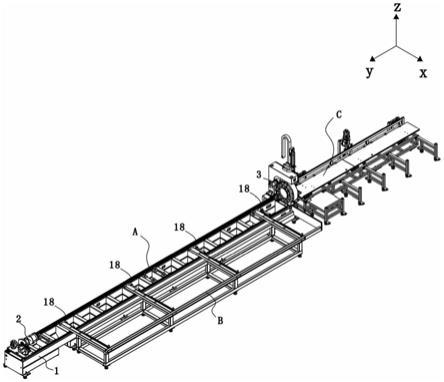
激光切管机
1.本技术是专利申请号为“202110683078.8,申请日为“2021年06月21日”,名称为“一种激光切管系统”的专利申请的分案申请
技术领域
2.本发明涉及激光切割设备领域,特别涉及一种激光切管机。
背景技术:
3.随着激光切管机的日益改进,激光切管机需要满足多种类型管道(如圆管、方管、异型管)以及重型长管的加工。激光切管机主要包括底架、分别设置在底架上的移动卡盘、固定卡盘、激光切割组件、多个用于支撑管件的随动支撑结构、用于驱动移动卡盘移动的驱动机构。随动支撑结构能够对管件进行支撑上料,以及减少管件在加工过程中产生的晃动,提高加工精度。为了保证现有底架和走线盒是独立设置的,走线盒设置在底架上,为了对多个随动支撑结构进行供电供气,电控箱的电线和气管通过走线盒连接各个随动支撑结构,但是走线盒会占用较多的机床空间,影响切管机的紧凑性,同时走线盒也会额外增加制造成本。另外,移动卡盘、固定卡盘、激光切割组件均需定期添加润滑油进行润滑维护,由于受到底架的干涉影响,每个工件润滑后所要回收的润滑油需要分别输送至一个对应的集油容器进行收集处理,所以无法将所有润滑油集中回收至同一个集油容器中。
4.可见,现有技术还有待改进和提高。
技术实现要素:
5.鉴于上述现有技术的不足之处,本发明的目的在于提供一种激光切管机,旨在通过上料装置多种类型的重型管材进行上料以及利用底架的结构,更好地进行走线。
6.为了达到上述目的,本发明采取了以下技术方案:
7.一种激光切管机,包括底架、若干个设置在底架上的随动支撑结构、依次设置在底架上的移动卡盘、固定卡盘以及激光切割组件、用于驱动移动卡盘移动的移动台驱动组件;所述底架包括相互平行的第一梁体和第二梁体、多个设置在第一梁体和第二梁体之间的连接梁体,所述第一梁体和第二梁体均由若干矩形管堆叠连接而成,所述第一梁体和/或第二梁体上开设有若干个与随动支撑结构位置相匹配的出线长孔,所述第一梁体和第二梁体的外侧壁上均开设有第一过线长孔,所述第一梁体和第二梁体的内侧壁上均开设有第二过线长孔;所述第一梁体包括第一下横梁和堆叠放置在第一下横梁顶面上的第一上横梁,第二梁体包括第二下横梁和堆叠放置在第二下横梁顶面上的第二上横梁,第一上横梁和第二上横梁均为矩形管,第一上横梁和/或第二上横梁的内侧壁上开设有若干个出线长孔,第一下横梁和第二下横梁的底部均设有若干组支脚组件。
8.所述随动支撑结构设置在第一梁体和第二梁体之间,所述随动支撑结构包括竖板、滑动设置在竖板上的滑座、设置在滑座顶部的承托组件、用于驱动滑座竖向移动的驱动装置;所述承托组件包括竖直设置的支承板、两块分别设置在支承板两端部上的侧板、可转
动地设置在两块侧板之间的滚筒;所述侧板的顶面高度高于滚筒的最高点。
9.所述移动卡盘包括设置在第一梁体和第二梁体的上表面上的轨道安装板、设置在轨道安装板上的y轴导轨,与y轴导轨滑动连接的移动台、设置在移动台上的卡盘主体、用于驱动卡盘主体转动的第一电机,所述第一电机通过第一齿轮传动组件带动卡盘主体转动,第一齿轮传动组件通过第一自动润滑组件进行润滑;所述第一齿轮传动组件的外部套有第一挡油罩;所述固定卡盘包括固定在底架上的支座、可转动地设置在支座上的装夹器、用于驱动装夹器转动的第二电机,所述第二电机通过第二齿轮传动组件带动装夹器转动,第二齿轮传动组件通过第二自动润滑组件进行润滑;所述第二齿轮传动组件的外部套有第二挡油罩。
10.所述移动台驱动组件包括竖直设置在移动台上的第三电机、设置在第三电机主轴上的y轴齿轮、设置在任一块轨道安装板上的y轴齿条,所述y轴齿轮与y轴齿条啮合传动,所述y轴齿条通过第三自动润滑组件进行润滑;所述轨道安装板上设有沿y轴延伸的集油槽,位于所述集油槽的底面开设第一回油孔,所述第一挡油罩设置在移动台上,所述移动台上开设有回油槽,所述第一挡油罩的底部开设有第二回油孔,所述第二回油孔与所述回油槽的一端连通;位于所述回油槽的另一端的底面上开设有与集油槽连通的第三回油孔,所述第一回油孔的输出端连接第一管道,所述第一管道穿过第一过线长孔连接至集油容器。
11.所述激光切割组件包括横梁支架、设置在横梁支架上的x轴滑移机构、设置在所述x轴滑移机构上的x轴滑移支架、设置在x轴滑移支架上的z轴滑移机构、设置在z轴滑移机构上的z轴滑移支架、设置在z轴滑移支架底部的激光切割头,所述x轴滑移机构包括设置在横梁支架上的x轴导轨和x轴齿条、安装在x轴滑移支架上的第四电机、设置在第四电机主轴上的x轴齿轮,所述第四电机通过第x轴齿轮和x轴齿条的啮合传动带动x轴滑移支架和设置在x轴滑移支架上的部件沿x轴运动,x轴齿条通过第四自动润滑组件进行润滑,x轴齿条的下方设置集油壳体。
