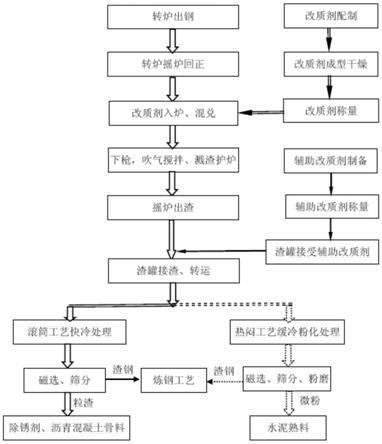
1.本发明涉及钢渣改性处理技术领域,特别涉及一种钢渣改质剂及钢渣热态改质处理工艺。
背景技术:
2.钢渣是钢铁生产过程中产生的大宗副产物之一,约占粗钢产量的10-15%,2019年中国粗钢产量9.96亿吨,新增钢渣量约1.2亿吨。钢渣主要由钙、硅、镁、铝、铁等金属氧化物和磷、硫非金属氧化物以及各类高熔点聚合物组成的复杂混合物,钢渣中还残存1.0-10.0%的游离氧化钙(f-cao)和游离氧化镁(f-mgo),这些高温过烧的氧化钙和氧化镁存在缓慢水化、体积逐渐膨胀的特性,严重制约着钢渣在建筑、道路工程上的利用。目前,我国的钢渣利用率不足30%,大量钢渣的堆存不仅占用土地,而且扬尘、污染土壤,给社会生活带来极大挑战。对钢渣进行改质处理,促使钢渣中不稳定的f-cao和f-mgo在高温钢渣预处理过程中快速的反应消耗掉,使钢渣快速恢复高效资源化禀性,提高其在水泥辅料、道路和建筑工程集料上的规模化高值利用已成为国内外研究的共识和热点。但鉴于钢渣温度、成分的复杂性、粘度随温度变化的敏感性,钢渣高温改质处理存在改质剂难加入、难混和、补热困难等问题,很多研究仍局限在实验室阶段,工业化规模的实施很难推进。
3.中国专利cn101033117a公开了“一种钢渣处理添加剂”通过向高温熔融钢渣中添加由粉煤灰、高炉渣、煤渣和煤粉组成的粒度在3-30mm的添加剂,其中粉煤灰(或煤渣)75-100%,高炉渣0-15%,煤0-10%,利用添加剂中的sio2、al2o3和c在高温状态下与钢渣中的f-cao、f-mgo、feo反应,除去影响钢渣稳定性的f-cao和f-mgo,同时还原回收金属铁,反应方程式如下:
4.sio2 ncao=ncao
·
sio2;
5.al2o3 mcao=mcao
·
al2o3;
6.c 2feo=2fe co2;
7.该专利对粉煤灰(或煤渣)、高炉渣和煤粉的物料配比有具体的要求和限制,也提到了每种物料的主要化学成分,但混配后最终添加剂的主要化学成分(如sio2、al2o3和c)却没有明确界定和限制。
8.中国专利cn110055370a公开了“一种新型高温钢渣改质剂及改性预处理工艺”,提出了利用单质硅物质和单质碳物质作为改质剂、通过向渣罐中预先加入单质硅物质和含单质碳物质、转炉出渣时再向渣罐中同时加入单质硅物质、出渣完毕后向物料中吹氮气、然后热闷处理的工艺方法。该方案强调了单质硅物质中单质硅含量(纯度)≥60%、单质碳物质中单质碳含量≥80%;改质剂中单质硅与单质碳的重量百分比为(10-30):1;改质剂的加入量为钢渣重量的3-5%。多点、多批次加入高纯度改质剂并吹氮气搅拌,增加改质剂与钢渣中不稳定成分接触反应的机会。缺点在于单质碳的密度较小,所述的几种来源(石墨、活性炭、无烟煤、烟煤、褐煤和煤矸石)多以细颗粒形状存在,很难混入高密度的熔渣中,烟尘大且有效利用率低;向渣罐内的钢渣中吹氮气不仅降低了钢渣的温度、提高钢渣粘度、阻碍活
性成分的反应速度,而且增加了扬尘点和为消除扬尘而追加的投资及运行费用。
9.中国专利cn109022645a公开了“一种钢渣改性及综合利用系统和方法”,提出了一种利用钢渣改性电弧炉补热熔化钢渣和改质剂(煤粉和石灰石),促使钢渣中游离氧化钙和氧化镁稳定化反应,同时还原回收钢渣中金属铁资源。这种工艺对钢渣改性控制灵活,效果明显,但投资大、运行费用高。
技术实现要素:
10.本发明的目的在于提供一种钢渣改质剂及钢渣热态改质处理工艺,可以针对高温钢渣进行改质处理,解决现有改质料与高温钢渣混合不均、改质不充分和现有钢渣改质工艺投资大、运行费用高等问题,而且可以大幅度降低钢渣中f-cao和f-mgo,整体工艺经济实用。
