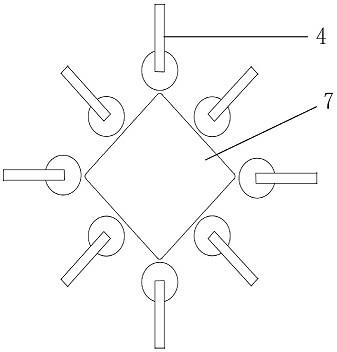
1.本发明涉及一种能够快速、准确地识别和消除铸坯表面缺陷的方法,属于金属的轧制技术领域。
背景技术:
2.铸坯的表面通常会存在一些缺陷,如结疤、皮下气泡、缩孔、皮下裂纹等,对于表面质量要求较高的轧钢产品,在进行轧制生产前,需要消除铸坯表面的这些缺陷,避免铸坯表面缺陷遗传到轧制工序,影响产品表面质量。
3.目前,铸坯表面缺陷的精整方法有火焰法、车削法、铣削法、风铲法、砂轮修磨法等,其中以火焰法和砂轮修磨法两种方式为主,而砂轮修磨在降低能源消耗的同时也极大地提高了生产效率和产品质量,利用砂轮修磨方法还可以对坯料的顶端进行塑形倒角,可以更好地保护轧制设备,且在修磨过程中不会有大量的飞屑产生,提高了生产的安全性,因此,砂轮修磨法在国内冶金行业中的应用更为普遍。
4.公开号为cn85100327a的中国专利《一种钢锭(坯)旋转修磨方法》对钢锭(坯)表面层缺陷作全扒皮修磨,使钢锭(坯)表面得到圆角过渡和较光滑、平整的修磨表面,以提高钢锭(坯)的修磨质量与修磨效率。
5.公开号为cn102205518a的中国专利《一种不锈钢铸坯表面修磨的方法》先对铸坯上表面进行修磨;上表面修磨后,将铸坯吊运到翻坯机上翻坯,即已修磨面向下,未修磨面翻到上,再将铸坯吊回修磨台车上,对铸坯的另一面按设定参数进行修磨,其中修磨角度为70-85
°
,即砂轮转动方向和铸坯行进方向成70-85
°
。
6.公开号为cn104029092a的中国专利《一种型钢钢坯表面砂磨方法》顺长度方向将钢坯安装到钢坯安装平台上,然后再调整吊链使得砂轮机砂轮片能够与钢坯表面接触;操作者手持砂轮机通过水平移动装置,将砂轮机拖动至钢坯起始位置,启动砂轮机并沿垂直于钢坯长度方向摆动砂轮机,使其完成砂轮片和钢坯一个接触面积的宽度方向的砂磨,然后逐渐沿长度方向拖动砂轮机完成对钢坯表面整体砂磨。
7.公开号为cn104625890a的中国专利《一种含mo奥氏体不锈钢连铸坯的修磨方法》将含mo奥氏体不锈钢连铸坯加热至1240℃,通过空气保持压强为2-3个大气压冷却到室温;将冷却的含mo奥氏体不锈钢连铸坯通过修模机进行修磨,共修磨三遍,其中第一、二遍每遍设定修磨损失率1.0%,道次间距35-50mm,每米修磨道次20-30条;第三遍为轻修磨,修磨损失率为0.5%,每米修磨道次30-40条,每道次间距20-35mm。
8.公开号为cn105619201a的中国专利《方钢、方坯去毛刺装置及其工艺方法》针对火焰切割后连铸方坯或者金属锯切的方钢在两端存在飞边和毛刺,提供一种自动化流水生产线,去毛刺速度快,去毛刺深度可调,去毛刺质量稳定可控,改善了工人劳动条件,提高去毛刺的效率。
9.现在冶金行业中主流的砂轮精整方法是全修磨和点修磨,全修磨是指对铸坯的四个面部和四个棱部进行全方位的修磨,优点是表面缺陷去除率高,缺点是效率低,质量损失
率高达3-5%;点修磨通常是人工对铸坯进行目视检查,发现缺陷后进行标记,然后使用手持砂轮机对缺陷位置进行人工打磨,优点是质量损失率低,缺点是表面缺陷去除率低,工作效率低,存在漏检缺陷的质量风险。
技术实现要素:
10.本发明的目的在于针对现有技术之弊端,提供一种铸坯表面缺陷的高效识别与精整方法,以快速、准确地识别和消除铸坯表面缺陷,降低铸坯的质量损失率,提高表面缺陷去除率和生产效率。
