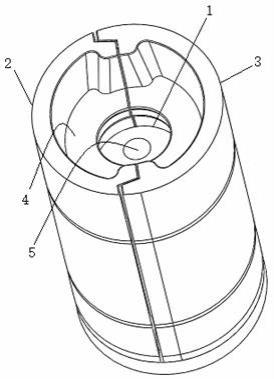
1.本发明涉及一种琉璃器具的制备工艺,具体而言涉及一种采用一种琉璃器具成型模具制备琉璃器具的工艺。
背景技术:
2.琉璃是用各种颜色的人造水晶为原料,在1000多度的高温下烧制而成的,其色彩流光溢彩,其品质晶莹剔透、光彩夺目。中国古代最初制作琉璃的材料,是从青铜器铸造时产生的副产品中获得的,然后经过提炼加工制成琉璃。
3.琉璃属于价值不菲的艺术品,原因有二:其一,古法琉璃材料特殊,而且其制作工艺相当复杂,火里来、水里去,要几十道工序才能完成,有的光制作过程就要十到二十天,且主要依靠手工。各个环节的把握相当困难,其火候把握之难更可以说是一半靠技艺一半凭运气。仅出炉一项,成品率就只有70%。更关键的是,古法琉璃不可回收,也就是说一旦出现一点点问题,十数天、几十道工序,多少人的努力就立刻付诸东流。其二,琉璃不仅仅是一种材质,更是一种文化产品,更重要的是,琉璃产品是独一无二的,没有两个一模一样的琉璃产品。
4.现有的琉璃器具的制备工艺(脱蜡工艺)如下:1)创意设计:将创意通过平面设计图稿进行表现;2)原型制作:根据图稿雕塑立体模型;3)制硅胶软模:在立体模型表面均匀涂抹硅胶,待硅胶凝固成硅胶软模(取出立体模型,但任需以石膏加以固定);4)灌制蜡模:调制蜡浆,在硅胶软模内灌入热融的蜡,待其自然冷却;5)拆取蜡模:将冷却后的蜡模自硅胶软模内脱出(或者说,将硅胶软模从蜡模上脱离开来);6)修整蜡模:冷却容易使蜡模收缩变形,对拆模时留下的模线痕迹,需要以工具细心地修整完美;7)制石膏模:调制正确比例的耐火石膏,在修饰后的蜡模外,灌注包埋,即成含蜡石膏模;8)蒸汽脱蜡:将整个含蜡石膏模置入脱蜡机内以蒸汽加温,脱蜡后即为耐火石膏硬模。
5.9)精选原料:为精确控制各种颜色的比例和流动的美感,需依造型与设计精选特定颜色与大小的琉璃原料,并安排色块的分布位置;10)进炉烧结:清模去尘后,将整个石膏硬模与配置好的琉璃料,放进炉内慢慢加温,使热熔软化的琉璃原料如麦芽糖般缓慢地流入石膏硬模内成型;11)拆除石膏:拆除石膏模,将冷却后的琉璃粗胚取出;12)切割修葺:将琉璃粗胚上注浆口部分多余的琉璃切割修葺;13)粗磨细磨:以粗、细研磨砂将琉璃的浇注口磨平整;
14)冷工细修:以钻石笔头及其它工具细心雕琢,使作品表面显得更为均匀细致;15)根据需要进一步进行喷砂、打磨、抛光等精细工艺,直至成为琉璃器具成品。
6.上述工艺步骤为单一琉璃器具的理论制备方法,在实际工业的“批量”生产过程中,还需要将立体模型转型为树脂硬膜,然后再通过树脂硬膜,转型为“批量”的硅胶软模。其原因是,由于立体模型往往是一种材质较软的泥膜(方便雕刻师傅雕塑成型),故在转型为硅胶软模的过程中或在存放的过程中会产生形变或损坏,从而不能通过一个立体模型转型为大量的硅胶软模,进而不能进行“批量”生产。
7.无论是理论制备方法还是工业制备方法,上述工艺中存在一个技术缺陷,该技术缺陷导致了在某些特殊琉璃器具的制备过程中,非常困难或者说难以实现。比如需要制备一种小口径的琉璃花瓶,具体遇到的技术难题如下:本身花瓶的造型为一中空结构,因此蜡模提供的模型也为一中空结构,中空结构内的硅胶软模需要从蜡模的空腔内取出(即上述工艺步骤5),但由于蜡模是一小口径的模型,因此空腔内的硅胶软模很难取出,即使取出大概率也会将蜡模破坏,导致后续工序无法进行。
8.传统的工艺中,为了制备诸如小口径花瓶类的器具,基本是通过“烧制技艺”实现,其大致的工艺步骤如下:1)化料:将所需要的各种颜料进入大炉熔炼,以熔融的琉璃在铁棒上旋转。
9.2)挑料:从1400多度高温的传统火炉中用1.5米长的吹筒中取出琉璃中取出琉璃体;3)吹制:从火炉中取出后不断进行旋转和造型,火炉里面取出的琉璃温度高,掌握好琉璃熔化的软度,几秒钟就要成型;4)塑型:在造型过程中,师傅们需要用手中的吹筒进行吹制,来保证琉璃的形状,由于尺度很难拿捏,所以成品率极低;5)退火:琉璃成型以后,师傅们要把烧制好的琉璃放到保温窑里面,500多度,保温4天,如果琉璃瓶身没有出现炸裂的情况,说明琉璃已退温成型。
