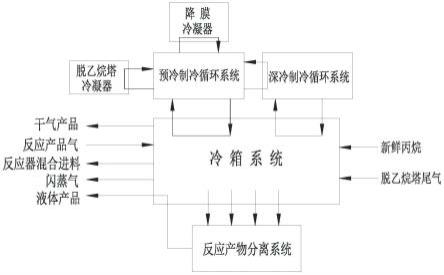
1.本发明涉及化工分离技术领域,尤其是涉及一种耦合式烷烃催化脱氢反应产物的分离方法和装置。
背景技术:
2.烷烃在催化剂的参与下,可以发生脱氢反应,生成附加值更高的烯烃和氢气。在各类烯烃中,丙烯是一种重要的石油化工基本原料。主要用于生产聚丙烯、环氧丙烷、丙烯酸、丙烯腈、烷基化油、生产高辛烷值汽油调和料等数十种石油化工产品和原料。近年来,由于丙烯下游各类化工产品的迅猛发展,国内丙烯的需求量持续快速增长。
3.长久以来,丙烯主要来自石脑油蒸汽裂解工艺和石油炼制的催化裂解工艺。近年来,在丙烯下游市场需求不断增长的背景下,一些新的、具有经济性的生产丙烯的技术吸引了人们的注意,并已成功工业化。其中包括甲醇制烯烃工艺(mto)、甲醇制丙烯工艺(mtp)、烯烃裂解工艺(ocp)及丙烷脱氢制丙烯工艺(pdh)。在以上各类生产丙烯的工艺中,采用丙烷定向生产丙烯的丙烷脱氢因其简单的工艺流程和优异的经济性,获得了巨大的成功。近几年国内新建和投产的丙烷脱氢装置多达二十余套,生产的丙烯规模超过1200万吨/年。因此,丙烷脱氢技术是目前最有竞争力的丙烯生产工艺,市场份额不断扩大。
4.丙烷脱氢反应产物中以氢气和碳三为主,还有少量的甲烷、碳二、氮气等。甲烷和部分碳二来自丙烷脱氢的副产物,部分碳二来自原料丙烷,氮气来自再生过程。反应器出口物料经过冷却、压缩、干燥后进入分离系统,丙烯和未反应的丙烷的混合物在冷箱中被逐步冷凝,并在下游精馏单元回收丙烯和再循环丙烷回反应器。因丙烷脱氢反应产物中含有大量的氢气,因此需要在深冷温度下,实现氢气和碳三的分离。富氢气复热后,经psa提纯得到纯氢产品,psa吸附下来的尾气作为燃料气外输。
5.现有工业化的丙烷脱氢反应产物分离过程均采用低温深冷工艺实现轻组分与碳三的分离,反应产物在板翅式换热器中经逐级冷却至-95~-125℃。根据不同工艺反应产物的组成差异情况,通常采用双膨胀制冷或外部单一组分制冷获得分离所需要的冷量,流程比较复杂、且碳三的回收率受限于反应产物的条件或外部制冷获得的最低制冷温度。整个分离装置的能耗和设备的投资都相当高。另外,经分离系统获得的碳三产品中必然含有一定量的氢气和碳二,需经脱乙烷塔分离出轻组分后送丙烯塔才能实现聚合级丙烯和丙烷的分离。目前工业上通过单独配置一套制冷机组给脱乙烷塔顶提供温位相匹配的冷量实现塔顶气相的部分冷凝。这样整个分离系统的机组复杂,且对装置的平稳操作提出了较高的要求。
技术实现要素:
6.本发明提供了一种耦合式烷烃催化脱氢反应产物的分离方法和装置,克服了现有技术中丙烷脱氢反应气分离效果不佳、能耗高、碳三回收率不高且机组复杂等缺陷。
7.本发明的目的可以通过以下技术方案来实现:
8.发明人在研究中发现,丙烷脱氢装置的原料丙烷均采用低温液态储存,根据烷烃催化脱氢反应的特点及进料要求,需将液态原料丙烷气化后进入反应器,这部分原料的气化需要吸收大量的热量,因此可将原料丙烷的气化与分离系统进行耦合,向分离系统提供冷量,实现能量的优化匹配;另外,脱乙烷塔的塔顶尾气含有大量的碳二和甲烷及少量的氢气,且压力较高(可达到2.25mpag~2.85mpag),经预冷并降压节流后能够产生-100℃~-160℃的冷量,因此也可将这部分冷量与分离系统进行耦合,实现能量的优化匹配,节约分离系统能耗。