11.为达到上述目的,本发明的技术方案是:
12.一种钢渣改质剂,其化学成分重量百分比为:金属硅:10.0~50.0%;sio2:30.0~80.0%;al2o3:5.0~20.0%;且,所述钢渣改质剂的粒度为3~10mm。
13.在本发明所述钢渣改质剂的成分设计中:
14.本发明所述钢渣改质剂成分中金属硅(si),来源于硅铁粉,属于强脱氧剂,主要用于还原转炉熔融钢渣中的部分铁的氧化物(如feo、fe2o3)。转炉熔融钢渣中铁氧化物的含量一般在10.0-25.0%之间,其中feo占10.5-13.0%。大量氧化铁的存在不仅浪费了铁资源,而且因其熔点较低,导致转炉熔融钢渣的粘度下降,钢渣与炉壁的粘附性能下降,不利于延长炉衬寿命的溅渣护炉作业。
15.一方面,钢渣改质剂中金属硅与转炉熔融钢渣中部分氧化铁发生还原反应后,降低了转炉熔融钢渣中氧化铁的含量,提高了钢渣与炉壁的粘附性能。向转炉熔融钢渣中加入其重量2.0-10.0%的钢渣改质剂,参与反应后基本上可以降低转炉熔融钢渣熔渣中氧化铁含量1.0-50.0%,转炉熔融钢渣的粘度随之增加。另一方面,金属硅与氧化铁反应时放出热量,弥补部分因钢渣改质剂熔化所吸收的热量,尽可能的保持炉内温度相对稳定,减少热振对炉壁耐材的不利影响。
16.金属硅还原的产物为sio2,它与钢渣改质剂中的sio2和al2o3同为酸性化合物,能够与转炉熔融钢渣中碱性的f-cao和f-mgo反应,生成性能稳定的高熔点硅酸盐和铝酸盐,不仅消除了转炉熔融钢渣中性能不稳定的“有害”成分,而且生成的高熔点物质有利于溅渣护炉作用,并能提升钢渣的胶凝活性。
17.假设加入5%的钢渣改质剂,其中的sio2和al2o3含量总和达到50-70%的话,理想条件下全部反应可以消耗掉转炉熔融钢渣中4-6%的f-cao和1-3%的f-mgo,转炉熔融钢渣的稳定性得到极大改善。
18.因此,当转炉出钢完毕,通过料仓向转炉内的熔融钢渣中加入转炉熔融钢渣重量2-10%的钢渣改质剂,利用转炉内熔融钢渣和高温炉壁(1500-1600℃)所具有的巨大的热量将钢渣改质剂快速熔化,实现钢渣改质剂和钢渣的液-液态充分混合。下枪吹氮气对钢渣改质剂和转炉熔融钢渣进行搅拌、混合,为钢渣改质剂中金属硅(si)和熔融钢渣中的feo的反应提供了充分的热力学和动力学条件,二者快速反应生成sio2和金属铁,反应式为si 2feo=2fe sio2,新生成的sio2以及钢渣改质剂中原有的sio2和al2o3与熔融钢渣中的f-cao
和f-mgo反应生成性能稳定的硅酸钙、硅酸镁以及硅铝酸镁等。转炉内熔融钢渣的熔点和粘度则因feo含量的降低而升高,有利于挂壁护炉,炉渣改质和溅渣护炉同时完成。
19.当转炉出渣时,在渣罐内事先加入转炉熔融钢渣重量5-20%的辅助改质剂,辅助改质剂主要包含二氧化硅和氧化铝,其成分重量百分比优选为:sio2:26.0~95.0%;al2o3:0.50~35.0%;cao:0.5~50.0%;mgo:0.1~8.0%;feo:0.05~1.0%。辅助改质剂可以由诸如石英砂、高炉渣或其它含硅铝的废耐材的一种或几种混合配置而成,形态以颗粒物为主,粒径30mm以下,也可以是熔融状态(如高炉熔渣等)。
20.依靠转炉熔融钢渣从转炉到渣罐的高度差所产生的冲击力实现熔渣和辅助改质剂的混合、搅拌,在接下来的渣罐从转炉下转运到渣处理工位的过程中,渣罐中的钢渣一直处于高温熔融状态,这个过程一般可以维持0.5-2.0小时(视渣罐转运距离而异),为钢渣中残余f-cao的稳定化反应提供了充分的热力学和动力学条件。经过改质处理的钢渣中f-cao含量下降到3.0%以下,性能稳定,被滚筒工艺快冷处理成粒径小于20mm的颗粒状钢渣,用于水泥熟料、沥青混凝土或其它场合的高价值工程建设领域。
