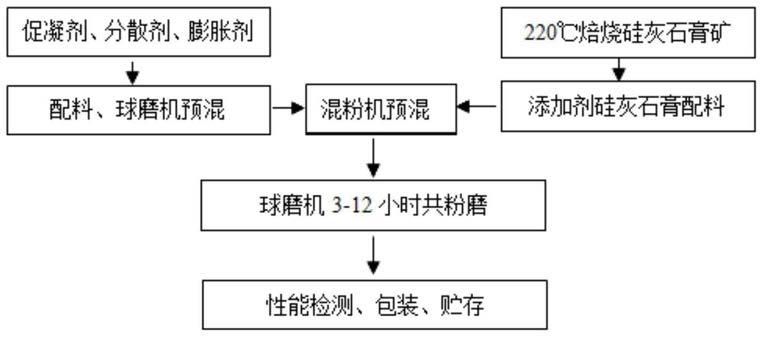
1.本发明属于陶瓷复合材料的制备方法,特别涉及一种采用伴生叶蜡石矿物的硅灰石膏为原料的铝合金精密铸造用铸型材料的制备方法。
背景技术:
2.随着现代材料制造业等领域的快速发展,石膏资源和质量越来越受关注,特别是优质石膏资源面临枯竭的状况,使得铸造用石膏材料的原料面临困境。硅灰石膏属低温热液产物,化学式caco3·
casio3·
caso4·
14h2o,六方柱形貌,常与含水的钙硅酸盐矿物共生,属矿山尾矿。面向未来的长远发展,开发新型的高性能强韧性的新型铸型材料,不能再以优质的石膏、硅灰石和滑石等天然矿产为原料生产。石膏型材料属于多矿物集合的新型复合材料,科学地选择适宜的矿山尾矿资源进行研究制备,能获得更加优异性能的复合材料,是当前国际前沿研究的潜一种在趋势,一些功能与结构一体化的新型材料,如多矿物集合相材料结构材料等,因其优异的性能可设计性和卓越的强韧性而吸引了国外诸多学者的研究。铸型材料要求的理论组成可由几种国内废弃的低质量矿产资源经科学配料后达到成分组成的精确相近,实现cao、mgo、al2o3、sio2、fe2o3和tio2成分的有效控制,控制材料的主次矿物的形成,制备出优质的铸型材料。目前尚未有直接生产方法的报道。
技术实现要素:
3.针对现有技术的不足,本发明提供了一种采用伴生叶蜡石矿物的硅灰石膏为原料的铝合金精密铸造用铸型材料的制备方法,该方法采用伴生叶蜡石矿物的硅灰石膏为原料的铝合金精密铸造用铸型材料,第一步是采用顽火辉石尾矿微粉(或镁橄榄石尾矿粉)、滑石微粉和硅石微粉分别形成铸型材料的促凝剂、分散剂和膨胀剂,在大型球磨机混磨工艺条件下,形成添加剂;第二步采用的天然用含有伴生叶蜡石的天然硅灰石膏,经煅烧形成主矿物相;第三步是采用大型球磨机在要求的运行转速和球磨时间进行混磨处理,采用不同的添加比例调整材料的强韧性,制备铝合金精密铸造用硅灰石膏铸型材料。
4.本发明提出一种用于铝合金精密铸造的具有多矿物集合相的高强韧性结构的铸型材料和制备这类复合材料的新方法。这类材料是在多矿物集合体基体的结构上,在凝固过程中形成大量的链状硅酸盐多晶体相,实现材料的功能。不同比例平衡状态下的氧化铝、氧化镁、氧化硅和氧化钙组元使得材料在烘干工艺环节形成矿物交叉簇生使得晶粒细化,晶粒细化起到强化材料的作用,大幅度提高材料的强韧性。这类复合材料兼具优良的车削性能、体积稳定性和抗热振稳定性,可以稳定的应用于850℃以下的温度范围内,在航空、航天和交通材料领域需求的高精密铝合金铸造具有广阔的应用前景,其优异的数控加工性能使得材料具有高的光洁度和精度,在要求快速铸型的精密铸件铸造中具有重要的应用价值。
5.为实现上述目的,针对铝合金精密铸造铸型材料的发展要求,以满足快速铸型和
精密铸件的要求为目标,以天然矿产资源综合利用为手段实现成本控制,提出一种具有高强韧性、体积安定性和优良的热振稳定性的铸型材料制备方法,该方法通过培烧预处理伴生叶蜡石矿物的硅灰石膏形成主矿物相,预混后的添加剂为辅料,在大型球磨机中混磨得到铝合金精密铸造用铸型材料。所述添加剂为促凝剂、分散剂和膨胀剂的混合。所述添加剂加入量为25~50%,伴生叶蜡石的硅灰石膏加入量为40~85%。