9.同时,采用混合冷剂制冷的方法可有效降低深冷分离的温度,提高碳三产品的回收率。本发明将以上三股冷量巧妙及有效地耦合入分离系统中,通过改变、调整物料原来的走向及连接形式,并按温度等级与预冷制冷循环及混合冷剂深冷制冷循环耦合在一起,共同向分离系统提供分离所需的冷量,且反应生成气本身不需节流膨胀制冷,仅通过调整合理的冷剂配比和操作参数,最终实现-160℃到-40℃的温度级位。在减少设备投资的提前下,达到充分回收碳三产品的目的。
10.本发明中耦合式烷烃催化脱氢反应产物的分离方法,包括以下步骤:
11.将烷烃催化脱氢反应器出口的反应产品气输入冷箱系统,得到冷却后产品;
12.将所述冷却后产品输入n级串联的气液分离罐进行气液分离,之后:
13.将第1~n-1级得到的气相产品重新输入冷箱系统,最终冷却至-95℃~-160℃,优选-115℃~-145℃,更优选-120℃~-138℃;
14.将1~n级得到的液相产品收集后复热送出冷箱系统,之后通过分离塔实现液相产品不同碳数产物的分离;
15.将第n级气液分离罐罐顶得到的循环气与新鲜丙烷按预设的氢/烃比经m级混合并在冷箱系统中经节流蒸发,向冷箱系统提供冷量,复热后送出冷箱系统,其中m≤n;
16.第n级气液分离罐罐顶得到的干气在冷箱系统中复热后送出冷箱系统;
17.将脱乙烷塔塔顶尾气引入冷箱系统,并经过多级冷箱冷却至第n级分离的温度后降压节流至125kpag~400kpag,优选200kpag~375kpag后返回冷箱并复热至15℃~45℃后送出冷箱系统;
18.所述冷箱系统的冷量还来自外部制冷循环系统。
19.进一步地,所述冷箱系统的换热器串联级数与所述n级分离罐级数相等且逐级匹配,所述冷箱系统由其中一级或多级构成预冷段,其余构成深冷段。
20.进一步地,新鲜丙烷流量的60%~100%分配给预冷段,其余分配给深冷段,且应满足分配流量与新鲜丙烷温度等级按照负相关匹配。
21.进一步地,所述冷箱系统的一部分冷量来自所述新鲜丙烷与循环气多级混合并节流气化蒸发以及脱乙烷塔塔顶尾气降温节流后产生的冷量;发明人在大量研究后发现,为了达到最优的能量耦合效果,新鲜丙烷流量的60%~100%需分配给预冷段,且应满足随温度等级的升高,分配逐级减少的原则。脱乙烷塔塔顶尾气应经冷箱系统多级预冷至第n级分离的温度后节流返回冷箱并复热至15℃~45℃出界区。
22.进一步地,各级气液分离罐的液相产品利用自身的压力返回冷箱系统复热并汇总后进入液体产品罐,之后再次泵入冷箱系统复热后进入脱乙烷塔实现氢气、碳一、碳二、碳三的分离。
23.进一步地,所述外部制冷循环系统包括:向预冷段提供冷量的预冷制冷循环系统和向深冷段段提供冷量的深冷制冷循环系统。
24.进一步地,所述n大于2,优选3~5,更优选3~4。
25.进一步地,所述预冷制冷循环系统中的制冷剂为氨、乙烷、乙烯、丙烯、丙烷、丁烷、戊烷中一种或多种的组合;
26.所述深冷制冷循环系统中的制冷剂为氮气、甲烷、乙烷、乙烯、丙烷、丙烯、丁烷中多种的组合。
27.进一步地,所述循环气流量与预设氢/烃比呈正比匹配;
28.当预设的氢/烃比为零时,循环气流量设置为零,此时新鲜丙烷仅在预冷段对应的级数节流蒸发。
29.进一步地,所述脱乙烷塔塔顶尾气经冷箱系统冷却至第n级分离的温度后节流返回冷箱系统,复热后送出冷箱系统。
30.本发明中耦合式烷烃催化脱氢反应产物的分离装置,包括冷箱系统、预冷制冷循环系统、深冷制冷循环系统,其中具体地:
31.冷箱系统分别与烷烃催化脱氢反应器出口、分离塔塔顶尾气出口连接,并与新鲜丙烷储罐连接,所述冷箱系统包括预冷段和深冷段;
32.预冷制冷循环系统与所述预冷段换热式连接,向烷烃催化脱氢反应器出口的反应产品气的预冷冷却分离过程提供冷量;