21.利用所述钢渣改质剂进行钢渣热态改质处理工艺,包括以下步骤:
22.1)转炉出钢完毕后,向转炉熔融钢渣中加入所述钢渣改质剂,所述钢渣改质剂加入量为转炉熔融钢渣重量的2.0~10.0%;
23.2)所述钢渣改质剂加入后,下枪对炉内钢渣和改质剂吹氮搅拌,完成转炉熔融钢渣炉内改质及溅渣护炉作业;
24.3)炉内改质后的转炉熔融钢渣出渣至装有辅助改质剂的渣罐中,搅拌、混合,实现转炉熔融钢渣的充分改质;辅助改质剂用量为转炉熔融钢渣重量的5~20%;所述辅助改质剂主要成分为sio2和al2o3;
25.4)将充分改质后的转炉熔融钢渣转运至渣处理工位,之后通过滚筒工艺快冷处理成粒状钢渣,或通过热闷工艺缓冷处理成粉状尾渣。
26.优选的,所述辅助改质剂按重量百分比包括:sio2:26.0~95.0%;al2o3:0.50~35.0%;cao:0.5~50.0%;mgo:0.1~8.0%;feo:0.05~1.0%。
27.优选的,所述辅助改质剂为石英砂、高炉渣、高炉熔渣、粉煤灰或其它含硅铝质废耐材中的一种或多种,优选高炉熔渣;
28.优选的,所述辅助改质剂粒度<30mm。
29.优选的,所述辅助改质剂为高炉熔渣时,高炉熔渣的加入量为转炉熔融钢渣重量的10~20%。
30.优选的,所述高炉熔渣按重量百分比包括:sio2:26-42%、al2o3:6-17%、cao:39-49%、mgo:0.1-8.0%、feo:0.1-1.0%。
31.优选的,步骤2)所述钢渣改质剂加入后,下枪对炉内钢渣和改质剂进行吹氮搅拌3~5min。
32.优选的,步骤3)中,所述搅拌方法为利用转炉炉口距渣罐底部的高度差,转炉熔融钢渣倾倒产生的冲击力来实现。
33.优选的,步骤1)中,所述转炉熔融钢渣的温度为1500~1550℃,转炉熔融钢渣为钢水总重量的8~15%。
34.所述转炉熔融钢渣按重量百分比包括:cao:40.0-45.0%、sio2:10.5-13.0%、
al2o3:1.0-1.5%、mgo:7.0-9.0%、mno:2.0-4.5%、feo:10.5-13.0%、tfe:18.0-23.0%、p2o5:1.2-2.4%、f-cao:3.5-8.5%,f-mgo:1.6-4.5%,二元碱度r≥3.5。
35.在本发明所述的钢渣热态改质处理工艺中:
36.转炉出钢完毕,摇炉复位,炉口竖直向上,此时,转炉中钢渣为1500-1550℃的熔融状态,渣量为钢水总重量的8-15%,其化学成分质量百分比为:cao:40.0-45.0%、sio2:10.5-13.0%、al2o3:1.0-1.5%、mgo:7.0-9.0%、mno:2.0-4.5%、feo:10.5-13.0%、tfe:18.0-23.0%、p2o5:1.2-2.4%、f-cao:3.5-8.5%,二元碱度r≥3.5。
37.之后通过料仓向转炉内的熔融钢渣中加入所述钢渣改质剂,钢渣改质剂的加入量为熔融钢渣重量的2-10%,然后放下喷枪吹氮搅拌3-5分钟,实施钢渣改质剂与钢渣的混合搅拌及溅渣护炉作业。
38.在完成上述作业过程中,钢渣改质剂在炉内大量高温熔融钢渣和炉壁高温辐射下快速熔化,在吹气搅拌的剧烈作用下,金属硅与熔融钢渣中的大部分氧化铁(feo和fe2o3的通称)充分接触、反应,生成sio2和金属铁,新生成的sio2与钢渣改质剂中原有的sio2和al2o3继续与炉渣中的f-cao和f-mgo反应,生成性能稳定的硅酸钙(ca3sio4和ca2sio4)、铝酸钙(mcao
·
