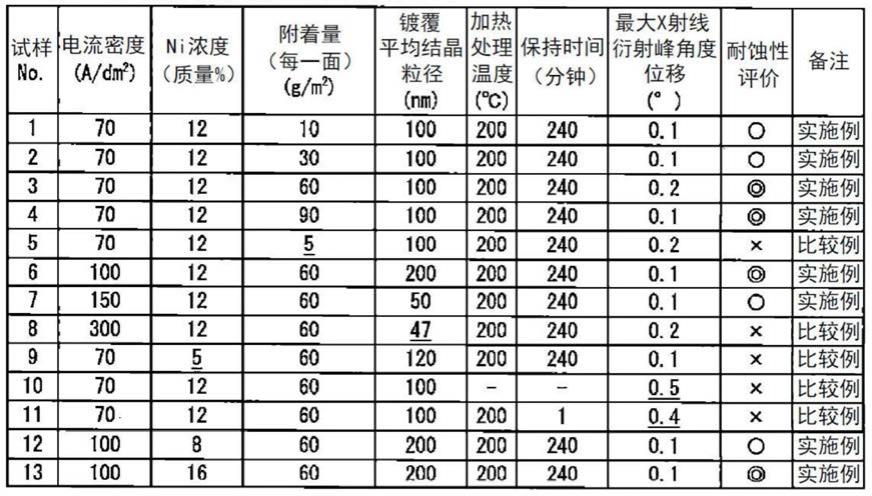
1.本发明涉及热冲压用镀覆钢板,更具体而言,涉及具有zn
‑
ni镀层的热冲压用镀覆钢板。
背景技术:
2.近年来,对于汽车用构件中使用的钢板的成型,大多使用了热冲压法(热压法)。所谓热冲压法是将钢板在加热至奥氏体区域的温度的状态下进行压制成型、在成型的同时通过压制模具进行淬火(冷却)的方法,是强度及尺寸精度优异的钢板的成型方法之一。
3.在热冲压中使用的钢板中,有时在钢板表面设置zn
‑
ni镀层。在专利文献1中,公开了一种热冲压用钢板,其在钢板表面依次具有附着量为0.01~5g/m2的镀层i和附着量为10~90g/m2的镀层ii,所述镀层i包含60质量%以上的ni,剩余部分由zn及不可避免的杂质构成,所述镀层ii包含10~25质量%的ni,剩余部分由zn及不可避免的杂质构成。此外,在专利文献2中,公开了一种热冲压用钢板,其在钢板表面具有附着量为10~90g/m2的镀层,所述镀层包含10~25质量%的ni,剩余部分由zn及不可避免的杂质构成,上述镀层的η相含有率为5质量%以下。进而,在专利文献3中,公开了一种热冲压用钢板,其在钢板表面具有熔点为800℃以上、每一面的附着量为10~90g/m2的zn
‑
ni镀层等镀层。此外,在专利文献4中,记载了一种热压构件的制造方法,其特征在于,该制造方法包括:将镀覆钢板加热至850~950℃,在上述加热后的镀覆钢板的温度为650~800℃时,开始热压成型,所述镀覆钢板具备基底钢板和形成于该基底钢板上的镀层,所述镀层含有10~25质量%的ni,剩余部分由zn及不可避免的杂质构成,上述镀层的每一面的附着量为10~90g/m2。
4.关于zn
‑
ni镀层,在专利文献5~7中,分别教导了通过调整该镀层的平均结晶粒径,可稳定地保持铬酸盐处理后的外观、提高压制加工性及提高化学转化处理性。
5.现有技术文献
6.专利文献
7.专利文献1:日本特开2012
‑
233247号公报
8.专利文献2:日本特开2016
‑
29214号公报
9.专利文献3:日本特开2012
‑
197505号公报
10.专利文献4:国际公开第2015/001705号
11.专利文献5:日本特开2009
‑
127126号公报
12.专利文献6:日本特开平6
‑
116781号公报
13.专利文献7:日本特开平3
‑
68793号公报
技术实现要素:
14.发明所要解决的课题
15.通过将在钢板上具有zn
‑
ni镀层的镀覆钢板进行热冲压而得到的成型体(热冲压成型体)通过该zn
‑
ni镀层中的zn来保证耐蚀性。关于该zn
‑
ni镀层中的zn,例如即使是热冲
压成型体受到损伤而钢板露出的情况下,比构成钢板的fe容易腐蚀的zn也先腐蚀而形成保护皮膜,具有通过该保护皮膜来防止钢板的腐蚀的作用(称为“替化防蚀作用”)。另一方面,在热冲压中由于将镀覆钢板加热至奥氏体区域的温度(例如900℃以上),因此在热冲压的加热时镀层中的zn与钢板中的fe相互扩散。若像这样zn向钢板中的扩散进展,则所得到的热冲压成型体的zn
‑
ni镀层中的zn浓度降低,上述替化防蚀作用不会充分发挥,有可能热冲压成型体的耐蚀性变得不充分。
16.对于专利文献1中记载的热冲压用钢板,在钢板表面与包含10~25质量%的ni的zn
‑
ni镀层(镀层ii)之间,设置包含60质量%以上的ni的zn
‑
ni镀层(镀层i),通过该镀层i来防止zn从最表层的镀层ii向基底钢板的扩散。为了得到这样的热冲压用钢板,需要准备2种具有不同镀浴组成的镀浴,从生产率的观点出发不优选。
17.对于专利文献2及3中记载的热冲压用钢板,对于抑制zn向钢板中的扩散,未进行任何研究,无法充分防止zn向钢板中的扩散,有可能热冲压成型体的耐蚀性变得不充分。此外,在专利文献4中,虽然教导了通过在规定的温度下开始热压成型来防止lme开裂,但对于用于防止上述那样的起因于zn向钢板中扩散的耐蚀性的降低的zn
‑
ni镀覆钢板的构成,未进行充分研究。
18.本发明鉴于这样的实际情况而进行,目的是提供通过新颖的构成而抑制zn向钢板中的扩散、能够得到具有得以改善的耐蚀性的热冲压成型体的热冲压用镀覆钢板。
19.用于解决课题的手段
20.本发明人们发现了:为了在热冲压时有效地抑制zn
‑
ni镀层中的zn向钢板中扩散、得到具有得以改善的耐蚀性的热冲压成型体,减少热冲压前的zn
‑
ni镀层中的残余应变(应力)是有效的。如在轧制后的金属板的再结晶中也已知的那样,若金属组织中的应变大,则在利用加热进行的金属组织的再结晶时,由于缓和应变,因此原子变得容易活动,但若应变小则原子变得难以活动。这也适用于金属的扩散,若zn
‑
ni镀层中的残余应变(应力)小,则可充分抑制热冲压加热时的zn从zn
‑
ni镀层向母材钢板的扩散及fe从母材钢板向zn
‑