33.深冷制冷循环系统与所述深冷段换热式连接,向烷烃催化脱氢反应器出口的反应产品气的深冷冷却分离过程提供冷量;
34.n级分离罐,与所述冷箱系统连接并逐级匹配,第n级分离罐罐顶气相分为干气和循环气两股物流,循环气与新鲜丙烷按预设的氢/烃比经m级混合并输入冷箱系统,其中m≤n,分离罐1~n级得到的液相产品的出口依次与液体产品罐、分离塔连接,实现不同碳数产物的分离。
35.进一步地,所述液体产品罐罐顶还设置降膜冷凝器;
36.所述分离塔为脱乙烷塔;
37.所述冷箱系统包括多级板翅式换热器。
38.进一步地,所述预冷制冷循环系统还分别与脱乙烷塔的冷凝器、降膜冷凝器、深冷制冷循环系统换热式连接。
39.本技术方案中为了阐述方便,均以丙烷脱氢反应产物进行举例,但实际多数烷烃脱氢反应产物均使用于本烷烃催化脱氢反应产物的分离方法和装置。
40.与现有技术相比,本发明具有以下技术优势:
41.1)节约分离的能耗:本发明的工艺流程是通过采用以下几点来达到节约分离能耗的目的:1.丙烷脱氢反应器产物在冷箱系统中逐步冷凝后需经历多次抽出,进入分离罐,分离出液相产品,气相返回冷箱进一步冷凝,再进入下一级分离罐。这样设计可以起到降低分离能耗的作用,减少外部制冷循环系统需要的能量;2.反应原料丙烷在多处与循环气(富氢气)混合后节流气化,产生冷量,将原料的冷量带入冷箱系统,减少外部制冷循环系统需要提供的冷量;3.将脱乙烷塔的尾气引入冷箱系统,经降温节流产生低温,向分离系统提供冷量,节约分离的能耗;4.采用混合冷剂制冷,保证整个传热过程中温差较小,可以实现反应
产物冷凝需求冷量与制冷生成冷量的精确匹配,实现“冷量匹配,温位相当”的目标,从而减少传热过程的不可逆性和损失,最终实现降低分离能耗的目标。
42.2)降低富氢气中碳三的损失:在丙烷脱氢反应产物分离过程中,反应产物的末级深冷温度与碳三的损失具有正相关性。本发明采用混合冷剂作为深冷制冷循环系统的制冷剂,可以通过冷剂配方组分的选取及组成的优化,达到预期的深冷温度,且与现有采用乙烯单一冷剂的制冷循环相比,可以突破乙烯制冷最低制冷温度的限制,产生-100℃以下温度的冷量,从而达到降低碳三产品损失率的目的。若与现有采用双膨胀的制冷流程相比,也可突破膨胀机的制冷温度,产生比膨胀机流程更低的温度,同样达到降低碳三产品损失率的目的。
43.3)设备、流程更紧凑,减少投资:与现有流程相比,通过将脱乙烷塔塔顶冷凝器的冷量整合到预冷制冷循环系统中,可以避免单独设置制冷机组,流程更加精简、紧凑,降低整个丙烷脱氢装置的设备投资,提高经济性。另外,若技术方案的预冷和深冷均采用混合冷剂制冷循环系统为分离系统提供冷量,则可以通过调整两个制冷循环系统各自的冷剂配方,使得两台压缩机功耗相当,则可以采用相同规格的动力装置,降低压缩机机组的成套难度和运行操作费用,提升装置整体经济性和可操作性。
44.4)冷箱系统操作更平稳:由于将原料丙烷按一定的温度等级匹配原则在冷箱系统中进行多级分配,这样保证了丙烷在冷箱系统中的完全气化,提供冷量;避免未气化的丙烷在流道内累积进而淹没流道,导致换热面积降低,气化率降低的恶性循环,最终导致分离系统停车的发生。
45.5)工艺更加环保:由于在传统的制冷循环系统中耦合了原料丙烷及脱乙烷塔塔顶尾气的冷量,使得外部制冷循环系统需要提供的冷量减少,制冷剂量减少;在装置停车时,火炬的泄放量减少,产生的温室气体量减少,泄放时间更短,因此工艺更加环保。同时,泄放量的减少还可降低火炬系统的设计载荷,减少设备投资和占地。
