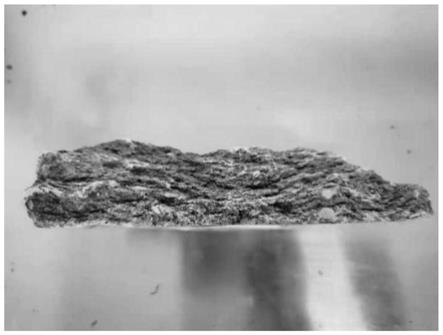
1.本发明涉及人造岩心技术领域,尤其涉及一种仿泥页岩岩心材料及其制备方法和应用。
背景技术:
2.泥页岩是泥岩与页岩之间的过渡岩石类型,有着页理发育不完善,比表面积大,结构复杂,脆性大,水化膨胀量大等特点,在当今鼓励页岩气开采的大环境下,泥页岩作为重要的生油岩石和盖层岩石有着与生俱来的研究价值,所以泥页岩层一直以来是岩土工程技术领域和油气钻探工程技术领域研究的重点。在页岩气开采钻井过程中经常因贯穿泥页岩层而发生底层坍塌和井壁失稳情况,为此需要对泥页岩进行大量的物理性能研究。但是目前,钻井勘探现场取芯费用高且困难,难以保证取出的岩心可以准确表征岩层的各项物理性能。而制作形成初期的泥页岩更困难,因为人造岩心技术虽日趋成熟但是往往造价昂贵,工艺复杂,成品质量可控性较差。并且如今的人造岩心多以水泥和石英砂混合浇筑、压实或烧结而成,或者在现场直接使用岩屑压制而成,以上两种造心方式对于泥页岩的层理结构和易水化膨胀性表达不是非常明确,因此不能相对准确地反应泥页岩的复杂结构更不能更加准确模拟形成初期泥页岩的各项物理性能。
技术实现要素:
3.本发明的目的在于克服现有技术中的缺陷,提供一种仿泥页岩岩心材料及其制备方法和应用。
4.为了实现上述发明目的,本发明提供以下技术方案:
5.本发明提供了一种仿泥页岩岩心材料,由包含下列质量份的组分制备得到:
6.水泥3~4份、二氧化硅0.1~0.3份、粉煤灰0.4~0.5份、氢氧化钙1~1.5份、黏土75~85份、水16~18份。
7.作为优选,所述二氧化硅的粒径为10~100nm,所述黏土的粒径小于等于5mm。
8.本发明还提供了所述材料的制备方法,包含下列步骤:
9.(1)将水泥、二氧化硅、粉煤灰和氢氧化钙混合,得到复合添加剂;
10.(2)将黏土和第一部分水混合,得到泥料;
11.(3)将复合添加剂和泥料分别均分后进行混合,得到中间材料;
12.(4)将中间材料和剩余组分进行混合得到混合粒料;
13.(5)将混合粒料顺次进行击实和养护,即得所述仿泥页岩岩心材料。
14.作为优选,所述步骤(1)中混合的方式为搅拌,所述搅拌的转速为100~110rpm,所述搅拌的时间为3~5min。
15.作为优选,所述步骤(2)中第一部分水的质量占全部水质量的82~87%;
16.所述混合的方式为搅拌,所述搅拌的转速为190~200rpm,所述搅拌的时间为3.5~5min。
17.作为优选,所述步骤(3)中复合添加剂的均分份数为8~10份,所述泥料的均分份数为3~5份;
18.所述步骤(3)中混合的放置方式为按照单份复合添加剂、单份泥料的方式进行交替放置,所述放置为放置完最后一份泥料后再次放置一份复合添加剂,放置完成后进行混合;
19.所述步骤(3)中混合的方式为搅拌,所述搅拌的速率为100~110rpm,所述搅拌的时间为3~4min。
20.作为优选,将中间材料按照复合添加剂的剩余份数进行均分,
21.所述步骤(4)中混合的放置方式为按照单份复合添加剂、单份中间材料的方式进行交替放置,复合添加剂和中间材料全部放置完成后加入剩余的水进行混合;
22.所述步骤(4)中混合的方式为搅拌,所述搅拌的转速为190~200rpm,所述搅拌的时间为3~4min。
23.作为优选,所述步骤(5)中击实的击锤质量为4~5kg,所述击实的锤落距为40~50cm,所述击实的锤落次数为90~100次,所述击实的锤迹相互重叠面积小于等于50%。
24.作为优选,所述步骤(5)中养护为顺次进行的养生和干燥;
25.所述养生的时间为1~3天,所述养生的温度为20~27℃,所述养生的湿度为85~~95%;
