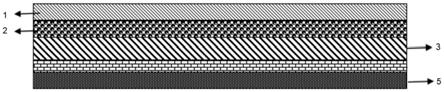
1.本发明涉及柔板与镍片焊接技术领域,涉及一种车载柔板与镍片激光焊接的方法。
背景技术:
2.随着新能源汽车产业的迅猛发展,动力电池柔板(车载柔板-fpc)需求也在迅速起量有望成为未来新的需求增长点,最新数据显示,汽车pcb中,fpc的占比已经由12%提升至15%。目前fpc应用涵盖车灯、显示模组、bms(电池管理系统)/vcu(整车控制器)/mcu(核心功率电子单元)三大动力控制系统、传感器、高级辅助系统等相关场景。
3.其中集成产品ccs(cellscontactsystem),也叫集成母排或者线束板集成件,ccs产品由fpc、塑胶结构件、铜铝排等组成,目前集成产品ccs,大多选用铜基fpc与铝排、塑胶结构件集成,而铜基fpc与铝排不能直接焊接,行业上多采用镍片作为过渡片将铜基fpc与铝排焊接在一起的,而镍片与铜基fpc通过回流焊方式焊接在一起。回流焊方式不但设备占用的空间大,且焊接时间长,产能低,且由于回流炉功率高,长时间工作以及避免焊盘氧化需要通氮气保护焊盘不氧化等,造成更多的能源消耗。
技术实现要素:
4.本发明要解决的技术问题是提供一种焊接时间短,焊接效率高,无需通入氮气保护的车载柔板与镍片激光焊接的方法。
5.为了解决上述技术问题,本发明解决其技术问题所采用的技术方案是:
6.一种车载柔板与镍片激光焊接的方法,包括以下步骤;
7.对铜基柔板进行前处理工艺后,在前处理后的铜基柔板上进行点锡后进行锡膏检查,将镍片贴片至锡膏上,对镍片、铜基柔板以及锡膏进行预热处理后,再对铜基柔板与镍片进行激光焊接。
8.进一步地,对铜基柔板的前处理工艺,包括微蚀处理、贴膜处理、曝光处理、显影处理、铜蚀刻处理、去膜处理、再次微蚀处理、贴保护膜处理或者osp制程处理中的一个或者多个处理步骤组合进行。
9.进一步地,所述铜基柔板中的铜层厚度为12-70um;所述铜基柔板中的pi层厚度为25-50um;所述镍片厚度为250-450um。
10.进一步地,对镍片、铜基柔板以及锡膏的预热处理,包括:
11.将镍片、铜基柔板以及锡膏放置在激光焊机平台上,采用激光对镍片、铜基柔板以及锡膏进行加热一段时间后,再进行激光焊接。
12.进一步地,采用激光对镍片、铜基柔板以及锡膏进行多段加热方式或者直接加热方式,其加热温度为150℃-220℃,加热时间为10-60s。
13.进一步地,对镍片、铜基柔板以及锡膏的预热处理,包括:
14.对镍片、铜基柔板以及锡膏采用恒温方法进行加热,其加热温度为180-220℃,加
热时间为20-60s。
15.进一步地,所述恒温方法可采用热风加热方式、红外加热方式、热平台加热方式或者热炉加热方式中的一种或者多种进行加热。
16.本发明的有益效果:
17.本发明中采用铜基柔板与镍片进行激光焊接方式取代回流焊方式,具有焊接时间短,焊接效率高,且能源损耗小等优点,相比于传统回流焊需要通氮气保护,采用激光焊接无需通入氮气保护,同时大大减小了设备占用空间;对镍片、铜基柔板以及锡膏进行预热处理,可使得助焊剂缓慢挥发,有效避免助焊剂遇高热因急速挥发造成锡膏飞溅造成铜焊盘露铜和锡珠等问题。
附图说明
18.图1是本发明的一种集成母排示意图。
19.图2是本发明的激光焊接工艺与传统焊接工艺对比例。
20.图中标号说明:1、镍片;2、锡膏;3、铜层;5、pi层;
具体实施方式
21.下面结合具体实施例对本发明作进一步说明,以使本领域的技术人员可以更好地理解本发明并能予以实施,但所举实施例不作为对本发明的限定。
22.实施例1
23.参阅图1,一种车载柔板与镍片激光焊接的方法,包括以下步骤;
