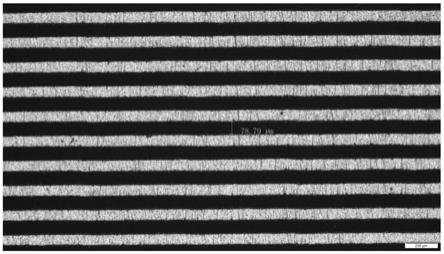
1.本发明涉及磁性功能材料领域,特别是涉及用于抑制铜面化学镀渗镀的预浸液及其制备方法和应用。
背景技术:
2.在印刷电路板(printed circuit board,pcb)的生产工艺中,化学镀镍金(或称化镍)和镍钯金是常见的对电路板上金属布线两种最终表面处理方式。化学镍金是通过化学反应在铜的表面化学镀上一层镍,然后再通过置换反应在镍的表面镀上一层金。此类处理方法使电路板后续具有可焊接、可接触导通、可打线以及可散热等多种功能。
3.由于铜表面无法自发地驱动镍离子的还原而实现非电解镍沉积,因此在化学镀镍之前须对电路板上的金属铜面进行活化。产业上通常使用钯活化液与电路板接触,利用铜面微量溶解后释放的电子使钯离子还原成金属钯,在铜表面形成薄的钯层作为化镍的催化触媒,进而产生镍的非电解沉积。但这种化学镀镍的方法通常会使钯金属不仅在铜面上沉积而且还会在电路板上的其他非施镀面上沉积(例如防焊油墨、干膜或裸露的线路板基材),从而导致后续的镍不仅在铜线上,而且还在铜线附近的板面上沉积,这种现象被称为“渗镀”。轻微时,在电路板面上产生点状沾金,严重时将导致铜面周围长胖,更严重时将导致线路间或接触垫间的架桥短路,特别是在线宽和线距为约75μm或更小的高密度电路中更容易出现短路现象。
4.为了避免出现上述现象,产业上一般在钯活化液处理电路板和化镍步骤之间加入后浸的工序,以清除吸附在非施镀面的多余钯离子。目前已知的改善方法有:(1)往活化槽中添加抑制剂减少钯在非施镀位置的吸附;(2)通过优化后浸配方,增强清洗效果。
5.目前尚未见通过改善预浸液配方来避免化镍金或镍钯金渗渡的相关报道,且传统的预浸液只是用来维持活化液的酸度以及使铜面在无氧化物状态下进入活化缸,常用的预浸液一般是硫酸或盐酸的低浓度水溶液,几乎没有避免渗渡的效果。
6.然而铜面在经过微蚀后,铜面被咬蚀释放出一价和二价铜离子,一价铜离子可能会发生歧化反应生成二价铜离子和铜单质,如果铜面被微蚀后经过预浸未能将歧化反应生产的铜单质去除,继续吸附在边缘位置或者基材位置,经活化槽后,钯会因为与单质铜发生置换反应进而吸附在铜面边缘或基材位置导致细线路板容易渗镀。为了加强化镍金/镍钯金防渗渡的效果,产业上迫切需要寻找一种合适的、能用于改善铜面化学镀的预浸液。
技术实现要素:
7.基于此,本发明提供一种可有效抑制铜面化学镀渗镀的预浸液。
8.本发明的技术方案如下:
9.一种用于抑制铜面化学镀渗镀的预浸液,每升所述预浸液包括水,5g~100g的酸性试剂,及0.05g~5g的预浸添加剂;
10.所述酸性试剂为硫酸和/或盐酸;
11.所述预浸添加剂为含氮芳杂环类化合物、脂肪族含氮羧酸类化合物、含硫脂肪酸类化合物、有机胺类化合物中的至少一种。
12.在其中一个实施例中,每升所述预浸液包括水,5g~60g的酸性试剂,及0.05g~3g的预浸添加剂。
13.在其中一个实施例中,所述预浸添加剂为含氮芳杂环类化合物和脂肪族含氮羧酸类化合物的混合物。
14.在其中一个实施例中,所述预浸添加剂为有机胺类化合物。
15.在其中一个实施例中,所述预浸添加剂为含氮芳杂环类化合物和有机胺类化合物的混合物。
