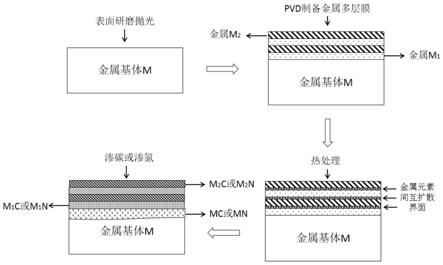
1.本发明属于金属材料表面处理方法技术领域,具体涉及利用化学热处理在金属表面制备陶瓷多层膜的方法。
背景技术:
2.过渡金属材料应用范围的日益增加对其表面强度、硬度和耐磨性的要求不断提高。例如,对用于搅拌摩擦焊的钨基合金,提高其表面的强度、硬度以及耐磨性不但能够延长设备零件的使用寿命,而且有利于提升焊接质量。在过渡金属表面制备陶瓷/陶瓷多层膜是提高其表面强度、硬度和耐磨性的有效手段之一,即在过渡金属表面交替制备两种陶瓷层,利用两种陶瓷相自身的高硬度和陶瓷层的层状排列实现强度、硬度和耐磨性的提高。
3.目前,陶瓷/陶瓷多层膜的制备方法主要包括物理气相沉积和化学气相沉积。物理气相沉积使用两种靶材(如ti靶和cr靶)轮流工作产生沉积粒子,并使沉积粒子与气氛反应,在表面交替地生成两种靶材对应的陶瓷层(如tin层和crn层)。化学气相沉积则是通过交替通入不同气体,使之反应并在金属表面生成陶瓷层。
4.然而,对于上述两类方法,由于沉积物质采用轮流供给的方式,通过气相沉积制备的陶瓷/陶瓷多层膜的层间界面存在物相突变,缺乏元素扩散,缺乏冶金结合,界面残余应力较大,层间结合强度较低。同时,多层膜和基体之间存在陶瓷相与金属相形成的尖锐界面,物相晶体学性质差异大,膜基界面结合强度低。因此,在使用过程中,外力作用易导致表面膜层的整体脱落。可见,膜基界面和层间界面缺乏冶金结合的问题制约了陶瓷/陶瓷多层膜力学性能的进一步提升。
技术实现要素:
5.本发明提供利用化学热处理在金属表面制备陶瓷多层膜的方法,解决了目前陶瓷/陶瓷多层膜的层间界面和膜基界面缺少元素互扩散,难以实现冶金结合的问题,显著提升了多层膜的界面结合强度,进而提高了多层膜的综合力学性能。
6.本发明是利用化学热处理在金属表面制备陶瓷多层膜的方法,具体包括以下步骤:
7.步骤1:将需要表面强化的金属基体表面进行预处理,并利用物理气相沉积方法制备具有碳化物或氮化物形成能力的金属/金属多层膜;
8.步骤2:将步骤1获得的试样进行高温热处理;
9.步骤3:将步骤2获得的试样进行化学热处理,,使步骤1中沉积的金属层和基体表层转变为碳化物层或氮化物层,从而获得陶瓷/陶瓷多层膜。
10.本发明的特点还在于:
11.所述化学热处理包括渗氮处理和渗碳处理;渗碳过程中,应使渗碳深度超过步骤1中制备的金属/金属多层膜的总厚度,使陶瓷层/金属层界面位于金属基体表层;
12.渗碳处理或渗氮处理温度需高于900摄氏度且低于金属/金属多层膜和金属基体
的熔点;渗碳处理或渗氮处理时间取决于渗碳温度和多层膜厚度,最终应使陶瓷层厚度大于步骤1中沉积的金属/金属多层膜的厚度,即膜基界面位于金属基体表面以内。
13.物理气相沉积方法包括真空蒸镀、溅射镀膜、离子镀等任意可以沉积具有碳化物形成能力的金属的物理气相沉积方法。步骤1中所述的需要表面强化的金属基体包括ti、zr、nb、ta、mo、w、cr中的一种元素形成的纯金属或以其为主要化学成分的合金。
14.步骤1中所述的具有碳化物形成能力的金属包括ti、zr、v、nb、ta、mo、w、cr、hf中的一种元素形成的纯金属或以之为主要化学成分的合金;具有氮化物形成能力的金属为ti、zr、hf、v、nb、ta、cr、mo、w中任意一种元素形成的纯金属或以之为主要化学成分的合金。
15.步骤1中所述的表面预处理是指用砂纸研磨并抛光,再分别用丙酮、酒精和超声波清洗,以去除表面污染物并降低表面粗糙度,保证沉积薄膜的质量。
16.步骤1中所述的所述金属/金属多层膜是两种不同的金属形成的多层膜,其中一种可与金属基体材料相同,金属/金属多层膜层数范围是2
‑
30层,总厚度范围是5
‑
30微米。
17.步骤2中所述热处理的目的是促进金属/金属多层膜层间界面的金属元素互扩散;热处理温度范围为900
‑
2000摄氏度,热处理时间为0.5
‑
48h,热处理后试样随炉冷却至室温。
