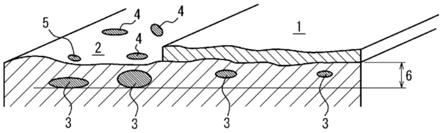
1.本发明涉及用于变压器及其他电气设备的铁芯等的方向性电磁钢板,涉及形成于这样的方向性电磁钢板表面的绝缘被膜及其有利的形成方法。
背景技术:
2.在方向性电磁钢板的制造工序中,一般将钢坯热轧后实施冷轧,然后实施脱碳退火后,为了二次再结晶进行成品退火。在这些工序中,在成品退火中发生二次再结晶,生成易磁化轴在轧制方向上对齐的巨大晶粒。
3.成品退火的作用除了二次再结晶之外,还有通过退火分离剂中的mgo与以脱碳退火中形成的sio2为主体的氧化层反应而形成镁橄榄石被膜、通过纯化除去杂质等各种作用。
4.镁橄榄石被膜在成品退火中的高温时形成,因此之后冷却到常温时,由于被膜与基铁的热膨胀率之差而对基铁赋予张力。
5.被赋予张力的基铁由于磁弹性效果而自旋在一定方向上对齐,静磁能增大。其结果是细化磁畴,减少具有这样的基铁的钢板的铁损。另一方面,镁橄榄石被膜的密合性差,或者镁橄榄石被膜的形成不足的钢板不易涂覆成品退火后涂覆的绝缘涂层,或者镁橄榄石被膜部分地剥落,因此绝缘性、防锈性劣化。因此,镁橄榄石被膜的质量好坏成为左右方向性电磁钢板的磁特性、被膜特性的重要因素。
6.因此,为了改善被膜的质量以往公开了各种方法。例如,在专利文献1中公开了使用如下退火分离剂的方法,上述退火分离剂是在平均粒径0.3~3μm的mgo中配合1种或2种以上的添加剂且根据添加剂在0.03~15μm的范围内调整该添加剂的平均粒径而得的。
7.在专利文献2中公开了使用如下退火分离剂添加物的方法,上述退火分离剂添加物在将平均粒径设为d(μm)、将bet比表面积设为s(m2/g)、将真密度设为ρ(g/cm3)时满足式:1.1≤ρsd/6≤4。
8.在专利文献3中公开了通过使二次再结晶退火时形成的被膜由镁橄榄石被膜与含有al、si的氧化物构成来提高张力效果、改善磁特性的方法。
9.在专利文献4中公开了通过规定形成镁橄榄石绝缘被膜的镁橄榄石粒子的粒径来形成均匀被膜的方法。
10.现有技术文献
11.专利文献
12.专利文献1:日本特开平9-249916号公报
13.专利文献2:日本特开2003-213337号公报
14.专利文献3:日本特开平6-17261号公报
15.专利文献4:日本特开昭53-5800号公报
技术实现要素:
16.然而,在专利文献1所记载的方法中,虽然整体上被膜的质量有所改善,但是存在即使在该文献1的发明范围内收纳平均粒径也有时不能得到所期望的被膜特性的问题。另外,专利文献2所记载的方法也同样地存在如下问题:即使规定添加剂的平均粒度,由于其粉体粒度的波动,也未必能够得到所期望的被膜特性。
17.进而,专利文献3所记载的方法存在如下问题:在对钢板施加外力时,在镁橄榄石被膜与包含al、si的氧化物的界面产生龟裂从而被膜劣化。另外,在专利文献4所记载的方法中,如果仅将镁橄榄石粒径收纳于规定范围内,则效果是有限的,很难说能够得到充分的被膜改善效果。
18.因此,本发明人等在专利文献5中提出了如下方法作为解决这些问题的方法:镁橄榄石膜部分进入基铁内部而形成固定部,在通过钢板的弯曲试验使被膜剥离时规定基铁表面上的被膜残留部的面积率。
19.专利文献5:日本特开平10-152780号公报
20.由此,虽然被膜密合性得到了改善,但是在磁特性上没有看到充分的改善效果。特别是磁通密度高但磁滞损耗没有有效地减少,作为结果,有铁损稍微提高的倾向。
21.如上所述,虽然通过各种技术,在一定程度上分别提高了被膜特性、磁特性,但是很难说得到了充分的效果。特别是从脱碳退火到成品退火,由于工序条件的微妙变动而在磁特性、被膜特性上容易产生问题。因此,非常需要改善从脱碳退火到成品退火形成的被膜质量。
22.本发明是鉴于上述情况而进行的,其目的在于提出具有有助于钢板的磁特性、特别是减少铁损且密合性良好的被膜的方向性电磁钢板,以及有利于得到这样的被膜的方法。
23.本发明的要旨构成如下。
24.1.一种方向性电磁钢板,其特征在于,具有形成于钢板的基铁表面的绝缘被膜,具有上述绝缘被膜部分进入上述基铁内部的固定部,上述固定部位于距离上述基铁表面的深度为3.5μm以下的范围,在将上述方向性电磁钢板通过弯曲试验使上述绝缘被膜从上述基铁剥离时的上述基铁表面上的上述绝缘被膜的残留部设为颈部时,对于该颈部,面积5μm2以下的个数为0.06个/μm2以下以及面积10~40μm2的个数为0.005个/μm2~0.011个/μm2以下。