16.在其中一个实施例中,所述预浸添加剂为脂肪族含氮羧酸类化合物和有机胺类化合物的混合物。
17.在其中一个实施例中,所述含氮芳杂环类化合物选自吡啶、羟基丙烷磺酸吡啶嗡盐、咪唑、1
‑
(2
‑
羟乙基)咪唑、1
‑
乙基
‑3‑
甲基咪唑甲磺酸盐、喹啉、嘧啶和三氮唑中的至少一种;和/或
18.所述脂肪族含氮羧酸类化合物选自n
‑
羟乙基乙二胺三乙酸三钠、乙二胺四乙酸三钠盐和氨基酸类化合物中的至少一种;和/或
19.所述含硫脂肪酸类化合物选自巯基乙酸、二甲基二硫代氨基甲酸钠、硫代乙醇酸、硫代水杨酸、2
‑
巯基乙醇、甲硫氨酸、3
‑
巯基丙酸和2
‑
巯基苯并噻唑中的至少一种;和/或
20.所述有机胺类化合物选自脂肪胺类、醇胺类和芳香胺类化合物中的至少一种。
21.在其中一个实施例中,所述氨基酸类化合物选自甘氨酸、丙氨酸、谷氨酸、l
‑
半胱氨酸和乙酰半胱氨酸中的至少一种;和/或
22.所述脂肪胺类化合物选自聚乙烯亚胺、二亚乙基三胺、1,4
‑
丁二胺、二乙胺和三乙胺中的至少一种;和/或
23.所述醇胺类化合物选自三乙醇胺和n
‑
n二甲基乙醇胺中的至少一种;和/或
24.所述芳香胺类化合物选自苯胺、邻甲苯胺和n
‑
甲基苯胺中的至少一种。
25.在其中一个实施例中,所述预浸添加剂为1
‑
(2
‑
羟乙基)咪唑和乙酰半胱氨酸的混合物。
26.在其中一个实施例中,所述预浸添加剂为聚乙烯亚胺。
27.在其中一个实施例中,所述预浸添加剂为1
‑
乙基
‑3‑
甲基咪唑甲磺酸盐和l
‑
半胱氨酸的混合物。
28.在其中一个实施例中,所述预浸添加剂为羟基丙烷磺酸吡啶嗡盐和乙酰半胱氨酸的混合物。
29.在其中一个实施例中,所述预浸添加剂为乙二胺四乙酸三钠盐和聚乙烯亚胺的混合物。
30.在其中一个实施例中,所述预浸添加剂为羟基丙烷磺酸吡啶嗡盐和二亚乙基三胺的混合物。
31.在其中一个实施例中,所述预浸添加剂为n
‑
羟乙基乙二胺三乙酸三钠和聚乙烯亚胺的混合物。
32.在其中一个实施例中,所述预浸添加剂为1
‑
(2
‑
羟乙基)咪唑和1,4
‑
丁二胺的混合
物。
33.在其中一个实施例中,每升所述预浸液包括水,5g~60g的硫酸,0.5g~1g的1
‑
(2
‑
羟乙基)的咪唑,及0.5g~1g的乙酰半胱氨酸。
34.在其中一个实施例中,每升所述预浸液包括水,5g~60g的硫酸,及0.5g~1g的n
‑
羟乙基乙二胺三乙酸三钠。
35.在其中一个实施例中,每升所述预浸液包括水,5g~60g的硫酸,及0.05g~0.5g的聚乙烯亚胺。
36.在其中一个实施例中,每升所述预浸液包括水,20g~50g的盐酸,及0.5g~1g的甘氨酸。
37.在其中一个实施例中,每升所述预浸液包括水,20g~50g的盐酸,及1g~5g的1,4
‑
丁二胺。
38.在其中一个实施例中,每升所述预浸液包括水,10g~20g的硫酸,0.5g~1g的1
‑
乙基
‑3‑
甲基咪唑甲磺酸盐,及0.05g~0.5g的l
‑
半胱氨酸。
39.在其中一个实施例中,每升所述预浸液包括水,50g~100g的硫酸,0.5g~1g的羟基丙烷磺酸吡啶嗡盐,及0.5g~1g的乙酰半胱氨酸。
