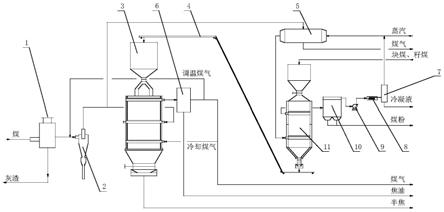
1.本发明属于煤气化、热解的煤化工技术领域,具体涉及一种气化热解耦合的块煤或者籽煤直立热解炉热解和干燥的系统,以及采用该系统将气化高温煤气的显热用于块煤或者籽煤的热解和干燥的方法。
背景技术:
2.基于我国“富煤、贫油、少气”是基本特征,以煤炭为主的资源禀赋是基本国情,煤炭作为我国主体能源的地位不会发生根本性转变。随着全球地缘政治局势变化、国际能源需求增加、资源市场争夺加剧,特别是油、气的对外依存使我国能源安全形势更加严峻。再加之我国煤炭资源利用方式主要直接燃烧为主,造成温室气体大量排放,面临碳达峰和碳中和的双碳限制。因此,大量开发绿色能源,改变能源消费结构,开发多种技术相耦合,梯级利用煤炭资源,清洁、高效的煤炭分质转化,减少煤炭的直接燃烧比重,多产化学制品以及对外依存度大的油、气,少排放甚至不排放二氧化碳,是当前我国煤化工必须解决的一个问题。
3.以热解为龙头,焦、气、油、化一体化多联产的煤炭分质利用技术,注重整体资源转化效率的最大化,能源利用的最优化,转化过程中污染物的集中、综合治理,是大幅提高煤炭转化效率、清洁利用的一种方式。
4.煤热解能产生高附加值的煤焦油、煤气,但目前的加热方式排放大量的二氧化碳,半焦的显热未回收利用,污水量巨大,无组织排放大,能源利用不充分;煤气化过程中产生大量的显热,回收工艺复杂,效率较低。
5.神木县三江煤化科技有限公司的sj系列炉、陕西冶金设计研究院有限公司的sh系列、中钢集团鞍山热能研究设计的znzl系列的基本原理类似,都是鼓入空气与煤气燃烧废气进行热解,将干燥、热解、冷却高度集成,机构紧凑、热效率较高,广泛应用生产实际中,取得了良好的经济效益和社会效益,但无独立的干燥系统,煤的外水同热解水变成污水,增加后续的污水处理费用,荒煤气含高达48%氮气和二氧化碳,有效气体组分低,热值只有1800大卡的低热值煤气,半焦基本采用水息焦方式,半焦含水量大,增加后续利用的成本,干馏炉炉壁和燃烧室采用异形耐火材料砌筑,投资巨大。
6.专利cn204644266u公开了一种干馏低变质烟煤的全循环干馏炉,热解的热量同样是通过燃烧煤气来提供,废气及碳排放大。息焦的方式是通过煤气直接与半焦换热来回收热量有所改进。
7.专利cn101691493a公开了一种外燃内热式煤干馏炉,用自身产生的煤气外部燃烧加热煤气产生的废气进行热解,干燥后的蒸汽循环息焦补热后再去干燥,过剩废气排入大气,此方法煤气质量同样含有大量的氮气和二氧化碳,且干燥段、热解段、息焦段靠气体分隔,难免造成互串,再加之息焦段含有未彻底热解而再息焦段产生的煤气会带入干燥段最终排入大气。
8.专利cn104130790a公开了一种间接换热的煤干馏工艺,是通过燃烧煤气加热间接
换热的蓄热材料,然后煤气与蓄热材料换热,换热后的煤气去干馏煤,加热蓄热材料后的烟气再去干燥,息焦用间接水冷加喷淋,热解产生的煤气大部分作为燃料使用掉,干燥后的水蒸汽、二氧化碳及voc全部排入大气。
9.专利cn104449782a公开了一种基于籽煤热解与荒煤气除尘耦合的热解除尘系统及方法,热解的热量也是通过燃烧煤气去间接换热煤气参与热解,同时热解之前利用煤层颗粒层对荒煤气进行过滤除尘,通过蒸汽间接换热息焦并补热后进行干燥,同样会有大量的二氧化碳排放,干燥段、热解段和息焦段同样存在煤气互串的风险。