12.所述第二挡油罩的底部设有第四回油孔,第四回油孔通过第二管道连接至集油容器;所述集油壳体的底部设有第五回油孔,第五回油孔通过第三管道连接至集油容器;所述第一管道、第二管道、第三管道的出油端分别连接在一个四通接头的接口上,四通接头上的其中一个接口通过第四管道连接至集油容器。
13.有益效果:
14.与现有技术相比,与电控箱连接的电线和气管通过第一过线长孔进入到第一梁体和第二梁体的走线腔中,电线和气管从对应的出线长孔穿出后即可与随动支撑结构连接,从而无需额外增设走线盒,充分利用了第一梁体或第二梁体的型材结构所提供的腔体空间,节省了设置走线盒带来的材料成本,线路排布整齐,更加美观规范。另外,为了便于对润滑油进行回收,脱离各部件的润滑油会汇流到一根回油管中,再由该回油管排送至一个设置在底架外部的集油容器中,为了防止回油管干涉移动卡盘的移动,回油管先穿过第一过线长孔,再穿过第二过线长孔伸展至设置底架外部的集油容器中,由于回油管会低于移动卡盘的高度,一方面不会干涉移动卡盘工作,另一方面润滑油也会在重力势能的作用下更好地输送至集油容器中。
附图说明
15.图1为本发明提供的激光切管机的立体图。
16.图2为底架的立体图。
17.图3为底架的部分结构示意图。
18.图4为图2中l1区域的局部放大图。
19.图5为尾料落料组件的结构示意图。
20.图6为移动卡盘和固定卡盘的立体图一。
21.图7为移动卡盘和固定卡盘的立体图二。
22.图8为图7中l2区域的局部放大图。
23.图9为移动卡盘和固定卡盘的立体图三。
24.图10为图9中l3区域的局部放大图。
25.图11为图9中l4区域的局部放大图。
26.图12为第一自动润滑组件的结构示意图。
27.图13为随动支撑结构的立体图。
28.图14为图13中l5区域的局部放大图。
29.图15为随动支撑结构的俯视图。
30.图16为上料装置的立体图一。
31.图17为上料装置的俯视图。
32.图18为图17中的a
‑
a剖面轴测图。
33.图19为图18中l6区域的局部放大图。
34.图20为上料装置的立体图二。
35.图21为图20中l7区域的局部放大图。
36.图22为接料架的立体图一。
37.图23为接料架的立体图二。
38.图24为接料架的左视图。
具体实施方式
39.本发明提供一种激光切管机,为使本发明的目的、技术方案及效果更加清楚、明确,以下参照附图并举实施例对本发明进一步详细说明。应当理解,此处所描述的具体实施例仅用以解释本发明,并不用于限定本发明的保护范围。
40.本文中,“前”为图1中接料架朝向激光切管机的方向,“后”与“前”反向。
41.请参阅图1
‑
图24,本发明提供一种激光切管系统,包括激光切管机a、用于对激光切管机a进行上料的上料装置b、用于接收激光加工成品的接料架c;所述激光切管机a包括底架1、若干个设置在底架上的随动支撑结构18、依次设置在底架1上的移动卡盘2、固定卡盘3以及激光切割组件5、用于驱动移动卡盘2移动的移动台驱动组件4;所述底架包括相互平行的第一梁体11和第二梁体12、多个设置在第一梁体和第二梁体之间的连接梁体13,所述第一梁体11和第二梁体12均由若干矩形管堆叠连接而成,所述第一梁体11和/或第二梁体12上开设有若干个与随动支撑结构位置相匹配的出线长孔151,所述第一梁体11和第二梁体12的外侧壁上均开设有第一过线长孔152,所述第一梁体11和第二梁体12的内侧壁上
均开设有第二过线长孔153。
42.激光切管机a在使用前需要进行合理的线路排布,与电控箱连接的电线和气管通过第一过线长孔152进入到第一梁体11和第二梁体12的走线腔中,电线和气管从对应的出线长孔151穿出后即可与随动支撑结构18连接,从而无需额外增设走线盒,充分利用了第一梁体11或第二梁体12的型材结构所提供的腔体空间,节省了设置走线盒带来的材料成本,线路排布整齐,更加美观规范。另外,移动卡盘2、固定卡盘3、激光切割组件5等部件均需定期添加润滑油进行润滑维护,为了便于对润滑油进行回收,脱离各部件的润滑油会汇流到一根回油管906中,再由该回油管906排送至一个设置在底架1外部的集油容器90中,为了防止回油管906干涉移动卡盘2的移动,回油管先穿过第一过线长孔152,再穿过第二过线长孔153伸展至设置底架1外部的集油容器90中,由于回油管906会低于移动卡盘2的高度,一方面不会干涉移动卡盘2工作,另一方面润滑油也会在重力势能的作用下更好地输送至集油容器90中。