40.在其中一个实施例中,每升所述预浸液包括水,5g~10g的盐酸,及1g~2g的3
‑
巯基丙酸。
41.在其中一个实施例中,每升所述预浸液包括水,5g~20g的硫酸,0.5g~1g的乙二胺四乙酸三钠盐,及0.5g~1g的聚乙烯亚胺。
42.在其中一个实施例中,每升所述预浸液包括水,10g~20g的盐酸,0.5g~1g的羟基丙烷磺酸吡啶嗡盐,及1g~2g的二亚乙基三胺。
43.在其中一个实施例中,每升所述预浸液包括水,10g~20g的盐酸,1g~2g的n
‑
羟乙基乙二胺三乙酸三钠,及0.5g~1g的聚乙烯亚胺。
44.在其中一个实施例中,每升所述预浸液包括水,10g~20g的硫酸,1g~2g的1
‑
(2
‑
羟乙基)咪唑,及0.5g~1g的1,4
‑
丁二胺。
45.本发明还提供如上所述的用于抑制铜面化学镀渗镀的预浸液的制备方法,包括如下步骤:
46.将所述的水、所述的酸性试剂与所述的预浸添加剂混合。
47.本发明还提供如上所述的用于抑制铜面化学镀渗镀的预浸液在化学镀镍中的应用。
48.本发明还提供一种在铜面化学镀镍的方法,包括如下步骤:
49.将表面含铜的基材浸泡在如上所述的用于抑制铜面化学镀渗镀的预浸液中进行预浸处理;
50.对预浸处理后的基材进行活化和化学镀镍处理。
51.在其中一个实施例中,所述表面含铜的基材为pcb线路板;所述pcb线路板上的铜线的线宽和相邻铜线的线距均为60μm~120μm。
52.在其中一个实施例中,预浸处理的时间为1min~5min;和/或
53.在化学镀镍的步骤之后,还包括在镍表面进行化学镀金的步骤。
54.本发明具有以下有益效果:
55.本发明提供的预浸液能够屏蔽掉施镀面边缘的一价铜离子,从而防止一价铜离子发生歧化反应在施镀面边缘及基材位置生长出铜单质,进而减少活化液中钯离子在施镀面边缘及基材位置与铜的置换反应导致的渗镀问题,或因镍槽活性太强导致的渗镀问题,最终起到降低因渗镀问题导致线路板良品率下降的问题。
56.另外,本发明的预浸液成本较低,制备方法和应用方法都非常简单,可满足行业技术要求,具有广阔的应用前景。
附图说明
57.图1为处理前的铜面线宽线距图,线宽约80.28μm;
58.图2为未使用预浸添加剂(对比例1)的化学镀镍金后的线宽线距图,线宽约47.57μm;
59.图3为使用预浸添加剂后(实施例3)的化学镀镍金后的线宽线距图,线宽约78.79μm。
具体实施方式
60.以下结合具体实施例和附图对本发明作进一步详细的说明。本发明可以以许多不同的形式来实现,并不限于本文所描述的实施方式。相反地,提供这些实施方式的目的是使对本发明公开内容理解更加透彻全面。
61.除非另有定义,本文所使用的所有的技术和科学术语与属于本发明的技术领域的技术人员通常理解的含义相同。本文中在本发明的说明书中所使用的术语只是为了描述具体的实施例的目的,不是旨在于限制本发明。
62.本文所使用的术语“和/或”、“或/和”、“及/或”的可选范围包括两个或两个以上相关所列项目中任一个项目,也包括相关所列项目的任意的和所有的组合,所述任意的和所有的组合包括任意的两个相关所列项目、任意的更多个相关所列项目、或者全部相关所列项目的组合。