24.首先对铜基柔板的前处理工艺,包括微蚀处理、贴膜处理、曝光处理、显影处理、铜蚀刻处理、去膜处理、再次微蚀处理、贴保护膜处理或者osp制程(铜面保护剂)处理中的一个或者多个处理步骤组合进行,再对铜基柔板进行前处理工艺后,在前处理后的铜基柔板上进行点锡后进行锡膏检查,将镍片贴片至锡膏上,所述铜基柔板为铜基单层柔板,所述铜基柔板中的铜层厚度为50um;所述铜基柔板中的pi层厚度为40um;所述镍片厚度为250um;对镍片、铜基柔板以及锡膏进行预热处理后,再对铜基柔板与镍片进行激光焊接。
25.本实施例中一个较优选的方案为将镍片、铜基柔板以及锡膏放置在激光焊机平台上,采用激光对镍片、铜基柔板以及锡膏进行加热一段时间后,其可按温度曲线的方式设置激光的加热温度和时间,用设置好的温度曲线对镍片和锡膏一起预热,再进行激光焊接,其焊接温度为240-270℃,焊接时间为1-5s;即每个焊点时间约为11-65s。
26.所述激光加热为采用温度曲线方式调整不同的温度和时间进行激光预热,包括不同数量段的温度曲线。
27.采用激光对镍片、铜基柔板以及锡膏进行多段加热方式或者直接加热方式,其加热温度为150℃-220℃,加热时间为10-60s。
28.即激光多段加热方式是对镍片、铜基柔板以及锡膏的加热温度以及时间预先设置多段,即第一段:加热温度设置为150℃,加热时间为10s;第二段:加热温度设置为170℃,加热时间为5s;第三段:加热温度设置为180℃,加热时间为5s;第四段:加热温度设置为200℃,加热时间为5s;第五段:加热温度设置为205℃,加热时间为10s,上述方式进行预热处理后,在进行激光焊接,激光焊接温度为255℃,焊接时间为2.5s。
29.激光直接加热方式是对镍片、铜基柔板以及锡膏的加热温度以及时间预先设置一段,即加热温度设置为200℃,加热时间为30s,上述方式进行预热处理后,在进行激光焊接,激光焊接温度为270℃,焊接时间为3s。
30.本实施例中另一个较优选的方案为对镍片、铜基柔板以及锡膏采用恒温方法进行加热,其加热温度为220℃,加热时间为40s;所述恒温方法可采用热风加热方式、红外加热方式、热平台加热方式或者热炉加热方式中的一种或者多种进行加热。
31.采用恒温方法进行与热处理后,再进行激光焊接,其焊接温度为270℃,其焊接时间较短,每个焊点时间约为1s。
32.本发明中采用铜基柔板与镍片进行激光焊接方式取代回流焊方式,具有焊接时间短,焊接效率高,且能源损耗小等优点,激光焊接平台设备尺寸小,相比于传统回流焊需要通氮气保护,采用激光焊接无需通入氮气保护,同时大大减小了设备占用空间;对镍片、铜基柔板以及锡膏进行预热处理,可使得助焊剂缓慢挥发,有效避免助焊剂遇高热因急速挥发造成锡膏飞溅造成铜焊盘露铜和锡珠等问题。
33.瞬时温度太高会导致锡膏中助焊剂快速挥发的飞溅问题会造成焊珠飞溅、镍片开口处露铜和助焊剂污染镍片表面等三个问题。
34.对镍片、铜基柔板以及锡膏进行预热处理,还可对烘干焊盘去除镍片、铜基柔板或者锡膏上的水分,避免水分蒸发造成的锡膏飞溅问题。
35.对镍片、铜基柔板以及锡膏的预热温度为150℃-220℃,预热温度太高,会使得铜焊盘上的osp保护剂挥发,影响激光焊接的质量。
36.现有普通的激光焊接,由于功率或温度过高导致的镍片损伤的问题;若是采用低温度控制的直接焊接方式,虽然达到了焊接拉力要求,但因焊接瞬时温度太高会导致锡膏中助焊剂快速挥发,从而引发锡膏飞溅,形成裸露铜焊盘的问题,以及助焊剂溢出导致的镍片外观不良问题等,同时一般回流焊方式有6-10米长的回流炉,且焊接时间为10-15分钟,一批次约焊接60pcs镍片与铜基fpc焊盘。单点时间约为10-15秒。
37.实施例2
38.一种车载柔板与镍片激光焊接的方法,包括以下步骤;
39.首先对铜基柔板的前处理工艺,包括微蚀处理、贴膜处理、曝光处理、显影处理、铜蚀刻处理、去膜处理、再次微蚀处理、贴保护膜处理或者osp制程(铜面保护剂)处理中的一个或者多个处理步骤组合进行,再对铜基柔板进行前处理工艺后,在前处理后的铜基柔板上进行点锡后进行锡膏检查,将镍片贴片至锡膏上,所述铜基柔板为铜基单层柔板,所述铜基柔板中的铜层厚度为20um;所述铜基柔板中的pi层厚度为50um;所述镍片厚度为450um;对镍片、铜基柔板以及锡膏进行预热处理后,再对铜基柔板与镍片进行激光焊接。