nal2o3)及橄榄石(mg2sio4 fe2sio4)等,达到转炉熔融钢渣高温改质的目的,并将熔融钢渣中部分氧化铁还原出来,增加金属收得率,提高钢渣中具有胶凝活性的硅酸盐含量,为钢渣的后续资源化利用创造了条件。随着熔融钢渣中游离氧化钙和氧化铁的逐步减少,钢渣的性能得到改善,粘度升高,挂壁性能和高温稳定性提高,溅渣护炉效率提高。
39.将经过炉内高温改质处理过的性能稳定的转炉熔融钢渣倒入事先装有辅助改质剂的渣罐中,转炉出渣时,随着转炉的倾动,熔融钢渣和熔化后的钢渣改质剂以液-液状态同时从转炉炉口倒出,冲向渣罐底部。因转炉炉口距离渣罐底部有超过3米(3-5米)的落差,钢渣和钢渣改质剂在下落过程中因重力而产生加速度运动,当落到渣罐底部时渣流的下落速度可达7-10m/s,为辅助改质剂中的氧化硅、氧化铝与钢渣中少量残余的f-cao和f-mgo接触、反应创造充足的动力学条件,实现钢渣的充分改质。
40.渣罐从转炉下经渣罐台车或抱罐车转运到渣处理车间,之后通过滚筒工艺快冷处理成性能稳定的粒状钢渣,在线磁选、筛分,粒/块状金属铁(俗称渣钢)直接返炼钢工序回用,粒径小于20mm的颗粒状钢渣(俗称尾渣)作为高性能商品渣直接被用于喷砂除锈、路面用沥青混凝土骨料等行业和工程中;完全改质后的转炉熔融钢渣也可以通过热闷工艺缓冷处理成粉状尾渣,经磁选、筛分和进一步磨粉处理,生成钢渣微粉,作为水泥熟料直接替代水泥。
41.因此,本发明在不影响炼钢工艺和不增加额外工艺设备的条件下,实现转炉熔融钢渣的炉内改质和炉外辅助改质,f-cao、f-mgo可以大幅度降低,钢渣的稳定性极大提高,为后续高价值利用创造了条件。
42.本发明的有益效果:
43.1、本发明选用金属硅的混合物而非其它现有技术方案中的单质碳作为改质剂,主要有几个方面的优点:
44.a)硅的密度比碳大,不易挥发,几乎全部参与反应,效率高;
45.b)硅的中间产物sio2是很好的改质剂,继续参与改质反应,反应的最终产物硅酸盐具有胶凝活性,是钢渣水泥的有效成分;
46.c)硅反应过程中不产生废气,不需要增强或额外增设尾气收集和净化设施,工艺过程相对简单、清洁。
47.2、混合充分:钢渣改质剂加入转炉内后受热熔化,钢渣改质剂和熔渣实现液-液同相混合,炉内喷吹搅拌,动力足,较炉外固液混合、搅拌工艺的混合效果好。
48.3、f-cao、f-mgo含量大幅降低:f-cao、f-mgo不仅在炉内与高温液相钢渣改质剂混合接触、反应,而且在炉渣倒入渣罐的瞬间,炉渣中残存的少量f-cao、f-mgo再次与辅助改质剂接触、反应,含量得到了大幅度降低。
49.4、尾渣性能好、利用价值高:改质后的转炉钢渣化学性能稳定,经过滚筒工艺的快冷粒化处理,析出的硅酸钙等晶粒细小、粒渣强度高,骨料性能突出,可以替代日益紧缺的碎石,用于钢渣沥青混凝土高等级公路建设、透水沥青混凝土、彩色路面砖、特种除锈剂等高价值工程领域,发挥钢渣特有的资源价值。
50.5、工艺简单:充分利用熔渣的显热、溅渣护炉工艺的喷吹搅拌动力和转炉倒渣时因高度差引起的冲击动力,这些操作都是转炉必须的作业,减少了额外的操作步骤。
附图说明
51.图1为本发明实施例钢渣热态改质工艺流程图。
具体实施方式
52.下面结合实施例对本发明作进一步说明。
53.实施例1
54.参见图1,本发明利用所述钢渣改质剂进行钢渣热态改质处理工艺,包括以下步骤:
55.1)某钢厂300吨转炉,每炉排渣25吨,转炉熔融钢渣二元碱度4.27,f-cao含量6.50%,转炉出钢完毕后,向转炉熔融钢渣中加入粒径为3.0~10.0mm的所述钢渣改质剂2.5吨;
56.2)所述钢渣改质剂加入后,对炉内钢渣下枪吹氮搅拌5min,完成转炉熔融钢渣炉内改质及溅渣护炉作业;
57.3)炉内改质后的转炉熔融钢渣倒入装有辅助改质剂的渣罐中,进行熔融钢渣与辅助改质剂的搅拌、混合,实现转炉钢渣的充分改质;