ni镀层的扩散。如果可抑制zn向钢板中的扩散及fe向镀层中的扩散,则在热冲压成型体的zn
‑
ni镀层中能够残留充分浓度的zn,可得到具有得以改善的耐蚀性的热冲压成型体。进而,本发明人们还发现了:为了得到具有得以改善的耐蚀性的热冲压成型体,除了控制zn
‑
ni镀层中的残余应变以外,在热冲压前的zn
‑
ni镀层中,将ni浓度、镀覆附着量、及平均结晶粒径控制在规定的范围是有效的。
21.本发明是基于上述见识而进行的,其主旨如下所述。
22.(1)一种热冲压用镀覆钢板,其具有钢板和形成于上述钢板的至少一面的zn
‑
ni镀层,在上述zn
‑
ni镀层中,ni浓度为8质量%以上,镀覆附着量以每一面计为10g/m2以上且90g/m2以下,平均结晶粒径为50nm以上,其中,将上述热冲压用镀覆钢板在200℃下进行1小时热处理后通过使用了co
‑
kα射线的x射线衍射分析而测定的上述zn
‑
ni镀层的最大x射线衍射峰的角度与在热处理之前通过使用了co
‑
kα射线的x射线衍射分析而测定的上述zn
‑
ni镀层的最大x射线衍射峰的角度之差为0.3
°
以下。
23.(2)根据(1)所述的热冲压用镀覆钢板,其中,上述钢板以质量%计含有:
24.c:0.05%以上且0.70%以下、
25.mn:0.5%以上且11.0%以下、
26.si:0.05%以上且2.00%以下、
27.al:0.001%以上且1.500%以下、
28.p:0.100%以下、
29.s:0.100%以下、
30.n:0.010%以下、
31.o:0.010%以下、
32.b:0%以上且0.0040%以下、
33.cr:0%以上且2.00%以下、
34.ti:0%以上且0.300%以下、
35.nb:0%以上且0.300%以下、
36.v:0%以上且0.300%以下、
37.zr:0%以上且0.300%以下、
38.mo:0%以上且2.000%以下、
39.cu:0%以上且2.000%以下、
40.ni:0%以上且2.000%以下、
41.sb:0%以上且0.100%以下、
42.ca:0%以上且0.0100%以下、
43.mg:0%以上且0.0100%以下、及
44.rem:0%以上且0.1000%以下,
45.剩余部分由铁及杂质构成。
46.(3)根据(2)所述的热冲压用镀覆钢板,其中,上述钢板以质量%计含有选自由下述元素构成的组中的至少一种:
47.b:0.0005%以上且0.0040%以下、
48.cr:0.01%以上且2.00%以下、
49.ti:0.001%以上且0.300%以下、
50.nb:0.001%以上且0.300%以下、
51.v:0.001%以上且0.300%以下、
52.zr:0.001%以上且0.300%以下、
53.mo:0.001%以上且2.000%以下、
54.cu:0.001%以上且2.000%以下、
55.ni:0.001%以上且2.000%以下、
56.sb:0.001%以上且0.100%以下、
57.ca:0.0001%以上且0.0100%以下、
58.mg:0.0001%以上且0.0100%以下、及
59.rem:0.0001%以上且0.1000%以下。
60.(4)根据(1)~(3)中任一项所述的热冲压用镀覆钢板,其中,上述镀覆附着量以每一面计为50g/m2以上。
61.发明效果
62.根据本发明,能够提供可得到具有得以改善的耐蚀性的热冲压成型体的热冲压用
镀覆钢板。
具体实施方式
63.<热冲压用镀覆钢板>
64.本发明的热冲压用镀覆钢板具有钢板和形成于钢板的至少一面的zn
‑
ni镀层。优选zn
‑
ni镀层形成于钢板的两面。此外,本发明中,zn
‑
ni镀层只要形成于钢板上即可,也可以在钢板与zn
‑
ni镀层之间设置其他的镀层。
65.[钢板]
[0066]
本发明中的钢板的成分组成只要能够将钢板用于热冲压则没有特别限定。以下,对本发明中的钢板中可包含的元素进行说明。需要说明的是,关于成分组成的表示各元素的含量的“%”只要没有特别说明,则是指质量%。
[0067]
优选的是,本发明中的钢板可以以质量%计含有c:0.05%以上且0.70%以下、mn:0.5%以上且11.0%以下、si:0.05%以上且2.00%以下、al:0.001%以上且1.500%以下、p:0.100%以下、s:0.100%以下、n:0.010%以下、及o:0.010%以下。
[0068]
(c:0.05%以上且0.70%以下)
[0069]
c(碳)是对于提高钢板的强度而言有效的元素。对于汽车用构件,例如有时要求980mpa以上的高强度。为了充分确保强度,优选将c含量设定为0.05%以上。另一方面,若过度地含有c则有时钢板的加工性降低,因此优选将c含量设定为0.70%以下。c含量的下限优选为0.10%,更优选为0.12%,进一步优选为0.15%,最优选为0.20%。此外,c含量的上限优选为0.65%,更优选为0.60%,进一步优选为0.55%,最优选为0.50%。
