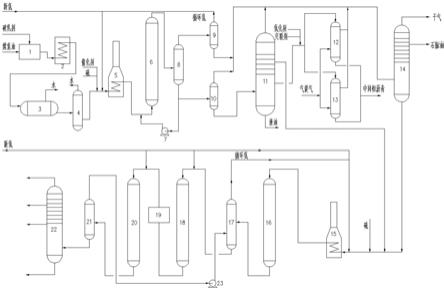
1.本发明属于煤焦油深加工技术领域,具体涉及一种用煤焦油制取中间相沥青 和特种油品的系统及方法。
背景技术:
2.煤焦油是炼焦、热解的副产物,根据炼焦、热解的温度区间、时间、工艺不 同,煤焦油分为高温煤焦油、中温煤焦油、中低温煤焦油。
3.煤焦油的组份复杂、灰分、沥青质含量高、分子结构复杂,且含有大量的 氮、氧、硫的化合物,碳氢比大。煤焦油轻组份目前多采用加氢的工艺路线生产 燃料油品、特种油品及化工品,或者先分馏再经精馏、萃取、结晶、络合等工艺 生产化工品;重组份多环芳烃含量高,多数作为生产碳材料的原料。
4.随着高级碳素材料的需求扩大,沥青基碳纤维、泡沫炭、c/c复合材料、c/ 金属复合材料、炭微球等展现了广阔的应用前景。在碳纤维方面相对于使用丙烯 腈等原料生产碳纤维,在模量、导热性方面有显著的优势,但煤焦油中特别是重 组份杂质、灰分、沥青质太高,通过溶剂萃取流程长能耗高且洁净度低,通过加 氢沥青质很容易缩聚结焦。如何处理煤焦油杂质获得生产高品质的碳材料的原料 是制取碳素材料的关键。
5.在对重质组份加氢中多采用悬浮床、浆态床,基本采用铁系固体催化剂,活 性较低,操作温度高,热裂解后加氢饱和为主要反应,开环轻质化严重,不利于 生成洁净的对后续加工有利的多环类物质,固体催化剂对设备的磨损也大。
6.申请号为201410178317.4的专利公开了一种中间相沥青及利用煤液化精制沥 青制备中间相沥青的方法,原料采用煤液化副产的精制沥青制备中间相沥青,但 是该方法中原料结构单一,可调节灵活性差,不能根据中间相沥青的产率和品质 需求而通过调整加氢液化的条件来调节原料的性质。
7.申请号为201210009243.2的专利公开了一种高温煤焦油加氢生产中间相沥青 的方法,采用高温煤焦油,通过水洗对原料脱盐,离心脱除喹啉不溶物,进行加 氢反应氢化沥青,同时分离轻质部分作为燃料油,重质部分缩合为中间相沥青。 但是该方法所用原料高温煤焦油杂质含量高,沥青质含量高,大多金属不是以离 子状态存在,而是络合状态形成化合物,通过水洗无法有效脱除,且大部分喹啉 不溶物是小于10μm的焦粉,很难通过离心方法脱除,所以,通过水洗和离心的 方法无法保证原料满足固定床加氢进料的条件,不能保证催化剂稳定运行。同 时,高温煤焦油50%以上是分子量大于2000的沥青质,在加氢过程中很容易缩聚 积碳堵塞催化剂的孔道,有限的空隙无法容纳大量的金属和杂质,该方法采用精 制催化剂加氢活性很高,杂质、沥青质缩合结焦会造成床层压降快速上升,固定 床加氢装置无法长期稳定运行。另外,该方法将生产中间相沥青和燃料油置于同 一段加氢生产,无法做到既能生产高收率、低软化点的中间相沥青又能使副产的 油品达标;高温煤焦油采用固定床加氢无法长周期运行。
8.申请号为201710831383.0的专利公开了一种基于中低温煤焦油加氢制取中间 相
沥青和油品的系统及方法,采用助剂结合电脱盐和热过滤进行了中低温煤焦油 的预处理,脱除灰分,采用新的催化剂级配方案加氢氢化后重质部分经热缩聚, 就可生产软化点低、灰分低、碳纯度高的中间相沥青,轻质组分进一步加氢处理 生产燃料油品,再通过中间相沥青碳化生产炭材料,这样既可降低碳材料成本又 可生产高品质的燃料油品或特种油品。该专利中预处理为保证固定床较长时间运 行,不仅要脱掉造成设备腐蚀的氯离子,还要脱掉造成催化剂失活的铁、钙、镁 离子和喹啉不溶物,预处理较为复杂;固定床加氢反应成本较低,仅适用于中低 温煤焦油,对于高温煤焦油或者大分子沥青质无法长周期运行,且后续加氢改质 反应中采用常规催化剂级配方案,操作压力高、投资大、加氢深度不足;在缩聚 反应中软化点较难调整。
