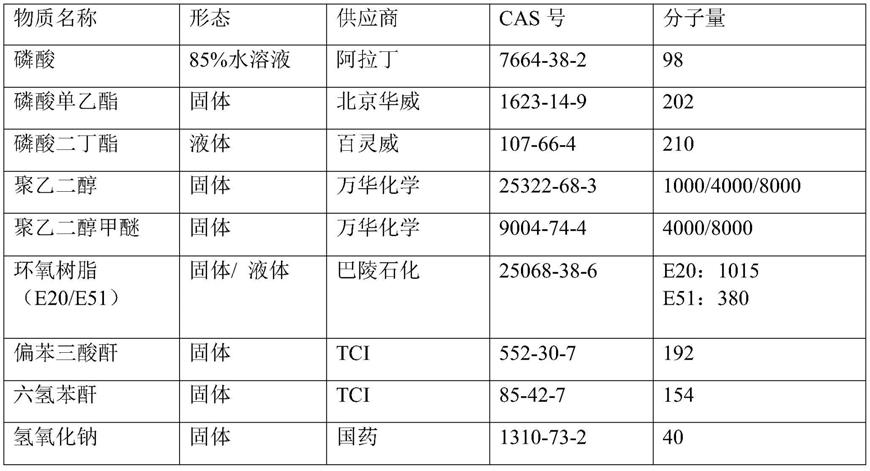
1.本发明属于涂料和胶粘剂领域,涉及一种环氧乳化剂的制备方法以及制得的乳化剂、含有该乳化剂的环氧树脂水分散体及该环氧树脂水分散体的制备方法。
背景技术:
2.环氧树脂含有大量的羟基、醚键等极性基团,对金属底材有优异的附着能力,含有的苯环、c-c链段等基团赋予其较好的耐热性、耐腐蚀性、韧性。与胺固化剂交联,可形成高交联密度的致密漆膜,具有优异的耐化学、耐盐雾性,在工业防腐领域有着不可替代的重要作用。环氧树脂因其具有优异的机械性能及防腐性能,被广泛地应用于防腐涂料的底漆及中间漆。
3.传统的环氧树脂涂料一般为溶剂型,溶剂型涂料是voc的重要来源,对环境造成很大污染,对人体也有极大的伤害,因而涂料向高固体分和水性涂料方向发展已成为涂料界的共识,成为新型材料的研究方向。水性环氧可以极大地降低传统溶剂型环氧的voc排放,同时随着工艺技术的日益成熟,水性环氧的防腐性能与溶剂型环氧愈来愈接近。故水性双组分环氧涂料在市场上已有许多应用,如高性能的集装箱底漆、工程机械和轨道交通的底漆和中间漆等,除此之外,水性环氧树脂在大巴、港口机械、桥梁、罐听涂料、地坪等方向也有相关应用,预计未来三年水性环氧市场年需求量在5万吨以上。作为水性环氧树脂,已知有使用传统的非离子表面活性剂(也称为非离子型乳化剂),利用混合机、球体磨等设备,通过相转法、机械研磨等方法制备环氧乳液。得到的乳液因乳化剂用量较大、体系粘度高,导致分散困难、乳液耐水性能差;体系游离的大量乳化剂,导致乳液体系不稳定,乳胶粒子易聚并沉淀,储存时间短。
4.为了改善上述缺陷,专利cn 103249777 a提出利用环氧组合物与酰胺组合物的反应,制备改进的环氧官能化非离子表面活性剂,之后通过相转法制备低乳化剂含量的水性环氧分散体。该分散体与结构相似的固化剂配合使用,可以达到理想的耐腐蚀效果,但是由于乳化剂用量较低,分散体粒径较大(800-950nm),使得分散体稳定性较差,50℃热储小于10天,影响了产品的储存稳定性。
5.研究发现,在环氧乳液体系中,为使乳液具有良好的稳定性,常使用非离子乳化剂分散环氧树脂,但是为了环氧树脂具有良好的分散性,非离子乳化剂的用量往往较高,会影响环氧乳液最终的耐水性能等应用性能。而在其他水性涂料领域经常将离子型乳化剂和非离子型乳化剂配合使用,所得乳液体系具有良好的稳定性和优良的应用性能。
6.专利cn 106221506 a使用离子乳化剂和非离子乳化剂复配,获得储存稳定,综合性能优良的环氧乳液,但是该乳液通过两种乳化剂复配使用,工艺相对复杂。因此,本发明在非离子活性环氧乳化剂的基础上,通过磷酸或磷酸酯上活泼氢与环氧的反应,获得了一种新型环氧乳化剂,兼具离子和非离子的结构。同时磷酸酯基团的引入,可使得涂料在成膜过程中,磷酸酯与基材金属形成致密的磷酸盐保护膜,钝化金属表面,防止水分和盐离子与金属接触,提高了漆膜的附着力和防腐性能。
技术实现要素:
7.本发明的目的在于提供了一种环氧乳化剂的制备方法以及制得的乳化剂、一种环氧树脂水分散体及该环氧树脂水分散体的制备方法,含有该乳化剂的环氧树脂水分散体稳定性好,并且固化后耐腐蚀性能优良。本发明的制备方法通过将非离子型乳化剂和磷酸酯基团反应,得到一种同时含有非离子及磷酸酯基的复合活性乳化剂,提高乳化效果,降低环氧树脂分散体中乳化剂用量,得到综合应用性能优良的环氧树脂分散体。