18.步骤3中所述渗碳处理包括固体渗碳、气体渗碳、间隙原子渗碳;渗氮处理可以选择固体渗氮、气体渗氮、离子渗氮;渗碳或渗氮过程中可通过抽真空或通入惰性气体防止氧化。
19.渗碳方法选择间隙原子渗碳,所述间隙原子渗碳方法的具体步骤为:
20.首先,选用含碳量范围为1.0
‑
4.0wt.%高碳钢或铸铁作为固体碳源;将固体碳源的其中一个表面打磨、抛光;然后,将固体碳源放置于制备了多层膜的金属基体之上,使多层膜表面和固体碳源的抛光表面相接触,将其放置在热压炉中,然后施加垂直于多层膜表面的压力2
‑
30mpa,在真空或惰性气体环境中加热至900
‑
1150摄氏度后保温,最后冷却至室温。
21.本发明的有益效果在于:
22.(1)本发明先制备金属/金属多层膜,并利用高温热处理促进金属层间的元素互扩散,使层间界面实现冶金结合,显著提高多层膜界面结合强度和综合力学性能。
23.(2)本发明通过渗碳处理或渗氮处理渗碳处理或渗氮处理处理将金属/金属多层膜改性为陶瓷/陶瓷多层膜,使陶瓷相原位析出。这一过程中不产生孔洞,晶界结合力高。且陶瓷相在层间界面的互扩散区析出时界面粗糙度较大,甚至形成两相混合区。与直接采用物理气相沉积方法制备陶瓷/陶瓷多层膜相比,解决了物相突变和成分突变造成的层间界面结合强度低的问题。
24.(3)本发明要求渗层超过金属/金属多层膜的厚度,即陶瓷层向内生长至金属基体表层。膜基界面(陶瓷/金属界面)在金属基体表层内而并非金属基体的初始表面。因此,膜基界面不受物理气相沉积工艺和层间元素互扩散程度的影响。膜基界面由基体金属及其碳化物或氮化物陶瓷构成,膜基界面结合强度高。
附图说明
25.图1为利用化学热处理在金属表面制备陶瓷多层膜的方法流程示意图。
具体实施方式:
26.下面结合具体实施方式对本发明进行详细说明。
27.本发明利用化学热处理在金属表面制备陶瓷多层膜的方法,如图1所示,图中m代表基体金属,m1和m2代表步骤1中沉积的两种金属。mc、m1c、m2c是金属m、m1和m2的碳化物,mn、m1n、m2n是金属m、m1和m2的氮化物。
28.具体包括以下步骤:
29.步骤1:将需要表面强化的金属基体表面进行预处理,并利用物理气相沉积方法制备具有碳化物或氮化物形成能力的金属/金属多层膜;
30.步骤1.1:针对具有碳(氮)化物形成能力且需要表面强化的金属,对其表面砂纸研磨并抛光,再分别用丙酮、酒精和超声波清洗,以保证沉积薄膜的质量;
31.优选地,需要表面强化的金属包括ti、zr、nb、ta、mo、w、cr中的一种元素形成的纯金属或以其为主要化学成分的合金(如ti6al4v、93w
‑
ni等);
32.步骤1.2:利用物理气相沉积镀膜,通过控制工艺参数,在基体上交替地沉积两种金属层,形成金属/金属多层膜。可沉积的金属包括ti、zr、v、nb、ta、mo、w、cr、hf中的一种元素形成的纯金属或以其为主要化学成分的合金。
33.优选地,物理气相沉积采用磁控溅射、阴极弧离子镀。
34.步骤2:将制备了多层膜的试样进行高温热处理,热处理温度范围为900
‑
2000摄氏度,热处理后试样随炉冷却至室温。
35.优选地,热处理时间为0.5
‑
48h。
36.步骤3:对其进行渗碳或渗氮处理,随着碳(或氮)原子向内扩散并与金属反应形成碳化物(或氮化物),将金属/金属多层膜改性成为碳化物(或氮化物)/碳化物(或氮化物)多层膜。渗碳或渗碳温度应高于900摄氏度且低于多层膜金属和金属基体的熔点。渗碳处理或渗氮处理渗碳处理或渗氮处理时间取决于渗碳温度和多层膜厚度,最终应使陶瓷层厚度大于步骤1中沉积的金属/金属多层膜的厚度,即膜基界面位于金属基体表面以内。渗碳处理或渗氮处理渗碳处理或渗氮处理后材料随炉冷却至室温。
37.优选地,渗碳方法选择固体渗碳,气体渗碳,渗氮方法选择固体渗氮、气体渗氮。渗碳处理或渗氮处理渗碳处理或渗氮处理温度范围为1000摄氏度至2000摄氏度。
38.更为优选的,渗碳方法选择间隙原子渗碳。首先,选用含碳量范围为1.0
‑
