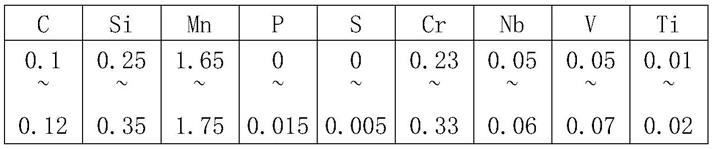
1.本发明涉及冶金行业连铸技术领域,尤其涉及一种宽厚板坯高强钢纵向裂纹缺陷的控制方法。
背景技术:
2.纵裂是连铸板坯常见的表面缺陷之一,据有关资料介绍,铸坯各类缺陷中有50%以上是裂纹缺陷。轻微的纵裂纹经板坯精整后对下工序不会产生影响,但严重的纵裂纹会使整个板坯报废,甚至会在浇铸过程中引起纵裂漏钢,给设备和生产带来严重的危害。包钢宽板铸机在浇铸高强系列钢种时,铸坯表面纵向裂纹缺陷严重,纵裂比例达13.2%,并且发现浇次第1炉纵裂比例明显高于其它炉次,其它炉次裂纹出现在每炉次前5块的占所有裂纹的50%以上。纵裂主要发生在上表面即内弧侧,长度短则10~20mm,长的达数米,可以贯穿整个板坯长度。深度在2~10mm不等。裂纹位置分布无明显规律,主要发生在q690d、q550d等钢种上,成份为碳含量在0.09%~0.15%的低合金钢。纵裂形态如图1。
3.关于板坯纵裂产生的原因有很多研究,纵裂产生的机理是在结晶器弯月面附近,伴随着初期固液相变,包晶反应引起的体积收缩及工艺参数引起的结晶器传热不均匀,导致初生坯壳厚度不均匀,在坯壳薄弱处产生应力集中,当应力超过坯壳的高温强度时就产生裂纹,微裂纹在二冷区强冷加以扩展。
4.包钢宽板铸机浇铸规格为1200~2300mm,有200、250、300三种断面,中间包工作液位38吨,每年浇铸高强钢8万吨左右。
5.由于包钢宽板铸机板坯纵裂主要发生在高强钢,所以成份是重要影响因素。特别是钢中[c]含量影响。这是因为[c]在0.09%
‑
0.14%时处于包晶区,发生δ
‑
fe向γ
‑
fe的转变,伴随着较大的体积收缩,坯壳与结晶器铜板间形成气隙,导热不均,产生应力集中,从而在坯壳薄弱处产生裂纹。
[0006]
申请号为201910257036.0的中国专利公开了一种宽板坯纵向裂纹控制工艺是通过提高锰硫比降低铸坯表面纵裂,并且主要针对宽厚比大的连铸机。本发明针对宽板铸机浇铸高强钢时通过优化工艺参数,优化炉次生产组织,优化炉次间转包操作等手段减少裂纹源,以达到降低纵裂发生率的目的,成本明显降低。
[0007]
申请号为202010674689.1的中国专利公开了一种解决高强钢铸坯裂纹的工艺方法是通过铸坯热装入炉,避免铸坯在冷却至室温的过程中导热系数变化引起的应力交替集中所致的高强钢铸坯裂纹。本发明通过对高强钢进行优化生产组织,优化操作等手段消除表面纵裂,不仅适用于热装,冷装效果同样良好。
[0008]
申请号为201910861784.x的中国专利公开了一种减少宽厚板连铸坯表面纵裂纹的开浇仅仅针对开浇第1炉,通过对第1炉工艺参数进行优化,使用专用保护渣达到对第1炉裂纹控制的目的,而对于其它炉次并未述及。本发明对第1炉浇铸通过优化炉次生产组织,对其它炉次间转包时由于夹杂物进入钢水形成裂纹源做了专门阐述。
技术实现要素:
[0009]
为了解决上述技术问题,本发明的目的是提供一种宽厚板坯高强钢纵向裂纹缺陷的控制方法,旨在降低产品缺陷发生率,提高产品质量合格率和市场占有率。
[0010]
为解决上述技术问题,本发明采用如下技术方案:
[0011]
一种宽厚板坯高强钢纵向裂纹缺陷的控制方法,包括以下步骤:
[0012]
(1)优化生产组织,避免直接用高强钢开浇;(2)优化炉次间换包操作,减少夹杂物进入钢水,从而减少裂纹源;(3)适当调大结晶器锥度;(4)适当减少结晶器水流量;
[0013]
其中:
[0014]
所述步骤(1)包括:浇铸高强钢时,将其它级别较低的包晶钢放在第1炉,高强钢跟在后面炉次连浇;
[0015]
所述步骤(2)的主要措施包括:在换包时,除混浇操作外,尽量保证满包操作,保证下一包拉开时中包液位不低于30吨;最大限度减少夹杂物进入钢水,减少裂纹源的产生;
[0016]
所述步骤(3)中浇铸高强钢时将结晶器锥度由9.9调整为11.5;
[0017]
所述步骤(4)中将结晶器水流量在4700l/min的基础上降低100
‑
200l/min,降低结晶器弯月面的冷却强度。
[0018]
进一步的,所述步骤(1)具体包括:
[0019]
浇铸第1炉拉速从0开始,逐渐涨速到正常拉速;宽厚板铸机涨速曲线为:开浇设备正常启动后直接涨到0.4m/min,稳定1min后再以0.1m/min2的加速度均匀涨速,每涨0.1m/min稳定1min,直到涨至正常拉速(0.9m/min以上)。