11.为实现上述目的,本发明采用如下技术方案:一种铸坯表面缺陷的高效识别与精整方法,所述方法在运送铸坯的辊道侧部安装沿运送方向依次排列的磁化线圈、测距传感器、喷头组、摄像机组和砂轮组,测距传感器检测到由磁化线圈充磁的铸坯后向设备控制器发送开始信号,设备控制器接收到该信号后控制喷头组向铸坯表面喷淋磁粉液,摄像机组从不同角度拍摄铸坯表面,并将照片上传到设备控制器,设备控制器根据照片判定铸坯是否存在表面缺陷,若发现缺陷则根据缺陷的类型、大小和部位控制砂轮组中相应的砂轮以设定的压力对缺陷区域进行修磨。
12.上述铸坯表面缺陷的高效识别与精整方法,所述方法包括以下步骤:a.将铸坯7放置在运行的辊道上,利用磁化线圈给匀速运行的铸坯连续充磁;b.当测距传感器探测到铸坯时,向设备控制器发送开始信号,设备控制器收到该信号后分别向喷头组、摄像机组、砂轮组发送启动信号;c.喷头组接收到启动信号后,从不同角度向铸坯表面喷淋磁粉液,使磁粉液覆盖铸坯整个表面;d.摄像机组接收到启动信号后,从不同角度拍摄铸坯表面,并将照片上传到设备控制器,设置在设备控制器中的缺陷识别单元根据照片判定铸坯是否存在表面缺陷,若发现缺陷则根据缺陷的类型、大小和部位向砂轮组发送相应的修磨信号;e.砂轮组接收到启动信号后,所有砂轮开始空转;当砂轮组接收到修磨信号时,砂轮组中与缺陷部位相对应的砂轮的下压机构按照修磨信号给定的压下时间、保持时间和砂轮压力动作,将砂轮压向铸坯,对缺陷区域进行修磨;f.当测距传感器探测到铸坯消失时,向设备控制器发送停止信号,设备控制器收到该信号后分别向喷头组、摄像机组、砂轮组发送停机信号,使喷头组、摄像机组、砂轮组在铸坯经过后停止运行。
13.上述铸坯表面缺陷的高效识别与精整方法,在利用磁化线圈对铸坯充磁之前,利用抛丸机去除铸坯表面的氧化铁皮。
14.上述铸坯表面缺陷的高效识别与精整方法,所述方法的步骤a~步骤f重复操作,对铸坯进行二次精整。
15.上述铸坯表面缺陷的高效识别与精整方法,所述修磨信号给定的压下时间=拍照时间差 固定时间,所述拍照时间差=该缺陷第一张有缺陷照片的拍摄时间-铸坯的第一张照片的拍摄时间,所述固定时间=测距传感器到砂轮组的距离/辊道运行速度。
16.上述铸坯表面缺陷的高效识别与精整方法,所述修磨信号给定的保持时间=该缺陷最后一张有缺陷照片的拍摄时间-该缺陷第一张有缺陷照片的拍摄时间。
17.上述铸坯表面缺陷的高效识别与精整方法,所述修磨信号给定的砂轮压力根据铸坯表面缺陷的类型设定,铸坯表面缺陷的类型包括结疤、皮下气泡、缩孔和皮下裂纹。
18.本发明采用图象识别技术判定铸坯是否存在表面缺陷,利用砂轮组对缺陷区域进行修磨,实现了缺陷识别与修磨自动化,该方法能够快速、准确地识别和消除铸坯表面缺陷,降低铸坯的质量损失率,提高表面缺陷去除率和生产效率。
附图说明
19.下面结合附图和具体实施方式对本发明作进一步详细的说明。
20.图1是本发明的设备布局示意图;图2是铸坯表面磁粉液喷淋示意图;图3是铸坯表面照片采集示意图;图4是铸坯周围修磨砂轮分布图。
21.图中各标号为:1、抛丸机,2、喷头组,3、摄像机组,4、砂轮组,5、辊道,6、测距传感器,7、铸坯。
具体实施方式
22.本发明提供了一种铸坯表面缺陷的高效识别与精整方法,该方法能够保证较高的生产效率、较高的表面缺陷去除率和较低的质量损失率。
