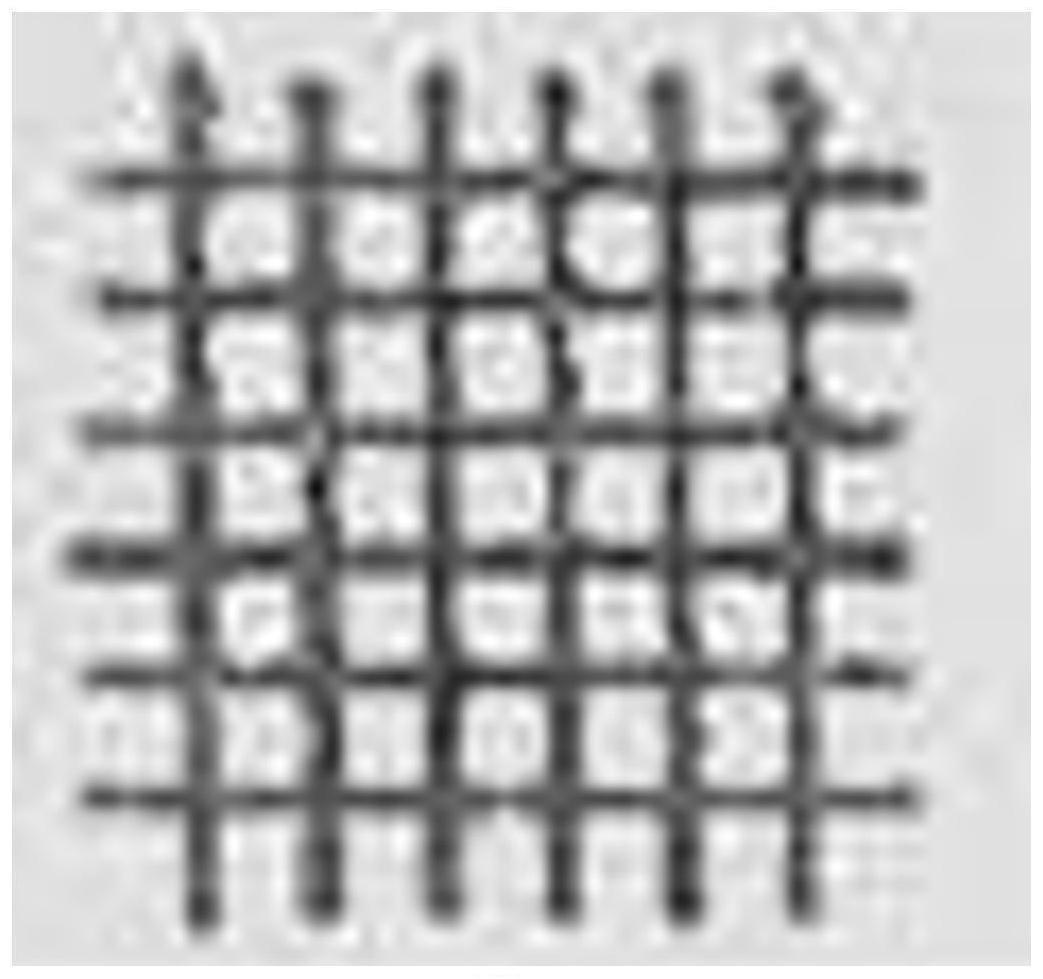
1.本发明涉及功能薄膜材料制备技术领域,特别是涉及一种热电材料焊接用复合薄膜的制备方法。
背景技术:
2.随着通讯设备的迅猛发展,通讯设备的集成程度和组装密度不断提高,在提供强大使用功能的同时,也导致了设备功耗和发热量的急剧增加。众所周知,ld光功率对温度非常敏感,温度升高将引起光功率输出减少(同时波长正向漂移),空间的紧缩、可插拔性要求和低温度规格为光模块的散热带来了挑战,为确保激光器有效工作必须采用tec进行精确温度控制。目前5g通信的推出对光模块散热提出了更高的要求,使用半导体主动制冷模块就显得越发重要且迫切。
3.微型tec用热电材料碲化铋晶片双面镀金属膜用于电极互联,采用酒精丙酮清洗衬底,室温下直流磁控溅射沉积cr-ni复合薄膜,经百格测试发现薄膜脱落面积》80%,结合力测试结果不理想,无法达到使用要求。
4.因此,在目前的磁控溅射工艺下,如何制备出既能用于热电材料碲化铋焊接用的cr-ni复合薄膜,又能保证薄膜的附着力,以达到使用要求,成为亟待攻克的技术难题。
技术实现要素:
5.本发明要解决的技术问题是克服现有技术中的技术缺陷,提供一种热电材料焊接用复合薄膜的制备方法。
6.为了解决上述技术问题,第一方面,本发明提供了一种热电材料焊接用复合薄膜的制备方法,包括以下步骤:
7.(1)安装靶材;所述靶材为cr靶材和/或ni靶材;
8.(2)打磨衬底至所述衬底的粗糙度为0.2μm≤ra≤0.4μm;所述衬底为碲化铋晶片;
9.(3)清洗衬底;
10.(4)直流磁控溅射生长金属薄膜,即成。
11.本发明在直流磁控溅射沉积金属薄膜前,通过对衬底作打磨处理,改变其粗糙度;清洗去除表面油污;有效地改善薄膜的附着力,保持溅射获得的薄膜表面光滑、金属光泽度高、组分均一。
12.作为本发明所述热电材料焊接用复合薄膜的制备方法的优选实施方式,在所述步骤(1)中,所述cr靶材的纯度≥99.9%,密度≥7.19g/cm3;所述ni靶材的纯度≥99.99%,密度≥8.90g/cm3。
13.作为本发明所述热电材料焊接用复合薄膜的制备方法的优选实施方式,在所述步骤(2)中,所述衬底为p型碲化铋晶片。
14.进一步的,所述碲化铋晶片的纯度≥99.99%,密度≥6.82g/cm3,厚度为1.3mm-1.6mm。
1.6mm,并用1500目砂纸进行打磨,测量其粗糙度;
56.(3)将衬底依次在丙酮、无水乙醇和去离子水超声清洗10min,之后用高纯氮气吹干;
57.(4)采用直流磁控溅射生长金属cr薄膜,靶材与衬底中心距离为7cm,氩气纯度为99.999%,靶材溅射功率密度为2.26w/cm2,溅射压力为0.6pa,生长温度为200℃,薄膜厚度为30nm;
58.(5)采用直流磁控溅射生长金属ni薄膜,靶材与衬底中心距离为7cm,氩气纯度为99.999%,靶材溅射功率密度为4.53w/cm2,溅射压力为0.6pa,生长温度为200℃,薄膜厚度为2000nm。
59.对比例2:一种热电材料焊接用复合薄膜的制备方法
60.该方法的具体实施步骤如下:
61.(1)在阴极靶位1上安装金属cr靶材,靶材纯度≥99.9%,密度≥7.19g/cm3;在阴极靶位2上安装ni靶材,靶材纯度≥99.99%,密度≥8.90g/cm3;
62.(2)衬底选用p型碲化铋晶片,纯度≥99.99%,密度≥6.82g/cm3,厚度1.3mm-1.6mm,并用1500目砂纸进行打磨,测量其粗糙度;
