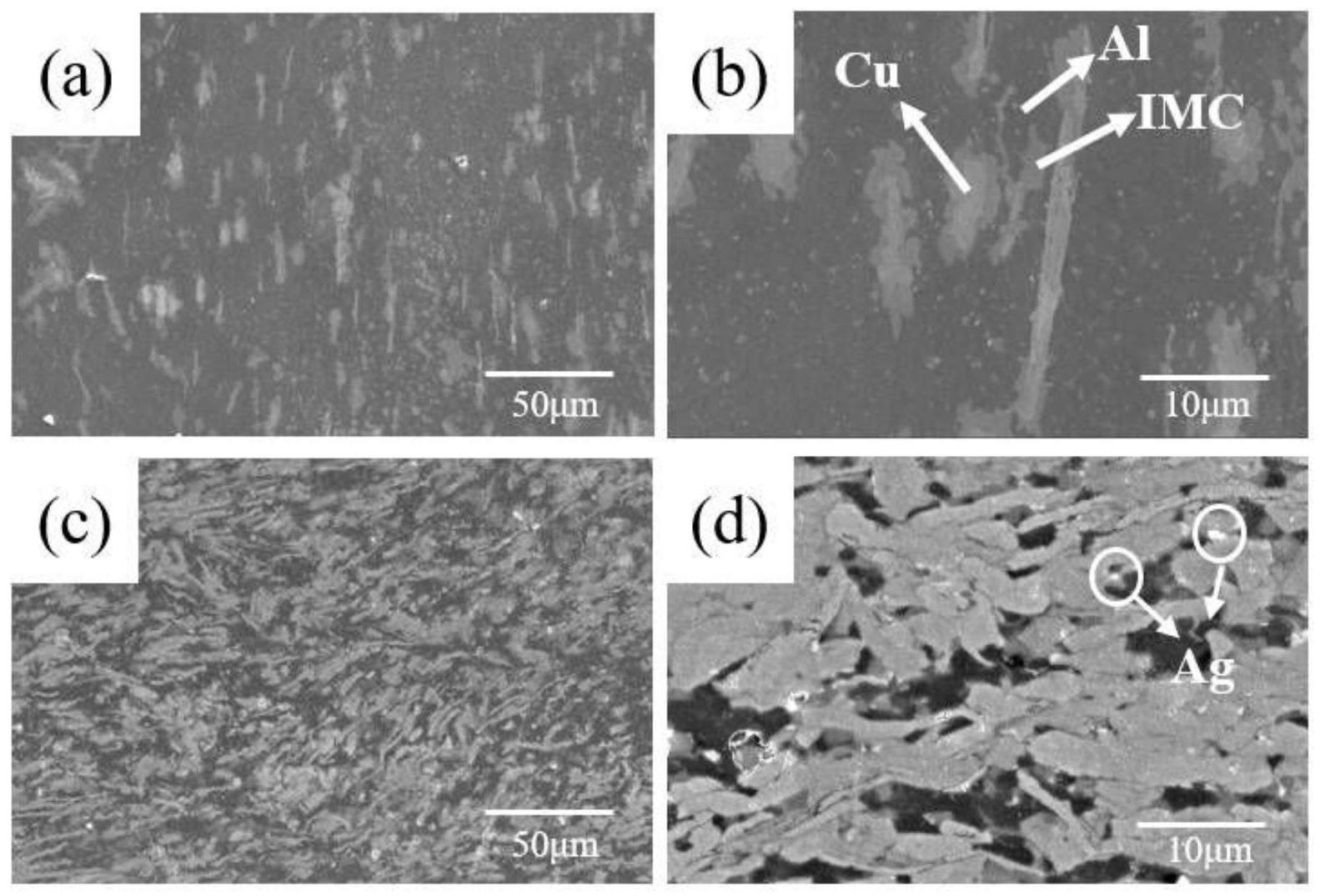
一种ag强化al-cu复合材料及其制备方法
技术领域
1.本发明涉及al-cu复合材料领域,具体涉及一种ag强化al-cu复合材料及其制备方法。
背景技术:
2.铝铜基复合材料在航空航天,汽车等领域有着极为广泛的应用,比如说高al复合材料的轻质量在汽车轻量化领域有很大的应用前景,高cu复合材料可以应用于电触头,这都是由于al-cu合金具备轻质量、高导电性、耐腐蚀性等众多优异的性能,并吸引许多人进行研究。al-cu合金的制备方法有铸造、焊接、粉末冶金等。粉末冶金技术的优势:烧结温度低,晶粒细小,可以通过控制界面反应来调控扩散速率;能够控制烧结样品的形状;烧结过程中涉及到液相烧结。
3.目前限制al-cu合金应用的因素之一是制备过程中产生的金属间化合物(imcs),这是因为imc与基体的界面处在材料工作的过程中很容易产生裂纹,成为失效的源头使al-cu合金的力学性能降低。cu-al复合材料样品中的imcs主要有al4cu9,alcu和al2cu三种。在al-cu-al多层复合材料在断裂过程中裂纹沿界面的扩展主要是通过imcs层进行,并且材料的电导率随着imcs的增加而降低。在拉伸加载下,材料破坏的过程首先是在imcs层产生裂纹,随后裂纹沿着al晶粒边界扩展,直致材料失效。imcs的产生使al-cu合金的机械性能大幅下降,限制了其应用,因此通过其他的方法提高al-cu合金的机械性能是很迫切的。
技术实现要素:
4.本发明的目的在于提供一种ag强化al-cu复合材料及其制备方法,al-cu复合材料中引入ag,通过弥散强化和固溶强化共同增强复合材料的力学性能,所得复合材料具有高致密度、高硬度、高拉伸强度等优点;制备方法简单,烧结温度低,具有广泛的工业应用前景。
5.为了解决上述技术问题,本发明采用如下技术方案:
6.提供一种ag强化al-cu复合材料,按质量百分比计,ag含量为2-5%,cu含量为20-65%,余量为al。
7.按上述方案,所述ag强化al-cu复合材料中存在ag2al相和ag(cu)固溶体。
8.按上述方案,所述ag强化al-cu复合材料通过将al粉、cu粉、ag粉和聚乙烯醇缩丁醛酯(pvb)混合后球磨、干燥、排胶、预压成型、真空热压烧结制备得到。优选地,al粉粒径为1-2μm,cu粉粒径为3-5μm,ag粉粒径为400-500nm。
9.按上述方案,所述ag强化al-cu复合材料致密度大于99%。
10.提供一种ag强化al-cu复合材料的制备方法,包括以下步骤:
11.1)将al粉、cu粉、ag粉和聚乙烯醇缩丁醛酯(pvb)混合后,加入溶剂进行球磨,球磨结束后经除气泡、过滤后得到金属粉非水基流延浆料;
12.2)将步骤1)所得浆料进行干燥、排胶得混合粉体,将混合粉体预压成型,最后在真
空热压环境下烧结制备得到al强化cu-ag复合材料。
13.按上述方案,所述步骤1)中,以al粉、cu粉和ag粉为总质量,按质量百分比计,ag粉占总质量的2-5%,cu粉占总质量的20-65%。
14.按上述方案,所述步骤1)中,聚乙烯醇缩丁醛酯质量占al粉、cu粉和ag粉总质量的2-3%。
15.按上述方案,所述步骤1)中,al粉粒径为1-2μm;cu粉粒径为3-5μm;ag粉粒径为400-500nm。