43.实际应用中,激光切管机a与上料装置b和接料架c配合使用,解决了人工上下料带来费时费力的问题。工作时,上料装置b将管件型材(圆管、方管、矩形管、工字钢、槽钢、多边形管、三角管、扇形管、d形管椭圆管等多种异型管)运输至随动支撑结构18的正上方,使得多个随动支撑结构18共同举升管件至合适的夹持高度,移动卡盘2将管件的一端夹紧并且带动管件朝固定卡盘3方向移动,固定卡盘3夹紧管件的另一端后即可使激光切割组件5实现切割加工,经过切割加工的成品会通过接料架c进行下料承接,整个激光切管系统自动化地完成管材的切割加工,减少人力搬运,提高切管效率。在切管过程中,随动支撑结构18为工件提供随动支撑,辅助激光切管机a切割工件,减少管件在切割过程中产生的晃动,提高加工精度,当激光切管机上的移动卡盘2逐渐靠近某个随动支撑结构18至设定距离时,控制中心控制该随动支撑结构18下降,取消对工件提供随动支撑,从而避让对移动卡盘2。
44.具体的,请参阅图2和图3,所述第一梁体11包括第一下横梁112和堆叠放置在第一下横梁112顶面上的第一上横梁111,第二梁体12包括第二下横梁122和堆叠放置在第二下横梁122顶面上的第二上横梁121,第一上横梁111和第二上横梁121均为矩形管。为了便于走线,第一上横梁111和/或第二上横梁121的内侧壁上开设有若干个出线长孔151,第一下横梁112和第二下横梁122的底部均设有若干组支脚组件14。每个出线长孔151位于一个随动支撑结构18的一旁,电线和气管借助第一上横梁111或第二上横梁121中内腔作为走线腔,从而无需额外增设走线盒,充分利用了第一上横梁111或第二上横梁121的型材结构所提供的腔体空间,消除了设置走线盒带来的材料成本,电线和气管从对应的出线长孔151中伸出即可与随动支撑结构18连接,线路排布整齐,更加美观规范。
45.当第一上横梁111和第二上横梁121上都设有出线长孔151时,使用人员可以根据实际走线习惯统一选择第一上横梁111上的出线长孔151或第二上横梁121上的出线长孔151进行排布,提高适用性。当然,电线可通过第一上横梁111上的出线长孔151进行走线,气管可通过第二上横梁121上的出线长孔151进行走线,线路排布合理。
46.需要理解的是,出线长孔151、第一过线长孔152以及第二过线长孔153中的长孔所指的是非圆形的孔,例如腰形孔、长方形孔等。
47.进一步的,请参阅图2
‑
图5,所述底架1上设有位于所述第一梁体11和第二梁体12之间的尾料落料组件,所述尾料落料组件形成一个用于接取管材尾料的尾料接收口161,该
结构简单、设置方便,通过该结构的设置,便于在完成切管后对尾料进行回收,移动卡盘2可将尾料直接投入到尾料接收口161中,工作人员可在尾料接收口161的下方放置接料盆。
48.优选的,所述尾料落料组件包括落料斜板162和两个支板163,所述落料斜板162设置在两个相邻的连接梁体13之间,两个支板163沿纵向延伸且与落料斜板162的下边沿连接,落料斜板162朝向第二梁体12,第二下横梁122上开设有与落料斜板162相适配的断口164,接料盆可通过断口164进入底架1的内部并且放置在落料斜板162下边沿的正下方,移动卡盘2将尾料投放到尾料接收口161后,尾料在落料斜板162的导引下滑入接料盆中,便于后续处理。
49.具体的,请参阅图3,所述连接梁体13包括连接第一上横梁111和第二上横梁121的第一连接管131、连接第一下横梁112和第二下横梁122的第二连接管132,第一连接管131堆叠设置在第二连接管132的上方。第一连接管131和第二连接管132也采用矩形管,连接强度好;第一连接管131的两端通过焊接的方式分别与第一上横梁111和第二上横梁121连接,第二连接管132的两端通过焊接的方式分别与第一下横梁112和第二下横梁122连接。
50.进一步的,请参阅图3和图4,所述第一梁体11和第二梁体12之间设有若干吊运支撑构件17,每个所述吊运支撑构件17包括设置在第一上横梁111和第二上横梁121之间的吊运连接管171、设置在吊运连接管171顶面上的吊运安装板172,每块吊运安装板172的上开设有吊环安装孔173,所述吊环安装孔173用于安装吊环,便于后续用吊臂吊运底架1。在本实施例中,为了便于提高吊运的平稳性,每个吊运连接管171上设有两块吊运安装板172,其中一块吊运安装板172靠近第一梁体11设置,另一块吊运安装板172靠近第二梁体12设置。
51.优选的,请参阅图2和图4,所述支脚组件14包括支撑板141和设置在支撑板141底部的脚杯142。支撑板141上设有与脚杯142上的调节螺杆144螺纹连接的螺纹孔,通过旋动调节螺杆144就能调节底架1的水平度,脚杯142的设置增大了其与地面的接触面积,从而提升摩擦力。
52.优选的,所述支撑板141上开设有地桩孔143,地桩孔143位于螺纹孔的一旁。在实际应用中,地桩孔143用于插入地桩,将底架1与地面固定,确保切管机的加工稳定性。