40.本实施例中一个较优选的方案为将镍片、铜基柔板以及锡膏放置在激光焊机平台上,采用激光对镍片、铜基柔板以及锡膏进行加热一段时间后,其可按温度曲线的方式设置激光的加热温度和时间,用设置好的温度曲线对镍片和锡膏一起预热,再进行激光焊接,其焊接温度为240-270℃,焊接时间为1-5s;即每个焊点时间约为11-65s。
41.采用激光对镍片、铜基柔板以及锡膏进行多段加热方式或者直接加热方式,其加热温度为150℃-220℃,加热时间为10-60s。
42.激光多段加热方式是对镍片、铜基柔板以及锡膏的加热温度以及时间预先设置多
段,即第一段:加热温度设置为160℃,加热时间为7s;第二段:加热温度设置为180℃,加热时间为8s;第三段:加热温度设置为190℃,加热时间为5s;第四段:加热温度设置为200℃,加热时间为6s;第五段:加热温度设置为215℃,加热时间为8s,上述方式进行预热处理后,在进行激光焊接,激光焊接温度为270℃,焊接时间为3s。
43.激光直接加热方式是对镍片、铜基柔板以及锡膏的加热温度以及时间预先设置一段,即加热温度设置为220℃,加热时间为45s,上述方式进行预热处理后,在进行激光焊接,激光焊接温度为240℃,焊接时间为5s。
44.本实施例中另一个较优选的方案为对镍片、铜基柔板以及锡膏采用恒温方法进行加热,其加热温度为210℃,加热时间为60s;所述恒温方法可采用热风加热方式、红外加热方式、热平台加热方式或者热炉加热方式中的一种或者多种进行加热。
45.采用恒温方法进行与热处理后,再进行激光焊接,其焊接温度为240℃,其焊接时间较短,每个焊点时间约为4.5s。
46.实施例3
47.一种车载柔板与镍片激光焊接的方法,包括以下步骤;
48.首先对铜基柔板的前处理工艺,包括微蚀处理、贴膜处理、曝光处理、显影处理、铜蚀刻处理、去膜处理、再次微蚀处理、贴保护膜处理或者osp制程(铜面保护剂)处理中的一个或者多个处理步骤组合进行,再对铜基柔板进行前处理工艺后,在前处理后的铜基柔板上进行点锡后进行锡膏检查,将镍片贴片至锡膏上,所述铜基柔板为铜基单层柔板,所述铜基柔板中的铜层厚度为35um;所述铜基柔板中的pi层厚度为30um;所述镍片厚度为300um;对镍片、铜基柔板以及锡膏进行预热处理后,再对铜基柔板与镍片进行激光焊接。
49.本实施例中一个较优选的方案为将镍片、铜基柔板以及锡膏放置在激光焊机平台上,采用激光对镍片、铜基柔板以及锡膏进行加热一段时间后,其可按温度曲线的方式设置激光的加热温度和时间,用设置好的温度曲线对镍片和锡膏一起预热,再进行激光焊接,其焊接温度为240-270℃,焊接时间为1-5s;即每个焊点时间约为11-65s。
50.采用激光对镍片、铜基柔板以及锡膏进行多段加热方式或者直接加热方式,其加热温度为150℃-220℃,加热时间为10-60s。
51.激光多段加热方式是对镍片、铜基柔板以及锡膏的加热温度以及时间预先设置多段,即第一段:加热温度设置为150℃,加热时间为10s;第二段:加热温度设置为160℃,加热时间为5s;第三段:加热温度设置为180℃,加热时间为5s;第四段:加热温度设置为190℃,加热时间为5s;第五段:加热温度设置为205℃,加热时间为10s,上述方式进行预热处理后,在进行激光焊接,激光焊接温度为255℃,焊接时间为2.5s。
52.激光直接加热方式是对镍片、铜基柔板以及锡膏的加热温度以及时间预先设置一段,即加热温度设置为190℃,加热时间为20s,上述方式进行预热处理后,在进行激光焊接,激光焊接温度为255℃,焊接时间为2s。
