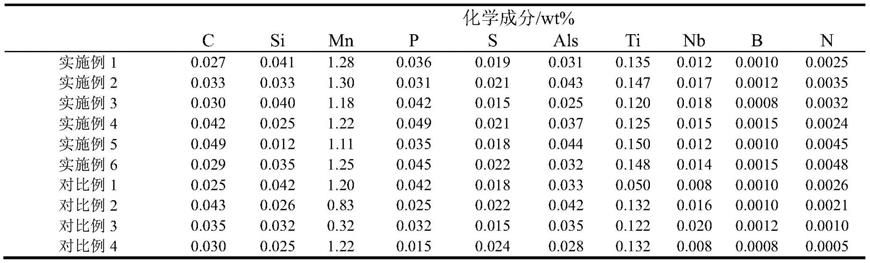
1.本发明属于金属材料冶炼领域,具体涉及一种双面搪瓷用钢及其制造方法和应用。
背景技术:
2.搪瓷钢是由优质钢板(基板)与特种功能无机非金属材料经新型静电干粉涂搪工艺涂搪及高温烧成的复合材料。它既有钢板等基材的坚韧、抗冲击等特性,又有无机搪瓷层超强耐酸碱、耐久、耐磨、不燃、易洁、美观和无辐射等特点,广泛地应用于环保、轻工、家电、冶金、化工、建筑等行业。随着人们对搪瓷制品的要求日益提高,对具有超深冲性能优良涂搪性能的搪瓷钢板的需求十分迫切。
3.在环保行业中,一些污、废水处理设施的储水罐、处理池等结构件均多采用搪瓷拼装罐,通过铆接而成,因搪瓷拼装罐所处环境复杂,其内表面受内侧污水、反应水的腐蚀,外表面处于空气中受到外界腐蚀,因此拼装板需双面搪瓷处理,这样才能具有较强耐腐蚀性能。随着对安全性与效益性的考虑,一些储水罐体的容量越来越大,从过去的几千立方逐渐扩展到几万立方,因此对容器的钢板的强度提出了更高的要求。对于5000m3以上污水处理罐需两次搪烧烧后屈服强度稳定达到420mpa以上,目前对于两次搪烧后样板能够稳定达到420mpa以上的相关研究较少。
4.因釉料中存在h2o,钢板在搪烧处理过程中会发生fe h2o
→
feo 2[h]反应,生成的大量[h]在釉层和基体的界面处聚集,极易产生鳞爆缺陷,导致整个部件报废。目前主要通过控制基板中的“氢陷阱”数量,提高基板的抗鳞爆性能。双面搪瓷钢相对单面搪瓷具有更高要求,单面搪瓷钢仅需单面涂搪,而双面搪瓷钢需双面涂搪,致使在搪烧过程中会产生2倍[h]原子,钢板需要容纳2倍的[h]原子量,因此更容易导致鳞爆,为解决该问题,双面搪瓷钢需要加倍的“氢陷阱”数量才能保证抗鳞爆性能。同时热轧双面搪瓷钢板经过钢板正反两面涂搪后,经过两次搪烧,第一次搪烧温度在860~930℃、第二次搪烧温度在850~900℃,该温度下钢板已发生相变,组织会发生再结晶,位错、晶粒尺寸、原子的富集度会重新分布,以及钢板中部分析出物会重新回熔和析出,这必然导致基板强度也会随之降低。
[0005]
如公开号为cn102796955b的发明专利《搪瓷钢用热轧中厚板及其制造方法》,公开了一种热轧搪瓷用钢,通过控制c元素分布,以及添加v、ti等微合金,控制轧制工艺,获得具有一定抗鳞爆性能的钢,但其搪烧后的屈服强度较低,为为250~290mpa。又如公开号为cn109423576a的发明专利《一种搪后40 0mpa级双面搪瓷用热轧钢板及其制造方法》,公开一种搪烧后强度>400mpa级的热轧双面搪瓷钢板,其化学成分(wt%)c:0.08~0.15、si≤0.10、mn:1.0~2.0、p:0.06~0.10、s≤0.006、ti:0.02~0.08、nb:0.01~0.05、v:0.020~0.055、als:0.01~0.045、n≤0.008、mo:0.015~0.30,当产品厚度>8mm时,添加b:0.0005~0.005,余量为fe和不可避免的其他杂质元素。该专利采用低c,高mn、以及高p成分体系提高搪烧后钢板强度,但由于p元素偏高,易导致偏析,铸坯分层等问题,进而降低性能,同时该专利添加的v、mo等均属于贵金属,提高材料的性能,稳定偏析作用。其搪烧后其屈服强度
