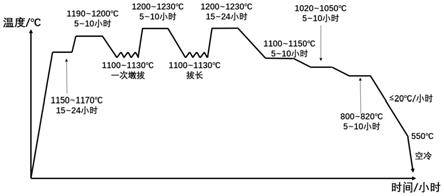
1.本发明属于金属材料热处理技术领域,具体涉及一种高温轴承钢碳化物细质弥散处理工艺。
背景技术:
2.航空发动机作为航空飞行器的动力装置,不仅代表了尖端工程技术的前沿,更引领了高品质特殊钢的发展进程。航空发动机主轴轴承需要在高温高转速的条件下承受剧烈的震动应力、弯曲扭矩以及恶劣的润滑条件,而轴承的开裂将会对航空发动机的完整性产生灾难性后果。随着航空发动机逐渐朝着大推重比、高可靠性、高耐久性、低耗油率、低成本的方向发展,作为航空发动机关键组件的主轴轴承工作条件也变得更加苛刻,需要轴承钢在高温环境运转时具有足够的硬度、强度与尺寸稳定性。
3.gcr4mo4v是我国目前航空发动机主轴轴承上用量最大的高温轴承钢,被广泛应用于316℃以下航空发动机主轴轴承的套圈与滚动体加工,然而由于该钢种合金元素含量高达9%,碳元素含量0.8%左右,在凝固结晶过程中由于元素偏析,极易出现块状、网状、大颗粒碳化物,以及合金元素与碳元素在枝晶组织中局部富集,造成铸锭化学成分的不均匀性,在后续加工过程中逐步遗传至钢材形成白蚀区甚至蝴蝶组织,进一步引发钢材服役寿命的缩短与性能的不稳定。
4.大量研究表明,夹杂物尺寸分布、碳化物尺寸及分布、晶粒尺寸及分布、残余奥氏体比例、残余应力等均为影响高温轴承钢服役寿命的关键因素,其中对gcr4mo4v而言,由于采取双真空冶炼工艺,氧元素含量已经可以实现5ppm的水平,很好地改善了夹杂物对疲劳寿命的影响,而晶粒尺寸、残余奥氏体比例、残余应力等更多地取决于后续热处理级深加工的工艺条件,唯有碳化物尺寸及分布是很难通过冶炼工艺优化、后续处理等方式加以改进的。
5.国内针对gcr4mo4v碳化物的研究很多,但是围绕碳化物细化及均匀化的研究却并不多见,且多围绕热加工对碳化物均质化、细质化的影响规律进行了研究,结果表明通过单一针对热加工方式及变形量进行优化的确可以在一定程度上改善碳化物颗粒尺寸粗大的问题,但是这种改变很有限,且对于碳化物均匀分布的改善几乎可以忽略。因此,通过工艺手段同时实现gcr4mo4v中碳化物的均质化与细质化,对于提升高温轴承服役寿命乃至提升航空发动机的整体水平都具有重要的意义。
技术实现要素:
6.本发明要解决的技术问题是一种高温轴承钢碳化物均质化与细质化程度不足的问题。
7.为解决上述技术问题,本发明采取的技术方案为:一种高温轴承钢碳化物细质弥散处理工艺,包括铸锭两段式预处理、铸锭墩拔加工、锻坯一次热处理、锻坯拔长加工、锻坯二次热处理工序,具体如下;
所述铸锭两段式预处理工序:将高温轴承钢铸锭放置于加热炉内加热至1150℃~1170℃,保温15小时~24小时;继续加热至1190℃~1200℃,保温5小时~10小时,出炉待温至1100℃~1130℃后开展墩拔加工;所述锻坯一次热处理工序:将墩拔后的高温轴承钢锻坯热装入1200℃~1230℃的加热炉内,保温5小时~10小时,出炉待温至1100℃~1130℃后开展拔长锻造;所述锻坯二次热处理工序:将拔长后的高温轴承钢锻坯热装入1200℃~1230℃的加热炉内,保温15小时~24小时;接着随炉冷却至1100℃~1150℃,保温5小时~10小时;接着随炉冷至1020℃~1050℃,保温5小时~10小时;接着随炉冷却至800℃~820℃,保温5小时~10小时;最后以≤20℃/小时的降温速率冷却至500℃~550℃,出炉空冷。
8.本发明所述铸锭墩拔加工工序采用常规工艺即可。
9.本发明所述锻坯拔长加工工序:将经过一次热处理的锻坯沿长度方向拔长锻造,锻造比不低于5。
10.本发明所述高温轴承钢为航空发动机主轴轴承用gcr4mo4v,其化学成分组成及其质量百分含量为:c:0.75%~0.85%,mn≤0.35%,si≤0.35%,cr:3.75%~4.25%,mo:4%~4.5%,v:0.9%~1.1%,w≤0.25%,p≤0.025%,s≤0.015%,ni≤0.25%,cu≤0.20%,co≤0.25%,余量为fe和不可避免的杂质。