9.因此,开发一种投资和运行成本较低,不受原料限制的加氢制软化点可调的 高品质沥青中间相、同时生产高品质油品的方法,有着重要的意义。
技术实现要素:
10.为了克服以上方法的不足,本发明提供了一种以煤焦油作为原料制取中间相 沥青和油品的方法,该方法可灵活调整中间相沥青的原料族组成、灰分,保证中 间相沥青和油品的质量同时满足要求。
11.同时,本发明还提供了一种能够实现上述方法的基于煤焦油加氢制取中间相 沥青和油品的系统。
12.本发明解决上述技术问题所采用的基于煤焦油加氢制取中间相沥青和油品的 方法包括以下步骤:
13.(1)煤焦油预处理
14.煤焦油与破乳剂通过混合器混合,经加热器加热后进入脱水罐分层脱水,氯 离子随水脱出,脱水后的煤焦油进入闪蒸塔进一步闪蒸脱掉微量的水,完成煤焦 油预处理。
15.(2)煤焦油浆态床加氢
16.将步骤(1)预处理后的煤焦油、纳米级催化剂异辛酸钼、液硫及氢气混 合,经加热炉加热至310~330℃后从浆态床反应器底部进入,在浆态床反应器内 进行加氢反应以饱和烯烃、脱金属、脱硫、脱氮、脱氧;加氢产物经第一高压分 离器分离,气相经减压冷却后进入冷低压分离器,液相一部分减压进入热低压分 离器、另一部分经高压循环泵与加热炉加热后的物料混合后进入浆态床反应器进 一步进行加氢反应;热低压分离器底部馏分进入减压塔,经减压塔减压后分为顶 部干气和石脑油馏分、中上部小于300℃的轻柴油馏分、中下部大于300℃的重 油馏分与底部渣油馏分;冷低压分离器底部出口馏分与热低压分离器顶部出口馏 分、减压塔顶部馏分混合进入第一分馏塔,冷低压分离器顶部气体排入循环氢管 线。
17.(3)重质组分热缩聚制取中间相沥青
18.将步骤(2)减压塔中下部分馏出的大于300℃的重油馏分与氢化剂及交联剂 混合依次从顶部进入从顶部进入其中一个热缩聚塔中,待该缩聚塔充满后再切换 至另一个热缩聚塔进料,热缩聚塔之间轮流切换运行进行热缩聚反应;热缩聚反 应过程中从热缩聚塔上部被惰性气体吹扫带出的轻组分石脑油和柴油馏分,与步 骤(2)中冷低压分离器底部出口馏分、热低压分离器顶部出口馏分及减压塔顶 部馏分混合进入第一分馏塔,分馏为干
气、石脑油馏分和柴油馏分,而热缩聚塔 内的重质组分从塔底流出经冷却破碎即为中间相沥青。
19.(4)轻质组分加氢制油品
20.将步骤(2)减压塔中上部分馏出的小于300℃的柴油馏分、步骤(3)第一 分馏塔分馏得到的柴油馏分、液硫、氢气混合进入第二加热炉加热后从第一精制 反应器顶部进入,在第一精制反应器内进行加氢精制脱硫、脱氮和芳烃饱和反 应,生成油从第一精制反应器底部排出进入高压气提塔被氢气压缩机循环氢气气 提,气提后的气相部分从高压气提塔顶部进入循环氢管线,气提后的液相部分从 高压气提塔底部排出与氢气混合进入异构反应器进行异构降凝,生成油从异构反 应器底部排出经换热器换热后进入第二精制反应器后精制,生成油再经第二高压 分离器分离,气相部分从顶部排出经氢气压缩机循环作为高压气提塔的气提气, 液相部分从底部排出进入第二分馏塔精馏为油品石脑油、航煤馏分、柴油馏分。
21.上述步骤(1)中,优选所述破乳剂注入量为100~500ppm,预处理的条件 为:温度120~150℃,压力1~2mpa。
