nmau np薄膜的稳定性大大提高。综上,经直流电焊接处理后所制备的9-ml 30-nm npg具有较高的电催化活性和稳定性,显示出作为甲醇电氧化等高效电催化剂的巨大潜力。
138.对比例1
139.和实施例1相比,在逐层处理过程中,在进行一下层的复合时,未进行等离子体处理。
140.结果发现,无法或者极少附着在已转移au np薄膜的基底上,因而无法转移制得致密的aunp薄膜到基底上,无法实现多次重复转移制得多层致密的au np薄膜。
141.对比例2
142.如本团队已发表的论文(chemical physics letters 754(2020)137603),当把气体氛围改成o2,等离子体清洗仪的功率增加至300w,处理时间增加为10min,用等离子体处理就会导致金纳米颗粒之间的焊接,进而会导致制得的纳米多孔的结构发生变化,层与层之间的互嵌性严重减弱(原本是以单个金纳米颗粒的形式为单体,通过各个向的纳米颗粒
的相互焊接制备立体效果较好的多孔金,如果用强的功率处理会导致单体变成单层的网状薄膜,会导致制得的三维纳米多孔金的立体效果大大降低)。
143.对比例3;
144.和实施例2相比,区别仅在于,9-ml 30-nm au np薄膜电焊接过程的电流强度为0.1a以及3a。
145.由图21(a)中9-ml 30-nm au np薄膜经过0.1a的直流电处理5分钟后的sem表征图,可知当电流强度低于下限时,au np之间无明显焊接效果,未成功制得三维纳米多孔金。由图21(b)中9-ml 30-nm au np薄膜经过3.0a的直流电处理5秒钟后制得的sem表征图,可知当电流强度高于上限时,会导致焊接过度,各层金纳米颗粒之间坍塌严重,制得的三维纳米多孔金的韧带过粗,立体效果较差。
146.实施例4
147.按实施例1的方法,制得两层复合的au np薄膜,且au np的粒径为50nm。标记为(50-nm au np薄膜)。分别对该双层膜进行不同体系以及电流方式的处理,例如:(a):将膜置于空气气氛直流电下处理,且直流电的强度为0.2a;(b)将双层膜浸渍在水中并在0.2a的直流电强化下电焊接。(c)和(a)相比,采用交流电替换所述的直流电。
148.由图22(a)和(b)中2-ml 50-nm au np薄膜经过0.2a的直流电在空气和水中焊接处理5min后的sem表征图可知,在空气中处理的au np之间的焊接效果更好。与单层au np薄膜不同,多层(n≥2)au np薄膜中au np在纵向是直接接触的,总体电阻更小。在干燥的空气中,au np之间的焊接实际上是电子局域化引起的au np表面原子的扩散(如图23所示)促成的,而在水的氛围中,不但存在表面原子扩散,还存在au原子在水中的扩散(扩散速度远远不及于au np之间直接接触的接触点的表面原子扩散的速度),并且这种扩散会大大减弱原本的au np表面原子的扩散,进而导致了多层au np薄膜在空气中的焊接效果比在水中更好。
149.由图22(a)和(c)中2-ml 50-nm au np薄膜经过0.2a的直流电和交流电在空气中焊接处理5min后的sem表征图可知,经交流电处理后的多层au np薄膜层与层之间存在严重的坍塌,这是因为ac作用下载au np之间的接触点出会产生很强的焦耳热,容易导致局部过度焊接,引起层与层之间的坍塌。相比之下,通过直流电处理后的多层au np薄膜层与层之间未见明显的坍塌,具有较好的三维立体结构。
150.机理
151.由图23的机理示意图可知,在直流电纳米焊接过程中,金属表面的局域电子会引起表面原子之间的静电排斥,进而引起金属表面原子在金属表面的扩散。在没有钎料,也没有运输载体(比如:溶液)存在情况下,之所以能够将金属纳米颗粒之间的间隙填充,是因为在直流电纳米焊接过程中,高的局域电子(电流)密度会引起金属表面原子的扩散。在直流电纳米焊接过程中,随着表面原子的扩散,首先会在金属纳米颗粒表面形成小的凸起,随后金属表面原子会沿着凸起的方向继续扩散,直到两个相邻金属颗粒表面的小凸起对接到一起,在相邻金属纳米颗粒之间建立细小的连接。最后,随着直流电纳米焊接的进一步进行,相邻金属纳米颗粒之间细小连接会越来越粗,直至纳米焊接处理时间的结束。
152.尽管已用具体实施例来说明和描述了本发明,然而应意识到,在不背离本发明的精神和范围的情况下可以作出许多其它的更改和修改。因此,这意味着在所附权利要求中
包括属于本发明范围内的所有这些变化和修改。
再多了解一些
本文用于企业家、创业者技术爱好者查询,结果仅供参考。