11.采用本发明提供的工艺处理高温轴承钢,得到的高温轴承钢锻坯碳化物细小弥散且分布均匀,大颗粒碳化物粒径为1.48μm~1.69μm,平均碳化物粒径1.37μm~1.67μm,经过淬火、回火处理后,高温轴承钢抗拉强度≥2700mpa,屈服强度≥2300mpa、延伸率≥3%,硬度≥65hrc。
12.本发明的设计思路为:由于高温轴承钢合金含量高,在凝固选分结晶过程不可避免产生粗大莱氏体组织以及网状一次碳化物,前者由于碳含量高达4.3%,导致其熔点很低,在高温条件下极易发生初熔;后者以mc型一次碳化物为主,固溶温度较高,且多为带有棱角、颗粒尺寸高达几十个微米的大块状碳化物,单纯依靠热加工破碎或是依靠热处理回溶难度很大。传统的实现高温轴承钢碳化物细化的方式是采取多次墩拔加工,利用复杂塑性加工将大块的莱氏体与一次碳化物机械破碎,但是这种方式存在几方面弊端:(1)加工过程中很容易沿大颗粒碳化物的棱角处产生应力集中,形成裂纹源并在后续加工过程乃至成品服役过程中不断扩展,大幅度影响服役寿命;(2)多次墩拔在一定程度上可以将几十微米的大颗粒碳化物破碎化,但是当破碎至小于20微米后,很难再进一步实现细化;(3)多次墩拔后碳化物弥散均匀分布的程度很难得到改善。因此,对于碳化物的进一步细化并均匀弥散分布而言,多次墩拔具有局限性。如要进一步实现碳化物的细质弥散分布,需要充分结合热力学与动力学相关理论,基于高温轴承钢中多类别碳化物的析出、回溶以及相互转变的规律,在机械破碎的同时采取创新性手段实现碳化物的回溶、溶质再分配以及弥散析出等效果。
13.本发明在明确了高温轴承钢中莱氏体组织、mc型、m2c型、m6c型碳化物的热力学特性、析出动力学特性以及转变规律等基础理论的基础上,将具有针对性的热处理工艺融合到热加工过程,同时将多次墩拔简化为一次墩拔,实现碳化物的进一步细化并弥散均匀分布:通过对铸锭采取两段式预处理实现大颗粒mc型碳化物棱角的钝化与圆度的提升,并在一定程度实现莱氏体组织的固溶与碳元素扩散;通过一次墩拔将未溶大颗粒碳化物以及莱
氏体组织机械破碎,并提供充足的形变储能为碳化物溶解提供动力;通过锻坯一次热处理实现初步破碎的大颗粒碳化物、莱氏体组织回溶到基体;通过拔长加工进一步将中等尺寸碳化物颗粒进行机械破碎,并提供形变储能为细化后的碳化物颗粒回溶提供动力;通过锻坯由高温区间向中温区间阶梯保温的二次热处理依次实现mc型碳化物的充分回溶与莱氏体的充分消除、mc型碳化物弥散析出、m2c型碳化物向m6c型碳化物转变、m6c型碳化物向mc型碳化物转变,最终通过以≤20℃/小时的冷却速率缓慢冷却至500℃出炉空冷,实现mc型以及m6c型碳化物以球形细小弥散析出,碳化物颗粒平均粒径细化至1.37μm~1.67μm,大颗粒碳化物粒径分布在1.48μm~1.69μm范围内。锻坯经过1120℃淬火、530℃保温2小时回火三次的标准热处理工艺处理后,抗拉强度≥2700mpa,屈服强度≥2300mpa,延伸率≥3%,硬度≥62hrc。
附图说明
14.图1为本发明提供的碳化物细质弥散处理工艺曲线示意图;图2为实施例1制备的高温轴承钢锻坯碳化物金相照片;图3为对比例制备的高温轴承钢锻坯碳化物金相照片;图4为实施例1制备的高温轴承钢锻坯碳化物粒径分布柱状图;图5为对比例制备的高温轴承钢锻坯碳化物粒径分布柱状图;图6为实施例1制备的高温轴承钢锻坯碳化物球形度分布柱状图;图7为对比例制备的高温轴承钢锻坯碳化物球形度分布柱状图。
具体实施方式
15.下面结合具体实施例对本发明做进一步详细的说明。
16.各实施例及对比实施例使用的高温轴承钢原始坯料为相同工艺条件下双真空(真空感应 真空自耗)冶炼的φ300mm
×
700mm规格gcr4mo4v真空自耗铸锭,各实施例及对比实施例用钢的化学成分见表1,球化退火后碳化物平均粒径以及最大碳化物粒径、热处理后力学性能见表2。
17.其中,碳化物粒径的测定方法为:随机选取10个以上视场进行金相观察,从所有视场中筛选出碳化物尺寸、分布最为恶劣的5个视场进行定量测定,每个视场测定碳化物颗粒个数不少于100个,对5个视场测定的全部碳化物颗粒粒径取平均值即得到碳化物平均粒径,选取最大值即得到最大碳化物粒径。