63.(3)使用jc-201清洁剂超声清洗60min,100℃烘烤0.5h;
64.(4)采用直流磁控溅射生长金属cr薄膜,靶材与衬底中心距离为7cm,氩气纯度为99.999%,靶材溅射功率密度为2.26w/cm2,溅射压力为0.6pa,生长温度为200℃,薄膜厚度为30nm;
65.(5)采用直流磁控溅射生长金属ni薄膜,靶材与衬底中心距离为7cm,氩气纯度为99.999%,靶材溅射功率密度为4.53w/cm2,溅射压力为0.6pa,生长温度为25℃,薄膜厚度为2000nm。
66.对比例3:一种热电材料焊接用复合薄膜的制备方法
67.该方法的具体实施步骤如下:
68.(1)在阴极靶位1上安装金属cr靶材,靶材纯度≥99.9%,密度≥7.19g/cm3;在阴极靶位2上安装ni靶材,靶材纯度≥99.99%,密度≥8.90g/cm3;
69.(2)衬底选用p型碲化铋晶片,纯度≥99.99%,密度≥6.82g/cm3,厚度1.3mm-1.6mm,未进行打磨处理,测量其粗糙度;
70.(3)使用jc-201清洁剂超声清洗60min,100℃烘烤0.5h;
71.(4)采用直流磁控溅射生长金属cr薄膜,靶材与衬底中心距离为7cm,氩气纯度为99.999%,靶材溅射功率密度为2.26w/cm2,溅射压力为0.6pa,生长温度为200℃,薄膜厚度为30nm;
72.(5)采用直流磁控溅射生长金属ni薄膜,靶材与衬底中心距离为7cm,氩气纯度为99.999%,靶材溅射功率密度为4.53w/cm2,溅射压力为0.6pa,生长温度为200℃,薄膜厚度为2000nm。
73.试验例:
74.实施例1-3和对比例1-3制备时,衬底的粗糙度采用zygo干涉仪测试,结果见表1。
75.表1粗糙度
[0076][0077][0078]
分别取实施例1-3和对比例1-3制备的复合薄膜,参照百格测试(百格测试的现象及等级标准见表2),检测各薄膜附着力,结果见表3。
[0079]
表2百格测试现象及等级标准
[0080][0081]
表3薄膜附着力
[0082][0083][0084]
从实施例1~3百格测试结果可看出,本发明制备方法中,在直流磁控溅射沉积金属cr-ni薄膜前,对碲化铋衬底进行1500砂纸打磨,jc-201清洁剂清洗、100℃烘烤,溅射过程中加热处理,得到的复合薄膜经百格测试后脱落无脱落,附着力较佳。且表面光滑、组分均一,适用于热电材料焊接用的cr-ni复合薄膜。
[0085]
从对比例1~3百格测试的结果可看出,本发明制备方法中,若溅射前未对衬底使用清洁剂清洗,得到的薄膜经百格测试后脱落面积≥15%,若溅射前未对衬底使用1500砂纸打磨处理,或溅射过程中未加热,得到的薄膜经百格测试后脱落面积≥65%。薄膜的脱落面积大,附着力差,不适用于热电材料焊接用的cr-ni复合薄膜。
[0086]
综上,本发明的制备方法中,在直流磁控溅射沉积金属cr-ni薄膜的过程中,可以通过对碲化铋衬底作打磨处理,改变其粗糙度;使用清洁剂清洗,去除表面油污;溅射时加热升温,增加膜层致密性。通过这种方法有效地改善薄膜的附着力,保持溅射获得的薄膜表面光滑、金属光泽度高、组分均一,以用于热电材料焊接。
[0087]
最后所应当说明的是,以上实施例仅用以说明本发明的技术方案而非对本发明保护范围的限制,尽管参照较佳实施例对本发明作了详细说明,本领域的普通技术人员应当理解,可以对本发明的技术方案进行修改或者等同替换,而不脱离本发明技术方案的实质和范围。
再多了解一些
本文用于企业家、创业者技术爱好者查询,结果仅供参考。