[0070]
(mn:0.5%以上且11.0%以下)
[0071]
mn(锰)是对于提高热冲压时的淬透性而言有效的元素。为了可靠地得到该效果,优选将mn含量设定为0.5%以上。另一方面,若过度含有mn,则有可能mn偏析而热冲压后的成型体的强度等变得不均匀,因此优选将mn含量设定为11.0%以下。mn含量的下限优选为1.0%,更优选为2.0%,进一步优选为2.5%,进一步更优选为3.0%,最优选为3.5%。mn含量的上限优选为10.0%,更优选为9.5%,进一步优选为9.0%,进一步更优选8.5%,最优选为8.0%。
[0072]
(si:0.05%以上且2.00%以下)
[0073]
si(硅)是对于提高钢板的强度而言有效的元素。为了充分确保强度,优选将si含量设定为0.05%以上。另一方面,若过度含有si,则有时加工性降低,因此优选将si含量设定为2.00%以下。si含量的下限优选为0.10%,更优选为0.15%,进一步优选为0.20%,最优选为0.30%。si含量的上限优选为1.80%,更优选为1.50%,进一步优选为1.20%,最优选为1.00%。
[0074]
(al:0.001%以上且1.500%以下)
[0075]
al(铝)是作为脱氧元素起作用的元素。为了得到脱氧的效果,优选将al含量设定为0.001%以上。另一方面,若过量地含有al,则有可能加工性降低,因此优选将al含量设定为1.500%以下。al含量的下限优选为0.010%,更优选为0.020%,进一步优选为0.050%,最优选为0.100%。al含量的上限优选为1.000%,更优选为0.800%,进一步优选为0.700%,最优选为0.500%。
[0076]
(p:0.100%以下)
[0077]
(s:0.100%以下)
[0078]
(n:0.010%以下)
[0079]
(o:0.010%以下)
[0080]
p(磷)、s(硫)、n(氮)及氧(o)为杂质,优选少,因此这些元素的下限没有特别限定。但是,也可以将这些元素的含量设定为超过0%或0.001%以上。另一方面,若过量地含有这些元素,则有可能韧性、延展性和/或加工性劣化,因此优选将p及s的上限设定为0.100%、将n及o的上限设定为0.010%。p及s的上限优选为0.080%,更优选为0.050%。n及o的上限优选为0.008%,更优选为0.005%。
[0081]
本发明中的钢板的基本成分组成如上所述。进而,该钢板根据需要也可以含有以下的任选元素中的至少一种来代替剩余部分的fe的一部分。例如,钢板也可以含有b:0%以上且0.0040%。此外,钢板也可以含有cr:0%以上且2.00%以下。此外,钢板也可以含有选自由ti:0%以上且0.300%以下、nb:0%以上且0.300%以下、v:0%以上且0.300%以下、及zr:0%以上且0.300%以下构成的组中的至少一种。此外,钢板也可以含有选自由mo:0%以上且2.000%以下、cu:0%以上且2.000%以下、及ni:0%以上且2.000%以下构成的组中的至少一种。此外,钢板也可以含有sb:0%以上且0.100%以下。此外,钢板也可以含有选自由ca:0%以上且0.0100%以下、mg:0%以上且0.0100%以下、及rem:0%以上且0.1000%以下构成的组中的至少一种。以下,对这些任选元素进行详细说明。
[0082]
(b:0%以上且0.0040%以下)
[0083]
b(硼)是对于提高热冲压时的淬透性而言有效的元素。b含量也可以为0%,但为了可靠地得到该效果,优选将b含量设定为0.0005%以上。另一方面,若过度含有b,则有可能钢板的加工性降低,因此优选将b含量设定为0.0040%以下。b含量的下限优选为0.0008%,更优选为0.0010%,进一步优选为0.0015%。此外,b含量的上限优选为0.0035%,更优选为0.0030%。
[0084]
(cr:0%以上且2.00%以下)
[0085]
cr(铬)是对于提高热冲压时的淬透性而言有效的元素。cr含量也可以为0%,但为了可靠地得到该效果,cr含量优选设定为0.01%以上。cr含量也可以为0.10%以上、0.50%以上或0.70%以上。另一方面,若过度含有cr,则有时钢材的热的稳定性降低。因此,cr含量优选设定为2.00%以下。cr含量也可以为1.50%以下、1.20%以下或1.00%以下。
[0086]
(ti:0%以上且0.300%以下)
[0087]
(nb:0%以上且0.300%以下)
[0088]
(v:0%以上且0.300%以下)
[0089]
(zr:0%以上且0.300%以下)
[0090]