10.以上专利热解需要的热源都是由燃烧煤气直接或者间接提供的,大部分专利干燥后的水汽、二氧化碳及少量的voc排入大气,热解过程中产生大量的污水,环境污染大,碳排放大,热效率和能源利用率有待于进一步提高。
11.专利cn107057770a公开了一种下行式热解和上流式气化耦合制备煤焦油和煤气的装置及方法,是粉煤气流床热解,与直立炉相比投资巨大,无法生产块状半焦或者籽焦,无法作为电石、铁合金的还原剂,所有热解煤都需磨到200微米左右,能耗较高。
技术实现要素:
12.本发明所要解决的技术在于克服现有技术的缺点,提供一种节能环保、产品质量高、工作效率高、实现能量综合利用、将煤气化和干燥及热解耦合做到分级转化和优化集成的煤气化热解耦合的直立热解炉热解和干燥系统及方法。
13.解决上述技术问题所采用的技术方案是:一种煤气化热解耦合的直立热解炉热解和干燥系统,气化炉的煤气导出口通过管道与旋风除尘器的入口、喷淋冷却分离器的煤气出口相连通,旋风除尘器的气相出口通过管道与热解装置的高温煤气总进气管和换热器煤气入口相连通,换热器的蒸汽出口通过管道与干燥装置的高温蒸汽进气总管入口相连通,干燥装置的蒸汽汇集管出口通过管道与布袋除尘器的入口相连通,布袋除尘器的气相出口通过引风机与空冷器的入口相连通,空冷器的出口通过气液分离器与换热器的蒸汽入口相连通,干燥装置出料口的下方设置有密封皮带输送器,密封皮带输送器的另一端位于热解装置进料口上方,热解装置的荒煤气出口与喷淋冷却分离器的入口相连通,热解装置的冷却煤气入口与喷淋冷却分离器的煤气出口相连通;
14.所述热解装置的结构为直立热解炉顶部设置有干煤缓冲仓,干煤缓冲仓底部设置有至少1个出料口,干煤缓冲仓的出料口与直立热解炉通过下料管相连通,干煤缓冲仓出料口与下料管之间设置有进料锁气阀,干煤缓冲仓外侧壁及下料管上设置有第一蒸汽盘管和第一保温层,直立热解炉的腔体为一个或通过耐火材料隔板均匀分割成至少2个独立的腔体,直立热解炉的腔体数量与干煤缓冲仓的出料口数量对应,直立热解炉的每个腔体内上部水平设置有至少2根并列且均匀分布的荒煤气集气管、中部水平设置有至少2根并列且均匀分布的高温煤气进气分布管、下部水平设置有至少2根并列且均匀分布的冷却煤气进气分布管,直立热解炉外侧壁上设置有与荒煤气集气管相连通的荒煤气汇集管、与高温煤气进气分布管相连通的高温煤气总进气管、与冷却煤气进气分布管相连通的冷却煤气总进气管,直立热解炉底部设置有推焦机,推焦机下方直立热解炉的每个腔体对应一个出料口且出料口上均设置有出料插板阀,直立热解炉的出料口正下方设置有刮板机,刮板机的另一端出料口正下方设置有第一焦缓冲仓,第一焦缓冲仓内顶部设置有喷淋器,第一焦缓冲仓
底部出口与第二焦缓冲仓顶部入口通过第一锁气阀相连通,第二焦缓冲仓底部出口上设置有第二锁气阀;
15.所述干燥装置的结构为干燥炉顶部进料口上设置有原煤缓冲仓,原煤缓冲仓与干燥炉的进料口之间设置有进料插板阀,干燥炉外壁上缠绕有第二蒸汽盘管,第二蒸汽盘管外设置有第二保温层,第二保温层外设置有保护壳,干燥炉内上部水平设置有至少2根并列且均匀分布的蒸汽集气管、下部水平设置有至少2根并列且均匀分布的高温蒸汽进气分布管,干燥炉外侧壁上设置有与蒸汽集气管相连通的蒸汽汇集管、与高温蒸汽进气分布管相连通的高温蒸汽进气总管,干燥炉的出料口上设置有振动排料阀。