16.按上述方案,所述步骤1)中,溶剂为乙醇和丁酮质量比为1:1的混合液。
17.按上述方案,所述步骤1)中,球磨条件为球磨24-48小时,球磨转速为100-120r/min。
18.按上述方案,所述步骤2)中,干燥条件为:26-28℃干燥24-48小时,干燥为了确保乙醇溶剂完全挥发。
19.按上述方案,所述步骤2)中,排胶条件为:升温速率为0.2-2℃/min,480-500℃下排胶1-1.5小时。
20.按上述方案,所述步骤2)中,预压成形条件为:将al-cu-ag混合粉体置于烧结磨具中,在20-30mpa的压力下预压5-10分钟。
21.按上述方案,所述步骤2)中,烧结条件为:温度为485-500℃,压力为250-300mpa,烧结时间为2-3小时。
22.按上述方案,所述步骤2)中,烧结时升温速率为10-15℃/min。
23.按上述方案,所述步骤2)中,事先在烧结模具表面涂阻焊剂,再装入预压成型的块体。阻焊剂的作用是防止烧结过程中烧结元素扩散到模具内部,造成对模具的污染。
24.本发明通过选择加入ag改性al-cu,有以下三个理由:一方面因为纯银纯铝的原子间距十分接近,al的晶格参数不会因为ag的大量加入而受到影响,因此,溶质失配可以被认为是最小的,溶质引起的应变可以在很大程度上被忽略。另一方面,引入的ag与al生成ag2al相,均匀分布在基体起到弥散强化的作用,同时也会形成ag(cu)固溶体,固溶体会造成部分晶格畸变,使材料的强度提高;此外,也会有部分ag聚集在al-cu界面处阻碍al-cu间的扩散,减少金属间化合物的生成,最终得到的al-cu-ag复合材料的力学性能得到了大幅提高。
25.本发明的有益效果如下:
26.1.本发明提供一种ag强化al-cu复合材料,al-cu复合材料中引入ag,通过弥散强化和固溶强化共同增强复合材料的力学性能,所得复合材料极限拉伸强度显著提升,致密度高,超过99%,硬度高。
27.2.本发明通过粉末冶金制造方法将ag元素引入制备al-cu-ag复合材料,引入的ag与al生成ag2al相,与cu形成ag(cu)固溶体,所得复合材料力学性能优异,同时制备方法简单,烧结温度低,条件温和可控,具有广泛的工业应用前景。
28.3.进一步地,使用纳米ag,并选择al粉和cu粉不同级配,不同粒径粉体相互配合,进行缝隙填充,复合材料可获得高致密度。同时,因为纳米ag熔点低,在200℃下即可软化,在高压的条件下能够流动并填充孔洞,有利于致密化的过程,降低烧结温度。
附图说明
29.图1实施例1和2制备所得al-cu-ag复合材料的sem图,其中(a)-(b)是实施例1制备所得al-20cu-ag复合材料的sem图,图(c)-(d)是实施例2制备所得al-50cu-ag复合材料的sem图。
30.图2是实施例2制备所得al-50cu-ag复合材料中的tem图像,其中图b是图a的晶界处存在的ag2al的局部放大图。
31.图3是实施例2制备所得al-50cu-ag复合材料中的ag(cu)固溶结构测试图,其中图(a)为ag(cu)固溶体的tem图像,图(b)为ag(cu)固溶体的hrtem图像,图(c)和(d)ag(cu)固溶体的eds图像。
32.图4是实施例1-3制备所得al-cu-ag复合材料与对应al-cu复合材料的拉伸强度图。
具体实施方式