ti(钛)、nb(铌)、v(钒)及zr(锆)是通过金属组织的微细化而提高抗拉强度的元素。这些元素的含量也可以为0%,但为了可靠地得到该效果,ti、nb、v及zr含量优选设定为0.001%以上,也可以为0.010%以上、0.020%以上或0.030%以上。另一方面,若过度含有ti、nb、v及zr,则效果饱和,同时制造成本上升。因此,ti、nb、v及zr含量优选设定为0.300%以下,也可以为0.150%以下、0.100%以下或0.060%以下。
[0091]
(mo:0%以上且2.000%以下)
[0092]
(cu:0%以上且2.000%以下)
[0093]
(ni:0%以上且2.000%以下)
[0094]
mo(钼)、cu(铜)及ni(镍)具有提高抗拉强度的作用。这些元素的含量也可以为0%,但为了可靠地得到该效果,mo、cu及ni含量优选设定为0.001%以上,也可以为0.010%以上、0.050%以上或0.100%以上。另一方面,若过度含有mo、cu及ni,则有时钢材的热的稳定性降低。因此,mo、cu及ni含量优选设定为2.000%以下,也可以为1.500%以下、1.000%以下或0.800%以下。
[0095]
(sb:0%以上且0.100%以下)
[0096]
sb(锑)是对于提高镀覆的浸润性、密合性而言有效的元素。sb含量也可以为0%,但为了可靠地得到该效果,sb含量优选设定为0.001%以上。sb含量也可以为0.005%以上、0.010%以上或0.020%以下。另一方面,若过度含有sb,则有时引起韧性的降低。因此,sb含量优选设定为0.100%以下。sb含量也可以为0.080%以下、0.060%以下或0.050%以下。
[0097]
(ca:0%以上且0.0100%以下)
[0098]
(mg:0%以上且0.0100%以下)
[0099]
(rem:0%以上且0.1000%以下)
[0100]
ca(钙)、mg(镁)及rem(稀土类金属)是通过调整夹杂物的形状而提高热冲压后的韧性的元素。这些元素的含量也可以为0%,但为了可靠地得到该效果,ca、mg及rem含量优选设定为0.0001%以上,也可以为0.0010%以上、0.0020%以上或0.0040%以上。另一方面,若过度含有ca、mg及rem,则效果饱和,同时制造成本上升。因此,ca及mg含量优选设定为0.0100%以下,也可以为0.0080%以下、0.0060%以下或0.0050%以下。同样地,rem含量优选设定为0.1000%以下,也可以为0.0800%以下、0.0500%以下0.0100%以下。
[0101]
上述元素以外的剩余部分由铁及杂质构成。这里所谓“杂质”是在工业上制造母材钢板时,通过以矿石、废铁等那样的原料为代表的制造工序的各种要因而混入的成分,包含并非对本发明中的母材钢板有意添加的成分的成分。此外,所谓杂质是上文说明的成分以外的元素,也包含以该元素特有的作用效果不会对本发明的热冲压用镀覆钢板的特性造成影响的水平包含于母材钢板中的元素。
[0102]
作为本发明中的钢板,没有特别限定,可以使用热轧钢板、冷轧钢板等一般的钢板。此外,本发明中的钢板只要是能够在钢板上形成后述的zn
‑
ni镀层并进行热冲压处理则可以是任意的板厚,例如可以为0.1~3.2mm。
[0103]
[zn
‑
ni镀层]
[0104]
本发明中的zn
‑
ni镀层是至少包含zn及ni的镀层,对于其他的成分没有特别限定。例如,zn
‑
ni镀层只要是将zn设定为主要成分(即zn浓度为50质量%以上)、ni浓度为8质量%以上的镀层即可,对于其他的成分没有特别限定。在该镀层中zn和ni是在zn中固溶有ni、或由zn和ni形成金属间化合物。该镀层可以通过任意的镀覆方法而形成,但例如优选通过电镀而形成。zn
‑
ni镀层形成于钢板的至少一面,优选形成于钢板的两面。当然,若进行热冲压成型,则由于产生fe等从基底的钢板向镀层的扩散或zn等从镀层向基底的钢板的扩散,因此热冲压后的镀层的成分组成根据热冲压时的加热条件(加热温度、保持时间等)而发生变化。
[0105]
(ni浓度)
[0106]
在本发明中的zn
‑
ni镀层中,ni浓度的下限为8质量%。通过将ni浓度设定为8质量%以上,抑制热冲压的加热时的zn的氧化、即抑制锌氧化物zno的过量生成,从而在热冲压后能够使zn
‑
ni镀层中残存充分浓度的zn,能够得到具有高耐蚀性的热冲压成型体。若ni浓度变得低于8质量%,则有可能在热冲压的加热时锌氧化物zno的生成显著进展,在热冲压后残存于zn
‑
ni镀层中的zn浓度变得不充分,热冲压成型体的耐蚀性变得不充分。ni浓度的下限优选为10质量%,更优选为12质量%。
[0107]
ni浓度的上限没有特别限定,从经济性的观点出发,优选为30质量%以下。例如ni浓度的上限也可以为28质量%、25质量%或20质量%。
[0108]
本发明中的zn
‑
