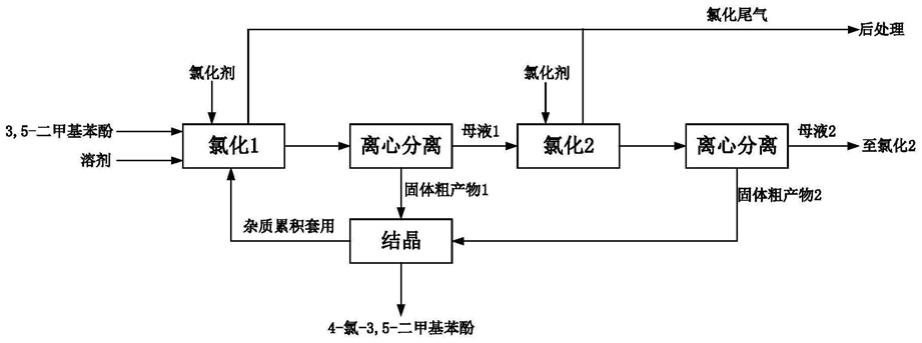
一种低温氯化制备4
‑
氯
‑
3,5
‑
二甲基苯酚的方法
技术领域
1.本发明属于精细化工领域,具体涉及一种低温氯化制备4
‑
氯
‑
3,5
‑
二甲基苯酚的方法。
背景技术:
[0002]4‑
氯
‑
3,5
‑
二甲基苯酚,结构如式(i)所示,是一种广谱的防霉抗菌剂,对多数革兰氏阳性、阴性菌、真菌、霉菌都有杀灭功效,它可作为防霉抗菌剂广泛应用于消毒或个人护理用品,如去屑香波,洗手液、肥皂和其它卫生用品等抗菌洗涤剂中。也可以作为防腐剂和防霉剂用于胶水、涂料、油漆、纺织、皮革、造纸等工业领域。4
‑
氯
‑
3,5
‑
二甲基苯酚由于其优异的杀菌和防腐功能,发展前景看好,已被广大消费者认可。
[0003][0004]4‑
氯
‑
3,5
‑
二甲基苯酚在工业上一般以3,5
‑
二甲基苯酚为原料,在氯化剂的作用下进行氯化反应得到,所用的氯化剂可以为硫酰氯或氯气。专利cn104326881a中提到一种以四氯乙烯为溶剂,苄硫酚和氯化铝为共催化剂,硫酰氯为氯化剂,通过低温氯化、高温氯化两阶段进行定向氯化反应合成4
‑
氯
‑
3,5
‑
二甲基苯酚的方法。该方法利用低温氯化保持产品4
‑
氯
‑
3,5
‑
二甲基苯酚的选择性,高温氯化提高底物的转化率,从而实现提高产品收率的目的。但是,在高温氯化(50~65℃)阶段,还是会导致产品的选择性降低,并且该方法的催化剂回收困难,对环境污染严重。
[0005]
专利cn102675055b中公开了一种高温氯化生产对氯间二甲苯酚的新方法,将硫酰氯气化后送入氯化塔下部,将液态原料进行预热升温后送入氯化塔上部,原料与气态硫酰氯在氯化塔内接触发生反应,物料通过循环泵强制外循环,循环泵出口设置换热器调节氯化塔内的温度。该方法可实现自动控制,连续化程度高,但是反应温度较高,产品选择性较差。
[0006]
专利cn103351282 b公开了一种4
‑
氯
‑
3,5
‑
二甲基苯酚的制备方法,由二价铜盐作催化剂,以3,5
‑
二甲基苯酚为原料,氧气为氧化剂,盐酸为氯化剂,在90~98℃下进行反应合成3,5
‑
二甲基
‑4‑
氯苯酚。该方法实际的3,5
‑
二甲基苯酚转化率达到99%时,产品的选择性仅达到80%,产品选择性低,产物分离难度增加。
[0007]
专利cn101823941b中公开了一种4
‑
氯
‑
3,5
‑
二甲基苯酚的绿色工业化制备方法,以水为溶剂,硫酰氯或氯气为氯化剂,将底物3,5
‑
二甲基苯酚通过多段控温的方式进行氯化反应。该方法的操作较为繁琐,难以在工业上大规模应用,而且反应过程中温度较高,导致反应选择性降低,反应过程生成的邻氯代副产物和二氯代副产物有10%以上。
[0008]
专利cn102659528a公开了连续釜式氯化工艺,该氯化工艺氯化剂通过分批次进行
加入,在一定程度上提高了反应的转化率和降低了副反应的发生,但是本发明人发现,在该氯化工艺中存在着晶体析出的问题,如氯化釜b和氯化釜c会有晶体析出,尤其是氯化釜c中析出的晶体更多,析出的晶体多,导致原料3,5
‑
二甲基苯酚发生包裹,影响了反应的转化率,该专利最后仅仅分析了氯化釜c的出料口的组分组成,为考虑原料的包裹问题,其分析结果与实际反应过程有一定的偏差。
技术实现要素:
[0009]
本发明所要解决的技术问题在于提供一种低温氯化制备4
