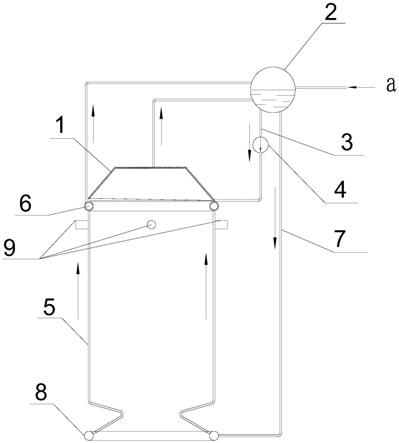
1.本发明涉及气化炉设备领域,具体涉及一种分开采用自然循环和强制循环的水冷壁气化炉及冷却方法。
背景技术:
[0002]“富煤、贫油、少气”是我国能源结构的基本特征,这一特征决定了我国的煤炭能源将在相当长一段时间占据能源生产和消费的主导地位,如何清洁、高效的利用煤炭资源已成为了实现碳中和目标的一个重要方向。煤炭气化技术就是一种高效清洁的洁净煤技术。当前的煤气化技术主要分为移动床气化、流化床气化、气流床气化和熔融床气化四类。其中,气流床气化技术因其气化强度高、单炉生产能力大、煤种适应范围广、碳转化率高等优点已成为煤炭气化技术的主要发展方向。现有技术中气流床气化炉炉壁主要分为两种形式,一种为耐火砖,另一种为水冷壁。由水冷壁取代耐火砖作为水冷壁气化炉气化室衬里,解决了耐火砖气化炉频繁更换耐火砖的问题,降低了维护成本和维护难度,同时水冷壁中工质回收气化炉内气化反应产生的热量,水冷壁出口的中压蒸汽可用于供热,也可作为气化反应中的气化剂或者后续化工产品生产用汽,因此得到了市场的广泛应用。
[0003]
但是现有技术中使用自然循环冷却水冷壁的水冷壁气化炉在使用过程中存在诸多问题。气化炉运行过程中,由于炉内高温合成气携带未燃尽煤粉冲刷撞击顶部水冷壁后,贴近顶部水冷壁壁面折转向下,在气化炉上部形成高温回流区,使气化炉顶部水冷壁承担巨大热负荷,容易过热烧损。而中下部圆柱段水冷壁没有高温合成气携带固体颗粒冲刷撞击后折转的过程,热负荷相对较低,不容易烧损。一旦顶部水冷壁过热烧损,会导致气化炉停车,影响生产,造成巨大经济损失。同时,由于现有技术的自然循环水冷壁气化炉的水冷壁采用一体式构成,施工难度大,维护质量难以保证,一旦烧损泄漏就会产生巨大安全问题和巨额停产损失。
[0004]
综上所述,现有技术中自然循环水冷壁气化炉的顶部圆台段水冷壁易烧损,且烧损后维护难度高,维护质量不能保证的问题。
技术实现要素:
[0005]
本发明的目的是为了解决现有技术中自然循环水冷壁气化炉的顶部圆台段水冷壁易烧损,且烧损后维护难度高,维护质量不能保证的问题,进而提供一种分开采用自然循环和强制循环的水冷壁气化炉及冷却方法。
[0006]
本发明的技术方案是:
[0007]
一种分开采用自然循环和强制循环的水冷壁气化炉,所述水冷壁气化炉装置包括气化炉本体,所述气化炉本体包括圆台段水冷壁1、圆柱段水冷壁5、上联箱6和下联箱8,圆台段水冷壁1、上联箱6、圆柱段水冷壁5和下联箱8沿竖直方向由上至下依次同轴设置;
[0008]
圆台段水冷壁1位于气化炉顶部,圆台段水冷壁1整体为下端开口的空心圆台形结构,圆台段水冷壁1为独立的盘管式水冷壁,圆柱段水冷壁5位于气化炉中下部,圆柱段水冷
壁5整体为两端开口的空心圆柱形结构,圆柱段水冷壁5为独立的竖直列管式水冷壁,上联箱6和下联箱8均为圆环形管状结构,圆柱段水冷壁5的竖直列管顶端与上联箱6进口连接,圆柱段水冷壁5的竖直列管底端与下联箱8出口连接;
[0009]
所述水冷壁气化炉装置还包括汽包2、强制循环下降管3、循环水泵4、自然循环下降管7和多个煤粉烧嘴9;圆台段水冷壁1的顶端设为圆台段水冷壁回水口b,所述圆台段水冷壁回水口b通过强制循环下降管3与汽包2下部连通,汽包2上部设有汽包给水管a,圆台段水冷壁1的底端设有圆台段水冷壁进水口c,所述圆台段水冷壁进水口c通过强制循环下降管3与循环水泵4出水口连接,循环水泵4进水口通过强制循环下降管3与汽包2下部连通;上联箱6出口通过自然循环下降管7与汽包2连通,下联箱8进口与汽包2下部连通;多个煤粉烧嘴9沿圆周方向均匀布置安装在圆柱段水冷壁5中上部。