22.上述步骤(2)中,优选所述纳米级催化剂异辛酸钼的平均粒径为100nm,其 注入量为80~500ppm。进一步优选所述加氢反应的条件为:压力为3~18mpa,反 应温度为330~410℃,氢油比为800~1500:1,总液体体积空速为0.1~0.8h-1
。
23.上述步骤(3)中,优选所述氢化剂为环烷烃,其注入量为重油馏分质量的 1%~3%;所述交联剂为烯烃、炔烃、醛中任意一种,其注入量为重油馏分质量的 2%~10%。进一步优选所述热缩聚反应是在惰性气体鼓泡气提下,以2.1~3.5℃ /min的升温速率加热、以8~25r/min转速搅拌,当温度升到250~320℃时,然 后升压到0.1~4.5mpa,继续以5~15℃/min的升温速率升温至360~490℃恒温 380~480min。
24.上述步骤(4)中,优选所述第一精制反应器加氢精制的反应温度为300~ 400℃,反应压力为4~21mpa,氢油比为800~1200:1,总液体体积空速为0.2~ 0.5h-1
;异构反应器异构降凝的反应温度为320~380℃,反应压力为4~21mpa, 氢油比为800~1500:1,总液体体积空速为0.5~1.5h-1
;第二精制反应器后精制 的反应温度为150~250℃,反应压力为4~21mpa,氢油比为600~1000:1,总液 体体积空速为0.3~1.8h-1
。
25.上述步骤(4)中,优选第一精制反应器加氢精制的催化剂是以硅改性γ
‑ꢀ
al2o3为载体,负载18%~26%wo3、6%~12%moo3、1%~2%nio作为活性组分;异构 反应器异构降凝的催化剂是以h型沸石为载体,负载3.5%~9.5%nio作为活性组 分;第二精制反应器后精制的催化剂是以sio2为载体,负载8%~15%nio作为活 性组分;其中,活性组分的负载量均以催化剂质量为100%计。
26.实现上述基于煤焦油加氢制取中间相沥青和油品的系统包括:煤焦油预处理 单元、煤焦油浆态床加氢单元、重质组分热缩聚制取中间相沥青单元、轻质组分 加氢制油品单元;其中,煤焦油预处理单元由混合器、加热器、脱水罐、闪蒸脱 水塔组成;煤焦油浆态床加氢单元包括第一加热炉、浆态床反应器、高压循环 泵、第一高压分离器、冷低压分离器、热低压分离器、减压塔;重质组分热缩聚 制取中间相沥青单元包括至少2个并联连接的热缩聚塔、第一分馏塔;热缩聚塔 轻质组分加氢制油品单元包括第二加热炉、第一精制反应器、高压气提塔、异构 反应器、换热器、第二精制反应器、第二高压分离器、第二分馏塔、氢
气压缩 机;所述混合器、加热器、脱水罐、闪蒸脱水塔、第一加热炉依次连通,第一加 热炉出口与浆态床反应器底部入口连通,浆态床反应器顶部出口与第一高压分离 器中部连通,第一高压分离器底部与热低压分离器连通并经高压循环泵与第一加 热炉底部入口连通,第一高压分离器顶部出口与冷低压分离器中部连通;冷低压 分离器顶部出口与第一加热炉连通,热低压分离器底部出口与减压塔中部连通; 热低压分离器顶部出口、冷低压分离器底部出口、减压塔顶部出口以及热缩聚塔 上部出口与第一分馏塔中下部连通;热低压分离器顶部出口、冷低压分离器底部 出口、减压塔顶部出口以及热缩聚塔上部出口与第一分馏塔连通;减压塔中上部 出口、第一分馏塔底部出口与第二加热炉连通;第二加热炉与第一精制反应器顶 部入口连通,第一精制反应器底部出口与高压气提塔中下部连通,高压气提塔顶 部出口与第二加热炉连通,高压气提塔底部出口与异构反应器顶部入口连通;异 构反应器底部出口经换热器与第二精制反应器顶部入口连通,第二精制反应器底 部出口与第二高压分离器中部连通,第二高压分离器顶部出口经氢气压缩机与高 压气提塔下部入口连通,第二高压分离器底部出口与第二分馏塔连通。