23.参看图1~图4,本发明采用的设备包括设备控制器(图中未画出)、抛丸机1、磁化线圈(图中未画出)、喷头组2、摄像机组3、砂轮组4、辊道5和测距传感器6,其中,抛丸机1用于去除铸坯表面的氧化铁皮,如果铸坯上没有氧化铁皮(例如第二次精整时氧化铁皮已经去除),则可以不用抛丸机1;磁化线圈用于对铸坯7进行充磁,以使喷淋到铸坯表面的磁粉液形成能够反映表面缺陷状况的图案;喷头组2包括多个磁粉液喷头,它们绕铸坯周向布置,可将磁粉液喷淋到铸坯7整个表面;摄像机组3包括绕铸坯周向布置的多个高清摄像机,可从不同角度拍摄铸坯7表面,砂轮组4包括绕铸坯周向布置的多个砂轮,每个砂轮均设有独立的下压机构,下压机构可在设备控制器的控制下使砂轮以设定的压力与铸坯接触或离开铸坯;辊道5用于输送铸坯;测距传感器6用于检测铸坯是否进入辊道5;设备控制器内设有缺陷识别单元和位置信号处理单元,缺陷识别单元用于识别铸坯表面缺陷,位置信号处理单元可根据喷头组2、摄像机组3、砂轮组4的距离和辊道7的运行速度计算喷头组2、摄像机组3和砂轮组4的启停时间。
24.本发明利用高清摄像机组对运行中的铸坯表面进行拍照,然后将铸坯照片上传到设备控制器,设置在设备控制器内的缺陷识别单元中有大量典型的、各种类型的缺陷形貌和数据,可利用图象识别技术对铸坯照片进行识别和判定,无缺陷照片不发送修磨信号,有缺陷照片时发送修磨信号,修磨信号包括根据照片的拍摄时间、缺陷类型、缺陷尺寸确定的每一个砂轮的压下时间、保持时间和砂轮压力,保持时间和砂轮压力取决于识别的缺陷类型和尺寸大小,压下时间=拍照时间差 固定时间,拍照时间差=该缺陷第一张有缺陷照片的拍摄时间-铸坯的第一张照片的拍摄时间,固定时间=测距传感器到砂轮组的距离/辊道运行速度,保持时间=该缺陷最后一张有缺陷照片的拍摄时间-该缺陷第一张有缺陷照片的拍摄时间。
25.本发明相比于现有修磨精整方法的不同之处在于,该方法对铸坯缺陷进行高精度、高效识别,对铸坯缺陷进行定点精准修磨,提高修磨效率和缺陷去除率,减小修磨质量损失,具体精整步骤为:1)铸坯7经过抛丸机1去除表面氧化铁皮,在辊道5运送下匀速向前运行;利用磁化线圈给铸坯7连续充磁;2)当测距传感器6探测到铸坯7进入时,向设备控制器发送开始信号,设备控制器收到该信号后,其中的位置信号处理单元分别向喷头组2、摄像机组3、砂轮组4发送启动信号;3)喷头组2接收到启动信号后,喷头组2中的多个喷头从不同角度向铸坯7表面喷淋磁粉液,保证磁粉液覆盖铸坯7整个表面;4)摄像机组3接收到启动信号后,摄像机组3中的多个摄像机从不同角度拍摄铸坯7表面,并将照片上传到设备控制器,设备控制器对照片进行识别和判定,无缺陷照片不发送信号,有缺陷照片则根据缺陷的类型、大小和部位向砂轮组4发送相应的修磨信号;5)砂轮组4接收到启动信号后,所有砂轮开始空转;当收到修磨信号时,砂轮组4中与缺陷部位相对应的砂轮的下压机构按照修磨信号给定的压下时间、保持时间和砂轮压力动作,将砂轮下压到铸坯表面,使砂轮与铸坯接触,在设定压力下保持一定时间,对缺陷区域进行修磨。
26.6)当测距传感器6探测到铸坯7消失时,向设备控制器发送停止信号,设备控制器中的位置信号处理单元根据喷头组2、摄像机组3、砂轮组4的距离和辊道7的运行速度分别向分别向喷头组2、摄像机组3、砂轮组4发出停机信号,使喷头组2、摄像机组3、砂轮组4在铸坯7经过后停止运行,停机信号设计为延迟信号,保证铸坯运行过程中各组均正常工作和运转。