33.下面结合实例进一步阐述本发明的内容,但本发明的内容不仅仅局限于下面的实施案例。
34.实施例1
35.提供一种ag强化al-cu复合材料的制备方法,包括以下步骤:
36.1)首先将al粉、cu粉、ag粉与pvb混合,其中按质量百分比计,以al粉、cu粉和ag粉为粉体总质量,pvb占粉体总质量的2.7%,铜粉占粉体总质量的20wt%,ag粉占粉体总质量的3%,铝粉的粒径为1μm,纯度为99.9%,铜粉的粒径为5μm,纯度为99.9%,银粉的粒径为500nm,纯度为99.9%;选取质量比为1:1的乙醇和丁酮作为溶剂,将上述原料置于球磨罐中,在行星球磨机中球磨24小时,转速为120r/min,使原料均匀混合,随后将料浆放入干燥箱在28℃下干燥24小时。
37.2)排胶、烧结:将步骤1)干燥后的粉体放置在排胶炉中,抽真空气氛,以0.2℃/min的速度升温到480摄氏度保温1小时排胶;将排胶完成的粉体置于直径25mm的碳化钨模具中,再施加30mpa的压力预压5分钟使其成型后取出,之后模具上喷涂阻焊剂,再将预压成型的块体放置在模具中,最后放在真空热压炉中,升温速度为10℃/min升温到485℃,压力为300mpa,保温2小时后自然冷却到室温,得到al-20cu-ag复合材料的拉伸强度为如图4所示的170.36mpa,远高于al-20cu的105.48mpa;硬度为113.5hv,致密度为99.12%。
38.实施例2
39.提供一种ag强化al-cu复合材料的制备方法,包括以下步骤:
40.1)首先将al粉、cu粉、ag粉与pvb混合,其中按质量百分比计,以al粉、cu粉和ag粉为粉体总质量,pvb占粉体总质量的2.7%,铜粉占粉体总质量的50wt%,ag粉占粉体总质量的3%,铝粉的粒径为1μm,纯度为99.9%,铜粉的粒径为5μm,纯度为99.9%,银粉的粒径为500nm,纯度为99.9%;选取质量比为1:1的乙醇和丁酮作为溶剂,将上述原料置于球磨罐中,在行星球磨机中球磨24小时,转速为120r/min,使原料均匀混合,随后将料浆放入干燥箱在28℃下干燥24小时。
41.2)排胶、烧结:将步骤1)干燥后的粉体放置在排胶炉中,抽真空气氛,以0.2℃/min的速度升温到480摄氏度保温1小时排胶;将排胶完成的粉体置于直径25mm的碳化钨模具
中,再施加30mpa的压力预压5分钟使其成型后取出,之后模具上喷涂阻焊剂,再将预压成型的块体放置在模具中,最后放在真空热压炉中,升温速度为10℃/min升温到485℃,压力为300mpa,保温2小时后自然冷却到室温,得到al-50cu-ag复合材料的拉伸强度为如图4所示的159.43mpa,远高于al-50cu的71.56mpa,硬度为163.3hv致密度为99.84%。
42.实施例3
43.提供一种ag强化al-cu复合材料的制备方法,包括以下步骤:
44.1)首先将al粉、cu粉、ag粉与pvb混合,其中按质量百分比计,以al粉、cu粉和ag粉为粉体总质量,pvb占粉体总质量的2.7%,铜粉占粉体总质量的62wt%,ag粉占粉体总质量的3%,铝粉的粒径为1μm,纯度为99.9%,铜粉的粒径为5μm,纯度为99.9%,银粉的粒径为500nm,纯度为99.9%,选取质量比为1:1的乙醇和丁酮作为溶剂,将上述原料置于球磨罐中,在行星球磨机中球磨24小时,转速为120r/min,使原料均匀混合,随后将料浆放入干燥箱在28℃下干燥24小时。