27.与现有技术相比,本发明的有益效果如下:
28.本发明方法中,预处理只脱除对设备腐蚀的氯离子,不用脱除造成催化剂积 碳的铁、钙、镁离子,也不需要过滤杂质,过程简洁;加氢采用浆态床反应器, 原料适应性强,特别是一些重质的、固含量大的劣质油品,所采用纳米级异辛酸 钼油容性催化剂活性高、加入量少、反应温度低,并可根据中间相沥青的需求深 度脱除硫、氮、氧及金属离子,并可调整芳烃的饱和度;热缩聚反应通过加入氢 化剂和交联剂调整中间相沥青的软化点和中间相含量的百分比,并对热缩聚反应 的加热速度和停留时间优化使其更利于生成域状的中间相沥青;油品精制脱氮、 异构降凝与后精制中,第一精制反应器采用钨、镍、钼组合的普通硫化态催化 剂,保证了脱氮的效果,异构反应器采用ni基h型沸石催化剂和第二精制反应 器采用镍基催化剂,用普通金属还原态催化剂替代贵金属催化剂,降低了投资成 本,再通过第二精制反应后无硫、氮的气体循环作为第一精制反应器产物气提 气,保证异构降凝、后精制还原态催化剂的长周期稳定运行。
附图说明
29.图1是实施例1制取中间相沥青和油品的方法流程图。
30.图中:1-混合器,2-加热器,3-脱水罐,4-闪蒸塔,5-第一加热炉,6-浆态 床反应器,7-高压循环泵,8-第一高压分离器,9-冷低压分离器,10-热低压分 离器,11-减压塔,12-第一热缩聚塔,13-第二热缩聚塔,14-第一分馏塔,15-第 二加热炉,16-第一精制反应器,17-高压气提塔,18-异构反应器,19-换热器, 20-第二精制反应器,21-第二高压分离器,22-第二分馏塔,23-氢气压缩机。图2是实施例1中以高温煤焦油为原料生产的中间相沥青和油品放大100倍 的图片。
具体实施方式
31.下面结合附图和实施例对本发明进一步详细说明,但本发明的保护范围不仅 限于这些实施例。
32.如图1所示,本实施例基于煤焦油加氢制取中间相沥青和油品的系统主要包 括煤焦油预处理单元、煤焦油浆态床加氢单元、重质组分热缩聚制取中间相沥青 单元、轻质组分加氢制油品单元;其中,煤焦油预处理单元由混合器1、加热器 2、脱水罐3、闪蒸脱水塔4组成;煤焦油浆态床加氢单元由第一加热炉5、浆态 床反应器6、高压循环泵7、第一高压分离器8、冷低压分离器9、热低压分离器 10、减压塔11连接构成;重质组分热缩聚制取中间相沥青单元由第一热缩聚塔 12、第二热缩聚塔13、第一分馏塔14连接构成;轻质组分加氢制油品单元由第 二加热炉15、第一精制反应器16、高压气提塔17、异构反应器18、换热器19、 第二精制反应器20、第二高压分离器21、第二分馏塔22、氢气压缩机23连接构 成。
33.煤焦油管线和破乳剂管线分别与混合器1连通,混合器1出口通过管线依次 与加热器2、脱水罐3、闪蒸脱水塔4连通,闪蒸脱水塔4出口通过管线与第一 加热炉5连通,新氢管线、催化剂管线以及液硫管线分别与闪蒸脱水塔4和第一 加热炉5之间的管线连通,第一加热炉5出口通过管线与浆态床反应器6底部入 口连通,浆态床反应器6顶部出口通过管线与第一高压分离器8中部连通,第一 高压分离器8底部通过管线与热低压分离器10连通并通过管线经高压循环泵7 与第一加热炉5底部入口连通,第一高压分离器8顶部出口通过管线与冷低压分 离器9中部连通;冷低压分离器9顶部出口通过循环氢管线与第一加热炉5连 通,热低压分离器10底部出口通过管线与减压塔11中部连通,减压塔11中下 