63.在使用本文中描述的“包括”、“具有”、和“包含”的情况下,意图在于覆盖不排他的包含,除非使用了明确的限定用语,例如“仅”、“由
……
组成”等,否则还可以添加另一部件。
64.除非相反地提及,否则单数形式的术语可以包括复数形式,并不能理解为其数量为一个。
65.在本发明中,“至少一种”指所列项目的任一种、任两种或任两种以上。
66.以下具体实施方式所用的原料、试剂材料等,如无特殊说明,均为市售购买产品。
67.本发明的技术方案如下:
68.一种用于抑制铜面化学镀渗镀的预浸液,每升所述预浸液包括水,5g~100g的酸性试剂,及0.05g~5g的预浸添加剂;
69.所述酸性试剂为硫酸和/或盐酸;
70.所述预浸添加剂为含氮芳杂环类化合物、脂肪族含氮羧酸类化合物、脂肪族含硫脂肪酸类化合物、有机胺类化合物中的至少一种。
71.通过调节酸和预浸添加剂的比例,可以进一步屏蔽施镀面边缘的一价铜离子。在其中一个较为优选的实施例中,每升所述预浸液包括水,5g~60g的酸性试剂,及0.05g~3g
的预浸添加剂。进一步地,所述酸性试剂为硫酸或盐酸。
72.在其中一个实施例中,所述预浸添加剂为含氮芳杂环类化合物和脂肪族含氮羧酸类化合物的混合物。这样的预浸添加剂能够更好地屏蔽铜面微蚀产生的在铜面边缘的一价铜离子,防止一价铜离子发生歧化反应在施镀面边缘及基材位置生长出铜单质,进而减少渗镀现象。
73.在其中一个实施例中,所述预浸添加剂为有机胺类化合物。这样的预浸添加剂能够更好地屏蔽铜面微蚀产生的在铜面边缘的一价铜离子,防止一价铜离子发生歧化反应在施镀面边缘及基材位置生长出铜单质,进而减少渗镀现象。
74.在其中一个实施例中,所述预浸添加剂为含氮芳杂环类化合物和有机胺类化合物的混合物。这样的预浸添加剂能够更好地屏蔽铜面微蚀产生的在铜面边缘的一价铜离子,防止一价铜离子发生歧化反应在施镀面边缘及基材位置生长出铜单质,进而减少渗镀现象。
75.在其中一个实施例中,所述预浸添加剂为脂肪族含氮羧酸类化合物和有机胺类化合物的混合物。这样的预浸添加剂能够更好地屏蔽铜面微蚀产生的在铜面边缘的一价铜离子,防止一价铜离子发生歧化反应在施镀面边缘及基材位置生长出铜单质,进而减少渗镀现象。
76.在其中一个实施例中,所述含氮芳杂环类化合物选自吡啶、羟基丙烷磺酸吡啶嗡盐、咪唑、1
‑
(2
‑
羟乙基)咪唑、1
‑
乙基
‑3‑
甲基咪唑甲磺酸盐、喹啉、嘧啶和三氮唑中的至少一种。
77.在其中一个实施例中,所述脂肪族含氮羧酸类化合物选自n
‑
羟乙基乙二胺三乙酸三钠、乙二胺四乙酸三钠盐和氨基酸类化合物中的至少一种。
78.在其中一个实施例中,所述氨基酸类化合物选自甘氨酸、丙氨酸、谷氨酸、l
‑
半胱氨酸和乙酰半胱氨酸中的至少一种。
79.在其中一个实施例中,所述含硫脂肪酸类化合物选自巯基乙酸、二甲基二硫代氨基甲酸钠、硫代乙醇酸、硫代水杨酸、2
‑
巯基乙醇、甲硫氨酸、3
‑
巯基丙酸和2
‑
巯基苯并噻唑中的至少一种。
80.在其中一个实施例中,所述有机胺类化合物选自脂肪胺类、醇胺类和芳香胺类化合物中的至少一种。
81.在其中一个实施例中,所述脂肪胺类化合物选自聚乙烯亚胺、二亚乙基三胺、1,4
‑
丁二胺、二乙胺和三乙胺中的至少一种。
