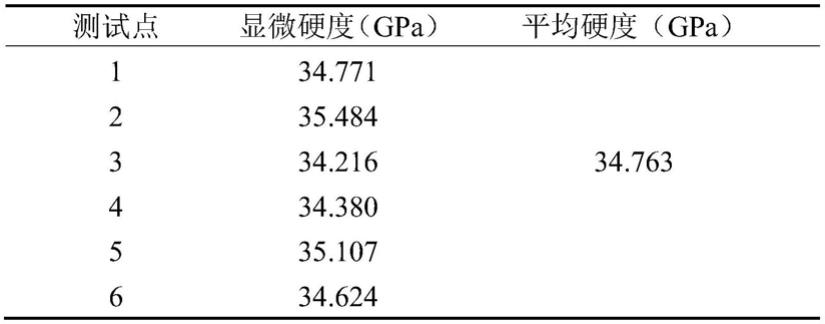
钛合金表面制备ti/tin复合涂层的方法及复合涂层
技术领域
1.本发明涉及一种在高载、冲击载荷等复杂工况下服役的高端装备零部件表面强化工艺,尤其涉及一种多弧离子镀ti/tin多层复合涂层的制备方法。
背景技术:
2.近年来,随着我国海洋工程、空间站、深空探测、天地往返以及核电等重大战略工程的实施,高端装备技术的迅猛发展以及工业应用产业化发展,对装备零部件的加工及材料性能要求越来越严苛,服役环境更趋向于高速、高温、重载、腐蚀介质等苛刻条件,使得关键部件材料可靠防护与长期可靠服役成为限制高端装备发展的主要瓶颈之一。材料表面防护技术作为表面工程技术中的一种重要表面改性手段,能够在不改变基体材料的成分及不削弱基体材料力学性能的基础上大大提高材料表面性能,有效地提高各类工件的品质性能、效率与使用寿命,对于提高高端装备稳定性及服役寿命有着重要作用。目前随着该技术的不断发展,已由普通环境下的材料保护技术向苛刻环境下的特种防护技术发展,主要包括高速、高温、重载环境下的长寿命润滑与强化技术,严酷海洋大气、深海环境下的腐蚀与防护技术,以及面向重大装备的维修与再制造技术等。
3.钛及钛合金具有密度小、比强度大、耐腐蚀性好、耐低温性好、无磁性、抗冲击性、焊接性能好等突出优点,被誉为“未来金属”、“海洋金属”等,是一种具有重大应用前景的先进材料。目前已在航空航天、海洋工程、化工、电力、医疗等领域得到广泛应用,但因其硬度较低、耐磨性差、摩擦系数较大,微动磨损会加剧磨损、增加磨损量,最终造成零部件功能的失效,因此对钛及钛合金表面进行强化处理成为了该领域的研究热点之一。目前国内外相关学者及研究机构针对钛合金强化处理已开展了大量研究,并取得了一定成果,主要有渗碳、渗氮、阳极氧化、离子注入、化学镀以及钛基复合强化涂层等等,但这些表面处理技术大都存在成本较高、能源消耗大、工艺复杂等问题以及由于形成的表面硬化层深度较薄,在较大载荷、较长时间的情况下,实际使用效果欠佳。tin作为硬质涂层的代表,经过多年的研究,已经获得了长足发展,是用于表面防护的主要涂层材料之一,已经广泛应用于高速钢、硬质合金和模具钢等材料上。国内外学者主要通过磁控溅射、多弧离子镀等物理气相沉积方法在以tin为代表的硬质涂层、纳米多层薄膜和超晶格薄膜等新型涂层方面开展了大量研究,但目前由于钛合金应用领域的拓展,服役条件的升级,对现有涂层结构、性能提出了更高的要求,尤其在高端装备产业化应用中面临新挑战,主要有以下三点:一是高端装备零部件精密程度越来越高,以tin涂层为例,其传统沉积工艺温度一般在400℃~500℃,由于制备工艺的局限,容易造成精密零件尺寸变化较大,直接影响零件的装配使用;二是纳米多层薄膜和超晶格薄膜虽然获得了长足发展,但由于纳米多层膜大量界面和点阵缺陷的存在、超晶格薄膜相同厚度控制的难点以及沉积效率低下等问题,具有超硬特征及新功能性质的纳米多层结构涂层和纳米复合涂层的制备还有许多理论和技术问题需要研究和解决,在工业应用特别是高端装备复杂形状零件表面的产业化应用仍存在较大的困难,限制了其在工业中的推广应用;三是高端装备零部件在冲击载荷、重载等复杂工况下的应用越来越
多,由于tin系列涂层的结合力随厚度增加而下降,且涂层使用过程中受到高的压应力,接触面过载容易发生剪切断裂,一般厚度不超过8μm,制备tin厚膜十分困难。同时因为tin与基体的物理性能差别很大,特别是韧性不足,膜层结构设计不合理,较厚膜层内应力大、结合不牢固,在重载、冲击载荷实际应用中容易从基体上崩裂而剥落、严重磨损等失效现象,极大的限制了其在重载、长寿命、高可靠性零部件表面的应用,已成为目前涂层工业应用领域的一个重要挑战。