[0010]
进一步地,圆台段水冷壁1高为h1,圆柱段水冷壁5高度h2,满足h2》h1,且h2=(5~20)h1。
[0011]
进一步地,圆台段水冷壁1的母线长l,满足l=(1.15~3)h1。
[0012]
进一步地,汽包2的数量为一个或者两个,当汽包2的数量为一个时,圆柱段水冷壁5和圆台段水冷壁1连接同一个汽包2;当汽包2的数量为两个时,圆柱段水冷壁5和圆台段水冷壁1分别连接对应的独立的汽包2。
[0013]
进一步地,圆台段水冷壁1由单管、双管或者多管绕成。
[0014]
进一步地,煤粉烧嘴9的数量为四个,所述四个煤粉烧嘴9沿圆周方向均匀布置安装在圆柱段水冷壁5中上部,且四个煤粉烧嘴9的轴线位于同一水平面上。
[0015]
一种基于具体实施方式一至六任意一项实施方式所述分开采用自然循环和强制循环的水冷壁气化炉的冷却方法,所述分开采用自然循环和强制循环的水冷壁气化炉方法是通过一下步骤实现的,
[0016]
步骤一、圆台段水冷壁1的强制循环过程:
[0017]
汽包2内的冷却水在循环水泵4的作用下由强制循环下降管3通入圆台段水冷壁1的圆台段水冷壁进水口c,经由圆台段水冷壁1吸热后从圆台段水冷壁回水口b由强制循环下降管3进入汽包2;
[0018]
步骤二、圆柱段水冷壁5的自然循环过程:
[0019]
汽包2内的冷却水由自然循环下降管7通入下联箱8,进入下联箱8内的冷却水再由下联箱8出口通入,经由圆柱段水冷壁5吸热后进入上联箱6,进入上联箱6内的冷却水由上联箱6出口通入,经由自然循环下降管7进入汽包2;
[0020]
步骤三、高温合成气的生成过程:
[0021]
煤粉与气化剂从位于气化炉上部的四个煤粉烧嘴9喷出后,在气化炉炉膛内剧烈混合,发生强烈的燃烧及气化反应,生成高温合成气,四股高温合成气流在气化炉炉膛中心区域对撞后,其中一部分气流偏转并冲向气化炉顶部,高温合成气流中携有未燃尽的煤粉,冲击气化炉顶部后贴近顶部圆台段水冷壁1壁面折转向下,另外一部分高温合成气偏转向下进入炉膛中下部。
[0022]
进一步地,步骤一和步骤二中所述的圆台段水冷壁1和圆柱段水冷壁5通入的冷却水温为120~140℃,圆柱段水冷壁5内工质流速为0.1~0.3m/s,圆台段水冷壁内工质流速为0.5~2m/s。
[0023]
进一步地,步骤一中采用强制循环的圆台段水冷壁1的进回水工质温升控制在8~12℃,当圆台段水冷壁1进回水工质温升低于8℃时,降低循环水泵4出力,降低强制循环工质流速;当圆台段水冷壁1进回水工质温升高于12℃,提高循环水泵4出力,提高强制循环工质流速。
[0024]
进一步地,步骤三中所述高温合成气中的成分包括co、h2和co2,步骤三中所述高温合成气中40%的气流偏转并冲向气化炉顶部,所述高温合成气中60%的高温合成气偏转向下进入炉膛中下部。
[0025]
本发明与现有技术相比具有以下效果:
[0026]
1、本发明将气化炉顶部圆台段单独采用工质流速更高、对流换热系数更大、换热效果更强的强制循环水冷壁,解决了现有技术中自然循环水冷壁气化炉的顶部圆台段水冷壁易烧损的问题。
[0027]