16.作为一种优选的技术方案,所述荒煤气集气管与直立热解炉内顶部之间的距离为0.5~1m,相邻两荒煤气集气管的间距为0.35~0.55m;所述高温煤气进气分布管与荒煤气集气管之间的距离为5~8m,相邻两高温煤气进气分布管的间距为0.35~0.55m;所述冷却煤气进气分布管与高温煤气进气分布管之间的距离为1~3m,冷却煤气进气分布管与推焦机之间的距离为0.5~1m,相邻两冷却煤气进气分布管的间距为0.35~0.55m。
17.作为一种优选的技术方案,所述荒煤气集气管为底部开口、顶部为等腰三角形的方管,所述荒煤气集气管的顶角β为55
°
~75
°
;所述高温煤气进气分布管为煤气外管内设置有煤气内管,煤气外管为底部开口、顶部为等腰三角形的方管,煤气外管的顶角α为55
°
~75
°
,煤气外管两侧壁上加工有均匀分布的斜布气孔,斜布气孔中心线与水平线之间的夹角为20
°
~70
°
,斜布气孔的孔径为5~8mm,煤气内管为圆管,煤气内管管壁上加工有均匀分布的径向布气孔,径向布气孔的开孔率为20%~60%、孔径为5~8mm;所述冷却煤气进气分布管的结构与高温煤气进气分布管的结构相同。
18.作为一种优选的技术方案,所述直立热解炉为支架上设置有横截面为矩形的热解炉本体,热解炉本体的长为6m或12m或18m或24m、宽为3~3.5m,热解炉本体的内侧壁上由内向外依次设置有耐磨层、隔热层。
19.作为一种优选的技术方案,所述蒸汽集气管与干燥炉内顶部之间的距离为0.5~1m,相邻两蒸汽集气管之间的距离为0.35~0.55m;所述高温蒸汽进气分布管与蒸汽集气管之间的距离为4~6m,高温蒸汽进气分布管与干燥炉内底部之间的距离为0.5~1m,相邻两高温蒸汽进气分布管之间的距离为0.35~0.55m。
20.作为一种优选的技术方案,所述蒸汽集气管为底部开口、顶部为等腰三角形的方管,所述蒸汽集气管的顶角为55
°
~75
°
;所述高温蒸汽进气分布管为蒸汽外管内设置有蒸汽内管,蒸汽外管为底部开口、顶部为等腰三角形的方管,蒸汽外管的顶角为55
°
~75
°
,蒸汽外管两侧壁上加工有均匀分布的斜布气孔,斜布气孔中心线与水平线之间的夹角为20
°
~70
°
,斜布气孔的孔径为5~8mm,蒸汽内管为圆管,蒸汽内管管壁上加工有均匀分布的径向布气孔,径向布气孔的开孔率为20%~60%、孔径为5~8mm。
21.作为一种优选的技术方案,所述干燥炉的横截面为矩形,干燥炉的长为6~24m、宽为3~3.5m。
22.作为一种优选的技术方案,所述气化炉为气流床气化炉或流化床气化炉或固定床气化炉。
23.本发明还提供一种煤气化热解耦合的方法,由以下步骤组成:
24.s1.煤气化
25.开工时,将煤输入气化炉气化,气化煤气经与调温氮气混合为温度为850~1000℃的混合煤气,经旋风除尘器除尘后减压为常压,一部分输入直立热解炉,另一部分输入到换热器;灰渣从气化炉底部排出;
26.s2.气化煤气与蒸汽换热
27.换热器内外部输入的温度为130~150℃的干燥蒸汽与温度为850~1000℃的混合煤气换热后变为温度为350~380℃、压力为常压的高温过热蒸汽并通过管道输入到干燥装置的高温蒸汽进气总管,由高温蒸汽进气分布管输入到干燥炉内,换热后的煤气作为产品输出;
28.s3.块煤或籽煤干燥