4.总体而言,目前国内外许多研究机构和学者就钛合金表面保护性、功能性薄膜的研究以及钛合金表面制备tin系列硬质耐磨涂层已取得了很大进展并产生了大量的研究成果及一批相关专利,但在较低温度下获得一定厚度且具有高硬度、良好韧性,能够在高载、冲击载荷下仍具有良好摩擦性能涂层制备与应用未见报道。
技术实现要素:
5.本发明的目的在于针对高端装备高精度、复杂服役工况要求,克服现有技术的不足,以普通tin涂层为例,提供一种利用多弧离子镀低温制备高载摩擦学ti/tin复合涂层的方法及复合涂层,满足tin涂层在高端装备零部件在高载、冲击载荷下的工业化应用需求,为硬质涂层的研究及拓展应用领域提供基础。
6.本发明是通过下述技术方案来实现的。
7.本发明一方面,提供了一种钛合金表面制备ti/tin复合涂层的方法,包括以下步骤:
8.钛合金预处理:对钛合金表面经打磨、抛光和清洗,吹干装炉;
9.镀膜机腔室抽真空:进行两级抽真空;
10.辉光清洗和弧光清洗:保持腔室真空环境,在保护气氛下,采用四个靶源的脉冲偏压多弧离子镀设备,分别对预处理后的钛合金辉光清洗和弧光清洗;
11.多弧离子镀ti/tin复合涂层:
12.通入氮气和氩气,保持腔室真空度,采用一对对称分布的低电流钛靶材,控制靶材的弧流、偏压,沉积打底层;
13.关闭氩气,控制氮气流量,保持镀膜机腔室真空环境,依次采用一对对称分布的高电流钛靶材沉积tin涂层1和tin涂层2;依此重复沉积tin涂层1和tin涂层2若干个循环,每次循环中间沉积一次复合过渡层;完成钛合金表面ti/tin复合涂层的制备。
14.优选的,对钛合金表面进行前期清洗:采用不同粗细的砂纸逐级打磨,颗粒度为0.5μm的金刚石抛光剂抛光至表面镜面,再依次放入酒精、丙酮和石油醚中超声波清洗,吹干装炉。
15.优选的,两级抽真空包括镀膜机腔室抽至真空度小于5
×
10
‑3pa,再升温至200℃~250℃,再抽真空至小于1
×
10
‑3pa。
16.优选的,辉光清洗时,向真空腔室内通入氩气,气压为40pa~80pa,点燃一对低电流钛靶材,施加500v~800v的负偏压,占空比30~60%,辉光清洗90min~120min。
17.优选的,弧光清洗时,通入氩气至真空度为0.01pa~5pa,点燃一对低电流钛靶材,施加150v~250v的负偏压,占空比30~40%,在弧流45a~55a下进行弧光清洗1min~3min。
18.优选的,沉积打底层时,通入比例为1:1氮气和氩气,使腔室真空度为1pa~5pa,一
对低电流钛靶材弧流为45a~55a,偏压为300v~450v,占空比为20~40%,沉积5~8min。
19.优选的,沉积tin涂层1时,点燃一对高电流钛靶材,控制弧流为80~90a,偏压为150v~250v,占空比为20~40%,沉积20~30min。
20.优选的,沉积tin涂层2时,点燃一对低电流钛靶材,控制弧流为45~55a,偏压为150v~250v,占空比为20~40%,沉积20~40min。
21.优选的,沉积复合过渡层时,控制一对低电流钛靶材弧流为10~20a,通入比例为4:1氩气和氮气,腔室内气压为1~10pa,偏压为300v~450v,占空比为30~50%,沉积20~30min。
