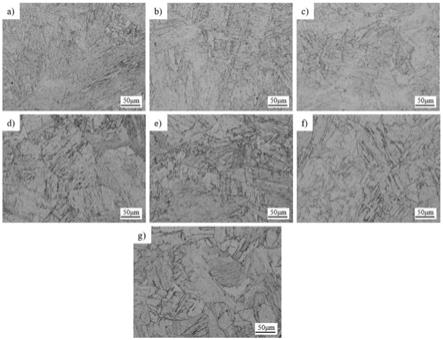
1.本发明涉及模具钢技术领域,尤其涉及一种高强度高热导率钢材料及热处理工艺、应用。
背景技术:
2.增材制造又称3d打印,是一种通过将材料从下往上逐步堆积来制造零部件的快速材料成型技术。增材制造技术作为制造业发展新方向的代表,已经被世界上较多的国家作为本国制造业长期发展战略中的关键技术之一。近几年来,由于增材制造技术的快速发展,已经成为了制造行业和材料加工领域的前沿研究热点之一,在军工、汽车、航空航天、模具、医疗、建筑德国领域的应用愈发广泛。此外,用于增材制造的材料也越来越多,从最初的非金属、钢、钛合金和铝合金发展到陶瓷材料、高熵合金、高温合金以及复合材料等。
3.选区激光熔化(selective lasermelting,slm)技术作为增材制造技术的重要组成部分,其原理是通过使用高能量的激光束按照预先设定的扫描策略逐层熔化粉末床上特定位置的粉末来制造出所需的零部件。因此,slm技术可以突破传统加工方法的限制,实现了快速自由制造零部件的目的,且成型出的零部件不进行后续处理的情况下即可达到几乎完全致密,且成型件由于组织分布均匀、晶粒细小的特点力学性能可与铸锻件相当,在制造复杂结构零件方面具备极大优势,这使得slm技术成为了发展潜力极为巨大的快速成型(rapid prototyping,rp)技术之一。
4.模具被称作“万业之母”,在电子、汽车、电机、电器、仪表、家电和通讯等领域应用广泛,模具制造技术的水平直接关系到一个国家研发和生产制造工业产品的能力。随着科学技术的快速发展和人们生活水平的日益提高,社会各群体对模具制造的产品提出了更高的要求,各模具制造厂商之间的竞争也日益激烈,这就更加加快了模具制造方面的发展速度,传统加工方法制造出的模具已经无法满足模具制造厂家对优质、高效、长寿模具的需求,随形冷却模具取代普通模具已成为必然。然而使用传统的加工方法制造随性冷却水道模具往往存在工序多、成本高、成型精度低、成本高甚至难加工的问题,而slm技术由于自身成型方式的原因而具备传统加工方法所不具备的特点,可以制备出形状结构复杂的随形冷却水道模具,这意味着slm技术制备出的模具能够具备更均匀的散热能力,零件成型周期将会明显缩短,产生可观的社会经济效益。目前市场上应用于slm模具制备的材料主要是马氏体时效钢和马氏体时效不锈钢,但是这些钢为了获得2gpa的超高强度而添加的大量的合金元素,这就导致了这些钢的热导率普遍低于20w/(mk),这代表着模具的生产效率将会受到极大的限制。目前市场急需开发出一种高强度高导热率的钢,以提高模具的生产效率,实现生产效率的提升,并使其能适用于slm成型。
5.早在20世纪60年代,由于生产生活的需要,人们开始对铸铁的热导率进行研究,但是高热导率模具钢的兴起却是在近几年,作为一种新型的高性能模具钢种,高热导率模具钢的最大特点就是其高于传统模具钢的热传导性能,能够显著提高模具开模的效率并且减少产生热裂现象的概率。国外的高热导率模具钢主要是日本大同公司的dha-thermo和西班
牙rovalma公司的htcs系列钢,htcs系列中以htcs-130应用最为广泛,国内的高热导率模具钢则有上海大学研发的sdcm钢种。表1是通过文献调研得到的几种高热导率模具钢的化学成分组成。
6.表1几种高热导率模具钢和h13钢化学成分(wt%)
[0007][0008]
对于合金热导率,学术界普遍认为合金元素添加量越多,合金的热导率越小,一般对于同种基体合金而言,存在以下热导率大小关系:纯金属热导率》中低合金热导率》高合金热导率,因为合金元素的添加将会增加合金内部的缺陷,而缺陷的增加将使电子和声子的平均自由程减小,因而热导率下降。在传统加工领域,典型的高导热模具钢已经研发出了htcs系列、sdcm系列、dha-thermo系列模具钢,这些钢均采用了低合金化的设计思路,然而这些钢均为含碳量0.4%(wt%)左右的中碳钢,钢材的强化方式为碳化物强化,组织为板条马氏体与针状马氏体的混合组织,使得其韧性较低,材料的slm成型性不良。