29.含水为8%~18%、温度为常温的块煤或籽煤通过皮带送入干煤缓冲仓,而后进入干燥炉内自上而下移动,同时,输入干燥炉内的高温过热蒸汽进入煤层自下而上流动,块煤或籽煤与高温过热蒸汽逆向接触换热,使块煤或籽煤干燥并升温至150~180℃,干燥并升温后的块煤或籽煤继续下移经振动排料阀排出,由密封皮带输送器输送到干煤缓冲仓;与干燥块煤或籽煤换热后的温度为130~150℃、压力为-8~-1kpa的微负压蒸汽通过蒸汽集气管输出到蒸汽汇集管,由蒸汽汇集管输出到布袋除尘器,布袋除尘器除尘后的气体经引风机进入空冷器冷却,再经蒸汽气液分离器分离,大部分蒸汽以凝结水排出,少部分不凝蒸汽作为换热蒸汽输入到换热器循环利用,布袋除尘器内的煤粉从底部出料口排出;
30.s4.块煤或籽煤热解
31.干煤缓冲仓内温度为150~180℃的块煤或籽煤下料到直立热解炉内,并在直立热解炉内自上而下移动,同时旋风除尘器输出的减压为常压、温度为850~1000℃的混合煤气由高温煤气总进气管和高温煤气进气分布管进入到直立热解炉内自下而上穿过热解段煤层,与150~180℃的块煤或籽煤逆向换热,块煤或籽煤吸收热量升温到500~700℃开始热解,热解后的荒煤气温度降为160~200℃进入荒煤气集气管,经荒煤气汇集管输出到喷淋冷却分离器,由喷淋冷却分离器快速分离为煤焦油、水和煤气,煤焦油和水导出,煤气分为三部分,一部分作为冷却煤气由高温煤气总进气管和高温煤气进气分布管进入直立热解炉循环利用、另一部分替换开工时的调温氮气经调温煤气管道与气化炉输出的气化煤气混合后进入旋风除尘器、剩余部分作为产品煤气导出;
32.s5.半焦冷却及产品半焦输出
33.直立热解炉内热解形成的半焦继续向下移动进入冷却段与冷却煤气逆流换热,冷却煤气被加热到400~550℃后与由高温煤气总进气管和高温煤气进气分布管进入的温度为850~1000℃的混合煤气再次混合为550~750℃煤气自下而上穿过热解段煤层,与150~180℃的块煤或籽煤逆向换热,半焦被冷却至60~80℃后经推焦机推入到直立热解炉的出料口,经直立热解炉的出料口排出到刮板机,关闭第一锁气阀,刮板机将半焦刮入到第一焦缓冲仓进行喷淋降温,汽提半焦并阻断煤气,待第一焦缓冲仓内的半焦量达到第一焦缓冲仓体积的1/2以上时,关闭第二锁气阀,打开第一锁气阀,让第一焦缓冲仓的半焦卸到第二焦缓冲仓内,然后关闭第一锁气阀,打开第二锁气阀卸料半焦到皮带作为产品送出。
34.作为一种优选的技术方案,所述气化炉为气流床气化炉时,煤采用过200目的煤粉,气化温度为1300~1600℃,气化压力小于0.5mpa,气化炉采用液态排渣;所述气化炉为流化床气化炉时,煤采用10cm以下粒煤,用氮气吹入气化炉,由蒸汽和氧气流化并气化,气
化温度为950~1050℃,气化压力小于0.5mpa,气化炉采用固态排渣;所述气化炉为固定床气化炉时,煤采用8~30cm煤块,气化温度为950~1050℃,气化压力小于0.5mpa,气化炉采用液态排渣。
35.本发明的有益效果如下:
36.1)本发明利用气化产生的高温煤气显热、冷却热解半焦煤气的回收热在料层分散混合,为低阶煤的热解提供所需的热量,梯度冷却、梯度加热解热、颗粒层过滤、重质组分轻质化耦合在一个热解装置,生产合成气、煤焦油、高质量高炉喷吹料,热效率高。
37.2)本发明采用气化煤气高温显热加热蒸汽,过热蒸汽干燥煤,大幅减少热解产生的污水,回收煤中外水作为工业补充用水,提供了水资源,减少污水处理的费用。
38.3)本发明热解干燥过程中无二氧化硫、氮氧化物、voc的排放,无温室气体二氧化碳的排放,热解装置、干燥装置结构简单紧凑,内构件少,投资少,规模可任意放大。
附图说明
39.图1是本发明煤气化热解耦合的直立热解炉热解和干燥系统的结构示意图。
40.图2是干燥装置11的结构示意图。
41.图3是图2的a-a剖视图。