4.0wt.%高碳钢或铸铁作为固体碳源。将固体碳源的其中一个表面打磨、抛光。然后,将固体碳源放置于制备了多层膜的金属基体之上,使多层膜表面和固体碳源的抛光表面相接触,将其放置在热压炉中,然后施加垂直于多层膜表面的压力2
‑
30mpa,在真空或惰性气体环境,如氩气,中加热至一定温度900
‑
1150摄氏度后保温,最后冷却至室温。
39.实施例1:
40.本实例包括以下步骤:
41.步骤1:将需要表面强化的金属钨(w)基体表面进行预处理,并利用磁控溅射方法制备具有铌(nb)/钽(ta)多层膜。
42.步骤1.1:准备一块金属钨(w)板,其纯度为99.9wt.%,对钨板加以表面处理,砂纸研磨并抛光,再分别用丙酮、酒精在超声波中清洗。
43.步骤1.2:利用磁控溅射方法在金属钨基体上交替地沉积铌(nb)和钽(ta)金属层,
形成nb/ta多层膜,共30层,总厚度30微米。
44.步骤2:将制备了多层膜的试样进行高温热处理,热处理温度为2000摄氏度,热处理保温时间为0.5小时,热处理后试样随炉冷却至室温。
45.步骤3:采用固体渗碳对其进行渗碳处理,将试样埋在渗碳剂(90wt%的炭黑粉末和10wt%的碳酸钠粉末)中放在渗碳罐里并通入氩气,随后将渗碳罐密封并放置于高温热处理炉子中。随着温度升高,碳原子向内扩散并与金属钽、铌反应形成nbc层,tac层,将nb/ta多层膜改性成为tac/nbc多层膜。渗碳温度为2000摄氏度。渗碳时间取决于渗碳温度和多层膜厚度,最终使渗碳层厚度为35微米,(大于ta/nb多层膜的厚度30微米),即膜基界面位于金属钨基体表面以内,形成wc/w膜基界面。渗碳后试样随炉冷却至室温。
46.通过上述方法,得到的多层膜具体以下特征:1)各陶瓷层致密无孔;2)碳化物体积分数高(80%
‑
95%);3)表面硬度可达2500hv;4)多层膜的层间界面结合力大于50n;5)多层膜与金属基体结合力大于100n;6)大幅度提高了钨基体的表面耐磨性能(比基体的耐磨性提高50倍以上)。
47.实施例2:
48.本实例包括以下步骤:
49.步骤1:将需要表面强化的钛合金(ti6al4v)板表面进行预处理,并利用阴极弧离子镀方法制备具有钨(w)/钽(ta)多层膜。
50.步骤1.1:准备一块钛合金(ti6al4v)板,对钛合金板加以表面处理,砂纸研磨并抛光,再分别用丙酮、酒精在超声波中清洗。
51.步骤1.2:利用阴极弧离子镀方法在钛合金基体上交替地沉积钨(w)和钽(ta)金属层,形成w/ta多层膜,共2层,总厚度5微米。
52.步骤2:将制备了多层膜的试样进行高温热处理,热处理温度为900摄氏度,热处理保温时间为48小时,热处理后试样随炉冷却至室温。
53.步骤3:采用间隙原子渗碳对其进行渗碳处理。首先,选择含碳量为4.0wt.%的铸铁作为固体碳源。将固体碳源的其中一个表面打磨、抛光。然后,将铸铁放置于制备了w/ta多层膜的钛合金之上,使多层膜表面与铸铁的抛光表面相接触,将其放置在热压炉中,然后施加垂直于多层膜表面的压力(30mpa),在氩气环境中加热至900摄氏度后保温,使钨层和钽层都转变为碳化物陶瓷层,且钛合金表层形成碳化钛/钛合金膜基界面。随后将试样冷却至室温。
54.通过上述方法,得到的多层膜具体以下特征:1)各陶瓷层致密无孔;2)碳化物体积分数高(约100%);3)表面硬度可达1800hv;4)多层膜的层间界面结合力大于40n;5)多层膜与金属基体结合力大于100n;6)大幅度提高了ti6al4v金属基体的表面耐磨性能(比基体的耐磨性提高30倍以上)。
55.实施例3:
56.本实例包括以下步骤:
57.步骤1:将需要表面强化的金属钼(mo)基体表面进行预处理,并利用阴极弧离子镀方法制备具有钼(mo)/锆(zr)多层膜。
58.步骤1.1:准备一块钼(mo)板,对钼板加以表面处理,砂纸研磨并抛光,再分别用丙酮、酒精在超声波中清洗。