53.本实施例中另一个较优选的方案为对镍片、铜基柔板以及锡膏采用恒温方法进行加热,其加热温度为200℃,加热时间为30s;所述恒温方法可采用热风加热方式、红外加热方式、热平台加热方式或者热炉加热方式中的一种或者多种进行加热。
54.采用恒温方法进行与热处理后,再进行激光焊接,其焊接温度为255℃,其焊接时间较短,每个焊点时间约为2s。
55.采用激光或者恒温方法对镍片、铜基柔板以及锡膏进行加热后激光焊接,可焊接方式大大减小了设备占用空间和焊接时间,采用多个激光焊头的方式可以提高产能;且激光焊接平台不需要通氮气,并且附加预热处理段和激光的功率小,能源损耗小。
56.现有回流焊方式有6-10米长的回流炉,且焊接时间为10-15分钟,一批次约焊接60pcs镍片与铜基fpc焊盘,其单点时间约为10-15秒,单点时间是指贴片后,单片镍片与铜基fpc焊盘焊接时间。
57.本发明在激光焊接前采用预热出库的方式作用是将镍片、锡膏和焊盘一起预热,在较高温度作用下,助焊剂将缓慢挥发,可以使得助焊剂先于焊接时挥发,避免助焊剂遇高热因急速挥发造成的飞溅问题,而飞溅问题会造成焊珠飞溅、镍片开口处露铜和助焊剂污染镍片表面等三个问题。
58.参阅图2,实施案例1:
59.采用本发明的激光预热并焊接:采用6段温度曲线,其中1-5段为预热段,第6段为焊接段。具体参数为:第1段,温度设置150℃,时间10秒;第2段,温度设置160℃,时间5秒;第3段,温度设置180℃,时间5秒;第4段,温度设置190℃,时间5秒;第5段,温度设置205℃,时间10秒;第6段,温度设置255℃,时间2.5秒。其中预热总时间为35秒,焊接时间为2.5秒。总时间为:37.5秒。单焊点时间为:37.5秒。本案例采用1个激光焊接头。
60.实施案例2:
61.采用本发明的激光预热并焊接:采用2段温度曲线,其中1段为预热段,第2段为焊接段。具体参数为:第1段,温度设置190℃,时间20秒;第6段,温度设置255℃,时间2.0秒。其中预热总时间为30秒,焊接时间为2.0秒。总时间为:22秒。单点时间为:22秒。本案例采用1个激光焊接头。
62.实施案例3:
63.采用本发明的热炉预热并激光焊接:采用热炉预热参数为:温度为恒温200℃,时间30秒;采用的激光焊接参数为:温度设置255℃,时间2.0秒。其中预热总时间为20秒/60pcs,焊接时间为2.0秒/pcs。总时间为:22秒。单点时间为:2.3秒。本案例采用1个激光焊接头。
64.对比案例1:
65.无预热直接激光焊接:采用的激光焊接参数为:温度设置255℃,时间2.0秒。总时间为:2.0秒。单点时间为:2秒。本对比案例采用1个激光焊接头。
66.对比案例2:
67.传统回流焊焊接:采用的12段温度曲线,其中1-7段为预热段,第8段为恒温段,第9-11段为焊接段,第12段为冷却段。具体参数为:第1段,温度设置150℃,时间150秒;第2段,温度设置165℃,时间30秒;第3段,温度设置175℃,时间30秒;第4段,温度设置185℃,时间40秒;第5段,温度设置195℃,时间30秒;第6段,温度设置205℃,时间30秒;第7段,温度设置215℃,时间30秒;第8段,温度设置235℃,时间30秒;第9段,温度设置240℃,时间20秒;第10段,温度设置255℃,时间20秒;第11段,温度设置240℃,时间20秒;第12段,温度设置50℃,时间180秒。其中预热(20-217℃)总时间为340秒,恒温(217-235℃)总时间为30秒,焊接时间(235-255℃)为60秒,冷却时间为180秒。总时间为:610秒/60pcs,单点时间为:10秒。
68.以上所述实施例仅是为充分说明本发明而所举的较佳的实施例,本发明的保护范
围不限于此。本技术领域的技术人员在本发明基础上所作的等同替代或变换,均在本发明的保护范围之内。本发明的保护范围以权利要求书为准。
再多了解一些
本文用于企业家、创业者技术爱好者查询,结果仅供参考。