42.图4是蒸汽集气管11-5的纵截面图。
43.图5是高温蒸汽进气分布管11-9的纵截面图。
44.图6是热解装置3的结构示意图。
45.图7是图6的左视图。
具体实施方式
46.下面结合附图和实施例对本发明进一步详细说明,但本发明不限于下述的实施方式。
47.实施例1
48.在图1中,本实施例的煤气化热解耦合的直立热解炉热解和干燥系统及方法由气化炉1、旋风除尘器2、热解装置3、密封皮带输送器4、换热器5、喷淋冷却分离器6、气液分离器7、空冷器8、引风机9、布袋除尘器10、干燥装置11连接构成。
49.气化炉1为气流床气化炉或流化床气化炉或固定床气化炉,气化炉1的煤气导出口通过管道与旋风除尘器2的入口、喷淋冷却分离器6的煤气出口相连通,旋风除尘器2的气相出口通过管道与热解装置3的高温煤气总进气管3-8入口和换热器5煤气入口相连通,换热器5的蒸汽出口通过管道与干燥装置11的高温蒸汽进气总管11-3入口相连通,干燥装置11的蒸汽汇集管11-2出口通过管道与布袋除尘器10的入口相连通,布袋除尘器10的气相出口通过引风机9与空冷器8的入口相连通,空冷器8的出口通过气液分离器7与换热器5的蒸汽入口相连通,干燥装置11出料口的下方设置有密封皮带输送器4,密封皮带输送器4的另一端位于热解装置3进料口上方,热解装置3的荒煤气出口与喷淋冷却分离器6的入口相连通,热解装置3的冷却煤气入口与喷淋冷却分离器6的煤气出口相连通。
50.在图2~5中,本实施例的干燥装置11由干燥炉11-1、蒸汽汇集管11-2、高温蒸汽进气总管11-3、振动排料阀11-4、蒸汽集气管11-5、第二蒸汽盘管11-6、第二保温层11-7、保护
壳11-8、高温蒸汽进气分布管11-9、进料插板阀11-10、原煤缓冲仓11-11连接构成。
51.干燥装置11顶部进料口上安装有原煤缓冲仓11-11,原煤缓冲仓11-11与干燥装置11的进料口之间安装有进料插板阀11-10,原煤缓冲仓11-11用于接收外部输送来的块煤或籽煤,干燥炉11-1的横截面为矩形,干燥炉11-1的长为6~24m、宽为3~3.5m,干燥炉11-1外壁上缠绕有第二蒸汽盘管11-6,第二蒸汽盘管11-6外加工有第二保温层11-7,第二保温层11-7外安装有保护壳11-8,干燥炉11-1内上部宽度方向前后壁之间水平安装有9根并列的且间距为0.35~0.55m的蒸汽集气管11-5、下部宽度方向前后壁之间水平安装有9根并列的且间距为0.35~0.55m的高温蒸汽进气分布管11-9,蒸汽集气管11-5与干燥炉11-1内顶部之间的距离为0.5~1m,高温蒸汽进气分布管11-9与蒸汽集气管11-5之间的距离为4~6m,高温蒸汽进气分布管11-9与干燥炉11-1内底部之间的距离为0.5~1m,蒸汽集气管11-5的结构为底部开口、顶部为等腰三角形的方管,蒸汽集气管11-5的顶角β为55
°
~75
°
,高温蒸汽进气分布管11-9为蒸汽外管3-15-1内设置有蒸汽内管11-9-2,蒸汽外管11-9-1为底部开口、顶部为等腰三角形的方管,蒸汽外管11-9-1的顶角α为55
°
~75
°
,蒸汽外管11-9-1两侧壁上加工有均匀分布的斜布气孔a,斜布气孔a中心线与水平线之间的夹角为20
°
~70
°