‑
氯
‑
3,5
‑
二甲基苯酚的方法,可以克服现有技术中低温氯化中产品结晶包裹原料所导致的转化率降低的问题。
[0010]
一种低温氯化制备4
‑
氯
‑
3,5
‑
二甲基苯酚的方法,包括:
[0011]
(1)3,5
‑
二甲基苯酚和氯化剂在低温下进行氯化反应,反应进行至有固体析出,进行固液分离,得到固体粗产物1与中间母液;
[0012]
(2)中间母液进一步在低温下进行氯化反应,反应完成后进行末次固液分离,得到固体粗产物2和最终母液;
[0013]
固体粗产物1和固体粗产物2经过后处理得到所述的4
‑
氯
‑
3,5
‑
二甲基苯酚。
[0014]
本发明人经过研究发现,低温氯化导致原料转化率降低的原因有两点:(1)析出的晶体密度小于溶剂密度,悬浮于溶剂表层,在溶剂表层聚集结块,阻挡氯化剂与底物的反应,而且反应装置越大,这种阻碍现象越明显,底物转化率越低;(2)晶体结块,会包裹原料,又会造成部分原料无法参与反应。以上两点是影响3,5
‑
二甲基苯酚在低温条件下转化率低的主要原因。本发明通过将析出的晶体及时与反应液分离,既可以避免晶体大面积结块,包裹原料,又可以避免析出的晶体阻挡氯化剂与底物的反应,特别适应于大生产工艺。此外,析出的晶体通过纯化处理,得到合格的产品,剩余的原料通过多次累积,回收后用于制备4
‑
氯
‑
3,5
‑
二甲基苯酚,使得剩余的原料转化完全。
[0015]
作为优选,步骤(1)中,氯化反应的温度为25~35℃,反应时间为5~8小时,由于固体产物及时从反应液中分离,较低的反应温度有利于产物转化率的提高。
[0016]
本发明中,所述的氯化剂可以采用现有技术中常用的对苯环进行氯化反应的试剂,作为优选,步骤(1)中,所述的氯化剂为硫酰氯、氯气中的一种或者两种。
[0017]
作为优选,步骤(1)中,氯化反应在卤代烃类溶剂中进行;所述的卤代烃类溶剂优选为氯取代的c1~c3烃类化合物;更优选为二氯甲烷、三氯甲烷、四氯化碳、三氯乙烯、四氯乙烯中的一种或多种组合,最优选为在四氯乙烯中进行。
[0018]
作为优选,所述的氯化剂为硫酰氯,硫酰氯分批加入,步骤(1)中,以质量计,3,5
‑
二甲基苯酚:硫酰氯=1:0.5~0.8;
[0019]
步骤(2)中,以质量计,3,5
‑
二甲基苯酚:硫酰氯=1:0.3~0.8。
[0020]
步骤(1)和步骤(2)中,两次氯化剂加入方式不限,可以是滴加,可以是计量泵转料,可以是喷射器喷射进料(增大接触面积),也可以是进料管插入液面以下进料(气体进料)等,作为优选,当氯化剂为硫酰氯时,步骤(1)和步骤(2)中,硫酰氯采用滴加的方式加入。
[0021]
作为优选,步骤(2)中,所述氯化反应的温度为30~35℃,反应时间为2~5小时。步骤(2)的反应可以比步骤(1)反应温度略高,以促进后期反应的进行。
[0022]
作为优选,步骤(1)和(2)中,所述固液分离的操作方式为离心或者过滤;
[0023]
所述固体粗产物1和固体粗产物2通过降温结晶得到4
‑
氯
‑
3,5
‑
二甲基苯酚。其中,降温结晶的具体过程如下:将固体粗产物1和固体粗产物2混合,加入1.5~2.0倍的溶剂(以混合固体质量计,优选为四氯乙烯),升温75~85℃搅拌溶解,然后以3~8℃/h的速率降温,最终温度控制在25~30℃,通过离心获得产品4
‑
氯
‑
3,5
‑
二甲基苯酚和结晶母液。