53.具体的,请参阅13
‑
15,所述随动支撑结构18设置在第一梁体11和第二梁体12之间,所述随动支撑结构18包括竖板181、滑动设置在竖板181上的滑座、设置在滑座顶部的承托组件183、用于驱动滑座竖向移动的驱动装置184;所述承托组件183包括竖直设置的支承板1831、两块分别设置在支承板1831两端部上的侧板1832、可转动地设置在两块侧板之间的滚筒1833;所述侧板1832的顶面高度高于滚筒1833的最高点。
54.多个随动支撑结构18安装在底架1上,底架1的一端设有可沿底架1横向移动的前卡盘,底架1的另一端固定有固定卡盘;工作时,上料机构19将管件(圆管、方管、异型管等)运输至动支撑结构的正上方,然后通过驱动装置184驱动承托组件183向上移动,使得多个随动支撑结构18上的滚筒1833共同举升管件至合适的夹持高度,即使管件(如圆管)在举升过程中沿滚筒1833的长度方向发生自移动,由于侧板1832的顶面高度高于滚筒1833的最高点,侧板1832对管件起到阻挡作用,防止管件脱离滚筒1833而滚落至地面上造成管件损伤。
55.随后,移动卡盘2通过移动夹持管件的前端并且驱动管件朝固定卡盘3方向移动,使得固定卡盘3能够夹持管件实现切割加工,在管件横向移动过程中,滚筒1833始终支撑管件,由于滚筒1833与管件之间为滚动摩擦,不会干涉管件横向移动,从而对管件起到随动支
撑的效果,减少管件在切割过程中产生的晃动。需要注意的是,当上料完后,上料装置b会复位以免干涉移动卡盘2移动,同样地,当某个随动支撑结构18干涉移动卡盘2的行进路径时,驱动装置184驱动承托组件183向下移动,取消对管件的随动支撑。
56.具体的,所述驱动装置184包括齿条1841、与齿条1841啮合传动的齿轮1842、固定在滑板182上的减速器1843和与减速器1843传动连接的驱动电机1844,所述齿轮1842套在驱动电机1844的主轴上;所述齿条1841沿竖向延伸且固定在竖板181上,所述齿轮1842设置在减速器1843的输出端上。驱动电机1844通过驱动齿轮1842正反向转动,在齿条1841的配合下,牵引滑板182竖向移动,从而使承托组件183达到举升管件的目的。驱动电机1844优选为伺服电机,由伺服电机配合减速器1843进行输出,可提供更大的支撑力,使随动支撑结构18能够支撑重型的管件。
57.进一步的,所述减速器1843通过侧向定位调整构件185固定在滑板182上,所述侧向定位调整构件185包括侧向调整板1851以及侧向调整螺钉,所述减速器1843固定在侧向调整板1851上,所述侧向调整板1851上设置有若干个沿横向延伸的调整长孔1852,所述滑板182设置有与调整长孔1852相对应的螺纹孔,所述侧向调整螺钉穿过所述调整长孔1852后螺纹连接在所述滑板182上。调整长孔1852中的长孔所指的是非圆形的孔,例如腰形孔、长方形孔等。由此,松开侧向调整螺钉移动侧向调整板1851即可改变驱动电机1844的位置,较为方便地调整齿轮1842与齿条1841的配合间隙,确保传动平稳性。
58.进一步的,所述竖板181上设有至少两根沿竖向延伸的导轨1861,所述滑板182通过上料滑块1862与对应的导轨1861滑动连接。通过这样设置,滑板182竖向移动顺畅、可靠,保证滚筒1833移动方向准确。
59.优选的,每根导轨1861的两端均设有挡块1863。挡块1863可以一对的形式设置,两个呈方形的挡块1863分别设置在导轨1861同一端的左右两侧,通过设置挡块1863,阻挡上料滑块1862脱离导轨1861。
60.优选的,所述滑板182上设有传感器支撑板1871,传感器支撑板1871上设有朝向竖板181的到位传感器1872,所述竖板181上设有能够触发到位传感器1872的上触发片1873和下触发片1874,所述上触发片1873位于下触发片1874的上方。上触发片1873和下触发片1874对应滑板182所能移动到的极限位置;在初始状态下,到位传感器1872正对朝向下触发片1874,控制系统通过控制驱动电机1844的启停从而控制承托组件183的上升高度;当到位传感器1872在上升过程中感应到上触发片1873时,到位传感器1872反馈信号至控制系统,表示滑板182和承托组件183上移至上极限高度,不能继续上移,此时转动驱动器应停止工作。
61.优选的,所述传感器支撑板1871上开设有沿竖向延伸的腰形调节孔1875,所述到位传感器1872能够安装在腰形调节孔75上。通过这样设置,到位传感器的位置在根据实际装配情况进行微调,适配性高。
62.请参阅图1、图16
‑