,斜布气孔a的孔径为5~8mm,蒸汽内管11-9-2为圆管,蒸汽内管11-9-2管壁上加工有均匀分布的径向布气孔b,径向布气孔b的开孔率为20%~60%、孔径为5~8mm,干燥炉11-1外侧壁上安装有与3根蒸汽集气管11-5相连通的蒸汽汇集管11-2、与3根高温蒸汽进气分布管11-9相连通的高温蒸汽进气总管11-3,干燥炉11-1的出料口上安装有振动排料阀11-4,高温蒸汽进气总管11-3接收换热器5输出的高温蒸汽后通过高温蒸汽进气分布管11-9输入到干燥炉11-1内,原煤缓冲仓11-11将块煤或籽煤输入干燥炉11-1内,原煤与高温蒸汽进行换热,换热后的蒸汽通过蒸汽集气管11-5输出到蒸汽汇集管11-2,由蒸汽汇集管11-2输出到布袋除尘器10,换热后的干燥块煤或籽煤通过振动排料阀11-4到密封皮带上。
52.在图6、7中,本实施例的热解装置3由干煤缓冲仓3-1、第一蒸汽盘管3-2、第一保温层3-3、进料锁气阀3-4、直立热解炉3-5、荒煤气汇集管3-6、下料管3-7、高温煤气总进气管3-8、冷却煤气总进气管3-9、出料插板阀3-10、推焦机3-11、荒煤气集气管3-12、隔热层3-13、耐磨层3-14、高温煤气进气分布管3-15、耐火材料隔板3-16、冷却煤气进气分布管3-17、刮板机3-18、喷淋器3-19、第一焦缓冲仓3-20、第一锁气阀3-21、第二焦缓冲仓3-22、第二锁气阀3-23连接构成。
53.直立热解炉3-5顶部安装有干煤缓冲仓3-1,干煤缓冲仓3-1用于接收由密封皮带输送器4输送来的干燥块煤或籽煤,干煤缓冲仓3-1底部设置有3个出料口,干煤缓冲仓3-1出料口与直立热解炉3-5通过下料管3-7相连通,下料管3-7为“人”字形管,干煤缓冲仓3-1出料口与下料管3-7之间安装有进料锁气阀3-4,干燥后的原煤通过干煤缓冲仓3-1进入直立热解炉3-5内,干煤缓冲仓3-1外侧壁及下料管3-7上安装有第一蒸汽盘管3-2和第一保温层3-3,用于对原煤进行保温,直立热解炉3-5结构为支架上安装有横截面为矩形的热解炉本体,热解炉本体的长为18m、宽为3~3.5m,热解炉本体的内侧壁上由内向外依次加工有耐磨层3-14、隔热层3-13,直立热解炉3-5的腔体通过耐火材料隔板3-16以每6m为一个单位均匀分割成3个独立的腔体,直立热解炉3-5的每个腔体内上部宽度方向前后壁之间水平安装有10根并列的间距为0.35~0.55m的荒煤气集气管3-12、中部宽度方向前后壁之间水平安装有10根并列的间距为0.35~0.55m的高温煤气进气分布管3-15、下部宽度方向前后壁之
间水平安装有10根并列的间距为0.35~0.55m的冷却煤气进气分布管3-17,荒煤气集气管3-12与直立热解炉3-5内顶部之间的距离为0.5~1m,高温煤气进气分布管3-15与荒煤气集气管3-12之间的距离为5~8m,冷却煤气进气分布管3-17与高温煤气进气分布管3-15之间的距离为1~3m,冷却煤气进气分布管3-17与推焦机3-11之间的距离为0.5~1m,相邻两冷却煤气进气分布管3-17的间距为0.35~0.55m,荒煤气集气管3-12的结构与蒸汽集气管11-5的结构相同,高温煤气进气分布管3-15和冷却煤气进气分布管3-17的结构与高温蒸汽进气分布管11-9的结构相同,直立热解炉3-5外侧壁上固定安装有与3根荒煤气集气管3-12相连通的荒煤气汇集管3-6、与高温煤气进气分布管3-15相连通的高温煤气总进气管3-8、与冷却煤气进气分布管3-17相连通的冷却煤气总进气管3-9,荒煤气集气管3-12收集直立热解炉3-5内由煤热解产生的荒煤气后输出到荒煤气汇集管3-6,再由荒煤气汇集管3-6输送到