26.所述干燥的时间为15~20天,所述干燥的温度为21~31℃,所述干燥的湿度为40~50%。
27.本发明还提供了所述材料在填埋中的应用。
28.本发明提供了一种仿泥页岩岩心材料,由水泥、二氧化硅、粉煤灰、氢氧化钙、黏土和水制备得到,具有节理性和脆硬性的特征,适合用于模拟泥页岩形成初期的各项物理性质,为泥页岩地质层的研究提供各项性质相似且价格低廉的试样。本发明还提供了仿泥页岩岩心材料的制备方法,将水泥、二氧化硅、粉煤灰和氢氧化钙混合,得到复合添加剂;将黏土和第一部分水混合,得到泥料;复合添加剂和泥料分步混合击实养护后,即可得到仿泥页岩岩心材料。本发明提供的制备方法简单,成品质量易于控制。本发明还提供了所述材料的应用,因为仿泥页岩岩心材料孔隙致密,层次清晰,裂隙细小分布均匀,具有出色的抗渗透能力和过滤阻隔气体能力,为类似垃圾填埋场等场所提供封层和盖层材料,降低废弃物处理的成本。
附图说明
29.图1为实施例1中复合添加剂和泥料交替放置分层示意图;
30.图2为实施例1中锤迹分布示意图;
31.图3为实施例1中仿泥页岩岩心材料的层理截面图;
32.图4为实施例1中仿泥页岩岩心材料的碎块浸水干燥状态图。
具体实施方式
33.本发明提供了一种仿泥页岩岩心材料,由包含下列质量份的组分制备得到:
34.水泥3~4份、二氧化硅0.1~0.3份、粉煤灰0.4~0.5份、氢氧化钙1~1.5份、黏土
75~85份、水16~18份。
35.在本发明中,所述水泥为3~4份,优选为3.2~3.8份,更优选为3.4~3.6份。
36.在本发明中,所述水泥优选为海螺pc42.5r型早强水泥,该水泥的早期反应速度快,早期强度高,有很强的胶凝作用帮助仿岩心材料成形并生成强度,帮助仿岩心材料获得脆硬性和水化膨胀性。
37.在本发明中,所述二氧化硅为0.1~0.3份,优选为0.14~0.26份,更优选为0.18~0.22份。
38.在本发明中,所述二氧化硅的粒径优选为10~100nm,进一步优选为20~90nm,更优选为40~70nm。
39.在本发明中,所述二氧化硅可以促进水泥的水化反应,氢氧化钙和黏土之间的火山灰反应和离子交换作用,同时帮助仿岩心材料裂隙的发育。
40.在本发明中,所述粉煤灰为0.4~0.5份,优选为0.42~0.48份,更优选为0.44~0.46份。
41.在本发明中,所述粉煤灰优选为二级c类粉煤灰,该粉煤灰钙含量高具有可观的反应活性,且粒径大小适宜缝隙填充岩心的孔隙;由于其反应速率与水泥相比较慢,可以促进微小裂隙的形成和层状结构的发展。
42.在本发明中,所述氢氧化钙为1~1.5份,优选为1.1~1.4份,更优选为1.2~1.3份。
43.在本发明中,所述氢氧化钙优选为工业氢氧化钙,可以帮助岩心基材形成高碱性环境,有利于各化学反应之间的反应;氢氧化钙的掺量较高,在干燥过程中会析出并形成层状结晶分布于岩心基材的颗粒之间,提高脆硬性、帮助微小裂隙发育和层状结构的形成。
44.在本发明中,所述黏土为75~85份,优选为76~84份,更优选为78~82份。
45.在本发明中,所述黏土的粒径优选小于等于5mm,进一步优选小于等于4mm,更优选小于等于3mm。
46.在本发明中,黏土的主要矿物成分为石英、长石等非黏土矿物和白云母、绿泥石和高岭石等黏土矿物;该类型土壤的颗粒粒径小,有较多的层状硅酸盐矿物,适宜形成泥页岩的层状结构。
47.本发明还提供了所述材料的制备方法,包含下列步骤:
48.(1)将水泥、二氧化硅、粉煤灰和氢氧化钙混合,得到复合添加剂;
49.(2)将黏土和第一部分水混合,得到泥料;