8.为了实现上述发明目的,本发明提供如下技术方案:
9.一种环氧乳化剂的制备方法,包括以下步骤:
10.(1)将聚醚与酸酐反应后得聚醚-酸酐产物,然后将得到的聚醚-酸酐产物与环氧树脂反应,得聚醚-酸酐-环氧产物;
11.(2)将步骤(1)得到的聚醚-酸酐-环氧产物与磷酸或磷酸酯反应得到环氧乳化剂。
12.所述步骤(2)制得的乳化剂可选地用或不用碱中和成盐。
13.在一种实施方式中,所述的聚醚结构通式如下:
[0014][0015]
在式ⅰ结构中,r选自h或c1-12的烷基,优选为h或c1-4的烷基;a选自h或甲基;n为整数,表示环氧乙烷基或环氧丙烷基的重复数,且n≥5,优选为11-180。
[0016]
优选的,本发明中所述的聚醚的数均分子量为300-10000。
[0017]
所述酸酐为分子中具有2-4个羧基的多元羧酸的酸酐,优选含有2-3个羧基的多元羧酸进行分子内脱水而得到的酐,例如可以是来自芳香族多元羧酸或环状脂肪族多元羧酸的酸酐等以往公知的酸酐,但优选来自芳香族多元羧酸的酸酐。作为芳香族多元羧酸的酸酐,可列举出例如六氢苯酐、偏苯三酸酐、均苯四甲酸酐、二苯甲酮-3,3’,4,4
’-
四羧酸酐等,它们中,优选六氢苯酐、偏苯三酸酐。此外,作为环状脂肪族多元羧酸的酸酐,可列举出例如氢化偏苯三酸酐、氢化均苯四甲酸酐等。
[0018]
所述环氧树脂的分子中至少含有两个环氧基团,所述环氧树脂可为饱和或不饱和的,所述环氧树脂可为脂族、环脂族、芳族或杂环的环氧基树脂,且还可含有羟基。它们也可包含其它在混合和反应条件下不引起干扰性副反应的取代基,例如烷基或芳基取代基、醚基等。优选地,所述环氧树脂的环氧值不大于0.6,优选不大于0.55,比如0.1-0.55,进一步优选为多缩水甘油醚。优选地,常用的多缩水甘油醚环氧树脂可以是多元酚或多元醇的缩水甘油醚,其中,多元酚例如为间苯二酚、氢醌、2,2-双(4
′-
羟基苯基)丙烷(双酚a)、二羟基二苯基甲烷(双酚f)的异构体混合物、4,4'二羟基二苯基环己烷、4,4'-二羟基-3,3'-二甲基二苯基丙烷、4,4'-二羟基联苯、4,4'-二羟基二苯甲酮、双(4'-羟基苯基)-1,1-乙烷、双(4'-羟基苯基)-1,1-异丁烷、双(4'-羟基-叔丁基苯基)-2,2-丙烷、双(2-羟基萘基)-甲烷、1,5-二羟基萘、三(4-羟基苯基)-甲烷、双(4-羟基苯基)乙醚、双(4-羟基苯基)砜及前述化合物的氯化和溴化产物。也可以使用多羟基醇的多缩水甘油醚,如乙二醇-1,2-二缩水甘油醚,丙二醇-1,2-二缩水甘油醚,丙二醇-1,3-二缩水甘油醚,丁二醇二缩水甘油醚,戊二醇二缩水甘油醚,新戊二醇二缩水甘油醚,己二醇二缩水甘油醚,二甘醇二缩水甘油醚,二丙
二醇二缩水甘油醚,高碳聚亚氧烷基乙二醇二缩水甘油醚(如:高碳聚氧乙烯二醇二缩水甘油醚和聚氧丙烯二醇二缩水甘油醚、混合型聚氧乙烯-丙烯二醇二缩水甘油醚),聚氧丁烯二醇二缩水甘油醚,甘油、三羟甲基丙烷、三羟甲基乙烷、季戊四醇、山梨糖醇的多缩水甘油醚,烷氧基化的多元醇如甘油、三羟甲基丙烷、季戊四醇的多缩水甘油醚,环己烷二甲醇、双(4-羟基环己基)甲烷和2,2-双(4-羟基环己基)丙烷的二缩水甘油醚,蓖麻油或三缩水甘油基三(2-羟基乙基)异氰脲酸酯的多缩水甘油醚。此外,所述多缩水甘油醚还可以是多元羧酸的多缩水甘油酯,其通过表氯醇或类似的环氧化合物与脂族、环脂族或芳族多元羧酸反应而制得。所述多元羧酸如草酸、琥珀酸、己二酸、戊二酸、邻苯二甲酸、对苯二甲酸、四氢邻苯二甲酸、六氢邻苯二甲酸、2,6-萘二羧酸、高碳二羧酸,二聚或三聚的亚麻酸。