59.步骤1.2:利用阴极弧离子镀方法在钼基体上交替地沉积钼(mo)和锆(zr)金属层,形成mo/zr多层膜,共15层,总厚度15微米。
60.步骤2:将制备了多层膜的试样进行高温热处理,热处理温度为1500摄氏度,热处理保温时间为24小时,热处理后试样随炉冷却至室温。
61.步骤3:采用间隙原子渗碳对其进行渗碳处理。首先,选择含碳量为1.0wt.%的高碳钢作为固体碳源。将高碳钢的其中一个表面打磨、抛光。然后,将高碳钢放置于制备了mo/zr多层膜的钼基体之上,使多层膜表面和高碳钢的抛光表面相接触,将其放置在热压炉中,然后施加垂直于多层膜表面的压力(2mpa),在氩气环境中加热至1150摄氏度后保温,使钼层和锆层分别转变为mo2c和zrc陶瓷层,且钼基体表层形成mo2c/mo膜基界面。随后将试样冷却至室温。
62.通过上述方法,得到的多层膜具体以下特征:1)各陶瓷层致密无孔;2)碳化物体积分数接近100%;3)表面硬度可达2400hv;4)多层膜的层间界面结合力大于40n;5)多层膜与金属基体结合力大于120n;6)大幅度提高了钼金属基体的表面耐磨性能(比基体的耐磨性提高60倍以上)。
63.实施例4:
64.本实例包括以下步骤:
65.步骤1:将需要表面强化的金属钽(ta)基体表面进行预处理,并利用磁控溅射离子镀方法制备具有钛(ti)/钒(v)多层膜。
66.步骤1.1:准备一块钽(ta)板,其纯度为99.9wt.%,对钽板加以表面处理,砂纸研磨并抛光,再分别用丙酮、酒精在超声波中清洗。
67.步骤1.2:利用磁控溅射离子镀方法在金属钨基体上交替地沉积钛(ti)和钒(v)金属层,形成ti/v多层膜,共20层,总厚度10微米。
68.步骤2:将制备了多层膜的试样进行高温热处理,热处理温度为1200摄氏度,热处理保温时间为12小时,热处理后试样随炉冷却至室温。
69.步骤3:采用气体渗碳对其进行渗碳处理,将甲烷气体通入渗碳炉中,设定渗碳温度为1000摄氏度。渗碳使ti/v多层膜转变为tic/vc陶瓷多层膜,且最终使渗碳层厚度为12微米(大于多层膜的厚度(10微米)),即膜基界面位于金属钽基体表面以内,形成tac/ta膜基界面。渗碳后试样随炉冷却至室温。
70.通过上述方法,得到的多层膜具体以下特征:1)各陶瓷层致密无孔;2)碳化物体积分数高(85%
‑
95%);3)表面硬度可达2300hv;4)多层膜的层间界面结合力大于60n;5)多层膜与金属基体结合力大于120n;6)大幅度提高了钽金属基体的表面耐磨性能(比基体的耐磨性提高60倍以上)。
71.实施例5:
72.本实例包括以下步骤:
73.步骤1:将需要表面强化的金属锆(zr)基体表面进行预处理,并利用磁控溅射离子镀方法制备具有钛(ti)/钼(mo)多层膜。
74.步骤1.1:准备一块锆(zr)板,其纯度为99.9wt.%,对锆板加以表面处理,砂纸研磨并抛光,再分别用丙酮、酒精在超声波中清洗。
75.步骤1.2:利用磁控溅射离子镀方法在金属钨基体上交替地沉积钛(ti)和钼(mo)
金属层,形成ti/mo多层膜,共10层,总厚度20微米。
76.步骤3:将制备了多层膜的试样进行高温热处理,热处理温度为1800摄氏度,热处理保温时间为15小时,热处理后试样随炉冷却至室温。
77.步骤4:采用气体渗氮对其进行渗氮处理,将氨气通入渗氮炉中,设定渗碳温度为1100摄氏度。渗氮使ti/mo多层膜转变为tin/mon陶瓷多层膜,且最终使渗氮层厚度为24微米,(大于多层膜的厚度(20微米)),即膜基界面位于金属zr基体表面以内,形成zrn/zr膜基界面。渗碳后试样随炉冷却至室温。
78.通过上述方法,得到的多层膜具体以下特征:1)各陶瓷层致密无孔;2)氮化物体积分数高(80%
‑
100%);3)表面硬度可达2400hv;4)多层膜的层间界面结合力大于70n;5)多层膜与金属基体结合力大于130n;6)大幅度提高了锆金属基体的表面耐磨性能(比基体的耐磨性提高50倍以上)。
再多了解一些
本文用于企业家、创业者技术爱好者查询,结果仅供参考。