为400~460mpa左右,未能稳定>420mpa。再如公开号为cn108950423b的发明专利《一种热轧双面搪瓷用高强钢、双面搪瓷钢及其制造方法》,其化学成分(wt%)c:0.08~0.15、si:0.15~0.5、mn:1.2~2.5、p:≤0.03、s≤0.006、ti:0.01~0.06、nb:0.01~0.10、v:0.02~0.10、als:0.006~0.08、n≤0.006、cr:0.15~0.65、mo:0.03~0.15、cu:0.1~0.35、余量为fe和不可避免的其他杂质元素,其搪烧后仍具有高强度,并具有良好的抗鳞爆性能。虽然该专利搪烧后屈服强度也达到了450~500mpa,但其添加成分种类较多,不利于现场实际操作。
技术实现要素:
[0006]
1.发明目的
[0007]
本发明的目的是提供一种双面搪瓷用钢及其制造方法和应用,该双面搪瓷用钢厚度为3.0~10.0mm,屈服强度≥480mpa,抗拉强度≥560mpa,延伸率≥15%,并具有优良的抗鳞爆性能,其氢渗透时间tb≥30min(换算成1mm),经过两次搪烧后,其屈服强度>420mpa,抗拉强度≥500mpa,延伸率≥20%,并具有良好密着性,可用环保行业拼装罐中。具体地,该钢采用低c、微b、高ti和高p的成分体系,利用mn、p的固溶强化结合控制ti、nb析出强化提高钢板搪烧后的强度,同时利用微b来避免由高p造成的组织成分偏析、性能降低等问题,通过轧制工艺,控制ti、nb、fetip、bn等的析出,既可以弥补搪烧后强度降低,又可以形成大量“氢陷阱”提高钢板的抗鳞爆性能。
[0008]
2.技术方案
[0009]
为了解决上述问题,本发明所采用的技术方案如下:
[0010]
本发明提供了一种双面搪瓷用钢,该钢的主要化学成分重量百分比为:
[0011]
c:0.025~0.049%;si:≤0.05%;mn:1.1~1.3%;p:0.031~0.049%;s:0.015~0.025%;ti:0.12~0.15%;nb:0.01~0.02%;als:0.025~0.045%;n:0.002~0.005%;b:0.0008~0.0016%;其余为fe和不可避免的杂质,其中成分体系需满足:
[0012]
公式1:公式1表示在本发明成分体系下p、mn、si的固溶强化作用对强度的贡献作用系数;
[0013]
公式2:公式2表示在本发明成分体系下ti、nb析出tin、tic、nbn、nbc以及ti4c2s2的强度贡献系数;
[0014]
其中:
[0015]
碳(c):是钢中最经济的强化元素,主要通过固溶强化和析出强化对提高钢的强度,在组织中易形成珠光体、贝氏体组织,另外,c会与ti、nb等元素形成第二相粒子,包括tic、ti(c、n)、nbc、nb(c、n)等复合粒子,这些粒子会均匀分布于组织中,在粒子和基体的界面处会形成大量共格与非共格界面可以储存大量氢原子,同时这些粒子会带来析出强化效果;但c元素不宜过高,在搪烧时c会与h2o发生反应,形成co和co2,导致釉层出现大量气孔;同时,c元素过高在原板中会形成大量碳化物,引起组织畸变,带来位错强化较高,随搪烧过程,组织发生了相变和再结晶过程,位错消失,晶粒长大,以及部分析出物重新形成,引发强度降低,因此c元素控制0.025~0.049%范围;
[0016]
硅(si):是一种强化元素,可以在铁素体中起到固溶作用,但si含量过高会影响钢板的塑性,以及表面的密着性能,因此si含量不易太高,控制≤0.050%;
[0017]
锰(mn):是强化基板的重要元素之一,可以有效提高钢板的强度,同时mn元素经济性较好,被广泛添加在钢板中,其可以扩大奥氏体相区,降低a
c3
线,在搪烧过程增加奥氏体溶解的氢含量,在后续冷却过程增加鳞爆可能性,mn含量控制1.1~1.3%;
[0018]