50.(3)将复合添加剂和泥料分别均分后进行混合,得到中间材料;
51.(4)将中间材料和剩余组分进行混合得到混合粒料;
52.(5)将混合粒料顺次进行击实和养护,即得所述仿泥页岩岩心材料。
53.在本发明中,所述步骤(1)中混合的方式优选为搅拌,所述搅拌的转速优选为100~110rpm,进一步优选为102~108rpm,更优选为104~106rpm;所述搅拌的时间优选为3~5min,进一步优选为3.5~4.5min,更优选为3.8~4.2min。
54.在本发明中,黏土使用前进行干燥,所述干燥的温度优选为100~110℃,进一步优选为102~108℃,更优选为104~106℃;所述干燥的时间优选为20~28h,进一步优选为22~26h,更优选为23~25h。
55.在本发明中,所述步骤(2)中第一部分水的质量优选占全部水质量的82~87%,进一步优选为83~86%,更优选为84~85%。
56.在本发明中,所述混合的方式优选为搅拌,所述搅拌的转速优选为190~200rpm,进一步优选为192~198rpm,更优选为194~196rpm;所述搅拌的时间优选为3.5~5min,进一步优选为4~4.5min,更优选为4.2~4.3min。
57.在本发明中,黏土和第一部分水混合完成后进行浸润,所述浸润的时间优选大于等于24h,进一步优选大于等于26h,更优选大于等于28h;所述浸润的温度优选为22~26℃,进一步优选为23~25℃,更优选为23.5~24.5℃。
58.在本发明中,所述步骤(3)中复合添加剂的均分份数优选为8~10份,进一步优选为8.5~9.5份,更优选为8.8~9.2份;所述泥料的均分份数优选为3~5份,进一步优选为3.5~4.5份,更优选为3.8~4.2份。
59.在本发明中,所述步骤(3)中混合的放置方式优选为按照单份复合添加剂、单份泥料的方式进行交替放置,所述放置优选为放置完最后一份泥料后再次放置一份复合添加剂,将泥料和复合添加剂放置完成后,两者以交替夹层的形式存在,然后进行下一步的混合。
60.在本发明中,所述步骤(3)中混合的方式优选为搅拌,所述搅拌的速率优选为100~110rpm,进一步优选为102~108rpm,更优选为104~106rpm;所述搅拌的时间优选为3~4min,进一步优选为3.2~3.8min,更优选为3.4~3.6min;搅拌结束后获得中间材料。
61.在本发明中,将中间材料按照复合添加剂的剩余份数进行均分。
62.在本发明中,所述步骤(4)中混合的放置方式优选为按照单份复合添加剂、单份中间材料的方式进行交替放置,复合添加剂和中间材料全部放置完成后,两者以交替夹层的形式存在,然后加入剩余的水进行混合。
63.在本发明中,所述步骤(4)中混合的方式优选为搅拌,所述搅拌的转速优选为190~200rpm,进一步优选为192~198rpm,更优选为194~196rpm;所述搅拌的时间为3~4min,进一步优选为3.2~3.8min,更优选为3.4~3.6min;所述搅拌结束后优选进行细化,细化后的粒径优选小于等于2mm,进一步优选小于等于1.5mm,更优选小于等于1mm;细化结束后优选进行静置,所述静置的时间优选为30~40min,进一步优选为32~38min,更优选为34~36min,所述静置的温度优选为19~26℃,进一步优选为20~25℃,更优选为22~23℃;静置结束后即为混合粒料。
64.在本发明中,获得混合粒料后优选将混合粒料进行均分,所述均分的份数优选为2~4份,更优选为3份。将单份混合粒料击实后,在其表面覆盖另一份混合粒料继续击实,直至所有单份混合粒料完成击实。