[0024]
作为优选,固液分离得到的母液、降温结晶得到的结晶母液加入到下一批次的氯化反应中进行套用。通过该套用操作,可以进一步提高原料的利用率,减少废液的排放处理。
[0025]
作为优选,低温氯化反应产生的尾气经过冷凝,进行回收。
[0026]
步骤(1)中,其中固液分离的次数无特别的限定,可以为一次或者多次,作为优选,所述固液分离的次数为一次,在转化率达到40~70%时进行,此时可以兼顾操作方便和反应收率的目的;作为另外的优选,所述固液分离的次数为多次,每次固液分离得到的固体合并为固体粗产物1,每次固液分离得到的中间母液继续进行反应。分离次数的增加可以及时转移析出的固体,有利于反应的发生,但是分离次数过多也会造成操作复杂,分离次数进一步优选为2~4次。
[0027]
同现有技术相比,本发明的有益效果体现在:
[0028]
(1)本发明在反应过程中及时将析出的晶体分离出来,一方面减少了原料的包裹,提高了转化率,另一方面减少了结晶物对反应的阻碍,增加了反应速率;
[0029]
(2)低温氯化能够提高产品的选择性,减少副产物的生成,因此废液处理量也会大幅度降低,有利于环保。
附图说明
[0030]
图1为本发明的制备4
‑
氯
‑
3,5
‑
二甲基苯酚的工艺流程图(以分离次数为一次作为示例)。
具体实施方式
[0031]
以下结合具体实施例对本发明作进一步的描述,实施例中得到的产物的纯度,如无特别说明为hplc纯度。
[0032]
实施例1
[0033]
氯化1:在500ml的四口烧瓶中加入61g 3,5
‑
二甲基苯酚,四氯乙烯122g,启动搅拌装置,保温在25~35℃之间,在此温度下匀速滴加33.6g硫酰氯,滴加时间为5小时,滴加完毕,取样分析,3,5
‑
二甲基苯酚一次转化率为48.78%。通过降温离心将析出的固体1与母液1分离,温度控制在20~25℃。
[0034]
氯化2:母液1重新加入到四口烧瓶中,然后启动搅拌装置,保温在30~35℃之间,在此温度下继续滴加33.6g硫酰氯,滴加时间为3小时,滴加完毕,取样分析,3,5
‑
二甲基苯酚二次转化率为47.78%。通过降温离心将析出的固体2与母液2分离,温度控制在20~25℃。
[0035]
将固体1与固体2合并处理,加入105.0g四氯乙烯,升温至80℃搅拌溶解,缓慢降温至25~30℃,经过离心、干燥后得到白色针状结晶产物4
‑
氯
‑
3,5
‑
二甲基苯酚(69.97g,
99.28%),原料的两次转化率之和为96.56%,产品收率88.84%,产品选择性92.01%,结晶离心母液作为原料套用至下一批反应。
[0036]
实施例2
[0037]
氯化1:在500ml的四口烧瓶中加入61g 3,5
‑
二甲基苯酚,四氯乙烯183g,启动搅拌装置,保温在25~35℃之间,在此温度下匀速滴加40.3g硫酰氯,滴加时间为6小时,滴加完毕,取样分析,3,5
‑
二甲基苯酚一次转化率为58.50%。通过降温离心将析出的固体1与母液1分离,温度控制在20~25℃。
[0038]
氯化2:母液1重新加入到四口烧瓶中,然后启动搅拌装置,保温在30~35℃之间,在此温度下继续滴加29.9g硫酰氯,滴加时间为4小时,滴加完毕,取样分析,3,5
‑
二甲基苯酚二次转化率为38.47%。通过降温离心将析出的固体2与母液2分离,温度控制在20~25℃。
[0039]