22.本发明另一方面,提供了一种所述方法制备得到的在钛合金表面制备具有高载摩擦学并能够承受一定冲击载荷具有良好承载力的tin复合涂层,该涂层包括依次分布的钛合金基体层、打底层、tin涂层1、tin涂层2、复合过渡层、tin涂层1、tin涂层2、复合过渡层、......tin涂层1、tin涂层2。
23.本发明由于采取以上技术方案,其具有以下有益效果:
24.1、本发明采用脉冲偏压以及间歇沉积工艺控制,在200℃~250℃下完成tin复合涂层制备,可以有效地降低沉积过程中的基体温升,实现较低温度沉积。
25.2、本发明在涂层制备前进行了有机溶剂及辉光、弧光离子溅射清洗,有效去除钛合金表面污染物及氧化层,提高了低温沉积tin复合涂层的结合力。
26.3、本发明通过控制氮气、氩气比例、弧流等参数,在钛合金表面制备了钛和氮化钛共存的打底层,使得涂层与基体之间物理及力学性能处于渐近变化状态,形成了良好的界面结合,确保了涂层与基体间的结合强度。
27.4、一定厚度的软ti层有利于能量消散,可调整多层涂层的残余应力,但过厚会造成涂层整体硬度及结合力降低,本发明设计了与相邻层面成分、结构和性能接近的多相混合结构复合过渡层,有效控制了膜层内应力,实现了具有高硬度、良好韧性厚膜涂层的制备。
28.5、本发明利用复合过渡层沉积过中脉冲高能量离子轰击作用改善了tin柱状晶结构,解决了柱状晶随膜层的增厚而粗大的问题,并通过设计膜层结构,周期性调节tin涂层1、tin涂层2及复合过渡层重复沉积,获得了软硬、疏密交替的ti/tin多层涂层,大大提高了界面及涂层整体承载能力。
29.6、本发明通过引入脉冲偏压,减小弧流以及间歇沉积工艺方法,有效降低了涂层表面的大颗粒尺寸和数量,改善了膜层表面质量,且操作简单,生产效率高,更适用于工业实际生产。
30.7、本发明制备的复合涂层厚度为18~21μm,涂层的结合力达150n以上,在5n~30n载荷、氮化硅球(半径为3.15mm)为对摩件球盘摩擦条件下,摩擦系数约为0.5~0.7,未出现膜层破裂及剥落现象,涂层表现出良好的摩擦性能;在转速200~300r/min,冲击载荷100~200n,冲击频率20hz下与gcr15环形件进行冲击滑动对摩实验,涂层表现出良好的承载能力与抗摩擦性能。
31.本发明可获得一种在重载、冲击载荷作用下具有良好摩擦性能ti/tin复合涂层的制备方法。
附图说明
32.此处所说明的附图用来提供对本发明的进一步理解,构成本技术的一部分,并不构成对本发明的不当限定,在附图中:
33.图1(a)、(b)为实施例1涂层表面形貌及能谱结果示意图;
34.图2为实施例2不同摩擦条件下tin涂层摩擦系数示意图;
35.图3(a)、(b)分别为实施例2磨痕形貌图;
36.图4为实施例3磨痕形貌图。
具体实施方式
37.下面将结合附图以及具体实施例来详细说明本发明,在此本发明的示意性实施例以及说明用来解释本发明,但并不作为对本发明的限定。
38.本发明实施例提供的在钛合金表面制备ti/tin复合涂层的方法,包括以下步骤:
39.1)前期清洗:采用不同粗细的砂纸逐级对钛合金表面进行打磨,并通过颗粒度为0.5μm的金刚石抛光剂进行抛光至表面镜面,再依次放入酒精、丙酮和石油醚等有机溶剂中进行超声波清洗,最后吹干装炉。
40.2)抽真空:将镀膜机腔室真空抽至小于5
×
10
‑3pa,打开加热装置,使腔室温度升至200℃~250℃,再抽真空至小于1
×
10
‑3pa。
41.3)辉光 弧光清洗:
42.向真空腔室内通入氩气,使气压升至40pa~80pa,打开脉冲偏压电源,点燃一对低电流钛靶材(多弧靶1和多弧靶4),施加500v~800v的负偏压,占空比30~60%,在试件随转台匀速旋转的同时,进行辉光清洗90min~120min;
43.抽真空至小于1
×
10
‑3pa,再通入氩气至真空度为0.01pa~5pa,开启偏压电源,施加150v~250v的负偏压,占空比30~40%,点燃多弧靶1和多弧靶4,在弧流45a~55a下进行弧光清洗1min~3min。
44.4)多弧离子镀ti/tin复合涂层:
45.①
沉积打底层:通入比例为1:1氮气和氩气,使腔室真空度为1pa~5pa,多弧靶1和多弧靶4的弧流为45a~55a,偏压为300v~450v,占空比为20~40%,沉积5~8min。
46.②
沉积tin涂层1:关闭氩气,控制氮气流量,使腔室真空度为0.1pa~2.0pa,点燃一对高电流钛靶材(多弧靶2和多弧靶3),控制弧流为80~90a,偏压为150v~250v,占空比为20~40%,沉积20~30min。
47.③
沉积tin涂层2:控制一对低电流钛靶材(多弧靶1和多弧靶4)弧流为45~55a,偏压为150v~250v,占空比为20~40%,沉积20~40min。
48.④
沉积复合过渡层:
49.重复六个循环完成,其中每次循环中间沉积一次复合过渡层。沉积复合过渡层时,控制一对低电流钛靶材(多弧靶1和多弧靶4)弧流为10~20a,通入比例为4:1氩气和氮气,腔室内气压为1~10pa,偏压为300v~450v,占空比为30~50%,沉积20~30min。
50.5)冷却出炉:关闭多弧、偏压电源及加热装置,自然冷却至低于60℃后,打开真空室,取出样件。
51.下面通过具体实施例来进一步说明本发明。
52.以普通tin涂层为例,提供一种利用多弧离子镀低温制备高载摩擦学ti/tin复合涂层的方法,满足tin涂层在高端装备零部件在高载、冲击载荷下的工业化应用需求,为硬质涂层的研究及拓展应用领域提供基础。
53.实施例1:
54.1)前期清洗:采用不同粗细的砂纸逐级进行打磨,并通过颗粒度为0.5μm的金刚石抛光剂进行抛光至表面镜面,再依次放入酒精、丙酮和石油醚有机溶剂中进行超声波清洗,最后吹干装炉;
55.2)抽真空:将镀膜机腔室真空抽至小于5
×
10
~3
pa,打开加热装置,使腔室温度升至200℃,再抽真空至小于1
×
10
~3
pa;
56.3)辉光 弧光清洗:向真空腔室内通入氩气,使真空室的气压升至50pa,打开脉冲偏压电源,点燃多弧靶1和多弧靶4,施加750v的负偏压,占空比45%,在试件随转台匀速旋转的同时,进行辉光清洗120min;
57.抽真空至小于1
×
10
~3
pa,再通入氩气至真空度为2pa,开启偏压电源,施加200v的负偏压,占空比35%,点燃多弧靶1和多弧靶4,在弧流50a下进行弧光清洗1min;
58.4)多弧离子镀ti/tin复合涂层:
59.沉积打底层:通入比例为1:1氮气和氩气,使腔室真空度为3pa,多弧靶1和多弧靶4弧流为50a,偏压为400v,占空比为30%,沉积5min。
60.沉积tin涂层1:关闭氩气,控制氮气流量为,使腔室真空度为0.1pa~2.0pa,多弧靶2和多弧靶3弧流为80a,偏压为200v,占空比为30%,沉积25min。
61.沉积tin涂层2:多弧靶1和多弧靶4弧流为50a,偏压为200v,占空比为30%,沉积30min。
