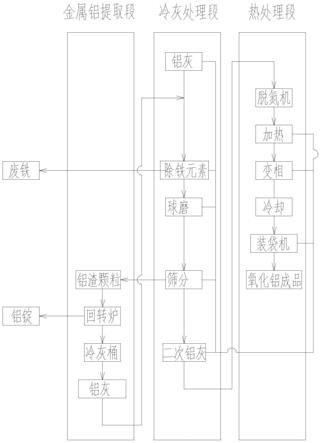
1.本发明涉及铝灰处理技术领域,更具体地说,涉及一种铝灰加工资源利用的方法。
背景技术:
2.铝灰是铝冶炼和铝加工产生的固体废弃物。一般铝灰中含有大量的金属铝,需进行回收处理,铝灰的成分复杂,因生产环节不同、生产厂家的原料及操作条件不同而略有变化,但通常含有金属铝,铝的氧化物、氮化物,氯盐以及一些其他成分。
3.目前,铝灰回收金属铝或氧化铝的工艺技术一直在不断的探索中。
4.比如专利申请号为cn202011108725.4公开了一种高效无害化处理铝灰的方法,但是,在此方案中,首先步骤1内需要加入水,开启搅拌,调浆,会有少部分的氨气产生,通过负压排气口排出收集处理,然后步骤2中需要再加入水,反应产生的氨气通过负压排气口排出收集处理,步骤3中还需要水洗,最后步骤4中经过洗涤,整个过程中用水量过大,水污染严重,实际生活中需要另外的水污染处置费,在一定程度上增加了投入成本,而且步骤1和步骤2均产生了氨气,但后续氨气没有循环使用于此反应内,而是作为一中需要处理的废气予以处理,在方案中发明人说明可以用稀硫酸吸收,制备硫酸铵另作他用,另外,还产生了较多的氯化盐副产物也需要进行处理。
5.比如专利申请号为cn201810062643.7公开了一种二次铝灰资源化利用方法,但是,此专利中需要复杂的化学反应,在具体的企业实施当中首先机会遇到项目土地性质定位的难题(化学反应的生成列入化工企业,所需土地为化工用地,一般很难取得土地使用权),生产流程较多较杂,工艺较复杂,流水线更长,通常不能形成完整的一条流水线,需要断开成两个以上流水线完成生产,而且会产生较多的副产物,还需要对副产物进行处理,成本很高。
技术实现要素:
6.针对现有技术中存在的问题,本发明的目的在于提供一种铝灰加工资源利用的方法,在处理时采用加入少量的水,将氮化铝转化成氨气并用水吸收转化为氨水,而氨水可以用于后续高温脱销步骤,实现了氨的循环利用;同时本方案脱氮的核心技术是铝灰通过旋转窑处理,相比于传统的处理方式,工艺流程更简单。
7.为解决上述问题,本发明采用如下的技术方案。
8.一种铝灰加工资源利用的方法,包括以下步骤:步骤一:冷灰处理段;s11:将待处理的铝灰破碎后投入处理线中,去除铝灰中的铁元素;s12:对s11处理后的铝灰进行球磨筛分,得到铝渣颗粒和二次铝灰,铝渣颗粒经过金属铝提取段处理,得到铝锭和铝灰,铝灰重新投入处理线中,具体投入磁选机中;步骤二:热处理段s21:将步骤一中的二次铝灰投入脱氮机中,加入一定量水混合搅拌,使铝灰中的
部分氮化铝转变成氨气收集;s22:将所得的部分脱氮的铝灰输送至旋转窑中,旋转窑有一定的斜度和转速,二次铝灰在重力的作用下从低温端向高温端移动,使得其先经过加热,蒸发游离水,再脱除结晶水,之后通过高温烧结变相,使得氧化铝晶相转变为α相,最后得到熟料经过冷却降温,装袋得到氧化铝成品。
9.进一步的,还包括步骤三:环保段;所述环保段包括烟气处理系统和除尘系统;所述烟气处理系统用于处理烟气中的氮氧化合物和氨气;所述除尘系统用于对铝灰中整个铝灰加工过程中的灰尘去除。
10.进一步的,所述烟气处理系统主要是脱硝处理和收集氨气,利用s21步骤中的氨气转变为氨水在热处理段过程中喷淋去除高温烟气内的氮氧化合物,使得s21步骤中的产生的氨气循环使用于s22步骤中,有效避免氨气处理的副产物产生,减少需要对副产物处理的麻烦。
11.进一步的,所述除尘系统包括旋风除尘和布袋除尘两种除尘方式,对整个生产过程中的灰尘进行处理,减少生产车间的灰尘量,保证工作人员的身体健康,同时减少灰尘对生产出的产品质量的影响。
12.进一步的,所述s12步骤中铝灰的粉碎筛分分别通过球磨机和筛分机完成。优选的,所述球磨机为刚玉球磨机,刚玉球磨机相比于传统的球磨机,不易产生铁的污染。