45.2)排胶、烧结:将步骤1)干燥后的粉体放置在排胶炉中,抽真空气氛,以0.2℃/min的速度升温到480摄氏度保温1小时排胶;将排胶完成的粉体置于直径25mm的碳化钨模具中,再施加30mpa的压力预压5分钟使其成型后去除,之后模具上喷涂阻焊剂,再将预压成型的块体放置在模具中,最后放在真空热压炉中,升温速度为10℃/min升温到485℃,压力为300mpa,保温2小时后自然冷却到室温,得到al-62cu-ag复合材料的拉伸强度为如图4所示的79.29mpa,远高于al-62cu的48.07mpa,硬度为170hv,致密度为99.31%。
46.图1为实施例1和2制备所得al-cu-ag复合材料的sem图,其中(a)-(b)是实施例1制备所得al-20cu-ag复合材料的sem图,图(c)-(d)是实施例2制备所得al-50cu-ag复合材料的sem图。图中显示:在图中亮的相和暗的相分别是cu和al,灰色相为imc(金属间化合物),未发现明显的孔洞。ag元素在基体中分布均匀,尺寸约为500nm,样品中有少量imc相生成,随着cu含量的增加,imc相也随之增加,同时ag元素部分发生聚集,还有一部分在基体中仍是均匀分布的状态。
47.图2是实施例2制备所得al-50cu-ag复合材料中的的tem图像,可显示ag2al强化结构。图中显示:在基体中析出的ag2al大多分布在界面处,在界面处由于缺陷的存在导致能量较高,能够为新相的形成提供成核位点,因此含ag化合物的偏析会倾向于在界面位置,导致了界面处含ag化合物的存在。
48.图3是实施例2制备所得al-50cu-ag复合材料中的ag(cu)固溶结构。图中显示:在eds中cu元素集中分布的位置伴随着ag元素的出现,根据hrtem图像得知ag(110)晶面的晶面间距由0.1443nm变为0.142nm,这是因为有cu原子扩散到ag晶格中,与ag原子发生互换,形成置换固溶体,导致其晶面间距发生变化。
49.在上述实施例中生成了弥散分布的ag2al相,对样品的整体强度起到第二相强化的作用。除此之外,根据固体经验电子理论(eet),ag-al合金中ag2al相最强共价电子对数为0.4733,远大于纯al和纯ag的0.2086和0.3649,ag2al中的共价电子对数主要集中在第一和第二近的ag-ag键上,这两个键被称为最强键和次强键,他们在晶胞内形成一个六边形的共价键网络,这种强键络的存在使位错运动时难以切割,从而对材料起到一定的强化作用。固相烧结过程中压力和温度的结合导致颗粒之间发生剪切,使al-cu颗粒上的氧化物涂层断裂,从而能够提高界面结合强度。由于纯ag与纯al的原子间距十分接近,加入的ag在al中
的固溶形成al(ag)固溶体并不会引起晶格畸变,对滑移面上的位错运动无显著影响,但是形成的ag(cu)固溶体造晶格畸变,增大位错运动的阻力,起到固溶强化的作用。根据和不含ag的样品比较结果,对强度增加贡献较大的是ag与cu之间形成置固溶体导致的固溶强化以及ag2al的形成所导致的第二相弥散强化。
50.以上仅为本发明的较佳实施例而已,并不用以限制本发明,凡在本发明的精神和原则之内,所作的任何修改、等同替换、改进等,均应包含在本发明的保护范围之内。
再多了解一些
本文用于企业家、创业者技术爱好者查询,结果仅供参考。