图21,所述上料装置b设在底架1的后方,所述上料装置b包括机架b4、上料滑轨b1、支撑块b2和连杆b3;所述上料滑轨b1固定在所述机架b4上,所述上料滑轨b1沿前后方向延伸;所述支撑块b2设置两个以上并沿左右方向排列,所述支撑块b2与所述上料滑轨b1相对滑动配合,所述支撑块b2的滑动方向沿上料滑轨b1的长度方向设置,所述支撑块b2支撑并运输管料;所有的所述支撑块b2分别固定连接所述连杆b3。
63.由上述可得,工作人员可把待搬运的管料可放置在支撑块b2上,由支撑块b2对管料进行支撑,当管料需要上料合适的位置时,可通过支撑块b2与上料滑轨b1的相对滑动带动管料往需要上料的位置移动,在支撑块b2滑动的过程中,通过该连杆b3的设置,实现支撑块b2的同步运动,其使用方便。
64.在实际使用中,由于支撑块b2滑动配合上料滑轨b1,支撑块b2与上料滑轨b1之间可发生相对滑动,进而,为了达到节省人力的目的,工作人员可通过推料装置驱动连接连杆b3。例如,工作人员可通过电动丝杆或电动推杆或伺服电缸等推料装置对连杆b3进行推动上料或进行拉动复位。
65.在一些实施例中,所述支撑块b2的底面开设有凹槽b21,所述凹槽b21沿前后方向延伸并贯穿所述支撑块b2,所述凹槽b21的内底面设有上料滑块,所述上料滑块配合连接所述上料滑轨b1,所述上料滑块可与所述上料滑轨b1相对滑动。
66.该结构简单、设置方便,凹槽b21内设置上料滑块,并利用上料滑块与上料滑轨b1相对滑动,实现了支撑块b2与上料滑轨b1之间相对滑动。
67.此外,凹槽b21可盖住上料滑轨b1和上料滑块,若为了进一步提高防尘效果,该凹槽b21的长度还可大于上料滑轨b1的长度。同时,通过该凹槽b21的设置,工作人员可利用凹槽b21进一步地进行限位,例如,可避免由于意外而出现使上料滑块倾侧而脱离上料滑轨b1的载荷的情况而导致上料滑块直接脱离上料滑块而使支撑块b2从上料滑轨b1上跌落的问题。
68.在实际使用中,该支撑块b2呈长条状,支撑块b2的长度方向与上料滑轨b1的长度方向同向,同时,凹槽b21的长度方向与上料滑轨b1的长度方向同向设置。
69.在一些实施例中,所述机架b4上设有支撑滑轮组件b5,所述支撑滑轮组件b5伸入所述凹槽b21内,所述支撑滑轮组件b5用于支撑所述凹槽b21的内底面。
70.在一些实施例中,所述支撑滑轮组件b5包括轴承主体b51和轴承座b52,所述轴承座b52固定连接所述机架b4,所述轴承主体b51设置在所述轴承座b52上,所述轴承主体b51可相对所述轴承座b52旋转,所述轴承主体b51的转动轴线沿左右方向延伸。
71.在一些实施例中,所述轴承座b52上开设有多个竖向设置的腰型孔b520,所述腰型孔b520通过螺丝固定连接所述机架b4,所述机架b4上设有限位块b6,所述限位块b6固定在所述轴承座b52的下方。使用时,工作人员可便捷地通过腰型孔b520以螺丝固定机架b4和轴承座b52,优选的,腰型孔b520的长度方向沿上下方向设置,一方面,可实现快速便捷地安装轴承主体b51,另外一方面,可运动安装后的轴承座b52在过大的载荷下向下滑动,起到对轴承座b52的保护作用。
72.在一些实施例中,轴承座b52包括底座b521、转轴b522,所述底座b521上设有两个相互平行的安装耳,所述底座b521固定连接所述机架b4,所述底座b521上开设有通孔,所述通孔贯穿两个所述安装耳,所述转轴b522穿过所述通孔,所述转轴b522的圆周面上开设有两道卡槽,两道所述卡槽分别设置于两个安装耳之间或两个安装耳的外侧,所述卡槽上配合有卡簧b5221,所述卡簧b5221的外径大于所述通孔的内径,所述轴承主体b51设置有若干个,所有的所述轴承主体b51套接在所述转轴b522上,所有的所述轴承主体b51设置于两个安装耳之间。该转轴b522用于安装套接轴承主体b51,使用时,通过卡槽、卡簧b5221的配合可实现对轴承主体b51的轴向限位,在需要更换轴承主体b51时,工作人员可通过拆卸卡簧
b5221后直接更换轴承主体b51,装拆十分方便。
73.在一些实施例中,所述机架b4上设有后定位块b72,所述支撑块b2的前端设有前定位块b71,所述前定位块b71和所述后定位块b72的高度分别高于所述支撑块b2的顶面,设置在所述支撑块b2上的管料设置于所述前定位块b71和所述后定位块b72之间。工件放置在支撑块b2上,通过后定位块b72和前定位块b71的设置,可对工件进行限位,避免在支撑块b2运动的过程中意外掉落。
74.在一些实施例中,所述连杆b3固定连接所述支撑块b2的最后端。使用时,工作人员可直接手动推动连杆b3从而带动所有支撑块b2同步运动,也可以是通过外设的推动构件,例如气缸、电动推杆等推动或拉动连杆b3,在推动构件与连杆b3的连接处一般可采用铰接的方式。