25.2.一种方向性电磁钢板的制造方法,其特征在于,是制造上述1所记载的方向性电磁钢板的方法,在对含有2~4质量%的si的钢进行热轧,实施1次或包括中间退火的多次冷轧,加工成最终板厚后进行一次再结晶退火,然后涂覆退火分离剂后进行成品退火,然后除去该退火分离剂,施加绝缘涂层并进行平坦化退火的一系列方向性电磁钢板的制造方法中,
26.以涂覆量a(g/m2)涂覆退火分离剂时,上述退火分离剂对水的溶解度为3g/l以下,含有浓度c(质量%)的具有累积50%粒径d(μm)的4倍以上粒径的粒子的体积分率为r(vol%)和粒度的标准偏差为sd(μm)的添加剂,上述累积50%粒径d、体积分率r、粒度的标准偏差sd、浓度c和涂覆量a满足以下各式
27.d≥1.8,
28.sd≤0.6
·
d,
29.0.15≤(a
·
c
·
r)/d3≤20。
30.3.根据上述2所记载的方向性电磁钢板的制造方法,其特征在于,将上述退火分离剂的主剂设为mgo。
31.4.根据上述2所记载的方向性电磁钢板的制造方法,其特征在于,将上述退火分离剂的主剂设为非反应性氧化物,将上述成品退火后的钢板表面的氧单位面积重量设为0.1g/m2以下。
32.5.根据上述3所记载的方向性电磁钢板的制造方法,其特征在于,使上述退火分离剂中含有1~20质量%的卤素,将上述成品退火后的钢板表面的氧单位面积重量设为0.1g/m2以下。
33.6.根据上述2~5中任一项所记载的方向性电磁钢板的制造方法,其特征在于,在加工成上述最终板厚的最终冷轧后且成品退火前的任一阶段中,将钢板表面的平均粗糙度sa调整为0.3μm以下,将最大谷深度sv调整为2μm~5μm。
34.7.根据上述2~6中任一项所记载的方向性电磁钢板的制造方法,其特征在于,上述成品退火包括在800~950℃的范围保持20~100小时的处理。
35.根据本发明,容易制造磁特性和被膜密合性良好的方向性电磁钢板,能够很有助于提高钢板的生产率和质量。
附图说明
36.图1是方向性电磁钢板的表层部的示意图。
37.图2的(a)和(b)是表示添加剂的粒度分布的图。
38.图3的(a)和(b)是表示变更添加剂的粒度分布时的通过弯曲试验使被膜剥离后的被膜截面的sem像的图。
39.图4的(a)和(b)是表示变更添加剂的粒度分布时的通过弯曲试验使被膜剥离后的钢板表面的sem像的图。
40.图5的(a)和(b)是表示颈部的面积率直方图的图。
具体实施方式
41.发明人等为了进一步改善方向性电磁钢板的被膜特性而进行了各种实验,结果发现如图1所示,成品退火后的方向性电磁钢板的表层部成为如下状态:在基铁2上形成有被膜1,该被膜1部分进入基铁2内部并形成固定部3。而且,也发现在将这样的钢板通过弯曲试验使被膜1从基铁2剥离时,形成露出于基铁2表面的被膜残留部(在本发明中称为“颈部”)4、5。图中,颈部4为粗大的颈部,颈部5为微小的颈部。
42.这里,在本发明中,将形成于基铁表面的被膜称为绝缘被膜(在本发明中也简称为被膜),规定了直接与基铁密合的被膜,但是这样的被膜可以是镁橄榄石被膜,也可以是通过绝缘涂层形成的被膜。应予说明,根据需要,也可以在该绝缘被膜的表面进一步形成具有绝缘功能的被膜,但是这样的不直接与基铁表面相接的绝缘被膜的表面的被膜不需要满足本发明的要件。
43.进而,发明人等新发现:上述颈部中的粗大颈部4的个数分布对被膜密合性有很大
贡献,并且,微小的颈部5对被膜密合性没有贡献,反而成为使磁滞损耗劣化的重要因素,另外,固定部3距离基铁2表面的深度6对被膜密合性不太重要,从磁特性的观点出发,反而固定部3的深度6优选较浅。
44.这里,本发明中的固定部3距离基铁2表面的深度6(在本发明中也称为固定部深度或固定深度)定义为在使用电子显微镜以2000倍在200μm长度的区域内观察被膜截面时,在该区域内固定部的最深部与其正上方的被膜-基铁界面位置最远离的部位(固定部)的分离距离。应予说明,上述被膜截面优选如下地制作:以cu薄膜为隔离物,使截面为表面地埋入树脂模中,使用金刚石研磨。
45.另外,颈部定义为:对于在弯曲试验中从基铁2剥离被膜1而得的面,观察使用电子显微镜得到的反射电子像,在该观察面(基铁2表面)上残留有面积0.1μm2以上的被膜的部分。这是因为残留的被膜部分中面积不足0.1μm2的被膜残留部分对本发明没有特别的影响。进而,本发明中的粗大的颈部定义为面积10~40μm2的基铁表面上的被膜残留部。另外,本发明中的微小的颈部定义为5μm2以下的基铁表面上的被膜残留部。
46.进而,本发明的弯曲试验与通常的弯曲密合性试验(例如参照上述专利文献1、2、4等)相同,是用不同直径的各种圆棒缠绕钢板并目视观察被膜剥离的试验,本次将在被膜剥离中直径最大的具有被膜残留部的样品用于颈部的观察。