65.在本发明中,所述步骤(5)中击实的击锤质量优选为4~5kg,进一步优选为4.2~4.8kg,更优选为4.4~4.6kg;所述击实的锤落距优选为40~50cm,进一步优选为42~48cm,更优选为44~46cm;所述击实的锤落次数优选为90~100次,进一步优选为92~98次,更优选为94~96次;所述击实的锤迹相互重叠面积优选小于等于50%,进一步优选小于等于40%,更优选小于等于30%。
66.在本发明中,所述步骤(5)中养护优选为顺次进行的养生和干燥。
67.在本发明中,所述养生的时间优选为1~3天,更优选为2天;所述养生的温度优选
为20~27℃,进一步优选为21~26℃,更优选为23~25℃;所述养生的湿度优选为85~95%,进一步优选为87~93%,更优选为88~92%。
68.在本发明中,所述干燥的时间优选为15~20天,进一步优选为16~19天,更优选为17~18天;所述干燥的温度优选为21~31℃,进一步优选为22~29℃,更优选为24~27℃;所述干燥的湿度优选为40~50%,进一步优选为42~48%,更优选为44~46%。
69.本发明还提供了所述材料在填埋中的应用。
70.在本发明中,所述填埋优选为在垃圾填埋场中阻止废气扩散。
71.下面结合实施例对本发明提供的技术方案进行详细的说明,但是不能把它们理解为对本发明保护范围的限定。
72.实施例1
73.取3.5份海螺pc42.5r型早强水泥、0.2份粒径为50nm的二氧化硅、0.45份二级c类粉煤灰、1.3份氢氧化钙、80份粒径为4mm的黏土和18份水。
74.将水泥、二氧化硅、粉煤灰和氢氧化钙混合,在105rpm转速下搅拌4min,得到复合添加剂。
75.将黏土在105℃下干燥24h,然后和15.3份水在198rpm转速下搅拌4min,搅拌结束后在24℃下浸润24h,浸润完成后得到泥料。
76.将复合添加剂均分为8份,将泥料均分为3份,先放置一份复合添加剂,然后放置一份泥料,重复上述步骤两次,泥料全部放置完成后覆盖一份复合添加剂,形成交替夹层形式,如图1所示。然后在107rpm转速下搅拌3.5min获得中间材料。
77.此时,复合添加剂剩余4份,将中间材料均分为4份,先放置一份复合添加剂,然后放置一份中间材料,全部放置完成后加入剩余的水进行混合,在198rpm转速下搅拌3.5min,搅拌结束后进行细化,细化后的粒径为2mm,然后在24℃下静置30min获得混合粒料。
78.将混合粒料均分为3份,进行单份混合粒料击实,击锤质量为4.5kg,锤落距为45cm,锤落次数为95次,相互重叠面积小于50%,锤迹分布示意图如图2所示。单份混合粒料击实完毕后,在其表面放置下一份混合粒料,按照上述工艺参数进行击实,直至所有粒料击实完成。将击实后的粒料进行养生,养生的温度为25℃,湿度为90%,时间为2天;然后控制温度为26℃、湿度为45%的条件下,干燥15天即得仿泥页岩岩心材料。
79.本实施例制备的仿泥页岩岩心材料的层理截面如图3所示,从图3中可以看出本实施例制备的岩心材料具有致密的层理性和裂隙发展情况;将本实施例制备的岩心材料破坏后,浸水3天并干燥,干燥后的状态如图4所示,从图4中可以看出,本实施例制备的岩心材料,在浸泡干燥后仍然具有节理特征,表明其节理性不会因为浸泡而消失。
80.将本实施例制备的岩心材料进行性能测试,结果记录在表1中。
81.实施例2
82.取3份海螺pc42.5r型早强水泥、0.1份粒径为20nm的二氧化硅、0.4份二级c类粉煤灰、1份氢氧化钙、75份粒径为3mm的黏土和16份水。
83.将水泥、二氧化硅、粉煤灰和氢氧化钙混合,在100rpm转速下搅拌3min,得到复合添加剂。