13.进一步的,所述s12步骤中的金属铝提取段包括以下步骤:第一步,先将铝渣颗粒趁热放入旋转窑中,加入打渣剂炒制回收金属铝,得到铝液和铝灰渣,铝液通过冷却通过叠锭机得到铝合金锭;第二步,将铝灰渣投入铝冷灰桶冷却,再次得到冷铝灰。
14.进一步的,所述旋转窑内温度保持在800
‑
1100℃,优选700
‑
900℃,加入打渣剂后加盖闷制20
‑
50min;所述冷灰桶冷却温度为40
‑
60℃,冷灰桶通过循环水喷淋,使得桶身与冷却水换热实现冷却降温。
15.进一步的,所述旋转窑内温度保持在800℃。
16.进一步的,加入打渣剂后加盖闷制30min进一步的,所述s22步骤中采用烘干方式蒸发铝灰滤渣中的游离水,烘干温度为100
‑
200℃,最好是120℃。
17.进一步的,所述s22步骤中采用加热方式脱除铝灰中的结晶水,加热温度为600
‑
800℃,最好是600℃。
18.进一步的,所述s22步骤中变相的温度为1200
‑
1300℃;所述s22步骤中通过水冷冷却降温至150
‑
200℃,最好是200℃。
19.相比于现有技术,本发明的优点在于:一、本方案的二次铝灰在脱氮机脱氮过程中,对氨气吸附并储存,在旋转窑处理的过程中调用储存的氨气高温喷淋,去除高温加热过程中产生的氮氧化合物,使得氨气可以在本方案中循环使用,相比于传统的将氨气收集或者用稀硫酸吸收转变为硫酸氨铵等另作他用,更加方便且节约资源。
20.二、本方案部分脱氮的铝灰通过旋转窑处理,先加热蒸发游离水,再脱除结晶水,之后通过高温烧结变相,冷却得到成品,相比于传统的处理方式,工艺流程简单,可以形成
一整条流水线,相比于申请号为cn202011108725.4的专利,水污染较小,氨气可以循环使用,不会产生氯化盐副产物,而且相比于申请号为cn201810062643.7的专利,流水线更短,工艺流程简单,也不会有氯化盐副产物产生,污染性大大降低。
21.三、本方案球磨过程中采用刚玉球磨机,相比于传统的球磨机,不易有铁的污染。
22.四、本方案投入成本较低,风险小,既适用于中小型厂家的投资生产,又适合大规模的生成,且生产后的产品价值高。
附图说明
23.图1为本发明的工艺流程图;图2为本发明增加环保段后的工艺流程图。
具体实施方式
24.实施例1:请参阅图1
‑
2,一种铝灰加工资源利用的方法,包括以下步骤:步骤一:冷灰处理段s11:将放置在料仓内待处理的铝灰通过提升机提升至磁选机中,去除铝灰中的铁元素,得到废铁。铁元素是铝合金熔炼配制中的有害杂质,须在熔炼前去除。提升至磁选机之前可以先通过破碎机进行初步破碎以便于废铁的获提取。破碎完成的碎铝料采用干式磁选,也可以通过破碎机自带磁选滚轴分离出废铁;s12:对s11处理后的铝灰先通过球磨机粉碎成颗粒,再通过提升机提升至筛分机筛分,得到铝渣颗粒和二次铝灰。铝渣颗粒趁热投入旋转窑中,然后加入打渣剂后加盖闷制30分钟,利用铝渣自燃原理产生的热能进行运转,旋转窑温度保持在800度左右,得到铝锭和铝灰渣。一般铝渣颗粒含液态金属铝约30%左右,通过旋转窑可将铝渣颗粒中50%以上液态铝进行分离、回收,经回收处理后铝渣颗粒中金属铝含量可降低至15%以下。铝锭可以冷却后通过叠锭机得到质量良好的铝合金锭。。铝灰渣投入铝渣斗内,通过叉车运输,从冷灰桶投料口倒入进行冷却处理,冷却方式为循环水喷淋间接冷却,通过水泵、喷淋水管将冷却水均匀布满冷却桶,热渣通过桶身与冷却水进行换热,可快速冷却至40~60℃,得到二次铝灰。二次铝灰重新放入料仓,进行提升磁选,再次经过自击研磨和钢球的研磨,研磨后输送到筛分机中,使二次铝灰中的铝和灰进一步分离,分离出的铝渣颗粒返回到旋转窑中继续炒制,经处理后的铝灰中金属铝含量可降低至2%(单质铝)以下。二次铝灰通过提升机放入中转料仓,等待进入热处理段。