技术实现要素:
[0009]
基于背景技术存在的技术问题,本发明提出了一种高强度高热导率钢材料及热处理工艺、应用,本发明强韧性好、热导率高,可用于高热导率模具、slm成型。
[0010]
本发明提出的一种高强度高热导率钢材料,其成分按重量百分比计包括:c 0.05-0.1%,ni 2.5-3.4%,al 0.3-0.8%,cu 1-1.3%,mn 1-1.5%,si 0-0.1%,mo 0.45-1.5%,cr 0-0.33%,v 0-0.1%,余量为fe。
[0011]
优选地,其成分按重量百分比计包括:c 0.05%,ni 3.4%,al 0.8%,cu 1%,mn 1.5%,si 0.1%,mo 0.45%,cr 0.33%,余量为fe。
[0012]
优选地,其成分按重量百分比计包括:c 0.05%,ni 3.4%,al 0.3%,cu 1.3%,mn 1%,si 0.1%,mo 0.6%,余量为fe。
[0013]
优选地,其成分按重量百分比计包括:c 0.05%,ni 2.5%,al 0.3%,cu 1%,mn 1%,si 0.1%,mo 1.5%,v 0.1%,余量为fe。
[0014]
考虑到现有高热导率模具钢材料,其过高的碳含量将会恶化合金的塑韧性,会降低合金产品的性能,还会使材料无法实现选区激光融化成型的问题,发明人采用低碳化设计来改善合金的韧性问题,并将si含量、cr含量控制在较低水平;但是低碳会降低合金的强度和硬度,发明人采用第二相强化的方法,加入ni、al、cu,通过ni、al、cu三者的复合作用对合金进行强化;另外控制各元素的含量使其处于低碳低合金水平,使得合金具有较高的热导率,满足高热导率模具钢的要求,并且相较于目前slm工艺使用的金属粉末不到20w/(m
·
k)的热导率,本发明所述合金的热导率均高于20w/(m
·
k),都达到了提高热导率的目的。
[0015]
当采用浇铸方法制备模具钢时,发明人对上述高强度高热导率钢材料的铸件(未经热处理的铸件)的性能进行性能检测发现:本发明所述合金的铸态组织均为板条马氏体与铁素体的混合组织,奥氏体体积分数要低于5%,且存在轻微的晶间偏析;铸态抗拉强度
均在850-950mpa范围内,属于高强钢,由于组织为塑韧性较好的板条马氏体和铁素体的混合组织而具备良好的塑性,延伸率在15-20%;其100℃条件下的热导率为29.9、29.5、31.1(w/m
·
k),其热导率的提升率符合3d打印高热导率模具钢设计初衷;然而其铸态硬度均达不到模具使用的要求。因此需要对铸件进行热处理,以获得性能更好的模具钢。
[0016]
由于所述高强度高热导率钢材料的铸态组织为铁素体与马氏体的混合组织,而铁素体的存在势必会导致高强度高热导率钢材料的强度和硬度降低,因此发明人设计对铸件进行固溶处理,消除铁素体组织以得到全马氏体组织,然而固溶处理后的铸件由于快速冷却的原因,材料内部将会产生极大的内应力,当铸件受到外力作用时,内应力汇合在一起形成应力集中,使材料塑性变差,因此发明人设计对固溶处理后的铸件进行时效处理,在析出第二相的同时消除内应力。发明人采用固溶 时效的热处理方式,对热处理的各个参数筛选,进一步提高上述高强度高热导率钢材料的性能,使其满足模具钢要求,提高模具钢性能。
[0017]
最终本发明提出了上述高强度高热导率钢材料的热处理工艺,包括如下步骤:
[0018]
s1、取各原料熔炼浇铸得到成分配比与上述高强度高热导率钢材料相同的铸件;
[0019]
s2、将铸件进行固溶处理,淬火,再于475-525℃保温时效处理0.5-8h得到高强度高热导率钢材料。