磷(p):一种固溶强化的元素,p在组织中存在两种形式,一种是以置换固溶方式存在,另一种以p的析出物fetip等形式存在,因为p原子直径比基体的原子半径大的多,会引起晶格畸变,从而增加“氢陷阱”数量与吸引力,同时畸变的晶格引起的应力场和应变场可以阻碍位错运动,增加钢板的强度,该位错不会因为温度的影响而发生变化,因此可以提高钢板搪烧后的强度;但p元素容易在晶界偏聚,导致基板塑韧性降低。因此本专利添加了微量b,可以优先在晶界处聚集,避免p的偏聚,可以降低部分p偏聚所带来的缺点;同时p元素含量不能过高,过高会导致连铸时中心偏析,进而导致铸坯分层,因此本专利控制p元素含量0.031~0.049%;
[0019]
硫(s):通常会与mn结合形成mns,同时如果钢中存在ti元素,可以形成ti(c、s)复合析出物,可以提高钢板的抗鳞爆性能;但硫含量过高会引起横向塑性和韧性差,因此本专利控制需控制s元素含量0.015~0.025%;
[0020]
钛(ti):容易与c、n复合,形成多种tin、tic、ti(c、n)以及ti(c、s)析出物,对钢板的抗鳞爆性能提升有很大作用;同时通过热轧工艺控制可以使析出物均匀分布于组织中,通过析出强化方式提高钢板的强度;同时避免组织中形成大量的tic析出物,该析出物主要在600~1000℃会发生回熔,因此在在搪烧过程会影响再次形成,进而影响搪烧后的强度,要优先控制难回熔性粒子析出,如tin、ti4s2c2等其它析出物,因此本专利ti:0.12~0.15%;
[0021]
铌(nb):可以有效的细化晶粒,可以在钢中置换固溶原子,在组织中会钉扎晶粒边界,进而降低晶粒的尺寸大小;同时nb形成的析出物nbn、nbc等可以起析出强化作用,提高钢板的强度,也可作为“氢陷阱”,提高抗鳞爆性能,本专利控制nb:0.01~0.02%;
[0022]
铝(al):可作为主要脱氧剂,同时铝对细化晶粒也有一定作用。铝的缺点是影响钢的热加工性能、焊接性能和切削加工性能。同时al在钢中已形成氧化物,降低材料的塑韧性。本发明中al含量控制范围为0.025~0.045%;
[0023]
氮(n):能提高钢的强度,低温韧性和焊接性,增加时效敏感性,会和ti、nb等形成析出物,提高抗鳞爆性能。本发明中n百分含量控制范围为0.002~0.005%;
[0024]
硼(b):适量的b元素可增加第二相形核点,提高钢板的抗鳞爆性能,并且b与c、n复合相增加的形核点可促进晶粒的形核,降低晶粒尺寸,提高钢板的强度,同时bn在1000~1200℃开始析出,在800~900℃完全析出,可通过加热温度、开轧温度、终轧温度控制bn的析出,并且在两次搪烧时bn并不会发生回熔,避免bn回熔引起的强度降低,保证了搪烧后的钢板强度;同时b元素可以优先在晶界处聚集,填补在“空位”、“缺陷”处,避免p元素在此位置的聚集、导致钢的塑韧性降低;本专利b:0.0008~0.0016%。
[0025]
优选地,上述双面搪瓷用钢的主要化学成分重量百分比为:
[0026]
c:0.027%;si:0.041%;mn:1.28%;p:0.036%;s:0.019%;ti:0.135%;nb:0.012%;als:0.031%;n:0.0025%;b:0.0010%;其余为fe和不可避免的杂质,此时:
[0027]
公式1:
[0028]
公式2:
[0029]
优选地,上述双面搪瓷用钢的主要化学成分重量百分比为:
[0030]
c:0.033%;si:0.033%;mn:1.3%;p:0.031%;s:0.021%;ti:0.147%;nb:0.017%;als:0.043%;n:0.0035%;b:0.0012%;其余为fe和不可避免的杂质,此时:
[0031]
公式1:
[0032]
公式2:
[0033]
优选地,上述双面搪瓷用钢的主要化学成分重量百分比为:
[0034]
c:0.030%;si:0.04%;mn:1.18%;p:0.042%;s:0.015%;ti:0.12%;nb:0.01~0.02%;als:0.025%;n:0.0032%;b:0.0008;其余为fe和不可避免的杂质,此时:
[0035]
公式1:
[0036]
公式2:
[0037]
优选地,上述双面搪瓷用钢的主要化学成分重量百分比为:
[0038]
c:0.0042%;si:0.025%;mn:1.22%;p:0.049%;s:0.021%;ti:0.125%;nb:0.015%;als:0.037%;n:0.0024%;b:0.0015%;其余为fe和不可避免的杂质,此时:
[0039]
公式1:
[0040]
公式2:
[0041]
优选地,上述双面搪瓷用钢的主要化学成分重量百分比为:
[0042]
c:0.049%;si:0.012%;mn:1.11%;p:0.035%;s:0.018%;ti:0.15%;nb:0.012%;als:0.044%;n:0.0045%;b:0.0010%;其余为fe和不可避免的杂质,此时:
[0043]
公式1:
[0044]
公式2:
[0045]
优选地,上述双面搪瓷用钢的主要化学成分重量百分比为:
[0046]
c:0.029%;si:0.035%;mn:1.25%;p:0.045%;s:0.022%;ti:0.148%;nb:0.014%;als:0.032%;n:0.0048%;b:0.0015%;其余为fe和不可避免的杂质,此时:
[0047]
公式1:
[0048]
公式2:
[0049]
优选地,上述双面搪瓷用钢,其屈服强度≥480mpa,抗拉强度≥560mpa,延伸率≥15%,氢渗透时间tb≥30min(换算成1mm)。
[0050]
本发明还提供了上述一种双面搪瓷用钢的制备方法,包括如下步骤:
[0051]
s1:铁水预处理,要求前扒渣和后扒渣;铁水脱硫后目标硫含量小于0.015%;
[0052]
s2:转炉冶炼,出钢前脱氧合金;
[0053]
s3:rh,调整化学成分至目标值,且保证净循环时间不小于6min;
[0054]
s4:连铸,中包目标温度控制在液相线温度以上20~35℃;
[0055]
s5:热轧工艺控制,为规避板坯表面及边角部出现裂纹进而导致热轧后的表面缺陷,连铸后采用热装轧制,板坯入加热轧炉表面温度≥400℃;出炉温度:1240~1260℃,使钢种ti、nb与c、s、n、p等元素充分的回熔,有利于后续热轧工艺控制第二相的重新析出;7机架热连轧,开轧温度为1080~1150℃,采用高的开轧温度,使组织中存在大量的形核点以及形变能,促进第二相形核,增加形核速率,同时增加组织中存在位错、空位等缺陷,可以增加mn、p、si等元素的固溶量,提供钢板的强度;终轧温度870~930℃,高的终轧温度有利于组织发生相变,促使铁素体晶粒更细,促进析出物析出,这些位置也是重要的形核位置;终轧后冷速控制25~60℃/s至卷取温度600~700℃,较高的冷速可以增加过冷度,促进析出物在缺陷位置大量形核,提高析出物的数量,降低析出物尺寸,有利于析出强化的效果;最终轧制成最终目标厚度。
[0056]
优选地,上述目标厚度为3.0~10.0mm。
[0057]