62.沉积复合过渡层:重复六个循环完成,其中每次循环中间沉积一次复合过渡层,沉积时,多弧靶1和多弧靶4弧流为10a,通入比例为4:1氩气和氮气,腔室内气压为5pa,偏压为350v,占空比为40%,沉积20min。
63.5)冷却出炉:关闭多弧、偏压电源及加热装置,自然冷却至低于60℃后,打开真空室,取出样件。
64.采用上述沉积工艺低温制备了约1.5μm的tin涂层1和约1.5μm的tin涂层2为基本单位,交替重复6次构成的tin复合涂层,涂层整体厚度18.6μm,表面大液滴数量及尺寸较小,表面质量良好(图1(a)、(b));由于混合结构的打底层以及过渡层沉积,涂层界面结合良好,通过划痕仪检测,膜基结合力达158n;利用纳米硬度计进行检测,平均纳米硬度达34.763gpa(表1)。
65.表1涂层显微硬度测试结果
[0066][0067]
实施例2:
[0068]
在tc4钛合金环形零件表面进一步采用以下实施例验证本发明的有益效果:
[0069]
1)前期清洗:采用不同粗细的砂纸逐级进行打磨,并通过颗粒度为0.5μm的金刚石抛光剂进行抛光至表面镜面,再依次放入酒精、丙酮和石油醚有机溶剂中进行超声波清洗,最后吹干装炉;
[0070]
2)抽真空:将镀膜机腔室真空抽至小于5
×
10~3pa,打开加热装置,使腔室温度升至250℃,再抽真空至小于1
×
10
‑3pa;
[0071]
3)辉光 弧光清洗:向真空腔室内通入氩气,使真空室的气压升至40pa,打开脉冲偏压电源,施加800v的负偏压,占空比30%,在试件随转台匀速旋转的同时,进行辉光清洗90min;抽真空至小于1
×
10
‑3pa,再通入氩气至真空度为5pa,开启偏压电源,施加150v的负偏压,占空比40%,点燃多弧靶1和靶4,在弧流45a下进行弧光清洗2min;
[0072]
4)多弧离子镀ti/tin复合涂层:
[0073]
沉积打底层:通入比例为1:1氮气和氩气,使腔室真空度为1pa,沉积打底层;多弧靶1和多弧靶4弧流为45a,偏压为300v,占空比为40%,沉积8min。
[0074]
沉积tin涂层1:关闭氩气,控制氮气流量,使腔室真空度为0.1pa~2.0pa,多弧靶2和多弧靶3弧流为90a,偏压为150v,占空比为40%,沉积30min。
[0075]
沉积tin涂层2:多弧靶1和多弧靶4弧流为45a,偏压为250v,占空比为40%,沉积20min。
[0076]
沉积复合过渡层:
[0077]
重复六个循环完成,其中每次循环中间沉积一次复合过渡层。沉积复合过渡层时,多弧靶1和多弧靶4弧流为15a,通入比例为4:1氩气和氮气,腔室内气压为10pa,偏压为300v,占空比为30%,沉积30min。
[0078]
采用上述沉积工艺低温制备了约1.5μm的tin涂层1和约1.5μm的tin涂层2为基本单位,交替重复6次构成的tin复合涂层,涂层整体厚度约21μm,表面大液滴数量及尺寸较小,表面质量良好;由于混合结构的打底层以及过渡层沉积,涂层界面结合良好,通过划痕仪检测,膜基结合力达170n;利用纳米硬度计进行检测,其纳米硬度达35.482gpa;分别在赫兹接触应力为1gpa、1.2gpa、1.5gpa,氮化硅(半径6.3mm)为对摩件、球盘式摩擦磨损试验机下进行了检测,摩擦系数约为0.7(图2),膜层未出现剥落等现象,2.0gpa时涂层表面产生磨粒磨损,但涂层整体良好(图3(a)、(b)),表现出良好抗摩擦性能。
[0079]
实施例3:
[0080]