高温合成气掠过水冷壁面换热和水冷壁内工质流动与水冷壁管换热都是对流换热过程,对流换热基本计算公式为:
[0028]
q=h*(t
w-tf)
[0029]
式中q为单位面积的固体表面与流体之间在单位时间内交换的热量,称作热流密度;tw、tf分别为固体表面和流体的温度;h称为对流换热系数,它表示在单位面积的固体表面上,当流体与固体表面之间的温度差为1k时,每单位时间内所传递的热量。h的大小反映对流换热的强弱,对流换热系数h的数值与换热过程中流体的物理性质、换热表面的形状、部位以及流体的流速等都有密切关系。物体表面附近的流体的流速愈大,其对流换热系数也愈大,水的自然对流对流换热系数为200~1000w/(m2·
k),水的强制对流对流换热系数为1000~15000w/(m2·
k),气体的强制对流对流换热系数为20~300w/(m2·
k)。
[0030]
气化炉使用纯氧与少量水蒸气作为气化剂,煤粉与气化剂从位于气化炉上部的烧嘴喷出后,在气化炉炉膛内剧烈混合,发生强烈的燃烧及气化反应,温度迅速升高,生成包括co、h2、co2等成分的高温合成气。在烧嘴附近形成2000k以上的高温区域,最高处可达2800k以上,气化炉上部布置有四个烧嘴,四股高温合成气流在炉膛中心区域对撞后,其中约40%的气流偏转并冲向气化炉顶部,高温合成气流冲击气化炉顶部后折转向下,在气化炉顶部区域形成温度高达1800k~2100k的高温回流区,这部分高温合成气中携有未燃尽的煤粉,高温合成气携带未燃尽煤粉的固体颗粒冲撞气化炉顶部圆台段水冷壁,使圆台段水冷壁与高温合成气流的对流换热系数相比未携带固体颗粒气流的圆柱段水冷壁对流换热系数提高2~6倍,通过对流传热提供给单位面积顶部水冷壁的热量相比中下部圆柱段水冷壁也随之大2~6倍。圆台段水冷壁接收着来自高温合成气携带未燃尽煤粉的大量的对流传热,圆台段水冷壁承受着巨大的热负荷,若不能实现充分冷却,容易烧损。
[0031]
现有技术采用的自然循环水冷壁内工质流速为0.1~0.3m/s,工质与水冷壁对流换热系数为200~1000w/(m2·
k),而强制循环水冷壁的工质流速为自然循环水冷壁的2~15倍,强制循环水冷壁的对流换热系数为自然循环水冷壁的5~30倍。若圆台段水冷壁内工质采用自然循环冷却,将导致以下问题:(1)自然循环管内工质流速低,对流换热系数小,会使得水冷壁内工质吸热量不足,导致水冷壁管壁冷却不足发生过热烧损。(2)由于管内工质流速低,造成管内工质的平均温升高,管内工质的平均温升可超过20℃。水冷壁管内工质平均温度升高,造成工质与水冷壁壁面温差小,致使水冷壁内工质吸热量进一步降低,无法对
圆台段水冷壁实现充分的冷却,导致水冷壁过热烧损。(3)自然循环水冷壁管内工质在水冷壁内不断吸热向上流动,温度逐渐升高,在水冷壁管的最高处温度达到最高,导致工质在水冷壁出口前的最大温升可超过30℃,与管壁温差进一步降低,换热量更少,管壁无法实现有效冷却,即顶部水冷壁最容易发生过热损坏。(4)由于工质温升最高可超过30℃,很容易发生在水冷壁管子内部形成一层连续的蒸汽膜把水冷壁内表面与工质隔开,致使水冷壁壁面得不到液体冷却发生传热恶化,水冷壁冷却不足发生过热烧损。
[0032]
本发明将顶部圆台段水冷壁设计为单独的蛇形盘管形式,采用强制循环方式冷却。强制循环水冷壁内工质流速为0.5~2m/s,水的强制对流对流换热系数为1000~15000w/(m2·