[0019]
所述磷酸酯为磷酸单酯,磷酸二酯中的一种或多种。
[0020]
所述磷酸单酯为磷酸单烷基酯,其中烷基链的碳原子个数为1-18,例如磷酸单甲酯、磷酸单乙酯、磷酸单丁酯、磷酸单(1-甲基乙基)酯、十二烷基磷酸单酯等,优选磷酸单甲酯、磷酸单乙酯、磷酸单(1-甲基乙基)酯、磷酸单丁酯。
[0021]
所述磷酸二酯为磷酸二烷基酯,其中烷基链的碳原子个数为1-18,例如磷酸二甲酯、磷酸二乙酯、磷酸二丁酯、磷酸二(1-甲基乙基)酯、十二烷基磷酸二酯等,优选磷酸二甲酯、磷酸二乙酯、磷酸二(1-甲基乙基)酯、磷酸二丁酯。
[0022]
所述碱为选自氢氧化钠和/或氢氧化钾。
[0023]
本发明中,所述步骤(1)中,所述聚醚与酸酐的酯化反应中,酸酐的酸酐基(-cooco-)总量相对于所述聚醚的羟基总量的摩尔比为1-1.2、更优选为1.0-1.1进行。上述酸酐基的比例小于1的情况下,水分散性环氧树脂中会残存有羟基,所以不优选。此外,上述酯化反应的反应温度可以为40-140℃,优选为80-130℃;上述酯化反应的反应时间可以为1-5小时,优选为1-3小时。上述酯化反应中,根据需要,步骤(1)所述酯化反应还可在溶剂中进行,所用溶剂可选择本领域公知的溶剂,例如乙二醇丁醚、二丙二醇二甲醚。
[0024]
在一种实施方式中,步骤(1)的聚醚-酸酐产物与环氧树脂的开环反应的反应条件可以为:在催化剂作用下于40-140℃,比如60℃、80℃、100℃或130℃,优选120-140℃下反应1-5h,优选1-3h。上述开环反应的催化剂为本领域所熟知,例如为三苯基膦、三苯基磷化氢、三氟化硼乙醚中的一种或多种,其用量可以为反应体系中固体总量的0.04wt%-5wt%,优选0.05wt%~1wt%,比如0.1wt%、0.2wt%、0.5wt%或0.8wt%。
[0025]
本发明中,所述步骤(1)中,加入的环氧树脂中所含的环氧基团的总摩尔量应大于等于聚醚-酸酐产物中所含的羧基的总摩尔量,例如,二者的比可以为1:1、1.5:1、2:1等,优选大于等于2:1比如5:1、10:1、100:1或更高。本领域技术人员理解,即使环氧树脂大为过量,由于后续最终可以用于配制环氧树脂分散体,因此环氧树脂过量不会影响环氧树脂分散体的制备。作为优选,本发明步骤(1)中,加入的环氧树脂中所含的环氧基团的总摩尔量与聚醚-酸酐产物中所含的羧基的总摩尔量之比应小于等于4。环氧树脂可以为上文提及的环氧树脂的一种或多种。
[0026]
在一种实施方式中,所述的聚醚-酸酐-环氧产物是聚醚-酸酐产物和分子内具有2个以上环氧基的环氧树脂混合,利用所述聚醚-酸酐产物的羧基与环氧树脂的环氧基团进行开环反应得到所述聚醚-酸酐-环氧产物,其中,所述聚醚-酸酐-环氧产物分子中含有至少一个环氧基团。
[0027]
本发明中,所述步骤(2)中,加入的聚醚-酸酐-环氧产物中所含的环氧基团的总摩尔量应大于等于磷酸或磷酸酯中所含的活泼氢的总摩尔量,例如,二者的比可以为1:1、1.5:1、2:1等,优选大于等于2:1比如5:1、10:1、100:1或更高。本领域技术人员理解,即使环氧树脂大为过量,由于后续最终可以用于配制环氧树脂分散体,因此环氧树脂过量不会影响环氧树脂分散体的制备。作为优选,本发明步骤(2)中,加入的聚醚-酸酐-环氧产物中所含的环氧基团的总摩尔量与磷酸或磷酸酯中所含的活泼氢的总摩尔量的比小于等于10。