部出口和氢化剂管线、交联剂管线通过管线分别与第一热缩聚塔12和第二热缩 聚塔13的顶部入口连通;热低压分离器10顶部出口、冷低压分离器9底部出 口、减压塔11顶部出口以及第一热缩聚塔12和第二热缩聚塔13上部出口通过 管线与第一分馏塔14中下部连通;减压塔11中上部出口、第一分馏塔14底部 出口、新氢管线、循环氢管线以及液硫管线通过管线与第二加热炉15连通;第 二加热炉15通过管线与第一精制反应器16顶部入口连通,第一精制反应器16 底部出口通过管线与高压气提塔17中下部连通,高压气提塔17顶部出口通过循 环氢管线与第二加热炉15连通,高压气提塔17底部出口和新氢管线通过管线与 异构反应器18顶部入口连通;异构反应器18底部出口经换热器19通过管线与 第二精制反应器20顶部入口连通,新氢管线和第二精制反应器20顶部入口连 通,第二精制反应器20底部出口通过管线与第二高压分离器21中部连通,第二 高压分离器21顶部出口通过管线经氢气压缩机23与高压气提塔17下部入口连 通,第二高压分离器21底部出口通过管线与第二分馏塔22连通。
34.需要进一步说明的是,热缩聚塔也可以根据煤焦油处理量以及所需中间相沥 青的品质和组分而增减调整,不仅限于2个塔,但是为了保证整个系统运行稳 定,至少设置2个塔为佳。
35.采用上述系统实现煤焦油加氢制取中间相沥青和油品的方法,具体由下述步 骤组成:
36.(1)煤焦油预处理
37.将煤焦油与破乳剂通过混合器1混合,经加热器2加热后进入脱水罐3分层 脱水,氯离子随水脱出,脱水后的煤焦油进入闪蒸塔4进一步闪蒸脱掉微量的 水,完成煤焦油预处理;其中,破乳剂为陕西中恒新材料有限公司zh-004型破 乳剂,其注入量为100~500ppm,预处理的条件为:温度100~150℃,压力1~ 2mpa。
38.(2)煤焦油浆态床加氢
39.将步骤(1)预处理后的煤焦油、纳米级催化剂异辛酸钼、液硫及氢气混 合,经加热
炉5加热至310~330℃后从浆态床反应器6底部进入,在浆态床反应 器6内进行加氢反应以饱和烯烃、脱金属、脱硫、脱氮、脱氧等,加氢产物经第 一高压分离器8分离,气相经减压冷却后进入冷低压分离器9,液相一部分减压 进入热低压分离器10、另一部分经高压循环泵7与加热炉5加热后的物料混合进 入浆态床反应器6进一步进行加氢反应。热低压分离器10底部馏分进入减压塔 11,经减压塔11减压后分为顶部干气和石脑油馏分、中上部小于300℃的轻柴油 馏分、中下部大于300℃的重油馏分以及底部渣油馏分。冷低压分离器9底部馏 分、热低压分离器10顶部馏分以及减压塔11顶部馏分混合后进入第一分馏塔 14,冷低压分离器9顶部气体排入循环氢管线。其中,纳米级催化剂异辛酸钼的 平均粒径为100nm,其注入量为80~500ppm;浆态床反应器6加氢反应压力为3 ~18mpa,反应温度为330~410℃,氢油比为800~1500:1,总液体体积空速为 0.1~0.8h-1
。
40.(3)重质组分热缩聚制取中间相沥青
41.将步骤(2)减压塔11中下部分馏出的大于300℃的重油馏分与氢化剂及交 联剂混合从顶部进入第一热缩聚塔12,待第一热缩聚塔12充满后再切换至第二 热缩聚塔13进料,第一热缩聚塔12和第二热缩聚塔13轮流切换运行进行热缩 聚反应。所述氢化剂为环烷烃,其注入量为重油馏分质量的1%~3%;所述交联剂 为烯烃、炔烃、醛等,其注入量为重油馏分质量的2%~10%。