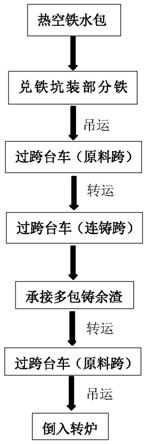
1.本发明涉及钢铁冶金节能环保领域,特别涉及一种热态铸余渣直接返转炉的方法。
背景技术:
2.钢包浇钢完毕时包内铸余渣的温度仍高达1400~1600℃,渣与钢水尚处于相对分层状态,残钢沉于包底。目前,绝大多数的钢铁企业都用渣包来收集铸余渣,然后外运到渣处理车间进行后续的“固废”处理。在铸余渣从钢包内倒出时钢水和渣很容易搅混,在冷态渣包内快速冷却,容易形成渣包形状。
3.为避免大渣砣的产生和减轻后续处理过程中的劳动强度和污染程度,一些钢厂开发并实施了格栅工艺:利用格栅的隔断作用将钢(铁)渣分隔成网格尺寸的小块。该工艺避免了大块渣钢砣的产生,提高了铸余渣的处理效率,同时提高了金属回收率,减少氧割、落锤造成的环境污染问题,受到一些钢厂的青睐。目前,除中国宝钢和少数钢厂采用格栅法处理铸余渣外,国内外大部分钢厂仍然采用原始的热泼-落锤工艺,不仅处理流程长、污染大,而且渣钢回收效率差、品位低。
4.为了充分利用热态铸余渣的余热和有效化学成分,国内许多企业都进行过直接将碳钢铸余渣返精炼工序的工业试验:将连铸浇注后的铸余渣连同钢包直接到转炉下接钢,然后进入lf炉进行精炼工序。试验显示:循环4次(1-2次效果较好)以内的精炼渣仍然具有脱硫能力,每包钢在多回收1.1吨钢水的基础上还可以降低石灰、萤石、铝矾土等熔剂的消耗,缩短精炼处理周期。存在的问题是,现代企业冶炼钢种的转换节奏较快,不同钢种及相应铸余渣的成分差别较大,不能混用,对热态铸余渣在精炼工序内的循环利用带来很大限制。同时,该方法只能减少铸余渣的排放量,并不能从根本上解决铸余渣的处理和出路问题。
5.针对现有处理铸余渣的工艺和技术都存在明显的缺陷和不足,本发明专利提出了热态铸余渣直接返转炉的工艺方法。通过铁水包内铁水与铸余渣的混兑,将铸余渣倒入到转炉内,回收其中的钢水。
6.现有铸余渣利用技术主要有以下几种处理工艺:
7.1、格栅法:为解决大块渣钢坨问题,如中国专利cn200510047315.2、cn200610025562.7及cn01201699.3提出了在渣罐中放置格栅的方法:将钢渣罐的空间分成多个部分,在格栅的隔断作用下,热态铸余渣倒入渣罐后被自行分隔成格栅尺寸的小块,冷却后的小渣砣相对容易破碎,提高了渣处理效率。该工艺解决了大块渣钢砣的问题,但铸余渣在红热状态下被泼地冷却,污染大,需要大量的混凝土格栅,费用高昂,另外处理过程渣钢无法分离,给后续利用带来影响。
8.2、滚筒法:如中国专利cn200810035081.3公开了一种滚筒法处理热态钢包渣/铸余渣的工艺方法。热态铸余渣由漏斗进入滚筒落渣区被钢球冷却,钢水和渣被钢球迅速夺取热量塑化、固化后被滚动的钢球带入水冷区,熔渣、钢球同时被水冷却,然后经由滚筒的
格栅式箅条排到外筒体,熔渣在外筒体内被水再冷却,最后排出。在高速滚动的钢球作用下,铸余渣中的渣和残钢得到很好的剥离。