25.步骤二:热处理段s21:将二次铝灰通过提升机投入脱氮机中,加入一定量水混合搅拌,使铝灰中的部分氮化铝转变成氨气,再将氨气吸附收集,可利用氨气吸附塔,再将氨气转变为氨水储存以备使用后续变相时的高温脱硝使用;s22:将所得的部分脱氮铝灰输送至旋转窑中,旋转窑有一定的斜度和转速,铝灰在重力的作用下从冷端向热端移动,先经过温度为120℃的烘干带加热,蒸发铝灰滤渣中的游离水;接着经过温度为700℃的预热带加热,脱除铝灰中的结晶水;再经过温度为1400℃的晶相转变带完成铝灰的煅烧变相,使得氧化铝晶相转化为α相;最后经过冷却带,通过二
次空气和窑头漏风冷却降温至200℃,装袋得到氧化铝成品。
26.旋转窑的燃料采用天然气,向窑内燃烧器中通入天然气和空气进行加热,窑体的旋转也强化了传热过程。旋转窑煅烧过程中,天然气燃烧会产生烟尘、so2、nxox;铝灰煅烧过程会产生no2;旋转窑旋转过程会产生粉尘。旋转窑废气直接从窑尾烟道排入烟气处理系统后通过p3排气筒排放。烟气处理系统内就可以利用到上述储存的氨水喷淋,去除高温烟气内的氮氧化合物。窑头冷却进料和出料过程会导致部分粉尘逸散,经集气罩收集后送入除尘系统处理后排放,未收集的粉尘大部分沉降在地面上,少量无组织排放。
27.试验例1:100kg待处理铝灰原料通过破碎机破碎后投入磁选机中,磁选10min时间,分离出废铁1.24kg,经过废铁处理后的铝灰通过球磨机球磨50min时间碾压成颗粒,再通过120目粒径的筛分机筛分,得到45.7kg铝渣颗粒和二次铝灰。铝渣颗粒趁热投入回转炉中,然后加入打渣剂后闷制30分钟,回转炉温度保持在800
‑
900度左右,得到23.3kg铝锭和21kg铝灰渣。铝灰渣通过冷灰桶冷却至40~60℃,得到20kg铝灰,重新投入处理线。
28.二次铝灰投入脱氮机中,加入3kg水混合搅拌5min时间,对产生的氨气吸附收集备用。搅拌结束后输送至旋转窑中,经过120℃的烘干带、700℃的预热带、1400℃的晶相转变带及冷却带降温至200℃,得到65.2kg氧化铝混合物,收回率65.2%。
29.试验例2:100kg待处理铝灰原料通过破碎机破碎后投入磁选机中,磁选10min,分离出废铁0.7kg,经过废铁处理后的铝灰通过球磨机球磨50min碾磨成颗粒,再通过120粒径的筛分机筛分,得到23.6kg铝渣颗粒和二次铝灰。铝渣颗粒趁热投入回转炉中,然后加入打渣剂后闷制30分钟,回转炉温度保持在800
‑
950度左右,得到14.2kg铝锭和铝灰渣。铝灰渣通过冷灰桶冷却至40~60℃,得到5.9kg铝灰,重新投入磁选机中。
30.二次铝灰投入脱氮机中,加入3kg水混合搅拌5min时间,对产生的氨气吸附收集备用。搅拌结束后输送至旋转窑中,经过120℃的烘干、700℃的预热、1400℃的晶相转变及冷却带降温至200℃,得到83.4kg氧化铝混合物,收回率83.4%。
31.试验例3:100kg待处理铝灰原料通过破碎机破碎后投入磁选机中,磁选10min时间,分离出废铁8.3kg,经过废铁处理后的铝灰通过球磨机球磨50min时间碾磨成颗粒,再通过60
‑
120目粒径的筛分机筛分,得到16.7kg铝渣颗粒和二次铝灰。铝渣颗粒趁热投入回转炉中,然后加入打渣剂后闷制30分钟,回转炉温度保持在800
‑
950度左右,得到11.2kg铝锭和铝灰渣。铝灰渣通过冷灰桶冷却至40~60℃,得到5.1kg铝灰,重新投入磁选机中。
32.二次铝灰投入脱氮机中,加入3 kg水混合搅拌5min时间,对产生的氨气吸附收集备用。搅拌结束后输送至旋转窑中,经过120℃的烘干、700℃的预热、1400℃的晶相转变带及冷却带降温至200℃,得到78.2kg氧化铝,收回率78.2%。
再多了解一些
本文用于企业家、创业者技术爱好者查询,结果仅供参考。