热缩聚反应是在惰 性气体鼓泡气提下,以2.1~3.5℃/min的升温速率加热、以8~25r/min转速搅 拌,当温度升到250~320℃时,然后升压到0.1~4.5mpa,继续以5~15℃/min 的升温速率升温至360~490℃恒温380~480min。热缩聚反应过程中从热缩聚塔 上部被惰性气体吹扫带出的轻组分为石脑油和柴油馏分,该馏分与步骤(2)中 冷低压分离器9底部馏分、热低压分离器10顶部馏分及减压塔11顶部馏分混合 进入第一分馏塔14,分馏为干气、石脑油馏分和柴油馏分,而热缩聚塔内的重 质组分从塔底流出经冷却破碎即为中间相沥青。热缩聚反应可以根据氢化剂的注 入比例调整软化点。
42.(4)轻质组分加氢制油品
43.将步骤(2)减压塔11中上部分馏出的小于300℃的柴油馏分、步骤(3)第 一分馏塔14分馏得到的柴油馏分、液硫、氢气混合进入第二加热炉15加热后从 第一精制反应器16顶部进入,在第一精制反应器16内进行加氢精制脱硫、脱氮 和芳烃饱和反应,生成油从第一精制反应器16底部排出进入高压气提塔17被氢 气压缩机23循环氢气气提,气提后的气相部分从高压气提塔17顶部进入循环氢 管线,气提后的液相部分从高压气提塔17底部排出与氢气混合进入异构反应器 18进行异构降凝,生成油从异构反应器18底部排出经换热器19换热后进入第二 精制反应器20后精制,生成油再经第二高压分离器21分离,气相部分从顶部排 出经氢气压缩机23循环作为高压气提塔17的气提气,液相部分从底部排出进入 第二分馏塔22精馏为油品石脑油、航煤馏分、柴油馏分(轻质白油系列)。第 一精制反应器16加氢精制的反应温度为300~400℃,反应压力为4~21mpa,氢 油比为800~1200:1,总液体体积空速为0.2~0.5h-1
;异构反应器18异构降凝的 反应温度为320~380℃,反应压力为4~21mpa,氢油比为800~1500:1,总液体 体积空速为0.5~1.5h-1
;第二精制反应器20后精制的反应温度为150~250℃, 反应压力为4~21mpa,氢油比为600~1000:1,总液体体积空速为0.3~1.8h-1
。 第一精制反应器16加氢精制的催化剂是以硅改性γ-al2o3为载体,负载18%~26% wo3、6%~12%moo3、1%~2%nio作为活性组分;异构反应器18异构降凝的催化剂 是以h型沸石为载体,负载3.5%~9.5%nio作为活性组分;第二精制反应器20 后精
制的催化剂是以sio2为载体,负载8%~15%nio作为活性组分。其中活性组 分负载量均以催化剂质量为100%计。第一精制反应器16加氢精制催化剂需要开 车时硫化,异构反应器18异构反应催化剂和第二精制反应器20后精制催化剂开 车时还原;第一精制反应器16精制后的生成油需通过第二高压分离器21分离后 的气相部分经氢气压缩机23气提,保证进入异构降凝和后精制的油品中硫、氮 含量均小于2ppm。
44.实施例1
45.以高温煤焦油为原料,按照表1反应条件按上述方法生产中间相沥青和油 品,并按照gjb 3075-97《军用柴油规范》、nb/sh/t 0913-2015《轻质白油》检 测方法对所得油品进行测定,结果见表2~4。所得中间相沥青软化点为185℃, 灰分0.18%,中间相沥青含量约90%,放大100倍的图片如图2。
46.表1典型反应条件
[0047][0048]
表2军用柴油
[0049]
[0050][0051]
表3轻质白油(w2-100)
[0052]
[0053][0054]
表4轻质白油(w2-ta)
[0055]
再多了解一些
本文用于企业家、创业者技术爱好者查询,结果仅供参考。