本发明还提供了上述双面搪瓷用钢在制备双面搪瓷钢中的应用,该双面搪瓷用钢经过两次搪烧,第一次搪烧860~930℃,第二次搪烧850~900℃,两次搪烧时间均为6~10min。
[0058]
优选地,上述双面搪瓷钢屈服强度>420mpa,抗拉强度≥500mpa,延伸率≥20%。
[0059]
3.有益效果
[0060]
本发明与现有技术相比,其有益效果在于:
[0061]
(1)本发明提供的一种双面搪瓷用钢,其屈服强度≥480mpa,抗拉强度≥560mpa,延伸率≥15%,并具有优良的抗鳞爆性能,其氢渗透时间tb≥30min(换算成1mm)。该钢采用低c、微b、高ti、高p的成分体系,利用mn、p的固溶强化结合控制ti、nb析出强化提高钢板搪烧后的强度,同时利用微b来避免由高p造成的组织成分偏析、性能降低等问题,通过轧制工艺,控制ti、nb、fetip、bn等的析出,既可以弥补搪烧后强度降低,又可以形成大量“氢陷阱”提高钢板的抗鳞爆性能。经过两次搪烧后,其屈服强度>420mpa,抗拉强度≥500mpa,延伸率≥20%,并具有良好密着性,可用环保行业拼装罐中。
[0062]
(2)本发明提供的一种双面搪瓷用钢及其制备方法,未采用cu、mo、v、cr等微合金元素,避免了cu可能引起的cu脆,mo、v和cr等元素引起的现场炼钢工艺复杂化问题带来的不必要的工艺控制,其制造简便,成本低廉、经济效益高。
[0063]
(3)本发明提供的一种双面搪瓷钢,采用本发明的双面搪瓷用钢,其屈服强度稳定≥420mpa,能够满足5000m3以上污水处理罐的要求。
附图说明
[0064]
图1是实施例1中双面搪瓷用钢金相组织(500倍);
[0065]
图2是实施例2中双面搪瓷用钢金相组织(500倍);
[0066]
图3是实施例3中双面搪瓷用钢金相组织(500倍);
[0067]
图4是实施例4中双面搪瓷用钢金相组织(500倍);
[0068]
图5是实施例5中双面搪瓷用钢金相组织(500倍);
[0069]
图6是实施例6中双面搪瓷用钢金相组织(500倍);
[0070]
图7是实施例1中双面搪瓷用钢二次搪烧后金相组织(500倍);
[0071]
图8是实施例2中双面搪瓷用钢二次搪烧后金相组织(500倍);
[0072]
图9是实施例3中双面搪瓷用钢二次搪烧后金相组织(500倍);
[0073]
图10是实施例4中双面搪瓷用钢二次搪烧后金相组织(500倍);
[0074]
图11是实施例5中双面搪瓷用钢二次搪烧后金相组织(500倍);
[0075]
图12是实施例6中双面搪瓷用钢二次搪烧后金相组织(500倍);
[0076]
图13是实施例2中搪瓷结果(双面无鳞爆);
[0077]
图14是实施例3中搪瓷结果(双面无鳞爆);
[0078]
图15是实施例3中密着性结果(一级);
[0079]
图16是实施例6中密着性结果(一级)。
具体实施方式
[0080]
下面结合具体实施例对本发明进一步进行描述。
[0081]
需要说明的是,除非另有定义,本文所使用的所有的技术和科学术语与属于本发明的技术领域的技术人员通常理解的含义相同。
[0082]
实施例中未注明具体条件者,按照常规条件或制造商建议的条件进行。所用试剂或仪器未注明生产厂商者,均为可以通过市售购买获得的常规产品。
[0083]
实施例
[0084]
本实施例提供本发明的双面搪瓷用钢、双面搪瓷钢及对比,各实施例及对比例的化学成分如表1所示,其余为必可避免的杂质和fe。
[0085]
表1实施例及对比例的化学成分
[0086][0087]
上述实施例及对比例的成分配比如表2所示:
[0088]
表2实施例及对比例的成分配比