75.在一些实施例中,所述机架b4上设有第一承载板b81,所述支撑块b2顶面的前端设有第二承载板b82,所述第一承载板b81的高于所述第二承载板b82,所述第一承载板b81用于承载管料,所述第二承载板b82设置于所述第一承载板b81的前侧。通过第一承载板b81和第二承载板b82的设置,形成了一个台阶。使用时,待加工的管料可放置在第一承载板b81上,在需要上料时,可推动第一承载板b81上的工件到第二承载板b82上,工作人员还可进一步地配合自动化的推料装置用于推动管料从第一承载板b81掉落到第二承载板b82上,以满足生产节拍。
76.本发明中的上料装置b可上12000mm长管;支撑块b2上能同时放4根φ380mm大管;适用管件型材:圆管、方管、矩形管、工字钢、槽钢、多边形管、三角管、扇形管、d形管椭圆管等多种异型管;四根重载型直线导轨,八个重载型上料滑块,保持了重型管承重单根管重超过1000kg;直线导轨上料滑块组合使得料臂送到切管机过程中轻松又准确。
77.具体的,请参阅图6
‑
图10,所述移动卡盘2包括设置在第一梁体11和第二梁体12的上表面上的轨道安装板71、设置在轨道安装板71上的y轴导轨21,与y轴导轨21滑动连接的移动台22、设置在移动台22上的卡盘主体23、用于驱动卡盘主体23转动的第一电机24,所述第一电机24通过第一齿轮传动组件25带动卡盘主体23转动,第一齿轮传动组件25通过第一自动润滑组件62进行润滑;所述第一齿轮传动组件25的外部套有第一挡油罩61;所述固定卡盘3包括固定在底架1上的支座3、可转动地设置在支座3上的装夹器31、用于驱动装夹器31转动的第二电机32,所述第二电机32通过第二齿轮传动组件33带动装夹器31转动,第二齿轮传动组件33通过第二自动润滑组件7进行润滑;所述第二齿轮传动组件33的外部套有第二挡油罩81。工作人员通过电控方式驱动第一自动润滑组件62、第二自动润滑组件7工作,自动输出合适的润滑油至润滑轮上,润滑轮均匀地将润滑油转移第一齿轮传动组件25和第二齿轮传动组件33上,减少传动阻力,提高激光切管机的工作效果。
78.通过第一挡油罩61和第二挡油罩81,即使第一齿轮传动组件25和第二齿轮传动组件33高速运动,润滑油只会飞溅至第一挡油罩61和第二挡油罩81的内壁上,并随第一挡油罩61和第二挡油罩81的内壁回流至第一挡油罩61和第二挡油罩81的底部,便于收集处理。
79.进一步的,所述移动台驱动组件4包括竖直设置在移动台182上的第三电机41、设置在第三电机41主轴上的y轴齿轮1842、设置在任一块轨道安装板71上的y轴齿条42,所述y轴齿轮与y轴齿条42啮合传动,所述y轴齿条42通过第三自动润滑组件82进行润滑;所述轨道安装板71上设有沿y轴延伸的集油槽72,位于所述集油槽72的底面开设第一回油孔73,所
述第一挡油罩61设置在移动台22上,所述移动台22上开设有回油槽63,所述第一挡油罩61的底部开设有第二回油孔,所述第二回油孔与所述回油槽63的一端连通;位于所述回油槽63的另一端的底面上开设有与集油槽72连通的第三回油孔64,所述第一回油孔73的输出端连接第一管道901,所述第一管道901穿过第一过线长孔152连接至集油容器90。通过配置第一挡油罩61,第一齿轮1842传动组件25动作飞溅的润滑油会回流至第一挡油罩61的底部,避免污染车间,继而润滑油会流入回油槽63中,润滑油在回油槽63的导流下通过第三回油孔64流入集油槽72中。此外,用于润滑y轴齿条42的润滑油也会直接滴落到集油槽72中,最后集油槽72中的润滑油会流入第一回油孔73输出至集油容器90实现收集,有利于后续重复利用润滑油。
80.优选的,请参阅图6
‑
图9,所述激光切割组件5包括横梁支架51、设置在横梁支架51上的x轴滑移机构、设置在所述x轴滑移机构上的x轴滑移支架52、设置在x轴滑移支架52上的z轴滑移机构、设置在z轴滑移机构上的z轴滑移支架53、设置在z轴滑移支架53底部的激光切割头54,所述x轴滑移机构包括设置在横梁支架51上的x轴导轨57和x轴齿条56、安装在x轴滑移支架52上的第四电机55、设置在第四电机55主轴上的x轴齿轮,所述第四电机55通过第x轴齿轮和x轴齿条56的啮合传动带动x轴滑移支架52和设置在x轴滑移支架52上的部件沿x轴运动,x轴齿条56通过第四自动润滑组件91进行润滑,x轴齿条56的下方设置集油壳体92。所述集油壳体92的底部设有第五回油孔,第五回油孔通过第三管道903连接至集油容器90。通过这样设置,从x轴齿条56上滴落到集油壳体92中的润滑油会自动流动至集油壳体92中,无需拆卸集油壳体92倾倒润滑油。
