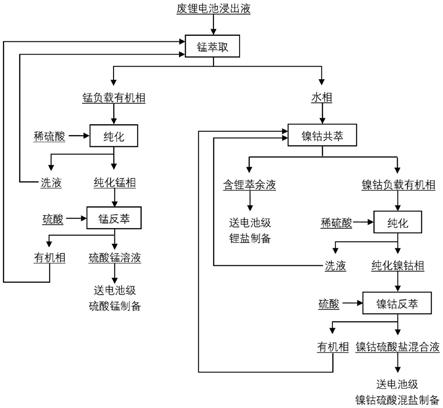
1.申请涉及湿法冶金分离技术领域,尤其涉及一种膦酸酯萃取剂及其对废锂电池浸出液中有价金属萃取分离的方法。
背景技术:
2.随着性能优良的锂电池在3c、动力、储能等领域应用越来越广泛,废锂电池报废量也将越来越多。废锂电池中含有毒电解液和锂、镍、钴、锰、铜、铝、石墨等有价资源,其清洁高效循环利用是锂电池产业全生命周期绿色管理的关键所在。
3.目前国内外废锂电池循环回收利用工艺可分为火法和湿法两种。湿法回收工艺具有处置规模可大可小、产品方案丰富灵活、资源综合回收利用效果好、可实现正极材料直接闭路循环等优点,已成为我国废锂电池主流处置工艺。废锂电池湿法处理流程一般为:
①
通过还原浸出使废锂电池粉末中锂、镍、钴、锰、铜、铁、铝等元素一起溶解进入浸出液;
②
通过中和沉淀或溶剂萃取等方法去除浸出液中的铜、铁、铝等杂质;
③
通过溶剂萃取实现镍、钴、锰、锂等有价金属的分离和富集;
④
负载有机相经反萃、浓缩结晶或共沉淀制备镍钴锰硫酸盐或三元前驱体产品,萃余液经浓缩结晶、沉淀制备锂盐产品。在有价金属萃取分离过程中,多采用酸性膦酸类萃取剂(p204、p507)皂化萃取实现镍、钴、锰与锂的分离和富集,普遍存在ph操作范围窄、皂化废液排放量大、锂与杂质离子(na
、nh
4
)分离困难、生产成本高等共性问题。
技术实现要素:
4.鉴于现有废锂电池浸出液中有价金属萃取分离工艺所存在的ph要求严格、皂化废液排放量大、锂回收率低等弊端,本技术提供了一种适用于高酸体系的新型膦酸酯萃取剂以及使用该萃取剂的非皂化梯级萃取分离废锂电池浸出液中有价金属的方法。
5.本技术的第一个目的在于提供一种膦酸酯萃取剂,包含如下结构式中的一种或两种:
[0006][0007][0008]
本技术的另一目的在于提供一种使用上述膦酸酯萃取剂对废锂电池浸出液中有价金属的萃取分离方法,具体包含如下步骤:
[0009]
(1)配制萃取有机相:将改质剂、稀释剂和膦酸酯萃取剂混合得到萃取有机相;
[0010]
(2)锰萃取:将萃取有机相与废锂电池浸出液进行混合萃取,得到锰负载有机相和
水相;
[0011]
(3)镍钴共萃:将萃取有机相与水相进行混合萃取,得到镍钴负载有机相和含锂萃余液;
[0012]
(4)锰负载有机相纯化:使用稀硫酸洗涤锰负载有机相,脱除其中夹杂的锂、镍、钴,洗液调整酸度后返回锰萃取工序循环使用;
[0013]
(5)镍钴负载有机相纯化:使用稀硫酸洗涤镍钴负载有机相,脱除其中夹杂的锂,洗液调整酸度后返回镍钴共萃工序循环使用;
[0014]
(6)锰反萃:将纯化后的锰负载有机相与硫酸混合反萃,所得水相为硫酸锰溶液,有机相经再生后返回锰萃取工序循环使用;
[0015]
(7)镍钴反萃:将纯化后的镍钴负载有机相与硫酸混合反萃,所得水相为硫酸镍和硫酸钴的混合溶液,有机相经再生后返回镍钴共萃工序循环使用。
[0016]
进一步地,步骤(1)中改质剂为正丁醇和/或异丁醇。
[0017]
进一步地,步骤(1)中稀释剂为磺化煤油。
[0018]
进一步地,步骤(1)中膦酸酯萃取剂、改质剂和稀释剂的体积比为20~50∶5~15∶35~75。
[0019]