10.该工艺易存在明显的技术缺陷,比如成品率极低,无法量产等情况。
技术实现要素:
11.为克服现有工艺的不足,本发明提供了一种琉璃器具成型模具及其制备工艺。该成型模具及其工艺适用于小口径造型的琉璃空腔器具的制作,同时可以应用于工业批量化制备琉璃器具,且成品率较高。
12.为解决上述技术问题,实现上述技术效果,本发明通过以下技术方案实现:一种琉璃器具成型模具,其包括中心定位模、第一侧模和第二侧模,所述中心定位模置于由所述第一侧模和所述第二侧模合模后形成的空腔内,且所述中心定位模与所述第一侧模和所述第二侧模之间留有琉璃器具的仿形腔体;所述第一侧模和所述第二侧模合模后上方为原料放置口,所述原料放置口的下方为浇筑口,所述浇筑口与所述仿形腔体联通。
13.一种琉璃器具制备工艺,包括以下步骤:1)模具制备:采用耐火石膏制作所述琉璃器具成型模具;2)精选原料:选择琉璃原料,放置在所述原料放置口;
3)进炉烧结:将放置有所述琉璃原料的所述成型模具放进炉内慢慢加温,使热熔软化的琉璃原料通过所述浇筑口流入所述仿形腔体内成型;4)拆除石膏:拆除石膏模,将冷却后的琉璃粗胚取出;5)切割修葺:将琉璃粗胚上注浆口部分多余的琉璃切割修葺;6)粗磨细磨:以粗、细研磨砂将琉璃粗胚的浇注口磨平整;7)冷工细修:对琉璃粗胚细心雕琢,使其表面均匀细致;8)根据需要进行喷砂、打磨、抛光工艺,直至成为琉璃器具成品。
14.与现有技术相比,本发明的有益效果为:本发明的工艺摒弃了蜡型的使用,通过中心定位模、第一侧模和第二侧模配合使用,直接以石膏模进行琉璃器具的制作,避免了小口径器具无法制备的窘境,同时可以通过批量化该成型模具进而进行批量化琉璃器具的制作。
15.上述说明仅是本发明技术方案的概述,为了能够更清楚了解本发明的技术手段,并可依照说明书的内容予以实施,以下以本发明的较佳实施例并配合附图详细说明如后。本发明的具体实施方式由以下实施例及其附图详细给出。
附图说明
16.此处所说明的附图用来提供对本发明的进一步理解,构成本技术的一部分,本发明的示意性实施例及其说明用于解释本发明,并不构成对本发明的不当限定。在附图中:图1为本发明的琉璃器具成型模具的结构示意图。
17.图2为本发明的琉璃器具成型模具的装配图。
18.图3为本发明的琉璃器具成型模具的第一侧模的结构示意图。
19.图4为本发明的琉璃器具成型模具的第二侧模的结构示意图。
20.图5为本发明的琉璃器具成型模具的中心定位模的结构示意图。
具体实施方式
21.下面将参考附图并结合实施例,来详细说明本发明。此处所作说明用来提供对本发明的进一步理解,构成本技术的一部分,本发明的示意性实施例及其说明用于解释本发明,并不构成对本发明的不当限定。
22.实施例1:参见1、图2所示,一种琉璃器具成型模具,其包括中心定位模1、第一侧模2和第二侧模3,所述中心定位模1置于由所述第一侧模2和所述第二侧模3合模后形成的空腔内,且所述中心定位模1与所述第一侧模2和所述第二侧模3之间留有琉璃器具的仿形腔体;所述第一侧模2和所述第二侧模3合模后上方为原料放置口4,所述原料放置口4的下方为浇筑口4,所述浇筑口4与所述仿形腔体联通。
23.进一步的,参见图3、图4所示,所述第一侧模2包括第一内胆205和第一外壁206,所述第一外壁206的侧壁与所述第一内胆205的外壁构成一侧模母头204;所述第二侧模3包括第二内胆305和第二外壁306,所述第二外壁306的侧壁与所述第二内胆305的外壁构成一侧模公头304;所述第一侧模2和所述第二侧模3合模后,所述侧模公头304与所述侧模母头204相互配合。