k),强制循环水冷壁的工质流速为自然循环水冷壁的2~15倍,强制循环水冷壁的对流换热系数为自然循环水冷壁的5~30倍,因此若在圆台段水冷壁采用强制循环冷却,有以下优势:(1)强制循环管内工质流速高,对流换热系数大,吸热量更大,对水冷壁面的冷却能力更强,可以实现对圆台段水冷壁的有效冷却。(2)采用强制循环可通过调整循环水泵出力控制工质流速,将水冷壁内工质平均温升控制在5~6℃,工质与水冷壁管壁温差小,吸热量进一步加大,冷却效果更好。(3)水冷壁管内工质在水冷壁内不断吸热向上流动,温度逐渐升高,在水冷壁管的最高处温度达到最高,但是强制循环水冷壁内工质流速高,可控制管内工质最大温升不超过12℃,管内工质与管壁温差大,在顶部水冷壁工质温度最高处也可以有充足的吸热量,实现对水冷壁的充分冷却降温。(4)当圆台段水冷壁1进回水工质温升低于8℃时,应降低循环水泵4出力,降低强制循环工质流速,追求更高的经济效益。当圆台段水冷壁1进回水工质温升高于12℃,应提高循环水泵4出力,提高强制循环工质流速,降低进回水工质温升,可以有效防止工质吸热饱和汽化使换热恶化。
[0033]
2、本发明通过将气化炉顶部水冷壁和中下部圆柱段水冷壁分开安装设置,解决现有技术中水冷壁气化炉的顶部圆台段水冷壁烧损后维护难度大,维修质量不能保证的问题。
[0034]
现有技术的水冷壁气化炉,不论自然循环水冷壁还是强制循环水冷壁,水冷壁均为一体式结构,若顶部圆台段水冷壁烧损,需要在停炉后在炉内对受损水冷壁管进行切割和焊接操作,圆台段水冷壁因为位置位于炉顶,且有一个倾斜的角度,在炉内进行切割和焊接操作的施工难度很高,质量不容易保证,焊接处容易出现气密问题,存在安全隐患,若在气化炉运行过程中出现爆管泄漏,将导致巨大的安全问题和经济损失。
[0035]
本发明的气化炉水冷壁分开采用自然循环和强制循环,气化炉顶部圆台段水冷壁采用强制循环冷却,中下部圆柱段水冷壁采用自然循环冷却,两套水冷壁分开安装。若气化炉顶部圆台段水冷壁烧损,可以直接吊装更换圆台段水冷壁,将损毁水冷壁发回厂家更换,确保了圆台段水冷壁的质量,大大降低了维护难度。而且强制循环水冷壁的管径小,管壁薄,降低了顶部盘管部分的钢材使用量,同时降低了顶部圆台段水冷壁管的重量,方便维护时吊装更换。
附图说明
[0036]
图1是本发明的分开采用自然循环和强制循环的水冷壁气化炉的结构示意图;
[0037]
图2是本发明的圆台段水冷壁1的主视图;
[0038]
图3是本发明的圆台段水冷壁1的俯视图;
[0039]
图4是本发明的气化炉内反应气流流动示意图。
[0040]
图中:1-圆台段水冷壁;2-汽包;3-强制循环下降管;4-循环水泵;5-圆柱段水冷壁;6-上联箱;7-自然循环下降管;8-下联箱;9-煤粉烧嘴;a-汽包给水管;b-圆台段水冷壁回水口;c-圆台段水冷壁进水口。
具体实施方式
[0041]
具体实施方式一:结合图1至图3说明本实施方式,本实施方式的一种分开采用自然循环和强制循环的水冷壁气化炉,所述水冷壁气化炉装置包括气化炉本体,所述气化炉本体包括圆台段水冷壁1、圆柱段水冷壁5、上联箱6和下联箱8,圆台段水冷壁1、上联箱6、圆柱段水冷壁5和下联箱8沿竖直方向由上至下依次同轴设置;
[0042]