[0028]
本发明中,所述步骤(2)的反应温度为40-140℃,比如60℃、80℃、100℃或130℃,优选70-100℃,反应时间1-5h,优选1-3h。
[0029]
本发明还提供采用上述方法制备的环氧乳化剂,该乳化剂既含有非离子型亲水基团又含有磷酸酯基团,乳化效果好。
[0030]
本发明还提供一种环氧树脂水分散体,其中,所述环氧树脂水分散体中含有上述的环氧乳化剂或上述方法制备的环氧乳化剂。本领域技术人员理解,为保证良好的乳化分散效果,分散体中乳化剂的含量通常不宜过小,然而过高同样面临成本问题。基于本发明的环氧乳化剂有优异的乳化效果,所述环氧乳化剂的加入量为所述环氧树脂水分散体总质量的0.1-35wt%,比如1wt%、5wt%、10wt%、20wt%或30wt%,优选1-20wt%。因环氧乳化剂制备过程中可加入过量的环氧树脂,所以若环氧乳化剂中环氧树脂的加入量过大时,本领域技术人员有动机根据常识提高环氧树脂分散体中加入的环氧乳化剂的比例使其大于50%,例如60%、70%等。
[0031]
本发明中,所述环氧树脂水分散体还包括环氧树脂和水,此外,除乳化剂、环氧树脂和水外,分散体中通常还可选择性的添加有其它助剂,例如环氧活性稀释剂(加入量占分散体质量的0-20%,比如c8-c14的缩水甘油醚组合物、苯基缩水甘油醚、丁基缩水甘油醚)、溶剂(如丙二醇甲醚(pmop)、乙二醇丁醚、二丙二醇二甲醚、丙酮、丁酮、丁醇等,加入量占分散体质量的0-20wt%)、增稠剂(如u905、u300等,加入量占分散体质量的0-5wt%;消泡剂如foamstar2410、902w、byk-024,-033,-028、a1001等,加入量占分散体质量的0-1wt%),以及其它常用助剂,这些助剂的添加为本领域所熟知,这里不再赘述。
[0032]
在本发明中,所述环氧树脂水分散体的制备方法如下:将本发明所述方法制备的环氧乳化剂、任选的其他助剂加入到环氧树脂中,并加入水使之分散形成环氧树脂水分散体。
[0033]
本发明的有益效果在于:本发明的方法制备的同时含有非离子及磷酸酯基的活性环氧乳化剂,并且在一种乳化剂上实现了离子型与非离子型乳化剂的配合使用,可以大大降低乳化剂的用量,相对于将非离子型乳化剂和离子型乳化剂两种乳化剂配合使用,工业化生产工艺相对简单,从而在相对简单工艺的基础上,降低了体系总乳化剂的使用量,进而提高分散体的稳定性和耐腐蚀等性能。同时,磷酸酯基团的引入能明显改善固化后漆膜的附着力,可使得涂料在成膜过程中,磷酸酯与基材金属形成致密的磷酸盐保护膜,钝化金属表面,防止水分和盐离子与金属接触,提高了漆膜的附着力和防腐性能。采用本发明的环氧乳化剂制备的环氧树脂水分散体,具有储存稳定性好、并且固化后附着力、耐腐蚀性和耐水性优良等特性,可应用于涂料和胶粘剂领域。
具体实施方式
[0034]
以下通过实施例对本发明做进一步的详细说明,但不应将此理解为本发明的范围仅限于以下的实例。在不脱离本发明上述方法思想的情况下,根据本领域普通技术知识和惯用手段做出的各种替换或变更,均应包含在本发明的范围内。
[0035]
以下实施例/对比例所用物料来源如下:
[0036]
表1
[0037][0038]
本发明的各例中采用如下的测试方法:
