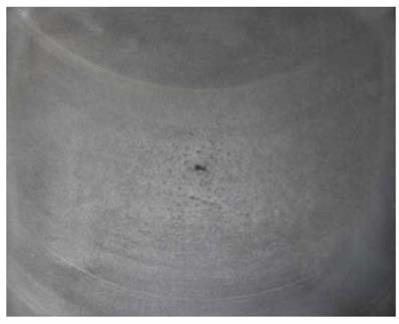
1.本发明涉及钢铁生产技术领域,特别是涉及一种超高强工程机械用弹簧钢冶炼方法。
背景技术:
2.弹簧在工作过程中主要承受压缩和拉伸交变应力,其主要的损坏形式有疲劳断裂和弹力衰减,而疲劳断裂往往与原材料的纯净度和成分均匀性有关。工程机械弹簧钢主要用于生产推土机和挖掘机中的张紧弹簧,其安装在履带内侧的张紧装置中,用于支撑履带的张紧轮,确保在机械行走时,履带始终保持一定的张力,避免履带脱轨。
3.为了满足工程机械弹簧材料轻量化、高性能化的要求,迫切要求提高其强度级别,其主要原因是弹簧的设计重量与其强度成反比,一般情况下弹簧强度每提高50mpa,可实现5%的轻量化,而弹簧强度的提高,必然会对原材料的夹杂物控制和成分均匀性控制提出更高要求。
4.目前,设计应力在1500mpa以上的超高强度工程机械弹簧钢开发存在以下问题:(1)非金属夹杂物控制方面,钢水脱氧不良,纯净度差;(2)成分均匀性控制方面,原材料制成弹簧后需要经过经过淬火 回火热处理,由于原材料中心部位存在合金元素偏析,常常导致弹簧中心部位存在未回火完全的回火马氏体组织。
技术实现要素:
5.本发明针对上述技术问题,克服现有技术的缺点,提供一种超高强工程机械用弹簧钢冶炼方法,包括:lf:采用硅铁粉 碳化硅作为脱氧剂,化渣后首先加入硅铁粉扩散脱氧,然后根据钢水实际脱氧情况,多次小批量加入碳化硅,并在lf整个冶炼周期保持小氩气量操作;连铸:末端电磁搅拌 轻压下结合工艺,保证铸坯中心部位成分均匀性,消除材料淬火 回火热处理后回火马氏体组织。
6.本发明进一步限定的技术方案是:前所述的一种超高强工程机械用弹簧钢冶炼方法,lf钢水进站加热化渣,化渣后取进站样前,加入硅铁粉进行渣面脱氧,增加前期脱氧强度;取进站样后至整个lf冶炼工序结束,加入碳化硅进行脱氧,并保证整个冶炼周期为小氩气量操作,防止加热过程中,钢液裸露吸气。
7.前所述的一种超高强工程机械用弹簧钢冶炼方法,化渣后取进站样前,加入50kg硅铁粉进行渣面脱氧;取进站样后至整个lf冶炼工序结束,每炉加入100-200kg碳化硅进行脱氧。
8.前所述的一种超高强工程机械用弹簧钢冶炼方法,lf全过程采用小氩气量操作,冶炼前期按200-300l/min控制,冶炼后期控制在100-200l/min。
9.前所述的一种超高强工程机械用弹簧钢冶炼方法,连铸控制钢水过热度20-40℃,
采用末端电磁搅拌和轻压下相配合的工艺,改善铸坯心部偏析情况,其中末端电磁搅拌使用参数为600a*8hz,促进末端钢水均匀,末端轻压下参数为0-3-3-3-2-0-0,消除凝固收缩形成的中心孔隙,同时防止晶间富集溶质液体向铸坯中心横向流动。
10.前所述的一种超高强工程机械用弹簧钢冶炼方法,lf出站氧含量低于10ppm。
11.前所述的一种超高强工程机械用弹簧钢冶炼方法,轧材中心偏析≤1.0级,材料制成弹簧后经过淬火 回火热处理,中心带状组织≤1.0级。
12.本发明的有益效果是:(1)本发明通过调整lf炉脱氧剂种类和加入方式以及连铸末端电磁搅拌 末端轻压下参数,能够消除或减轻铸坯中心部位缩孔,防止中心晶间富集溶质液体向铸坯中心横向流动,改善钢水纯净度以及轧材中心偏析水平;(2)本发明吨钢毛利约500元,每年可实现经济效益约500万元。
附图说明
13.图1、2为实施例1产品显微图;图3、4为实施例2产品显微图;图5、6为实施例3产品显微图。
具体实施方式
14.实施例1本实施例提供的一种超高强工程机械用弹簧钢冶炼方法,包括:lf工艺:进站化渣后取样前加入50kg硅铁粉进行强扩散脱氧,取进站样后分批次小批量加入碳化硅100kg,整个冶炼过程保持小氩气量操作,冶炼结束软吹时间为25mim。
15.经由上述工艺生产的轧材,非金属夹杂物检测结果见表1。
16.表1 实施例1轧材非金属夹杂物评级a粗a细b粗b细c粗c细d粗d细ds0.50.00.50.50.00.01.00.50.0连铸工艺:连铸过程采用末端电磁搅拌 末端轻压下工艺,改善坯料中心质量。过热度20℃,末端电磁搅拌为600a*8hz,促进中心钢液混合均匀,末端轻压下采用0-3-3-3-2-0-0,减轻铸坯中心部位缩孔以及防止中心晶间富集溶质液体向铸坯中心横向流动。
17.如图1、图2,经由上述工艺生产的铸坯中心偏析为0.5级,弹簧经过淬、回火后带状组织评级为0.5级。
18.实施例2本实施例提供的一种超高强工程机械用弹簧钢冶炼方法,包括:(1)lf工艺:进站化渣后取样前加入50kg硅铁粉进行强扩散脱氧,取进站样后分批次小批量加入碳化硅160kg,整个冶炼过程保持小氩气量操作,冶炼结束软吹时间为23mim。