进一步地,步骤(2)中,所述废锂电池浸出液的ph值为0.5~6,有价金属含量分别为li 3~30g/l、ni 5~60g/l、co 5~60g/l、mn 5~60g/l。
[0020]
进一步地,步骤(2)和步骤(3)中萃取工序工艺参数为:o/a相比为1∶3~3∶1,萃取温度为20~60℃,萃取时间为5~15min,萃取方式为多级逆流萃取,萃取级数为2~12级。
[0021]
进一步地,步骤(4)和步骤(5)中纯化工序工艺参数为:o/a相比为1∶1~4∶1,稀硫酸浓度为0.5~1.5mol/l,洗涤温度为20~60℃,洗涤时间为5~15min,洗涤方式为多级逆流洗涤,洗涤级数为2~6级。
[0022]
进一步地,步骤(6)和步骤(7)中反萃工序工艺参数为:o/a相比为1∶1~3∶1,硫酸浓度为4~6mol/l,反萃温度为20~60℃,反萃时间为5~15min,反萃方式为多级逆流反萃,反萃级数为2~6级。
[0023]
本技术的有益效果如下:
[0024]
本技术提供的膦酸酯萃取剂在萃取分离废锂电池浸出液中有价金属之前不需要进行皂化预处理,可在较宽的ph范围内快速高效分离废锂电池浸出液中镍、钴、锰与锂,避免了传统膦酸萃取剂皂化废水处置以及锂钠/铵分离困难、生产成本高等缺点,实现了废锂电池浸出液中有价金属的高效分离和清洁回收。
附图说明
[0025]
为了更清楚地说明本技术实施例或现有技术中的技术方案,下面将对实施例或现有技术描述中所需要使用的附图作简单地介绍,显而易见地,下面描述中的附图仅仅是本技术的实施例,对于本领域普通技术人员来讲,在不付出创造性劳动的前提下,还可以根据提供的附图获得其他的附图。
[0026]
图1为本技术提供的废锂电池浸出液中有价金属萃取分离方法的工艺流程图。
具体实施方式
[0027]
本技术提供了一种膦酸酯萃取剂,包含如下结构式中的一种或两种:
[0028][0029][0030]
在本技术中,当膦酸酯萃取剂为式(i)膦酸单烷基酯和式(ii)膦酸双烷基酯组成的复合膦酸酯萃取剂时,复合膦酸酯萃取剂中膦酸单烷基酯与膦酸双烷基酯的质量比为1∶5~5∶1,优选为1∶4~2∶1。
[0031]
本技术提供了一种采用上述萃取剂萃取分离废锂电池浸出液中有价金属的方法,包括如下步骤:
[0032]
(1)配制萃取有机相:将改质剂、稀释剂和膦酸酯萃取剂混合得到萃取有机相;
[0033]
(2)锰萃取:将萃取有机相与废锂电池浸出液进行混合萃取,得到锰负载有机相和水相;
[0034]
(3)镍钴共萃:将萃取有机相与水相进行混合萃取,得到镍钴负载有机相和含锂萃余液;
[0035]
(4)锰负载有机相纯化:使用稀硫酸洗涤锰负载有机相,脱除其中夹杂的锂、镍、钴,洗液调整酸度后返回锰萃取工序循环使用;
[0036]
(5)镍钴负载有机相纯化:使用稀硫酸洗涤镍钴负载有机相,脱除其中夹杂的锂,洗液调整酸度后返回镍钴共萃工序循环使用;
[0037]
(6)锰反萃:将纯化后的锰负载有机相与硫酸混合反萃,所得水相为硫酸锰溶液,有机相经再生后返回锰萃取工序循环使用;
[0038]
(7)镍钴反萃:将纯化后的镍钴负载有机相与硫酸混合反萃,所得水相为硫酸镍和硫酸钴的混合溶液,有机相经再生后返回镍钴共萃工序循环使用。
[0039]
在本技术步骤(1)中,改质剂为正丁醇和/或异丁醇,优选为正丁醇。
[0040]
在本技术步骤(1)中,稀释剂为磺化煤油。
[0041]