9.3、热态循环:如中国专利cn201210500164.1、cn200610012345.4公开了热态铸余渣循环利用的方法:铸钢完毕,将钢包内浇余的热态钢渣倒入空钢包内,将盛有浇余热态钢渣的钢包运至转炉处,向其内出钢,然后实施钢水精炼、浇注,循环利用。该方法可充分利用热态钢渣的硫容量和强还原性,迅速调整渣系组成,形成低熔点渣系,改善炉渣流动性,同时缩短了高碱度炉渣的成渣时间,提高精炼效率,降低电耗和冷渣料消耗,降低生产成本。
10.4、热态分离:如中国专利cn200710037196.1和cn200720066237.5公开了一种铸余渣和钢水的分离方法及装置,通过将钢包中的铸余渣和钢水一起倒入专用渣包内,在适当补热保温的情况下使铸余渣和钢水静止分层。等到渣钢分层充分后,开启渣包下部的滑动水口排放钢水,包内剩余的铸余渣通过倾倒或扒渣方式进行后续处理。该方法使铸余渣和钢水热态分离,简单方便,清洁无污染,不但利用了钢水自身的热量,避免了能量浪费,同时防止铸余渣和钢水冷却结砣,另外还能够使铸余渣与钢水快速分离,可以分别进行单独回收,提高生产效率,增加经济效益。
11.还有如德国专利de19519284公开了一种处理铸余渣的方法,其是仿照连铸机的冷却原理将热态铸余渣直接倒入一简易结晶器中,使铸余渣快速冷却并排放,由于铸余渣为渣钢混合物,不但含有钢水还带有相当数量的熔渣,而熔渣的导热性很差,能否被结晶器快速冷却,结果不得而知,该专利未见实际投用的报道。
12.通过上述专利文献的检索分析可知,到目前为止还没有非常完善、令人满意的铸余渣处理工艺和方法。
13.常规的热泼工艺占地大、能耗高、污染严重、金属回收率低;格栅工艺仅仅避免了大渣砣的生成,降低了对大渣砣冷却、破碎消耗和由此产生的污染问题,但渣罐消耗没有减少,格栅成本额外增加;滚筒处理工艺环保效果好,但进料口粘钢严重、冷钢清理频繁,劳动强度大,工艺不完善;热态循环工艺能充分利用、回收铸余渣的热能和金属,处理成本最低,但大量的生产试验表明:鉴于硫容量的需求,铸余渣最多只能循环4次,以1-2次为主,另外,随着品种钢冶炼转换节奏加快,铸余渣的热态循环受到极大限制,该工艺的使用效果和铸余渣减排量大打折扣,铸余渣还需要选择适当的终端处理工艺。
技术实现要素:
14.本发明的目的在于提供一种热态铸余渣直接返转炉的方法,在回收钢水的同时,将铸余渣转化为转炉渣,后续采用清洁高效的滚筒工艺进行处理,具有显著的经济效益和环保效益。
15.为达到上述目的,本发明的技术方案是:
16.一种热态铸余渣直接返转炉的方法,其包括如下步骤:
17.1)铁水包准备
18.采用刚向转炉倒完铁水的铁水包作为承接铸余渣的铁水包;
19.2)承接铁水
20.将准备好的铁水包吊运到原料跨的受铁坑,此时,铁水包内壁温度在700℃以上,向铁水包倒入铁水,铁水装入量为铁水包容量5~15%体积比,铁水温度要求1200~1550
℃;
21.3)铁水包转运
22.装好部分铁水后,将铁水包迅速吊运到过跨台车上,然后将台车从原料跨开到连铸跨的铸余渣接收工位,等待接收铸余渣;铁水包从受铁坑兑完铁水转运到铸余渣接收工位,转运时间控制在50分钟以内;
23.4)接收铸余渣
24.一台连铸机钢水浇注完毕后,将钢包吊运到连铸跨的铁水包上方,把铸余渣迅速倒入铁水包内;当另一台连铸机浇注完毕后,同样将铸余渣倒入铁水包;期间,铁水包等待时间为控制在3.5小时以内,铸余渣接收量为铁水包容量的2~10%体积比;