19.经由上述工艺生产的轧材,非金属夹杂物检测结果见表2。
20.表2 实施例2轧材非金属夹杂物评级a粗a细b粗b细c粗c细d粗d细ds0.50.01.00.50.50.00.50.50.0
(2)连铸工艺:连铸过程采用末端电磁搅拌 末端轻压下工艺,改善坯料中心质量。过热度29℃,末端电磁搅拌为600a*8hz,促进中心钢液混合均匀,末端轻压下采用0-3-3-3-2-0-0,减轻铸坯中心部位缩孔以及防止中心晶间富集溶质液体向铸坯中心横向流动。
21.如图3、图4,经由上述工艺生产的铸坯中心偏析为0.5级,弹簧经过淬、回火后带状组织评级为0.5级。
22.实施例3本实施例提供的一种超高强工程机械用弹簧钢冶炼方法,包括:(1)lf工艺:进站化渣后取样前加入50kg硅铁粉进行强扩散脱氧,取进站样后加入分批次小批量加入碳化硅200kg,整个冶炼过程保持小氩气量操作,冶炼结束软吹时间为29mim。
23.经由上述工艺生产的轧材,非金属夹杂物检测结果见表3。
24.表3 实施例1轧材非金属夹杂物评级a粗a细b粗b细c粗c细d粗d细ds1.00.00.00.00.50.00.50.50.0(2)连铸工艺:连铸过程采用末端电磁搅拌 末端轻压下工艺,改善坯料中心质量。过热度40℃,末端电磁搅拌为600a*8hz,促进中心钢液混合均匀,末端轻压下采用0-3-3-3-2-0-0,减轻铸坯中心部位缩孔以及防止中心晶间富集溶质液体向铸坯中心横向流动。
25.如图5、图6,经由上述工艺生产的铸坯中心偏析为1.0级,弹簧经过淬、回火后带状组织评级为1.0级。
26.除上述实施例外,本发明还可以有其他实施方式。凡采用等同替换或等效变换形成的技术方案,均落在本发明要求的保护范围。
技术特征:
1.一种超高强工程机械用弹簧钢冶炼方法,其特征在于:包括:lf:采用硅铁粉 碳化硅作为脱氧剂,化渣后首先加入硅铁粉扩散脱氧,然后根据钢水实际脱氧情况,多次小批量加入碳化硅,并在lf整个冶炼周期保持小氩气量操作;连铸:末端电磁搅拌 轻压下结合工艺,保证铸坯中心部位成分均匀性,消除材料淬火 回火热处理后回火马氏体组织。2.根据权利要求1所述的一种超高强工程机械用弹簧钢冶炼方法,其特征在于:lf钢水进站加热化渣,化渣后取进站样前,加入硅铁粉进行渣面脱氧,增加前期脱氧强度;取进站样后至整个lf冶炼工序结束,加入碳化硅进行脱氧,并保证整个冶炼周期为小氩气量操作,防止加热过程中,钢液裸露吸气。3.根据权利要求2所述的一种超高强工程机械用弹簧钢冶炼方法,其特征在于:化渣后取进站样前,加入50kg硅铁粉进行渣面脱氧;取进站样后至整个lf冶炼工序结束,每炉加入100-200kg碳化硅进行脱氧。4.根据权利要求1所述的一种超高强工程机械用弹簧钢冶炼方法,其特征在于:lf全过程采用小氩气量操作,冶炼前期按200-300l/min控制,冶炼后期控制在100-200l/min。5.根据权利要求1所述的一种超高强工程机械用弹簧钢冶炼方法,其特征在于:连铸控制钢水过热度20-40℃,采用末端电磁搅拌和轻压下相配合的工艺,改善铸坯心部偏析情况,其中末端电磁搅拌使用参数为600a*8hz,促进末端钢水均匀,末端轻压下参数为0-3-3-3-2-0-0,消除凝固收缩形成的中心孔隙,同时防止晶间富集溶质液体向铸坯中心横向流动。6.根据权利要求1所述的一种超高强工程机械用弹簧钢冶炼方法,其特征在于:lf出站氧含量低于10ppm。7.根据权利要求1所述的一种超高强工程机械用弹簧钢冶炼方法,其特征在于:轧材中心偏析≤1.0级,材料制成弹簧后经过淬火 回火热处理,中心带状组织≤1.0级。
技术总结
本发明公开了一种超高强工程机械用弹簧钢冶炼方法,涉及钢铁生产技术领域,包括:LF:采用硅铁粉 碳化硅作为脱氧剂,化渣后首先加入硅铁粉扩散脱氧,然后根据钢水实际脱氧情况,多次小批量加入碳化硅,并在LF整个冶炼周期保持小氩气量操作;连铸:末端电磁搅拌 轻压下结合工艺,保证铸坯中心部位成分均匀性,消除材料淬火 回火热处理后回火马氏体组织。能够消除或减轻铸坯中心部位缩孔,防止中心晶间富集溶质液体向铸坯中心横向流动,改善钢水纯净度以及轧材中心偏析水平。净度以及轧材中心偏析水平。净度以及轧材中心偏析水平。
技术研发人员:黄术明 郑宏伟 牛帅 赵治国 邓伟
受保护的技术使用者:南京钢铁股份有限公司
技术研发日:2021.11.26
技术公布日:2022/3/8
再多了解一些
本文用于企业家、创业者技术爱好者查询,结果仅供参考。