在本技术步骤(1)中,膦酸酯萃取剂、改质剂和稀释剂的体积比为20~50∶5~15∶35~75;优选为为40~50∶5~15∶35~55。
[0042]
在本技术步骤(2)中,废锂电池浸出液的ph值为0.5~6,有价金属含量分别为li 3~30g/l、ni 5~60g/l、co 5~60g/l、mn 5~60g/l。
[0043]
在本技术步骤(2)和步骤(3)中,萃取工序工艺参数为:o/a相比为1∶3~3∶1,萃取温度为20~60℃,萃取时间为5~15min,萃取方式为多级逆流萃取,萃取级数为2~12级;优选地,(2)和步骤(3)萃取工序工艺参数为:o/a相比为1∶2~2∶1,萃取温度为40~50℃,萃取时间为6~12min,萃取方式为多级逆流萃取,萃取级数为4~10级。
[0044]
在本技术步骤(4)和步骤(5)中,纯化工序工艺参数为:o/a相比为1∶1~4∶1,稀硫酸浓度为0.5~1.5mol/l,洗涤温度为20~60℃,洗涤时间为5~15min,洗涤方式为多级逆流洗涤,洗涤级数为2~6级;优选地,步骤(4)和步骤(5)纯化工序工艺参数为:o/a相比为1∶
1~2∶1,稀硫酸浓度为0.75~1.25mol/l,洗涤温度为30~45℃,洗涤时间为6~9min,洗涤方式为多级逆流洗涤,洗涤级数为4~5级。
[0045]
在本技术步骤(6)和步骤(7)中,反萃工序工艺参数为:o/a相比为1∶1~3∶1,硫酸浓度为4~6mol/l,反萃温度为20~60℃,反萃时间为5~15min,反萃方式为多级逆流反萃,反萃级数为2~6级;优选地,步骤(6)和步骤(7)反萃工序工艺参数为:o/a相比为1∶1~2∶1,硫酸浓度为4.5~5.5mol/l,反萃温度为35~50℃,反萃时间为7~13min,反萃方式为多级逆流反萃,反萃级数为3~5级。
[0046]
下面将对本技术实施例中的技术方案进行清楚、完整地描述,显然,所描述的实施例仅仅是本技术一部分实施例,而不是全部的实施例。基于本技术中的实施例,本领域普通技术人员在没有做出创造性劳动前提下所获得的所有其他实施例,都属于本技术保护的范围。
[0047]
实施例1
[0048]
本实施例萃取分离的废锂电池浸出液的初始ph值为3,其中有价金属含量分别为li 7g/l、ni 38g/l、co 27g/l、mn 30g/l。
[0049]
萃取分离上述废锂电池浸出液中有价金属的方法,包括以下步骤:
[0050]
(1)配制萃取有机相:以式(ⅱ)的膦酸双烷基酯为萃取剂、正丁醇为改质剂、磺化煤油为稀释剂,三者按照膦酸酯萃取剂∶改质剂∶稀释剂=40∶10∶50的体积比混合得到萃取有机相;
[0051]
(2)锰萃取:将萃取有机相与废锂电池浸出液进行混合萃取,控制o/a相比为1∶2,萃取温度为40℃,萃取时间为5min,萃取方式为多级逆流萃取,萃取级数为6级,得到锰负载有机相和水相。经检测计算,锰萃取率可达99.81%,而锂、镍和钴萃取率均低于4%;
[0052]
(3)镍钴共萃:将萃取有机相与水相进行混合萃取,控制o/a相比为1∶1,萃取温度为40℃,萃取时间为10min,萃取方式为多级逆流萃取,萃取级数为10级,得到镍钴负载有机相和含锂萃余液。经检测计算,镍和钴萃取率分别为99.69%和99.74%,而锂萃取率低于1%;
[0053]