[0020]
优选地,在s2中,固溶温度为880-920℃,固溶时间为20-40min。
[0021]
优选地,在s2中,固溶温度为900℃,固溶时间为30min。
[0022]
优选地,在s2中,于475-525℃保温时效处理0.5-4h。
[0023]
优选地,在s2中,于500℃保温时效处理4h。
[0024]
优选地,在s2中,用水淬火至铸锭温度为室温。
[0025]
优选地,在s2中,时效后,空冷至室温得到高强度高热导率钢材料。
[0026]
本发明还提出了上述高强度高热导率钢材料在高热导率模具中的应用。
[0027]
本发明还提出了上述高强度高热导率钢材料在选区激光熔化中的应用;优选,在采用选区激光熔化法制备高热导率模具中的应用。
[0028]
采用合金粉末进行选区激光熔化,合金粉末的成分配比与上述高强度高热导率钢材料相同。
[0029]
有益效果:
[0030]
针对现有高热导率模具钢材料,其过高的碳含量将会恶化合金的塑韧性,会降低合金产品的性能,还会使材料无法实现选区激光融化成型的问题;本发明采取了低碳低合金化、第二相强化的合金设计思路,在改善合金塑韧性的同时,使得合金具有较高的热导率、强度和硬度,使其满足高热导率模具钢的要求,并适用于选区激光融化成型。另外,本发明还筛选了合适的热处理工艺,优化合金的各项性能。
附图说明
[0031]
图1为热处理前实施例1-3的金相照片,其中,a为实施例1,b为实施例2,c为实施例3。
[0032]
图2为实施例1在不同时效温度下时效4h后的金相照片,其中,a为425℃,b为450℃,c为475℃,d为500℃,e为525℃,f为550℃,g为575℃。
[0033]
图3为实施例1在不同时效温度下时效4h后的金相sem照片,其中,a为425℃,b为500℃,c为575℃,右上角为标定区域放大10000倍的组织照片。
[0034]
图4为实施例2在不同时效温度下时效4h后的金相照片,其中,a为425℃,b为450℃,c为475℃,d为500℃,e为525℃,f为550℃,g为575℃。
[0035]
图5为实施例3在不同时效温度下时效4h后的金相照片,其中,a为425℃,b为450℃,c为475℃,d为500℃,e为525℃,f为550℃,g为575℃。
[0036]
图6为不同时效时间后实施例1-3的金相组织照片,其中,a-d为实施例1,a为0h,b为0.5h,c为1h,d为4h;i-l为实施例2,i为0h,j为0.5h,k为1h,l为4h;m-p为实施例3,m为0h,n为0.5h,o为1h,p为4h。
[0037]
图7为按照实施例1配方采用激光选区熔化成型设备制得的成型件照片。
具体实施方式
[0038]
下面,通过具体实施例对本发明的技术方案进行详细说明。
[0039]
用津岛生产的20kn规格的agxplus电子万能试验机,严格按照国家标准《gb/t228-2002金属材料室内拉伸试验方法》进行拉伸性能测试。
[0040]
用硬度测量仪器为hvs-1000a型硬度计,按照标准《gb/t230金属材料洛氏硬度试验》进行硬度测量实验。
[0041]
实施例1-3、对比例1-2
[0042]
取各种纯金属材料,用酒精对各种纯金属材料表面进行清洗处理,然后使用真空感应熔炼炉熔炼浇铸制备铸锭,各铸锭的成分配比如表2所示。
[0043]
表2实施例1-3、对比例1-2的配方
[0044]
含量%cnialcumnsimo其他fe实施例10.053.40.811.50.10.450.33crbal.实施例20.053.40.31.310.10.6/bal.实施例30.052.50.3110.11.50.1vbal.对比例10.052.50.3210.11.50.1vbal.对比例20.052.50.31.510.11.50.1vbal.