25.5)铸余渣转运
26.铁水包接收完铸余渣后,将铁水包通过过跨台车由连铸跨的铸余渣接收工位运送到原料跨的铁水包工位;
27.6)铸余渣返转炉
28.用行车将铁水包吊运到转炉平台,将其中的铁水和铸余渣混合物倒入转炉,整个操作时间控制在30分钟以内。
29.优选的,步骤2)从铁水包向转炉倒完铁水到装完部分铁水的时间控制在45分钟以内。
30.优选的,步骤3)铁水包从受铁坑兑完铁水转运到铸余渣接收工位,转运时间控制在4~30分钟。
31.优选的,步骤4)接收铸余渣过程中,钢水浇注完毕后,将钢包吊运到连铸跨的铁水包上方,在5分钟以内完成将铸余渣倒入铁水包内。
32.优选的,步骤5)铁水包接收完铸余渣后,在40分钟以内将铁水包通过过跨台车由连铸跨的铸余渣接收工位运送到原料跨的铁水包工位。
33.步骤6)铸余渣返回转炉后,由于铁水包内壁会粘有少量的炉渣,不宜直接进入下一次铸余渣返转炉流程。
34.步骤6)铸余渣返回转炉后,经过转炉吹炼过程,铸余渣转化为转炉渣,采用滚筒工艺进行处理。
35.在传统转炉炼钢工艺中,转炉出钢后,进行加废钢操作,然后倒入脱硫铁水进行冶炼,倒完铁水后铁水包吊运倒铁水接收工位受铁,进入下一个循环流程。在本发明技术,炼钢厂必须配备从原料跨到连铸跨的过跨台车,可使台车上的铁水包在两个跨之间来回移动。
36.在本发明所述热态铸余渣直接返转炉方法中:
37.铁水包必须采用刚倒完铁水的铁水包,这样铁水包内的耐材蓄热充足,以减少倒入的铁水和铸余渣的温降。对于新烘烤过的铁水包,不得用于承接铸余渣。
38.承接铁水,将准备好的铁水包吊运到原料跨的受铁坑,此时,铁水包内壁温度在700℃以上,从铁水包向转炉倒完铁水到兑完部分铁水的时间控制在45分钟以内。
39.铁水装入量为铁水包容量5~15%体积比;铁水装入量的确定考虑到铸余渣保温需要和钢种对硫含量的要求,装入铁水量太少,不能满足铸余渣保温的需要,铁水装入量太多,由于这部分铁水不经脱硫直接入转炉,对钢水硫含量影响较大。
40.铁水温度要求1200-1550℃,铁水温度过低时,不能预装铁水去接收铸余渣。
41.铁水包转运,装好部分铁水后,将铁水包迅速吊运到过跨台车上,然后将台车从原料跨开到连铸跨的铸余渣接收工位,等待接收铸余渣。铁水包从受铁坑兑完铁水转运到铸余渣接收工位,所需时间控制在50分钟以内。
42.接收铸余渣,钢水浇注完毕后,将钢包吊运到连铸跨的铁水包上方,把铸余渣迅速倒入铁水包内,5分钟内完成倾倒作业;当另一台连铸机浇注完毕后,同样将铸余渣转入铁水包;当又一钢包浇注完毕,同样转入铁水包。期间,铁水包等待时间为3.5小时以内,铸余渣接收量为铁水包容量2~10%体积比。
43.铸余渣转运,铁水包接收完最后一包铸余渣后,40分钟内将铁水包通过过跨台车由连铸跨的铸余渣接收工位运送到原料跨的铁水包工位。
44.铸余渣返转炉,用行车将铁水包中的铁水和铸余渣混合物倒入转炉,整个操作时间控制在30分钟以内。