81.优选的,请参阅图10,所述第一管道901、第二管道902、第三管道903的出油端分别连接在一个四通接头905的接口上,四通接头905上的其中一个接口通过第四管道904连接至集油容器90。通过这样设置,所有润滑油汇流到一个集油容器90中,便于统一处理润滑油。集油容器90具有可采用胶桶或胶盒。需要说明的是,所述第一管道901、第二管道902、第三管道903以及第四管道904均为回油管。
82.进一步的,请参阅图12,第一自动润滑组件62包括第一供油组件、第一支架621、固设在第一支架621上的第一轴622、可转动地设置在第一轴622上的第一润滑轮623,所述第一润滑轮623与第一齿轮1842传动组件25的传动齿抵接,第一轴622上设有第一添油通道624,第一供油组件包括第一供油泵65和第一润滑油分配器66,所述第一润滑油分配器66上的出油口处均设有第一单向压力阀,所述第一添油通道624通过接管与第一润滑油分配器66的出油口连通。
83.在实际应用中,第一齿轮传动组件25包括套在第一电机24主轴上的第一输出齿轮(图中不可见)和套在卡盘主体23上的第一回转齿轮(图中不可见),第一输出齿轮和第一回转齿轮啮合传动,第一润滑轮623与第一输出齿轮相抵接。工作人员打开第一供油泵65,润滑油即可通过第一添油通道624流入第一润滑轮623处,通过第一润滑轮623将润滑油添均匀转移至第一输出齿轮的传动齿上,第一回转齿轮也得到良好的润滑,进而降低第一输出齿轮与第一回转齿轮之间的传动阻力,保持第一输出齿轮与第一回转齿轮的运动顺畅性。
84.进一步的,所述第二自动润滑组件7包括竖直贯穿移动台22的第二轴、可转动地设置在第二轴上的第二润滑轮,所述第二润滑轮与y轴齿条42的传动齿抵接;所述第二轴上设有第二添油通道,所述第二添油通道通过接管与第一润滑油分配器66的出油口连通。同样
地,当工作人员打开第一供油泵65,润滑油即可通过第二添油通道流入第二润滑轮处,通过第二润滑轮将润滑油添均匀转移至y轴齿条42的传动齿上,y轴齿轮也得到良好的润滑,进而降低y轴齿轮与y轴齿条42之间的传动阻力,保持y轴齿轮与y轴齿条42的运动顺畅性。
85.通过这样设置,第一供油泵65能够同时对第一润滑轮623和第二润滑轮进行供油,第一供油泵65的进口管道与油箱连接,该第一供油泵65的出口管道与润滑油分配器的进油口连接,通过配置第一单向压力阀,确保出油压力稳定,不会发生倒流。
86.进一步的,所述第三自动润滑组件82包括第二供油组件、第二支架、可转动地设置在第三轴上的第三润滑轮,所述第三润滑轮与第二齿轮传动组件33的传动齿抵接;第二供油组件包括第二供油泵83和第二润滑油分配器84,所述第三轴上设有第三添油通道,所述第二润滑油分配器84上的出油口处均设有第二单向压力阀,所述第三添油通道通过接管与第二润滑油分配器84的出油口连通。
87.在实际应用中,第二齿轮传动组件33包括套在第二电机32主轴上的第二输出齿轮和套在卡盘主体23上的第二回转齿轮,第二输出齿轮和第二回转齿轮啮合传动,第三润滑轮与第二回转齿轮相抵接。工作人员打开第二供油泵83,润滑油即可通过第二添油通道流入第一润滑轮623处,通过第三润滑轮将润滑油添均匀转移至第二回转齿轮的传动齿上,第二输出齿轮也得到良好的润滑,进而降低第二输出齿轮与第二回转齿轮之间的传动阻力,保持第二输出齿轮与第二回转齿轮的运动顺畅性。
88.进一步的,请参阅图8,所述第四自动润滑组件91包括设置在横梁支架51上的第四轴911、可转动地设置在第四轴911上的第四润滑轮912,所述第四润滑轮912与x轴齿条56的传动齿抵接;所述第四轴911上设有第四添油通道913,所述第四添油通道913通过接管与第二润滑油分配器84的出油口连通。同样地,当工作人员打开第二供油泵83,润滑油即可通过第四添油通道913流入第四润滑轮912处,通过第四润滑轮912将润滑油添均匀转移至x轴齿条56的传动齿上,x轴齿轮也得到良好的润滑,进而降低x轴齿轮与x轴齿条56之间的传动阻力,保持x轴齿轮与x轴齿条56的运动顺畅性。
89.通过这样设置,第二供油泵83能够同时对第三润滑轮和第四润滑轮912进行供油,第二供油泵83的进口管道与油箱连接,该第二供油泵83的出口管道与润滑油分配器的进油口连接,通过配置第二单向压力阀,确保出油压力稳定,不会发生倒流。
90.优选的,所述第一润滑轮623、第二润滑轮、第三润滑轮、第四润滑轮912均由疏孔材料制成。疏孔材料具体可为毛毡或棉纶材料,毛毡或棉纶具有良好的液体保持性,能够较好地保持润滑油。
91.进一步的,所述装夹器31为多爪卡盘,所述多爪卡盘包括沿圆周方向布置且可开合的四个卡爪。
92.具体的,请参阅图1、图22
‑