84.将黏土在100℃下干燥20h,然后和13.6份水在198rpm转速下搅拌5min,搅拌结束后在23℃下浸润26h,浸润完成后得到泥料。
85.将复合添加剂均分为9份,将泥料均分为4份,先放置一份复合添加剂,然后放置一份泥料,重复上述步骤两次,泥料全部放置完成后覆盖一份复合添加剂,形成交替夹层形式,然后在100rpm转速下搅拌3分钟获得中间材料。
86.此时,复合添加剂剩余4份,将中间材料均分为4份,先放置一份复合添加剂,然后放置一份中间材料,全部放置完成后加入剩余的水进行混合,在190rpm转速下搅拌3min,搅拌结束后进行细化,细化后的粒径为1.5mm,然后在22℃下静置40min获得混合粒料。
87.将混合粒料均分为2份,进行单份混合粒料击实,击锤质量为4kg,锤落距为40cm,锤落次数为90次,相互重叠面积小于50%,单份混合粒料击实完毕后,在其表面放置下一份混合粒料,按照上述工艺参数进行击实,直至所有粒料击实完成。将击实后的粒料进行养生,养生的温度为25℃,湿度为85%,时间为2天;然后控制温度为28℃、湿度为40%的条件下,干燥20天即得仿泥页岩岩心材料。
88.将本实施例制备的岩心材料进行性能测试,结果记录在表1中。
89.实施例3
90.取4份海螺pc42.5r型早强水泥、0.3份粒径为80nm的二氧化硅、0.5份二级c类粉煤灰、1.5份氢氧化钙、85份粒径为4mm的黏土和18份水。
91.将水泥、二氧化硅、粉煤灰和氢氧化钙混合,在110rpm转速下搅拌5min,得到复合添加剂。
92.将黏土在110℃下干燥28h,然后和15份水在194rpm转速下搅拌4.5min,搅拌结束后在23℃下浸润28h,浸润完成后得到泥料。
93.将复合添加剂均分为10份,将泥料均分为4份,先放置一份复合添加剂,然后放置一份泥料,重复上述步骤两次,泥料全部放置完成后覆盖一份复合添加剂,形成交替夹层形式,然后在110rpm转速下搅拌4分钟获得中间材料。
94.此时,复合添加剂剩余5份,将中间材料均分为5份,先放置一份复合添加剂,然后放置一份中间材料,全部放置完成后加入剩余的水进行混合,在200rpm转速下搅拌4min,搅拌结束后进行细化,细化后的粒径为2mm,然后在22℃下静置35min获得混合粒料。
95.将混合粒料均分为4份,进行单份混合粒料击实,击锤质量为5kg,锤落距为50cm,锤落次数为100次,相互重叠面积小于50%,单份混合粒料击实完毕后,在其表面放置下一份混合粒料,按照上述工艺参数进行击实,直至所有粒料击实完成。将击实后的粒料进行养生,养生的温度为25℃,湿度为95%,时间为3天;然后控制温度为31℃、湿度为50%的条件下,干燥15天即得仿泥页岩岩心材料。
96.将本实施例制备的岩心材料进行性能测试,结果记录在表1中。
97.表1
[0098][0099]
由以上实施例可知,本发明提供了一种仿泥页岩岩心材料,由水泥、二氧化硅、粉
煤灰、氢氧化钙、黏土和水制备得到,具有节理性和脆硬性的特征,适合用于模拟泥页岩形成初期的各项物理性质,为泥页岩地质层的研究提供各项性质相似且价格低廉的试样。根据实施例的结果可知,本技术提供的仿泥页岩岩心材料,泊松比达到0.23,抗压强度为6.24mpa,水化膨胀性为0.46%/h,饱和强度为4.28mp,综合脆性指数为60.9%,具有优异的综合性能,适合用于岩石力学与地质研究。
[0100]
以上所述仅是本发明的优选实施方式,应当指出,对于本技术领域的普通技术人员来说,在不脱离本发明原理的前提下,还可以做出若干改进和润饰,这些改进和润饰也应视为本发明的保护范围。
再多了解一些
本文用于企业家、创业者技术爱好者查询,结果仅供参考。