[0089][0090]
上述实施例及对比例的制备方法,其中实施例1的双面搪瓷用钢的制备方法为:
[0091]
s1:铁水预处理,要求前扒渣和后扒渣;铁水脱硫后目标硫含量小于0.015%;
[0092]
s2:转炉冶炼,出钢前脱氧合金;
[0093]
s3:rh,调整化学成分至目标值,且保证净循环时间不小于6min;
[0094]
s4:连铸,中包目标温度控制在液相线温度以上20~35℃;
[0095]
s5:热轧工艺控制,入加热轧炉表面温度450℃;出炉温度:1242℃,使钢种ti、nb与c、s、n、p等元素充分的回熔,有利于后续热轧工艺控制第二相的重新析出;7机架热连轧,开轧温度为1098℃,采用高的开轧温度,使组织中存在大量的形核点以及形变能,促进第二相形核,增加形核速率,同时增加组织中存在位错、空位等缺陷,可以增加mn、p、si等元素的固溶量,提供钢板的强度;终轧温度915℃,高的终轧温度有利于组织发生相变,促使铁素体晶粒更细,促进析出物析出,这些位置也是重要的形核位置;终轧后冷速控制35℃/s至卷取温度650℃,较高的冷速可以增加过冷度,促进析出物在缺陷位置大量形核,提高析出物的数量,降低析出物尺寸,有利于析出强化的效果;最终轧制成最终目标厚度。
[0096]
实施例2-6及对比例的双面搪瓷用钢的制备步骤与实施例1的双面搪瓷用钢的制备步骤相似,区别在于具体的参数设置,其具体工艺参数如表3所示:
[0097]
表3实施例及对比例的双面搪瓷用钢的制备工艺参数
[0098]
[0099][0100]
上述实施例及对比例的力学性能如表4所示:
[0101]
表4实施例及对比例的力学性能
[0102][0103]
上述实施例及对比例的氢渗透时间如表5所示(实验方法采用国际标准《iso17081》):
[0104]
表5实施例及对比例的氢渗透时间
[0105][0106]
根据实验结果,本发明专利的氢渗透实验结果要远远好于对比例,且氢渗透时间(换算成1mm)>30min。同时根据实际搪瓷效果(见附图1-16,实施例中双面搪瓷用钢金相组织、双面搪瓷用钢二次搪烧后金相组织、双面无鳞爆的搪瓷结果、一级密着性结果)可知,本专利实施后得到的热轧双面搪瓷钢具有良好的抗鳞爆性能和密着性能。
[0107]
上述实施例可以看出,采用化学成分满足本专利设计要求的实施例1~6,利用本专利方法制备的热轧双面搪瓷钢板,厚度3.0~10.0mm,制备的双面搪瓷用钢屈服强度≥480mpa,抗拉强度≥560mpa,延伸率≥15%,该双面搪瓷用钢经过两次搪烧(第一次搪烧860~930℃,第二次搪烧850~900℃,两次搪烧时间均为6~10min)后,屈服强度仍能稳定>420mpa以上,抗拉强度≥500mpa,延伸率≥20%,且具有优良的抗鳞爆性能,氢渗透时间:tb≥30min(换算成1mm)。如实施例1,获得热轧双面搪瓷钢板,其屈服强度602mpa,抗拉强度707mpa,延伸率26.5%,形成的组织为多边形铁素体,且晶粒度≥8.0,同时经过两次搪烧后,屈服强度430mpa,抗拉强度506mpa,延伸率34.5%,同时搪烧后的晶粒度>8.0,实验钢板双面搪瓷不鳞爆,氢渗透时间tb>30min。
[0108]
上述说明仅对本发明进行了具体的示例性描述,需要说明的是本发明具体的实现并不受上述方式的限制,只要采用了本发明的技术构思和技术方案进行的各种非实质性的改进,或未经改进将本发明的技术构思和技术方案直接应用于其它场合的,均在本发明的保护范围之内。
再多了解一些
本文用于企业家、创业者技术爱好者查询,结果仅供参考。