圆台段水冷壁1位于气化炉顶部,圆台段水冷壁1整体为下端开口的空心圆台形结构,圆台段水冷壁1为独立的盘管式水冷壁,圆柱段水冷壁5位于气化炉中下部,圆柱段水冷壁5整体为两端开口的空心圆柱形结构,圆柱段水冷壁5为独立的竖直列管式水冷壁,上联箱6和下联箱8均为圆环形管状结构,圆柱段水冷壁5的竖直列管顶端与上联箱6进口连接,圆柱段水冷壁5的竖直列管底端与下联箱8出口连接;
[0043]
所述水冷壁气化炉装置还包括汽包2、强制循环下降管3、循环水泵4、自然循环下降管7和多个煤粉烧嘴9;圆台段水冷壁1的顶端设为圆台段水冷壁回水口b,所述圆台段水冷壁回水口b通过强制循环下降管3与汽包2下部连通,汽包2上部设有汽包给水管a,圆台段水冷壁1的底端设有圆台段水冷壁进水口c,所述圆台段水冷壁进水口c通过强制循环下降管3与循环水泵4出水口连接,循环水泵4进水口通过强制循环下降管3与汽包2下部连通;上联箱6出口通过自然循环下降管7与汽包2连通,下联箱8进口与汽包2下部连通;多个煤粉烧嘴9沿圆周方向均匀布置安装在圆柱段水冷壁5中上部。
[0044]
本实施方式中,圆台段水冷壁1采用盘管形式,水冷壁整体为圆台形,水冷壁以强制循环冷却,圆台段水冷壁1的进水口设置在圆台盘管底部,回水口设置在圆台盘管顶部,进回水口均向盘管外侧引出。圆柱段水冷壁5采用竖直列管形式,水冷壁以自然循环冷却。两套水冷壁分开制造安装。
[0045]
具体实施方式二:结合图1至图3说明本实施方式,本实施方式的圆台段水冷壁1高为h1,圆柱段水冷壁5高度h2,满足h2》h1,且h2=(5~20)h1。其它组成和连接关系与具体实施方式一相同。
[0046]
具体实施方式三:结合图1至图3说明本实施方式,本实施方式的圆台段水冷壁1的母线长l,满足l=(1.15~3)h1。其它组成和连接关系与具体实施方式一或二相同。
[0047]
具体实施方式四:结合图1至图3说明本实施方式,本实施方式的汽包2的数量为一个或者两个,当汽包2的数量为一个时,圆柱段水冷壁5和圆台段水冷壁1连接同一个汽包2;当汽包2的数量为两个时,圆柱段水冷壁5和圆台段水冷壁1分别连接对应的独立的汽包2。如此设置,圆柱段水冷壁5和圆台段水冷壁1可以连接同一个汽包2,也可以连接对应的独立的汽包(5)。其它组成和连接关系与具体实施方式一、二或三相同。
[0048]
具体实施方式五:结合图1至图3说明本实施方式,本实施方式的圆台段水冷壁1由单管、双管或者多管绕成。如此设置,圆台段水冷壁1由单管绕成,但是可根据情况选择双管或其他管数绕成。其它组成和连接关系与具体实施方式一、二、三或四相同。
[0049]
具体实施方式六:结合图1至图3说明本实施方式,本实施方式的煤粉烧嘴9的数量为四个,所述四个煤粉烧嘴9沿圆周方向均匀布置安装在圆柱段水冷壁5中上部,且四个煤粉烧嘴9的轴线位于同一水平面上。如此设置,煤粉与气化剂从位于气化炉上部的四个煤粉烧嘴9喷出,通过将四个煤粉烧嘴9布置在同一水平面上,能够保证生成的四股高温合成气在炉膛中心区域对撞。其它组成和连接关系与具体实施方式一、二、三、四或五相同。
[0050]
具体实施方式七:结合图1至图4说明本实施方式,本实施方式的一种基于具体实施方式一至六任意一项实施方式所述分开采用自然循环和强制循环的水冷壁气化炉的冷却方法,所述分开采用自然循环和强制循环的水冷壁气化炉方法是通过一下步骤实现的,
[0051]
步骤一、圆台段水冷壁1的强制循环过程:
[0052]
汽包2内的冷却水在循环水泵4的作用下由强制循环下降管3通入圆台段水冷壁1的圆台段水冷壁进水口c,经由圆台段水冷壁1吸热后从圆台段水冷壁回水口b由强制循环下降管3进入汽包2;