在tc4钛合金环形零件表面进一步采用以下实施例验证本发明的有益效果:
[0081]
1)前期清洗:采用不同粗细的砂纸逐级进行打磨,并通过颗粒度为0.5μm的金刚石抛光剂进行抛光至表面镜面,再依次放入酒精、丙酮、石油醚有机溶剂中进行超声波清洗,最后吹干装炉;
[0082]
2)抽真空:将镀膜机腔室真空抽至小于5
×
10~3pa,打开加热装置,使腔室温度升至220℃,再抽真空至小于1
×
10
‑3pa;
[0083]
3)辉光 弧光清洗:向真空腔室内通入氩气,使真空室的气压升至80pa,打开脉冲偏压电源,施加500v的负偏压,占空比60%,在试件随转台匀速旋转的同时,进行辉光清洗110min;抽真空至小于1
×
10
‑3pa,再通入氩气至真空度为0.01pa,开启偏压电源,施加250v的负偏压,占空比30%,点燃多弧靶1和靶4,在弧流55a下进行弧光清洗3min;
[0084]
4)多弧离子镀ti/tin复合涂层:
[0085]
沉积打底层:通入比例为1:1氮气和氩气,使腔室真空度为5pa,沉积打底层;多弧靶1和多弧靶4弧流为55a,偏压为450v,占空比为20%,沉积6min。
[0086]
沉积tin涂层1:关闭氩气,控制氮气流量,使腔室真空度为0.1pa~2.0pa,多弧靶2和多弧靶3弧流为85a,偏压为250v,占空比为20%,沉积20min。
[0087]
沉积tin涂层2:多弧靶1和多弧靶4弧流为55a,偏压为150v,占空比为20%,沉积40min。
[0088]
沉积复合过渡层:
[0089]
重复六个循环完成,其中每次循环中间沉积一次复合过渡层。沉积复合过渡层时,多弧靶1和多弧靶4弧流为20a,通入比例为4:1氩气和氮气,腔室内气压为1pa,偏压为450v,占空比为30%,沉积25min。
[0090]
采用上述沉积工艺低温制备了约1.5μm的tin涂层1和约1.5μm的tin涂层2为基本单位,交替重复6次构成的tin复合涂层,表面质量良好;以gcr15环形件为对摩件、在冲击滑动摩擦试验器下进行了模拟检测,tin涂层表面受到反复交变应力,在转速为200r/min,冲击力为100n,冲击频率20hz,时间2小时工况下,涂层表面完好;在转速为300r/min,冲击力为200n时,涂层出现少量划痕,发生了磨粒磨损,但整体并未发生严重磨损与擦伤(图4),显示出良好的耐磨性,有效阻挡了强大冲击载荷对钛合金基体材料的损伤,验证了制备的tin厚膜涂层在冲击载荷下能够对基体材料起到了有效防护作用,膜层未出现剥落等现象,表现出良好抗摩擦性能。
[0091]
从以上实施例可以看出,采用本发明方法制备的复合涂层,涂层表现出良好的承载能力与抗摩擦性能。通过本发明方法可获得一种在重载、冲击载荷作用下具有良好摩擦性能ti/tin复合涂层。本发明解决了tin涂层与基体间结合力差的问题,并通过软硬、疏密交替的多层膜层设计,抑制了tin柱状晶的生长,改善了厚膜制备存在的内应力大问题,大大提高了界面及涂层整体承载能力,突破了钛合金表面高载摩擦学tin厚膜的制备难题,并且沉积温度低,可有效避免零件产品的尺寸变形,对高端装备零部件重载、冲击载荷等复杂工况下的应用提供了一种新思路。
[0092]
本发明并不局限于上述实施例,在本发明公开的技术方案的基础上,本领域的技术人员根据所公开的技术内容,不需要创造性的劳动就可以对其中的一些技术特征作出一些替换和变形,这些替换和变形均在本发明的保护范围内。
再多了解一些
本文用于企业家、创业者技术爱好者查询,结果仅供参考。