45.铸余渣热态返生产最大的难点在于温降引起的粘包和对生产现场物流调度的影响。中国专利cn201210500164.1、cn200610012345.4公开了热态铸余渣循环利用的方法:铸钢完毕,将钢包内浇余的热态钢渣倒入空钢包内,将盛有浇余热态钢渣的钢包运至转炉处,向其内出钢,然后实施钢水精炼、浇注,循环利用。该方法只适用于成分相同或相近的钢种,并且要提前安排好转炉出钢量,使钢包具有承接铸余渣的空间。同时该专利技术只适合低氧化性铸余渣,难以实现铸余渣大规模返生产。
46.本发明的创新在于:
47.(1)铁水包通过预装部分铁水承接多包铸余渣,解决了由于温降引起的粘包问题。
48.采用铁水包预装部分铁水承接铸余渣,主要是防止铸余渣返生产过程中金属熔体的凝固。高炉铁水碳含量一般在4.5%左右,熔点约1150℃,而铸余渣中钢水碳含量一般小于0.2%,熔点约1500℃,当铁水包内没有铁水时,由于铸余渣中钢水的过热度较小,当铸余渣倒入铁水包时,钢水很快就会凝固,返生产工艺无法进行;而当铁水包内装有部分铁水时,承接铸余渣时,由于铸余渣中的钢水量较少,铁水碳含量稍有上升,铁水熔点也稍有升高。重包承接铸余渣,本质上是将钢水转变为铁水,实现多包合罐,以尽量减少返回炉次,减少对物流和调度的影响。参见图1所示铁水碳含量与熔点的关系图。
49.(2)由于一次可以返回多包铸余渣,大大减轻了对现场物流和调度的影响,可实现铸余渣大规模返生产。
50.(3)在整个铸余渣返转炉过程中,通过预装铁水、铁水包转运、铸余渣承接和倒入转炉等环节的紧凑衔接,实现铸余渣的安全顺利返转炉。
51.本发明的有益效果:
52.1.本发明方法完全回收了铸余渣中的剩余钢水,提高了炼钢过程的金属回收率,显著提高经济效益。
53.2.铸余渣返回转炉后,铸余渣的冶金功能得到进一步发挥,节约炼钢熔剂,降低了生产成本。
54.3.现有较为先进的铸余渣格栅处理工艺,吨渣处理成本在150~300元;本发明技术的运用,将铸余渣转变为转炉渣,采用滚筒工艺,吨转炉渣的处理成本为15~35元。因此本发明技术的实施,不仅解决了现有铸余渣处理过程中的流程长和污染严重的问题,实现
了炼钢过程的清洁生产,而且大大降低了钢渣处理成本。
55.热态铸余渣直接返转炉的上述效果,可促进炼钢过程的节能减排,提高产品竞争力。
附图说明
56.图1为铁水接铸余渣铁水碳含量变化示意图;
57.图2为本发明所述热态铸余渣直接返转炉方法的工艺流程图;
58.图3为本发明所述热态铸余渣直接返转炉方法实施例的工艺布置图。
具体实施方式
59.参见图2,本发明所述的热态铸余渣直接返转炉的方法,其包括如下步骤:
60.1)铁水包准备
61.采用刚向转炉倒完铁水的铁水包作为承接铸余渣的铁水包;
62.2)承接铁水
63.将准备好的铁水包吊运到原料跨的受铁坑,此时,铁水包内壁温度在700℃以上,向铁水包倒入铁水,铁水装入量为铁水包容量5~15%体积比,铁水温度要求1200~1550℃;
64.3)铁水包转运
65.装好部分铁水后,将铁水包迅速吊运到过跨台车上,然后将台车从原料跨开到连铸跨的铸余渣接收工位,等待接收铸余渣;铁水包从受铁坑兑完铁水转运到铸余渣接收工位,转运时间控制在50分钟以内;
66.4)接收铸余渣