46.6)开车更加简洁、平稳、快速:由于采用预冷和深冷双循环制冷系统向分离装置提供冷量,开车优先启动预冷循环系统,向冷箱系统提供预冷冷量,待稳定后启动深冷循环系统,向冷箱系统提供深冷冷量。此类工艺安全简单,操作容易。开车过程更加平稳和方便,开车效率高,开车时间缩短,提升了装置整体的操作性。
附图说明
47.图1为本发明的工艺流程示意简图;
48.图2本发明具体实施例1的流程示意图;
49.图3本发明具体实施例2的流程示意图;
50.图4本发明具体实施例3的流程示意图;
51.图5本发明具体实施例4的流程示意图;
52.图6本发明具体实施例5的流程示意图;
53.图7对比例1的流程示意图。
54.各附图标记所代表的内容具体为:
55.板翅式换热器:ex-101、ex-102、ex-103、ex-104;气液分离罐v-101、v-102、v-103、v-104、v-201;碳三产品罐v-105;降膜冷凝器e-201;脱乙烷塔塔顶冷凝器e-301;碳三产品
泵p-101a/b。
具体实施方式
56.本实施例中所提供的一种耦合式丙烷脱氢反应产物的分离方法和装置,该方法可以通过采用以下技术方案来实现:
57.丙烷脱氢反应器出口的反应产品气经冷却、压缩、净化和过滤等预处理后进入分离系统,在分离系统的冷箱系统中冷却后抽出进入气液分离罐进行气液分离,气相继续进入冷箱系统冷却至下一级气液分离,直至达到预期的冷却温度及满足碳三产品回收率要求。末级分离罐罐顶气相(富氢气)被分为干气和循环气两股物流,循环气需要与新鲜丙烷按一定的氢/烃比经m级(m≤n)混合并在冷箱系统中经节流蒸发提供冷量,复热后再送出分离系统界区,进入反应器;干气则复热后送出界区。若预设的氢/烃比为零,则不需要循环气,且新鲜丙烷仅需要在预冷段节流蒸发。脱乙烷塔塔顶尾气经多级冷箱系统中的换热器冷却至第n级分离的温度后节流返回冷箱系统,复热后送出分离系统界区。各级气液分离罐的罐底液体利用自身的压力返回冷箱系统复热并汇总后进入液体产品罐,后续泵入冷箱系统复热后进入脱乙烷塔实现氢气/碳一/碳二与碳三的分离。脱乙烷塔的塔顶尾气进入冷箱系统,经多级冷却后节流降压并返回冷箱系统复热提供冷量后送出界区。液体产品罐产生的闪蒸气采用降膜换热器冷凝后,气相进入冷箱系统复热出界区,冷凝下来的液相(主要是碳三)由于自身重力回流至液体产品罐。
58.冷箱系统(板翅式换热器)是分离系统的关键设备之一,包括换热芯体及配套的管道及仪表等组件,主要满足多股流的换热需求,具有结构紧凑,换热效率高的优点。分离系统的冷量一部分来源于新鲜丙烷原料进料与富氢气混合物在冷箱系统中的节流蒸发,另一部分来自外部制冷循环系统提供,另外将脱乙烷塔塔顶尾气引入冷箱系统,经降温节流产生低温,向分离系统提供冷量。为了精简流程及降低投资和能耗,外部制冷循环系统由预冷及深冷两个相对独立的制冷循环系统构成,其基本组成如下:制冷循环压缩机、配套的各级吸入罐、管道及管件、控制仪表及换热器等。预冷制冷循环系统可采用单一组分作为制冷剂,也可采用含有氨、乙烷、乙烯、丙烷、丙烯、丁烷和戊烷中两种及以上组分组成的混合制冷剂。深冷制冷循环系统采用多组分的混合物作为混合制冷剂,混合冷剂的配方可以是:氮气、甲烷、乙烷、乙烯、丙烷、丙烯、丁烷中两种及以上组分构成的组合。预冷制冷循环系统主要承担原料入口温度至-15℃~-65℃的冷量补充,一部分冷量还用于深冷循环系统混合制冷剂的冷凝,并向脱乙烷塔塔顶冷凝器和液体产品罐罐顶的降膜冷凝器提供冷量;深冷制冷循环系统主要承担预冷末端制冷温度至-95℃~-160℃的冷量补充,也可以是原料入口温度至-95℃~-160℃的冷量补充。制冷循环系统的制冷剂在冷箱系统中复热吸收反应产物冷却放出的热量后气化回到各制冷循环系统中的压缩机一段吸入罐,后经过压缩冷却并节流形成低温制冷剂进入冷箱系统,提供冷量,完成制冷循环。