24.优选的,所述第一内胆205的边沿与所述第二内胆305的边沿紧密配合,所述第一外壁206的侧壁与所述第二外壁306的侧壁之间留有间隙。当所述第一侧模2和第二侧模3合模时,虽然第一内胆205的边沿与所述第二内胆305的边沿紧密配合,但由于模具材料为石膏,可能存在配合无法做到预想的紧密,此时由于第一外壁206的侧壁与所述第二外壁306的侧壁之间留有间隙,通过紧固侧模外壁的方式进一步压紧第一内胆205与所述第二内胆305之间配合关系。
25.优选的,所述侧模公头304与所述侧模母头204的接触面为斜面。考虑到石膏材质的“坚硬”属性,斜面的设置可以更好的实现两者直接的紧密配合。
26.进一步的,所述第一内胆205的边沿上开设有第一气道207,所述第一气道207一端联通外界,另一端联通所述第一内胆205的底部;所述中心定位模1与所述第一侧模2和所述第二侧模3合模后,所述第一气道207形成所述仿形腔体由下向上的一个气体通路。进一步的,所述第二内胆305的边沿上开设有第二气道307,所述第二气道307一端联通外界,另一端联通所述第二内胆305的底部;所述中心定位模1与所述第一侧模2和所述第二侧模3合模后,所述第二气道307形成所述仿形腔体由下向上的一个气体通路。
27.优选的,所述第一气道207与所述第二气道307相互配合形成一气流通道。
28.气体通路或气流通道的设置具有非常重要的意义,当热熔软化的琉璃原料通过所述浇筑口流入所述仿形腔体内时,腔体内的气体可以由腔体底部随气体通路或气流通道排出到外界,假如没有气体通路或气流通道,腔体的气体会直接通过热熔软化的琉璃原料内部及边沿挤压出来,导致琉璃原料内部存在微小的气孔,同时也会降低琉璃原料的流入速度。
29.进一步的,参见图5所述,所述中心定位模1包括底座101和主体104,所述底座101与所述主体104之间为一凸台102;所述第一侧模2的底部为第一底座201,所述第一底座201上开设有第一凹台202,所述第一底座201放置在所述底座101时,所述第一凹台202与所述凸台102紧密配合;所述第二侧模3的底部为第二底座301,所述第二底座301上开设有第二凹台302,所述第二底座301放置在所述底座101时,所述第二凹台302与所述凸台102紧密配合。
30.优选的,所述第一凹台202与所述凸台102的接触面为斜面;所述第二凹台302与所述凸台102的接触面为斜面。考虑到石膏材质的“坚硬”属性,斜面的设置可以更好的实现两者直接的紧密配合。
31.优选的,所述第一底座201上设置有第一定位块203,所述第二底座301上设置有第二定位块303,所述底座101上与所述第一定位块203和所述第二定位块303相对应的位置开设有定位孔103。定位孔和定位块的设置是一种优选的方案,可以防止中心定位模在侧模腔体内自由的转动或移动。
32.实施例2:一种琉璃器具的制备工艺,包括以下步骤:1)模具制备:采用耐火石膏制作所述琉璃器具成型模具;2)精选原料:选择琉璃原料,放置在所述原料放置口4;3)进炉烧结:将放置有所述琉璃原料的所述成型模具放进炉内慢慢加温,使热熔软化的琉璃原料通过所述浇筑口4流入所述仿形腔体内成型;
4)拆除石膏:拆除石膏模,将冷却后的琉璃粗胚取出;5)切割修葺:将琉璃粗胚上注浆口部分多余的琉璃切割修葺;6)粗磨细磨:以粗、细研磨砂将琉璃粗胚的浇注口磨平整;7)冷工细修:对琉璃粗胚细心雕琢,使其表面均匀细致;8)根据需要进行喷砂、打磨、抛光工艺,直至成为琉璃器具成品。
33.本实施中的工艺已取消了现有脱蜡工艺中原型制作、制硅胶软模、灌制蜡模、拆取蜡模、修整蜡模、蒸汽脱蜡等相关工序步骤,一方面简化的工艺流程,另一方面全新的方案拓宽了各种造型的琉璃工艺品的工业化批量生产的道路。
34.以上所述仅为本发明的优选实施例而已,并不用于限制本发明,对于本领域的技术人员来说,本发明可以有各种更改和变化。凡在本发明的精神和原则之内,所作的任何修改、等同替换、改进等,均应包含在本发明的保护范围之内。
再多了解一些
本文用于企业家、创业者技术爱好者查询,结果仅供参考。