[0039]
(1)分散体粒径测试:将分散体系用水稀释至浓度为170ppm(质量含量),然后用zetasizer nano zs粒径测试仪测试;
[0040]
(2)粘度测试:gb/t 15357-2014;
[0041]
(3)分散体系稳定性测试及其货架期预测:gt/t 5208;
[0042]
(4)耐中性盐雾性能:gb/t 1771。
[0043]
(5)划格法附着力:gb/t 9286。
[0044]
以下实施例/对比例中,所用试剂如未特别说明,均为分析纯;所述含量如未特别说明,为质量含量。
[0045]
乳化剂的制备:
[0046]
实施例1a:将500g熔融脱水后聚乙二醇(分子量为1000)注入釜内,保持釜内温度80℃,然后将184.8g六氢苯酐加入反应釜内,保持80℃,反应约3h,取样测试酸值达理论值(通过naoh反滴定测定,下同)后,然后注入760g环氧树脂e51,搅拌均匀后加0.7224g三苯基膦(tpp)催化剂,140℃恒温反应5h,测试酸值达理论值后,加入5.8g的磷酸,80℃搅拌反应约3h,测试环氧值达到理论环氧值(通过盐酸-丙酮法测定,下同)后出料。
[0047]
实施例2a:将500g熔融脱水后的聚乙二醇(分子量为1000)注入釜内,保持釜内温度80℃,然后将169.4g六氢苯酐加入反应釜内,保持80℃,反应约3h,取样测试酸值达理论值后,注入760g液态环氧树脂e51,搅拌均匀后加0.715g三苯基膦(tpp)催化剂,140℃恒温反应5h,测试酸值达理论值后,加入5.8g的磷酸,80℃搅拌反应约3h后,加入2g氢氧化钠,80℃反应1h,测试环氧值达到理论环氧值后出料。
[0048]
实施例3a:将1000g熔融脱水后聚乙二醇(分子量为4000)注入釜内,保持釜内温度80℃,然后将77g六氢苯酐加入反应釜内,升温至110℃,反应约3h,取样测试酸值达理论值后,注入285g环氧树脂e51,搅拌均匀后加5.45g三苯基膦(tpp)催化剂,130℃恒温反应3h,测试酸值达理论值后,加入15.15g的磷酸单乙酯,80℃搅拌反应约3h,测试环氧值达到理论环氧值后出料。
[0049]
实施例4a:将2000g熔融脱水后的聚乙二醇(分子量为8000)注入釜内,保持釜内温度100℃,然后将77g六氢苯酐加入反应釜内,升温至130℃,反应约3h,取样测试酸值达理论值后,然后注入507.5g环氧树脂e20,搅拌均匀后加25.85g三苯基膦(tpp)催化剂,120℃恒温反应3h,测试酸值达理论值后,加入26.25g的磷酸二丁酯,80℃搅拌反应约3h,测试环氧值达到理论环氧值后出料。
[0050]
实施例5a:将1000g熔融脱水后的聚乙二醇单甲醚(分子量为4000)注入釜内,保持釜内温度80℃,然后将48g偏苯三酸酐加入反应釜内,升温至110℃,反应约3h,取样测试酸值达理论值后,然后注入190g环氧树脂e51,搅拌均匀后加6.19g三苯基膦(tpp)催化剂,130℃恒温反应3h,测试酸值达理论值后,加入2.88g的磷酸,80℃搅拌反应约3h,测试环氧值达到理论环氧值后出料。
[0051]
实施例6a:将1000g熔融脱水后的聚乙二醇单甲醚(分子量为4000)注入釜内,保持釜内温度80℃,然后将48g偏苯三酸酐加入反应釜内,升温至110℃,反应约3h,取样测试酸值达理论值后,然后注入190g环氧树脂e51,搅拌均匀后加6.19g三苯基膦(tpp)催化剂,130℃恒温反应3h,测试酸值达理论值后,加入2.88g的磷酸,80℃搅拌反应约3h后,加入1g氢氧化钠,80度反应1h,测试环氧值达到理论环氧值后出料。