将固体1与固体2合并处理,加入105.0g四氯乙烯,升温至80℃搅拌溶解,缓慢降温至25~30℃,经过离心、干燥后得到白色针状结晶产物4
‑
氯
‑
3,5
‑
二甲基苯酚(69.62g,99.42%),原料的两次转化率之和为96.97%,产品收率88.52%,产品选择性91.29%,结晶离心母液作为原料套用至下一批反应。
[0040]
实施例3
[0041]
氯化1:在500ml的四口烧瓶中加入61g 3,5
‑
二甲基苯酚,四氯乙烯305g,启动搅拌装置,保温在25~35℃之间,在此温度下匀速滴加46.9g硫酰氯,滴加时间为8小时,滴加完毕,取样分析,3,5
‑
二甲基苯酚一次转化率为68.09%。通过降温离心将析出的固体1与母液1分离,温度控制在20~25℃。
[0042]
氯化2:母液1重新加入到四口烧瓶中,然后启动搅拌装置,保温在30~35℃之间,在此温度下继续滴加26.3g硫酰氯,滴加时间为2小时,滴加完毕,取样分析,3,5
‑
二甲基苯酚二次转化率为29.32%。通过降温离心将析出的固体2与母液2分离,温度控制在20~25℃。
[0043]
将固体1与固体2合并处理,加入108.0g四氯乙烯,升温至80℃搅拌溶解,缓慢降温至25~30℃,经过离心、干燥后得到白色针状结晶产物4
‑
氯
‑
3,5
‑
二甲基苯酚(71.10g,99.35%),原料的两次转化率之和为97.41%,产品收率90.33%,产品选择性92.73%,结晶离心母液作为原料套用至下一批反应。
[0044]
实施例4
[0045]
氯化1:在500ml的四口烧瓶中加入61g 3,5
‑
二甲基苯酚,四氯乙烯305g,启动搅拌装置,保温在25~35℃之间,在此温度下匀速滴加44.0g硫酰氯,滴加时间为7小时,滴加完毕,取样分析,3,5
‑
二甲基苯酚一次转化率为64.81%。通过降温离心将析出的固体1与母液1分离,温度控制在20~25℃。
[0046]
氯化2:母液1重新加入到四口烧瓶中,然后启动搅拌装置,保温在30~35℃之间,在此温度下继续滴加29.2g硫酰氯,滴加时间为3小时,滴加完毕,取样分析,3,5
‑
二甲基苯酚二次转化率为32.93%。通过降温离心将析出的固体2与母液2分离,温度控制在20~25℃。
[0047]
将固体1与固体2合并处理,加入110.0g四氯乙烯,升温至80℃搅拌溶解,缓慢降温至25~30℃,经过离心、干燥后得到白色针状结晶产物4
‑
氯
‑
3,5
‑
二甲基苯酚(72.61g,
99.41%),原料的两次转化率之和为97.74%,产品收率92.31%,产品选择性94.44%,结晶离心母液作为原料套用至下一批反应。
[0048]
实施例5
[0049]
氯化1:在500ml的四口烧瓶中加入61g 3,5
‑
二甲基苯酚,四氯乙烯305g,启动搅拌装置,保温在25~35℃之间,在此温度下匀速滴加51.2g硫酰氯,滴加时间为8小时,滴加完毕,取样分析,3,5
‑
二甲基苯酚一次转化率为72.32%。通过降温离心将析出的固体1与母液1分离,温度控制在20~25℃。
[0050]
氯化2:母液1重新加入到四口烧瓶中,然后启动搅拌装置,保温在30~35℃之间,在此温度下继续滴加22.0g硫酰氯,滴加时间为2小时,滴加完毕,取样分析,3,5
‑
二甲基苯酚二次转化率为23.08%。通过降温离心将析出的固体2与母液2分离,温度控制在20~25℃。