59.下面结合附图和具体实施例对本发明进行详细说明。
60.实施例1
61.如图2所示,丙烷脱氢反应器出口的反应产品气经冷却、压缩、净化和过滤等预处理后进入分离系统板翅式换热器ex-101,经冷却冷凝至-10℃后送入气液分离罐v101,分离出的液相进入碳三产品罐v-105,气相进入板翅式换热器ex-102进一步冷却冷凝至-38℃后
进入气液分离罐v-102,分离出的液相碳三与下一级分离出的液相碳三混合后在板翅式换热器ex-102中复热并利用自身压力汇总至碳三产品罐v-105,气相进入板翅式换热器ex-103进一步冷却冷凝后进入气液分离罐v-103,分离出的液相碳三与下一级分离出的并在板翅式换热器ex-104中复热后的液相碳三混合后依次在板翅式换热器ex-103、板翅式换热器ex-102中复热并利用自身压力汇总至碳三产品罐v-105,气相进入板翅式换热器ex-104被冷却至-115℃后进入气液分离罐v-104。在末级气液分离罐v-104的顶部获得干气和循环气,其中干气依次返回板翅式换热ex-104、ex103、ex-102、ex-101,复热至30℃后送出界区;循环气与新鲜丙烷进料在沿循环气输入冷箱系统方向的每一级板翅式换热器入口处进行混合后经板翅式换热ex-104、ex-103、ex-102、ex-101复热至30℃后送出界区。脱乙烷塔塔顶尾气经冷箱系统多级冷却至-115℃后节流至255kpag后返回冷箱系统,复热至25℃后送出冷箱系统。
62.本实施例中,反应产品气一共经历了四次气液分离,循环气与原料丙烷也经历了四次混合。丙烷在混合处按温度从高到低的顺序依次的流量分配比约为:7:2:0.7:0.3,其中新鲜丙烷流量的90%分配给预冷段。各级气液分离罐分离得到的液相产品汇至碳三产品罐v-105,碳三产品罐v-105罐顶的闪蒸气经降膜冷凝器e-201冷凝,未被冷凝下来的闪蒸气依次经板翅式换热ex-102、ex-101复热后送出界区,冷凝下来的液体由于自身重力回流至碳三产品罐v-105,最终经碳三产品泵p-101a/b加压至板翅式换热器ex-101复热至35℃后送入脱乙烷塔进行氢气/碳一/碳二与碳三的分离。
63.分离系统外部需要提供的冷量采用丙烯预冷和混合冷剂深冷两套制冷循环系统来获得。丙烯预冷制冷循环系统可以提供-41℃和-15℃两个温位的丙烯冷剂,其中-15℃的丙烯冷剂供脱乙烷塔冷凝器使用,-41℃的丙烯冷剂供板翅式换热器ex-102和碳三产品罐v-105罐顶的降膜冷凝器e-201使用。丙烯制冷压缩机采用离心式,出口压力1.77mpag,出口气相丙烯经循环冷却水冷却至43℃。
64.混合冷剂深冷制冷循环系统采用甲烷、乙烯和丙烷作为制冷剂,在混合冷剂压缩机加压至2.19mpag后经过冷却循环水冷却至43℃后依次进入板翅式换热器ex-101和ex-102预冷至-38℃后进入气液分离罐v-201。罐顶气相冷剂依次进入板翅式换热器ex-103、ex-104冷却至末级分离温度后节流至320kpag,后进入板翅式换热器ex-104复热,并与经过板翅式换热器ex-103冷却的罐底液相冷剂混合进入板翅式换热器ex-103复热至-40℃后进入混合冷剂制冷压缩机吸入罐,压缩至出口压力,完成制冷循环。