47.另外,在弯曲试验后测定颈部面积时,将剥离的部分剪切为sem中的表面观察用,以加速电压5kv、2000倍的倍率拍摄照片,使用图像解析装置(旭化成工程制图像解析软件“a像君”)对该照片进行面积测定。
48.以下,对发现本发明的实验进行叙述。
49.将包含c:0.04质量%(以下,关于钢板成分的质量%仅用%表示)、si:3.3%、al:0.008%、n:0.003%、mn:0.08%和sb:0.02%且剩余部分由fe和不可避免免的杂质构成的电磁钢坯在1300℃下加热30分钟后,进行热轧而制成2.2mm的板厚,然后夹入在1050℃下1分钟的中间退火而进行冷轧,加工成最终板厚0.23mm。然后,对这样的最终板厚的钢板进行脱碳退火后,根据表1所示的各种条件涂覆以mgo为主体且根据表1所示的各种条件配合添加剂(硫酸锶)而得的退火分离剂,然后进行在820℃保持50小时后在1200℃保持5小时的纯化退火作为成品退火。这里,在表1所示的各种条件中,a为退火分离剂的涂覆量(g/m2),c为添加剂的浓度(质量%),r为添加剂中的粗粒的体积分率(vol%),d为添加剂的平均粒径(累积50%粒径:μm)和sd为添加剂粒度的标准偏差:μm)。
50.应予说明,对于表1中的添加剂的粒度分布使用岛津制sald
‑
3100来测定。此时的分散介质为0.2质量%六偏磷酸水溶液,分散使用超声波均化器以300w的输出进行3分钟来测定。以表1的no.1(添加剂无粗粒条件)和no.14(添加剂有粗粒条件)为典型例,将该测定结果示于图2(a)和(b)。
51.对这样得到的纯化退火后的钢板用电子显微镜进行被膜的截面观察。进而,对该纯化退火后的钢板涂覆绝缘涂层,进行烧结进行去应力退火后,调查磁测定和弯曲密合性。应予说明,磁测定使用jis
‑
c2550的方法。
52.被膜的截面观察使用电子显微镜,以2000倍观察200μm长度区域,将在该区域内固定部的最深部与其正上方的被膜-基铁界面位置最远离的部位的分离距离定义为固定部深度,求出其距离。以表1的no.1和no.14为典型例,将该观察面示于图3(a)和(b)。
53.如上所述,弯曲密合性以在钢板上缠绕圆筒而被膜不剥离的最小弯曲直径(mm)来评价。进而,在弯曲试验中对剥离被膜的部分从基铁表面用电子显微镜拍摄反射电子像,对其进行图像解析来求出颈部面积。图像解析中使用的图像如图4(a)和(b)所示,以倍率2000倍解析面积计10000μm2来进行。应予说明,颈部面积的测定方法如上所述。
54.将以上的磁特性和被膜密合性的评价结果示于表1。
55.进而,在表1所示的例子中,作为代表例,对于使用粗粒少的硫酸锶的情况(表1的条件no.1)和使用粗粒多的硫酸锶的情况(表1的条件no.14)的颈部的面积率的直方图,示于图5(a)和(b)。应予说明,图3(a)、图4(a)和图5(a)均为表1的条件no.1的实验结果,图3(b)、图4(b)和图5(b)均为表1的条件no.14的实验结果。
[0056][0057]
由图5可知,对于使用粗粒多的硫酸锶的样品,大多具有大的颈部,另一方面,对于使用粗粒少的硫酸锶的样品,以小的颈部为主,大的颈部少。另外,对于被膜的密合性,粗粒
多的硫酸锶较好。进而,由表1可知,在5μm2以下的小的颈部多的条件、固定部深度深的条件下有铁损劣化的倾向,在平均粒径d小的条件、大的颈部少的条件下发生被膜劣化。
[0058]
由于这样大的颈部的面积率而钢板的被膜密合性改变的理由尚未明确,但是发明人等如下认为。
[0059]
原本,被膜的剥离是通过如下方式而引起的:由于钢板的杨氏模量与被膜的杨氏模量的差异,在对钢板施加弯曲应力时在基铁被膜界面固定部受到剪切应力而被破坏。可知在图4(b)的照片中,在被膜密合性良好的条件下残留有大的颈部,在图4(a)的照片中,在被膜密合性不良的条件下大的颈部的存在频率降低。由此认为,大的颈部与被膜密合性有很大关系,小的颈部不一定对被膜密合性产生影响。另外,从磁特性的观点出发,如果具有凹凸,则妨碍磁畴壁的移动而增加磁滞损耗(wh),因此对密合性影响小的固定部需要尽量减少。进而,在剥离被膜时,固定部被颈部破坏,以该颈部为界从被膜分离,保持原样存在于钢板内部。因此,如果有不去掉整个固定部而刚好破坏颈部的深度,则即使固定部不存在于基铁深处,被膜的密合性也没有实质差异。如果是这样,则果然如果考虑对磁滞损耗的影响,则固定部深度优选尽量减小。
[0060]
具体而言,为了实现如上所述的固定部的形态,在本次实验中添加剂的硫酸锶的粒度有很大影响。对于该理由,认为如下。
[0061]