[0045]
取实施例1-3、对比例1-2制得的铸锭,分别测量各个铸锭在各实验温度点下的密度、比热、热扩散系数,并根据公式λ=αρc
p
(注:α-热扩散系数cm2s-1
;ρ-密度g
·
cm-3
;c
p-比热容j/(g
·
k);λ-导热系数w/(m
·
k)),计算在各实验温度点下的热导率,结果如表3所示。
[0046]
表3实施例1-3、对比例1-2的热导率(w/(m
·
k))
[0047]
[0048][0049]
由表3可以看出:在25-100℃温度范围内,对比例1-2的热导率提升率并不理想,相对实施例1-3来说要小很多;实施例1-3的热导率均保持在30w/(m
·
k)左右。各组的热导率随温度的变化趋势都是先增大后减小,在400℃热导率达到最大值,根据固体导热原理,这可能是因为随着温度升高,不仅仅晶格振动加剧,原子间的间距也将会增加,虽然更加剧烈的晶格振动会造成电子与声子更容易发生散射而使电子、声子自由程减小,但是原子间距的增大会使得固溶元素造成的晶格畸变相对减少,晶格畸变导致的电子散射会相应减弱,二者综合作用的结果使得各组的热导率在400℃以下时随着温度升高而升高,在400℃以上时则随着温度升高而减小。
[0050]
实施例4(不同时效温度的结果)
[0051]
取实施例1-3制得的铸锭进行热处理,具体热处理步骤为:于900℃固溶30min,然后用水淬火至铸锭温度为室温,再进行时效处理4h,然后空冷至室温得到模具钢。考察不同时效温度处理后模具钢的金相组织和性能。结果如表4-5、图1-5所示。
[0052]
图1为热处理前实施例1-3的金相照片,其中,a为实施例1,b为实施例2,c为实施例3。
[0053]
由图1可以看到:实施例1-3内部均未发现明显的气孔、裂纹等缺陷,熔炼出的组织都极为致密,实施例1-3均由白色的铁素体和灰色马氏体组成,铁素体以块状形式存在;实施例1-3的金相照片中均存在黑色的网状物存在,这些黑色的网络基本沿着晶界分布,考虑到金相组织为未经热处理的组织,由此判断黑色网状部分的出现是元素偏析所导致的。
[0054]
图2为实施例1在不同时效温度下时效4h后的金相照片,其中,a为425℃,b为450℃,c为475℃,d为500℃,e为525℃,f为550℃,g为575℃。
[0055]
由图2可以看出:实施例1经过热处理后得到的组织为板条马氏体,铸态时的块状铁素体组织经过热处理后全部消失。
[0056]
图3为实施例1在不同时效温度下时效4h后的金相sem照片,其中,a为425℃,b为500℃,c为575℃,右上角为标定区域放大10000倍的组织照片。
[0057]
由图3可以看出:不同时效温度下马氏体板条之间的界面为小角度界面,马氏体板条间相互平行。时效温度为425℃时,马氏体板条非常细小,宽度约为200nm,马氏体板条之间界面明显,存在较大块的白色颗粒状物体,其尺寸小于1μm,其可能为析出的碳化物或者是残余奥氏体;当时效温度升高到500℃时,马氏体板条的宽度较425℃时有着较小幅度的增加,马氏体板条的界面仍然明显,板条界面上的白色颗粒物数量减少且尺寸变小;当温度继续增加到575℃后,马氏体板条之间的界面非常模糊几乎消失,板条界面上几乎不存在白色颗粒物,考虑到时效时间仅为4h且碳化物溶解温度要高于575℃,可以初步判断白色颗粒物为残余奥氏体。显然,从组织变化情况可以判断575℃时效后的试样为过时效状态。
[0058]
图4为实施例2在不同时效温度下时效4h后的金相照片,其中,a为425℃,b为450℃,c为475℃,d为500℃,e为525℃,f为550℃,g为575℃。
[0059]