65.实施例2
66.如图3所示,丙烷脱氢反应器出口的反应产品气经冷却、压缩、净化和过滤等预处理后进入分离系统板翅式换热器ex-101,经冷却冷凝至-8℃后送入气液分离罐v101,分离出的液相进入碳三产品罐v-105,气相进入板翅式换热器ex-102进一步冷却冷凝至-37℃后进入气液分离罐v-102,分离出的液相碳三与下一级分离出的液相碳三混合后在ex-102中复热并利用自身压力汇总至碳三产品罐v-105,气相进入板翅式换热器ex-103进一步冷却冷凝后进入气液分离罐v-103,分离出的液相碳三与下一级分离出的并在板翅式换热器ex-104中复热后的液相碳三混合后依次在板翅式换热器ex-103、板翅式换热器ex-102中复热并利用自身压力汇总至碳三产品罐v-105,气相进入板翅式换热器ex-104被冷却至-122℃后进入气液分离罐v-104。在末级气液分离罐v-104的顶部获得干气并依次返回板翅式换热
ex-104、ex103、ex-102、ex-101,复热至15℃后送出界区;由于预设的氢/烃比为零,新鲜丙烷进料在经ex-101预冷至-8℃后抽出80%与经ex-102冷却至-37℃后返回ex-102复热后的丙烷混合,并在ex-101复热至33℃后送出界区,其中新鲜丙烷流量的100%分配给预冷段。脱乙烷塔塔顶尾气经冷箱系统多级冷却至-122℃后节流至285kpag后返回冷箱系统,复热至33℃后送出冷箱系统。
67.本实施例中,反应产品气一共经历了四次气液分离,由于预设的氢/烃比为零,第四级分离罐不产生循环气,原料丙烷仅在预冷段分两级蒸发气化。丙烷在两处按温度从高到低的顺序依次的流量分配比约为:8:2。各级气液分离罐分离得到的液相产品汇至碳三产品罐v-105,碳三产品罐v-105罐顶的闪蒸气经降膜冷凝器e-201冷凝,未被冷凝下来的闪蒸气依次经板翅式换热ex-102、ex-101复热后送出界区,冷凝下来的液体由于自身重力回流至碳三产品罐v-105,最终经碳三产品泵p-101a/b加压至板翅式换热器ex-101复热至33℃后送入脱乙烷塔进行氢气/碳一/碳二与碳三的分离。
68.分离系统外部需要提供的冷量采用丙烯预冷和混合冷剂深冷两套制冷循环系统来获得。丙烯预冷制冷循环系统可以提供-41℃和-15℃两个温位的丙烯冷剂,其中-15℃的丙烯冷剂供脱乙烷塔冷凝器使用,-41℃的丙烯冷剂供板翅式换热器ex-102和碳三产品罐v-105罐顶的降膜冷凝器e-201使用。丙烯制冷压缩机采用离心式,出口压力1.65mpag,出口气相丙烯经循环冷却水冷却至40℃。
69.混合冷剂深冷制冷循环系统采用氮气、乙烯和丙烯作为制冷剂,在混合冷剂压缩机加压至2.21mpag后经过冷却循环水冷却至40℃后依次进入板翅式换热器ex-101和ex-102预冷至-37℃后进入气液分离罐v-201。罐顶气相冷剂依次进入板翅式换热器ex-103、ex-104冷却至末级分离温度后节流至345kpag,后进入板翅式换热器ex-104复热,并与经过板翅式换热器ex-103冷却的罐底液相冷剂混合进入板翅式换热器ex-103复热至-41℃后进入混合冷剂制冷压缩机吸入罐,压缩至出口压力,完成制冷循环。
70.实施例3