[0053]
步骤二、圆柱段水冷壁5的自然循环过程:
[0054]
汽包2内的冷却水由自然循环下降管7通入下联箱8,进入下联箱8内的冷却水再由下联箱8出口通入,经由圆柱段水冷壁5吸热后进入上联箱6,进入上联箱6内的冷却水由上联箱6出口通入,经由自然循环下降管7进入汽包2;
[0055]
步骤三、高温合成气的生成过程:
[0056]
煤粉与气化剂从位于气化炉上部的四个煤粉烧嘴9喷出后,在气化炉炉膛内剧烈混合,发生强烈的燃烧及气化反应,生成高温合成气,四股高温合成气流在气化炉炉膛中心区域对撞后,其中一部分气流偏转并冲向气化炉顶部,高温合成气流中携有未燃尽的煤粉,冲击气化炉顶部后贴近顶部圆台段水冷壁1壁面折转向下,另外一部分高温合成气偏转向下进入炉膛中下部。其它组成和连接关系与具体实施方式一、二、三、四、五或六相同。
[0057]
具体实施方式八:结合图1至图4说明本实施方式,本实施方式的步骤一和步骤二中所述的圆台段水冷壁1和圆柱段水冷壁5通入的冷却水温为120~140℃,圆柱段水冷壁5内工质流速为0.1~0.3m/s,圆台段水冷壁内工质流速为0.5~2m/s。其它组成和连接关系与具体实施方式一、二、三、四、五、六或七相同。
[0058]
具体实施方式九:结合图1至图4说明本实施方式,本实施方式的步骤一中采用强制循环的圆台段水冷壁1的进回水工质温升控制在8~12℃,当圆台段水冷壁1进回水工质温升低于8℃时,降低循环水泵4出力,降低强制循环工质流速;当圆台段水冷壁1进回水工质温升高于12℃,提高循环水泵4出力,提高强制循环工质流速。如此设置,当圆台段水冷壁1进回水工质温升低于8℃时,应降低循环水泵4出力,降低强制循环工质流速,追求更高的经济效益。当圆台段水冷壁1进回水工质温升高于12℃,应提高循环水泵4出力,提高强制循环工质流速,防止工质吸热饱和汽化使换热恶化,影响设备运行安全。其它组成和连接关系与具体实施方式一、二、三、四、五、六、七或八相同。,
[0059]
具体实施方式十:结合图1至图4说明本实施方式,本实施方式的步骤三中所述高温合成气中的成分包括co、h2和co2,步骤三中所述高温合成气中40%的气流偏转并冲向气化炉顶部,所述高温合成气中60%的高温合成气偏转向下进入炉膛中下部。其它组成和连接关系与具体实施方式的一、二、三、四、五、六、七、八或九相同。
[0060]
实施例:一台应用本发明的80000nm3/h造气量的气化炉,采用本发明所述分开采
用自然循环和强制循环的水冷壁气化炉及冷却方法前,两年发生了三次爆管泄漏事故,均有2处以上的泄漏点,事故位置均发生在顶部圆台段水冷壁,平均每次停车检修2个月,产生了巨大的经济损失。应用本发明所述分开采用自然循环和强制循环的水冷壁气化炉及冷却方法后,已运行4年顶部水冷壁不发生烧损,相比现有的其它技术,可减少各类经济损失总计8000万元。
[0061]
本发明已以较佳实施案例揭示如上,然而并非用以限定本发明,任何熟悉本专业的技术人员,在不脱离本发明技术方案范围内,当可以利用上述揭示的结构及技术内容做出些许的更动或修饰为等同变化的等效实施案例,但是凡是未脱离本发明技术方案的内容,依据本发明的技术实质对以上实施案例所做的任何简单修改、等同变化与修饰,均仍属本发明技术方案范围。
再多了解一些
本文用于企业家、创业者技术爱好者查询,结果仅供参考。