由图4可以看出:实施例2经热处理后,模具钢的组织为全马氏体组织。
[0060]
图5为实施例3在不同时效温度下时效4h后的金相照片,其中,a为425℃,b为450℃,c为475℃,d为500℃,e为525℃,f为550℃,g为575℃。
[0061]
由图5可以看出:实施例3经热处理后,模具钢的组织为全马氏体组织。
[0062]
表4经不同时效温度时效4h后的实施例1-3硬度(hrc)
[0063]
时效温度(℃)实施例1实施例2实施例342540.4036.7037.2045043.7336.0737.6747542.7739.3339.1750043.1338.5036.7352542.2735.9737.6755040.7332.8038.1757535.2028.8735.93
[0064]
由表4可以看出:实施例1模具钢硬度处于最高水平,实施例2-3的硬度稍低。实施例1-3的硬度随时效温度的变化趋势均为先增大后减小,时效温度为425℃和575℃时的硬度要明显低于其他时效温度处理后的硬度,这是因为时效温度较低时经时效处理后模具钢内部析出物的数量相对较少,析出物起到的硬化作用并不明显,而时效温度较高时析出相在完全析出后仍然处于高温下,这时候原本细小弥散的析出相会出现聚合长大的现象,使得析出相的硬化作用减弱,因而硬度降低,所以对于实施例1-2而言,合适的时效温度区间为450-525℃。对于实施例3,当时效温度在425-575℃范围内时,其硬度随时效温度的改变波动较小,这可能是因为实施例3模具钢含有较少的al和cu元素,析出相起到的强化作用有限。al元素的添加能明显提高模具钢的硬度,因为al元素能与ni形成nial相,nial相与富cu相的交互析出将会提高材料的硬度。
[0065]
使用岛津电子万能试验机对实施例1-3模具钢经过不同热处理后的拉伸力学性能进行了测量,测量结果如表5所示。
[0066]
表5经不同时效温度时效4h后实施例1-3的拉伸性能
[0067][0068]
备注:ts为抗拉强度,el为延伸率。
[0069]
由表5可以看出:时效温度在425-575℃温度范围内时,随着时效温度增加,各模具钢的抗拉强度均呈现先增加后减小的趋势。显然时效温度选择在475℃-525℃是更合适的,时效温度过低时模具钢内部第二相析出量未达到峰值而强度提升有限,为欠时效状态;而时效温度过高时,第二相聚集长大的同时马氏体板条之间的界面消失,使得强度显著降低,为过时效状态;
[0070]
延伸率与时效温度之间的关系则不明显,随着时效温度增加,延伸率总体上呈一个增加的趋势,增加的幅度较小,这可能是因为时效温度越高,内应力的消除越彻底,同时晶粒内部的位错经过滑移和攀移后使位错密度降低,多因素共同作用下延伸率呈现出了随时效温度增加而增加的趋势。实施例1模具钢的抗拉强度最高,这是因为实施例1中的al、ni含量高于实施例2-3,因而时效过程中可以析出更多的nial相强化基体。
[0071]
由图1-5、表4-5的结果可以看出,当在温度475-525℃范围内时效4h时,实施例1-3模具钢能获得较高的硬度,同时强度和塑性有着较好的配合。因此在研究时效时间对组织力学性能的影响规律时,选定时效温度为500℃。
[0072]
实施例5(不同时效时间的结果)
[0073]
取实施例1-3制得的铸锭进行热处理,具体热处理步骤为:于900℃固溶30min,然后用水淬火至铸锭温度为室温,在500℃进行时效处理,然后空冷至室温得到模具钢。考察不同时效时间处理后模具钢的金相组织和性能。结果如表6-7、图6所示。
[0074]