通常,镁橄榄石被膜的形成是固相反应,因此这样的被膜的形成容易受到反应助剂中的添加剂的粒径的影响。因此,如果添加剂的粒径大,则与钢板的反应性降低,如果粒径小,则与钢板的反应性增大。即,在粒度均匀的粉体中也均匀地形成被膜而成为平坦的膜,另一方面,适当存在相对于平均粒径为粗粒的添加剂,根据与钢板的接触部位而被膜的形成速度不同,钢板与被膜的界面产生凹凸。该凹凸成为形成固定部的原因。
[0062]
如果考虑这样的理由,则通过使粒度分布整体均匀并适当存在粗粒,可以在减少微小的固定部的同时增加具有一定程度大小的固定部。然而,认为被膜的形成速度由添加剂中的粒度的相对大小引起,因此不能用粒度的绝对值表示。
[0063]
因此,本发明人等进行上述实验的详细解析。其结果发现,具有添加剂的平均粒径的4倍以上粒径的粒子作为粗粒对粗大的固定部的形成有强烈的影响。而且,一并发现为此将退火分离剂的涂覆量a、添加剂的浓度c、添加剂平均粒径d和粗粒的体积分率(以下也称为含有率)r收纳于规定的关系是重要的。
[0064]
即,计算使用这些a、c、d和r的(a
·
c
·
r)/d3(以下简记为acr/d3)而导出的值表示钢板表面的单位面积的粗粒添加剂的存在频率。而且如果该值变高,则粗粒存在于钢板表面的频率变高,粗大的固定部增加,微小的固定部减少。但是,如果粗粒的存在频率过高,则固定部深度过深,导致磁滞损耗的增加。因此,重要的是根据粗粒的存在频率调整退火分离剂的涂覆量、添加剂的浓度而适当调整带入表面的粗粒的量。如果进行这样的处理,则可以得到兼顾磁特性和被膜密合性的被膜。
[0065]
应予说明,这样的被膜形成速度的变化仅限于平均粒径为一定程度大的添加剂。这是因为在微小的添加剂中,即使包含粗大的粒子,在粗大的粒子的间隙中也浸入微小的粒子,微小粒子在退火初期反应,因此在被膜形成的反应速度上不易发生变化。
[0066]
接下来,对本发明的构成要件的限定理由进行叙述。
[0067]
根据本发明的绝缘被膜形成部分进入基铁内部的固定部和将该固定部与被膜上
部连接的颈部,在通过钢板的弯曲试验将被膜从基铁剥离时,对于残留于基铁表面的颈部,将面积5μm2以下的个数设为0.06个/μm2以下。如果面积5μm2以下的个数超过0.06个,则磁滞损耗增大而铁损劣化。优选为0.05个/μm2以下。应予说明,颈部面积的下限不特别限定,从测定精度的观点出发,设为0.01μm2左右。另外,个数越少,铁损越减少,因此也可以为0个/μm2。
[0068]
对于颈部,将面积为10~40μm2的个数设为0.005个/μm2~0.011个/μm2的范围。即,为了确保被膜密合性,面积为10~40μm2的颈部需要0.005个/μm2以上。另一方面,如果凹凸过剧烈,则导致磁滞损耗的增大,因此设为0.011个/μm2以下。优选为0.006个/μm2~0.009个/μm2以下。应予说明,颈部的面积超过40μm2被视为由颈部与被膜上部连接的与所谓的固定在形式上不同且被膜上部和下部一体化的厚膜部,因此在本发明中不作为个数测定的对象。
[0069]
进而,固定部距离基铁表面的深度设为3.5μm以下。如果超过该值,则磁滞损耗增大而铁损劣化。优选为3.0μm以下。应予说明,这样的深度的下限不特别限制,但是从测定精度的观点出发,优选为0.1μm左右。
[0070]
接下来,作为本发明的材料的钢的优选成分的组成范围如下。
[0071]
c:0.01~0.10%
[0072]
c如果不足0.01%,则失去由c产生的晶界强化效果,在板坯上产生裂纹等,产生对制造造成妨碍的缺陷。另一方面,如果超过0.10%,则在脱碳退火中难以减少到不发生磁时效的0.004%以下。因此,c优选设为0.01~0.10%的范围。更优选为0.02%~0.08%。
[0073]
si:2~4%
[0074]
si是提高钢的比电阻、减少铁损所需的元素。如果小于2%,则上述效果不足,另一方面,如果超过4%,则加工性降低,难以轧制并制造。因此,si优选设为2~4%的范围。更优选为2.8%~3.7%。
[0075]
mn:0.01~0.5%
[0076]
mn是改善钢的热加工性所需的元素。如果小于0.01%,则上述效果不足。另一方面,如果超过0.5%,则产品板的磁通密度降低。因此,mn优选设为0.01~0.5%的范围。更优选为0.02%~0.20%。
[0077]
对于除这些以外的成分,为了产生二次再结晶,分为利用抑制剂的情况和不利用的情况。
[0078]
首先,在为了产生二次再结晶而利用抑制剂的情况下,例如,在利用aln系抑制剂时,优选分别以al:0.01~0.04%、n:0.003~0.015%的范围含有al和n。另外,在利用mns
·