[0052]
实施例7a:将2000g熔融脱水后的聚乙二醇单甲醚(分子量为8000)注入釜内,保持釜内温度100℃,然后将57.6g偏苯三酸酐加入反应釜内,升温至130℃,反应约3h,取样测试酸值达理论值后,然后注入761.25g环氧树脂e20,搅拌均匀后加22.55g三苯基膦(tpp)催化剂,120℃恒温反应3h,测试酸值达理论值后,加入10.1g的磷酸单乙酯,80℃搅拌反应约3h,测试环氧值达到理论环氧值后出料。
[0053]
对比例8a:将2000g溶融脱水后的聚乙二醇单甲醚(分子量为8000)注入釜内,保持釜内温度100℃,然后将53g偏苯三酸酐加入反应釜内,升温至130℃,反应约3h,取样测试酸值达理论值后,注入170g液态环氧树脂e51,搅拌均匀后加6g三苯基膦(tpp)催化剂,130℃恒温反应3h,测试酸值达理论值后出料。
[0054]
环氧树脂水分散体的制备:
[0055]
实施例1b:将400g熔融环氧树脂e20注入分散釜内,维持釜内温度100℃,然后注入活性乳化剂(100g,实施例1a)和溶剂丙二醇甲醚(pmop,70g),800r/min搅拌混合20min;之后降温至75℃,提升转速为1200r/min,2h内滴加373g去离子水(初始1/2水量缓慢滴加),待水滴加完毕,体系降温至50℃出料。分散体测定如下:分散体粒径约为420nm(测试仪器:zetasizer nano zs,测试方法:将分散体分散于去离子水中测试,下同);粘度:1400cp(测试仪器:brookfield粘度计dv1,测定方法:25℃直接测试,下同);固含:53%。
[0056]
实施例2b:将400g熔融环氧树脂e20注入分散釜内,维持釜内温度100℃,然后注入活性乳化剂(44.5g,实施例2a)和溶剂丙二醇甲醚(pmop,72g),800r/min搅拌混合20min;之后降温至75℃,提升转速为1200r/min,2h内滴加355g去离子水(初始1/2水量缓慢滴加),待
水滴加完毕,体系降温至50℃出料。分散体测定如下:分散体粒径约为430nm;粘度:920cp;固含:51%。
[0057]
实施例3b:将400g熔融环氧树脂e20注入分散釜内,维持釜内温度100℃,然后注入活性乳化剂(21g,实施例3a)和溶剂丙二醇甲醚(pmop,71g),800r/min搅拌混合20min;之后降温至75℃,提升转速为1200r/min,2h内滴加334g去离子水(初始1/2水量缓慢滴加),待水滴加完毕,体系降温至50℃出料。分散体测定如下:分散体粒径约为540nm;粘度:1130cp;固含:51%。
[0058]
实施例4b:将400g熔融环氧树脂e20注入分散釜内,维持釜内温度100℃,然后注入活性乳化剂(44.5g,实施例4a)和溶剂丙二醇甲醚(pmop,75g),800r/min搅拌混合20min;之后降温至75℃,提升转速为1200r/min,2h内滴加369g去离子水(初始1/2水量缓慢滴加),待水滴加完毕,体系降温至50℃出料。分散体测定如下:分散体粒径约为550nm;粘度:870cp;固含:50%。
[0059]