27.本方法还可以进行二次精整,即上料、抛丸、铸坯充磁、磁粉喷淋、拍照识别、砂轮定点修磨、铸坯充磁、磁粉喷淋、二次拍照识别、砂轮定点修磨、下料,通过二次拍照识别,检验修磨效果,查漏补缺,对漏检缺陷和打磨效果较差的缺陷进行二次打磨,实现高精度铸坯精整。
28.本发明实现了对铸坯缺陷的精准打磨,生产过程自动化,铸坯表面缺陷去除率高,生产效率提高。与全扒皮相比,质量损失大幅度降低,质量损失率可控制在1%以下,生产过程中铸坯没有翻钢动作,减少了磕碰和刮蹭造成的铸坯表面缺陷。
29.实施例1某钢厂scm435铸坯150mm*150mm*12000mm批量使用本发明进行铸坯精整,共计精整10个批次,精整前约453.8吨,精整后约451.5吨,质量损失率为0.5%,其中1支铸坯的具体生产情况为:scm435铸坯150mm*150mm*12000mm上料,经过抛丸机去除表面氧化铁皮,在辊道运送下匀速向前运行;利用磁化线圈给铸坯连续充磁;测距传感器探测到铸坯进入,设备控制器中的位置信号处理单元分别向喷头组、摄像机组、砂轮组发出启动信号,喷头组接收到启动信号从不同角度向铸坯表面喷淋磁粉液,保证磁粉液覆盖铸坯整个表面;摄像机组接收到启动信号从不同角度拍摄铸坯表面,将照片上传到设备控制器,设备控制器对照片进行识别和判定,识别出10个有缺陷照片,发出10个反馈信息传递到砂轮组;砂轮组接收到启动
信号,砂轮开始空转;收到设备控制器的10个修磨信号,对10个缺陷区域进行了修磨;当测距传感器探测到铸坯消失时,设备控制器中的位置信号处理单元分别向喷头组、摄像机组、砂轮组发出停机信号。
30.实施例2某钢厂55sicr铸坯160mm*160mm*12000mm批量使用本发明进行铸坯精整,共计精整8个批次,精整前约371.2吨,精整后约368.8吨,质量损失率为0.6%,其中1支铸坯的具体生产情况为:55sicr铸坯160mm*160mm*12000mm上料,经过抛丸、铸坯充磁、磁粉喷淋、拍照识别,设备控制器对照片进行识别和判定,识别出13个有缺陷照片,发出13个修磨信号到砂轮组,砂轮组接收到设备控制器的13个修磨信号后,对13个缺陷区域进行定点修磨,55sicr铸坯在辊道运送下继续匀速向前运行,经铸坯充磁、磁粉喷淋和二次拍照识别,设备控制器对照片进行二次识别和判定,识别出2个有缺陷照片,发出2个修磨信号到砂轮组;砂轮组收到设备控制器发送的2个修磨信号后,对2个缺陷区域进行了修磨;当测距传感器探测到铸坯消失时,设备控制器中的位置信号处理单元分别向喷头组、摄像机组、砂轮组发出停机信号。
31.实施例3某钢厂gcr15铸坯150mm*150mm*12000mm批量使用本发明进行铸坯精整,共计精整15个批次,精整前约695.7吨,精整后约691.5吨,质量损失率为0.6%,其中1支铸坯的具体生产情况为:gcr15铸坯150mm*150mm*12000mm上料,上料,经过抛丸、铸坯充磁、磁粉喷淋、拍照识别,设备控制器对照片进行识别和判定,识别出6个有缺陷照片,发出6个修磨信号到砂轮组,砂轮组接收到设备控制器的6个修磨信号后,对6个缺陷区域进行定点修磨,gcr15铸坯在辊道运送下继续匀速向前运行,经铸坯充磁、磁粉喷淋和二次拍照识别,设备控制器对照片进行二次识别和判定,识别出0个有缺陷照片,未发出修磨信号;当测距传感器探测到铸坯消失时,设备控制器中的位置信号处理单元分别向喷头组、摄像机组、砂轮组发出停机信号。
再多了解一些
本文用于企业家、创业者技术爱好者查询,结果仅供参考。