71.如图4所示,丙烷脱氢反应器出口的反应产品气经冷却、压缩、净化和过滤等预处理后进入分离系统板翅式换热器ex-101,经冷却冷凝至-15℃后送入气液分离罐v101,分离出的液相进入碳三产品罐v-105,气相进入板翅式换热器ex-102进一步冷却冷凝至-30℃后进入气液分离罐v102,分离出的液相碳三与下一级分离出的并在板翅式换热器ex-103中复热后的碳三混合后在板翅式换热器ex-102中复热并利用自身压力汇总至碳三产品罐v-105,气相进入板翅式换热器ex-103,冷却至-130℃后进入气液分离罐v-103。在末级气液分离罐v-103的顶部获得干气和循环气,其中干气依次返回板翅式换热ex-103、ex-102、ex-101,复热至35℃后送出界区;循环气与新鲜丙烷进料在沿循环气输入冷箱系统方向的每一级板翅式换热器入口处进行混合后经板翅式换热ex-103、ex-102、ex-101复热至40℃后送出界区。脱乙烷塔塔顶尾气经冷箱系统多级冷却至-130℃后节流至300kpag后返回冷箱系统,复热至40℃后送出冷箱系统。
72.本实施例中,反应物一共经历了三次气液分离,循环气与原料丙烷也经历了三次混合。丙烷在混合处按温度从高到低的顺序依次的流量分配比约为:6.5:2:1.5,其中新鲜丙烷流量的85%分配给预冷段。各级气液分离罐分离得到的液相产品汇至碳三产品罐v-105,碳三产品罐v-105罐顶的闪蒸气经降膜冷凝器e-201冷凝,未被冷凝下来的闪蒸气依次
经板翅式换热ex-102、ex-101复热后送出界区,冷凝下来的液体由于自身重力回流至碳三产品罐v-105,最终经碳三产品泵p-101a/b加压至板翅式换热器ex-101复热至36℃后送入脱乙烷塔进行氢气/碳一/碳二与碳三的分离。
73.分离系统外部需要提供的冷量采用氨预冷和混合冷剂深冷两套制冷循环系统来获得。氨预冷制冷循环系统可以提供-33℃和-15℃两个温位的冷量,其中-15℃的冷量供脱乙烷塔冷凝器使用,-33℃的冷量供板翅式换热器ex-102和v-105罐顶的降膜冷凝器e-201使用。氨制冷压缩机采用离心式,出口压力1.54mpag,出口气相氨经循环冷却水冷却至40℃。
74.混合冷剂深冷制冷循环系统采用氮气、乙烷和丙烯作为制冷剂,在混合冷剂压缩机加压至2.08mpag后经过冷却循环水冷却至40℃后依次进入板翅式换热器ex-101、ex-102和ex-103预冷至末级分离温度后节流至285kpag后进入板翅式换热器ex-103复热至-38℃后进入混合冷剂制冷压缩机吸入罐,压缩至出口压力,完成制冷循环。
75.实施例4
76.本实施例流程同实施例1,如图5所示,区别在于:
77.丙烷在四处按温度从高到低的顺序依次的流量分配比为:6:2.5:1:0.5,其中新鲜丙烷流量的85%分配给预冷段。分离系统中气相进入板翅式换热器ex-104被冷却至-138℃后进入气液分离罐v-104。脱乙烷塔塔顶尾气经冷箱系统多级冷却至-138℃后节流至225kpag后返回冷箱系统,复热至20℃后送出冷箱系统。预冷制冷循环系统采用丙烷和丙烯的混合冷剂,同时提供-40℃和-15℃两个温度等级的冷量。深冷制冷循环系统的混合冷剂采用氮气、甲烷、乙烷、丙烷和丁烷作为制冷剂,在深冷混合冷剂压缩机加压至2.11mpag后经过冷却循环水冷却至42℃后依次进入板翅式换热器ex-101和ex-102预冷至-37℃后进入气液分离罐v-201。罐顶气相冷剂依次进入板翅式换热器ex-103、ex-104冷却至-138℃后节流至285kpag后进入板翅式换热器ex-104复热,并与经过板翅式换热器ex-103冷却的罐底液相冷剂混合后依次通过翅式换热器ex-103、ex-102和ex-101复热至25℃后进入混合冷剂制冷压缩机吸入罐,压缩至出口压力,完成制冷循环。