82.在其中一个实施例中,所述醇胺类化合物选自三乙醇胺和n
‑
n二甲基乙醇胺中的至少一种。
83.在其中一个实施例中,所述芳香胺类化合物选自苯胺、邻甲苯胺和n
‑
甲基苯胺中的至少一种。
84.在其中一个实施例中,所述预浸添加剂为1
‑
(2
‑
羟乙基)咪唑和乙酰半胱氨酸的混合物。
85.在其中一个实施例中,所述预浸添加剂为聚乙烯亚胺。
86.在其中一个实施例中,所述预浸添加剂为1
‑
乙基
‑3‑
甲基咪唑甲磺酸盐和l
‑
半胱氨酸的混合物。
87.在其中一个实施例中,所述预浸添加剂为羟基丙烷磺酸吡啶嗡盐和乙酰半胱氨酸的混合物。
88.在其中一个实施例中,所述预浸添加剂为乙二胺四乙酸三钠盐和聚乙烯亚胺的混合物。
89.在其中一个实施例中,所述预浸添加剂为羟基丙烷磺酸吡啶嗡盐和二亚乙基三胺的混合物。
90.在其中一个实施例中,所述预浸添加剂为n
‑
羟乙基乙二胺三乙酸三钠和聚乙烯亚胺的混合物。
91.在其中一个实施例中,所述预浸添加剂为1
‑
(2
‑
羟乙基)咪唑和1,4
‑
丁二胺的混合物。
92.在其中一个实施例中,所述预浸添加剂为1
‑
(2
‑
羟乙基)咪唑和1,4
‑
丁二胺的混合物。
93.在其中一个实施例中,每升所述预浸液包括水,5g~60g的硫酸,0.5g~1g的1
‑
(2
‑
羟乙基)的咪唑,及0.5g~1g的乙酰半胱氨酸。
94.在其中一个实施例中,每升所述预浸液包括水,5g~60g的硫酸,及0.5g~1g的n
‑
羟乙基乙二胺三乙酸三钠。
95.在其中一个实施例中,每升所述预浸液包括水,5g~60g的硫酸,及0.05g~0.5g的聚乙烯亚胺。
96.在其中一个实施例中,每升所述预浸液包括水,20g~50g的盐酸,及0.5g~1g的甘氨酸。
97.在其中一个实施例中,每升所述预浸液包括水,20g~50g的盐酸,及1g~5g的1,4
‑
丁二胺。
98.在其中一个实施例中,每升所述预浸液包括水,10g~20g的硫酸,0.5g~1g的1
‑
乙基
‑3‑
甲基咪唑甲磺酸盐,及0.05g~0.5g的l
‑
半胱氨酸。
99.在其中一个实施例中,每升所述预浸液包括水,50g~100g的硫酸,0.5g~1g的羟基丙烷磺酸吡啶嗡盐,及0.5g~1g的乙酰半胱氨酸。
100.在其中一个实施例中,每升所述预浸液包括水,5g~10g的盐酸,及1g~2g的3
‑
巯基丙酸。
101.在其中一个实施例中,每升所述预浸液包括水,5g~20g的硫酸,0.5g~1g的乙二胺四乙酸三钠盐,及0.5g~1g的聚乙烯亚胺。
102.在其中一个实施例中,每升所述预浸液包括水,10g~20g的盐酸,0.5g~1g的羟基丙烷磺酸吡啶嗡盐,及1g~2g的二亚乙基三胺。
103.在其中一个实施例中,每升所述预浸液包括水,10g~20g的盐酸,1g~2g的n
‑
羟乙基乙二胺三乙酸三钠,及0.5g~1g的聚乙烯亚胺。
104.在其中一个实施例中,每升所述预浸液包括水,10g~20g的硫酸,1g~2g的1
‑
(2
‑
羟乙基)咪唑,及0.5g~1g的1,4
‑
丁二胺。
105.本发明还提供如上所述的用于抑制铜面化学镀渗镀的预浸液的制备方法,包括如下步骤:
106.将所述的水、所述的酸性试剂与所述的预浸添加剂混合。
107.本发明还提供如上所述的用于抑制铜面化学镀渗镀的预浸液在化学镀镍中的应用。
108.在其中一个较为优选的实施例中,本发明所述的用于抑制铜面化学镀渗镀的预浸液的配制方法为:
109.先加目标体积1/2的水(例如纯化水),向其中添加目标浓度量的浓硫酸或浓盐酸,得到酸溶液,继续往酸溶液中添加目标浓度量的预浸添加剂,最后加水至目标体积,即得到目标预浸液。
110.本发明还提供一种在铜面化学镀镍的方法,包括如下步骤:
111.将表面含铜的基材浸泡在如上所述的用于抑制铜面化学镀渗镀的预浸液中进行预浸处理;
112.对预浸处理后的基材进行活化和化学镀镍处理。
113.在其中一个实施例中,预浸处理的时间为1min~5min。
114.在其中一个实施例中,在化学镀镍的步骤之后,还包括在镍表面进行化学镀金的步骤。
115.在其中一个实施例中,所述表面含铜的基材为pcb线路板。
116.在其中一个实施例中,所述pcb线路板上的铜线的线宽和相邻铜线的线距均为60μm~120μm。
117.在本领域中,经微蚀的含铜线路基板(或pcb线路板)上进行化镍金的一般步骤如下:
118.铜线路基板
→
活化
→
清洗
→
化学镀镍
→
化学镀金
119.上述每两个步骤之间都可以加入水洗的步骤。
120.本发明创造性地在铜线路基板活化之前,对其进行预浸处理,同时,为了避免清洗试剂影响试验效果的判断,活化之后采用水(如纯化水)进行清洗,本发明试验的步骤如下:
121.铜线路基板
→
预浸
→
活化
→
水洗
→
化学镀镍
→
化学镀金
122.预浸步骤:将配制好的预浸液常温放置于活化槽之前,使用时将其加入到预浸槽中,铜线路基板在预浸槽中的浸渍时间约1min~5min。
123.活化步骤:活化液使用行业内常用的钯离子活化液,钯活化时间大约1分钟,活化步骤的温度为室温。
124.水洗步骤:在室温条件下,使用纯化水对非施镀区的钯进行清除。
125.化学镀镍步骤:镍浴可以使用行业内常用的化学镍镀液,此处所用的镀浴是5183系列镍浴(市售可得,广东东硕科技有限公司提供),操作温度80℃,ph值为4.3,时间为20分钟。
126.化学镀金步骤:金浴同样可以使用业内常用的化学金镀液,此处所用的镀浴是5186系列金浴(市售可得,广东东硕科技有限公司提供),操作温度82℃,ph值为4.4,时间为6分钟。
127.以下结合具体实施例和对比例进行进一步说明。
128.实施例1
129.本实施例提供一种用于抑制铜面化学镀渗镀的预浸液及其制备方法。
130.1、本实施例中的预浸液总体积为1l,其组成包括水、98%(质量占比)浓硫酸50g,
1
‑
(2
‑
羟乙基)咪唑0.5g和乙酰半胱氨酸0.5g。
131.2、本实施例中预浸液的制备方法如下:
132.在反应容器中加入0.5l纯化水,向纯化水中添加50g的98%浓硫酸,然后往酸溶液中添加0.5g的1
‑
(2
‑
羟乙基)咪唑和0.5g的乙酰半胱氨酸,最后加纯化水至1l。
133.实施例2至实施例12和对比例1至对比例5的预浸液配方见表1,预浸液体积均为1l,均含有纯化水(原料1),制备方法均与实施例1相同,区别仅在于将对应原料种类替换为表1所示原料。将各实施例和对比例制得的预浸液备用于活化之前的预浸槽内。