喷淋冷却分离器6,高温煤气总进气管3-8与旋风除尘器2的气相出口相连通,旋风除尘器2输出的高温煤气通过高温煤气总进气管3-8进入到高温煤气进气分布管3-15,再由高温煤气进气分布管3-15输入到直立热解炉3-5内,喷淋冷却分离器6输出的部分冷却煤气由冷却煤气总进气管3-9输入到冷却煤气进气分布管3-17,再由冷却煤气进气分布管3-17输出到直立热解炉3-5内,直立热解炉3-5底部固定安装有推焦机3-11,推焦机3-11下方直立热解炉3-5的每个腔体对应一个出料口且出料口上均安装有出料插板阀3-10,推焦机3-11用于将煤热解产生的半焦推入到热解炉的出料口,直立热解炉3-5的出料口正下方安装有刮板机3-18,刮板机3-18的另一端出料口正下方安装有第一焦缓冲仓3-20,打开出料插板阀3-10半焦输出到刮板机3-18,刮板机3-18将直立热解炉3-5排出的半焦输送到第一焦缓冲仓3-20,第一焦缓冲仓3-20内顶部安装有喷淋器3-19,喷淋器3-19用于对半焦进行降温,第一焦缓冲仓3-20底部出口与第二焦缓冲仓3-22顶部入口通过第一锁气阀3-21相连通,第二焦缓冲仓3-22底部出口上安装有第二锁气阀3-23,最终的产品半焦通过第二锁气阀3-23排出。
54.采用上述系统实现煤气化热解耦合的方法,具体由下述步骤组成:
55.s1.煤气化
56.开工时,将煤输入气化炉1气化,气化煤气经与调温氮气混合为温度为850~1000℃的混合煤气,经旋风除尘器2除尘后减压为常压,一部分输入直立热解炉3-5,另一部分输入到换热器5;灰渣从气化炉1底部排出。其中,气化炉1为气流床气化炉时,煤经磨碎机磨碎到200目的煤粉,由蒸汽和氧气吹入气化炉1气化,气化温度为1300~1600℃,气化压力小于0.5mpa,气化炉1采用液态排渣,灰渣从气化炉1底部排出;气化炉1为流化床气化炉时,煤采用10cm以下粒煤,用氮气吹入气化炉1,由蒸汽和氧气流化并气化,气化温度为950~1050℃,气化压力小于0.5mpa,气化炉1采用固态排渣;气化炉1为固定床气化炉时,煤采用8~30cm煤块,由顶部装入气化炉1,气化温度为950~1050℃,气化压力小于0.5mpa,气化炉1采用液态排渣。
57.s2.气化煤气与蒸汽换热
58.换热器5内外部输入的温度为130~150℃的干燥蒸汽与温度为850~1000℃的混合煤气换热后变为温度为350~380℃、压力为常压的高温过热蒸汽并通过管道输入到干燥装置11的高温蒸汽进气总管11-3,由高温蒸汽进气分布管11-9输入到干燥炉11-1内,换热后的煤气作为产品输出;
59.s3.块煤或籽煤干燥
60.含水为8%~18%、温度为常温的块煤或籽煤通过皮带送入干煤缓冲仓,而后进入干燥炉11-1内自上而下移动,同时,输入干燥炉11-1内的高温过热蒸汽进入煤层自下而上流动,块煤或籽煤与高温过热蒸汽逆向接触换热,使块煤或籽煤干燥并升温至150~180℃,干燥并升温后的块煤或籽煤继续下移经振动排料阀11-4排出,由密封皮带输送器4输送到干煤缓冲仓3-1;与干燥块煤或籽煤换热后的温度为130~150℃、压力为-8~-1kpa的微负压蒸汽通过蒸汽集气管11-5输出到蒸汽汇集管11-2,由蒸汽汇集管11-2输出到布袋除尘器10,布袋除尘器10除尘后的气体经引风机9进入空冷器8冷却,再经蒸汽气液分离器7分离,大部分蒸汽以凝结水排出,少部分不凝蒸汽作为换热蒸汽输入到换热器5循环利用,布袋除尘器10内的煤粉从底部出料口排出;