18.每个碳化物粒径的测定方法为先选取任意方向碳化物颗粒最大长度a(长轴尺寸),然后测定垂直于a方向的碳化物颗粒最大尺寸b(短轴长度),碳化物粒径d以及球形度s按下式计算:按下式计算:锻坯热的力学性能在经过热处理后进行测定,热处理工艺为:(1)球化退火处理:加热至840℃保温4小时,以30℃/小时冷却至730℃保温4小时,以30℃/小时冷却至550℃空冷;
(2)淬火回火处理:1120℃保温30分钟后油淬,之后再进行3次530℃保温2小时空冷回火。
19.各实施例中碳化物细质弥散处理工艺路线如图1所示。
20.实施例1首先将经“真空感应 真空自耗”冶炼制备的φ300mm
×
700mm规格gcr4mo4v真空自耗铸锭放置于加热炉内加热至1150℃,保温15小时,继续加热至1190℃,保温5小时,出炉待温至1100℃后开展墩拔加工,墩拔后锻坯尺寸为250mm
×
250mm
×
790mm的方截面坯料;将墩拔后的锻坯热装入1200℃的加热炉内,保温5小时,出炉待温至1100℃后开展拔长锻造;拔长后锻坯尺寸为100mm
×
100mm
×
4900mm,拔长锻造比为6.25;将拔长后的锻坯热装入1200℃的加热炉内,保温15小时,接着随炉冷却至1100℃,保温5小时,接着随炉冷至1020℃,保温5小时,接着随炉冷却至800℃,保温5小时,最后以20℃/小时的降温速率冷却至500℃,出炉空冷。
21.锻坯经过球化退火后碳化物分布金相照片如图2所示,碳化物粒径分布柱状图如图4所示,碳化物球形度分布柱状图如图6所示,碳化物平均粒径、最大颗粒碳化物粒径、经过淬火回火后的力学性能等指标如表2所示。
22.实施例2首先将经“真空感应 真空自耗”冶炼制备的φ300mm
×
700mm规格gcr4mo4v真空自耗铸锭放置于加热炉内加热至1170℃,保温24小时,继续加热至1200℃,保温10小时,出炉待温至1130℃后开展墩拔加工,墩拔后锻坯尺寸为300mm
×
300mm
×
530mm的方截面坯料;将墩拔后的锻坯热装入1230℃的加热炉内,保温10小时,出炉待温至1130℃后开展拔长锻造;拔长后锻坯尺寸为100mm
×
100mm
×
4700mm,拔长锻造比为9;将拔长后的锻坯热装入1230℃的加热炉内,保温24小时,接着随炉冷却至1150℃,保温10小时,接着随炉冷至1050℃,保温10小时,接着随炉冷却至820℃,保温10小时,最后以20℃/小时的降温速率冷却至550℃,出炉空冷。
23.锻坯经过球化退火后碳化物分布金相照片、碳化物粒径分布柱状图、碳化物球形度分布柱状图与实施例1相似,不再重复展示;碳化物平均粒径、最大颗粒碳化物粒径、经过淬火回火后的力学性能等指标如表2所示。
24.实施例3首先将经“真空感应 真空自耗”冶炼制备的φ300mm
×
700mm规格gcr4mo4v真空自耗铸锭放置于加热炉内加热至1150℃,保温20小时,继续加热至1190℃,保温8小时,出炉待温至1100℃后开展墩拔加工,墩拔后锻坯尺寸为250mm
×
250mm
×
790mm的方截面坯料;将墩拔后的锻坯热装入1200℃的加热炉内,保温8小时,出炉待温至1100℃后开展拔长锻造;拔长后锻坯尺寸为100mm
×
100mm
×
4900mm,拔长锻造比为6.25;将拔长后的锻坯热装入1200℃的加热炉内,保温20小时,接着随炉冷却至1100℃,保温8小时,接着随炉冷至1020℃,保温8小时,接着随炉冷却至800℃,保温8小时,最后以20℃/小时的降温速率冷却至550℃,出炉空冷。
25.锻坯经过球化退火后碳化物分布金相照片、碳化物粒径分布柱状图、碳化物球形度分布柱状图与实施例1相似,不再重复展示;碳化物平均粒径、最大颗粒碳化物粒径、经过淬火回火后的力学性能等指标如表2所示。
26.实施例4首先将经“真空感应 真空自耗”冶炼制备的φ300mm
×
700mm规格gcr4mo4v真空自耗铸锭放置于加热炉内加热至1160℃,保温24小时,继续加热至1195℃,保温10小时,出炉待温至1120℃后开展墩拔加工,墩拔后锻坯尺寸为350mm