ni镀层也可以进一步包含fe、cr及co中的1种或2种以上。这些元素可以是有意添加的元素,也可以是在制造上不可避免地混入的元素。此外,zn
‑
ni镀层的成分组成的剩余部分为zn及杂质。在本发明的特定的实施方式中,zn
‑
ni镀层以质量%计含有ni:8%以上且30%以下、fe、cr及co中的1种或2种以上:0%以上且5%以下、及c:低于1%,剩余部分由铁及杂质构成。优选zn
‑
ni镀层以质量%计含有ni:8%以上且30%以下,剩余部分由铁及杂质构成。zn
‑
ni镀层中的“杂质”是在制造zn
‑
ni镀层时,通过以原料为代表的制造工序的各种要因而混入的成分等。
[0109]
(镀覆附着量)
[0110]
在本发明中的zn
‑
ni镀层中,钢板的每一面的镀覆附着量的下限为10g/m2。通过将每一面的镀覆附着量设定为10g/m2以上,在热冲压后可确保充分厚度的镀层,能够获得具有高耐蚀性的热冲压成型体。若每一面的镀覆附着量变得低于10g/m2,则有可能保证耐蚀性的zn
‑
ni镀层的厚度变得不充分,无法得到具有得以改善的耐蚀性的热冲压成型体。钢板的每一面的镀覆附着量的下限优选为16g/m2,更优选为20g/m2,进一步优选为24g/m2,进一步更优选为30g/m2,特别优选为40g/m2,最优选为50g/m2。特别是若钢板的每一面的镀覆附着量为50g/m2以上,则可确保充分厚度的zn
‑
ni镀层,热冲压成型体的耐蚀性进一步改善,因此优选。
[0111]
钢板的每一面的镀覆附着量的上限没有特别限定,从经济性的观点出发优选为90g/m2。钢板的每一面的镀覆附着量的上限优选为80g/m2,更优选为76g/m2,进一步优选为70g/m2,最优选为60g/m2。
[0112]
本发明中的zn
‑
ni镀层的ni浓度及镀覆附着量的测定通过电感耦合等离子体(icp)发射光谱分析来进行。具体而言,本发明中的镀覆附着量通过从具有zn
‑
ni镀层的镀覆钢板用10%hcl将镀层溶解,对所得到的溶液进行icp分析而求出。需要说明的是,本发明中的镀覆附着量由于为每一面的量,因此在钢板的两面形成有zn
‑
ni镀层的情况下,以两面的镀覆附着量相同而算出。
[0113]
(平均结晶粒径)
[0114]
在本发明的zn
‑
ni镀层中,zn
‑
ni镀覆的平均结晶粒径为50nm以上。通过将平均结晶粒径设定为50nm以上,在热冲压的加热时zn
‑
ni镀层中的zn变得难以活动,能够有效地抑制zn向钢板中扩散。这样的话,由于在热冲压后能够在该镀层中残存充分浓度的zn,因此能够获得具有得以改善的耐蚀性的热冲压成型体。若平均结晶粒径变得低于50nm,则在热冲压的加热时zn
‑
ni镀覆中的zn变得容易活动,有可能比较多的zn扩散到钢板中,有可能热冲压成型体的耐蚀性变得不充分。镀覆的平均结晶粒径优选为超过50nm,更优选为55nm以上
或60nm以上,进一步优选为70nm以上。
[0115]
镀覆的平均结晶粒径的上限没有特别限定,如下文所述的那样为了增大平均结晶粒径,需要降低电镀时的电流密度,因此从生产率的观点出发,镀覆的平均结晶粒径的上限优选为300nm,更优选为250nm,进一步优选为200nm。
[0116]
zn
‑
ni镀覆的平均结晶粒径的测定通过x射线衍射(xrd)法来进行。具体而言,使用通过利用co
‑
kα射线的xrd(真空管电压:40kv及真空管电流:200ma)而测定的衍射峰的半值幅b,通过以下的scherrer的式子而求出:
[0117]
平均结晶粒径(nm)=kλ/bcosθ(1)
[0118]
(式中,k:scherrer常数,λ:co
‑
kα射线波长(nm),θ为布拉格角(弧度))。需要说明的是,k为根据微晶的形状而变化的值,但本发明中设定为k=0.9即可。
[0119]
如上所述,本发明中,zn
‑
ni镀覆的平均结晶粒径为50nm以上。这样的具有比较大的结晶粒径的zn
‑
ni镀覆例如可以通过以比较低的电流密度(典型而言为150a/dm2以下)进行电镀来获得。
[0120]
(热处理前后的最大x射线衍射峰的角度的位移)
[0121]
本发明的热冲压用镀覆钢板在200℃下进行1小时热处理后通过使用了co
‑
kα射线的x射线衍射分析而测定的zn
‑
ni镀层的最大x射线衍射峰的角度(2θ)与在热处理之前通过使用了co
‑
kα射线的x射线衍射分析而测定的zn
‑
ni镀层的最大x射线衍射峰的角度(2θ)之差为0.3
°
以下。需要说明的是,该热处理前后的zn
‑
ni镀层的最大x射线衍射峰的角度的位移包括低角度侧位移或高角度侧位移中的任意情况,即,是指热处理前后的zn
‑
ni镀层的最大x射线衍射峰的角度之差的绝对值为0.3
°
以下。这是表示zn
‑
ni镀层中的残余应变的程度的指标,越小意味着在本发明的热冲压用钢板的zn
‑
ni镀层中残余应变越少。若热处理前后的最大x射线衍射峰的角度的位移为0.3
°