61.s4.块煤或籽煤热解
62.干煤缓冲仓3-1内温度为150~180℃的块煤或籽煤下料到直立热解炉3-5内,并在直立热解炉3-5内自上而下移动,同时旋风除尘器2输出的减压为常压、温度为850~1000℃的混合煤气由高温煤气总进气管3-8和高温煤气进气分布管3-15进入到直立热解炉3-5内自下而上穿过热解段煤层,与150~180℃的块煤或籽煤逆向换热,块煤或籽煤吸收热量升温到500~700℃开始热解,热解后的荒煤气温度降为160~200℃进入荒煤气集气管3-12,经荒煤气汇集管3-6输出到喷淋冷却分离器6,由喷淋冷却分离器6快速分离为煤焦油、水和煤气,煤焦油和水导出,煤气分为三部分,一部分作为冷却煤气由高温煤气总进气管3-8和高温煤气进气分布管3-15进入直立热解炉3-5循环利用、另一部分替换开工时的调温氮气经调温煤气管道与气化炉1输出的气化煤气混合后进入旋风除尘器2、剩余部分作为产品煤气导出;
63.s5.半焦的冷却及产品半焦输出
64.直立热解炉3-5内热解形成的半焦继续向下移动进入冷却段与冷却煤气逆流换热,冷却煤气被加热到400~550℃后与由高温煤气总进气管3-8和高温煤气进气分布管3-15进入的温度为850~1000℃的混合煤气再次混合为550~750℃煤气自下而上穿过热解段煤层,与150~180℃的块煤或籽煤逆向换热,半焦被冷却至60~80℃后经推焦机3-11推入到直立热解炉3-5的出料口,经直立热解炉3-5的出料口排出到刮板机3-18,关闭第一锁气阀3-21,刮板机3-18将半焦刮入到第一焦缓冲仓3-20进行喷淋降温,汽提半焦并阻断煤气,待第一焦缓冲仓3-20内的半焦量达到第一焦缓冲仓3-20体积的1/2以上时,关闭第二锁气阀3-23,打开第一锁气阀3-21,让第一焦缓冲仓3-20的半焦卸到第二焦缓冲仓3-22内,然后关闭第一锁气阀3-21,打开第二锁气阀3-23卸料半焦作为产品送出。
65.实施例2
66.在本实施例中,直立热解炉3-5的结构为支架上安装有横截面为矩形的热解炉本体,热解炉本体的长为6m、宽为3~3.5m,直立热解炉3-5的腔体为一个腔体,直立热解炉3-5的腔体内上部宽度方向前后壁之间水平安装有8根并列的间距为0.35~0.55m的荒煤气集气管3-12、中部宽度方向前后壁之间水平安装有8根并列的间距为0.35~0.55m的高温煤气进气分布3-15、下部宽度方向前后壁之间水平安装有8根并列的间距为0.35~0.55m的冷却煤气进气分布管3-17。其他零部件及零部件的连接关系与实施例1相同。采用该系统实现煤气化热解耦合的方法也与实施例1相同。
67.实施例3
68.在本实施例中,直立热解炉3-5的结构为支架上安装有横截面为矩形的热解炉本体,热解炉本体的长为24m、宽为3~3.5m,直立热解炉3-5的腔体通过耐火材料隔板3-16以每6m为一个单位均匀分割成4个独立的腔体,直立热解炉3-5的每个腔体内上部宽度方向前后壁之间水平安装有9根并列的间距为0.35~0.55m的荒煤气集气管3-12、中部宽度方向前后壁之间水平安装有9根并列的间距为0.35~0.55m的高温煤气进气分布3-15、下部宽度方向前后壁之间水平安装有9根并列的间距为0.35~0.55m的冷却煤气进气分布管3-17。其他零部件及零部件的连接关系与实施例1相同。采用该系统实现煤气化热解耦合的方法也与实施例1相同。
再多了解一些
本文用于企业家、创业者技术爱好者查询,结果仅供参考。