×
350mm
×
400mm的方截面坯料;将墩拔后的锻坯热装入1220℃的加热炉内,保温10小时,出炉待温至1120℃后开展拔长锻造;拔长后锻坯尺寸为100mm
×
100mm
×
4850mm,拔长锻造比为12.25;将拔长后的锻坯热装入1220℃的加热炉内,保温24小时,接着随炉冷却至1120℃,保温10小时,接着随炉冷至1040℃,保温10小时,接着随炉冷却至810℃,保温10小时,最后以10℃/小时的降温速率冷却至520℃,出炉空冷。
27.锻坯经过球化退火后碳化物分布金相照片、碳化物粒径分布柱状图、碳化物球形度分布柱状图与实施例1相似,不再重复展示;碳化物平均粒径、最大颗粒碳化物粒径、经过淬火回火后的力学性能等指标如表2所示。
28.实施例5首先将经“真空感应 真空自耗”冶炼制备的φ300mm
×
700mm规格gcr4mo4v真空自耗铸锭放置于加热炉内加热至1160℃,保温22小时,继续加热至1195℃,保温8小时,出炉待温至1120℃后开展墩拔加工,墩拔后锻坯尺寸为300mm
×
300mm
×
530mm的方截面坯料;将墩拔后的锻坯热装入1220℃的加热炉内,保温9小时,出炉待温至1120℃后开展拔长锻造;拔长后锻坯尺寸为100mm
×
100mm
×
4700mm,拔长锻造比为9;将拔长后的锻坯热装入1220℃的加热炉内,保温22小时,接着随炉冷却至1130℃,保温8小时,接着随炉冷至1040℃,保温8小时,接着随炉冷却至810℃,保温9小时,最后以10℃/小时的降温速率冷却至530℃,出炉空冷。
29.锻坯经过球化退火后碳化物分布金相照片、碳化物粒径分布柱状图、碳化物球形度分布柱状图与实施例1相似,不再重复展示;碳化物平均粒径、最大颗粒碳化物粒径、经过淬火回火后的力学性能等指标如表2所示。
30.对比例本对比例采用传统生产工艺,首先将经“真空感应 真空自耗”冶炼制备的φ300mm
×
700mm规格gcr4mo4v真空自耗铸锭放置于加热炉内加热至1150℃,保温4小时,出炉待温至1100℃后开展2次墩拔加工,2次墩拔后锻坯尺寸为250mm
×
250mm
×
790mm的方截面坯料;将墩拔后的锻坯热装入1150℃的加热炉内,保温4小时,出炉待温至1100℃后开展拔长锻造;拔长后锻坯尺寸为100mm
×
100mm
×
4900mm,拔长锻造比为6.25。
31.锻坯经过球化退火后碳化物分布金相照片如图3所示,碳化物平均粒径分布柱状图如图5所示,碳化物球形度分布柱状图如图7所示,碳化物平均粒径、最大颗粒碳化物粒径、经过淬火回火处理后的力学性能等指标如表2所示。
32.表1 实施例及对比例高温轴承钢化学成分及质量分数(wt%)
表2 实施例及对比实施例碳化物粒径及热处理后力学性能通过实施例1~实施例5以及对比例可见,采用本发明公开的碳化物细质弥散处理工艺可以将gcr4mo4v高温轴承钢中的碳化物平均粒径由传统工艺条件下的8.74μm左右细化至1.37μm~1.66μm,最大碳化物颗粒尺寸由传统工艺条件下的25.26μm细化至1.48μm~1.69μm,碳化物粒径分布集中,且形貌几乎全部为等轴形,对提升材料综合性能起到极大促进作用。采用本发明公开的碳化物细质弥散处理工艺处理的gcr4mo4v高温轴承钢经过标准的球化退火、淬火、回火处理后,屈服强度达到2314mpa~2522mpa,抗拉强度2790mpa~2872mpa,表面硬度65.3hrc~65.8hrc,延伸率3.14%~3.82%,与传统工艺条件制备同等规格gcr4mo4v高温轴承钢相比,分别提升了9.4%~19.2%、9%~12.3%、4.6%~5.4%、96.25%~138.7%。
33.以上实施例仅用以说明而非限制本发明的技术方案,尽管参照上述实施例对本发明进行了详细说明,本领域的普通技术人员应当理解:依然可以对本发明进行修改或者等同替换,而不脱离本发明的精神和范围的任何修改或局部替换,其均应涵盖在本发明的权利要求范围当中。
再多了解一些
本文用于企业家、创业者技术爱好者查询,结果仅供参考。