(4)锰负载有机相纯化:使用稀硫酸洗涤锰负载有机相,脱除其中夹杂的锂、镍、钴,控制稀硫酸浓度为1mol/l,o/a相比为3∶1、洗涤温度40℃、洗涤时间8min,萃取方式为多级逆流萃取,萃取级数为6级,洗液调整酸度后返回锰萃取工序循环使用。经检测计算,锂、镍和钴去除率均大于99%;
[0054]
(5)镍钴负载有机相纯化:使用稀硫酸洗涤镍钴负载有机相,脱除其中夹杂的锂,控制稀硫酸浓度为0.5mol/l,o/a相比为4∶1、洗涤温度40℃、洗涤时间5min,萃取方式为多级逆流萃取,萃取级数为4级,洗液调整酸度后返回镍钴共萃工序循环使用。经检测计算,锂去除率大于99%;
[0055]
(6)锰反萃:将纯化后的锰负载有机相与硫酸混合反萃,控制硫酸浓度为4mol/l,o/a相比为2∶1、洗涤温度40℃、洗涤时间8min,萃取方式为多级逆流萃取,萃取级数为4级,所得水相为硫酸锰溶液,有机相经再生后返回锰萃取工序循环使用。经检测计算,锰反萃率为99.86%;
[0056]
(7)镍钴反萃:将纯化后的镍钴负载有机相与硫酸混合反萃,控制硫酸浓度为5mol/l,o/a相比为2∶1、洗涤温度40℃、洗涤时间10min,萃取方式为多级逆流萃取,萃取级
数为5级,所得水相为硫酸镍和硫酸钴的混合溶液,有机相经再生后返回镍钴共萃工序循环使用。经检测计算,镍和钴反萃率分别为99.83%和99.78%。
[0057]
实施例2
[0058]
本实施例萃取分离的废锂电池浸出液的初始ph值为4,其中有价金属含量分别为li 12g/l、ni 50g/l、co 32g/l、mn 36g/l。
[0059]
萃取分离上述废锂电池浸出液中有价金属的方法,包括以下步骤:
[0060]
(1)配制萃取有机相:以式(i)的膦酸单烷基酯为萃取剂、正丁醇为改质剂、磺化煤油为稀释剂,三者按照膦酸酯萃取剂∶改质剂∶稀释剂=35∶15∶50的体积比混合得到萃取有机相;
[0061]
(2)锰萃取:将萃取有机相与废锂电池浸出液进行混合萃取,控制o/a相比为1∶1,萃取温度为45℃,萃取时间为8min,萃取方式为多级逆流萃取,萃取级数为4级,得到锰负载有机相和水相。经检测计算,锰萃取率可达99.76%,而锂、镍和钴萃取率均低于3%;
[0062]
(3)镍钴共萃:将萃取有机相与水相进行混合萃取,控制o/a相比为1∶1,萃取温度为45℃,萃取时间为10min,萃取方式为多级逆流萃取,萃取级数为11级,得到镍钴负载有机相和含锂萃余液。经检测计算,镍和钴萃取率分别为99.69%和99.75%,而锂萃取率低于1%;
[0063]
(4)锰负载有机相纯化:使用稀硫酸洗涤锰负载有机相,脱除其中夹杂的锂、镍、钴,控制稀硫酸浓度为1mol/l,o/a相比为3∶1、洗涤温度40℃、洗涤时间8min,萃取方式为多级逆流萃取,萃取级数为6级,洗液调整酸度后返回锰萃取工序循环使用。经检测计算,锂、镍和钴去除率均大于99%;
[0064]
(5)镍钴负载有机相纯化:使用稀硫酸洗涤镍钴负载有机相,脱除其中夹杂的锂,控制稀硫酸浓度为0.5mol/l,o/a相比为4∶1、洗涤温度45℃、洗涤时间8min,萃取方式为多级逆流萃取,萃取级数为4级,洗液调整酸度后返回镍钴共萃工序循环使用。经检测计算,锂去除率大于99%;
[0065]