mnse系抑制剂的情况下,优选含有上述量的mn以及s:0.002~0.03%和se:0.003~0.03%中的1种或2种。如果各添加量小于上述下限值,则不能充分地得到抑制剂效果。另一方面,如果超过上限值,则抑制剂成分在板坯加热时由于未固溶而残留,导致磁特性的降低。应予说明,aln系和mns
·
mnse系的抑制剂也可以并用。
[0079]
另一方面,在为了产生二次再结晶而不利用抑制剂的情况下,极力减少作为上述抑制剂形成成分的al、n、s和se的含量,优选使用减少到al:小于0.01%、n:小于0.005%、s:小于0.005%和se:小于0.005%的钢材料。
[0080]
除上述成分以外,为了改善磁特性,本发明的方向性电磁钢板还可以适当地添加
选自ni:0.001~0.15%、sb:0.005~0.50%、sn:0.005~0.20%、p:0.01~0.08%、bi:0.005~0.05%、mo:0.005~0.10%、b:0.0002~0.0025%、cu:0.01~0.2%、te:0.0005~0.010%、cr:0.01~0.2%、nb:0.0010~0.010%、v:0.001~0.010%、ti:0.001~0.010%和ta:0.001~0.010%中的1种或2种以上。
[0081]
根据本发明的钢板可以在用常规精炼工艺将具有上述成分组成的钢熔炼后,用以往公知的造锭-分锭轧制法或连续铸造法制造钢材料(板坯),或也可以用直接铸造法制造100mm以下厚度的薄铸片。在上述板坯的情况下,根据常规方法,例如在含有抑制剂成分的情况下加热到1400℃左右,另一方面,在不含有抑制剂成分的情况下加热到1300℃以下的温度后,提供给热轧。应予说明,在不含有抑制剂成分的情况下,可以在铸造后不加热而直接进行热轧。另外,在薄铸片的情况下,可以进行热轧,也可以省略热轧而直接进入以后的工序。
[0082]
然后,热轧而得到的热轧板根据需要实施热轧板退火。为了得到良好的磁特性,该热轧板退火的退火温度优选设为800~1150℃的范围。如果小于800℃,则由热轧形成的带状组织残留,难以得到整粒的一次再结晶组织,二次再结晶的进行受到阻碍。另一方面,如果超过1150℃,则热轧板退火后的粒径过大,仍然难以得到整粒的一次再结晶组织。
[0083]
热轧后或热轧板退火后的热轧板进行1次冷轧或包括中间退火的2次以上冷轧而制成最终板厚的冷轧板。上述中间退火的退火温度优选设为900~1200℃的范围。如果小于900℃,则有中间退火后的再结晶粒变细、进而一次再结晶组织中的goss核减少而产品板的磁特性降低的倾向。另一方面,如果超过1200℃,则与热轧板退火时同样,晶粒过大而难以得到整粒的一次再结晶组织。
[0084]
另外,制成最终板厚的冷轧(以下称为最终冷轧)可以使最终冷轧时的钢板温度上升到100~300℃来进行、在最终冷轧过程中在100~300℃的温度下实施1次或多次时效处理。由此,改善一次再结晶集合组织,进一步提高磁特性。
[0085]
最终冷轧后进行一次再结晶退火,涂覆退火分离剂后进行成品退火。这些工序在本发明中为了形成良好的被膜而严格管理。
[0086]
一次再结晶退火的升温速度不特别限定,但是如果在500~700℃之间以50℃/秒以上进行,则二次再结晶晶粒被细化而铁损得到改善,因此优选。另外,均热时间为80秒~200秒,更优选为90秒~150秒。如果均热时间小于80秒,则有脱碳不足、一次粒生长不足的风险,如果超过200秒,则有一次粒生长过量的风险。进而,本发明也可以在成品退火时进行保定退火。
[0087]
一次再结晶退火后涂覆退火分离剂。退火分离剂在主剂中使用mgo(主要成分为mgo)的情况下通过浆料化而将带入的水分量设为1.0质量%~3.9质量%,这是有效的。这是为了在控制mgo的反应性的同时调整成品退火时带入气氛的水分量。如果偏离该范围,则有无论如何都不形成所期待的形状的基底被膜的风险。应予说明,退火分离剂中的主剂是指相对于退火分离剂整体以50vol%以上的比率包含的成分,在本发明中为上述mgo或后述非反应性氧化物。
[0088]
在本发明中,作为退火分离剂,对水的溶解度为3g/l以下,含有浓度c(质量%)的具有累积50%粒径d(μm)的4倍以上粒径的粒子的体积分率为r(vol%)和粒度的标准偏差为sd(μm)的添加剂,进而,以涂覆量a(g/m2)将该退火分离剂涂覆于钢板。此时,重要的是上
述累积50%粒径d、体积分率r、粒度的标准偏差sd、浓度c和涂覆量a满足以下各式:
[0089]
d≥1.8,
[0090]
sd≤0.6
·
d,
[0091]
0.15≤(a
·
c
·
r)/d3≤20。
[0092]