以下,则在zn
‑
ni镀层中残存的应变少,在热冲压的加热时zn
‑
ni镀层的zn变得难以活动,能够抑制zn向钢板中的扩散及fe向镀层中的扩散。若热处理前后的最大x射线衍射峰的角度的位移超过0.3
°
,则在zn
‑
ni镀层中存在比较大的应变,在热冲压的加热时zn
‑
ni镀层的zn变得容易活动,有可能无法充分抑制zn向钢板中的扩散。热处理前后的最大x射线衍射峰的角度的位移优选为0.2
°
以下。
[0122]
热处理前后的最大x射线衍射峰的角度的位移越小越优选,因此下限没有特别限定。例如也可以为超过0
°
或0.1
°
以上。
[0123]
本发明中的热处理前后的最大x射线衍射峰的角度的位移的测定如上所述通过x射线衍射(xrd)法来进行。具体而言,对于本发明的热冲压用镀覆钢板的zn
‑
ni镀层通过使用了co
‑
kα射线的xrd来测定最大x射线衍射峰的角度(2θ)。同样地,对于将该镀覆钢板在200℃下进行1小时热处理后的zn
‑
ni镀层通过使用了co
‑
kα射线的xrd来测定最大x射线衍射峰的角度(2θ)。接着,将热处理前后的最大x射线衍射峰的角度进行比较,确定热处理前后的最大x射线衍射峰的角度的位移。需要说明的是,热处理通过退火炉来进行,对于炉内气氛,为了防止氧化而在氮气氛下进行。作为测定条件,采用电压:45kv、电流:40ma、测定角:10
°
~90
°
、狭缝:1/2
°
、步进尺寸:0.1
°
、入射角:2
°
。
[0124]
本发明的热冲压用镀覆钢板的zn
‑
ni镀层在热处理前后的最大x射线衍射峰的角度的位移为0.3
°
以下,因而在zn
‑
ni镀层中残存的应变少。为了得到这样的zn
‑
ni镀层,例如优选在热冲压前用退火炉(baf)等任意的炉进行加热处理。加热处理温度为150~250℃下
即可。若加热处理温度过低则无法充分缓和zn
‑
ni镀层的应变,若过高则有可能钢板及镀层的金属组织发生变化。加热处理的时间为1~48小时即可,优选为2~12小时。若加热处理的时间过短(例如几分钟左右),则有时无法充分缓和应变。此外,例如,从防止zn
‑
ni镀层的氧化等观点出发,加热处理气氛为包含1~10%的氢的氮气氛、且至上述加热处理温度为止的升温速度为20~100℃/小时即可。
[0125]
(抗拉强度)
[0126]
本发明的热冲压用镀覆钢板可以具有任意适宜的抗拉强度,对于具有任意适宜的抗拉强度的热冲压用镀覆钢板能够抑制热冲压的加热时的zn向钢板中的扩散而达成得以改善的耐蚀性。因此,抗拉强度没有特别限定,例如也可以为440mpa以上、590mpa以上或780mpa以上,和/或也可以为1470mpa以下、1320mpa以下、1180mpa以下、1100mpa以下或980mpa以下。抗拉强度通过从与钢板的轧制方向成直角的方向采集jis5号拉伸试验片,依据jis z 2241(2011)进行拉伸试验来测定。
[0127]
上述那样的在钢板上具有zn
‑
ni镀层的镀覆钢板在本领域技术人员所公知的任意条件的热冲压中都可以使用。作为热冲压的加热方式,没有限定,例如可列举出炉加热、通电加热、及感应加热等。此外,热冲压时的加热温度只要根据钢板的成分组成加热至奥氏体区域则可以是任意温度,例如为800℃以上、850℃以上、900℃以上或950℃以上。通过上述那样的加热方式将镀覆钢板加热至奥氏体区域后,可以用压制模具进行成型及淬火。需要说明的是,加热后,可以在该温度下保持1~10分钟后进行冷却,也可以不保持而进行冷却。此外,淬火(冷却)可以以1~100℃/秒的冷却速度进行。
[0128]
若使用本发明的热冲压用镀覆钢板,则在热冲压的加热时zn
‑
ni镀层中的zn难以活动,能够防止zn向钢板中的扩散。因此,能够使热冲压后的zn
‑
ni镀层中残存充分浓度的zn,其结果是,能够获得耐蚀性优异的热冲压成型体。
[0129]
[热冲压用镀覆钢板的制造方法]
[0130]
以下对本发明的热冲压用镀覆钢板的制造方法的例子进行说明。本发明的热冲压用镀覆钢板可以通过在钢板的至少一面、优选两面通过例如电镀形成zn
‑
ni镀层而获得。
[0131]
(钢板的制造)
[0132]
为了制造本发明的热冲压用镀覆钢板而使用的钢板的制造方法没有特别限定。例如,可以通过将钢液的成分组成调整为所期望的范围,进行热轧、卷取、进而冷轧而获得钢板。本发明中的钢板的板厚例如为0.1mm~3.2mm即可。
[0133]