(6)锰反萃:将纯化后的锰负载有机相与硫酸混合反萃,控制硫酸浓度为4mol/l,o/a相比为1.5∶1、洗涤温度45℃、洗涤时间10min,萃取方式为多级逆流萃取,萃取级数为4级,所得水相为硫酸锰溶液,有机相经再生后返回锰萃取工序循环使用。经检测计算,锰反萃率为99.89%;
[0066]
(7)镍钴反萃:将纯化后的镍钴负载有机相与硫酸混合反萃,控制硫酸浓度为5mol/l,o/a相比为1∶1、洗涤温度45℃、洗涤时间10min,萃取方式为多级逆流萃取,萃取级数为5级,所得水相为硫酸镍和硫酸钴的混合溶液,有机相经再生后返回镍钴共萃工序循环使用。经检测计算,镍和钴反萃率分别为99.86%和99.80%。
[0067]
实施例3
[0068]
本实施例萃取分离的废锂电池浸出液的初始ph值为2,其中有价金属含量分别为li 5g/l、ni 35g/l、co 23g/l、mn 27g/l。
[0069]
萃取分离上述废锂电池浸出液中有价金属的方法,包括以下步骤:
[0070]
(1)配制萃取有机相:以式(i)膦酸单烷基酯20wt.% 式(ii)膦酸双烷基酯80wt.%为萃取剂、异丁醇为改质剂、磺化煤油为稀释剂,三者按照膦酸酯萃取剂∶改质剂∶稀释剂=40∶15∶45的体积比混合得到萃取有机相;
[0071]
(2)锰萃取:将萃取有机相与废锂电池浸出液进行混合萃取,控制o/a相比为1∶2,萃取温度为40℃,萃取时间为10min,萃取方式为多级逆流萃取,萃取级数为6级,得到锰负载有机相和水相。经检测计算,锰萃取率可达99.81%,而锂、镍和钴萃取率均低于3%;
[0072]
(3)镍钴共萃:将萃取有机相与水相进行混合萃取,控制o/a相比为1∶1,萃取温度为40℃,萃取时间为10min,萃取方式为多级逆流萃取,萃取级数为8级,得到镍钴负载有机相和含锂萃余液。经检测计算,镍和钴萃取率分别为99.84%和99.90%,而锂萃取率低于1%;
[0073]
(4)锰负载有机相纯化:使用稀硫酸洗涤锰负载有机相,脱除其中夹杂的锂、镍、钴,其中稀硫酸浓度为1mol/l,o/a相比为2∶1、洗涤温度40℃、洗涤时间8min,萃取方式为多级逆流萃取,萃取级数为4级,洗液调整酸度后返回锰萃取工序循环使用。经检测计算,锂、镍和钴去除率均大于99%;
[0074]
(5)镍钴负载有机相纯化:使用稀硫酸洗涤镍钴负载有机相,脱除其中夹杂的锂,控制稀硫酸浓度为0.5mol/l,o/a相比为4∶1、洗涤温度40℃、洗涤时间5min,萃取方式为多级逆流萃取,萃取级数为4级,洗液调整酸度后返回镍钴共萃工序循环使用。经检测计算,锂去除率大于99%;
[0075]
(6)锰反萃:将纯化后的锰负载有机相与硫酸混合反萃,控制硫酸浓度为4mol/l,o/a相比为1∶1、洗涤温度40℃、洗涤时间8min,萃取方式为多级逆流萃取,萃取级数为3级,所得水相为硫酸锰溶液,有机相经再生后返回锰萃取工序循环使用。经检测计算,锰反萃率为99.87%;
[0076]
(7)镍钴反萃:将纯化后的镍钴负载有机相与硫酸混合反萃,控制硫酸浓度为5mol/l,o/a相比为1∶1、洗涤温度40℃、洗涤时间5min,萃取方式为多级逆流萃取,萃取级数为4级,所得水相为硫酸镍和硫酸钴的混合溶液,有机相经再生后返回镍钴共萃工序循环使用。经检测计算,镍和钴反萃率分别为99.99%和99.83%。