58.4)将充分改质后的转炉熔融钢渣转运至500m外的钢渣处理车间,之后通过滚筒工艺快冷处理成粒状钢渣。
59.粒状钢渣经在线磁选、筛分,粒/块状金属铁(俗称渣钢)直接返炼钢工序回用,颗粒状钢渣(俗称尾渣)粒径小于20mm,其中小于10mm的粒渣不低于85%,钢渣中的游离氧化钙下降到1.55%(表1所示),满足水泥行业和道路、建筑工程基本要求,作为高性能商品渣直接送用户开展高价值资源化利用,改质前后转炉钢渣的成分见表1。
60.表1
[0061][0062]
实施例2
[0063]
1)某钢厂250吨转炉,每炉排渣25吨,转炉熔融钢渣二元碱度3.86,f-cao含量5.50%,转炉出钢完毕后,向转炉熔融钢渣中加入粒径为3.0~10.0mm的所述钢渣改质剂1.5吨;
[0064]
2)所述钢渣改质剂加入后,对炉内钢渣下枪吹氮搅拌5min,完成转炉熔融钢渣炉内改质及溅渣护炉作业;
[0065]
3)炉内改质后的转炉熔融钢渣倒入装有5吨辅助改质剂的渣罐中,辅助改质剂选用干燥高炉渣,利用转炉炉口距渣罐底部的高度差,转炉钢渣倾倒产生的冲击力对辅助改质剂进行搅拌、混合,实现转炉钢渣的充分改质;
[0066]
4)将充分改质后的转炉熔融钢渣转运至300m外的钢渣处理车间,之后通过滚筒工艺快冷处理成粒状钢渣。
[0067]
粒状钢渣经在线磁选、筛分,粒/块状金属铁(俗称渣钢)直接返炼钢工序回用,颗粒状钢渣(俗称尾渣)的粒径0.5~20mm,其中小于10mm的粒渣不低于85%,钢渣中的游离氧化钙下降到1.23%,满足水泥行业和道路、建筑工程基本要求,作为高性能商品渣直接送用户开展高价值资源化利用,改质前后转炉钢渣的成分见表2。
[0068]
表2
[0069][0070]
实施例3
[0071]
1)某钢厂250吨转炉,每炉排渣25吨,转炉熔融钢渣二元碱度3.64,f-cao含量7.30%,转炉出钢完毕后,向转炉熔融钢渣中加入粒径为3.0~10.0mm的所述钢渣改质剂1.0吨;
[0072]
2)所述钢渣改质剂加入后,对炉内钢渣下枪吹氮搅拌3min,完成转炉熔融钢渣炉内改质及溅渣护炉作业;
[0073]
3)炉内改质后的转炉熔融钢渣倒入装有4吨辅助改质剂的渣罐中,辅助改质剂选用高炉熔渣,利用转炉炉口距渣罐底部的高度差,转炉钢渣倾倒产生的冲击力对辅助改质
剂进行搅拌、混合,实现转炉钢渣的充分改质;
[0074]
4)将充分改质后的转炉熔融钢渣转运至300m外的钢渣处理车间,之后通过滚筒工艺快冷处理成粒状钢渣。
[0075]
粒状钢渣经在线磁选、筛分,粒/块状金属铁(俗称渣钢)直接返炼钢工序回用,颗粒状钢渣(俗称尾渣)的粒径0.5~30mm,其中小于10mm的粒渣不低于85%,钢渣中的游离氧化钙下降到2.23%,满足水泥行业和道路、建筑工程基本要求,作为高性能商品渣直接送用户开展高价值资源化利用,改质前后转炉钢渣的成分见表3。
[0076]
表3
[0077][0078]
其它实施例的操作过程同实施例1、2、3,但钢渣改质剂、辅助改质剂的化学成分和加入量不同,钢渣改质后f-cao和f-mgo含量随之发生变化,本发明实施例1~6添加的钢渣改质剂及辅助改质剂成分见表4,改质过程中工艺控制条件参见表5,钢渣改质前后f-cao和f-mgo含量参见表6。
[0079]
表4 单位:重量百分比
[0080][0081]
表5
[0082]
[0083][0084]
表6
[0085][0086]
由表6可以看出,钢渣改质后f-cao和f-mgo含量得到了大幅度降低,改质后钢渣中f-cao含量可降低77%,改质后钢渣中f-mgo含量可降低75%。
再多了解一些
本文用于企业家、创业者技术爱好者查询,结果仅供参考。