所使用的钢板的成分组成没有特别限定,如上所述,钢板优选以质量%计含有c:0.05%以上且0.70%以下、mn:0.5%以上且11.0%以下、si:0.05%以上且2.00%以下、al:0.001%以上且1.500%以下、p:0.100%以下、s:0.100%以下、n:0.010%以下、及o:0.010%以下,剩余部分由铁及杂质构成。此外,钢板也可以以质量%计进一步含有选自由b:0.0005%以上且0.0040%以下、cr:0.01%以上且2.00%以下、ti:0.001%以上且0.300%以下、nb:0.001%以上且0.300%以下、v:0.001%以上且0.300%以下、zr:0.001%以上且0.300%以下、mo:0.001%以上且2.000%以下、cu:0.001%以上且2.000%以下、ni:0.001%以上且2.000%以下、sb:0.001%以上且0.100%以下、ca:0.0001%以上且0.0100%以下、mg:0.0001%以上且0.0100%以下、及rem:0.0001%以上且0.1000%以下构成的组中的至少一种。
[0134]
(zn
‑
ni镀层的形成)
[0135]
本发明中的zn
‑
ni镀层的形成方法只要可得到本发明的ni浓度、镀覆附着量及平均结晶粒径则没有特别限定,可以通过电镀而形成。特别是为了得到比较大的结晶粒径的zn
‑
ni镀覆,优选以比较低的电流密度进行电镀,例如可以以150a/dm2以下、100a/dm2以下或70a/dm2以下进行电镀。电流密度的下限没有特别限定,从生产率的观点出发,为10a/dm2或20a/dm2即可。另一方面,若以280a/dm2以上进行电镀,则有可能平均结晶粒径变成50nm以下。用于形成zn
‑
ni镀层的浴组成例如为硫酸镍
·
6水合物:150~350g/l、硫酸锌
·
7水合物:10~150g/l、及硫酸钠:25~75g/l即可。
[0136]
镀浴例如可以使用硫酸,例如调整ph至2.0以下、1.5以下或1.0以下,进而,镀浴的温度例如设定为45℃以上、50℃以上或55℃以上较佳。
[0137]
在通过电镀来制造本发明的热冲压用镀覆钢板的情况下,通过适当变更电镀时的电流密度、浴组成及通电时间,能够调整zn
‑
ni镀层的ni浓度、镀覆附着量、及平均结晶粒径。更具体而言,ni浓度可以通过变更电流密度及浴组成来调整,镀覆附着量可以通过变更电流密度及通电时间来调整,粒径可以通过变更电流密度来调整。
[0138]
如上所述在钢板上通过电镀而形成zn
‑
ni镀层后,为了缓和该镀层的应变,例如用退火炉(baf)等任意的炉进行加热处理较佳。加热处理温度为150~250℃下即可。若加热处理温度过低则无法充分缓和zn
‑
ni镀层的应变,若过高则有可能钢板及镀层的金属组织发生变化。加热处理的时间为1~48小时即可,优选为2~12小时。此外,例如,从防止zn
‑
ni镀层的氧化等观点出发,加热处理气氛优选为包含氢的还原气氛,更具体而言,为包含1~10%的氢的氮气氛,至上述加热处理温度为止的升温速度为20~100℃/小时即可。ni由于在比较低温的含氢气氛下被还原,因此认为通过在该含氢气氛下被还原的ni可抑制zn的氧化。此外,通过这样的含氢气氛下的加热处理,能够缓和在热冲压前残存于zn
‑
ni镀层中的应变(应力),因此,能够获得上述的200℃下1小时的热处理前后的最大x射线衍射峰的角度的位移为0.3
°
以下的本发明的热冲压用镀覆钢板。
[0139]
实施例
[0140]
对于本发明的热冲压用镀覆钢板,以下列举出几个例子更详细地进行说明。但是,并非有意通过以下说明的特定的例子来限制权利要求书中记载的本发明的范围。
[0141]
[热冲压用镀覆钢板的试样的制作]
[0142]
将板厚为1.4mm的冷轧钢板浸渍于具有以下的浴组成的镀浴中,通过电镀在该冷轧钢板上的两面形成zn
‑
ni镀层,得到热冲压用镀覆钢板的试样no.1~13。需要说明的是,所使用的全部的钢板以质量%计含有c:0.50%、mn:3.0%、si:0.50%、al:0.100%、p:0.010%、s:0.020%、n:0.003%、o:0.003%、及b:0.0010%,剩余部分为铁及杂质。
[0143]
镀浴组成
[0144]
·
硫酸镍
·
6水合物:250g/l(固定)
[0145]
·
硫酸锌
·
7水合物:10~150g/l(可变)
[0146]
·
硫酸钠:50g/l(固定)
[0147]
浴的ph使用硫酸而设定为1.5,将浴温维持在50℃下。需要说明的是,试样no.8由于为以高电流密度(300a/dm2)的镀覆,因此为了防止镀覆烧焦,浴的ph设定为1.0,将浴温维持在70℃下。为了得到所期望的zn
‑
ni镀层的镀覆附着量及平均结晶粒径,调整电流密度
及通电时间。此外,为了得到所期望的ni浓度,基于所设定的电流密度,适当调整硫酸锌
·
7水合物的浓度。将为了制造各试样而设定的电流密度示于表1中。
[0148]
通过icp分析来确定通过电镀得到的各试样的ni浓度及每一面的镀覆附着量。具体而言,用10%hcl从各试样仅将镀层溶解,通过对所得到的溶液进行icp分析而求出ni浓度及每一面的镀覆附着量。将各试样的ni浓度及每一面的镀覆附着量示于表1中。
[0149]
通过xrd来确定zn