[0020]
与现有技术相比,本发明的有益技术效果:
[0021]
通过优化生产组织和操作方法,最大限度降低夹杂物进入钢水,减少裂纹源;调整工艺参数,采用弱冷降低弯月面冷却强度,使初生坯壳传热慢、收缩小,冷却均匀,降低裂纹发生的几率。连铸板坯裂纹缺陷的发生率由13.2%降低到0.8%,明显地减少了生产损失,提高了产品质量合格率和市场占有率,有效地解决了背景技术中存在的问题。
附图说明
[0022]
下面结合附图说明对本发明作进一步说明。
[0023]
图1为本发明高强钢纵裂照片。
[0024]
图2为本发明换包操作时中间包液位控制曲线。
具体实施方式
[0025]
为了使本发明实施案例的目的、技术方案和优点更加清楚,下面将结合实施案例对本发明实施案例中的技术方案进行清晰的、完整的描述。
[0026]
一种宽厚板坯高强钢纵向裂纹缺陷的控制方法,包含以下步骤:(1)优化生产组织,避免直接用高强钢开浇;(2)优化炉次间换包操作,减少夹杂物进入钢水,从而减少裂纹源;(3)适当调大结晶器锥度;(4)适当减少结晶器水流量。
[0027]
所述步骤(1)优化生产组织,避免直接用高强钢开浇包括:浇铸高强钢时,将其它级别较低的包晶钢放在第1炉,高强钢跟在后面炉次连浇。
[0028]
所述步骤(2)优化炉次间换包操作,减少夹杂物进入钢水,从而减少裂纹源,主要
措施包括在换包时,除混浇操作外,尽量保证满包操作,保证下一包拉开时中包液位不低于30吨。最大限度减少夹杂物进入钢水,减少裂纹源的产生。
[0029]
所述步骤(3)适当调大结晶器锥度中,浇铸高强钢时将结晶器锥度由9.9调整为11.5。
[0030]
所述步骤(4)适当减少结晶器水流量中,将结晶器水流量在4700l/min的基础上减少100
‑
200l/min,降低结晶器弯月面的冷却强度。
[0031]
本发明具体实施方案如下:
[0032]
1、优化生产组织,避免直接用高强钢开浇。
[0033]
浇次第1炉是连铸过程中最不稳定阶段。浇铸初期,水温和拉速偏低,结晶器传热和润滑均不稳定,钢水过热度高,这些均对铸坯表面造成影响。
[0034]
进一步的,浇铸第1炉拉速从0开始,逐渐涨速到正常拉速。包钢宽厚板铸机涨速曲线为:开浇设备正常启动后直接涨到0.4m/min,稳定1min后再以0.1m/min2的加速度均匀涨速,每涨0.1m/min稳定1min,直到涨至正常拉速0.9m/min以上。
[0035]
进一步的,在浇次间隔,结晶器进水温度和二冷水温度下降,结晶器正常控制进水温度应为36
±
2℃,但停浇后能降到25℃以下,甚至在冬季浇次间隔长时能降到10℃以下。二冷水温正常应控制在25℃左右,但浇次间隔也能降到15℃以下。
[0036]
进一步的,开浇第1炉过热度偏高,当过热度大于35℃时,钢水凝固推迟,坯壳厚度减薄且坯壳平均温度升高,即使应力不变的情况下,由于钢的整体温度向脆性区移动,纵裂倾向加重。
[0037]
由于开浇第一炉存在以上不利因素,发生纵裂几率大,避免高强钢在同浇次第一炉的浇铸,换成其它级别较低的钢种开浇,高强钢跟在后面炉次连浇。
[0038]
优化炉次间换包操作,减少夹杂物进入钢水,从而减少裂纹源。
[0039]
统计2020年12月到2021年1月的10个浇次共69炉高强钢,其中裂纹出现在每炉次前5块的占所有裂纹的50%以上,说明在炉次过程中换包操作时有夹杂物进入钢水,众所周知,夹杂物是潜在的裂纹源,特别是存在一些脆性氧化物和脆性硅酸盐等夹杂物时,如钢件受到应力作用时更易开裂。
[0040]
包钢宽板铸机中间包工作液位是38吨,溢流液位42吨,我们在换包时,尽量保证满包操作,保证下一包拉开时中包液位不低于30吨,如遇异钢种混浇需要控制到30吨以下(一般控到12吨),在下一包拉开后全流控制到30吨。30吨以后缓慢控流至工作液位,做到最大限度地减少夹杂物进入钢水,从而减少裂纹源。换包时具体操作曲线如图2。
[0041]
3、适当调大结晶器锥度。
[0042]