67.一台连铸机钢水浇注完毕后,将钢包吊运到连铸跨的铁水包上方,把铸余渣迅速倒入铁水包内;当另一台连铸机浇注完毕后,同样将铸余渣倒入铁水包;期间,铁水包等待时间为控制在3.5小时以内,铸余渣接收量为铁水包容量的2~10%体积比;
68.5)铸余渣转运
69.铁水包接收完铸余渣后,将铁水包通过过跨台车由连铸跨的铸余渣接收工位运送到原料跨的铁水包工位;
70.6)铸余渣返转炉
71.用行车将铁水包吊运到转炉平台,将其中的铁水和铸余渣混合物倒入转炉,整个操作时间控制在30分钟以内。
72.优选的,步骤2)从铁水包向转炉倒完铁水到装完部分铁水的时间控制在45分钟以内。
73.优选的,步骤3)铁水包从受铁坑兑完铁水转运到铸余渣接收工位,转运时间控制在4~30分钟。
74.优选的,步骤4)接收铸余渣过程中,钢水浇注完毕后,将钢包吊运到连铸跨的铁水包上方,在5分钟以内完成将铸余渣倒入铁水包内。
75.优选的,步骤5)铁水包接收完铸余渣后,在40分钟以内将铁水包通过过跨台车由连铸跨的铸余渣接收工位运送到原料跨的铁水包工位。
76.步骤6)铸余渣返回转炉后,由于铁水包内壁会粘有少量的炉渣,不宜直接进入下一次铸余渣返转炉流程。
77.步骤6)铸余渣返回转炉后,经过转炉吹炼过程,铸余渣转化为转炉渣,采用滚筒工艺进行处理。
78.实施例1
79.参见图3,其所示为本发明实施例的一炼钢厂工艺布置图,包括三台连铸机1、2、3和三台转炉8、9、10,过跨台车5可在轨道上在连铸跨和原料跨之间来回移动。
80.对于刚将铁水倒入转炉的铁水包,放置到原料跨内的受铁坑7装入部分铁水,将铁水包迅速吊运到过跨台车5上,然后将过跨台车5从原料跨开到连铸跨的铸余渣接收工位4,等待接收铸余渣,接收完最后一包铸余渣后,将铁水包通过过跨台车5由连铸跨的铸余渣接收工位4运送到原料跨的铁水包工位6,用行车将铁水包中的铁水和铸余渣混合物倒入转炉8、9、10。
81.以年产800万吨的炼钢厂(3座250吨转炉)为例:
82.250吨的铁水包向转炉内装入铁水后,将铁水包吊运到受铁坑,用时16分钟;此时测得铁水包内壁温度为924℃,鱼雷罐车内铁水温度为1280℃,由鱼雷罐车向铁水包倒入约30吨铁水;然后将铁水包吊运到过跨台车上,再将铁水包运送到连铸跨的铸余渣接收工位,耗时18分钟。
83.铁水包在台车上等待6分钟后,接收第一包铸余渣,重量为5.1吨,铸余渣倾倒过程为2分钟;又过了40分钟,接收第二包铸余渣,重量为5.5吨,铸余渣倾倒过程为3分钟;又过了30分钟,接收第三包铸余渣,重量为4.5吨,铸余渣倾倒过程为2.5分钟;又过了25分钟,接收第四包铸余渣,重量为6.1吨,铸余渣倾倒过程为1.5分钟;这样在110分钟内,共接收4包铸余渣,合计21.2吨。
84.将装有铁水和铸余渣的铁水包13分钟内由连铸跨转运到原料跨;再由行车吊运倒入已加入废钢的转炉,废钢加入量为25吨,从铁水包吊运并将铸余渣混合物倒入转炉时间为25分钟;然后再向转炉倒入175吨脱硫铁水,进行转炉吹炼,转炉渣采用滚筒工艺进行处理。
85.本次操作共实现铸余渣返生产21.2吨,直接经济效益约14840元。