即,如果是d小于1.8μm的粉体作为添加剂,则即使存在粗大颗粒,微细粉也分散在其周围而被涂覆,因此在上述的被膜形成中不能得到差异而不能得到所期望的固定形状。因此,添加剂中的累积50%粒径d设为1.8μm以上,优选设为2.1μm以上。
[0093]
另外,如果acr/d3的值低于0.15,则具有一定大小的颈部的形成不足,如果acr/d3的值大于20,则过于促进颈部的形成而磁滞损耗增加,因此限定于该范围。优选为0.25~20。
[0094]
添加剂粒度的标准偏差设为0.6d以下。如果大于0.6d,则分布过宽,因此微小的颈部也增加,磁滞损耗增加。优选设为0.25d以下。
[0095]
应予说明,上述d的下限值不特别限定,但是工业上为0.2μm左右。
[0096]
作为这样的退火分离剂的添加剂,有mg、ca、ti、cr、mn、fe、cu、sr、v、co、zn、sn、sb、ba、bi和mo的氧化物、氢氧化物、硫酸盐、磷酸盐、硼酸盐、硅酸盐、碳酸盐等。除这些以外,还可以复合添加例如水溶性的化合物或平均粒径不足1.8μm的微细添加剂。
[0097]
另外,在将绝缘被膜设为镁橄榄石被膜的情况下,在退火分离剂中使用mgo。通过使用以mgo为主剂并添加满足上述条件的添加剂而得的退火分离剂,可以将上述被膜结构的绝缘被膜形成于钢板上。
[0098]
在不形成该镁橄榄石被膜的情况下、即作为实现无膜镜面化的情况下使用的退火分离剂,可以代替mgo而使用al2o3、mgal2o4等非反应性氧化物作为主剂。或者也可以使用在主剂中使用mgo并含有1~20质量%的卤素作为副剂而得的退火分离剂。如果使用这些退火分离剂,则成品退火后的钢板表面的氧单位面积重量成为0.1g/m2以下,几乎不形成氧化膜。另一方面,如果满足退火分离剂中的添加剂的粒度等上述限制,则在基铁侧形成满足上述条件的固定部。在成品退火后,该固定部内的被膜部分与覆盖基铁表面的薄膜一起从基铁表面剥离,结果该固定部在基铁侧成为空腔而残留。在之后的绝缘涂层涂覆时,涂层材料进入该空腔,在烧结后成为与绝缘被膜一体的固定部,结果发挥与上述固定部相同的效果。其结果可以提高绝缘涂层的密合性。应予说明,此时,不用说由这样的涂层而形成的绝缘被膜满足本发明的要件。
[0099]
无论使用上述的不同主剂的退火分离剂中的哪一个,在涂覆该退火分离剂后进行成品退火都是同样的。在该成品退火中,在800~950℃的范围保持20~100小时对减少微小的固定部而增加粗大的固定部是有效的。这是因为在该保定退火中,为了降低表面能量,底垢中的二氧化硅富集在被膜表面和被膜基铁界面,然后发生正式的被膜形成。应予说明,如果小于20小时,则效果少,如果超过100小时,则粗大的固定部过于发达而磁滞损耗劣化,因此优选为该范围。更优选为30小时~80小时。
[0100]
另外,上述成品退火的均热温度如果低于800℃,则有脱碳不足或一次粒生长不足的风险,另一方面,如果超过950℃,则有相同地脱碳不足或一次粒生长过量的风险。应予说明,更优选为800℃~930℃。
[0101]
上述成品退火的气氛设为湿氢气氛,调整露点,由此以均热整体的平均计将ph2o/
ph2抑制为0.65以下,更优选抑制为0.55以下。这是因为如果高于0.65,则有在表面容易生成feo、被膜劣化的风险。应予说明,气氛氧化性也可以在加热带、均热带、最终均热带分别控制。另外,如果在成品退火的均热的最后将ph2o/ph2设为0.2以下,更优选设为0.15以下,则成为还原气氛,更有利于调整形成于表层的内部氧化膜的形态来改善磁特性、被膜。
[0102]
进而,为了改善磁特性,已知在一次再结晶退火前、中或后进行氮化处理的方法,在本发明中也可以结合这样的方法来进行。
[0103]
如上所述,本发明也可以应用于利用无膜镜面化的铁损改善方法。即,可以在以下情况中应用本发明:通过在退火分离剂中使用上述非反应性氧化物而将成品退火后的表面的氧单位面积重量设为0.1g/m2以下,或者在退火分离剂的主剂中使用mgo并含有1~20质量%的卤素作为副剂而将成品退火后的表面的氧单位面积重量设为0.1g/m2以下。在这种情况下,成品退火后不存在成为固定部的氧化物,固定部成为空腔,在之后的绝缘涂层涂覆时涂层进入空腔内,因此涂层成为固定部并发挥功能。
[0104]
另外,在退火分离剂的主剂mgo中添加卤化物而镜面化的情况下,在无膜的钢板表面形成凹凸,绝缘涂层进入其中进一步形成固定部。通常,在充分镜面化的钢板中,为了保持与绝缘涂层的密合性,用pvd、cvd等方法在绝缘涂层与钢板之间形成粘合剂,但是在退火分离剂的主剂mgo中添加卤化物而镜面化的情况下,在钢板表面形成有适度的凹凸,因此即使直接实施涂层,也可以保持被膜密合性。进而,剥离钢板表面的被膜而镜面化,结果固定部深度也变浅,因此也抑制磁滞损耗的劣化。