134.表1
135.[0136][0137]
应用测试部分:
[0138]
准备经过常规微蚀处理的18块含铜线路的fr
‑
4环氧树脂/玻璃纤维硬板,尺寸均为10cm
×
10cm,并且基板上面的线宽和线距均为80μm~90μm。上述基板均按照前述对含铜线路板化镍金的步骤,通过预浸、活化、清洗、化学镀镍以及化学镀金的过程依次在基板上沉积金属镍和金,以此作为应用实施例1~应用实施例12和应用对比例1~应用对比例6,其中预浸步骤中分别使用上述实施例1~实施例12和对比例1~对比例6制备得到的预浸液进行预浸5min,。
[0139]
按照本发明的方法对微蚀的含铜线路板进行预浸,然后再进行活化、水洗、化学镀镍以及化学镀金处理,对处理所得的基板在金相显微镜下观察铜线路的镍金渗镀情况。
[0140]
采用金相显微镜观察经过化镍金的所有基板的铜线路的镍金渗镀情况。在本试验中,使用化镍金后线距与原始线距的比值表示铜线路的渗镀情况,数值越大,表示线距变化越小,渗镀情况越轻微,反之则说明渗镀情况越严重。渗镀试验结果见表2。
[0141]
表2
[0142][0143][0144]
由表2可知,使用本发明实施例1至实施例12制得的预浸液对基板进行预浸处理,并经化学镀镍金后,线距是在原始线距的70%以上,采用实施例3的预浸液进行预浸处理,最终的线距甚至能达到原始线距的98%。而采用对比例1至对比例6的、不在本发明范围内
的预浸液对基板进行预浸处理,并化学镀镍金后,线距只有原始线距的59.3%~65%。可见,按照本发明所述的预浸液能够有效地预防非镀区的多余钯的吸附,并且能够有效地防止铜线、铜面之间架桥发生“渗镀”现象。
[0145]
图1为处理前的铜面线宽线距图,线宽约80.28μm。
[0146]
图2为采用对比例1的预浸液(仅为硫酸溶液)对基板进行预浸处理后,再经化学镀镍金后的线宽线距图,线宽约47.57μm,占原始线距的59.3%。
[0147]
图3为采用实施例3的预浸液(含有硫酸和聚乙烯亚胺预浸添加剂)对基板进行预浸处理后,再经化学镀镍金后的线宽线距图,线宽约78.79μm,占原始线距的98.1%。
[0148]
以上所述实施例的各技术特征可以进行任意的组合,为使描述简洁,未对上述实施例中的各个技术特征所有可能的组合都进行描述,然而,只要这些技术特征的组合不存在矛盾,都应当认为是本说明书记载的范围。
[0149]
以上所述实施例仅表达了本发明的几种实施方式,便于具体和详细地理解本发明的技术方案,但并不能因此而理解为对发明专利保护范围的限制。应当指出的是,对于本领域的普通技术人员来说,在不脱离本发明构思的前提下,还可以做出若干变形和改进,这些都属于本发明的保护范围。应当理解,本领域的普通技术人员在本发明提供的技术方案的基础上,通过合乎逻辑的分析、推理或者有限的试验得到的技术方案,均在本发明所附权利要求的保护范围内。因此,本发明专利的保护范围应以所附权利要求的内容为准,说明书及附图可以用于解释权利要求的内容。
再多了解一些
本文用于企业家、创业者技术爱好者查询,结果仅供参考。