图6为不同时效时间后实施例1-3的金相组织照片,其中,a-d为实施例1,a为0h,b为0.5h,c为1h,d为4h;i-l为实施例2,i为0h,j为0.5h,k为1h,l为4h;m-p为实施例3,m为0h,n为0.5h,o为1h,p为4h。
[0075]
由图6可以看出:实施例1-3模具钢的组织为全马氏体组织,对于同一种模具钢,经过不同时效时间时效处理后,通过金相照片看不到组织的变化,可以认为在500℃时效处理时微观组织对于时效时间并不敏感。
[0076]
表6在500℃时效不同时间后实施例1-3的硬度(hrc)
[0077]
热处理工艺实施例1实施例2实施例3固溶 时效0h37.033.132.6固溶 时效0.5h38.835.535.2固溶 时效1h40.334.334.8固溶 时效2h40.834.536.3固溶 时效4h43.138.536.7固溶 时效8h42.735.935.7
[0078]
由表6可以看出:实施例1-3模具钢经过固溶处理后硬度可以达到30hrc以上,其中实施例1模具钢固溶态硬度最高为37hrc;实施例1模具钢硬度最高,实施例1模具钢硬度随时效时间的延长呈逐步增加的趋势,实施例2-3模具钢的硬度在时效0.5h时硬度要高于时效1h的硬度,硬度随时效时间的变化趋势为波浪形,先减小再增加,这是因为在时效0.5h时大量富铜相快速析出,提高了材料的硬度,而时效时间增加到1h时不仅有析出相持续析出使硬度增加,还会发生位错的重新排布而导致材料内部位错密度降低而使硬度降低,两者综合作用的结果决定了时效1h时的硬度与时效0.5h时硬度大小关系;时效时间达到4h后,继续增加时效时间到8h,硬度的变化很小,说明相对于时效温度时效时间对硬度的影响较小。
[0079]
使用岛津电子万能试验机对实施例1-3模具钢经过不同热处理后的拉伸力学性能进行了测量,测量结果如表7所示。
[0080]
表7 500℃时效不同时间后实施例1-3的拉伸性能
[0081][0082]
备注:ts为抗拉强度,el为延伸率。
[0083]
由表7可以看出:实施例1-3模具钢时效处理后的延伸率要普遍高于仅经过固溶处理的延伸率,这是因为时效处理后应力得到了释放,材料内部的位错密度降低,塑性得到了提高;时效时间低于4h时,经时效处理的模具钢的强度反而低于固溶态的强度,时效时间达到4h后模具钢的强度超过固溶态的强度,短时间时效强度降低的原因可能是位错密度减小导致的,而时效时间达到4h后因为析出相有充分的时间析出而使得材料强度增加;实施例1
模具钢的强度在时效时间为2h和4h时超过了1100mpa,其强度超过实施例2-3模具钢100mpa以上,al元素显然能起到提高强度的作用。实施例1-3模具钢最优热处理工艺为900℃固溶 500℃时效,在这一热处理工艺下实施例1-3模具钢的硬度、强度和延伸率均更好,实施例1模具钢硬度为43.1hrc,强度为1121.8mpa,延伸率为10.9%。
[0084]
实施例6
[0085]
使用安徽哈特三维的雾化制粉设备制备模具钢粉末,添加原材料时严格按照实施例1的配方进行添加,模具钢粉末。然后使用哈特三维生产的3d打印模具专机hit-m150激光选区熔化成型设备制备高热导率模具钢,所得成品的照片如图7所示,图7为按照实施例1配方采用激光选区熔化成型设备制得的成型件照片。
[0086]
以上所述,仅为本发明较佳的具体实施方式,但本发明的保护范围并不局限于此,任何熟悉本技术领域的技术人员在本发明揭露的技术范围内,根据本发明的技术方案及其发明构思加以等同替换或改变,都应涵盖在本发明的保护范围之内。
再多了解一些
本文用于企业家、创业者技术爱好者查询,结果仅供参考。