‑
ni镀层的平均结晶粒径。首先,通过各试样的使用了co
‑
kα射线的xrd(真空管电压:40kv及真空管电流:200ma)求出衍射峰的半值幅b。然后,使用求出的半值幅b,通过以下的scherrer式计算平均结晶粒径:
[0150]
平均结晶粒径(nm)=kλ/bcosθ
ꢀꢀ
(1)
[0151]
(式中,k:scherrer常数=0.9、λ:co
‑
kα射线波长(nm)、θ为布拉格角(弧度))。其中,设定为在co
‑
kα射线波长λ=0.179nm、布拉格角θ=50.1~50.3
°
的范围内确认到的衍射线的角度。将各试样的平均结晶粒径示于表1中。
[0152]
对于试样no.1~9、12及13,形成zn
‑
ni镀层后,用包含4%氢的氮气氛的退火炉(baf)在200℃的温度下进行4小时(240分钟)的加热处理。升温速度设定为50℃/小时。在保持4小时后,用12小时进行缓慢冷却,从退火炉中取出。对于试样no.10,在形成zn
‑
ni镀层后未进行上述加热处理。对于试样no.11,用1分钟加热至200℃,立即进行水冷。需要说明的是,表1中的“加热处理温度”及“保持时间”分别表示加热处理的温度及时间。
[0153]
接着,对于试样no.1~13中的zn
‑
ni镀层,通过使用了co
‑
kα射线的xrd来测定最大x射线衍射峰的角度。此外,将试样no.1~13在退火炉中在200℃下进行1小时热处理,再次对zn
‑
ni镀层通过使用了co
‑
kα射线的xrd来测定最大x射线衍射峰的角度。由所测定的热处理前后的最大x射线衍射峰的角度算出最大x射线衍射峰的角度的位移量。在各试样中,最大x射线衍射峰的角度2θ在50.1~50.3
°
附近被观测到,该峰是起因于ni
‑
zn的γ相的峰。将各试样的最大x射线衍射峰的位移量示于表1中。需要说明的是,作为测定条件,采用电压:45kv、电流:40ma、测定角:10
°
~90
°
、狭缝:1/2
°
、步进尺寸:0.1
°
、入射角:2
°
。
[0154]
[热冲压用镀覆钢板的评价]
[0155]
对如上所述得到的热冲压用镀覆钢板的试样no.1~13进行热冲压。热冲压是将大气炉升温至900℃,保持4分钟后,使用前端r:3mm的v弯曲模具进行成型及淬火(冷却速度:50℃/秒)。对于所得到的各热冲压成型体,作为耐蚀性的评价试验进行了盐水喷雾试验(依据jaso m609
‑
91法)。该盐水喷雾试验将(1)盐水喷雾2小时(5%nacl、35℃);(2)干燥4小时(60℃);及(3)湿润2小时(50℃、湿度95%以上)设定为1个循环而实施了合计6个循环(合计48小时)。为了防止从端面起的腐蚀,将各试样的端面通过胶带进行密封而试验。各试样设定为宽度50mm、长度100mm。
[0156]
耐蚀性的评价通过对盐水喷雾试验48小时后的试样的平面部用光学显微镜进行观察,确定锈产生面积率z来进行。具体而言,首先,对试样的表面用扫描仪读入。之后,使用图像编辑软件选择产生了锈的区域,求出锈产生面积率。对5个试样进行该步骤,将锈产生面积率平均化而确定“锈产生面积率z”。z<10%的情况设定为“耐蚀性
◎”
,10%≤z≤30%的情况设定为“耐蚀性〇”,及z>30%的情况设定为“耐蚀性
×”
,将结果示于表1中。
[0157]
[表1:热冲压用镀覆钢板的特性及评价结果]
[0158][0159]
就本发明的热冲压用镀覆钢板的试样no.1~4、6、7、12、及13而言,热冲压成型体的耐蚀性良好。特别是关于试样no.3、4、6及13,ni浓度为10质量%以上,并且,每一面的镀覆附着量为50g/m2以上,可确保充分的ni浓度及充分的厚度的zn
‑
ni镀层,耐蚀性更加良好。
[0160]
就试样no.5而言,热冲压成型体的耐蚀性不充分。可认为这是由于:镀覆附着量不足,zn
‑
ni镀层薄,该镀层对于赋予耐蚀性而言厚度不充分。
[0161]
就试样no.8而言,热冲压成型体的耐蚀性不充分。可认为这是由于:电镀时的电流密度高,镀覆粒径变小,因此无法抑制热冲压的加热时的zn向钢板中的扩散。
[0162]
就试样no.9而言,热冲压成型体的耐蚀性不充分。可认为这是由于:热冲压前的初期的ni浓度低,在热冲压的加热时许多zn被氧化成zno,热冲压后的镀层的zn浓度降低。
[0163]
就试样no.10及11而言,热冲压成型体的耐蚀性不充分。可认为这是由于:衍射峰的位移大,即,残存于镀层中的应变大,在热冲压的加热时无法充分抑制zn向钢板中的扩散。
[0164]
产业上的可利用性
[0165]
根据本发明,能够提供在热冲压后可确保得以改善的耐蚀性的热冲压用镀覆钢板,由此,能够提供可以适宜用于汽车用构件等的耐蚀性优异的热冲压成型体。因此,本发明可以说是产业上的价值极高的发明。
再多了解一些
本文用于企业家、创业者技术爱好者查询,结果仅供参考。