[0105]
在本发明中,在从最终冷轧到成品退火的任一阶段中,将钢板表面的平均粗糙度调整为0.3μm以下,将最大谷深度调整为2μm~5μm,这对实现根据本发明的被膜形态是有效的。即,通过将平均粗糙度设为0.3μm以下,可以更容易将5μm2以下的固定部的个数减少到0.06个/μm2以下。另外,通过将最大谷深度设为2μm~5μm,可以更容易实现在确保10~40μm2以上的粗大的固定颈的个数的同时将固定部距离基铁表面的深度设为3.5μm以下。
[0106]
进而,优选将脱碳退火前的钢板表面的平均粗糙度sa调整为0.3μm以下,将最大谷深度sv调整为2μm~5μm,也可以在成品退火时进行保定退火。应予说明,上述sa的下限值不特别限定,但是工业上为0.5μm左右。另外,上述粗糙度根据iso25178的定义。
[0107]
调整成这样的钢板表面的粗糙度的方法有很多。例如,可以使用使最终冷轧的辊的粗糙度图案适当化的方法、通过在冷轧后重新通过具有适当的粗糙度的辊来对钢板施加粗糙度的方法、通过激光加工、蚀刻而在表面形成凹凸的方法等任意方法。
[0108]
作为其他制造条件,成品退火中的气氛露点设为20℃以下,这防止由抑制剂氧化引起的劣化,因此优选。进而在上述成品退火后为了发生二次再结晶而利用抑制剂的情况下,为了将上述抑制剂形成成分从产品板除去,优选在氢气氛下实施在1200℃左右、具体在1150~1240℃的范围的温度保持2~50小时的纯化退火。
[0109]
进行上述成品退火、纯化退火后的钢板进行除去附着于钢板表面的未反应的退火分离剂的水洗、冲刷、酸洗等。然后,为了减少铁损,优选实施平坦化退火来进行形状矫正。这是由于一般在线圈状态下进行成品退火,所以为了防止由于线圈的卷绕特性而导致磁特性劣化。
[0110]
进而,在层叠使用钢板的情况下,优选在上述平坦化退火中或其前后在钢板表面形成绝缘涂层。此时,为了进一步减少铁损,优选应用可以对钢板赋予张力的张力赋予被膜
作为绝缘涂层。另外,为了形成被膜密合性优异且铁损减少效果大的张力赋予被膜,也可以采用如下方法:通过粘合剂涂覆张力被膜的方法,用物理蒸镀法、化学蒸镀法使无机物蒸镀于钢板表层后涂覆张力被膜的方法。但是,在本发明中,由于适当地形成了表面的凹凸,所以即使不使用粘合剂也可以得到充分的密合性。
[0111]
应予说明,在无膜镜面化的情况下,也可以在进行成品退火后到涂覆绝缘涂层前用辊、蚀刻、激光加工等对钢板施加凹凸来调整规定的颈部。
[0112]
为了进一步减少铁损,优选实施磁畴细化处理。作为磁畴细化的方法,可以很好地使用一般实施的如下方法:在最终产品板的表面照射电子束、激光束、等离子体等热能来导入线状或点状的热应变的方法,在最终产品板的表面导入线状或点状的压痕、划痕等加工应变的方法,在冷轧成最终板厚的钢板表面在中间工序中实施蚀刻加工来形成线状或点状的槽的方法等。
[0113]
实施例
[0114]
(实施例1)
[0115]
将包含c:0.06%、si:3.28%、al:0.02%、n:80质量ppm、mn:0.07%、s:0.005%和cu:0.06%且剩余部分由铁和不可避免杂质构成的板坯加热到1400℃,热轧成2.2mm厚,夹入1050℃、2分钟的中间退火并冷轧到0.23mm厚,加工成最终板厚的钢板。然后,通过激光照射对钢板表面进行精细加工,变更钢板的表面性状(平均粗糙度sa和最大谷深度sv)。然后,对该钢板以800℃
×
120秒、水蒸汽分压p(h2o)/p(h2):0.4进行退火作为一次再结晶退火。
[0116]
进而,在一次再结晶退火后的钢板的表面涂覆退火分离剂。即,使用使平均粒径1.2μm、粒径的标准偏差为0.4μm的mgo中含有6质量%的平均粒径为0.3μm的tio2以及2质量%(浓度c)的平均粒径(累积50%粒径)d为2.0μm且其4倍以上粒度的粒子的含有率r为4.7vol%、粒度的标准偏差为0.4μm的mno而得的退火分离剂,以涂覆量a:9g/m2将该退火分离剂涂覆于钢板。应予说明,此时的acr/d3为10.6。
[0117]
然后,在900℃保持30小时然后在1160℃下进行10小时的纯化退火作为成品退火。纯化退火后除去未反应退火分离剂后,涂覆磷酸镁
‑
二氧化硅系的绝缘涂层并烧结,在800℃下进行10秒的平坦化退火。
[0118]
将调查这样得到的钢板的磁特性和被膜密合性而得的结果示于表2。通过将表面粗糙度收纳于适当范围,磁滞损耗减少而铁损得到改善,并且可以得到被膜密合性也良好的值。
[0119]
表2
[0120]
[0121]
(实施例2)
[0122]