[0077]
实施例4
[0078]
本实施例萃取分离的废锂电池浸出液的初始ph值为3,其中有价金属含量分别为li 15g/l、ni 60g/l、co 50g/l、mn 55g/l。
[0079]
萃取分离上述废锂电池浸出液中有价金属的方法,包括以下步骤:
[0080]
(1)配制萃取有机相:以式(i)膦酸单烷基酯25wt.% 式(ii)膦酸双烷基酯75wt.%为萃取剂、异丁醇为改质剂、磺化煤油为稀释剂,三者按照膦酸酯萃取剂∶改质剂∶稀释剂=25∶15∶60的体积比混合得到萃取有机相;
[0081]
(2)锰萃取:将萃取有机相与废锂电池浸出液进行混合萃取,控制o/a相比为1∶1.5,萃取温度为40℃,萃取时间为8min,萃取方式为多级逆流萃取,萃取级数为8级,得到锰负载有机相和水相。经检测计算,锰萃取率可达99.76%,而锂、镍和钴萃取率均低于3%;
[0082]
(3)镍钴共萃:将萃取有机相与水相进行混合萃取,控制o/a相比为2∶1,萃取温度为40℃,萃取时间为10min,萃取方式为多级逆流萃取,萃取级数为8级,得到镍钴负载有机相和含锂萃余液。经检测计算,镍和钴萃取率分别为99.879%和99.84%,而锂萃取率低于1%;
[0083]
(4)锰负载有机相纯化:使用稀硫酸洗涤锰负载有机相,脱除其中夹杂的锂、镍、钴,控制稀硫酸浓度为1.5mol/l,o/a相比为3∶1、洗涤温度40℃、洗涤时间8min,萃取方式为
多级逆流萃取,萃取级数为6级,洗液调整酸度后返回锰萃取工序循环使用。经检测计算,锂、镍和钴去除率均大于99%;
[0084]
(5)镍钴负载有机相纯化:使用稀硫酸洗涤镍钴负载有机相,脱除其中夹杂的锂,控制稀硫酸浓度为1mol/l,o/a相比为3∶1、洗涤温度40℃、洗涤时间5min,萃取方式为多级逆流萃取,萃取级数为5级,洗液调整酸度后返回镍钴共萃工序循环使用。经检测计算,锂去除率大于99%;
[0085]
(6)锰反萃:将纯化后的锰负载有机相与硫酸混合反萃,控制硫酸浓度为6mol/l,o/a相比为1.5∶1、洗涤温度40℃、洗涤时间8min,萃取方式为多级逆流萃取,萃取级数为5级,所得水相为硫酸锰溶液,有机相经再生后返回锰萃取工序循环使用。经检测计算,锰反萃率为99.83%;
[0086]
(7)镍钴反萃:将纯化后的镍钴负载有机相与硫酸混合反萃,控制硫酸浓度为6mol/l,o/a相比为1∶1、洗涤温度40℃、洗涤时间10min,萃取方式为多级逆流萃取,萃取级数为6级,所得水相为硫酸镍和硫酸钴的混合溶液,有机相经再生后返回镍钴共萃工序循环使用。经检测计算,镍和钴反萃率分别为99.88%和99.84%。
[0087]
本说明书中各个实施例采用递进的方式描述,每个实施例重点说明的都是与其他实施例的不同之处,各个实施例之间相同相似部分互相参见即可。
[0088]
对所公开的实施例的上述说明,使本领域专业技术人员能够实现或使用本技术。对这些实施例的多种修改对本领域的专业技术人员来说将是显而易见的,本文中所定义的一般原理可以在不脱离本技术的精神或范围的情况下,在其它实施例中实现。因此,本技术将不会被限制于本文所示的这些实施例,而是要符合与本文所公开的原理和新颖特点相一致的最宽的范围。
再多了解一些
本文用于企业家、创业者技术爱好者查询,结果仅供参考。