图24,所述接料架c设置在固定卡盘3的一旁,该接料架c包括架体c6、上下运动机构c1、支撑架c2、接料板c3、摆动机构c4;所述上下运动机构c1设置在所述架体c6上;所述支撑架2滑动配合所述架体c6,所述支撑架c2可与所述架体c6发生沿上下方向的相对滑动,所述上下运动机构c1带动所述支撑架c2上下运动;所述接料板3设置在所述支撑架c2上,所述接料板c3铰接所述支撑架,所述接料板c3用于接住管料,所述摆动机构c4设置在所述支撑架c2上,所述摆动机构c4带动所述接料板c3摆动,调整接料板c3与水平面的夹角。
93.由上述可得,通过上下运动机构c1带动支撑架c2上下运动,该接料板c3用于管料,在上下运动机构1的带动下,接料板c3也随着支撑架c2上下运动,可实现接料板3接住从不同高度下掉落的工件,以减少工件掉落时的落差,达到保护工件的目的,由于接料架c与支撑架c2铰连接,使得接料板c3可相对支撑架c2绕铰接部相对摆动,其摆动的动力由摆动机构c4提供,从而通过接料板c3摆动倾斜后,在接料板c3上的工件可依靠重力的作用向下滑落。
94.在一些实施例中,该接料架c还包括放置架c5,所述接料板c3的摆动的轴线沿左右方向设置,所述放置架c5设置于所述接料板c3前侧,所述放置架c5用于对接所述接料板c3。该结构简单、设置方便,通过该结构的设置,在摆动机构c4带动接料板c3向向下倾斜后,接料板c3上的工件可滑落到放置架c5上。
95.优选的,放置架c5的前侧设置有限位柱c51,所述限位柱c51用于对管料进行限位。在放置架c5的前侧对工件的滑落方向进行限位,能够有效地避免从接料板c3上滑落到放置架c5上的工件滑落到地面。
96.在一些实施例中,所述接料架c固定连接所述架体c6。该接料架c与架体c6固定连接,从而实现一体化的设置,可提高整体架体c6的稳定性。
97.在一些实施例中,所述上下运动机构c1包括设置在所述架体c6上的电机c11、与所述架体c6相对转动连接的丝杆c13、通过螺纹配合所述丝杆c13的螺母c12,所述螺母c12固定连接所述支撑架c2,所述丝杆c13沿竖向设置,所述电机c11驱动连接所述丝杆c13。丝杆13与螺母12组成了一组运动副,通过电机c11带动丝杆c13旋转,螺母c12固定连接支撑架c2而限制了螺母c12绕丝杆c13轴线旋转的自由度,在电机c11带动丝杆c13旋转时,在丝杆c13与螺母c12的螺纹配合下,丝杆c13沿着上下方向运动,进一步地带动支撑架c2上下运动。
98.在一些实施例中,所述支撑架c2上设有若干条沿竖向延伸的下料滑轨c21,所述架体c6上固定地设有若干个所述下料滑块c61,所述下料滑块c61滑动配合所述下料滑轨c21。使用时,通过下料滑轨c21和下料滑块c61的滑动配合,实现对支撑架c2和架体c6的相对滑动,同时,通过下料滑轨c21和下料滑块c61的设置,对支撑架c2的上下运动进行导向,提高支撑架c2上下运动时的稳定性。
99.在一些实施例中,所述摆动机构c4包括设置在所述支撑架c2上的第一转轴c41、设置在所述接料板c3上的第二转轴c42,以及气缸c43,所述气缸c43通过第一转轴c41可相对转动地连接所述支撑架c2,所述气缸c43通过第二转轴c42可相对转动地连接所述接料板c3,所述第一转轴c41和所述第二转轴c42的轴线分别沿左右方向延伸。该结构简单、设置方便,使用时,在气缸c43的带动下,实现接料板c3的摆动,可选的,气缸c43的活动部连接第二转轴c42,气缸c43的固定部连接第一转轴c41。
100.在本发明的描述中,需要理解的是,术语“中心”、“纵向”、“横向”、“长度”、“宽度”、“厚度”、“上”、“下”、“前”、“后”、“左”、“右”、“竖直”、“水平”、“顶”、“底”、“内”、“外”、“顺时针”、“逆时针”等指示的方位或位置关系为基于附图所示的方位或位置关系,仅是为了便于描述本发明和简化描述,而不是指示或暗示所指的装置或元件必须具有特定的方位、以特定的方位构造和操作,因此不能理解为对本发明的限制。
101.在本发明的描述中,需要说明的是,除非另有明确的规定和限定,术语“安装”、“相连”、“连接”应做广义理解,例如,可以是固定连接,也可以是可拆卸连接,或一体地连接;可
以是机械连接,也可以是电连接或可以相互通讯;可以是直接连接,也可以通过中间媒介间接相连,可以是两个元件内部的连通或两个元件的相互作用关系。对于本领域的普通技术人员而言,可以根据具体情况理解上述术语在本发明中的具体含义。
102.可以理解的是,对本领域普通技术人员来说,可以根据本发明的技术方案及其发明构思加以等同替换或改变,而所有这些改变或替换都应属于本发明的保护范围。
再多了解一些
本文用于企业家、创业者技术爱好者查询,结果仅供参考。