78.此具体实施例通过采用将混合冷剂复热至常温的方法可以有效降低混合冷剂压缩机入口管线及压缩机本体材质的要求,起到节省设备投资,提高混合冷剂压缩机操作稳定性的好处。与具体实施例1和2相比,还可降低预冷制冷循环压缩机的能耗。
79.实施例5
80.实施例5如图6所示,流程与实施例4大体一致,主要区别在于:
81.丙烷在四处按温度从高到低的顺序依次的流量分配比为:3.2:2.8:2.2:1.8,其中新鲜丙烷流量的60%分配给预冷段。分离系统中气相进入板翅式换热器ex-104被冷却至-148℃后进入气液分离罐v-104。脱乙烷塔塔顶尾气经冷箱系统多级冷却至-148℃后节流至310kpag后返回冷箱系统,复热至35℃后送出冷箱系统。预冷制冷循环系统采用乙烯、丙烯和戊烷的混合冷剂。预冷混合压缩机出口水冷器冷却至45℃后,依次进入板翅式换热器ex-101和ex-102冷凝冷却至-55℃后经过节流减压至175kpag后返回板翅式换热器ex-102和ex-101,复热至常温后进入预冷混合压缩机一段吸入罐后经两级压缩至2.15mpag后完成制冷循环。
82.深冷制冷循环系统采用甲烷、乙烯和丙烯作为制冷剂,在深冷混合冷剂压缩机加
压至2.38mpag后经过冷却循环水冷却至45℃后依次进入板翅式换热器ex-101和ex-102预冷至-55℃后进入气液分离罐v-201。罐顶气相冷剂依次进入板翅式换热器ex-103、ex-104冷却至-148℃节流至335kpag后进入板翅式换热器ex-104复热,并与经过板翅式换热器ex-103冷却的罐底液相冷剂混合后依次通过翅式换热器ex-103、ex-102和ex-101复热至27℃后进入混合冷剂制冷压缩机吸入罐,压缩至出口压力,完成制冷循环。
83.此具体实施例的预冷循环系统采用混合冷剂,通过缩小预冷传热过程中的温差,可降低传热过程的不可逆性和损失,减少预冷循环压缩机的能耗,达到降低整个分离装置能耗的增益效果。
84.同时,此具体实施例通过采用双循环混合冷剂制冷,并通过调整两套混合冷剂的配方,使得两台混合冷剂压缩机的功耗一致,因此可匹配相同规格的动力装置,达到降低压缩机机组的成套难度和运行操作难度的增益效果。
85.对比例1
86.采用如图7所示的丙烷脱氢反应产物的分离流程和装置,分离装置的构成与实施例1保持一致。
87.对比例1与实施例1的工艺流程参数也保持一致,主要区别在于:1.对比例1未采用新鲜原料丙烷与循环气在多处混合节流蒸发的设计;2.对比例1未采用脱乙烷塔塔顶尾气降温节流并复热向分离系统提供冷量的设计。
88.实施例1与对比例1中两台制冷压缩机的轴功率对比如下:
[0089] 单位对比例1实施例1预冷循环压缩机轴功率kw92352455深冷循环压缩机轴功率kw24711765制冷循环冷却器总负荷mw28.9510.43
[0090]
通过对比可以看出,对比例1由于未将原料丙烷和脱乙烷塔塔顶尾气的冷量耦合入分离系统,因此两台外部制冷压缩机的轴功率均大于实施例1中的数值,且制冷循环冷却器的总负荷也远远大于实施例1,说明实施例1在节约分离系统能耗方面有很大的优势。
[0091]
上述的对实施例的描述是为便于该技术领域的普通技术人员能理解和使用发明。熟悉本领域技术的人员显然可以容易地对这些实施例做出各种修改,并把在此说明的一般原理应用到其他实施例中而不必经过创造性的劳动。因此,本发明不限于上述实施例,本领域技术人员根据本发明的揭示,不脱离本发明范畴所做出的改进和修改都应该在本发明的保护范围之内。
再多了解一些
本文用于企业家、创业者技术爱好者查询,结果仅供参考。