板坯浇铸时,一般通过合理调整结晶器锥度和优化保护渣性能来减少气隙热阻。锥度设置应与工艺拉速、断面和钢种的收缩特性相适应,包晶钢结晶器锥度调节一般控制在1.0%~1.2%之间,用锥度测量仪进行测量校准。由于包钢宽厚板产品品种多,一个浇次包括多个钢种,经常将包晶钢和中碳钢安排在同一个浇次内,但包晶钢和中碳钢锥度相差较大,在实际调整时往往取加权平均数,这样对包晶钢来说锥度偏小,结晶器下部受热不均并产生应力,从而导致纵裂产生。
[0043]
浇铸高强钢时,避免与中碳钢安排在一个浇次,这样同浇次其它钢种锥度也不受影响,并且将锥度在原来的基础上适当增大,使结晶器下部与坯壳充分接触,减少了气隙的
产生,坯壳传热更加均匀。
[0044]
4、适当减少结晶器水流量。
[0045]
结晶器弱冷、宽窄面铜板热通量保持一定的比例有助于减少表面纵向裂纹。实现结晶器弱冷最有效的方式就是减小结晶器水量,通过将水流量在4700l/min的基础上减少100
‑
200l/min,降低结晶器冷却强度,达到弱冷减轻表面纵裂的目的。
[0046]
通过以上措施,包钢宽厚板高强钢裂纹缺陷的发生率由13.2%降低到0.8%,明显地减少了生产损失,提高了产品质量合格率和市场占有率。
[0047]
以下结合实施例对本发明技术效果做进一步描述:
[0048]
实施例1:
[0049]
该实施例是运用本发明的控制方法控制高强钢q550d的纵向裂纹,q550d的化学成份见表1。
[0050]
浇铸断面2000
×
250的q550d时,将结晶器宽侧水流量由4700l/min调整为4600l/min,结晶器锥度由9.9调整为11.5。浇次第1炉安排其它级别较低包晶钢,第2炉开始浇铸q550d,第1炉和第2炉执行异钢种混浇操作:将中间包液位控制到12吨时第2炉全流拉开浇铸,中间包液位到达30吨以后缓慢控流至工作液位。第3炉以后在换包时保证中间包满包操作,即在下一炉拉开时中包液位不低于30吨。浇铸过程中,拉速稳定在0.9m/min。冷装轧制后钢板经表检检查,纵裂发生率为零。
[0051]
表1:q550d化学成份
[0052][0053]
实施例2:
[0054]
该实施例是运用本发明的控制方法控制高强钢q690d的纵向裂纹,q690d的化学成份见表2。
[0055]
浇铸断面2000
×
250的q690d时,将结晶器宽侧水流量由4700l/min调整为4550l/min,结晶器锥度由9.9调整为11.5。浇次第1炉安排其它级别较低包晶钢,第2炉开始浇铸q690d,第1炉和第2炉执行异钢种混浇操作:将中间包液位控制到12吨时第2炉全流拉开浇铸,中间包液位到达30吨以后缓慢控流至工作液位。第3炉以后在换包时保证中间包满包操作,即在下一炉拉开时中包液位不低于30吨。浇铸过程中,拉速稳定在0.9m/min。冷装轧制后钢板经表检检查,纵裂发生率为零。
[0056]
表2:q690d化学成份
[0057][0058]
实施例3:
[0059]
该实施例是运用本发明的控制方法控制高强钢q550d
‑
zm的纵向裂纹,q550d
‑
zm的
化学成份见表3。
[0060]
浇铸断面1600
×
250的q550d
‑
zm时,将结晶器宽侧水流量由4700l/min调整为4500l/min,结晶器锥度由8.0调整为9.2。浇次第1炉安排其它级别较低包晶钢,第2炉开始浇铸q550d
‑
zm,第1炉和第2炉执行异钢种混浇操作:将中间包液位控制到12吨时第2炉全流拉开浇铸,中间包液位到达30吨以后缓慢控流至工作液位。第3炉以后在换包时保证中间包满包操作,即在下一炉拉开时中包液位不低于30吨。浇铸过程中,拉速稳定在1.0m/min。经直接热装,轧制后钢板未发现裂纹。
[0061]
表3:q550d
‑
zm化学成份
[0062][0063]
本发明避免第1炉水温低、过热度高、拉速低等不利因素影响,最大限度降低夹杂物进入钢水,减少裂纹源;采用弱冷有利于降低弯月面冷却强度,使初生坯壳传热慢、收缩小,冷却均匀,降低裂纹发生的几率。连铸板坯裂纹缺陷的发生率由13.2%降低到0.8%,明显地减少了生产损失,提高了产品质量合格率和市场占有率。
[0064]
以上所述的实施例仅是对本发明的优选方式进行描述,并非对本发明的范围进行限定,在不脱离本发明设计精神的前提下,本领域普通技术人员对本发明的技术方案做出的各种变形和改进,均应落入本发明权利要求书确定的保护范围内。
再多了解一些
本文用于企业家、创业者技术爱好者查询,结果仅供参考。