6.所述伴生叶蜡石矿物的硅灰石膏是多种硅酸盐矿物的集合相,主矿物相是含有钙的化合物、以及其它少量镁质矿物相,具有六方针状晶型,其中硅灰石膏中cao含量为16~27%,so3不小于8%,co2的含量不小于5%。
7.所述混磨时间为3~12小时,球磨机转速控制在12~95转/分钟。
8.所述促凝剂为顽火辉石尾矿微粉或镁橄榄石尾矿粉,所述顽火辉石尾矿微粉含有质量分数6-27%的活性mgo。
9.所述分散剂为滑石微粉,滑石微粉为含有质量分数12-23%al2o3的纳米级滑石微粉,膨胀剂为硅石微粉,硅石微粉为sio2含量大于99%的火成岩硅石粉体。
10.所述培烧预处理的温度为220℃,处理时间为2小时。
11.所述促凝剂、分散剂和膨胀剂的质量比为1:0.2~0.4:0.1~0.3。
12.添加剂的制备具体工艺如下:
13.以铸型材料工艺制备添加剂为例进行说明,采用伴生叶蜡石矿物的硅灰石膏为原料的铝合金精密铸造用铸型材料工艺流程如图1。原料中,采用顽火辉石尾矿微粉(或者镁橄榄石尾矿粉)做促凝剂、采用滑石微粉做分散剂和采用硅石微粉做膨胀剂形成添加剂,主要成份分别为含有活性mgo的纳米级天然顽火辉石粉体,平均粒径d
50
=0.32μm;含有al2o3的纳米级滑石微粉,平均粒径d
50
=1.46μm;含有sio2的火成岩硅石粉体,平均粒径d
50
=5.92μm;这些添加剂形成原料在大型球磨机中混磨45min混合均匀,混合的比例范围为1:0.2~0.4:0.1-0.3。混磨后即为添加剂,储存于密闭的添加剂原料仓中备用。
14.伴生叶蜡石的天然硅灰石膏的制备具体工艺如下:
15.伴生叶蜡石的天然硅灰石膏采用山西交口天然硅灰石膏矿石为原料,这些原料由于伴生大量的叶蜡石、镁橄榄石、石英等矿物,应用受限,大部分属于矿山尾矿,不同矿点的矿物原料的化学成分,al2o3、sio2、cao和mgo等氧化物的含量也有差异。将约不大于5-30cm块状矿物原料经拣选分级后置于焙烧窑中,在220℃焙烧预处理,获得伴生叶蜡石的天然硅灰石膏。焙烧预处理后的硅灰石膏在大型球磨机中球磨1-3小时,测得平均粒径d
50
=12.73μm,即形成主矿物相,储存于密闭的原料仓中备用。
16.配料与混磨制备伴生叶蜡石的硅灰石膏铸型材料的具体工艺如下:
17.配料中,添加剂加入量的加入质量分数是25~50%,伴生叶蜡石的硅灰石膏加入量是40~85%,采用电子配料车按照比例进行配料,每个电子配料车的按照3吨的总重量进行操作。
18.配料后通过混粉机预混合,预混后的添加剂与硅灰石膏在大型球磨机中共粉磨3~12小时,达到混均和磨细的作用,控制平均粒径在1~15μm范围内。粉磨后形成铸型材料,装入带有塑料袋的袋中密封储存备用。
19.本发明有益效果:
20.本发明得到的铸型材料适用于铝合金精密铸造,铸型材料主晶相是硅灰石膏,次
晶相以叶蜡石、蒙脱石和石英,同时含有少量滑石、顽火辉石(镁橄榄石)、硅灰石等相。具有好的体积安定性、优良的抗热振稳定性和机械加工性能以及加工过后高的表面光洁度,满足铸造要求的退让性和溃散性,适合大型和超异性精密铸件对铸型材料的要求。
附图说明
21.下面结合附图及实施方式对本发明作进一步详细的说明:
22.图1:伴生叶蜡石矿物的硅灰石膏铸型材料工艺流程图。
具体实施方式
23.下面结合具体实施例对本发明进行进一步描述,但本发明的保护范围不受实施例的限制,如果该领域的技术熟练人员根据上述发明内容对本发明做出一些非本质的改进和调整,仍属于本发明的保护范围。
24.本发明公开了一种用于铝合金精密铸造采用伴生叶蜡石矿物的硅灰石膏为原料的铸型材料的制备方法,具体制备工艺如图1所示,其步骤为将促凝剂、分散剂和膨胀剂预混磨形成添加剂,它们分别由活性mgo的纳米级天然顽火辉石尾矿粉体(或镁橄榄石尾矿粉)、含有al2o3的纳米级滑石微粉和火成岩硅石粉体组成。以山西交口的伴生叶蜡石的天然硅灰石膏矿石为原料,选择5~30cm块状矿石置于焙烧窑中在220℃焙烧预处理,得到伴生叶蜡石的天然硅灰石膏块,在大型球磨机中球磨1~3小时,得到伴生叶蜡石的天然硅灰石膏粉。按照比例配料,将添加剂和硅灰石膏粉共粉磨即制备获得硅灰石膏铸型材料。
25.实施例1
26.硅灰石膏铸型材料(高强韧型)
27.步骤一:添加剂的制备
28.采用顽火辉石尾矿微粉(或镁橄榄石尾矿粉)做促凝剂、采用滑石微粉做分散剂和采用硅石微粉做膨胀剂,主要成份分别为含有活性mgo的纳米级天然顽火辉石粉体,平均粒径d
50
=7.32μm;含有al2o3的纳米级滑石微粉,平均粒径d
50
=1.46μm;含有sio2的火成岩硅石粉体,平均粒径d
50
=5.92μm;配料比例范围为1:0.3:0.15,在大型球磨机中混磨45min混合均匀,形成添加剂。
29.步骤二:伴生叶蜡石的天然硅灰石膏的制备
30.伴生叶蜡石的天然硅灰石膏采用山西交口天然硅灰石膏矿石为原料,矿点选择在河北交口符山。选择5~30cm块状矿石置于焙烧窑中在220℃焙烧预处理,获得伴生叶蜡石的天然硅灰石膏。焙烧预处理后的硅灰石膏在大型球磨机中球磨2小时,平均粒径d
50
=12.73μm,形成伴生叶蜡石的天然硅灰石膏粉。
31.步骤三:硅灰石膏铸型材料的制备
32.添加剂加入量的加入质量分数45%,伴生叶蜡石的硅灰石膏粉加入量55%,配料后通过混粉机预混合后在大型球磨机中共粉磨3小时,达到平均粒径在1~15μm范围内,形成硅灰石膏铸型材料。
33.实验表明,伴生叶蜡石的天然硅灰石膏铸型材料110℃烘干后的耐压强度为4.3mpa,35cm正方体230℃快速烘干后无裂纹、耐压强度为3.9mpa。
34.实施例2
35.硅灰石膏铸型材料(高热振稳定性型)
36.步骤一:添加剂的制备
37.采用与实施例1相同的方法制备,与实施例1不同的是,添加剂的组成中外加了5%的镁橄榄石尾矿微粉,镁橄榄石尾矿微粉的mgo含量约为27%。步骤二:伴生叶蜡石的天然硅灰石膏的制备
38.采用与实施例1相同的方法进行伴生叶蜡石的天然硅灰石膏的制备。
39.步骤三:硅灰石膏铸型材料的制备
40.采用与实施例1相同的方法进行硅灰石膏铸型材料的制备。
41.实验表明,伴生叶蜡石的天然硅灰石膏铸型材料110℃烘干后的耐压强度为4.1mpa,35cm正方体480℃烘干后无裂纹、耐压强度为3.3mpa。与例1比较,强度略有降低,热振稳定性大幅度提高。
再多了解一些
本文用于企业家、创业者技术爱好者查询,结果仅供参考。