86.对于年产800万吨钢水的炼钢厂,每年产生铸余渣约16万吨,铸余渣直接返转炉,直接经济效益约10880万元。
87.实施例2
88.以年产1000万吨的炼钢厂(3座350吨转炉)为例:
89.350吨的铁水包向转炉内装入铁水后,将铁水包吊运到受铁坑,用时42分钟;此时测得铁水包内壁温度为715℃,鱼雷罐车内铁水温度为1540℃,由鱼雷罐车向铁水包倒入约19吨铁水;然后将铁水包吊运到过跨台车上,再将铁水包运送到连铸跨的铸余渣接收工位,耗时48分钟。
90.铁水包在台车上等待18分钟后,接收第一包铸余渣,重量为7.1吨,铸余渣倾倒过程为2分钟;又过了12分钟,接收第二包铸余渣,重量为6.3吨,铸余渣倾倒过程为3分钟;这样在35分钟内,共接收2包铸余渣,合计13.4吨。
91.将装有铁水和铸余渣的铁水包38分钟内由连铸跨转运到原料跨;再由行车吊运倒
入已加入废钢的转炉,废钢加入量为34吨,从铁水包吊运并将铸余渣混合物倒入转炉时间为6分钟;然后再向转炉倒入284吨脱硫铁水,进行转炉吹炼,转炉渣采用滚筒工艺进行处理。
92.本次操作共实现铸余渣返生产13.4吨,直接经济效益约10981元。
93.对于年产1000万吨钢水的炼钢厂,每年产生铸余渣约20万吨,铸余渣直接返转炉,直接经济效益约16390万元。
94.实施例3
95.以年产300万吨的炼钢厂(3座120吨转炉)为例:
96.120吨的铁水包向转炉内装入铁水后,将铁水包吊运到受铁坑,用时5分钟;此时测得铁水包内壁温度为1200℃,鱼雷罐车内铁水温度为1210℃,由鱼雷罐车向铁水包倒入约17吨铁水;然后将铁水包吊运到过跨台车上,再将铁水包运送到连铸跨的铸余渣接收工位,耗时10分钟。
97.铁水包在台车上等待35分钟后,接收第一包铸余渣,重量为2.0吨,铸余渣倾倒过程为1分钟;又过了40分钟,接收第二包铸余渣,重量为2.5吨,铸余渣倾倒过程为3.5分钟;又过了30分钟,接收第三包铸余渣,重量为2.2吨,铸余渣倾倒过程为5分钟;又过了38分钟,接收第四包铸余渣,重量为2.1吨,铸余渣倾倒过程为1.5分钟;又过了48分钟,接收第五包铸余渣,重量为2.2吨,铸余渣倾倒过程为3分钟;这样在205分钟内,共接收4包铸余渣,合计11吨。
98.将装有铁水和铸余渣的铁水包5分钟内由连铸跨转运到原料跨;再由行车吊运倒入已加入废钢的转炉,废钢加入量为13吨,从铁水包吊运并将铸余渣混合物倒入转炉时间为29分钟;然后再向转炉倒入96吨脱硫铁水,进行转炉吹炼,转炉渣采用滚筒工艺进行处理。
99.本次操作共实现铸余渣返生产11吨,直接经济效益约9014元。
100.对于年产300万吨钢水的炼钢厂,每年产生铸余渣约6万吨,铸余渣直接返转炉,直接经济效益约4917万元。
101.综上所述,本发明将钢包浇注完毕后的铸余渣收集到装有部分铁水的铁水包中,将铁水和铸余渣混合物直接倒入转炉,补足铁水后进行转炉炼钢。通过本发明方法,在回收铸余渣中钢水的同时,将铸余渣转化为转炉渣,不但进一步发挥了铸余渣的冶金功能,也使炉渣更容易处理,同时,减轻现有铸余渣处理过程环境污染,达到炼钢工艺节能减排的综合效果。
再多了解一些
本文用于企业家、创业者技术爱好者查询,结果仅供参考。