[0051]
将固体1与固体2合并处理,加入108.0g四氯乙烯,升温至80℃搅拌溶解,缓慢降温至25~30℃,经过离心、干燥后得到白色针状结晶产物4
‑
氯
‑
3,5
‑
二甲基苯酚(68.48g,99.29%),原料的两次转化率之和为95.40%,产品收率86.95%,产品选择性91.14%,结晶离心母液作为原料套用至下一批反应。
[0052]
实施例6(套用实验)
[0053]
氯化1:将实施例1中的母液1、2与固体降温结晶制备4
‑
氯
‑
3,5
‑
二甲基苯酚过程中产生的结晶母液混合,加入到在500ml的四口烧瓶中,补充59.5g 3,5
‑
二甲基苯酚,四氯乙烯20g,启动搅拌装置,保温在25~35℃之间,在此温度下匀速滴加33.6g硫酰氯,滴加时间为5小时,滴加完毕,取样分析,3,5
‑
二甲基苯酚一次转化率为47.29%。通过降温离心将析出的固体1与母液1分离,温度控制在20~25℃。
[0054]
氯化2:母液1重新加入到四口烧瓶中,然后启动搅拌装置,保温在30~35℃之间,在此温度下继续滴加33.6g硫酰氯,滴加时间为2小时,滴加完毕,取样分析,3,5
‑
二甲基苯酚二次转化率为48.20%。通过降温离心将析出的固体2与母液2分离,温度控制在20~25℃。
[0055]
将固体1与固体2合并处理,加入105.0g四氯乙烯,升温至80℃搅拌溶解,缓慢降温至25~30℃,经过离心、干燥后得到白色针状结晶产物4
‑
氯
‑
3,5
‑
二甲基苯酚(70.12g,99.29%),原料的两次转化率之和为96.49%,产品收率89.03%,产品选择性92.27%,结晶离心母液作为原料套用至下一批反应。
[0056]
实施例7:
[0057]
氯化1:在500ml的四口烧瓶中加入61g 3,5
‑
二甲基苯酚,二氯甲烷305g,启动搅拌装置,保温在25~35℃之间,在此温度下向溶液中匀速通入氯气,氯气流量为1.5l/h,反应时间为6小时,滴加完毕,取样分析,3,5
‑
二甲基苯酚一次转化率为63.28%。通过降温离心将析出的固体1与母液1分离,温度控制在20~25℃。
[0058]
氯化2:母液1重新加入到四口烧瓶中,然后启动搅拌装置,保温在30~35℃之间,在此温度下向母液1中继续匀速通入氯气,氯气流量为1.2l/h,反应时间为4小时,滴加完毕,取样分析,3,5
‑
二甲基苯酚二次转化率为32.95%。通过降温离心将析出的固体2与母液2分离,温度控制在20~25℃。
[0059]
将固体1与固体2合并处理,加入150.0g二氯甲烷,升温至80℃搅拌溶解,缓慢降温
至25~30℃,经过离心、干燥后得到白色针状结晶产物4
‑
氯
‑
3,5
‑
二甲基苯酚(68.93g,99.32%),原料的两次转化率之和为96.23%,产品收率87.52%,产品选择性90.95%,结晶离心母液作为原料套用至下一批反应。
[0060]
实施例8
[0061]
氯化1:在500ml的四口烧瓶中加入61g 3,5
‑
二甲基苯酚,四氯乙烯305g,启动搅拌装置,保温在25~35℃之间,在此温度下匀速滴加30.0g硫酰氯,滴加时间为4小时,滴加完毕,取样分析,3,5
‑
二甲基苯酚一次转化率为39.63%。通过降温离心将析出的固体1与母液1分离,温度控制在20~25℃。
[0062]