将包含c:0.03%、si:3.4%、al:0.006%、n:30质量ppm、mn:0.07%、p:0.02%和mo:0.02%且剩余部分由铁和不可避免杂质构成的板坯加热到1400℃,热轧成2.2mm厚,夹入1050℃、2分钟的中间退火而冷轧到0.23mm厚,加工成最终板厚。然后,在钢板表面进行防染印花后进行蚀刻,在钢板表面形成图案化的孔。此时的平均粗糙度sa为0.3μm,最大谷深度sv为3.9μm。然后,以860℃
×
80秒、水蒸汽分压p(h2o)/p(h2):0.5进行退火作为一次再结晶退火。
[0123]
进而,在一次再结晶退火后的钢板的表面涂覆退火分离剂。即,使用使平均粒径0.8μm、粒径的标准偏差为0.3μm的mgo中含有4质量%的平均粒径为0.3μm的tio2以及4质量%(浓度c)的平均粒径d为6.2μm且其4倍以上粒度的粒子的含有率r为3.2vol%、粒度的标准偏差为0.52μm的滑石(mg3si4o
10
(oh)2)而得的退火分离剂,以涂覆量a:10g/m2将该退火分离剂涂覆于钢板。应予说明,此时的acr/d3为0.53。
[0124]
然后,在850℃保持30小时或者不保定而直接进行1160℃10小时的纯化退火作为成品退火。纯化退火后除去未反应退火分离剂,涂覆磷酸镁
‑
二氧化硅系的绝缘涂层并烧结,在800℃下进行10秒的平坦化退火。
[0125]
将调查这样得到的钢板的磁特性和被膜密合性而得的结果示于表3。通过表面粗糙度的适当化、向退火分离剂添加剂中导入粗大颗粒以及追加保定退火,与no.9相比,磁滞损耗减少而铁损得到改善。
[0126]
表3
[0127][0128]
(实施例3)
[0129]
将包含c:0.03%、si:3.32%、al:0.01%、n:60质量ppm、mn:0.07%和sb:0.04%且剩余部分由铁和不可避免杂质构成的板坯加热到1400℃,热轧成2.2mm厚,夹入1050℃、2分钟的中间退火并冷轧到0.23mm,加工成最终板厚。此时通过调整最终冷轧的辊粗糙度,将钢板表面的平均粗糙度sa调整为0.22μm,将最大谷深度sv调整为3.2μm。然后,以850℃
×
90秒、水蒸汽分压p(h2o)/p(h2):0.3进行退火作为一次再结晶退火。
[0130]
进而,在一次再结晶退火后的钢板的表面涂覆退火分离剂。即,使用使平均粒径0.9μm、粒径的标准偏差为0.4μm的mgo中含有6质量%的bicl3以及1.5质量%(浓度c)的平均粒径d为3.6μm且其4倍以上粒度的粒子的含有率r为2.2vol%、粒度的标准偏差为1.5μm
的sno而得的退火分离剂,以涂覆量a:10g/m2将该退火分离剂涂覆于钢板。应予说明,此时的acr/d3为0.7。
[0131]
然后,在850℃保持30小时或者不保定而直接进行1160℃10小时的纯化退火作为成品退火。纯化退火后除去未反应退火分离剂。在该阶段的钢板表面没有氧化膜的残留,从钢板表面向基铁侧形成有10μm2左右大小的空腔。在该成品退火后的钢板上涂覆磷酸镁
‑
二氧化硅系的绝缘涂层并烧结,在800℃下进行10秒的平坦化退火。然后,通过照射电子束对这样的钢板进行磁畴细化处理。
[0132]
将调查这样得到的钢板的磁特性和被膜密合性而得的结果示于表4。如表4所示,可知在绝缘涂层中形成有根据本发明的固定部。其结果可知由于铁损有效地减少了所以实现了基于无膜镜面化的铁损减少,以及磁滞损耗减少而铁损得到改善。进而,即使不采取特别的工序,也保持着绝缘涂层与基铁的密合性。
[0133]
(实施例4)
[0134]
将具有与实施例3相同成分的钢锭以与实施例2相同的工序进行直到一次再结晶退火。然后,在主剂中使用氧化铝并在其中以浓度c成为1.5质量%的方式含有平均粒径d为3.6μm且其4倍以上粒度的粒子的含有率r为2.2vol%、粒度的标准偏差为1.5μm的sno而得到退火分离剂,以涂覆量a:10g/m2将该退火分离剂涂覆于钢板。此时的acr/d3为0.7。成品退火以后以与实施例2相同的工序进行处理。将调查这样得到的钢板的磁特性和被膜密合性而得的结果一并记载于表4。如表4所示,可知在退火分离剂中使用非反应性的al2o3的情况下,在绝缘涂层中也形成有根据本发明的固定部。其结果可以得到铁损、被膜密合性都良好的结果。
[0135]
表4
[0136][0137]
符号说明
[0138]1ꢀꢀ
被膜
[0139]2ꢀꢀ
基铁
[0140]3ꢀꢀ
固定部
[0141]4ꢀꢀ
颈部(面积率10~40μm2)
[0142]5ꢀꢀ
颈部(面积率5μm2以下)
[0143]6ꢀꢀ
固定部深度
再多了解一些
本文用于企业家、创业者技术爱好者查询,结果仅供参考。