实施例5b:将400g熔融环氧树脂e20注入分散釜内,维持釜内温度100℃,然后注入活性乳化剂(34.8g,实施例5a)和溶剂丙二醇甲醚(pmop,75g),800r/min搅拌混合20min;之后降温至75℃,提升转速为1200r/min,2h内滴加343g去离子水(初始1/2水量缓慢滴加),待水滴加完毕,体系降温至50℃出料。分散体测定如下:分散体粒径约为560nm;粘度:850cp;固含:51%。
[0060]
实施例6b:将400g熔融环氧树脂e20注入分散釜内,维持釜内温度100℃,然后注入活性乳化剂(4g,实施例6a)和溶剂丙二醇甲醚(pmop,75g),800r/min搅拌混合20min;之后降温至75℃,提升转速为1200r/min,2h内滴加298g去离子水(初始1/2水量缓慢滴加),待水滴加完毕,体系降温至50℃出料。分散体测定如下:分散体粒径约为660nm;粘度:1850cp;固含:52%。
[0061]
实施例7b:将400g熔融环氧树脂e20注入分散釜内,维持釜内温度100℃,然后注入活性乳化剂(70.6g,实施例7a)和溶剂丙二醇甲醚(pmop,75g),800r/min搅拌混合20min;之后降温至75℃,提升转速为1200r/min,2h内滴加377g去离子水(初始1/2水量缓慢滴加),待水滴加完毕,体系降温至50℃出料。分散体测定如下:分散体粒径约为490nm;粘度:1050cp;固含:51%。
[0062]
对比例8b:将400g熔融环氧树脂e20注入分散釜内,维持釜内温度100℃,然后注入活性乳化剂(90g,实施例8a)和溶剂丙二醇甲醚(pmop,75g),800r/min搅拌混合20min;之后降温至75℃,提升转速为1200r/min,2h内滴加400g去离子水(初始1/2水量缓慢滴加),待水滴加完毕,体系降温至50℃出料。分散体测定如下:分散体粒径约为960nm;粘度:4850cp;固含:51%。
[0063]
环氧树脂水分散体的性能测试:
[0064]
表2
[0065][0066]
表3
[0067][0068]
将按表2配制的水性环氧防锈漆i组分与按表3配置的ii组分以8.5:1的比例混合后,熟化半小时,以干膜厚70-80um的厚度将双组分环氧漆涂布在表面打磨处理过的碳钢板上,室温流平15分钟后,在80℃条件下烘烤30分钟,并在25℃条件下养护7天,得到双组分环氧的固化膜。根据gb/t 1771标准进行耐中性盐雾性能的测定。在规定的测试时间(500h)内,要求板面空白处不生锈,不起泡,板面划口处锈蚀、起泡宽度扩散小于2mm,即可定义为5分,板面空白处不生锈,少量起泡,板面划口处锈蚀扩散小于2mm定义为4分,板面空白处生锈,起泡,板面划口处锈蚀、起泡宽度扩散小于2mm定义为3分。测定结果见表4。
[0069]
表4
[0070]
分散体实施例/对比例1b2b3b4b5b6b7b8b分散体粒径(nm)420430540550560660490960分散体50℃储存时间(天)262623232218257环氧漆耐盐雾(500h)55-555453附着力00000102分散体货架期(月)》15》15》15》15》13》12》15《6
[0071]
从上述性能的对比中可以看出,添加本发明的磷酸或磷酸酯改性的环氧乳化剂,可以有效地降低分散体粒径、提高分散体稳定性以及提高产品的耐盐雾性能。
再多了解一些
本文用于企业家、创业者技术爱好者查询,结果仅供参考。