氯化2:母液1重新加入到四口烧瓶中,然后启动搅拌装置,保温在30~35℃之间,在此温度下继续滴加22.0g硫酰氯,滴加时间为2小时,滴加完毕,取样分析,3,5
‑
二甲基苯酚二次转化率为29.51%。通过降温离心将析出的固体2与母液2分离,温度控制在20~25℃。
[0063]
氯化3:母液2重新加入到四口烧瓶中,然后启动搅拌装置,保温在30~35℃之间,在此温度下继续滴加21.2g硫酰氯,滴加时间为2小时,滴加完毕,取样分析,3,5
‑
二甲基苯酚三次转化率为29.32%。通过降温离心将析出的固体3与母液3分离,温度控制在20~25℃。
[0064]
将固体1、固体2与固体3合并处理,加入108.0g四氯乙烯,升温至80℃搅拌溶解,缓慢降温至25~30℃,经过离心、干燥后得到白色针状结晶产物4
‑
氯
‑
3,5
‑
二甲基苯酚(72.73g,99.37%),原料的三次转化率之和为98.46%,产品收率92.43%,产品选择性93.87%,结晶离心母液作为原料套用至下一批反应。
[0065]
对比例1
[0066]
在500ml的四口烧瓶中加入61g 3,5
‑
二甲基苯酚,四氯化碳305g,然后启动搅拌装置,保温在25
‑
35℃之间,在此温度下匀速滴加67.1g硫酰氯,滴加时间为8小时,滴加完毕,取样分析,3,5
‑
二甲基苯酚转化率为88.42%。
[0067]
反应液再分别经结晶、离心、干燥得到白色针状结晶产物4
‑
氯
‑
3,5
‑
二甲基苯酚(63.9g,99.64%),产品收率81.43%,产品选择性92.10%。
[0068]
对比例2
[0069]
在500ml的四口烧瓶中加入61g 3,5
‑
二甲基苯酚,四氯化碳305g,然后启动搅拌装置,在25
‑
35℃匀速滴加33.6g硫酰氯,滴加时间为4小时。然后,将反应温度升至60~65℃,在此温度下匀速滴加16.8g硫酰氯,滴加时间为2小时。最后,将反应温度升至80~85℃,在此温度下继续匀速滴加16.8g硫酰氯,滴加时间为2小时。滴加完毕,取样分析,3,5
‑
二甲基苯酚转化率为99.15%。
[0070]
反应液分别经结晶、离心、干燥得到白色针状结晶产物4
‑
氯
‑
3,5
‑
二甲基苯酚(65.6g,99.58%),产品收率83.62%,产品选择性84.34%。
[0071]
对比例3
[0072]
在500ml的四口烧瓶中加入61g 3,5
‑
二甲基苯酚,四氯乙烯95.8g,然后启动搅拌装置,硫酰氯进样口延伸到液面以下,位于搅拌桨上方,保温在35~40℃之间,在此温度下硫酰氯进料45.8g,进料时间为5小时,有少量固体析出;将反应温度控制在30~35℃,在此温度下硫酰氯继续进料19.6g,进料时间为2小时,固体析出量增加;将反应温度控制在20~
25℃,在此温度下硫酰氯再进料8.0g,进料时间为1小时,固体析出量大大增加,悬浮于液面之上;硫酰氯进料完毕,取样分析,3,5
‑
二甲基苯酚转化率为88.74%。
[0073]
反应液再分别经结晶、离心、干燥得到白色针状结晶产物4
‑
氯
‑
3,5
‑
二甲基苯酚(63.9g,99.47%),产品收率81.36%,产品选择性91.68%。
[0074]
对比例3的结果表明,如果采用改变温度分段进行反应,但是反应中间不将产物与母液进行分离,也会导致晶体包裹原料,隔绝反应,降低总的转化率和收率。
再多了解一些
本文用于企业家、创业者技术爱好者查询,结果仅供参考。